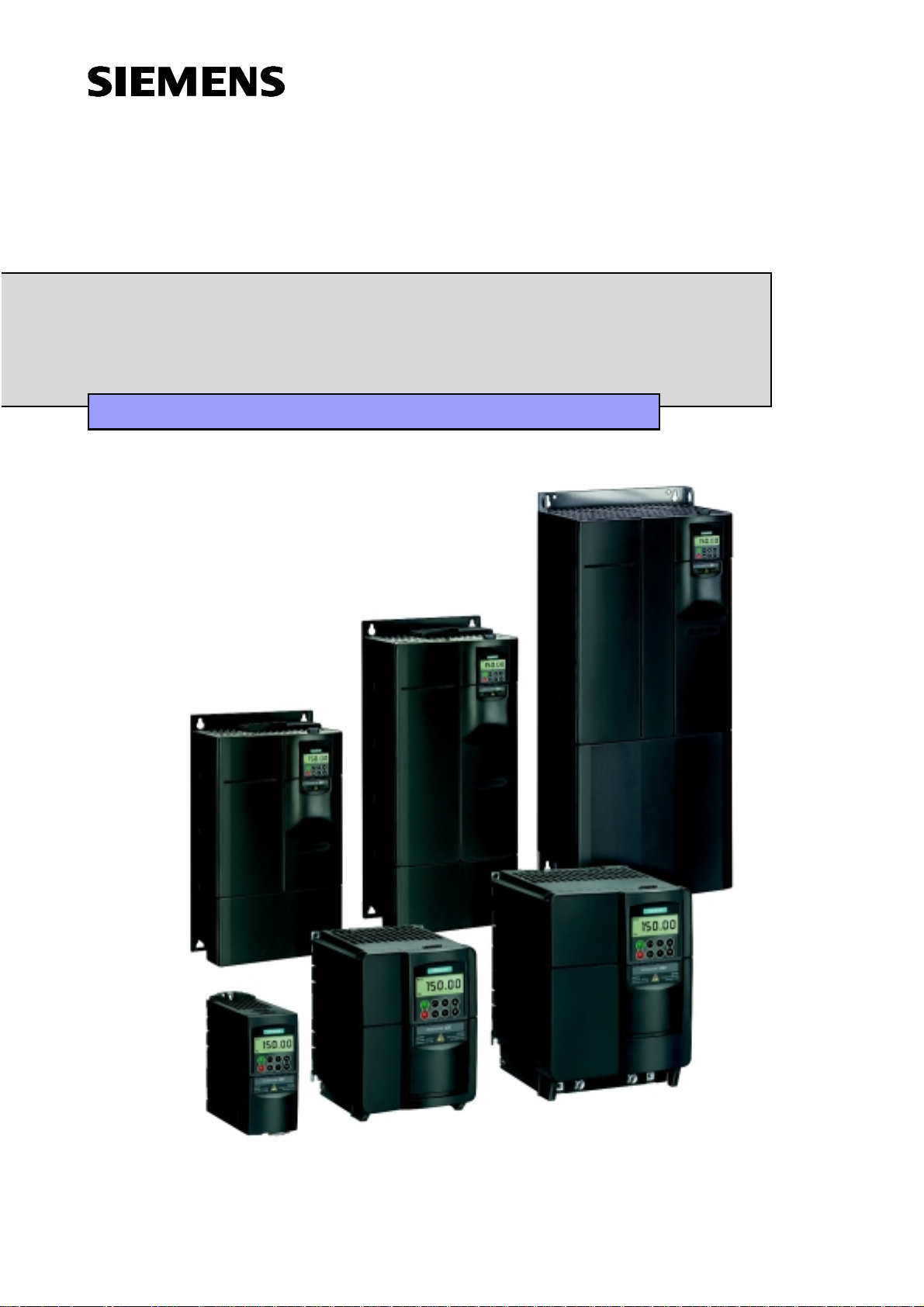
MICROMASTER 440
Operating instructions Issue A1
User Documentation
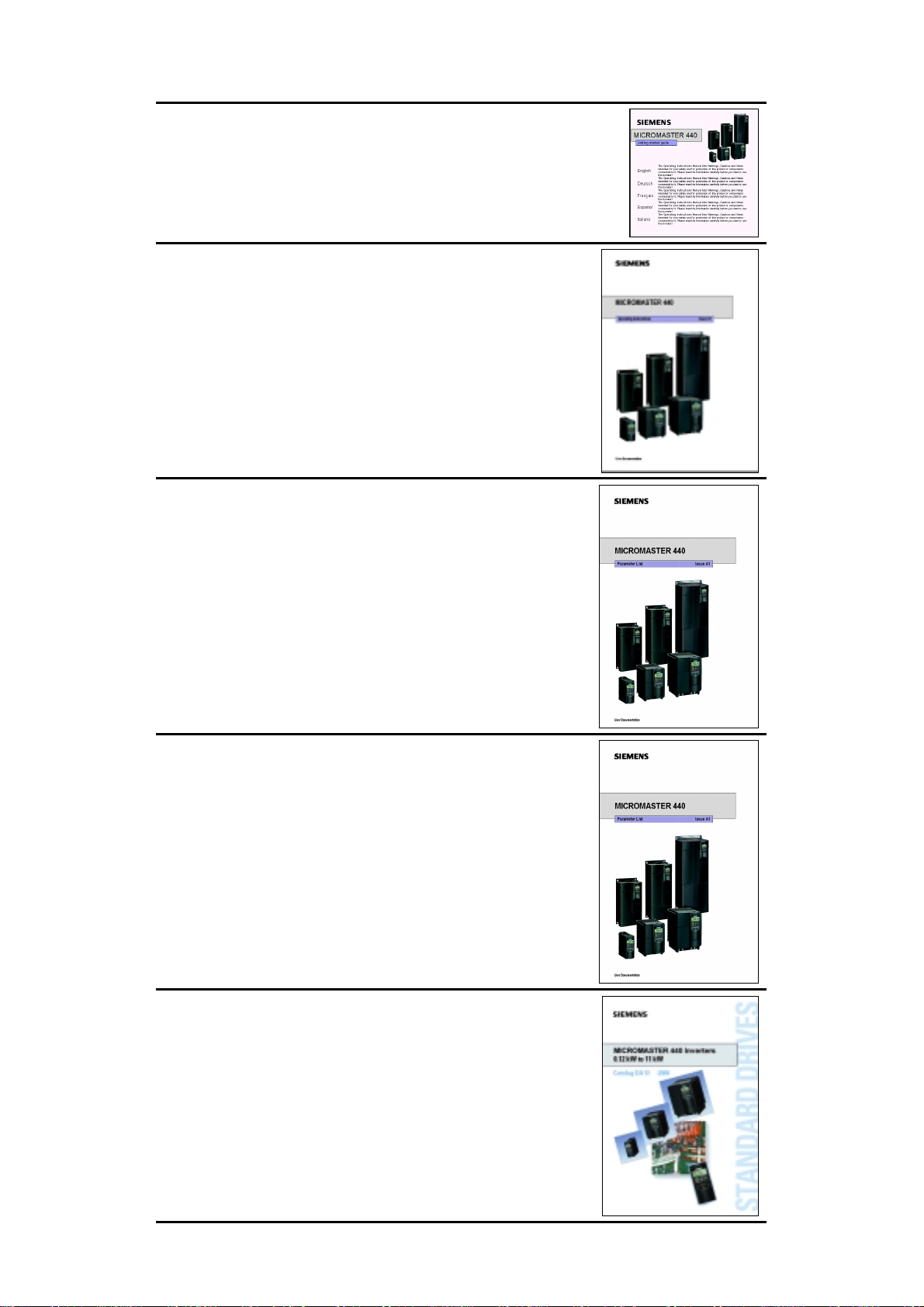
MICROMASTER 440 DOCUMENTATION
Getting Started Guide
Is for quick commissioning with SDP and BOP.
Operating Instructions
Gives information about features of the MM440,
Installation, Commissioning, Control modes, System
Parameter structure, Troubleshooting, Specifications
and available options of the MM440.
Parameter List
The Parameter List contains the description of all
Parameters structured in functional order and a
detailed description. The Parameter list also includes
a series of function plans.
Reference Manual
The Reference Manual gives detailed information
about engineering communication troubleshooting
and maintenance.
Catalogues
In the catalogue you will find all the necessary
information to select an appropriate inverter, as well
as filters, chokes, operator panels and
communication options.
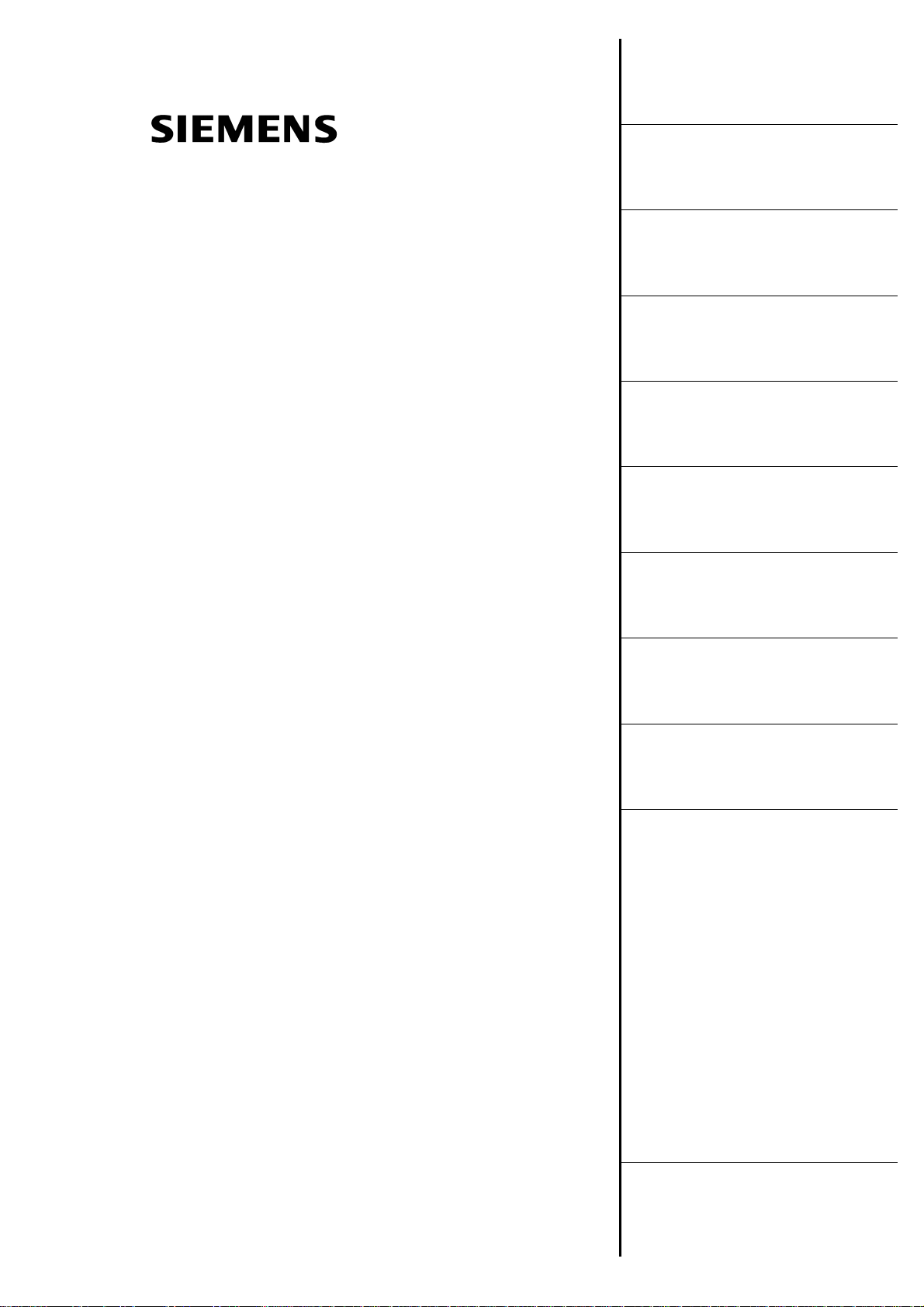
MICROMASTER 440
Operating instructions
User Documentation
Issue A1
Valid for
Converter Type Control Version
MICROMASTER 440 04.2001
Overview
1
Installation
2
Commissioning
3
Using the
MICROMASTER 440
4
System Parameters
5
Troubleshooting
6
MICROMASTER 440
Specifications
7
Available options
8
Electro-Magnetic
Compatibility
9
Appendices
A
B
C
D
E
F
G
H
I
J
K
L
Index
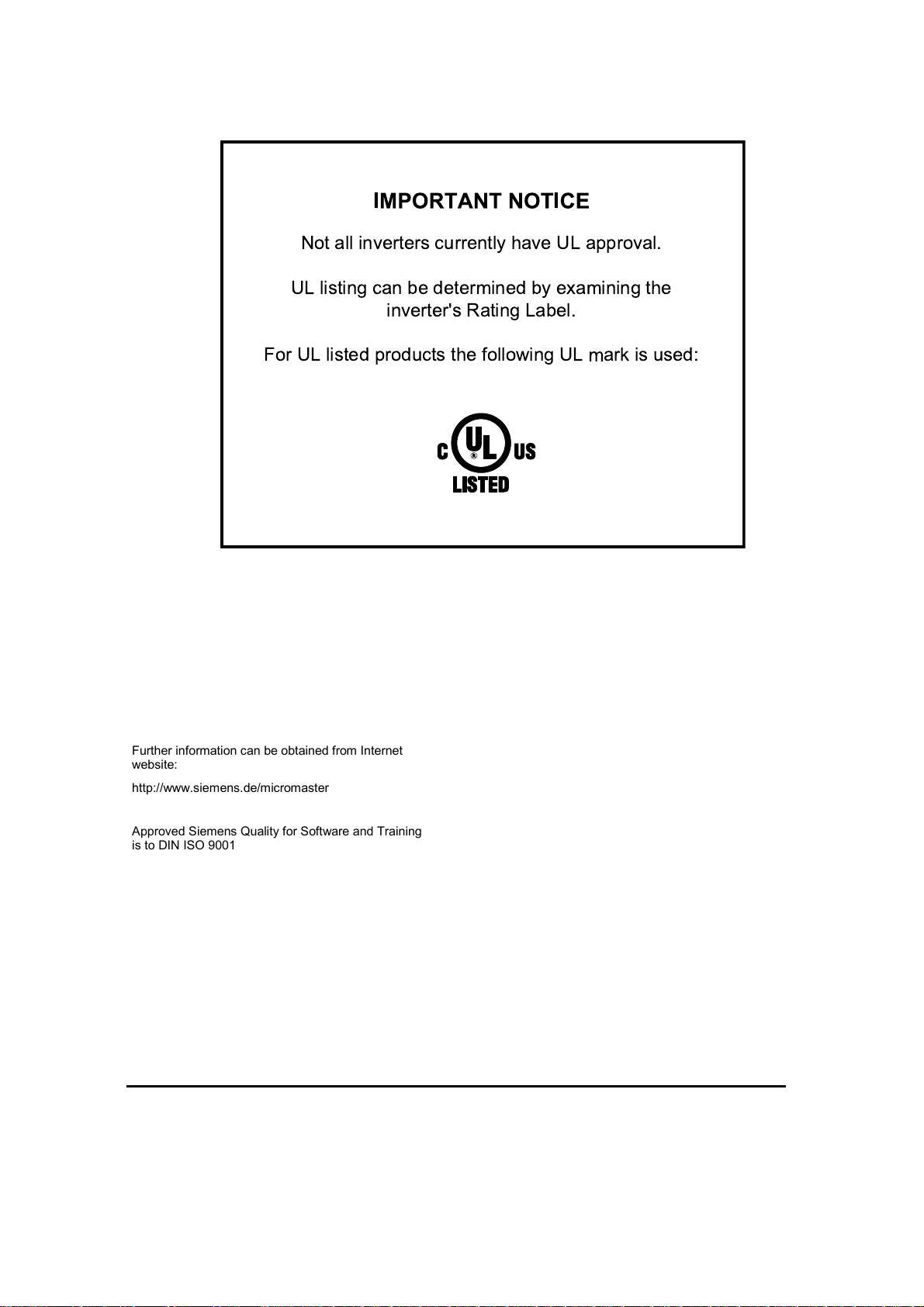
MICROMASTER 440 Operating instructions
4 6SE6400-5CA00-0BP0
IMPORTANT NOTICE
Not all inverters currently have UL approval.
UL listing can be determined by examining the
inverter's Rating Label.
For UL listed products the following UL mark is used:
Further information can be obtained from Internet
website:
http://www.siemens.de/micromaster
Approved Siemens Quality for Software and Training
is to DIN ISO 9001, Reg. No. 2160-01
The reproduction, transmission or use of this document,
or its contents is not permitted unless authorized in
writing. Offenders will be liable for damages. All rights
including rights created by patent grant or registration of a
utility model or design are reserved.
© Siemens AG 2001. All Rights Reserved.
MICROMASTER® is a registered trademark of Siemens
Other functions not described in this document may be
available. However, this fact shall not constitute an
obligation to supply such functions with a new control, or
when servicing.
We have checked that the contents of this document
correspond to the hardware and software described.
There may be discrepancies nevertheless, and no
guarantee can be given that they are completely identical.
The information contained in this document is reviewed
regularly and any necessary changes will be included in
the next edition. We welcome suggestions for
improvement.
Siemens handbooks are printed on chlorine-free paper
that has been produced from managed sustainable
forests. No solvents have been used in the printing or
binding process.
Document subject to change without prior notice.
