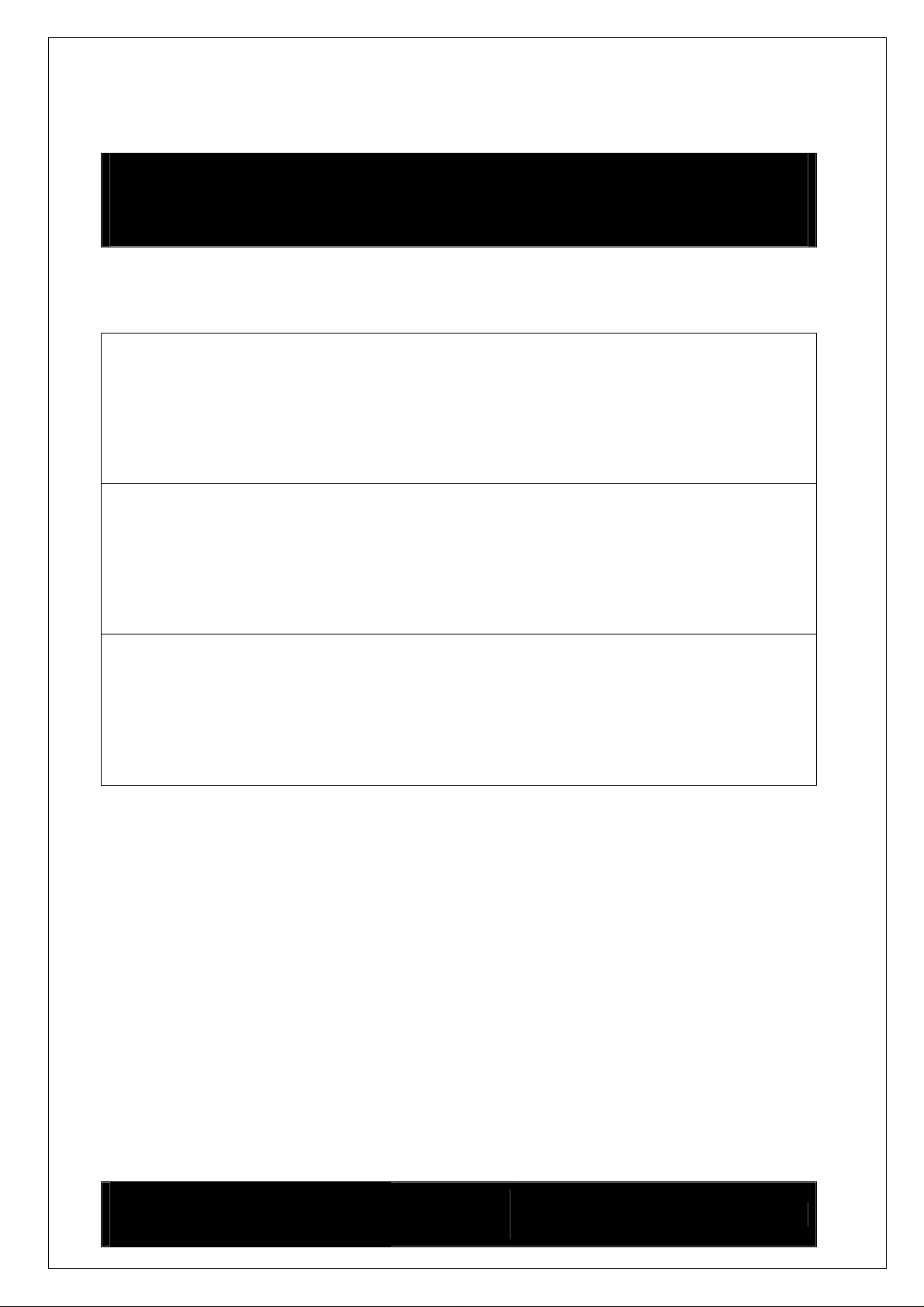
User guide and maintenance
manual
D
E
U
T
D
E
U
T
Z
Z
E
n
gii
n
E
n
g
9
1
9
1
n
4
4
e
e
03120382
01/01/2002
33522910601_0_1
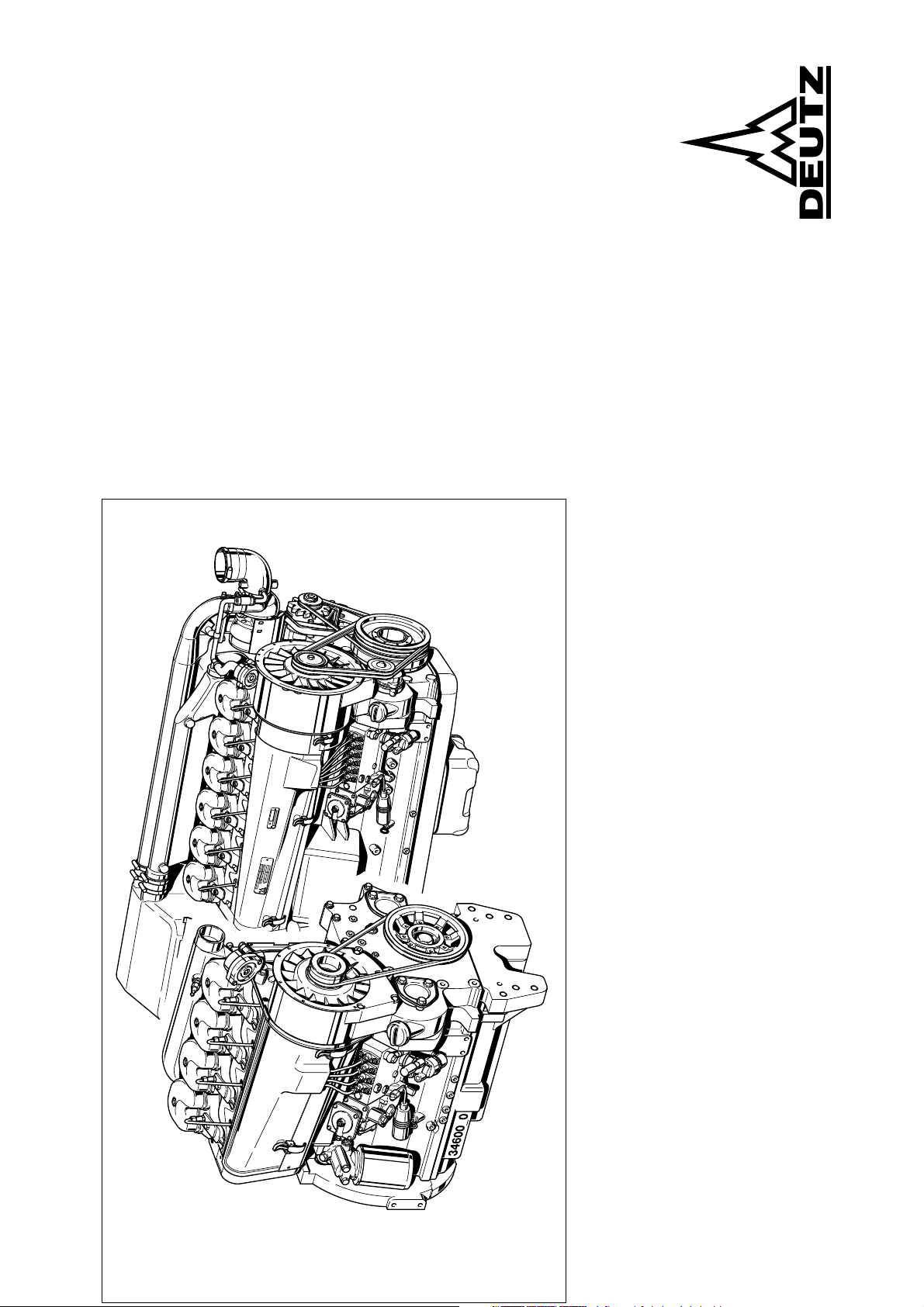
Operation Manual
914
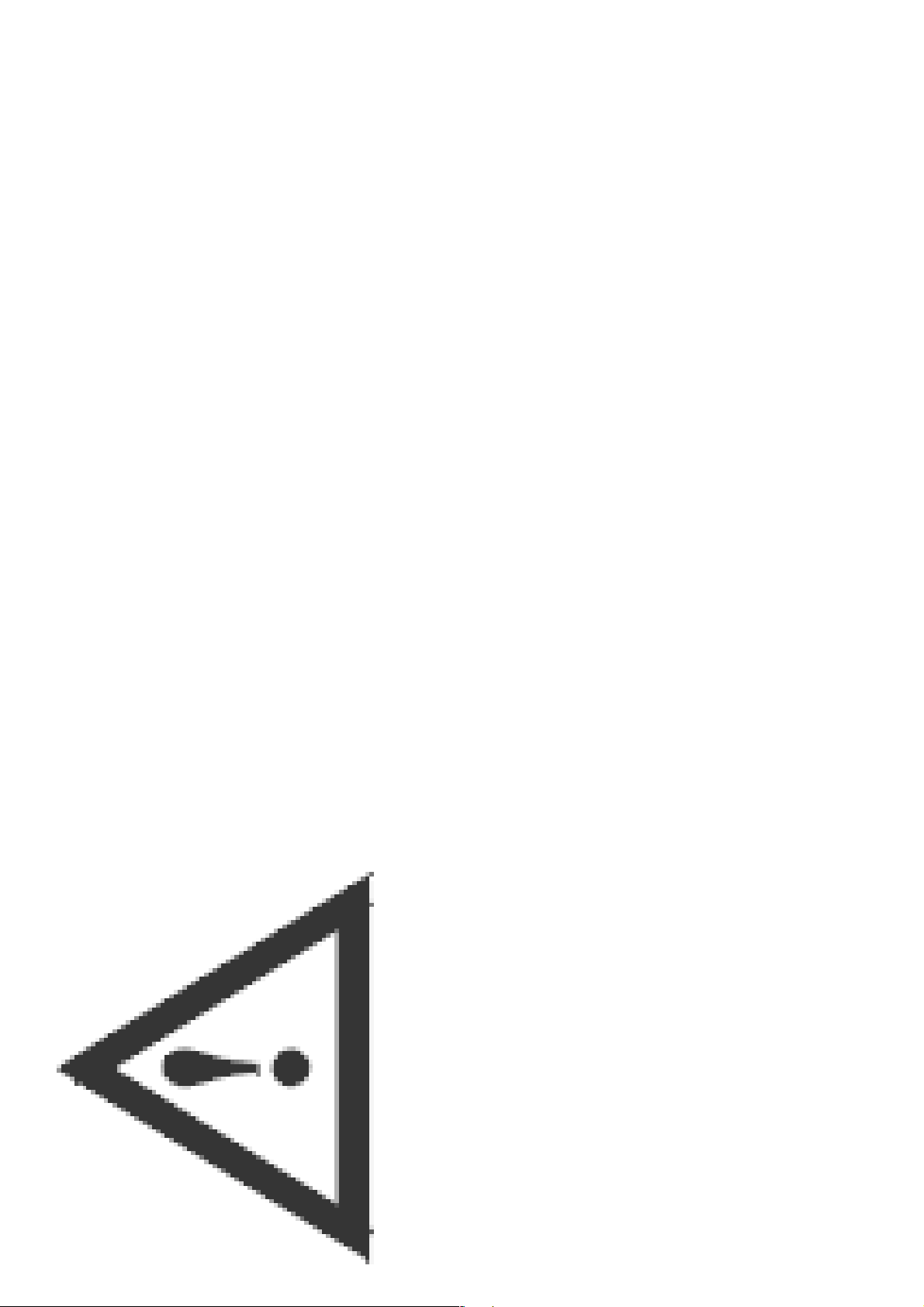
validate any liability claims against the manu-
facturer for resultant damage.
