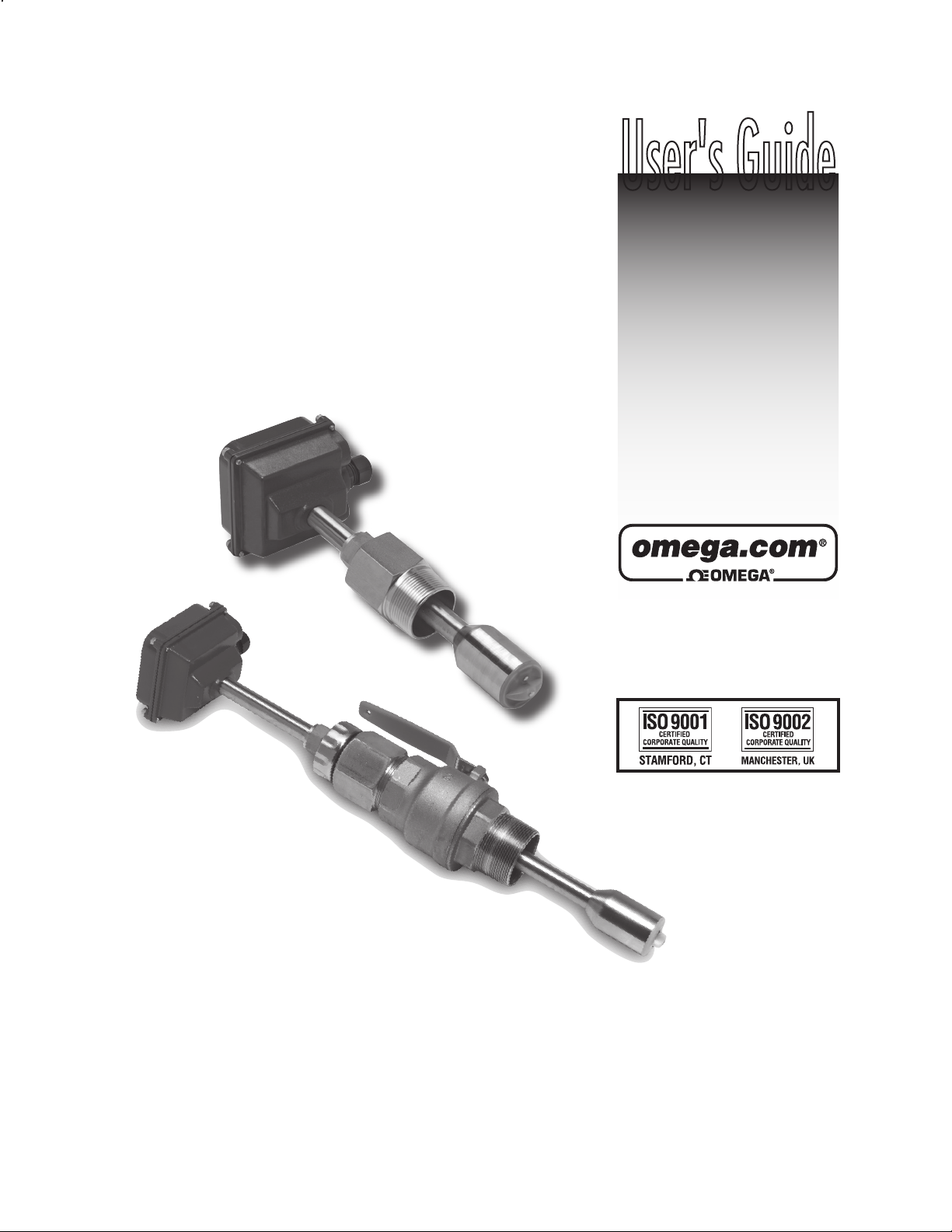
FMG-900 SERIES
Insertion Magnetic Flow Meter
User's Guide
Shop online at
omega.com
email: Info@omega.com
For latest product manuals:
omegamanual.Info
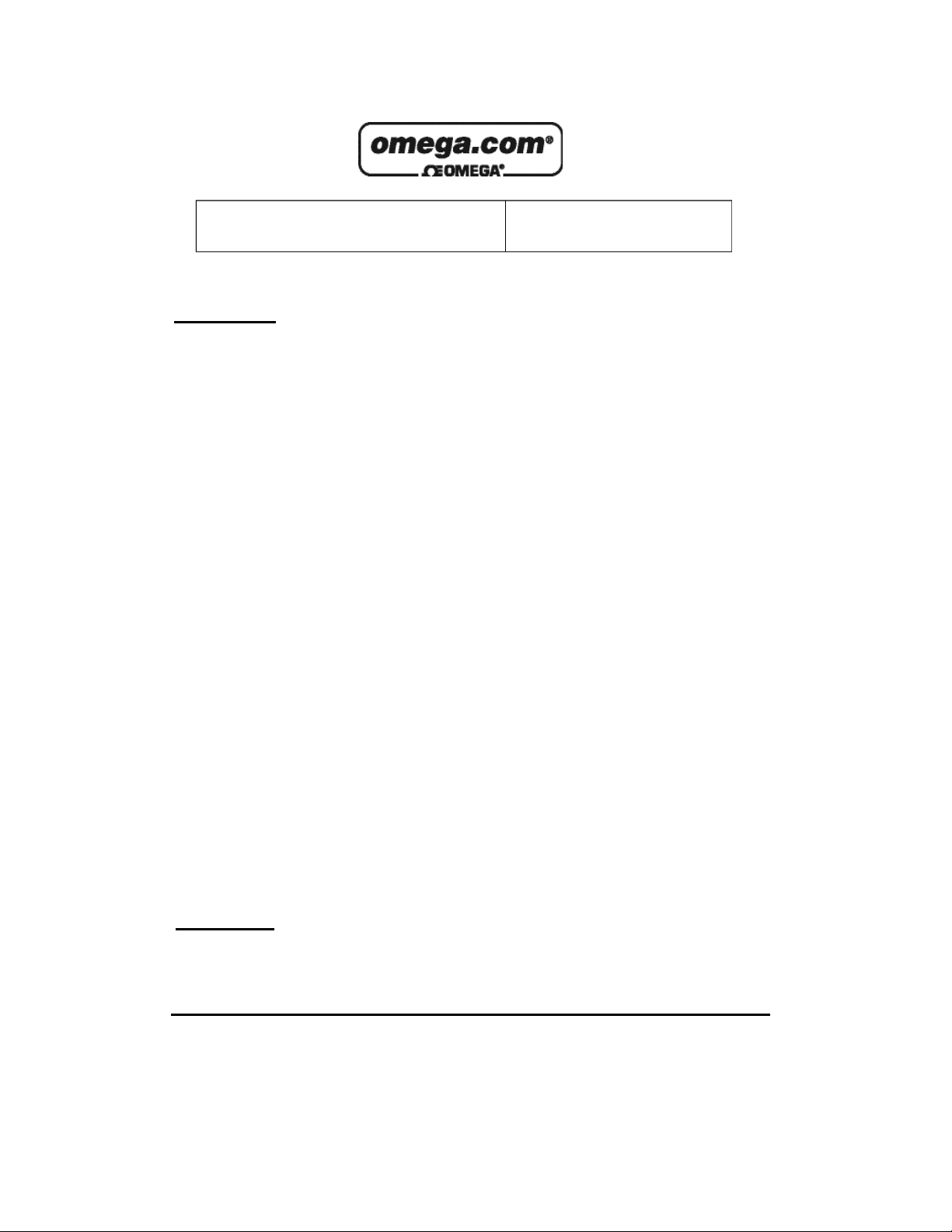
Servicing North America:
U.S.A.: One Omega Drive, P.O. Box 4047
ISO 9001 Certified
Stamford, CT 06907-0047
TEL: (203) 359-1660 FAX: (203) 359-7700
e-mail: info@omega.com
Canada: 976 Bergar
Laval (Quebec) H7L 5A1, Canada
TEL: (514) 856-6928 FAX: (514) 856-6886
e-mail: info@omega.ca
For immediate technical or application assistance:
U.S.A. and Canada: Sales Service: 1-800-826-6342 / 1-800-TC-OMEGA
®
Customer Service: 1-800-622-2378 / 1-800-622-BEST
®
Engineering Service: 1-800-872-9436 / 1-800-USA-WHEN
®
TELEX: 996404 EASYLINK: 62968934 CABLE: OMEGA
Mexico: En Espan˜ol: (001) 203-359-7803 e-mail: espanol@omega.com
FAX: (001) 203-359-7807 info@omega.com.mx
Servicing Europe:
Benelux: Postbus 8034, 1180 LA Amstelveen, The Netherlands