Order number: 6SE6400-5CA00-0BP0 Siemens-Aktiengesellschaft
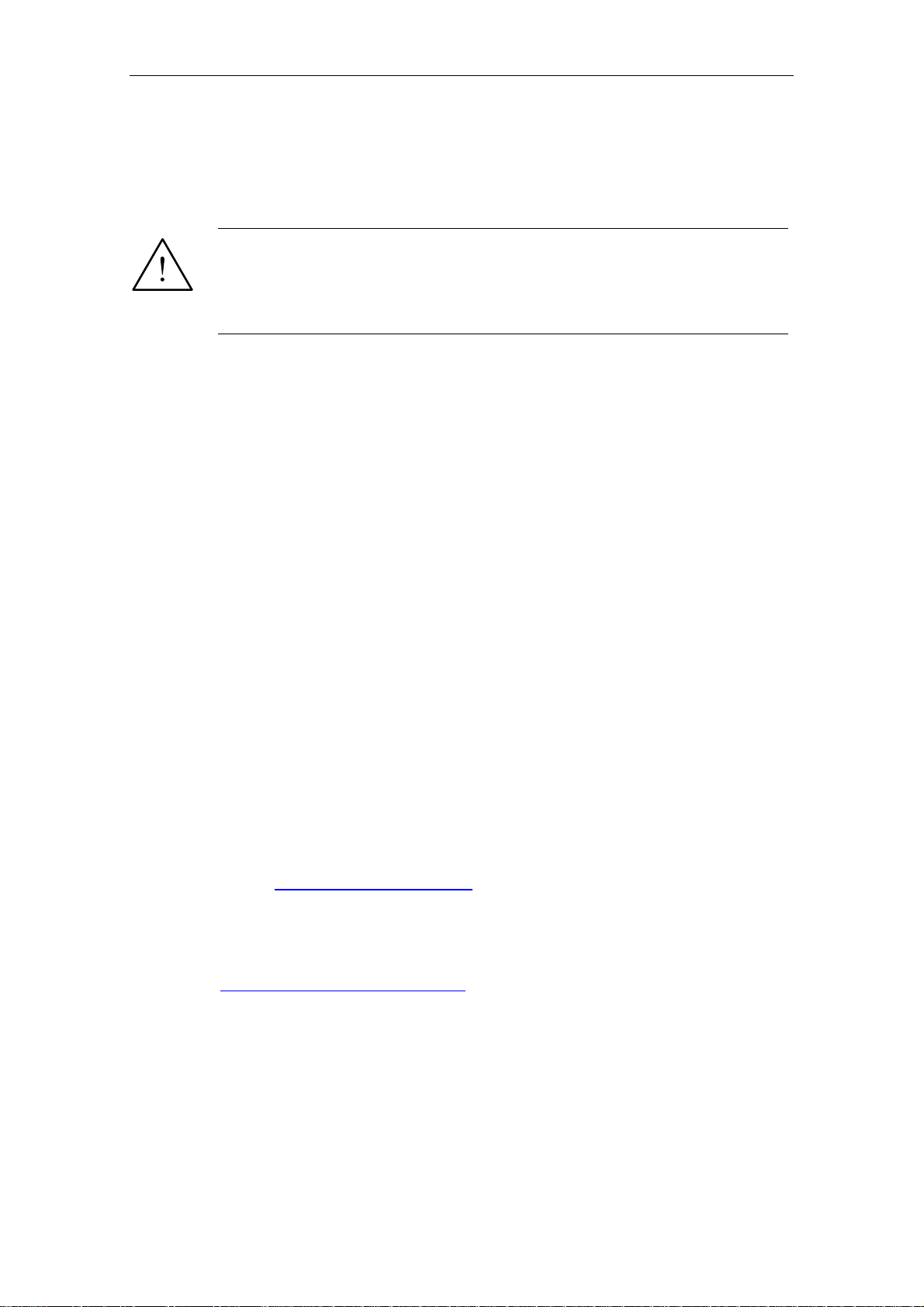
International English Foreword
MICROMASTER 440 Operating instructions
6SE6400-5CA00-0BP0
5
Foreword
User Documentation
Warning
Before installing and commissioning the inverter, you must read all safety
instructions and warnings carefully including all the warning labels attached to the
equipment. Make sure that the warning labels are kept in a legible condition and
replace missing or damaged labels.
MICROMASTER documentation is structured within three distinct levels:
Getting Started Guide
The Getting Started Guide is designed to give the user quick access to all the
basic information required to install and set up your MICROMASTER 440 for
operation.
Operating Instructions
The Operating Instructions provide detailed information for installation and
operation of your MICROMASTER 440. The Operating Instructions also
provide detailed descriptions of the parameters available for customizing the
functions of the MICROMASTER 440.
Reference Manual
The Reference Manual contains in-depth information on all technical issues
relating to the MICROMASTER 440 Inverter.
Parameter List
The Parameter List contains a complete detailed listing of all MICROMASTER
440 parameters.
Information is also available from:
Technical Support Nuremberg
Tel: +49 (0) 180 5050 222
Fax: +49 (0) 180 5050 223
Email: techsupport@ad.siemens.de
Monday to Friday: 7:00 am to 5:00 pm (local time)
Internet Home Address
Customers can access technical and general information at:
http://www.siemens.de/micromaster
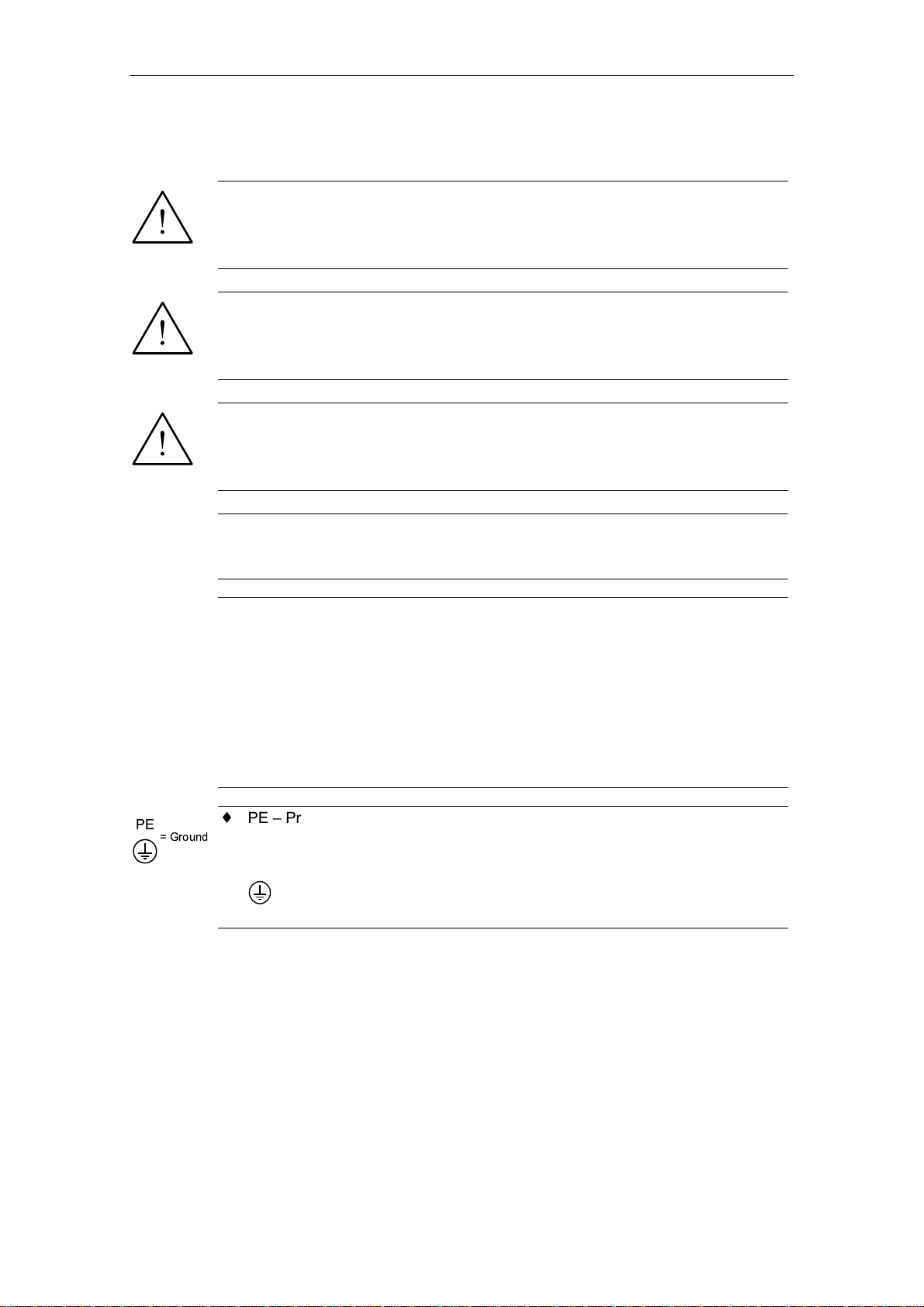
Foreword International English
MICROMASTER 440 Operating instructions
6 6SE6400-5CA00-0BP0
Definitions and Warnings
Danger
For the purpose of this documentation and the product warning labels, "Danger"
indicates that death, severe personal injury or substantial damage to property will
result if proper precautions are not taken.
Warning
For the purpose of this documentation and the product warning labels, "Warning"
indicates that death, severe personal injury or substantial damage to property can
result if proper precautions are not taken.
Caution
For the purpose of this documentation and the product warning labels, "Caution"
indicates that minor personal injury or material damage can result if proper
precautions are not taken.
Note
For the purpose of this documentation, "Note" indicates important information
relating to the product or highlights part of the documentation for special attention.
Qualified personnel
For the purpose of this Instruction Manual and product labels, a "Qualified person"
is someone who is familiar with the installation, mounting, start-up and operation
of the equipment and the hazards involved.
He or she must have the following qualifications:
1. Trained and authorized to energize, de-energize, clear, ground and tag
circuits and equipment in accordance with established safety procedures.
2. Trained in the proper care and use of protective equipment in accordance with
established safety procedures.
3. Trained in rendering first aid.
PE
= Ground
♦ PE – Protective Earth uses circuit protective conductors sized for short circuits
where the voltage will not rise in excess of 50 Volts. This connection is
normally used to ground the inverter.
♦
- Is the ground connection where the reference voltage can be the same
as the Earth voltage. This connection is normally used to ground the motor.
Use for intended purpose only
The equipment may be used only for the application stated in the manual and only
in conjunction with devices and components recommended and authorized by
Siemens.
Contact address
Should any questions or problems arise while reading this manual, please contact
the Siemens office concerned using the form provided at the back this manual.
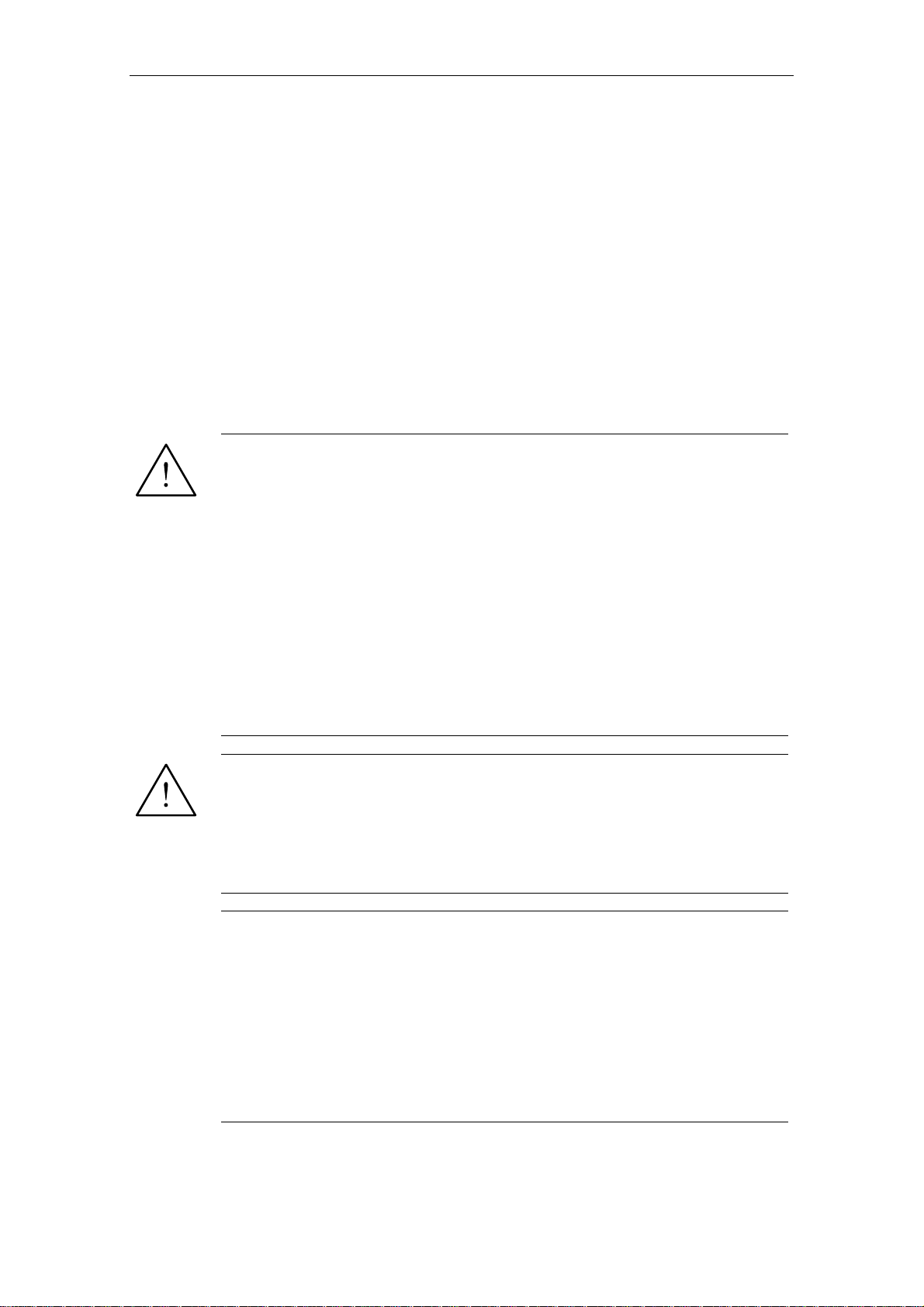
International English Foreword
MICROMASTER 440 Operating instructions
6SE6400-5CA00-0BP0
7
Safety Instructions
The following Warnings, Cautions and Notes are provided for your safety and as a
means of preventing damage to the product or components in the machines
connected. This section lists Warnings, Cautions and Notes, which apply generally
when handling MICROMASTER 440 Inverters, classified as General, Transport &
Storage, Commissioning, Operation, Repair and Dismantling & Disposal.
Specific Warnings, Cautions and Notes that apply to particular activities are
listed at the beginning of the relevant chapters and are repeated or supplemented
at critical points throughout these sections.
Please read the information carefully, since it is provided for your personal
safety and will also help prolong the service life of your MICROMASTER 440
Inverter and the equipment you connect to it.
General
Warnings
♦ This equipment contains dangerous voltages and controls potentially
dangerous rotating mechanical parts. Non-compliance with Warnings or
failure to follow the instructions contained in this manual can result in loss of
life, severe personal injury or serious damage to property.
♦ Only suitable qualified personnel should work on this equipment, and only
after becoming familiar with all safety notices, installation, operation and
maintenance procedures contained in this manual. The successful and safe
operation of this equipment is dependent upon its proper handling,
installation, operation and maintenance.
♦ Risk of electric shock. The DC link capacitors remain charged for five minutes
after power has been removed. It is not permissible to open the
equipment until 5 minutes after the power has been removed.
♦ HP ratings are based on the Siemens 1LA motors and are given for
guidance only; they do not necessarily comply with UL or NEMA HP
ratings.
Caution
♦ Children and the general public must be prevented from accessing or
approaching the equipment!
♦ This equipment may only be used for the purpose specified by the
manufacturer. Unauthorized modifications and the use of spare parts and
accessories that are not sold or recommended by the manufacturer of the
equipment can cause fires, electric shocks and injuries.
Notes
♦ Keep these operating instructions within easy reach of the equipment and
make them available to all users
♦ Whenever measuring or testing has to be performed on live equipment, the
regulations of Safety Code VBG 4.0 must be observed, in particular §8
“Permissible Deviations when Working on Live Parts”. Suitable electronic
tools should be used.
♦ Before installing and commissioning, please read these safety instructions
and warnings carefully and all the warning labels attached to the equipment.