Manipulations of the injection and regulating
system may also influence the performance
of the engine, and its emissions. Adherence
to legislation on pollution cannot be guaran-
teed under such conditions.
● Unauthorized engine modifications will in-
given in this Operation Manual. This will
enable you to avoid accidents, preserve the
manufacturer’s warranty and maintain the
engine in peak operating condition.
Safety guidelines / Accident prevention
● Please read and observe the information
the application specified in the scope of
supply, as described by the equipment manu-
facturer and is to be used only for the
● This engine has been built exclusively for
air intake area to the blower.
The manufacturer shall not be held respon-
sible for any damage which results from
such work.
● Do not change, convert or adjust the cooling
intended purpose. Any use exceeding that
scope is considered to be contrary to the
intended purpose. The manufacturer will
not assume responsibility for any damage
resulting therefrom. The risks involved are
erations on the engine, the use of DEUTZ
original parts is prescribed. These are spe-
cially designed for your engine and guaran-
tee perfect operation.
Non-compliance results in the expiry of the
warranty!
● When carrying out maintenance/repair op-
to be borne solely by the user.
pose also implies compliance with the con-
ditions laid down by the manufacturer for
operation, maintenance and servicing. The
engine should only be operated by person-
nel trained in its use and the hazards in-
● Use in accordance with the intended pur-
should only be carried out when the engine
is switched off and has cooled down.
You must ensure that the electrical systems
● Maintenance and cleaning of the engine
volved.
and other generally accepted safety and
industrial hygiene regulations must be ob-
● The relevant accident prevention guidelines
have been switched off and the ignition key
has been removed.
Accident prevention guidelines concerning
electrical systems (e.g. VDE-0100/-0101/-
0104/-0105 Electrical protective measures
against dangerous touch voltage) are to be
observed.
When cleaning with fluids, all electrical com-
ponents are to be covered impermeably.
served.
injury through:
- turning/hot components
- engines with positive ignition
- ignition systems (high electrical voltage)
You must avoid contact at all times!
● When the engine is running, there is a risk of
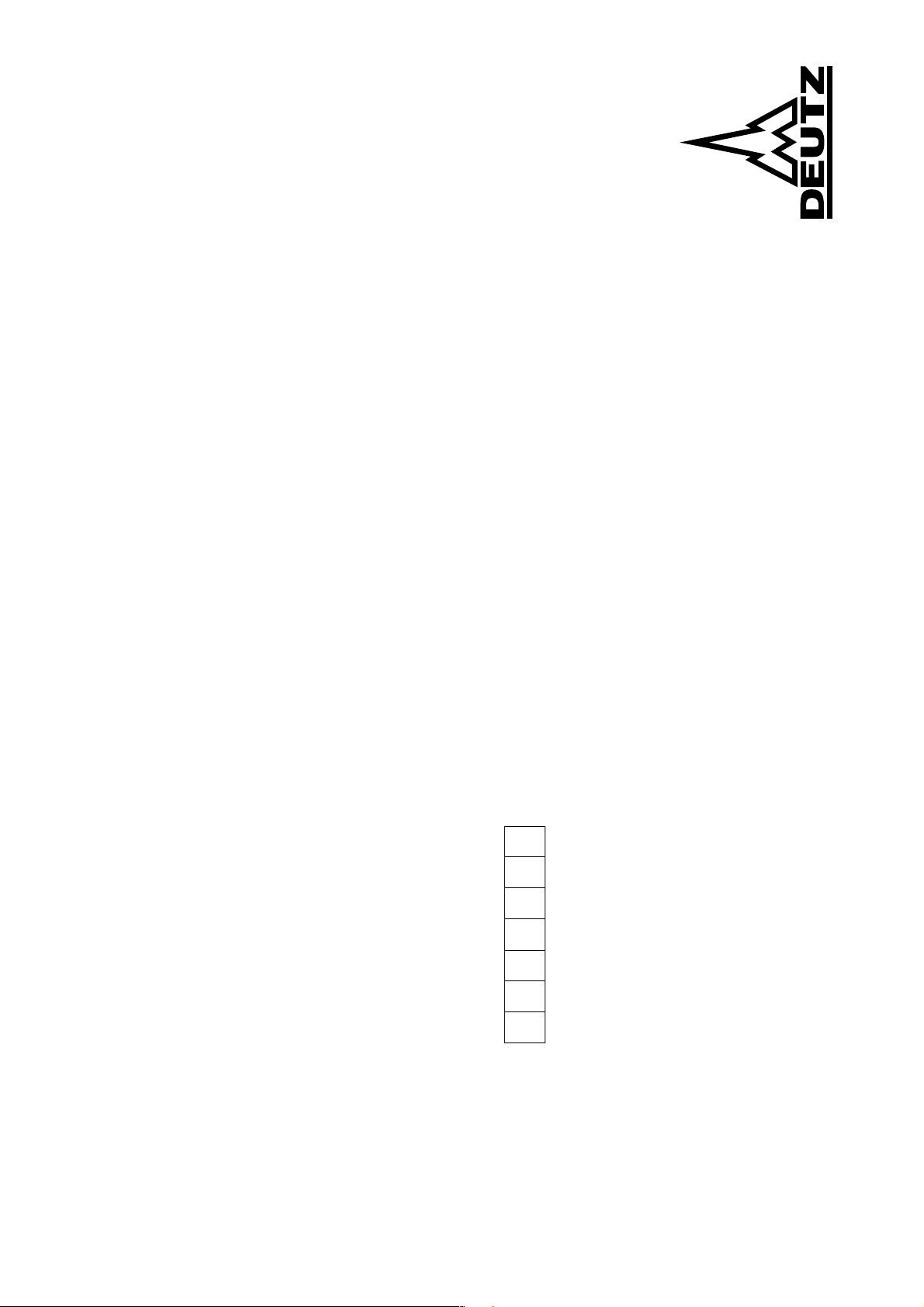
Operation Manual
914
0312 0382 en
Engine Serial Number
Technical modifications required to improve
our engines are reserved with regard to speci-
fication data and other technical information
contained in this Operation Manual. No parts of
this Manual may be reproduced in any form or
by any means without our written approval.
Please enter the engine serial number here.
This number should be quoted when inquiring
about Customer Service, Repairs or Spare
Parts (see Section 2.1).
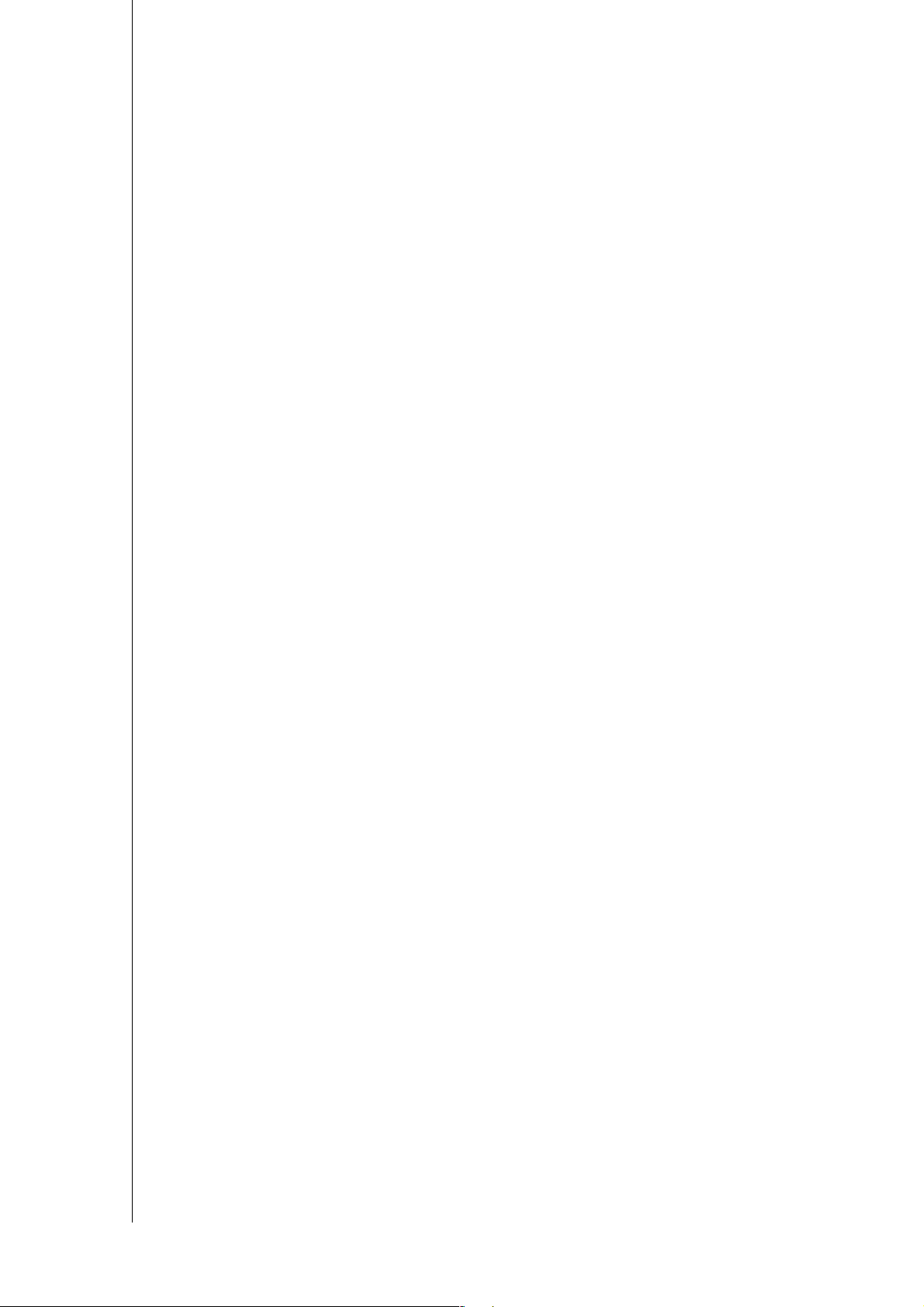
Foreword
Dear Customer,
Air / liquid-cooled Deutz engines are designed
for a large number of applications. Conse-
quently, a wide range of variants is offered to
meet the requirements of specific cases.