TEL: +31 (0)20 3472121 FAX: +31 (0)20 6434643
Toll Free in Benelux: 0800 0993344
e-mail: sales@omegaeng.nl
Czech Republic: Frystatska 184, 733 01 Karviná, Czech Republic
TEL: +420 (0)59 6311899 FAX: +420 (0)59 6311114
Toll Free: 0800-1-66342 e-mail: info@omegashop.cz
France: 11, rue Jacques Cartier, 78280 Guyancourt, France
TEL: +33 (0)1 61 37 2900 FAX: +33 (0)1 30 57 5427
Toll Free in France: 0800 466 342
e-mail: sales@omega.fr
Germany/Austria: Daimlerstrasse 26, D-75392 Deckenpfronn, Germany
TEL: +49 (0)7056 9398-0 FAX: +49 (0)7056 9398-29
Toll Free in Germany: 0800 639 7678
e-mail: info@omega.de
United Kingdom: One Omega Drive, River Bend Technology Centre
ISO 9002 Certified
Northbank, Irlam, Manchester
M44 5BD United Kingdom
TEL: +44 (0)161 777 6611 FAX: +44 (0)161 777 6622
Toll Free in United Kingdom: 0800-488-488
e-mail: sales@omega.co.uk
OMEGAnet
®
Online Service Internet e-mail
omega.com i n f o @ o m e g a . c o m