Make sure that the warning labels are kept in a legible condition and replace
missing or damaged labels
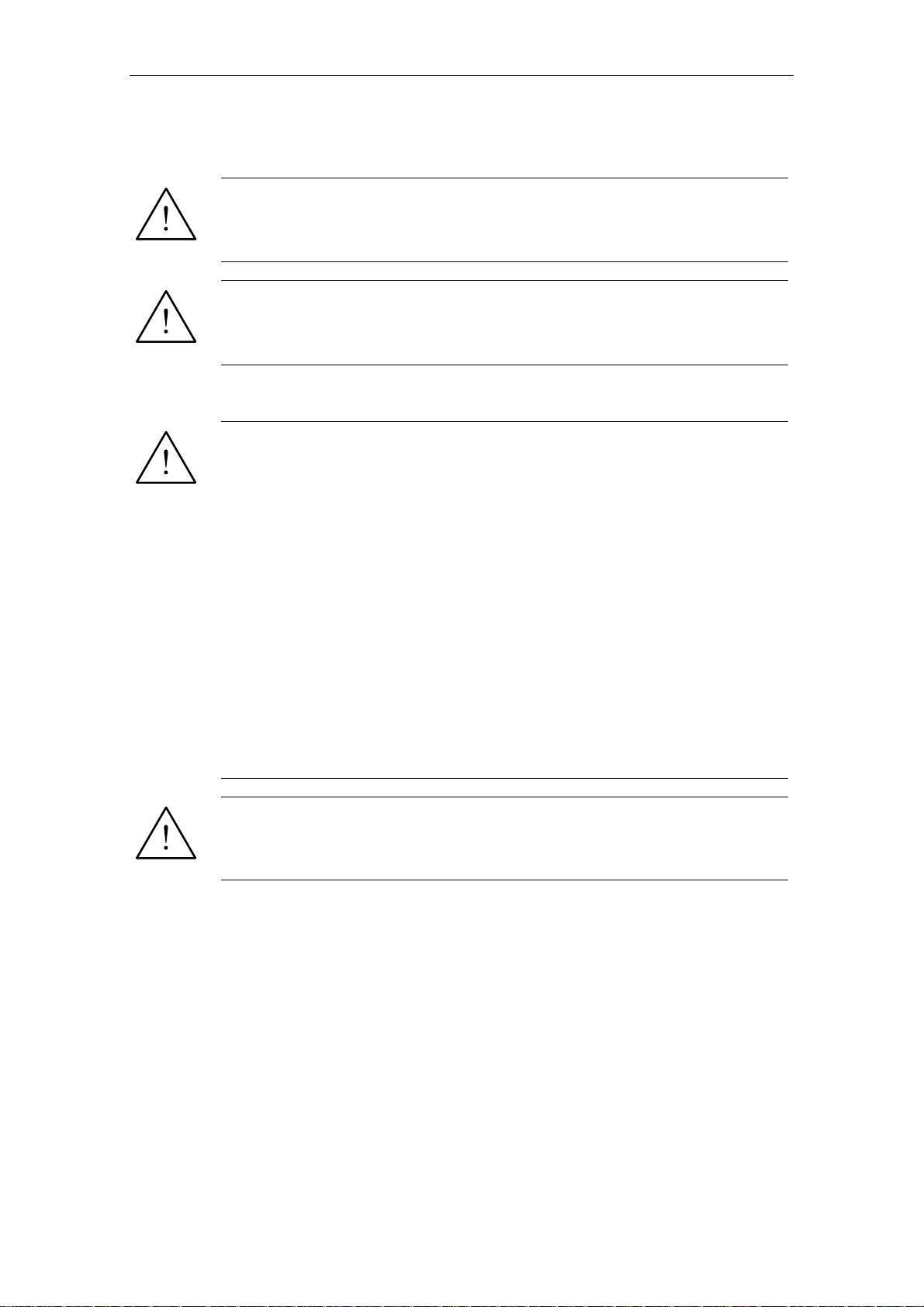
Foreword International English
MICROMASTER 440 Operating instructions
8 6SE6400-5CA00-0BP0
Transport & Storage
Warning
♦ Correct transport, storage, erection and mounting, as well as careful
operation and maintenance are essential for proper and safe operation of the
equipment.
Caution
♦ Protect the inverter against physical shocks and vibration during transport and
storage. Also be sure to protect it against water (rainfall) and excessive
temperatures (see table on page 78).
Commissioning
Warnings
♦ Work on the device/system by unqualified personnel or failure to comply with
warnings can result in severe personal injury or serious damage to material.
Only suitably qualified personnel trained in the setup, installation,
commissioning and operation of the product should carry out work on the
device/system.
♦ Only permanently-wired input power connections are allowed. This equipment
must be grounded (IEC 536 Class 1, NEC and other applicable standards).
♦ If a Residual Current-operated protective Device (RCD) is to be used, it must
be an RCD type B.
♦ Machines with a three-phase power supply, fitted with EMC filters, must not
be connected to a supply via an ELCB (Earth Leakage Circuit-Breaker - see
DIN VDE 0160, section 5.5.2 and EN50178 section 5.2.11.1).
♦ The following terminals can carry dangerous voltages even if the inverter is
inoperative:
- the power supply terminals L/L1, N/L2, L3.
- the motor terminals U, V, W, DC+/B+, DC-, B- and DC/R+
♦ This equipment must not be used as an ‘emergency stop mechanism’ (see
EN 60204, 9.2.5.4)
Caution
The connection of power, motor and control cables to the inverter must be carried
out as shown in Figure 2-4 on page 30, to prevent inductive and capacitive
interference from affecting the correct functioning of the inverter.
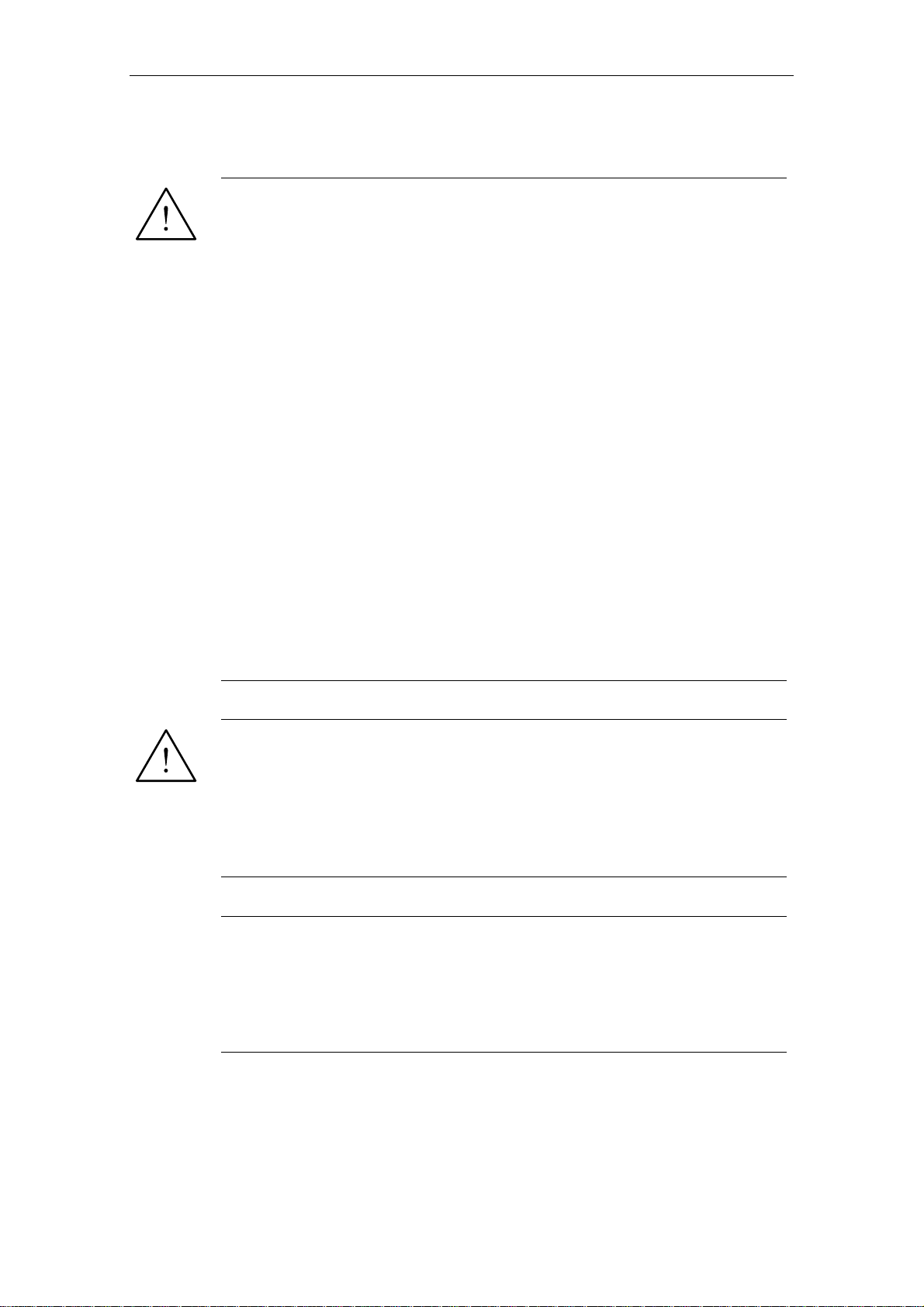
International English Foreword
MICROMASTER 440 Operating instructions
6SE6400-5CA00-0BP0
9
Operation
Warnings
♦ MICROMASTERS operate at high voltages.
♦ When operating electrical devices, it is impossible to avoid applying
hazardous voltages to certain parts of the equipment.
♦ Emergency Stop facilities according to EN 60204 IEC 204 (VDE 0113) must
remain operative in all operating modes of the control equipment. Any
disengagement of the Emergency Stop facility must not lead to uncontrolled
or undefined restart.
♦ Wherever faults occurring in the control equipment can lead to substantial
material damage or even grievous bodily injury (i.e. potentially dangerous
faults), additional external precautions must be taken or facilities provided to
ensure or enforce safe operation, even when a fault occurs (e.g. independent
limit switches, mechanical interlocks, etc.).
♦ Certain parameter settings may cause the inverter to restart automatically
after an input power failure.
♦ Motor parameters must be accurately configured for motor overload
protection to operate correctly.
♦ This equipment is capable of providing internal motor overload protection in
accordance with UL508C section 42. Refer to P0610 (level 3) and P0335, I
2
t
is ON by default. Motor overload protection can also be provided using an
external PTC (disabled by default P0601).
♦ This equipment is suitable for use in a circuit capable of delivering not more
than 10,000 symmetrical amperes (rms), for a maximum voltage of
230V/460V/575V when protected by a H or K type fuse (see Tables starting
on page 77).
♦ This equipment must not be used as an ‘emergency stop mechanism’ (see
EN 60204, 9.2.5.4)
Repair
Warnings
♦ Repairs on equipment may only be carried out by Sieme n s Serv ic e, by
repair centers authorized by Siemens or by qualified personnel who are
thoroughly acquainted with all the warnings and operating procedures
contained in this manual.
♦ Any defective parts or components must be replaced using parts contained in
the relevant spare parts list.
♦ Disconnect the power supply before opening the equipment for access
Dismantling & Disposal
Notes
♦ The inverter’s packaging is re-usable. Retain the packaging for future use or
return it to the manufacturer.
♦ Easy-to-release screw and snap connectors allow you to break the unit down
into its component parts. You can then re-cycle these component parts,
dispose of them in accordance with local requirements or return them to
the manufacturer.
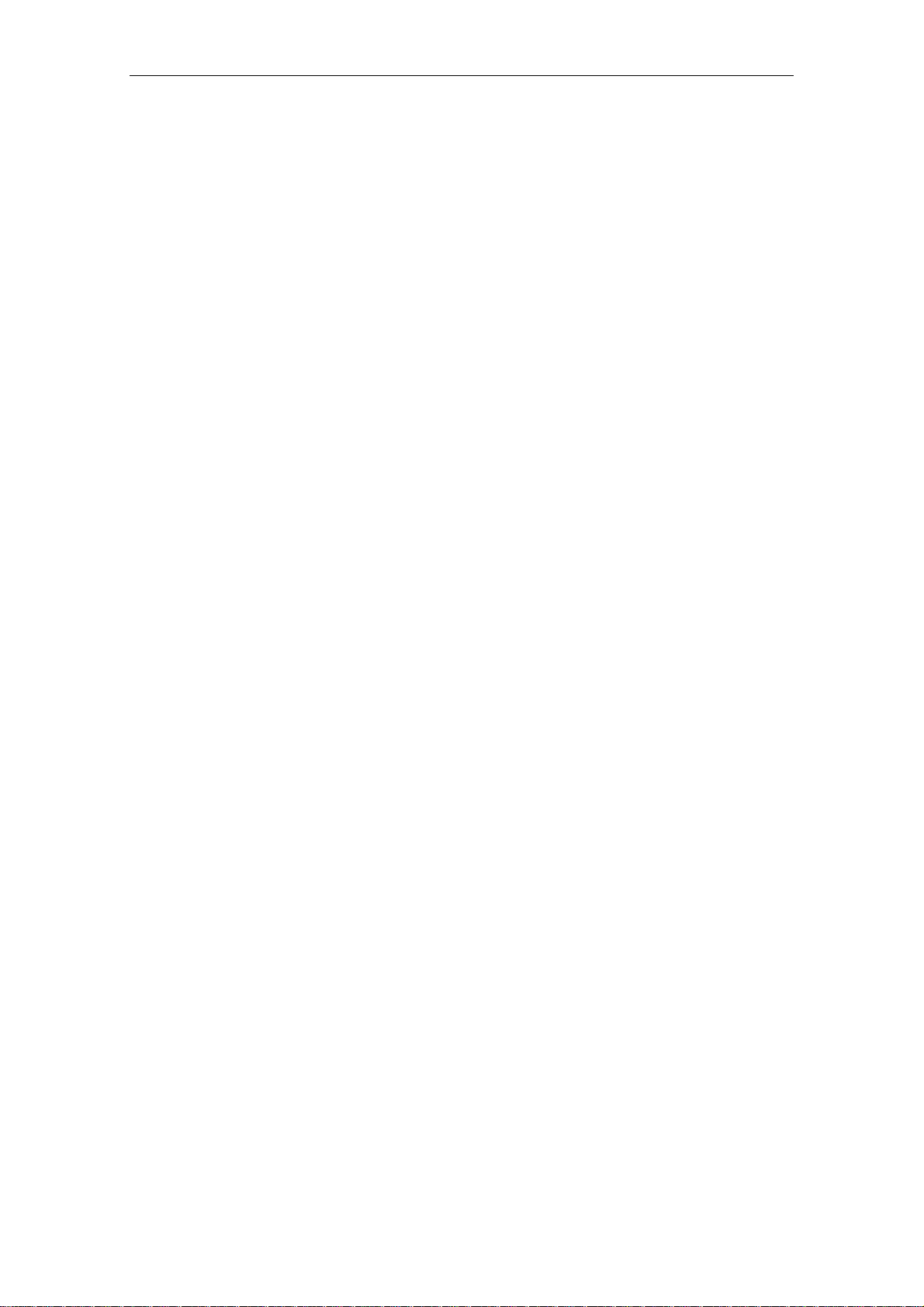
Foreword International English
MICROMASTER 440 Operating instructions
10 6SE6400-5CA00-0BP0
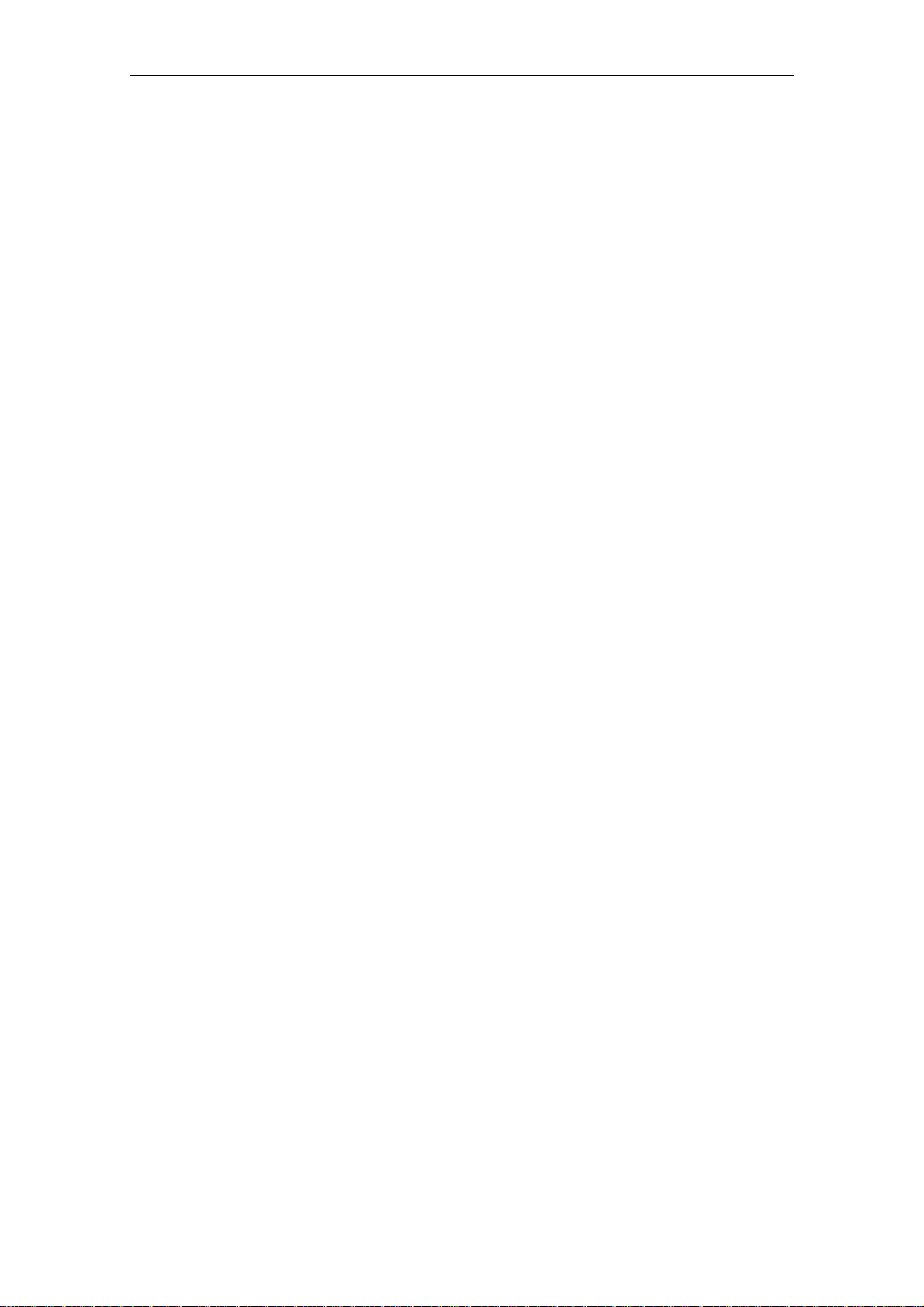
International English Table of Contents
MICROMASTER 440 Operating instructions
6SE6400-5CA00-0BP0
11
Table of Contents
1 Overview ................................................................................................................ 15
1.1 The MICROMASTER 440 .......................................................................................16
1.2 Features ..................................................................................................................16
2 Installation .............................................................................................................19
2.1 General.................................................................................................................... 21
2.2 Ambient operating conditions.................................................................................. 22
2.3 Mechanical Installation ............................................................................................23
2.4 Electrical Installation................................................................................................ 25
3 Commissioning .....................................................................................................31
3.1 Block Diagram .........................................................................................................33
3.2 Commission Modes................................................................................................. 34
3.3 General operation.................................................................................................... 43
4 Using the MICROMASTER 440.............................................................................45
4.1 Frequency Setpoint (P1000) ................................................................................... 46
4.2 Command Sources (P0700).................................................................................... 47
4.3 OFF and braking Functions..................................................................................... 47
4.4 Control Modes (P1300) ...........................................................................................49
4.5 Faults and warnings ................................................................................................50
5 System Parameters...............................................................................................51
5.1 Introduction to MICROMASTER System Parameters............................................. 52