Your engine is appropriately equipped for the
installation concerned, which means that not
all of the components described in this Opera-
tion Manual are necessarily mounted to your
engine.
We have endeavoured to highlight any differ-
ences so that you will be able to locate theses
differences relevant to your engine.
Please read this Manual before starting your
engine, and always observe the operating and
maintenance instructions.
We are available to help with any additional
inquiries
Sincerely,
DEUTZ AG
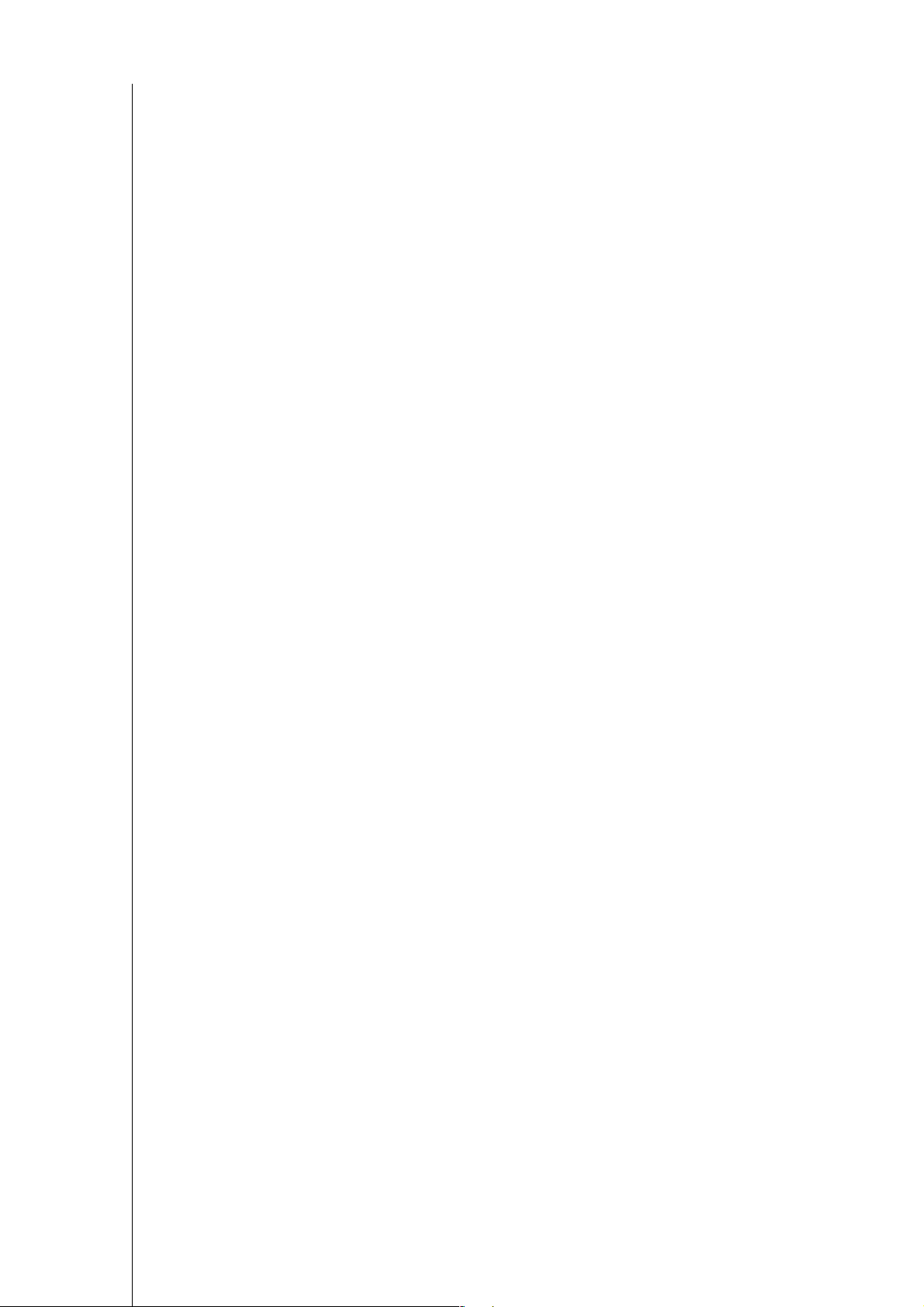
Index
6.4.3 Clean Oil Bath Air Filter
6.4.4 Dry Type Air Cleaner
6.5 Belt Drives
6.5.1 Check V-belts
6.5.2 Change fan belt
6.5.3 Tension alternator belts
6.5.4 Change alternator belts
6.5.5 Check warning system
6.5.6 Tension/change air compressor
belts
6.5.7 Air compressor model with dual belts
(adjust if necessary)
6.6 Adjustments
6.6.1 Check valve clearance
6.7 Accessories
6.7.1 Battery
6.7.2 Rotary Current Alternator
6.7.3 Transportation Shackles
6.8 Engine cleaning
6.8.1 Engine cleaning
Altitude
6.9 Additional Maintenance Work
6.9.1 Check fastenings
6.9.2 Check functioning of glow plugs
Settings
7 Faults, Causes and Remedies
7.1 Fault Table
8 Engine Preservation
8.1 Preservation
8.1.1 Preserve engine
8.1.2 Remove engine preservation
9 Technical Specification
9.1 Engine Specifications and
9.2 Screw Tightening Torques
9.3 Tools
10 Service
3.2 Starting
3.2.1 Starting
3.3 Monitoring Operation
3.3.1 Engine Oil Pressure
3.3.2 Engine temperature
3.3.3 Cooling fan drive
3.4 Shutting off
3.4.1 Mechanical shut-off
1 General
2 Engine Description
2.1 Model
2.1.1 Rating Plate
2.1.2 Position of the Rating Plate
2.1.3 Engine Serial Number
2.1.4 Cylinder numbering
2.1.5 Direct injection
3.4.2 Electrical shut-off
3.5 Operating Conditions
3.5.1 Winter Operation
3.5.2 High Ambient Temperature, High
4 Operating Media
4.1 Lube Oil
4.1.1 Quality
4.1.2 Viscosity
Intercooler over air-intake line
Intercooler over air-intake line
2.2 Engine Illustrations
2.2.1 Operation side BF3L 914
2.2.2 Air outlet side BF3L 914
2.2.3 Operation side F4L 914
2.2.4 Air outlet side F4L 914
2.2.5 Operation side BF6L 914
2.2.6 Air outlet side BF6L 914 C
4.2 Fuel
4.2.1 Quality
4.2.2 Winter Fuel
5 Routine Maintenance
5.1 Maintenance Plan
5.2 Maintenance Diagram
5.3 Maintenance Work Completed
6 Service and Maintenance
6.1 Lube oil system
6.1.1 Oil change intervals
6.1.2 Check Oil Level / Change Engine Oil
Intercooler over flywheel
Intercooler over flywheel
2.2.7 Operation side BF6L 914 C
2.2.8 Air outlet side BF6L 914
2.3 Lube Oil Circuit Schematic
2.3.1 Lube Oil Circuit Schematic
2.4 Fuel System Plan
2.4.1 Fuel System
exhaust thermostat
2.5 Engine cooling
2.5.1 Amount of cool air regulated by
6.1.3 Replace Oil Filter
6.1.4 Change bypass-oil filter use
6.2 Fuel System
6.2.1 Replace fuel filter
6.2.2 Precleaning fuel/clean fuel filter
6.3 Cooling system
6.3.1 Cleaning Intervals
6.4 Combustion Air Filter
6.4.1 Cleaning Intervals
6.4.2 Emptying Cyclone Type Precleaner
exhaust thermostat and solenoid valve
2.5.2 Amount of cool air regulated by
3 Engine Operation
3.1 Commissioning
3.1.1 Pour in Engine Oil
3.1.2 Filling Oil Bath Air Filter with Engine Oil
3.1.3 Pour in Fuel
3.1.4 Bleed
3.1.5 Other Preparations
3.1.6 Additional maintenance work
3.1.7 Change-over switch for oil heater
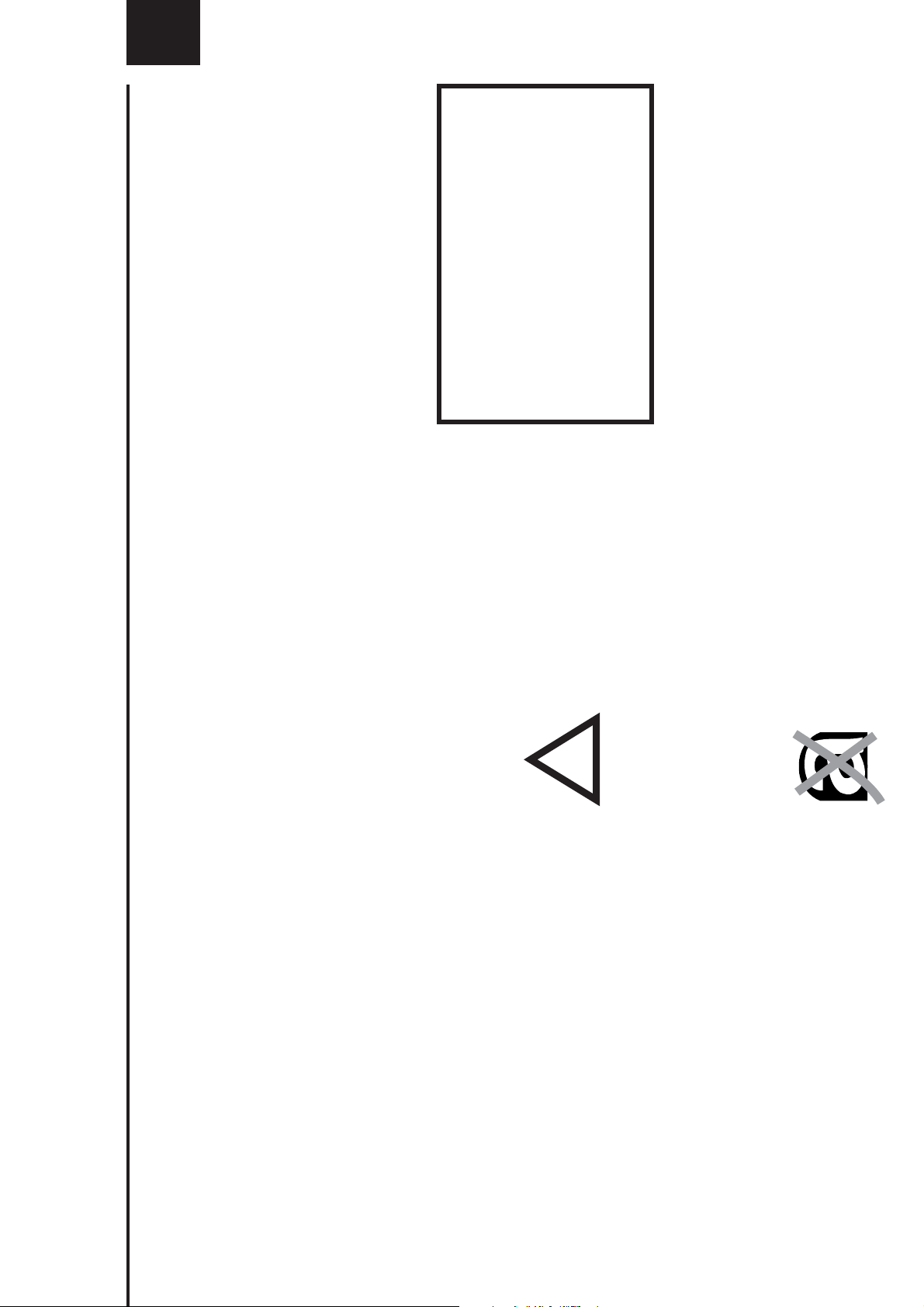
1
General
Service
California
Proposition 65 Warning
Please contact one of our authorized service
representatives in the event of breakdowns or for
spare parts inquiries. Our trained specialists will
carry out repairs quickly and professionally, using
only genuine spare parts.