It is the policy of OMEGA Engineering, Inc. to comply with all worldwide safety and EMC/EMI
regulations that apply. OMEGA is constantly pursuing certification of its products to the European New
Approach Directives. OMEGA will add the CE mark to every appropriate device upon certification.
The information contained in this document is believed to be correct, but OMEGA accepts no liability for any
errors it contains, and reserves the right to alter specifications without notice.
WARNING: These products are not designed for use in, and should not be used for, human applications.
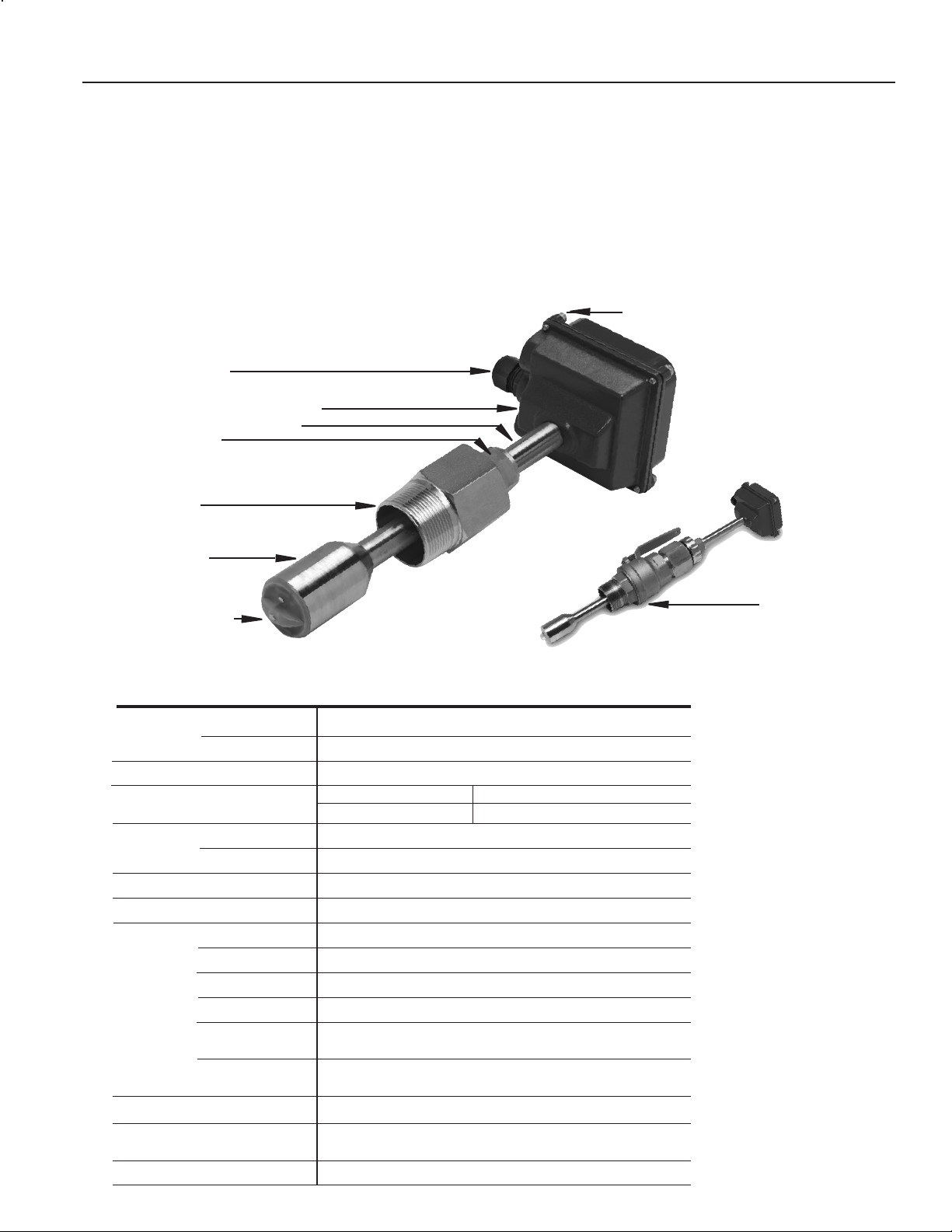
The complete lack of moving parts of this insertion flow sensor
is the source of its reliability. There is no rotor to stop turning
in dirty water and there are no bearings to wear out. Brass
and stainless steel models withstand a variety of temperature,
pressure, and chemical conditions. Reverse flow output and
immersibility are optional.