5.2 Parameter Overview................................................................................................ 53
5.3 Parameter List (short form) ..................................................................................... 54
6 Troubleshooting....................................................................................................67
6.1 Troubleshooting with the Status Display Panel....................................................... 68
6.2 Troubleshooting with the Basic Operator Panel...................................................... 69
6.3 Fault messages .......................................................................................................70
7 MICROMASTER 440 Specifications.....................................................................77
8 Available options...................................................................................................89
8.1 Available options ..................................................................................................... 90
9 Electro-Magnetic Compatibility (EMC)................................................................91
9.1 Electro-Magnetic Compatibility (EMC) ....................................................................92
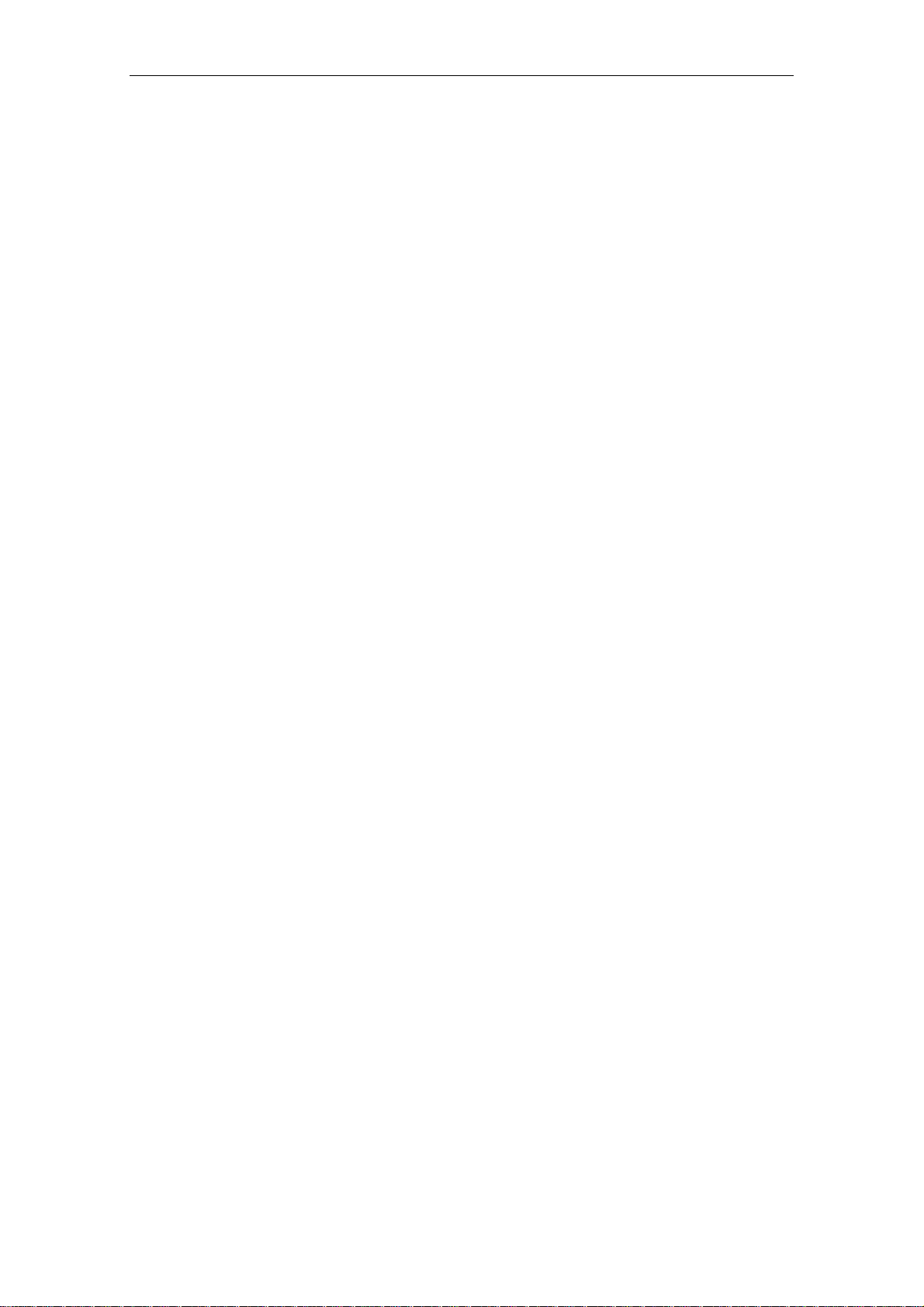
Table of Contents International English
MICROMASTER 440 Operating instructions
12 6SE6400-5CA00-0BP0
A - Changing the Operator Panel .............................................................................................97
B - Removing Covers Frame Size A.........................................................................................98
C - Removing the I/O Board......................................................................................................99
D - Removing Covers Frame Sizes B and C..........................................................................100
E - Removal of Covers Frame Size D and E..........................................................................101
F - Removal of Covers Frame Size F......................................................................................102
G - Removing ‘Y’ Cap Link Frame Size A..............................................................................103
H - Removing ‘Y’ Cap Link Frame Sizes B and C.................................................................104
I - Removing ‘Y’ Cap Link Frame Sizes D and E...................................................................105
J - Removing ‘Y’ Cap Link Frame Sizes F ............................................................................. 106
K - Applicable Standards ........................................................................................................107
L - List of Abbreviations..........................................................................................................108
Index ...............................................................................................................................109

International English Table of Contents
MICROMASTER 440 Operating instructions
6SE6400-5CA00-0BP0
13
List of Illustrations
Figure 2-1 Drill pattern for MICROMASTER 440....................................................................................22
Figure 2-2 MICROMASTER 440 Connection Terminals ........................................................................26
Figure 2-3 Motor and Power Connections..............................................................................................27
Figure 2-4 Wiring Guidelines to Minimize the Effects of EMI .................................................................29
Figure 3-1 Inverter block diagram ..........................................................................................................33
Figure 3-2 Panels available for the MICROMASTER 440 Inverter.........................................................34
Figure 3-3 Basic operation with SDP .....................................................................................................36
Figure 3-4 DIP locations on I/O board and the Control Board................................................................36
Figure 3-5 Buttons on the Basic Operator Panel....................................................................................38
Figure 3-6 Changing parameters via the BOP .......................................................................................39
Figure 3-7 Typical Motor Rating Plate Example.....................................................................................41
Figure 5-1 Quick Commissioning Flowchart...........................................................................................51
List of Tables
Table 2-1 Dimensions and Torques of MM440 (all frame sizes)...........................................................23
Table 3-1 Default settings for operation using the Status Display Panel...............................................35
Table 3-2 Default settings for operation using the BOP........................................................................39
Table 6-1 Inverter conditions indicated by the LEDs on the SDP .........................................................68
Table 7-1 MICROMASTER 440 Performance Ratings .........................................................................78
Table 7-2 Wire Sizes & Terminal Torques – Field Wiring Connectors ..................................................79
Table 7-3 MICROMASTER 440 Specifications.....................................................................................79
Table 9-1 Class 1 - General Industrial ..................................................................................................94
Table 9-2 Class 2 - Filtered Industrial ...................................................................................................94
Table 9-3 Class 3 - Filtered for Residential, Commercial and Light Industry ........................................95
Table 9-4 Compliance Table.................................................................................................................96
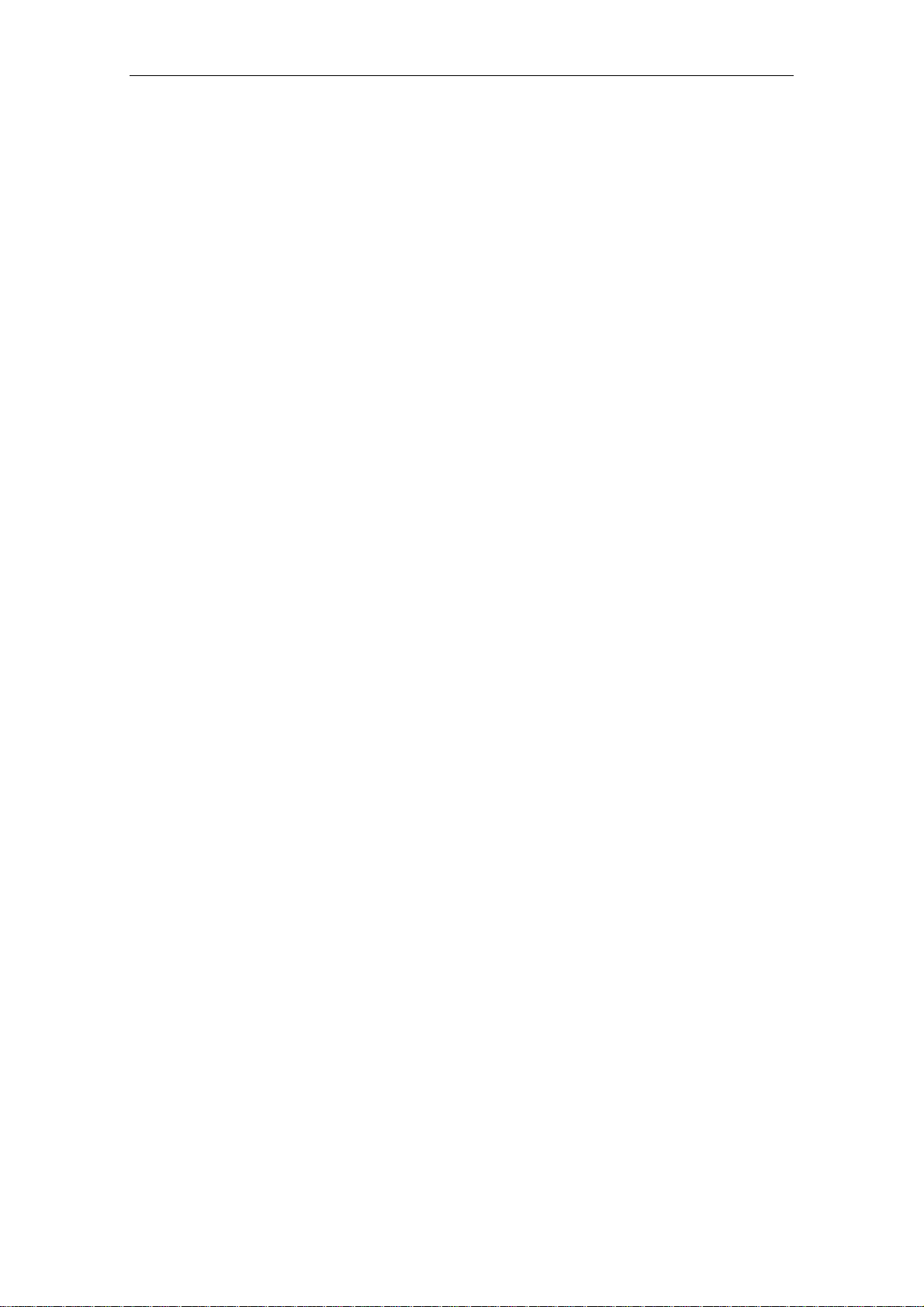
Table of Contents International English
MICROMASTER 440 Operating instructions
14 6SE6400-5CA00-0BP0
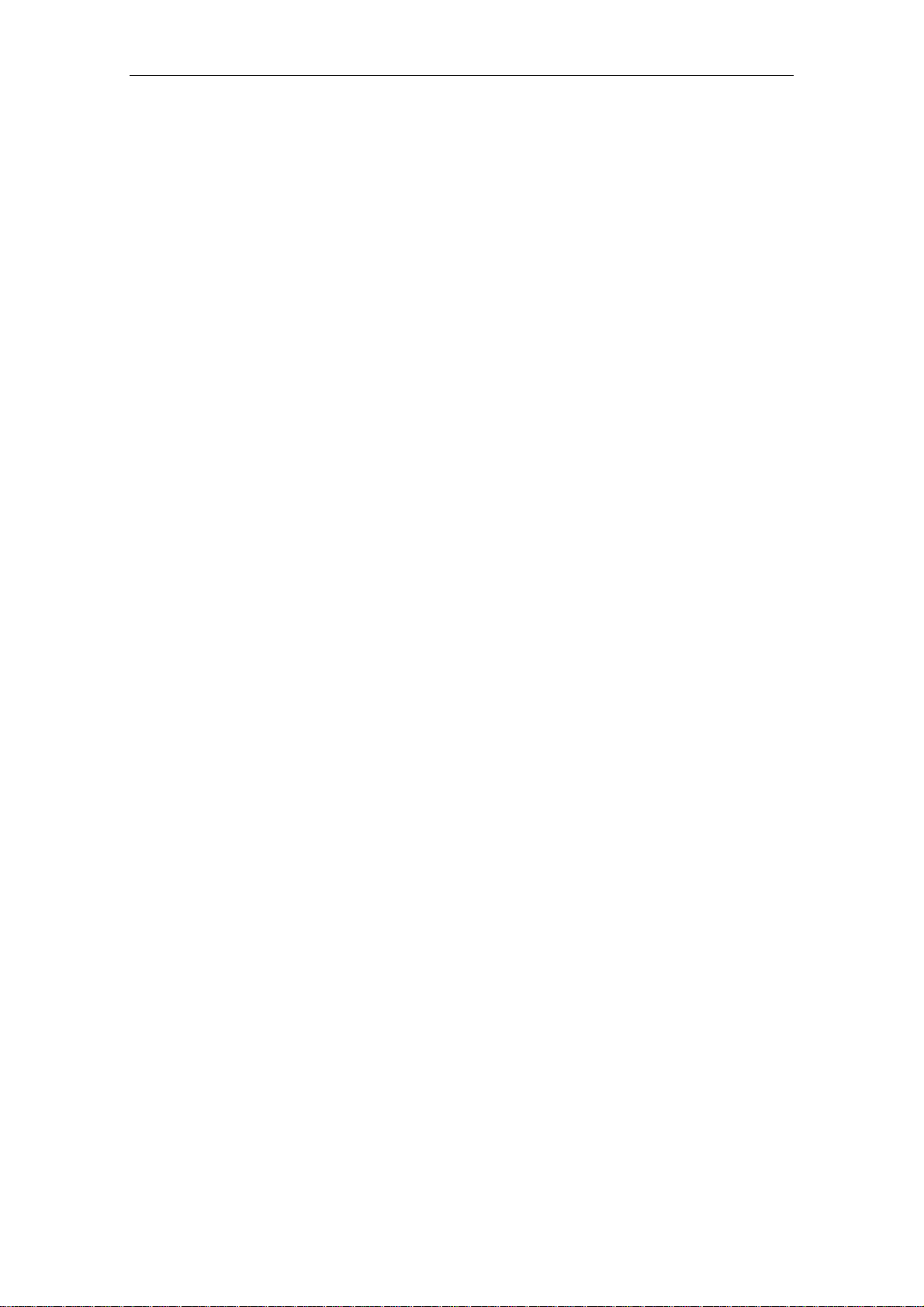
International English 1 Overview
MICROMASTER 440 Operating instructions
6SE6400-5CA00-0BP0
15
1 Overview
This Chapter contains:
A summary of the major features of the MICROMASTER 440 range.
1.1 The MICROMASTER 440 .......................................................................................16
1.2 Features ..................................................................................................................16
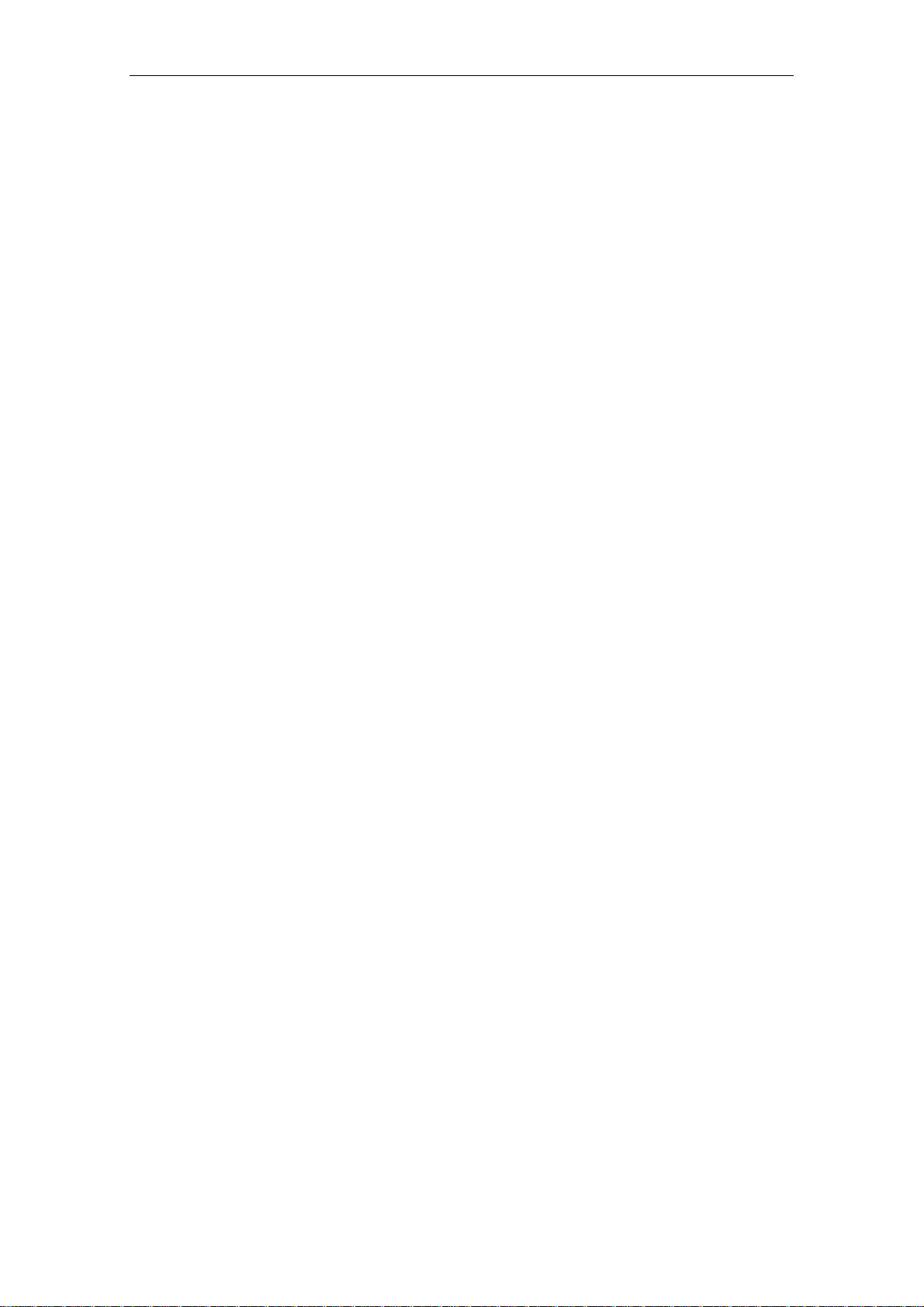
1 Overview International English
MICROMASTER 440 Operating instructions
16 6SE6400-5CA00-0BP0
1.1 The MICROMASTER 440
The MICROMASTER 440s are a range of frequency inverters for controlling the
speed of three phase AC motors. The various models available range from the 120
W single-phase input to the 75 kW three phase input.
