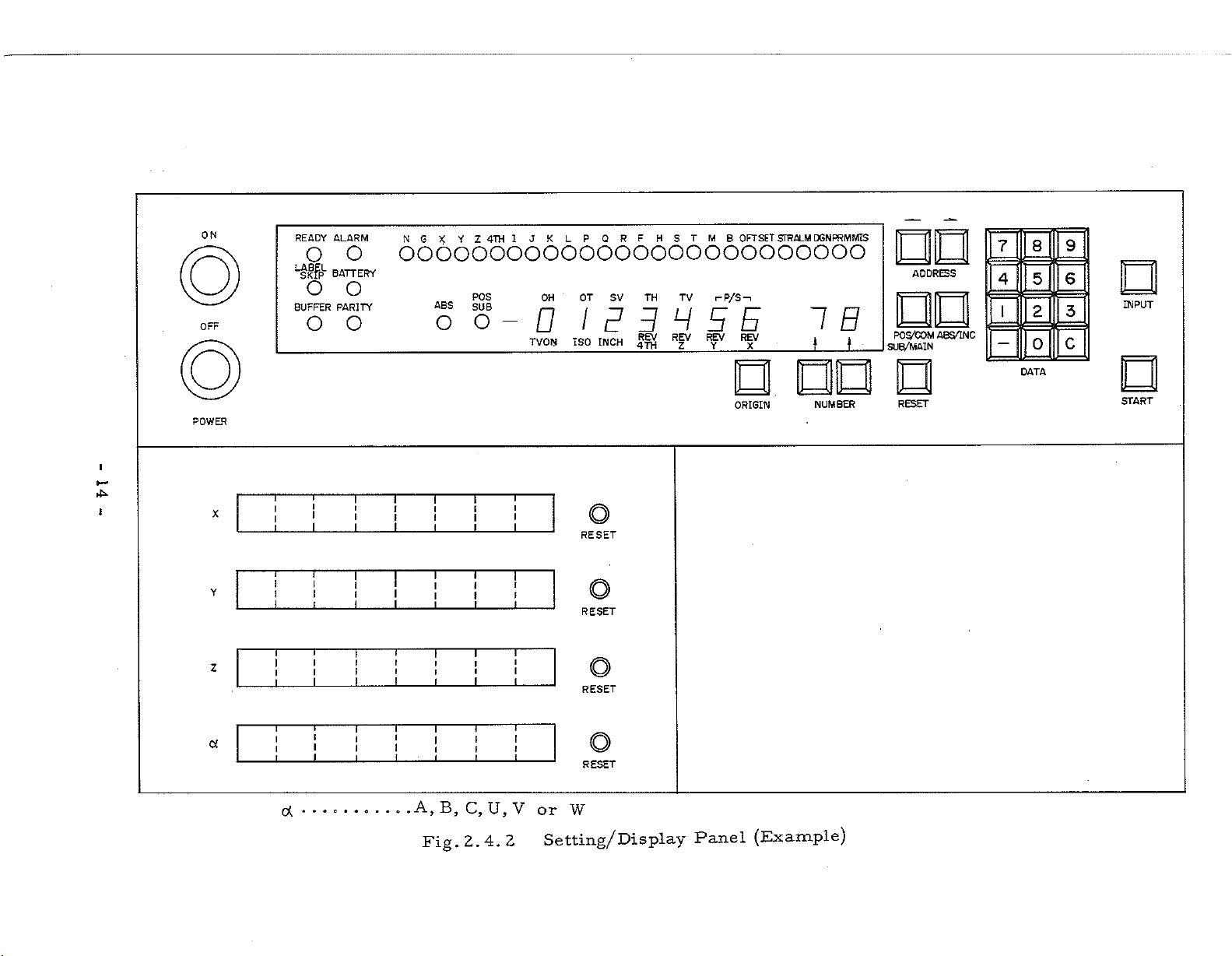
ON
OFF
READY
o
LABEL
SKIP
o
BUFFER
o
ALARM
o
BATTERY
o
PARITY
o
NG
XYZ
4TH
LP
QRF
HSTMB
OFTSET
JK
I
STRALM
DGNPRMMIS
oooooooooooooooooooooooooo
POS
OH
OT
SV
oo-OIPBHEE
ISO
TVON
INCH
TH
REV
4TH
TV
REV
Z
i-P/S-.
REV
Y
REV
X
IB
_
J
t
ADDRESS
PO
A8S/1NC
S/COM
SUB/MAIN
8
5
2
0
DATA
9
6
INPUT
E
c
7
4
I
NUMBER
Panel
ORIGIN
(Example)
POWER
I
4ÿ
!
X
Y
Z
a
T
T
I
1
T
1
1
T
I
l
1
I
i
1
(X
T T
i
I
i
I
T
1
1
I
f
I
i
1
T
T
i
f
f
I
I
T
T
I
J
i
i
I
1
T
1
I
I
1
I
T
II
I
T
T
r
r
l
f
I
1
T
I
i
I
I
1
A,
B,
2.4.
Fig,
T
1
I
T
I
f
I
i
T
\
F
1
C,U,V
T
RESET
I
i
I
I
T
i
1
T
I
i
2
RESET
RESET
RESET
W
or
Setting/Display
O
o
RESET
START