A rapidly reversing magnetic field is produced in the lower
housing. As the fluid moves through this field, a voltage is
generated that is measured and translated into a frequency
signal proportional to flow rate. This square wave signal can
be sent directly to a PLC or other control or can be converted
using any of the Omega family of indicators and converters.
The adapter fitting of the FMG-900 Series sensor is standard
male NPT, and can be directly threaded into ordinary saddles
or threaded weld fittings. The FMG905 and 906 include an
isolation valve, allowing hot-tap installation, or installation and
removal under pressure. A bronze ball valve is standard, with
a 316 stainless steel valve optional.
GENERAL INFORMATION
FEATURES
Valve assembly for
hot tap installation
FMG905/906
Brass or 316 stainless shaft
Rugged cast aluminum housing
Adapter fitting
Compression nut
Sensor housing
Electrodes and cap
Housing screw (connect ground to one)
Cable strain relief
FMG901/902
SPECIFICATIONS
12-24 Vdc, 250 mA
12-24 Vdc, 40 mA
0.28 - 20 ft/sec (0.08 - 6.09 m/sec)
FMG901/902 FMG905/906
1-1/2” Male NPT 2” Male NPT
0˚ to 180˚ F (-17˚ to 82˚ C)
32˚ to 200˚ F (0˚ to 93˚ C)
200 psi (13.8 bar)
20 microSiemens/cm
316 SS or Brass
Hastelloy
PVDF
Cast aluminum, powder-coated
Bronze (stainless optional) with bronze ball valve
EPDM
+/- 1% of full scale
Square wave pulse, opto isolated, 550 Hz @ 20 ft/sec
6 mA max, 30 Vdc forward flow standard; reverse flow optional
Software, defaults to zero flow
Power Full Power
Low Power
Flow Range
Fitting Size
Temperature Ambient
Fluid
Pressure
Minimum Conductivity
Materials Shaft/Fitting
Electrodes
Electrode Cap
Housing
Valve Assembly
(905/906 Only)
O-Ring
(905/906 Only)
Calibration Accuracy
Output
Empty Pipe Detection
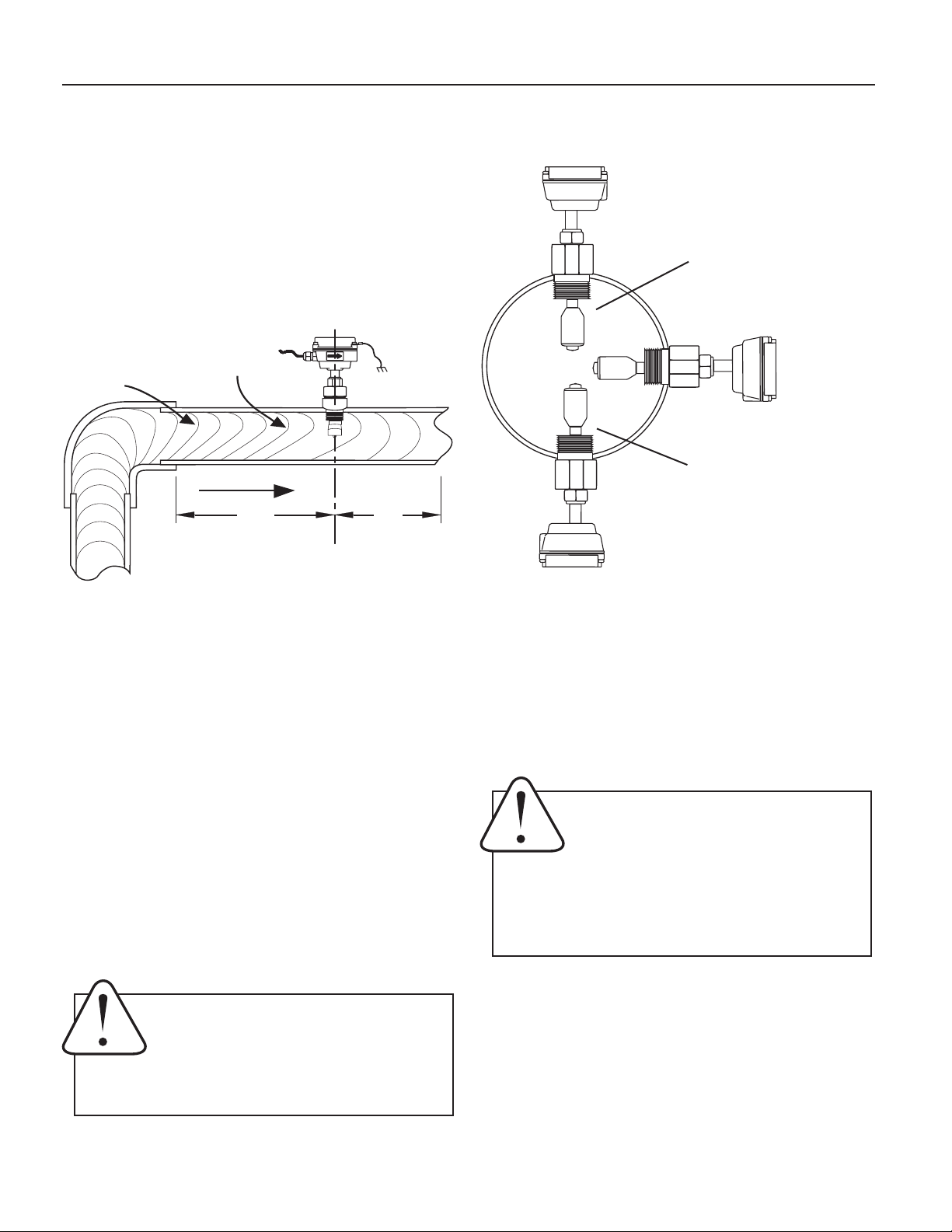
Piping. For best results, the FMG-900 Series sensor should