The inverters are microprocessor-controlled and use state-of-the-art Insulated Gate
BipoIar Transistor (IGBT) technology. This makes them reliable and versatile. A
special pulse-width modulation method with selectable Pulse frequency permits
quiet motor operation. Comprehensive protective functions provide excellent
inverter and motor protection.
The MICROMASTER 440 with its default factory settings is ideal for a large range
of simple motor control applications. The MICROMASTER 440 can also be used
for more advanced motor control applications via its comprehensive functionality.
The MICROMASTER 440 can be used in both 'stand-alone' applications as well as
being integrated into 'Automation Systems'.
1.2 Features
Main Characteristics
Easy to install, parameterize and commission
Rugged EMC design
Can be operated on IT line supplies
Fast repeatable response time to control signals
Comprehensive range of parameters enabling configuration for a wide range of
applications
Simple cable connection
Output relays
Analog outputs (0 – 20 mA)
6 Isolated and switchable NPN/PNP digital inputs
2 Analog inputs:
♦ AIN1: 0 – 10 V, 0 – 20 mA and -10 to +10 V
♦ AIN2: 0 – 10 V, 0 – 20 mA
The 2 analog inputs can be used as the 7
th
and 8
th
digital inputs
BiCo technology
Modular design for extremely flexible configuration
High switching frequencies for low-noise motor operation
Detailed status information and integrated message functions
External options for PC communications, Basic Operator Panel (BOP),
Advanced Operator Panel (AOP), PROFIBUS communications module
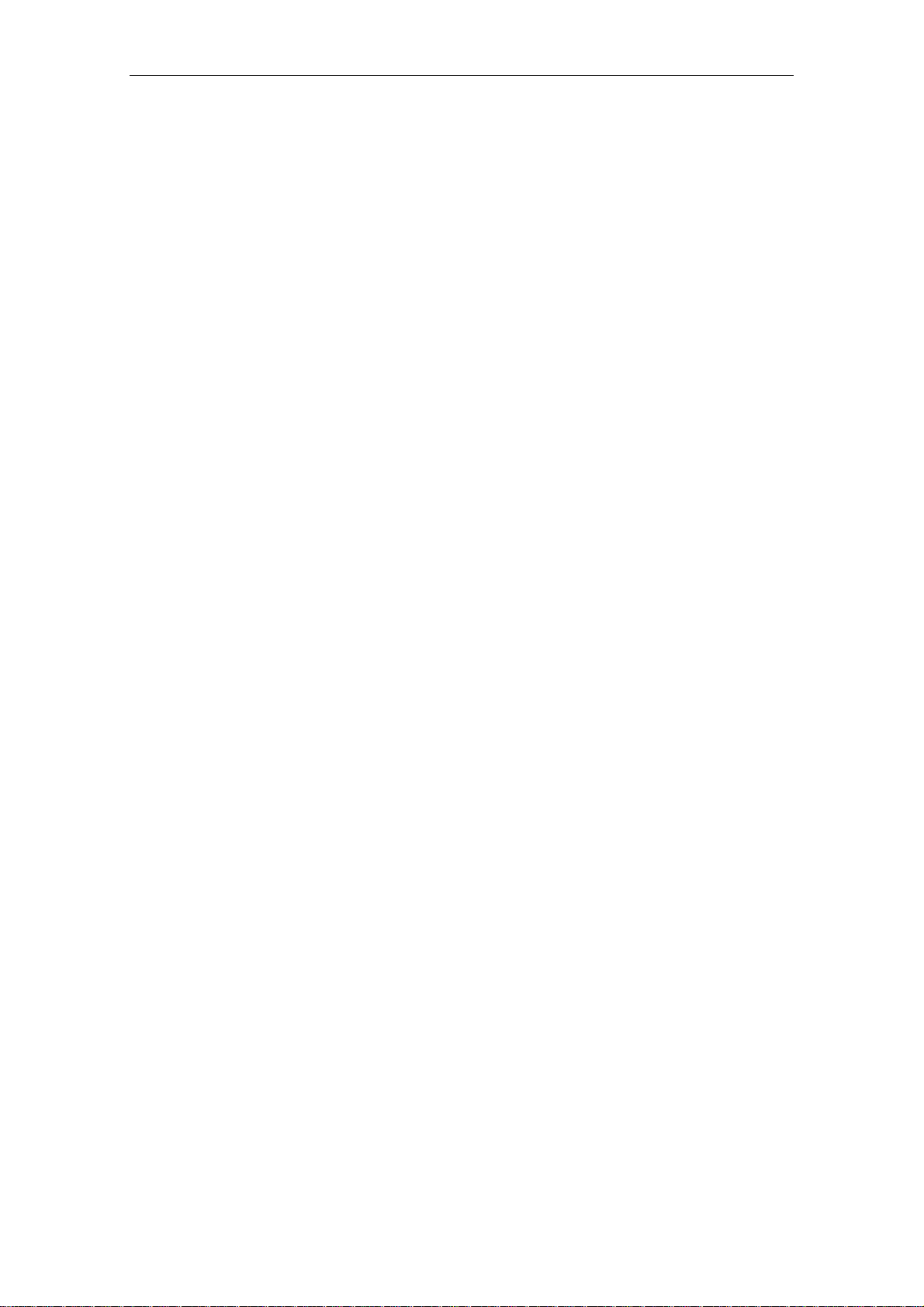
International English 1 Overview
MICROMASTER 440 Operating instructions
6SE6400-5CA00-0BP0
17
Performance Characteristics
Sensorless Vector Control
Flux Current Control (FCC) for improved dynamic response and motor control
Fast Current Limitation (FCL) for trip-free operation
Built-in DC injection brake
Compound braking to improve braking performance
Acceleration/deceleration times with programmable smoothing
Closed-loop control using PID (Proportional, Integral and Differential) control
loop function, with auto-tuning
Built-in braking chopper
Selectable up and down ramps
4-point ramp smoothing
Multi-point V/f characteristic
parameter sets which can be switched, allowing one inverter to control several
alternative processes
Protection characteristics
Overvoltage/undervoltage protection
Overtemperature protection for the inverter
Ground fault protection
Short-circuit protection
I
2
t thermal motor protection
PTC/KTY for motor protection
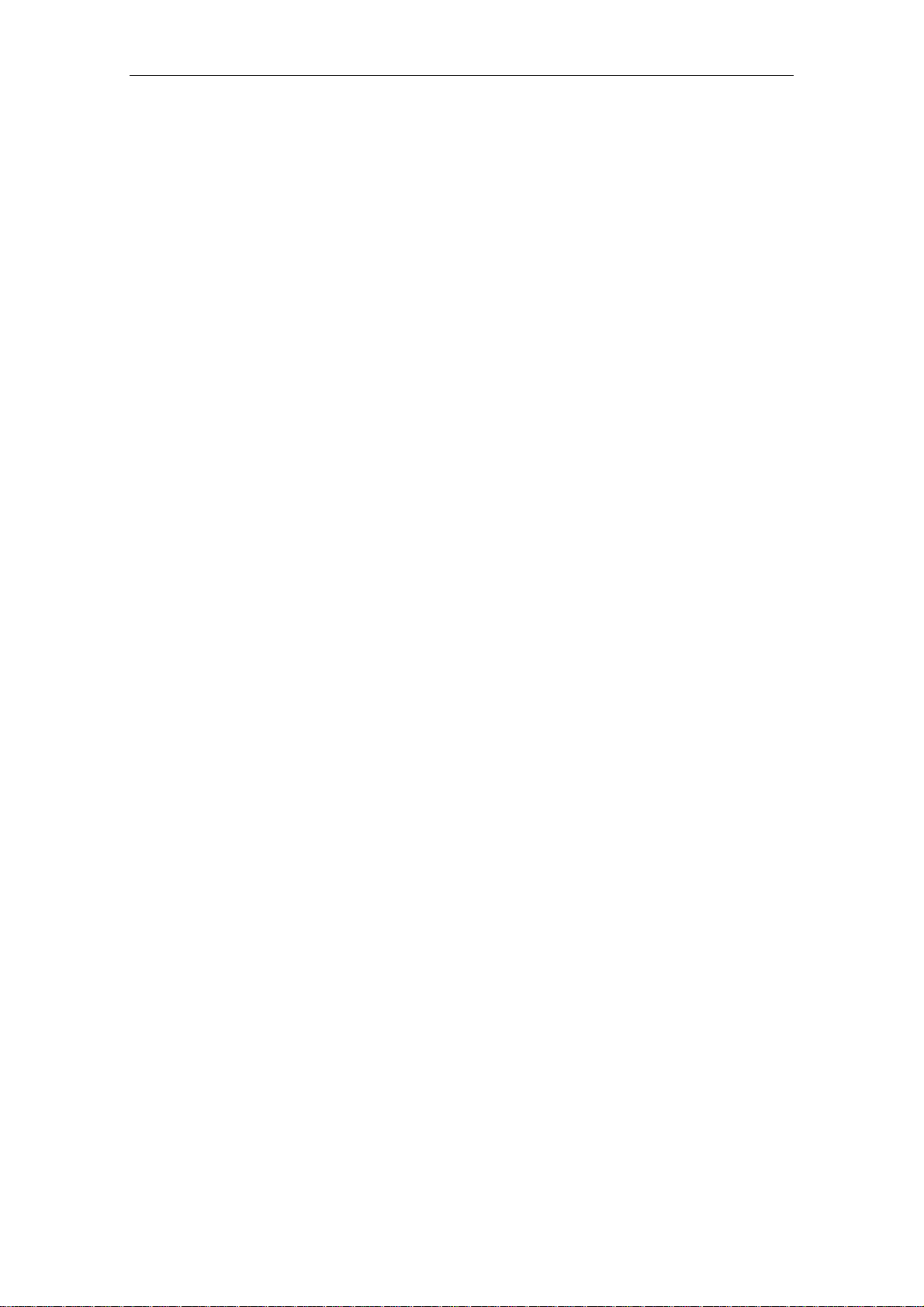
1 Overview International English
MICROMASTER 440 Operating instructions
18 6SE6400-5CA00-0BP0
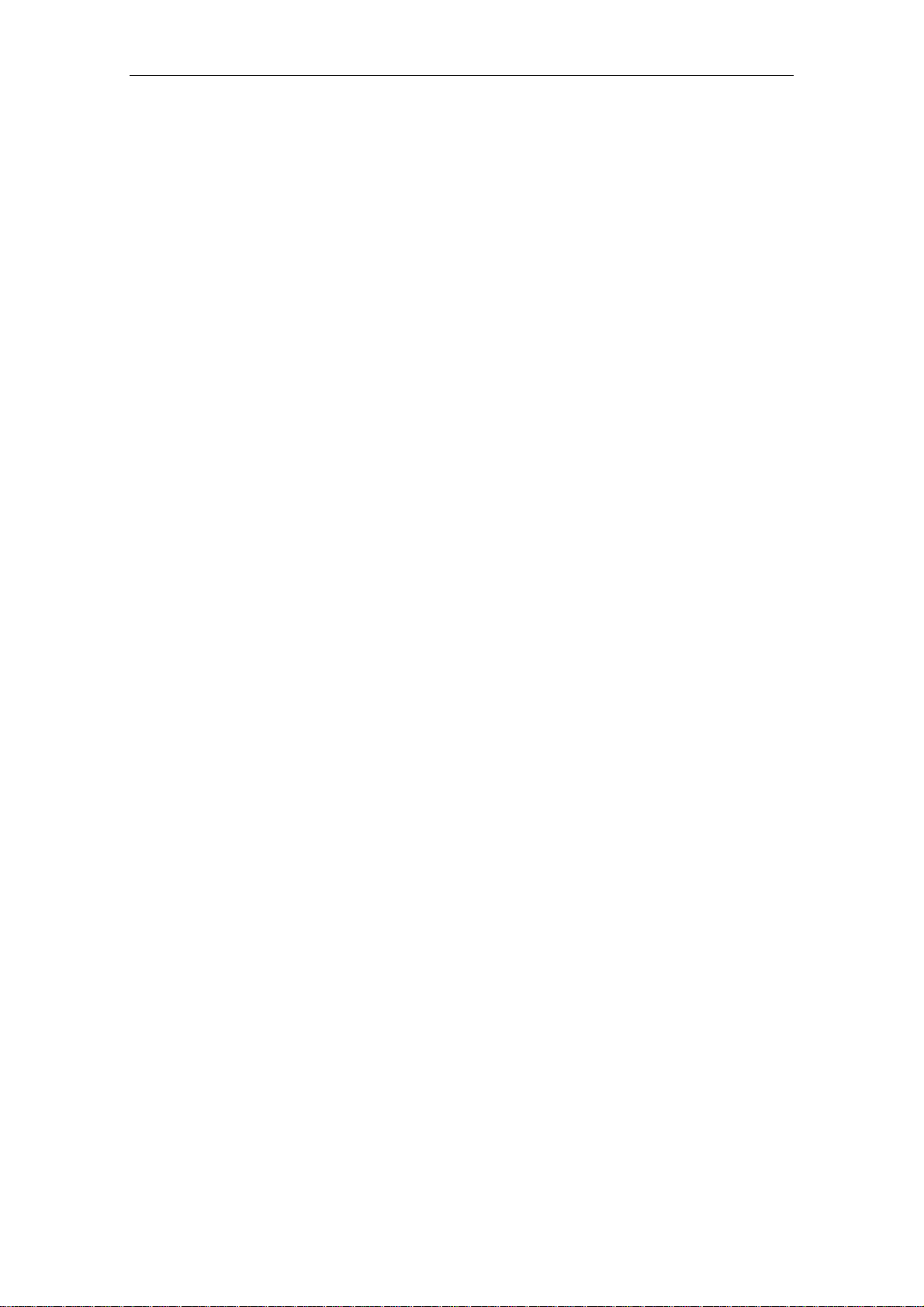
International English 2 Installation
MICROMASTER 440 Operating instructions
6SE6400-5CA00-0BP0
19
2 Installation
This Chapter contains:
General data relating to installation
Dimensions of Inverter
Wiring guidelines to minimize the effects of EMI
Details concerning electrical installation
2.1 General.................................................................................................................... 21
2.2 Ambient operating conditions.................................................................................. 22
2.3 Mechanical Installation ............................................................................................23
2.4 Electrical Installation................................................................................................ 25
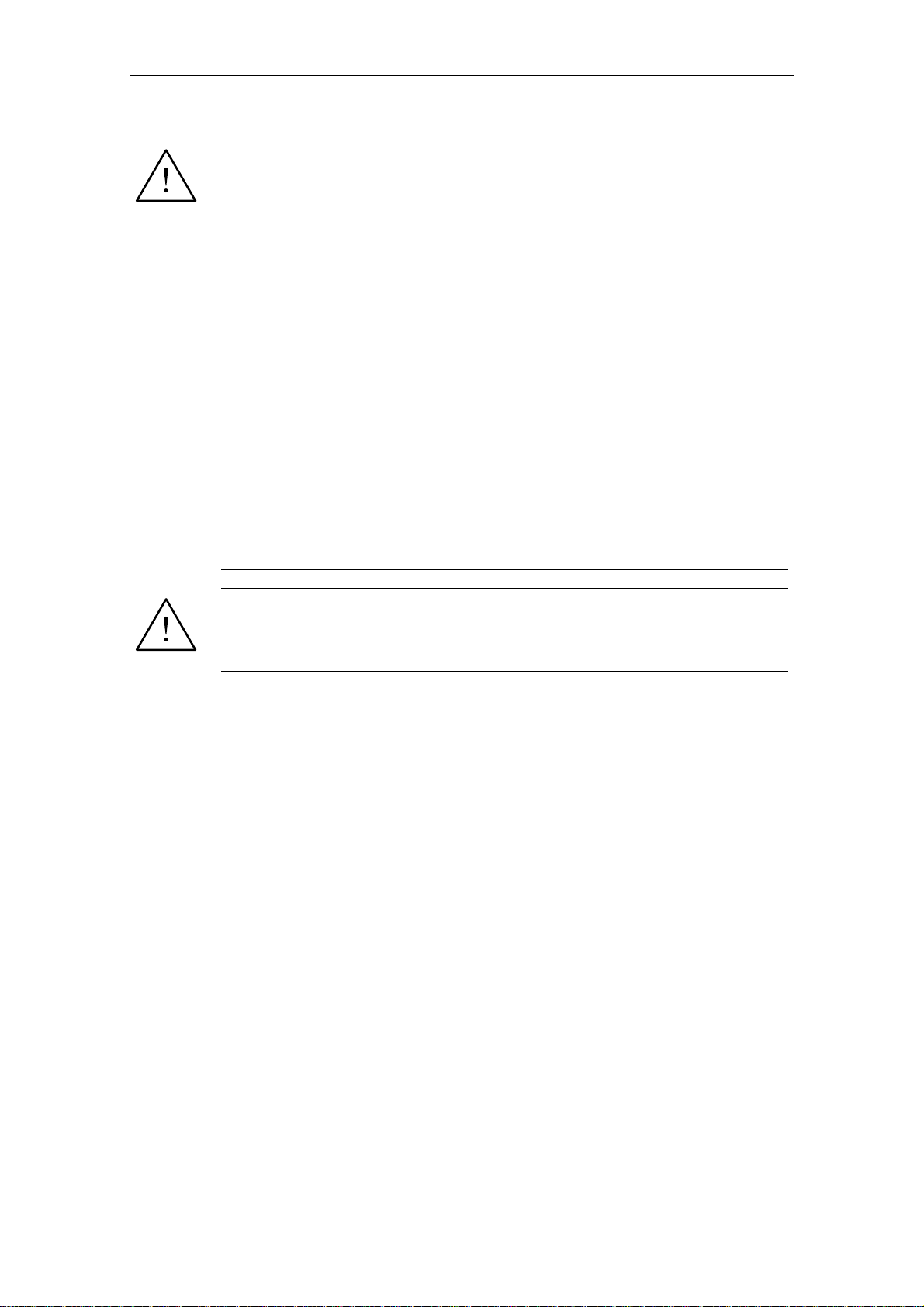
2 Installation International English
MICROMASTER 440 Operating instructions
20 6SE6400-5CA00-0BP0
Warnings
♦ Work on the device/system by unqualified personnel or failure to comply with
warnings can result in severe personal injury or serious damage to material.