Original parts from DEUTZ AG are always produced
in accordance with state-of-the-art technology.
Please turn to the end of this manual for further
service information.
Diesel engine exhaust and some of its consti-
tuents are known to the State of California to
cause cancer, birth defects, and other repro-
ductive harm.
Care and Maintenance
Sound care and maintenance practices will ensure
that the engine continues to meet the requirements
placed on it. Recommended service intervals must
be observed and service and maintenance work
carried out conscientiously.
Special care should be taken under abnormally
This symbol is used for all safety
warnings. Please follow them
demanding operating conditions.
Safety
carefully. The attention of operating
personnel should be drawn to these
safety instructions. General safety
!
and accident prevention regulations laid down by
law must also be observed.
Asbestos
DEUTZ original parts are asbestos-
free.
DEUTZ Diesel Engines
are the product of many years of research and
development. The resulting know-how, coupled
with stringent quality standards, guarantee their
long service life, high reliability and low fuel
consumption.
It goes without saying that DEUTZ Diesel Engines
meet the highest standards for environmental
protection.
Beware of Running Engine
Shut the engine down before carrying out mainte-
nance or repair work. Ensure that the engine cannot
be accidentally started. Risk of accidents.
When the work is complete, be sure to refit any
panels and guards that may have been removed.
Never fill the fuel tank while the engine is running.
Observe industrial safety regulations when running
the engine in an enclosed space or underground.
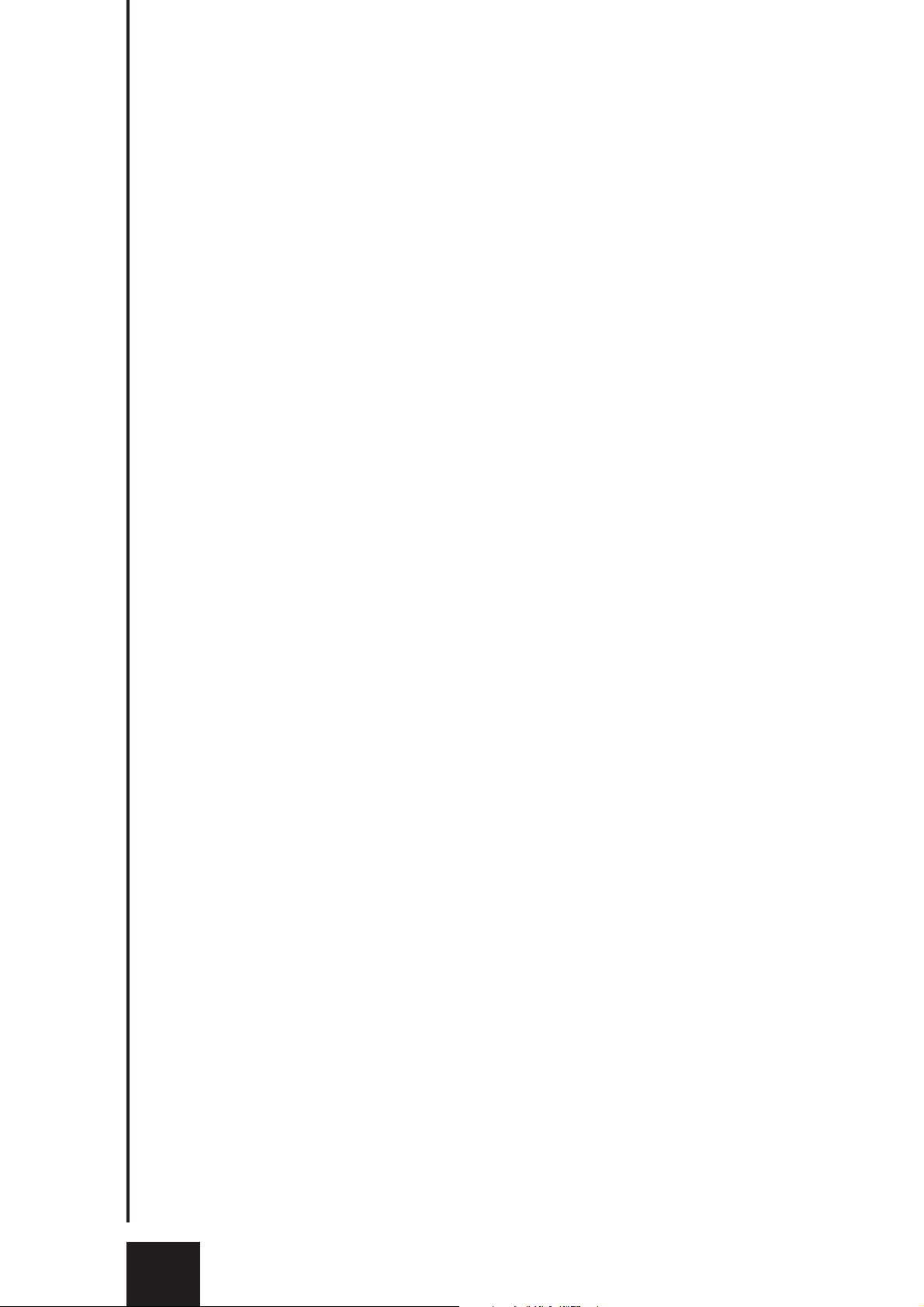
1
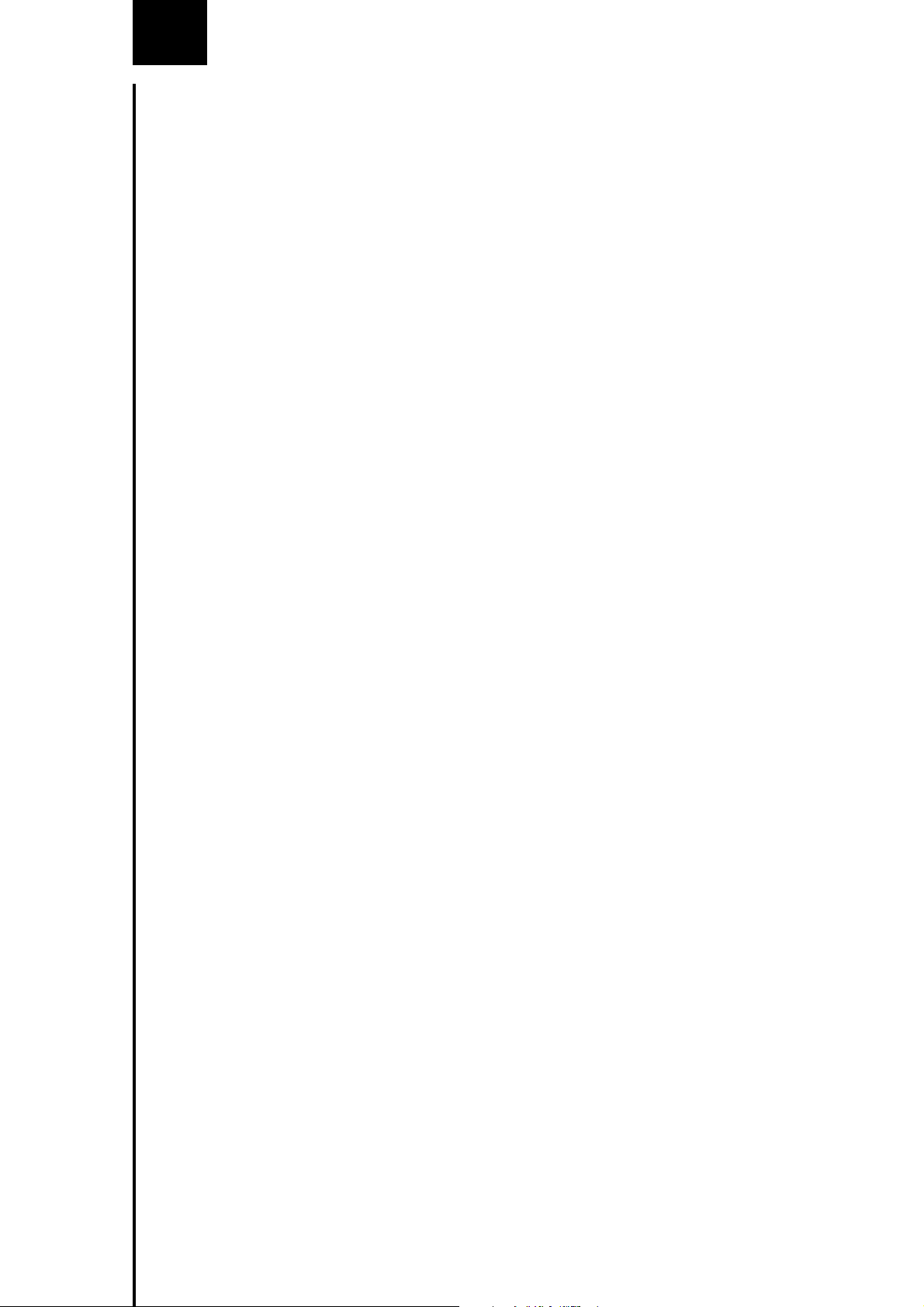
2
Engine Description
© 2001
2.1 Model
2.2 Engine Illustrations
2.3 Lube Oil Circuit Schematic
2.4 Fuel System Plan
2.5 Engine cooling
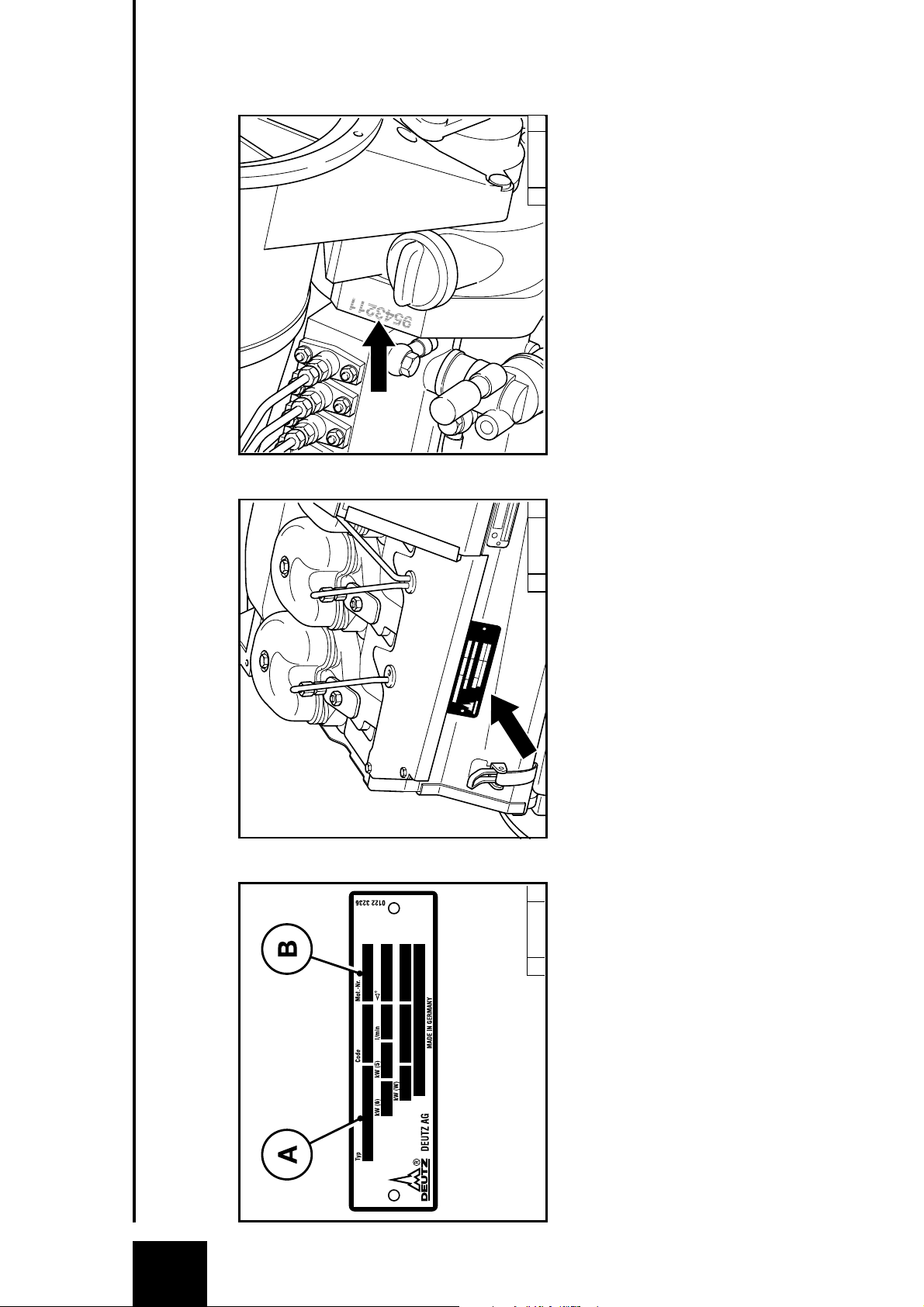
2.1.3 Engine Serial Number
Plate
© 34 571 0 © 34 572 0
The engine serial number is stamped on the
crankcase (arrow) as well as the rating
plate.
2.1.2 Position of the Rating
Engine Description 2.1 Model
2.1.1 Rating Plate
2
The rating plate C is attached to the crankcase.
© 34 570 0
The model A, the engine serial number B and
Depending on the model, a second rating
plate may be affixed to the air duct hood.
the performance data are stamped on the
rating plate.
The model and engine serial number must be
given when ordering parts.
© 2001
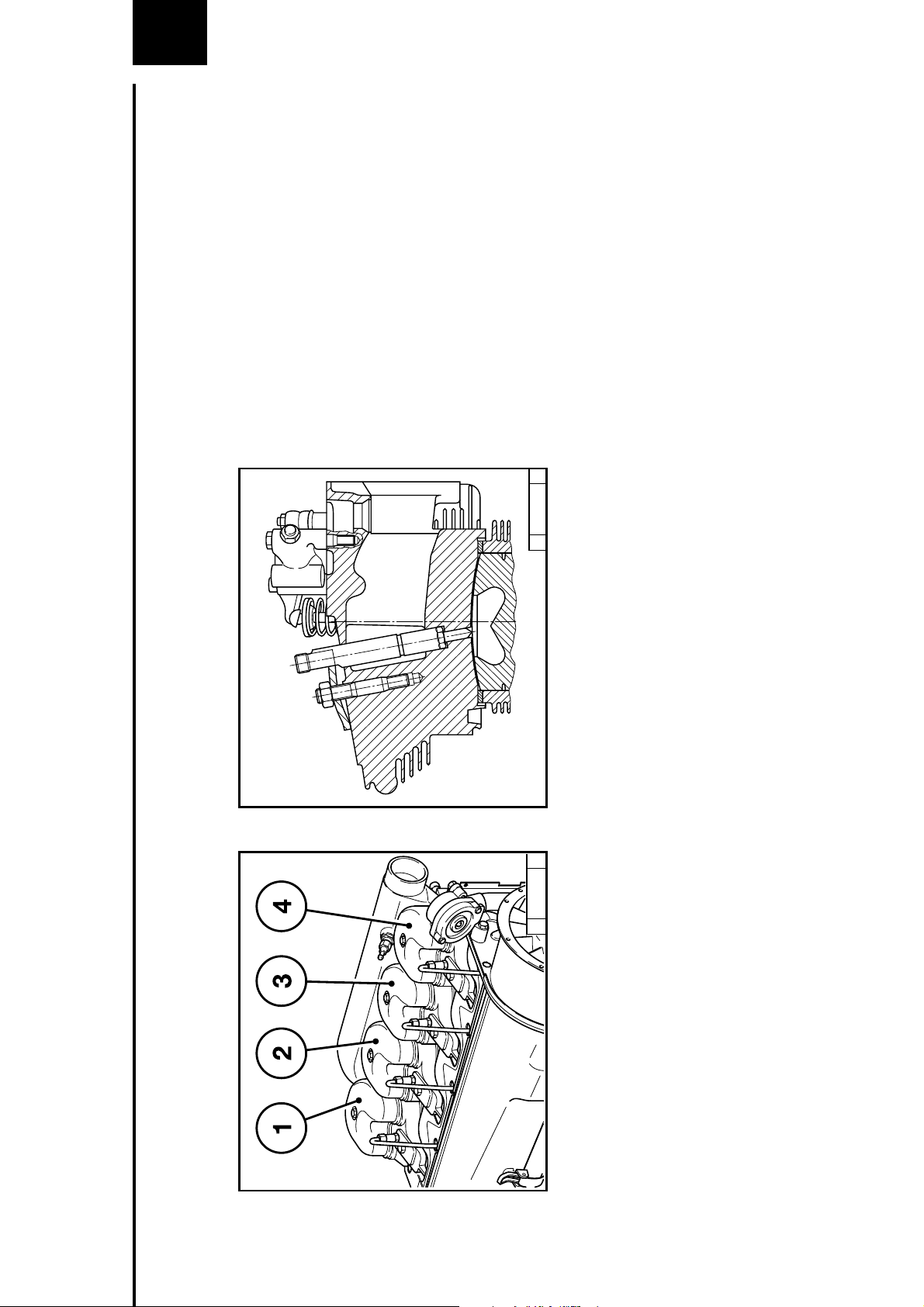
2
© 2001
B/FL 914
2.1.5 Direct injection
© 35 215 0
© 34 599 0
Engines with direct injection are used if high
output is required.
2.1 Model Engine Description
2.1.4 Cylinder numbering
Cylinders are numbered consecutively,
beginning at the flywheel.