be installed with at least ten diameters of straight pipe
upstream and five downstream. Certain extreme situations
such as partially-opened valves are particularly difficult and
may require more straight diameters upstream (see Straight
Pipe Recommendations).
Immersion. The FMG901/902 Series standard sensors
are not designed for continuous underwater operation.
Chemical Injection or Fertigation. When any magmeter,
by any manufacturer, is used in a chemical injection ap-
plication (including fertigation), the chemical line must be
placed downstream of the magmeter OR far enough up-
stream for complete mixing to occur before the fluid reaches
the meter. When unmixed chemical or fertilizer alternates
with water passing through the meter, the rapid changes
in conductivity may cause sudden spikes and drops in the
meter’s reading, resulting in inaccurate measurement. The
magmeter will restabilize, however, with a steady flow of
fluid of uniform conductivity.
Caution: These flow sensors are not
recommended for installation down-
stream of a boiler feedwater pump
where installation fault may expose
the flow sensor to boiler pressure and tempera-
ture. Maximum recommended temperature is
200°F.
INSTALLATION
DISTORTED FLOWS
FLOW
POSITIONING THE METER
Horizontal is the preferred installation orientation, since it
improves low-flow per formance and avoids problems with
trapped air and sediment. Bottom, top, and vertical pipe
installations are all acceptable if required by the piping
layout (See Full Pipe Recommendations).
Fair (Unacceptable if
air is present)
Best
Position
Fair (Unacceptable if fluid
contains sediment)
Faster Flow
Causes Meter
To Read High
10X
5X
Distorted
Flow Profile
Caution: In chemical injection or fer-
tigation applications, install chemical
line downstream of magmeter, or far
enough upstream to allow complete
mixing of fluids before the meter.