Only suitably qualified personnel trained in the setup, installation,
commissioning and operation of the product should carry out work on the
device/system.
♦ Only permanently-wired input power connections are allowed. This equipment
must be grounded (IEC 536 Class 1, NEC and other applicable standards).
♦ If a Residual Current-operated protective Device (RCD) is to be used, it must
be an RCD type B.
♦ Machines with a three-phase power supply, fitted with EMC filters, must not
be connected to a supply via an ELCB (Earth Leakage Circuit-Breaker
EN50178 Section 5.2.11.1).
♦ The following terminals can carry dangerous voltages even if the inverter is
inoperative:
- the power supply terminals L/L1, N/L2, L3.
- the motor terminals U, V, W, DC+/B+, DC-, B- and DC/R+
♦ Always wait 5 minutes to allow the unit to discharge after switching off before
carrying out any installation work.
♦ This equipment must not be used as an ‘emergency stop mechanism’ (see
EN 60204, 9.2.5.4)
♦ The minimum size of the earth-bonding conductor must be equal to or greater
than the cross-section of the power supply cables.
Caution
The connection of power, motor and control cables to the inverter must be carried
out as shown in Figure 2-4 on page 30, to prevent inductive and capacitive
interference from affecting the correct functioning of the inverter.
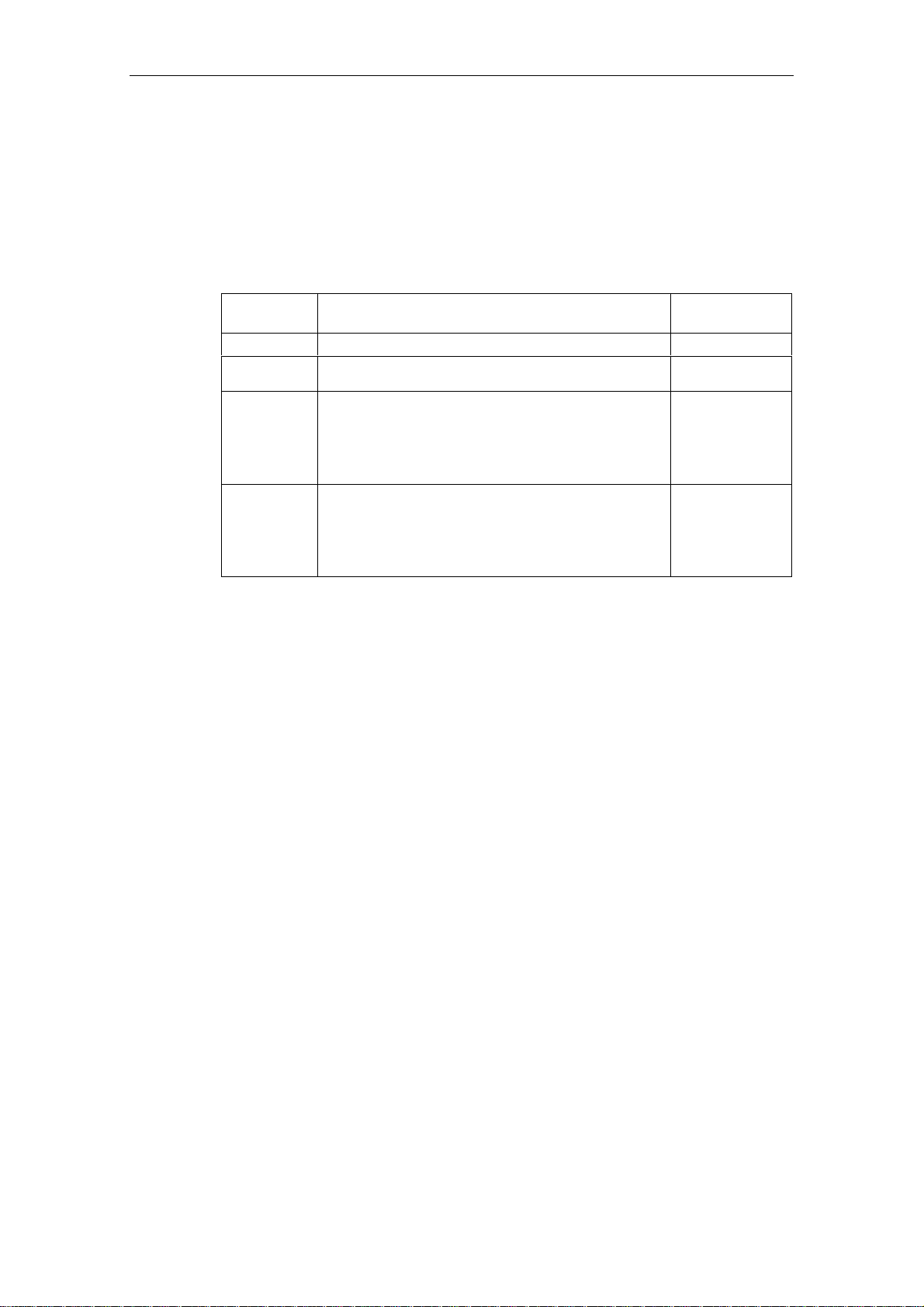
International English 2 Installation
MICROMASTER 440 Operating instructions
6SE6400-5CA00-0BP0
21
2.1 General
Installation after a Period of Storage
Following a prolonged period of storage, you must reform the capacitors in the
inverter. It is important that the time of storage is calculated from the time of
manufacture and not the time of delivery. The requirements are listed below.
Period of
Storage
Required Action
Preparation
Time
1 year or less No reforming required No preparation
1 to 2 years
Apply power to the inverter for one hour before issuing the run
command
1 hour
2 to 3 years
Use a variable AC supply
Apply 25% of input voltage for 30 minutes
Increase volts to 50% for a further 30 minutes
Increase volts to 75% for a further 30 minutes
Increase volts to 100% for a further 30 minutes
Inverter ready for run signal
2 hours
3 years and
over
Use a variable AC supply
Apply 25% of input voltage for 2 hours
Increase volts to 50% for a further 2 hours
Increase volts to 75% for a further 2 hours
Increase volts to 100% for a further 2 hours
Inverter ready for run signal
8 hours
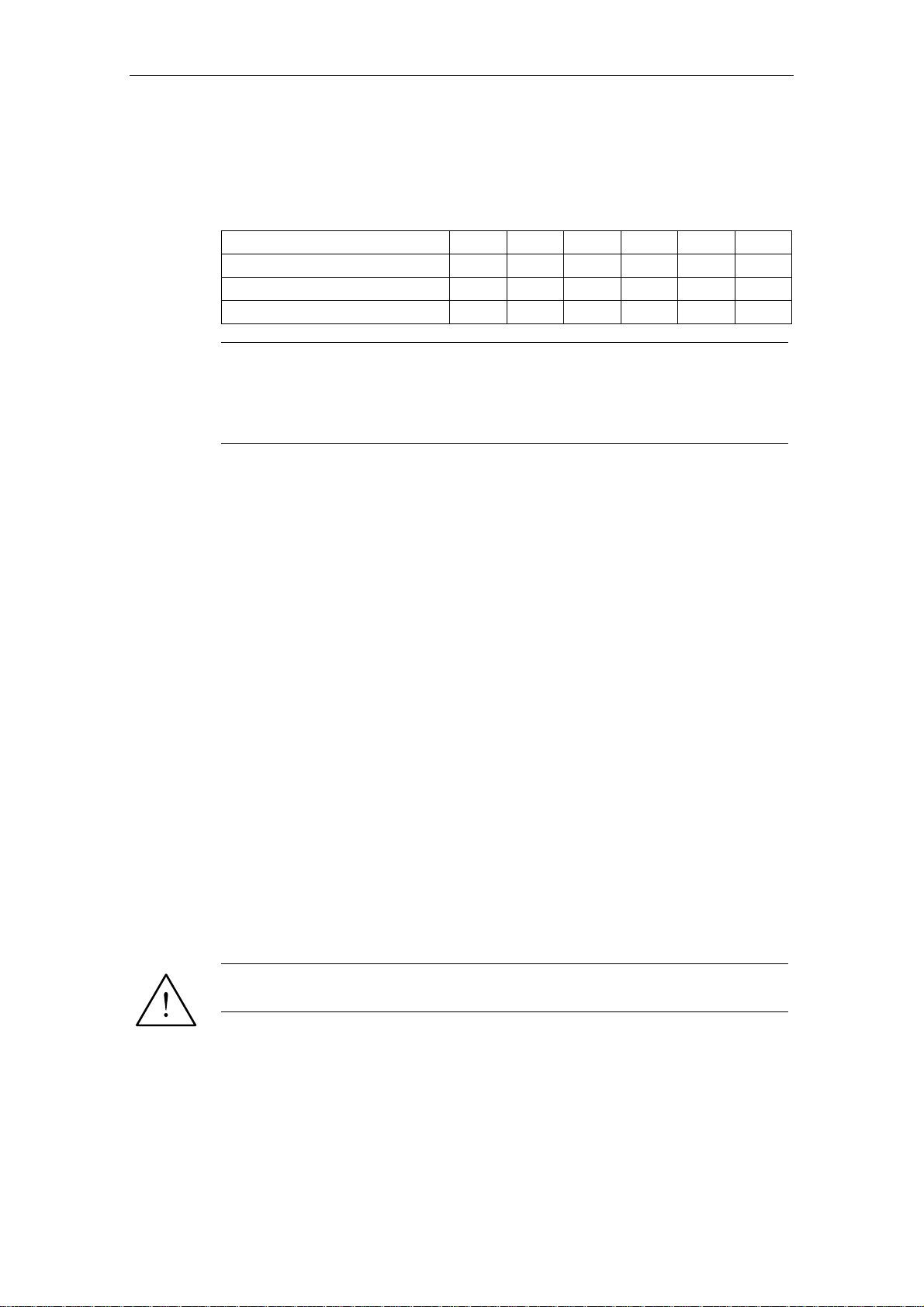
2 Installation International English
MICROMASTER 440 Operating instructions
22 6SE6400-5CA00-0BP0
2.2 Ambient operating conditions
Temperature
Frame Size ABCDEF
Min. [°
°°
° C]
-10 -10 -10 -10 -10 -10
Max. [°
°°
° C]
50 50 50 50 50 50
Max. (Variable Torque) [°
°°
° C]
- - 40404040
Note
The variable torque rating is the capability of the inverter to increase the nominal
power output for use with pump and fan applications.
When variable torque is selected the inverter ceases to have an overload
capacity.
Humidity Range
95% Non-condensing
Altitude
If the inverter is to be installed at an altitude > 1000m, derating will be required.
(Refer to MM440 Reference Manual)
Shock
Do not drop the inverter or expose to sudden shock.
Vibration
Do not install the inverter in an area where it is likely to be exposed to constant
vibration.
Electromagnetic Radiation
Do not install the inverter near sources of electromagnetic radiation.
Atmospheric Pollution
Do not install the inverter in an environment, which contains atmospheric pollutants
such as dust, corrosive gases, etc.
Water
Take care to site the inverter away from potential water hazards, e.g. do not install
the inverter beneath pipes that are subject to condensation. Avoid installing the
inverter where excessive humidity and condensation may occur.
Installation and overheating
Warning
The inverters MUST not be mounted in an horizontal position.
Mount the inverter vertically to ensure optimum cooling, see Figure 2-1 on page 23.
It is also possible to mount the inverters side-by-side.
Ensure that the inverter’s air vents are not obstructed. Allow 100 mm clearance
above and below the inverter.
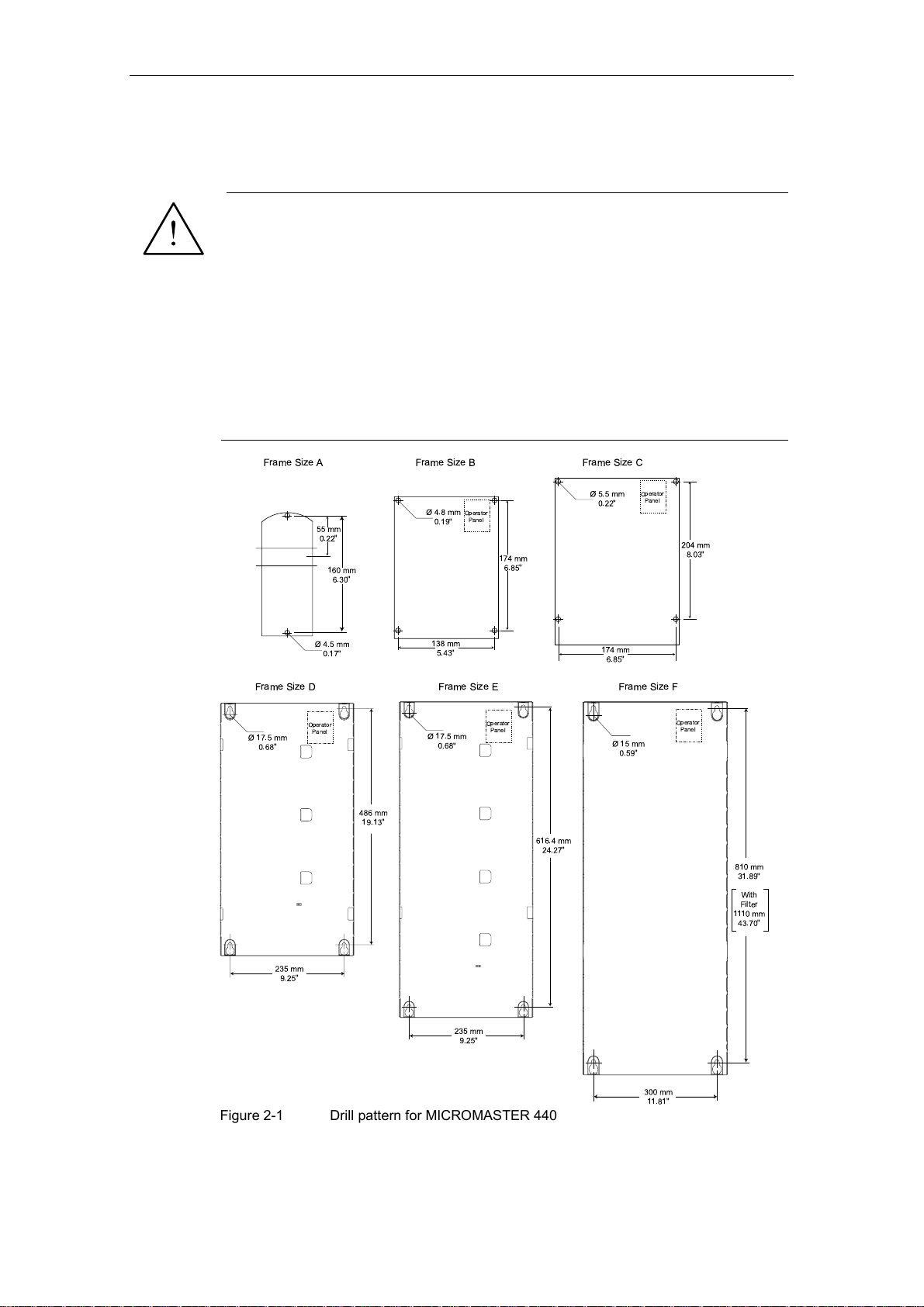
International English 2 Installation
MICROMASTER 440 Operating instructions
6SE6400-5CA00-0BP0
23
2.3 Mechanical Installation
Warning
THIS EQUIPMENT MUST BE GROUNDED.
♦ To ensure the safe operation of the equipment, it must be installed and
commissioned by qualified personnel in full compliance with the warnings laid
down in these operating instructions.
♦ Take particular note of the general and regional installation and safety
regulations regarding work on dangerous voltage installations (e.g. EN
50178), as well as the relevant regulations regarding the correct use of tools
and personal protective equipment (PPE).
♦ The mains input, DC and motor terminals, can carry dangerous voltages even
if the inverter is inoperative; wait 5 minutes to allow the unit to discharge after
switching off before carrying out any installation work.