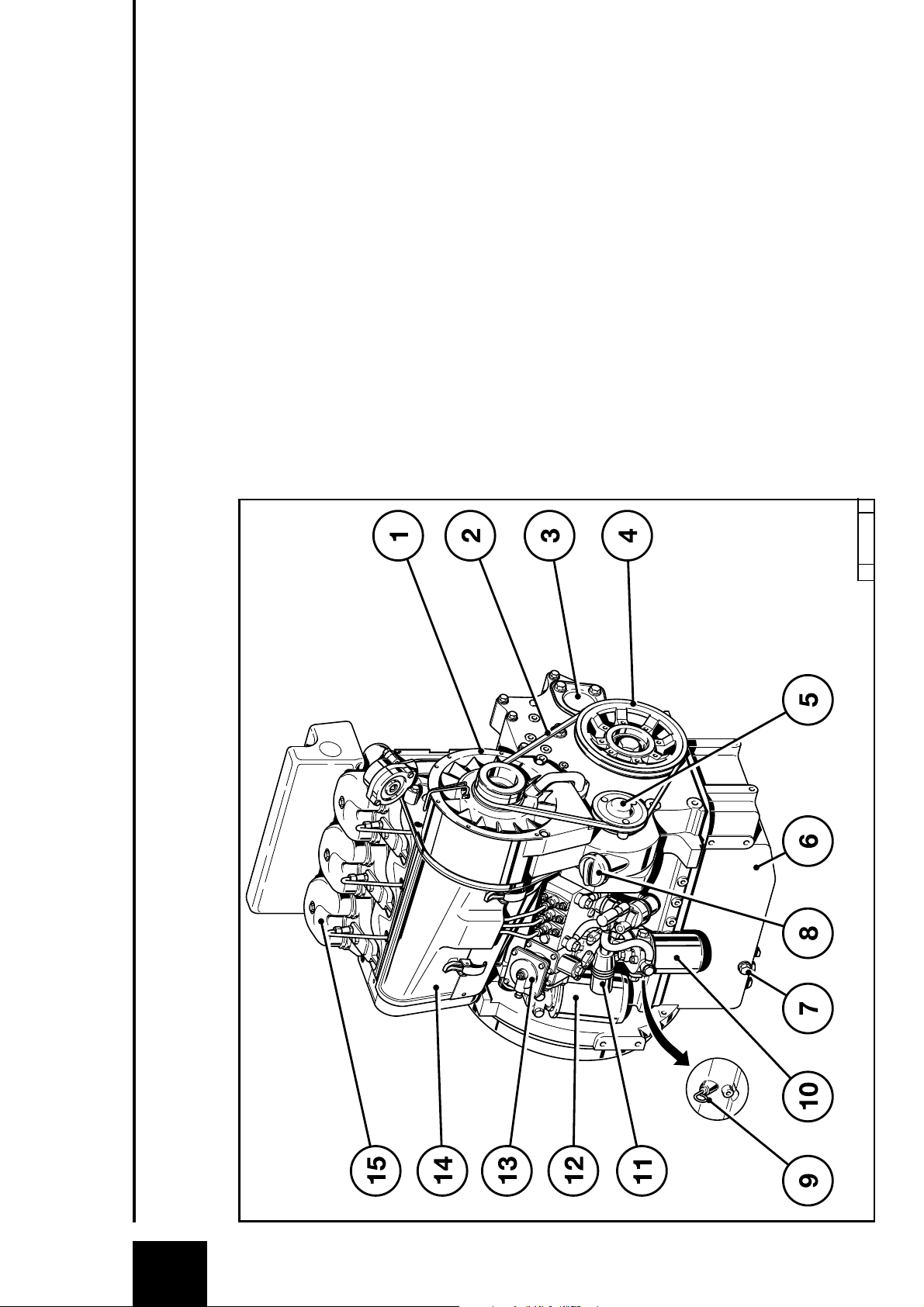
1 Cooling fan
2 V-Belts (fan)
3 Optional attachment of hydraulic pumps
4 V-belt washer
5 Tension roller
6 Oil pan
7 Oil drain screw
8 Oil filler neck
9 Oil dipstick
11 Solenoid (shut-off magnet)
10 Fuel change filter
12 Lube oil filter
13 Full-stop depending on charge air pressure
14 Air duct hood
15 Cylinder head cover
© 34 575 0
BF3L 914
Engine Description 2.2 Engine Illustrations
2.2.1 Operation side
2
© 2001
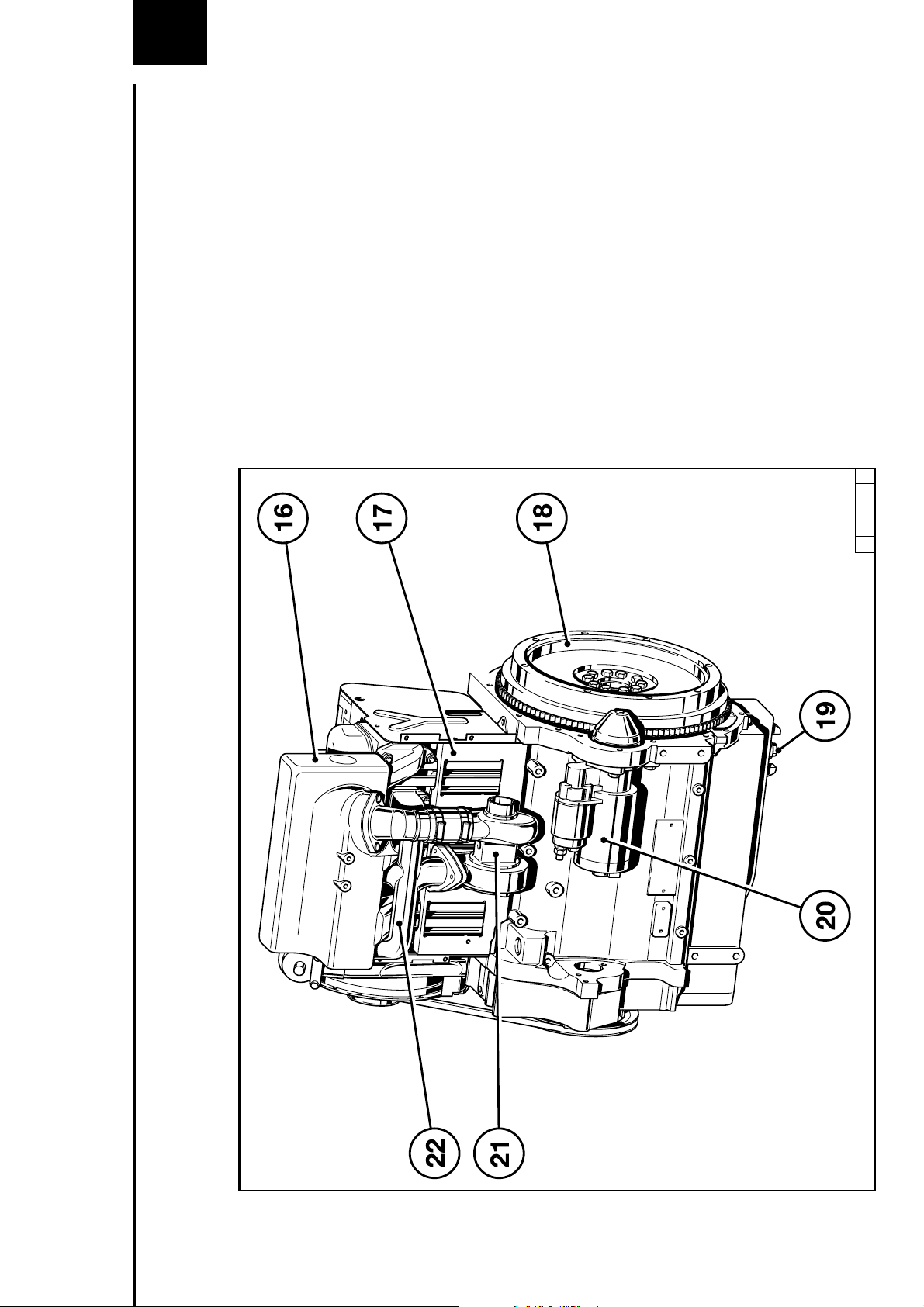
2
16 Air-intake line
17 Shielding plate
18 Flywheel
19 Oil drain screw
20 Starter
21 Exhaust turbocharger manifold
© 2001
© 34 576 0
BF3L 914
2.2 Engine Illustrations Engine Description
2.2.2 Exhaust side
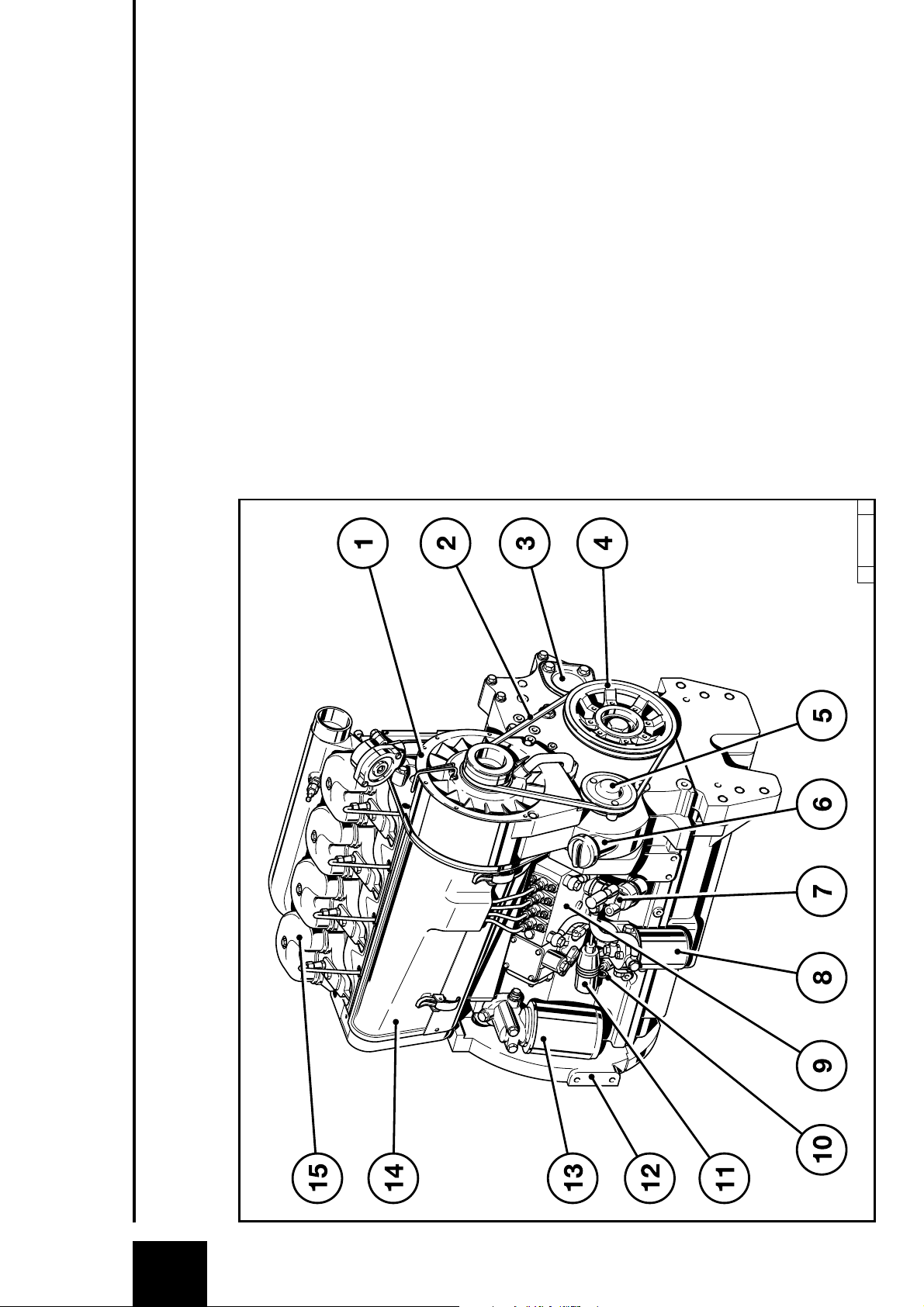
1 Cooling fan
2 V-Belts (fan)
3 Optional attachment of hydraulic pumps
4 V-belt washer
5 Tension roller
6 Oil filler neck
7 Fuel pump
8 Fuel change filter
9 Injection pump
11 Shut-off magnet
10 Oil dipstick
12 SAE housing
13 Lube oil filter
14 Air duct hood
15 Cylinder head cove
© 34 597 0
F4L 914
Engine Description 2.2 Engine Illustrations
2.2.3 Operation side
2
© 2001
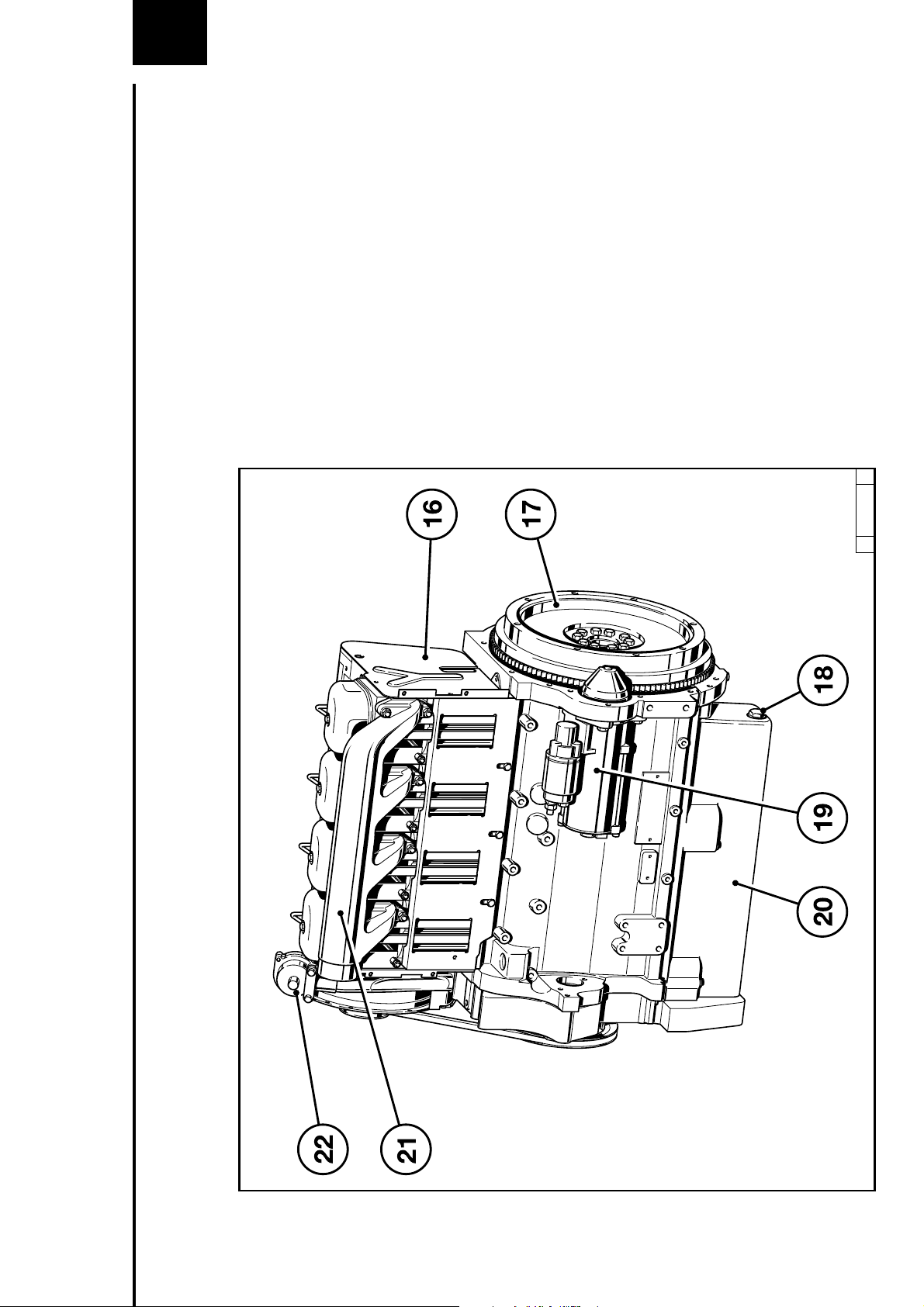
2
16 Date plate
17 Flywheel
18 Oil drain screw
19 Starter
20 Oil pan
21 Air-intake manifold
22 Crankcase ventilation
© 2001
© 34 576 0
F4L 914