4
160 mm
6.30"
55 mm
0.22"
Ø 4.5 mm
0.17"
Ø 4.8 mm
0.19"
174 mm
6.85"
138 mm
5.43"
Ø 5.5 mm
0.22"
204 mm
8.03"
174 mm
6.85"
Frame Size A
Frame Size D Frame Size E Frame Size F
Frame Size B Frame Size C
Ø 17.5 mm
0.68"
486 mm
19.13"
235 mm
9.25"
616.4 mm
24.27"
810 mm
31.89"
With
Filter
1110 mm
43.70"
Ø 17.5 mm
0.68"
Ø15mm
0.59"
235 mm
9.25"
300 mm
11.81"
Operator
Panel
Operator
Panel
Operator
Panel
Operator
Panel
Operator
Panel
Figure 2-1 Drill pattern for MICROMASTER 440
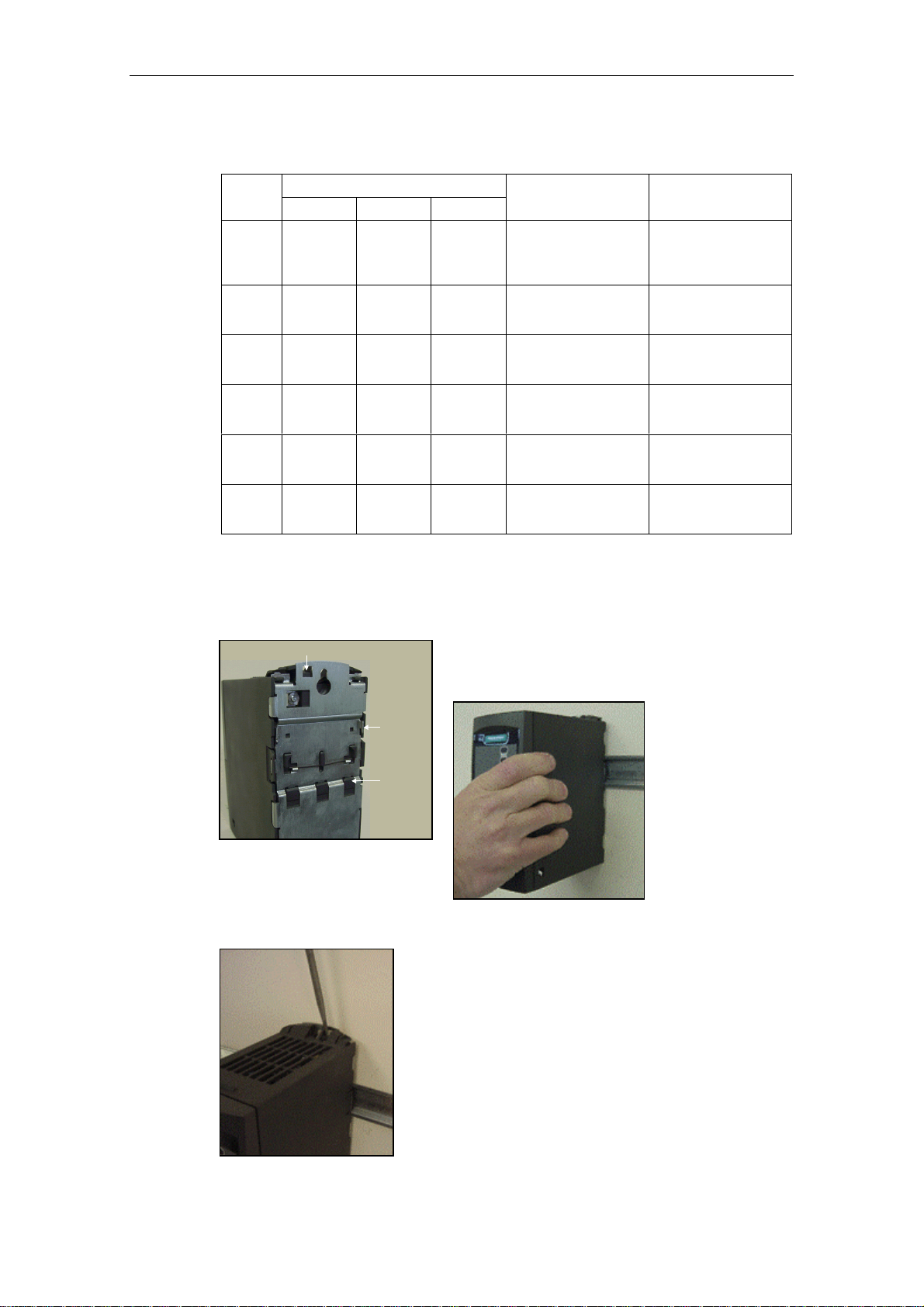
2 Installation International English
MICROMASTER 440 Operating instructions
24 6SE6400-5CA00-0BP0
Release Mechanism
Upper DIN
rail latch
Lower DIN
rail latch
Table 2-1 Dimensions and Torques of MM440 (all frame sizes)
Overall Dimensions
Frame-
Size
Height Width Depth
Fixing Method Tightening Torque
A 173 mm 73 mm 149 mm
2 x M4 Bolts
2 x M4 Nuts
2 x M4 Washers
Connecting to DIN rail
2.5 Nm
with washers fitted
B 202 mm 149 mm 172 mm
4 x M4 Bolts
4 x M4 Nuts
4 x M4 Washers
2.5 Nm
with washers fitted
C 245 mm 185 mm 195 mm
4 x M5 Bolts
4 x M5 Nuts
4 x M5 Washers
2.5 Nm
with washers fitted
D 520 mm 275 mm 245 mm
4 x M8 Bolts
4 x M8 Nuts
4 x M8 Washers
3.0 Nm
with washers fitted
E 650 mm 275 mm 245 mm
4 x M8 Bolts
4 x M8 Nuts
4 x M8 Washers
3.0 Nm
with washers fitted
F
850 mm
with filter
1150 mm
350 mm 300 mm
4 x M8 Bolts
4 x M8 Nuts
4 x M8 Washers
3.0 Nm
with washers fitted
2.3.1 DIN Rail Mounting Frame Size A
Fitting the Inverter to the DIN Rail
1. Fit the inverter to the DIN rail using the upper
DIN rail latch.
2. Push the
inverter against
the DIN rail
and the lower
DIN rail latch
should click
into place.
Removing the Inverter from the DIN Rail
1. To disengaged the release mechanism of the
inverter, insert a screwdriver into the release
mechanism.
2. Apply a downward pressure and the lower DIN rail
latch will disengage.
3. Pull the inverter from the DIN rail.
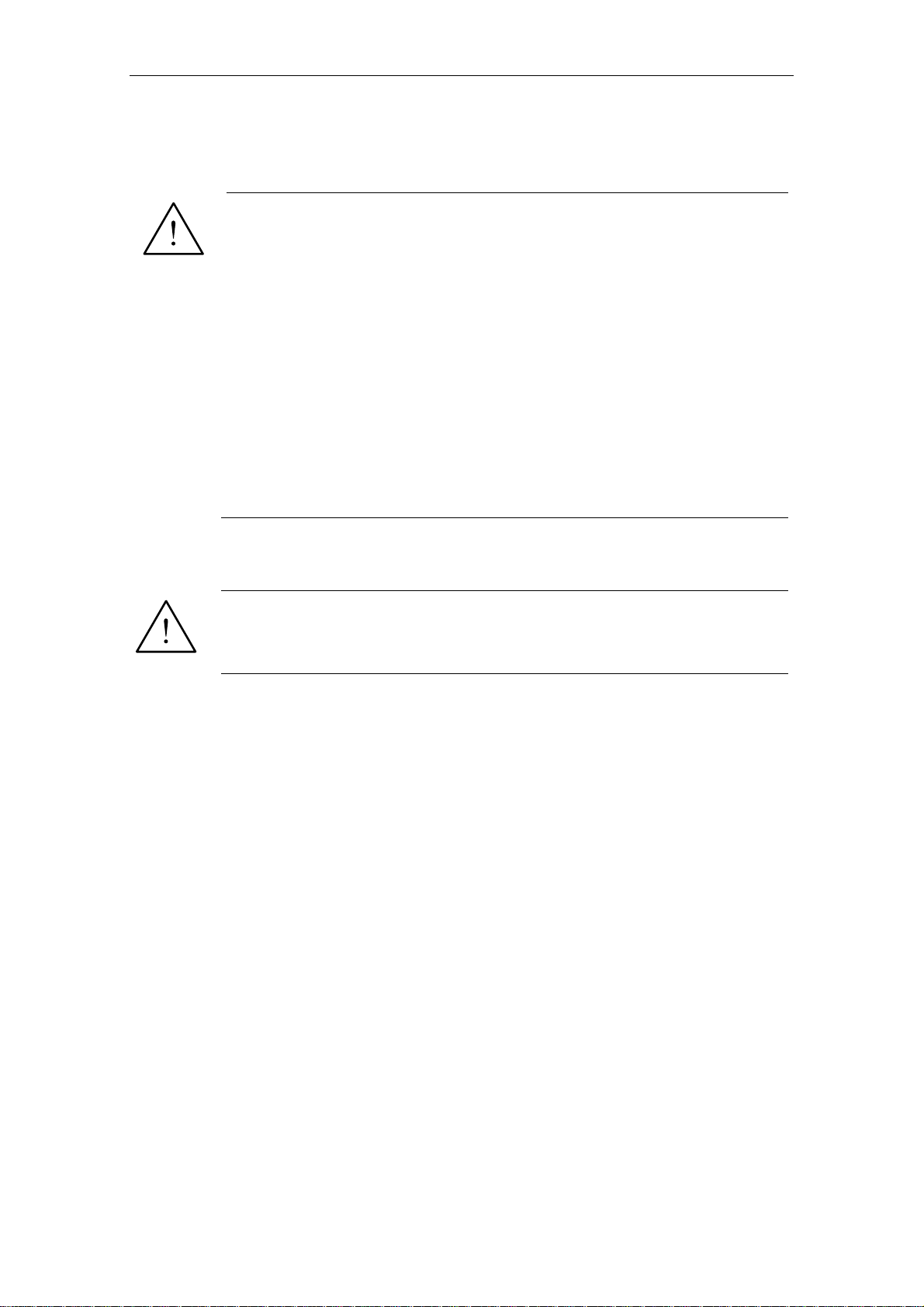
International English 2 Installation
MICROMASTER 440 Operating instructions
6SE6400-5CA00-0BP0
25
2.4 Electrical Installation
Warning
THIS EQUIPMENT MUST BE GROUNDED.
♦ To ensure the safe operation of the equipment, it must be installed and
commissioned by qualified personnel in full compliance with the warnings laid
down in these operating instructions.
♦ Take particular note of the general and regional installation and safety
regulations regarding work on dangerous voltage installations (e.g. EN
50178), as well as the relevant regulations regarding the correct use of tools
and personal protective gear.
♦ The mains input, DC and motor terminals, can carry dangerous voltages even
if the inverter is inoperative; wait 5 minutes to allow the unit to discharge after
switching off before carrying out any installation work.
♦ The inverters can be installed in a side-by-side configuration, but a distance
of 100 mm (3.94 inches) must be maintained if the inverters are installed on
top of each other.
2.4.1 General
Warning
The inverter must always be grounded. If the inverter is not grounded correctly,
extremely dangerous conditions may arise within the inverter, which could prove
potentially fatal.
Operation with ungrounded (IT) supplies
The MICROMASTER will operate from ungrounded supplies and will continue to
operate if an input phase is shorted to ground. If an output phase is shorted to
ground, the MICROMASTER will trip and indicate F0001.
On ungrounded supplies, it will be necessary to remove the ‘Y’ capacitor from the
inside of the unit and fit an output choke. The procedure for removing this capacitor
is described in Appendices G, H, I and J.
Operation with Residual Current Device
If an RCD (also referred to as ELCB or RCCB) is fitted, the MICROMASTER
inverters will operate without nuisance tripping, provided that:
A type B RCD is used.
The trip limit of the RCD is 300mA.
The neutral of the supply is grounded.
Only one inverter is supplied from each RCD.
The output cables are less than 50m (screened) or 100m (unscreened).
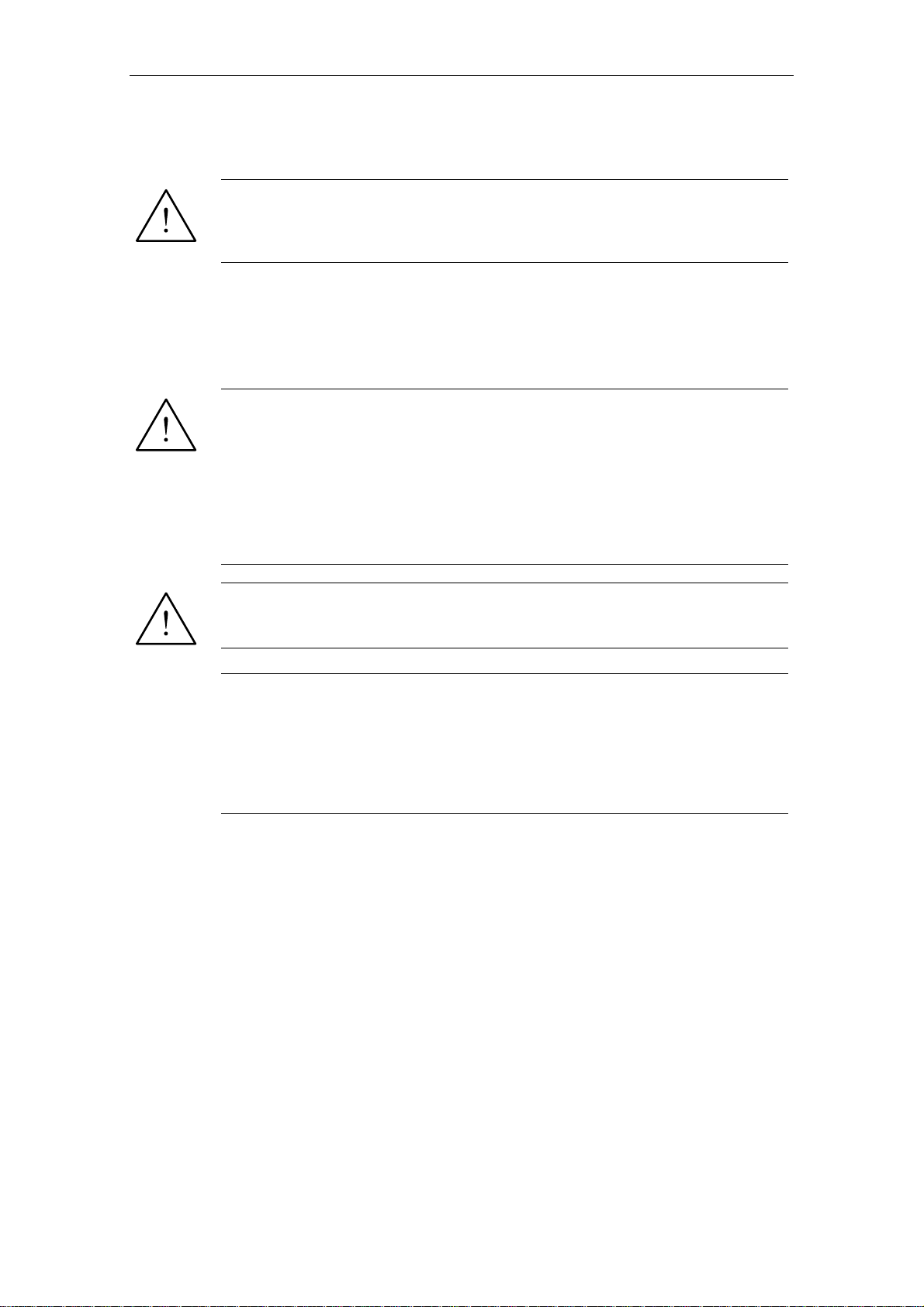
2 Installation International English
MICROMASTER 440 Operating instructions
26 6SE6400-5CA00-0BP0
Operation with long cables
Caution
The control, power supply and motor leads must be laid separately. Do not feed
them through the same cable conduit/trunking. Never use high voltage insulation
test equipment on cables connected to the inverter.
All inverters will operate at full specification with cable lengths up to 50 m screened
or 100 m unscreened.
2.4.2 Power and motor connections
Warning
♦ Isolate the mains electrical supply before making or changing connections to
the unit.
♦ Ensure that the inverter is configured for the correct supply voltage: single /
three-phase 230 V MICROMASTERS must not be connected to a higher
voltage supply.
♦ When synchronous motors are connected or when coupling several motors in
parallel, the inverter must be operated with voltage/frequency control
characteristic (P1300 = 0, 2 or 3).
Caution
After connecting the power and motor cables to the proper terminals, make sure
that the covers have been replaced properly before supplying power to the unit!
Note
♦ Ensure that the appropriate circuit-breakers/fuses with the specified current
rating are connected between the power supply and inverter (see Tables
starting on page 77).
♦ Use Class 1 60/75
o
C copper wire only (for UL compliance). For tightening
torque see table on page 79.
♦ To tighten up the power terminal screws use a 4 - 5 mm cross-tip screwdriver.
Access to the power and motor terminals
The procedure for accessing the power and motor terminals on the
MICROMASTER 440 Inverter is illustrated in Appendices. Please also refer to the
photographs showing the Power Terminal connections and the Control Terminal
connections on the inside of the back cover of this manual.
When the covers have been removed to reveal the terminals, connect the power
and motor connections as shown on the next page.