2.2 Engine Illustrations Engine Description
2.2.4 Exhaust side

1 Cooling fan
2 V-Belts (fan)
3 V-belt pulley on crankshaft
4 Tension roller
5 Oil filler neck
6 Oil drain screw
7 Fuel pump with fuel precleaning
8 Fuel filter cartridge
9 Injection pump
11 Oil dipstick
10 Shut-off lifting magnet
12 LDA
13 Lube oil filter cartridge
14 Engine oil cooler
15 Air duct hood
16 Cylinder head cover
© 34 577 0
BF6L 914 C- intercooler over air-intake line
2.2 Engine Illustrations Engine Description
2.2.5 Operation side
2
© 2001
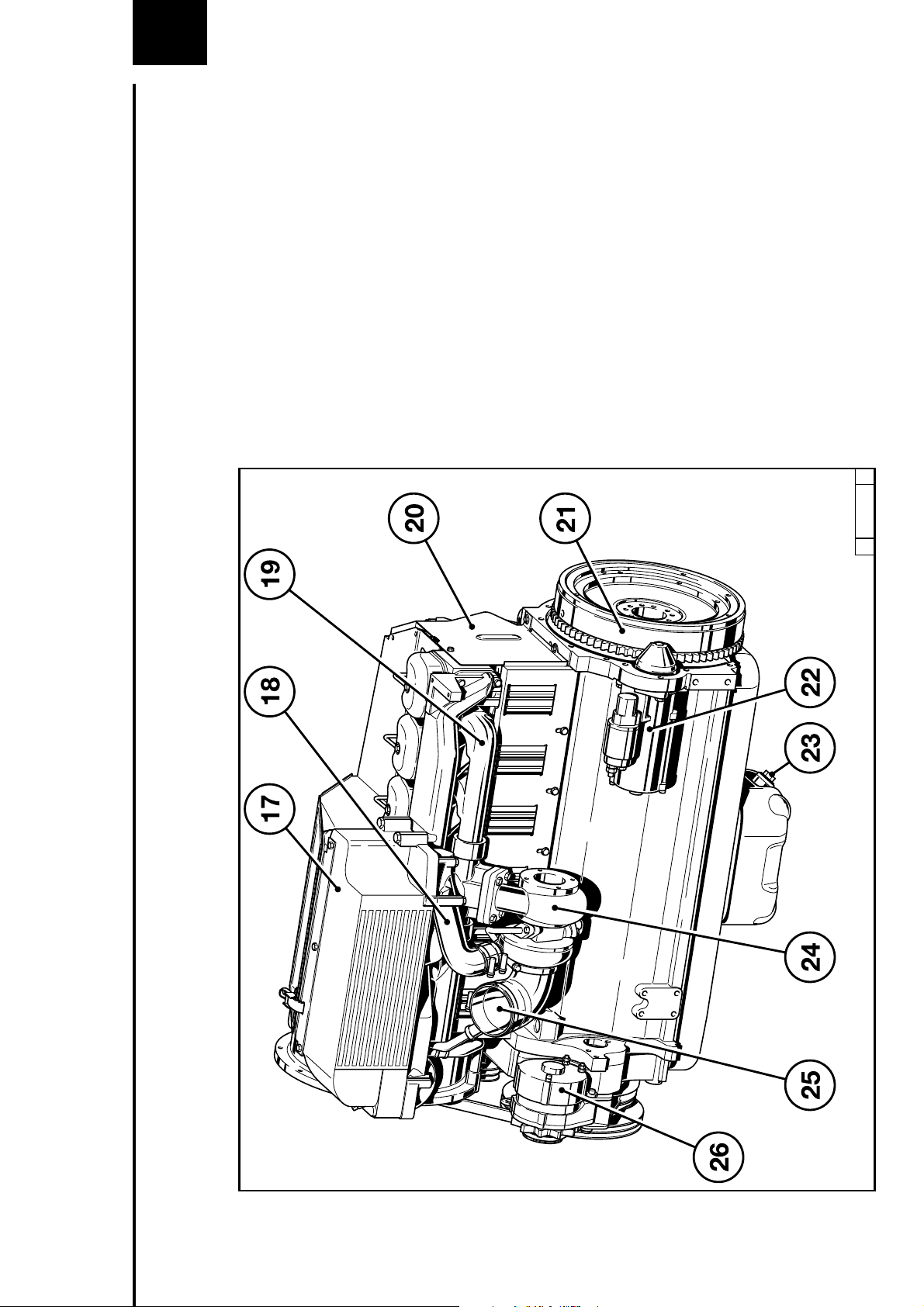
2
17 Intercooler
18 Air-intake line
19 Exhaust manifold line
20 Date plate
21 Flywheel
22 Starter
23 Oil drain screw
24 Turbocharger
25 Air-intake manifold to exhaust turbocharger
26 Alternator
© 2001
© 34 578 0
BF6L 914 C- intercooler over air-intake line
2.2 Engine Illustrations Engine Description
2.2.6 Exhaust side
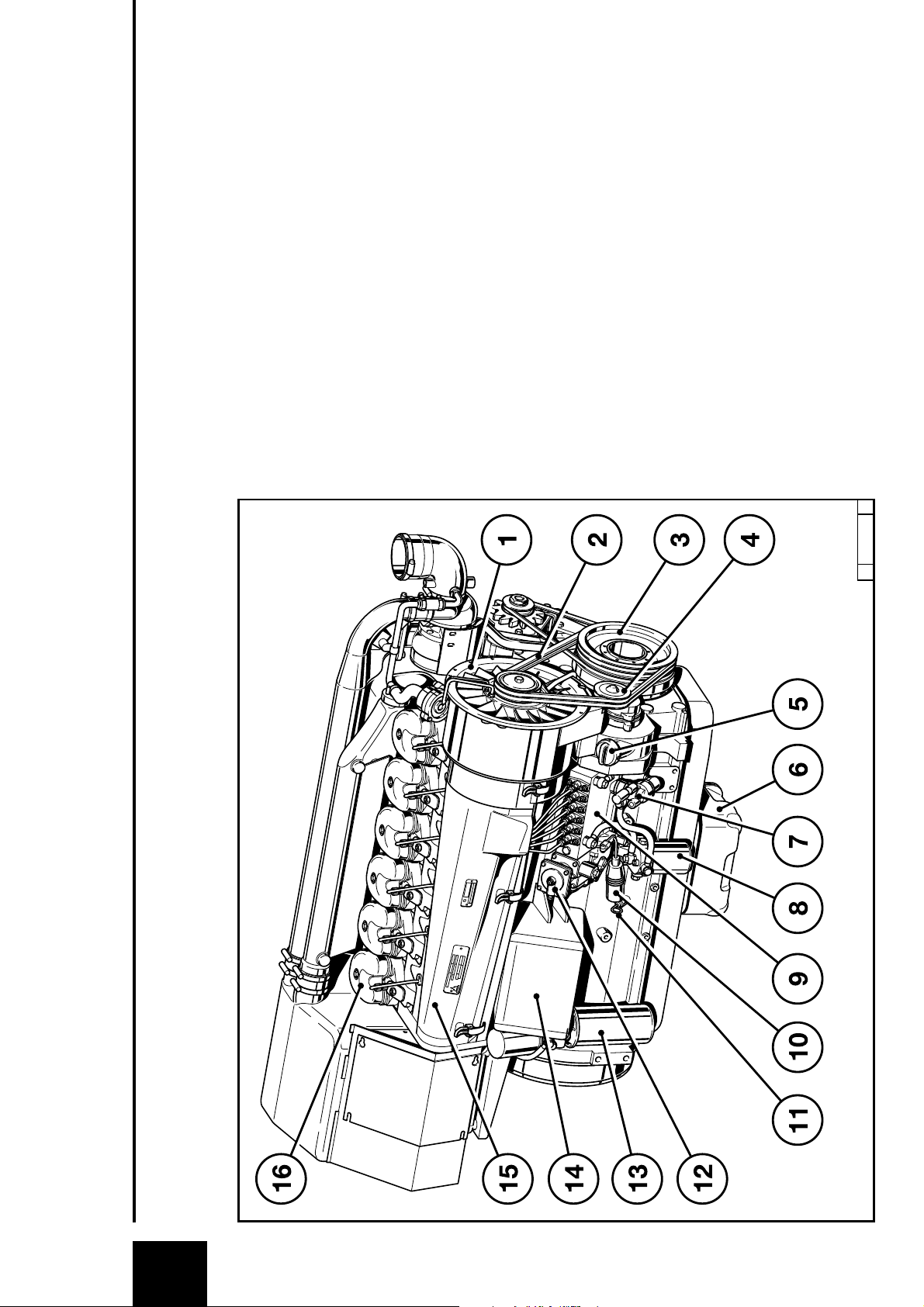
1 Cooling fan
2 V-Belts (fan)
3 V-belt pulley on crankshaft
4 Tension roller
5 Oil filler neck
6 Oil drain screw
7 Fuel pump with fuel precleaning
8 Fuel filter cartridge
9 Injection pump
11 Oil dipstick
10 Shut-off lifting magnet
12 LDA
13 Lube oil filter cartridge
14 Engine oil cooler
15 Air duct hood
16 Cylinder head cover
© 35 579 0
BF6L 914 C- intercooler over flywheel