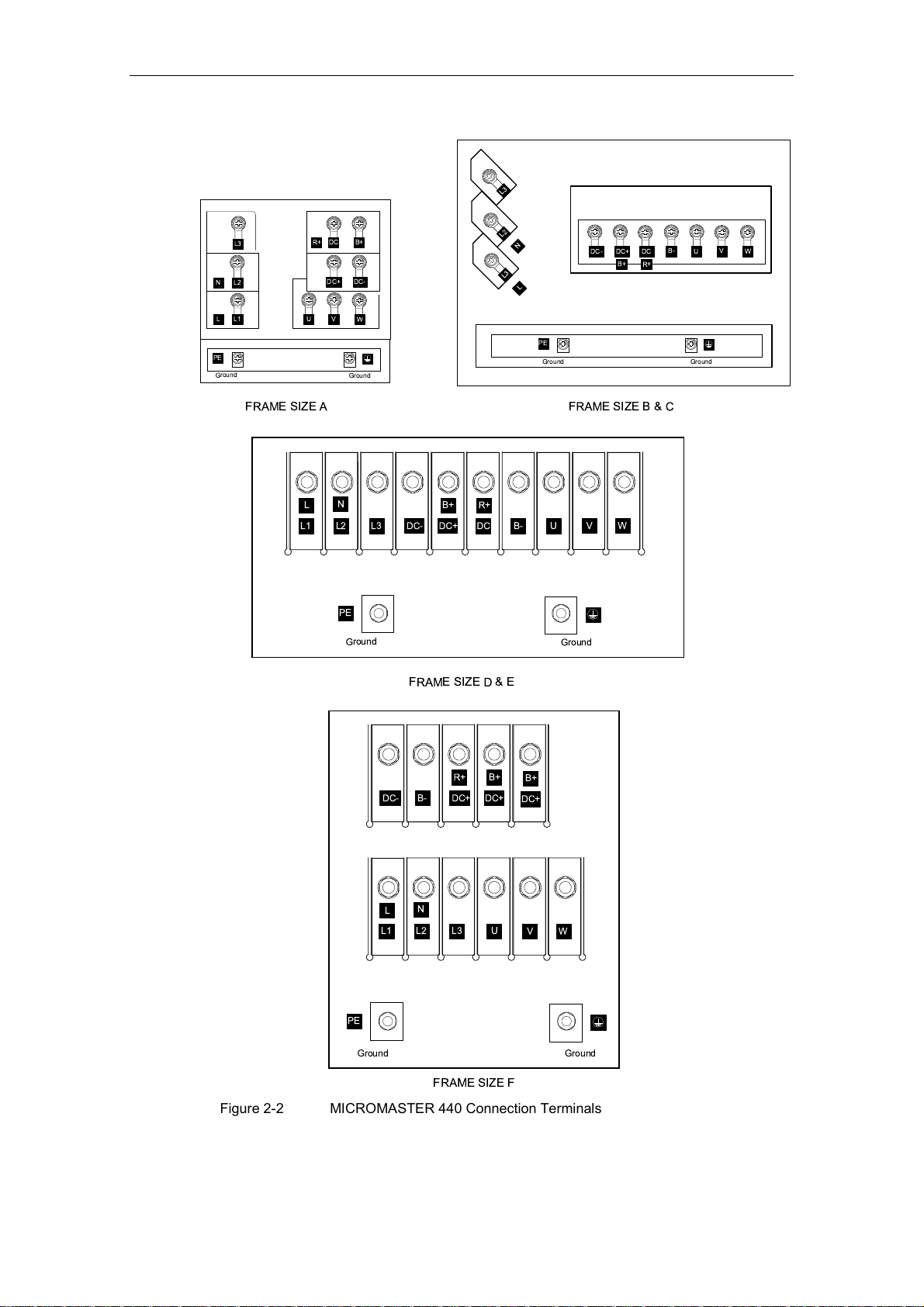
International English 2 Installation
MICROMASTER 440 Operating instructions
6SE6400-5CA00-0BP0
27
L3
L2
L1
N
L
DC
DC+
B+
DC-
WU
V
PE
R+
Ground
Ground
L3
L2
L3
L
N
DCDC-
DC+
VB-
U
W
PE
B+
R+
Ground
Ground
FRAME SIZE A
FRAME SIZE F
FRAME SIZE B & C
L1 UB-DCDC+L2 L3 DC-
WV
N
L
B+ R+
PE
Ground
Ground
FRAME SIZED&E
Ground Ground
DC- DC+ DC+B-
B+R+
PE
L1 UL2 L3
WV
N
L
DC+
B+
Figure 2-2 MICROMASTER 440 Connection Terminals
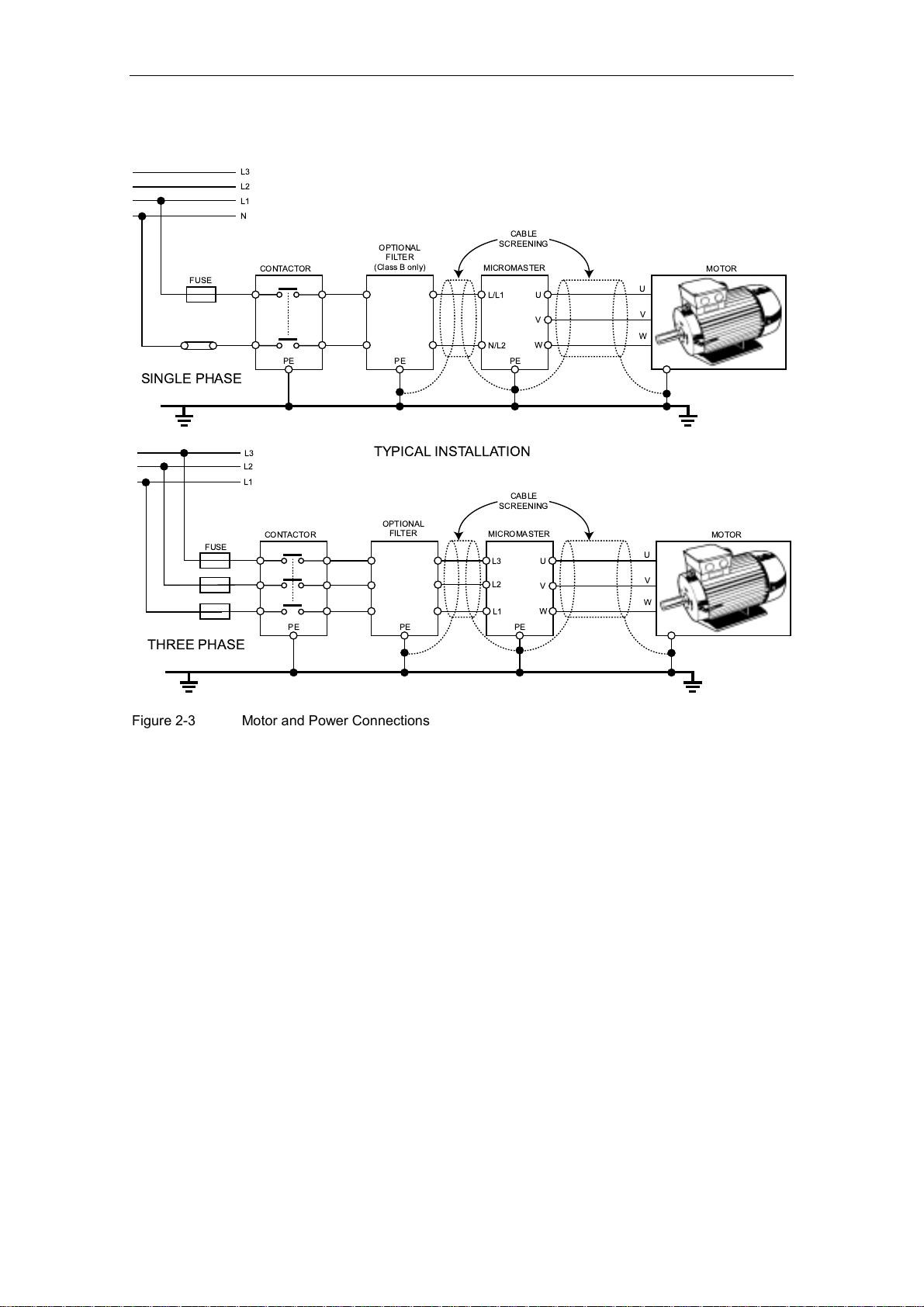
2 Installation International English
MICROMASTER 440 Operating instructions
28 6SE6400-5CA00-0BP0
CONTACTOR
FUSE
N
L1
L2
L3
OPTIONAL
FILTER
(Class Bonly)
MICROMASTER
MOTOR
U
U
V
V
W
W
L/L1
N/L2
PE
PEPE
SINGLE PHASE
CONTACTOR
FUSE
L1
L2
L3
L1
L2
L3
OPTIONAL
FILTER
MICROMASTER
MOTOR
U
U
V
V
W
W
PE
PEPE
THREE PHASE
TYPICAL INSTALLATION
CABLE
SCREENING
CABLE
SCREENING
Figure 2-3 Motor and Power Connections
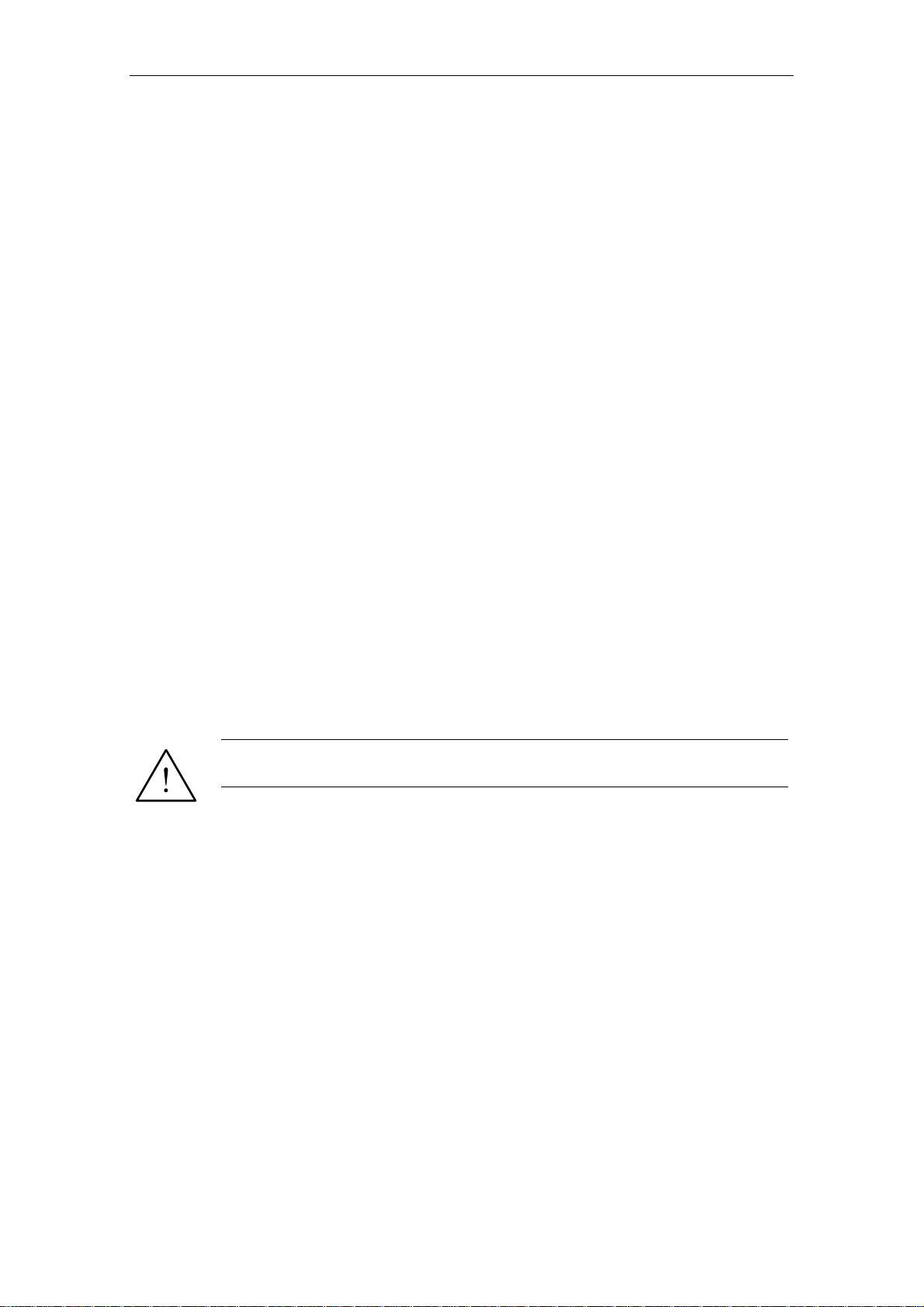
International English 2 Installation
MICROMASTER 440 Operating instructions
6SE6400-5CA00-0BP0
29
2.4.3 Avoiding Electro-Magnetic Interference (EMI)
The inverters are designed to operate in an industrial environment where a high
level of EMI can be expected. Usually, good installation practices will ensure safe
and trouble-free operation. If you encounter problems, follow the guidelines stated
below.
Action to Take
Ensure that all equipment in the cubicle is well grounded using short, thick
grounding cable connected to a common star point or busbar
Make sure that any control equipment (such as a PLC) connected to the
inverter is connected to the same ground or star point as the inverter via a
short thick link.
Connect the return ground from the motors controlled by the inverters directly
to the ground connection (PE) on the associated inverter
Flat conductors are preferred as they have lower impedance at higher
frequencies
Terminate the ends of the cable neatly, ensuring that unscreened wires are as
short as possible
Separate the control cables from the power cables as much as possible, using
separate trunking, if necessary at 90º to each other.
Whenever possible, use screened leads for the connections to the control
circuitry
Ensure that the contactors in the cubicle are suppressed, either with R-C
suppressors for AC contactors or 'flywheel' diodes for DC contactors fitted to
the coils. Varistor suppressors are also effective. This is important when the
contactors are controlled from the inverter relay
Use screened or armored cables for the motor connections and ground the
screen at both ends using the cable clamps
Warning
Safety regulations must not be compromised when installing inverters!
2.4.4 Screening Methods
Frame Sizes A, B and C
For frame sizes A, B and C the Gland Plate Kit is supplied as an option. It allows
easy and efficient connection of the necessary screening. See the Gland Plate
Installation Instructions contained on the Document CD-ROM, supplied with the
MM440.
Frame Sizes D, E and F
The Gland Plate is factory fitted. The installation of the screening is accomplished
using the same methodology as in frame sizes A, B and C.
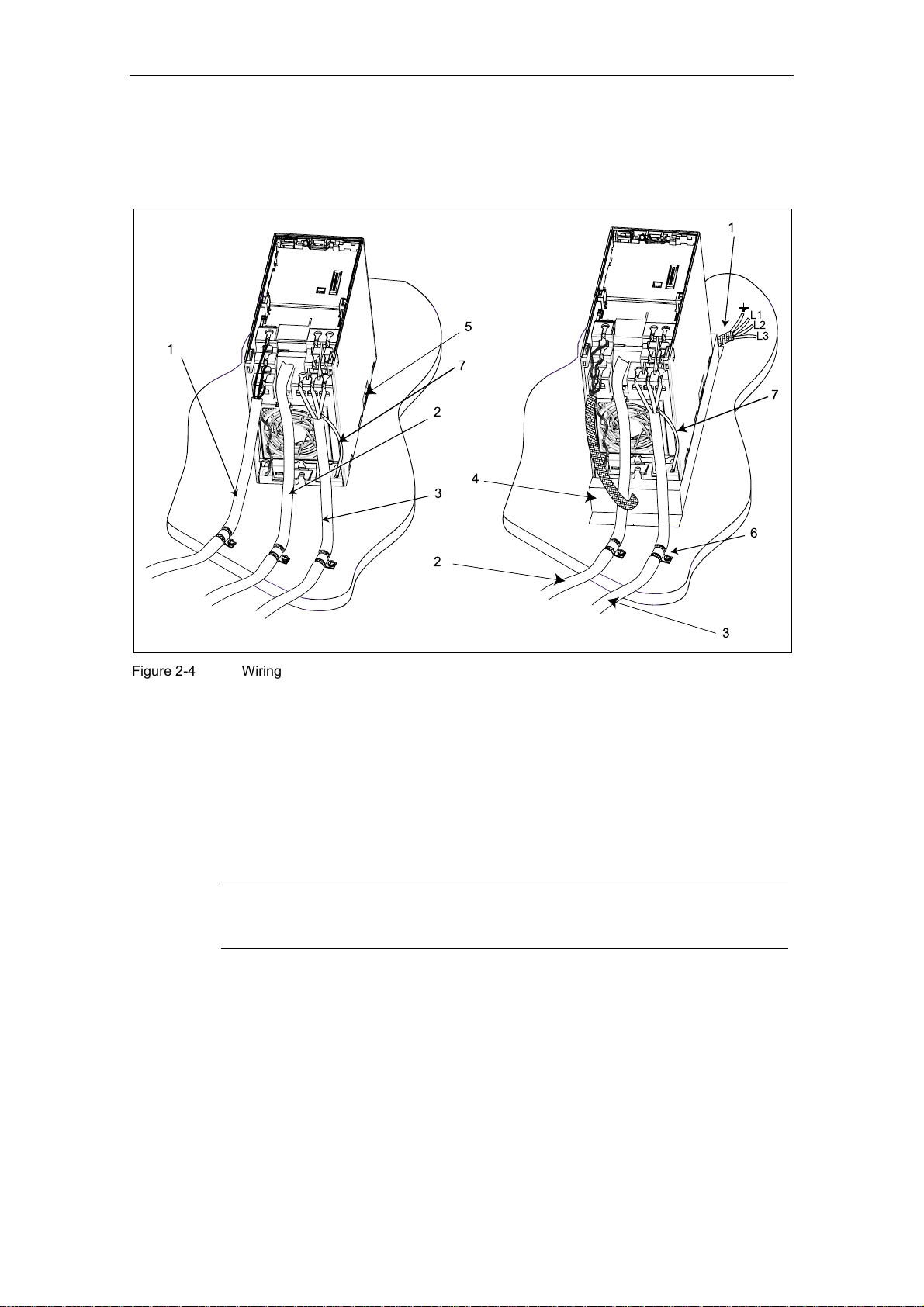
2 Installation International English
MICROMASTER 440 Operating instructions
30 6SE6400-5CA00-0BP0
Screening without a Gland Plate
Should a Gland Plate not be available, then the inverter can be screened using the
methodology shown in Figure 2-4.
L3
L2
L1
1
1
2
5
7
7
2
3
4
3
6
Figure 2-4 Wiring Guidelines to Minimize the Effects of EMI
Legend
1 Mains power input
2 Control cable
3 Motor cable to I/O board
4 Footprint filter
5 Metal back plate
6 Use suitable clips to fix motor and control cable screens securely to metal
back plate
7 Screen cable
Note
To enhance the screening of the motor and control cables, the optional Gland
Plate can be used (not shown in Figure 2-4).