Engine Description 2.2 Engine Illustrations
2.2.7 Operation side
2
© 2001
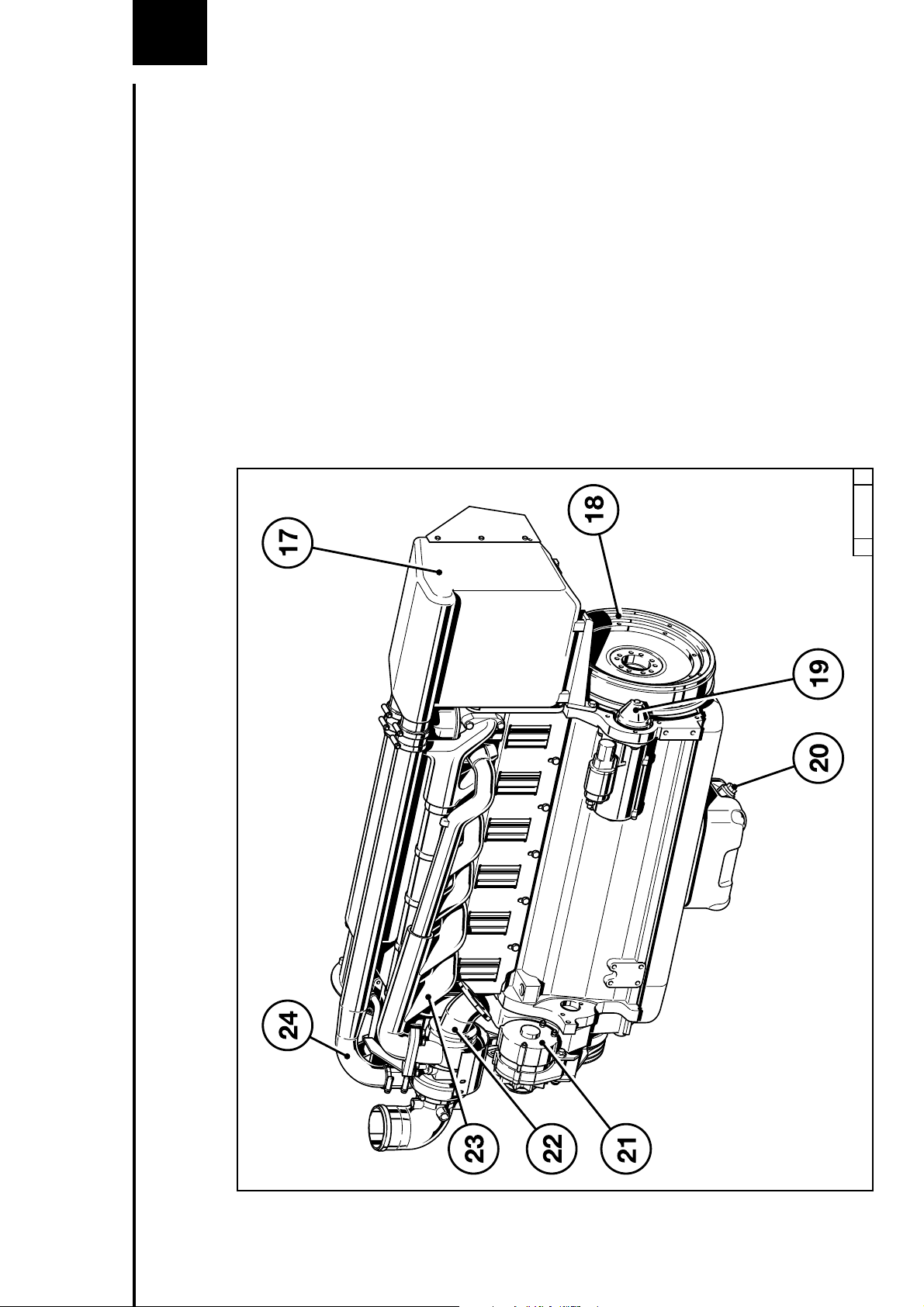
2
17 Intercooler
18 Flywheel
19 Starter
20 Oil drain screw
21 Alternator
22 Exhaust connection supports
23 Exhaust manifold line
24 Air-intake manifold to exhaust turbocharger
© 2001
© 34 580 0
BF6L 914 - intercooler over flywheel
2.2 Engine Illustrations Engine Description
2.2.8 Exhaust side
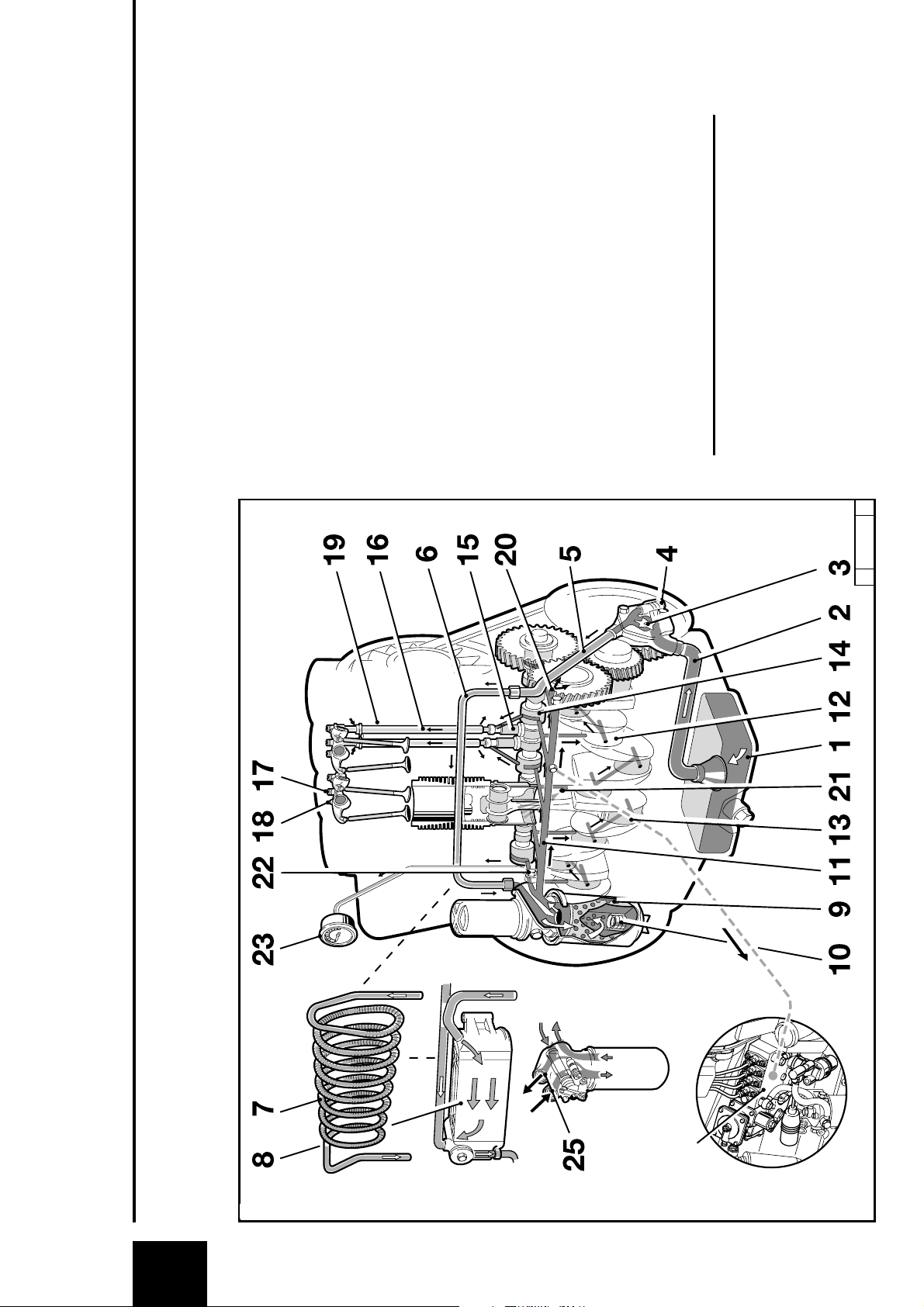
1 Oil pan
2 Intake manifold
3 Oil pump
4 Oil pressure regulating valve
5 Pressure oil line
rocker arm)
6 Short-circuit line or alternative
7 Ribbed tube coil or alternative
8 Block oil cooler
9 Lube oil filter
11 Main oil channel
10 Safety valve
12 Crankshaft bearing
13 Con-rod bearing
14 Camshaft bearing
15 Tappet
16 Pushrod (hollow, for oil intake to lubricate
17 Rocker arm bearings
schematic
18 Rocker arm lubrication
19 Pushrod protective tube
20 Throttle bore (to lubricate cogwheels)
21 Spray nozzle for piston cooling
22 Connection for oil pressure gauge
23 Oil pressure gauge
24 Injection pump connected to lube oil circuit
Please contact DEUTZ Service when
changing-over.
25 Connection option for oil heater **
** here the filter carrier must be exchanged.
© 34 581 0
FL 914
Engine Description 2.3 Lube Oil Circuit Schematic
2.3.1 Lube Oil Circuit Schematic
2
24
© 2001
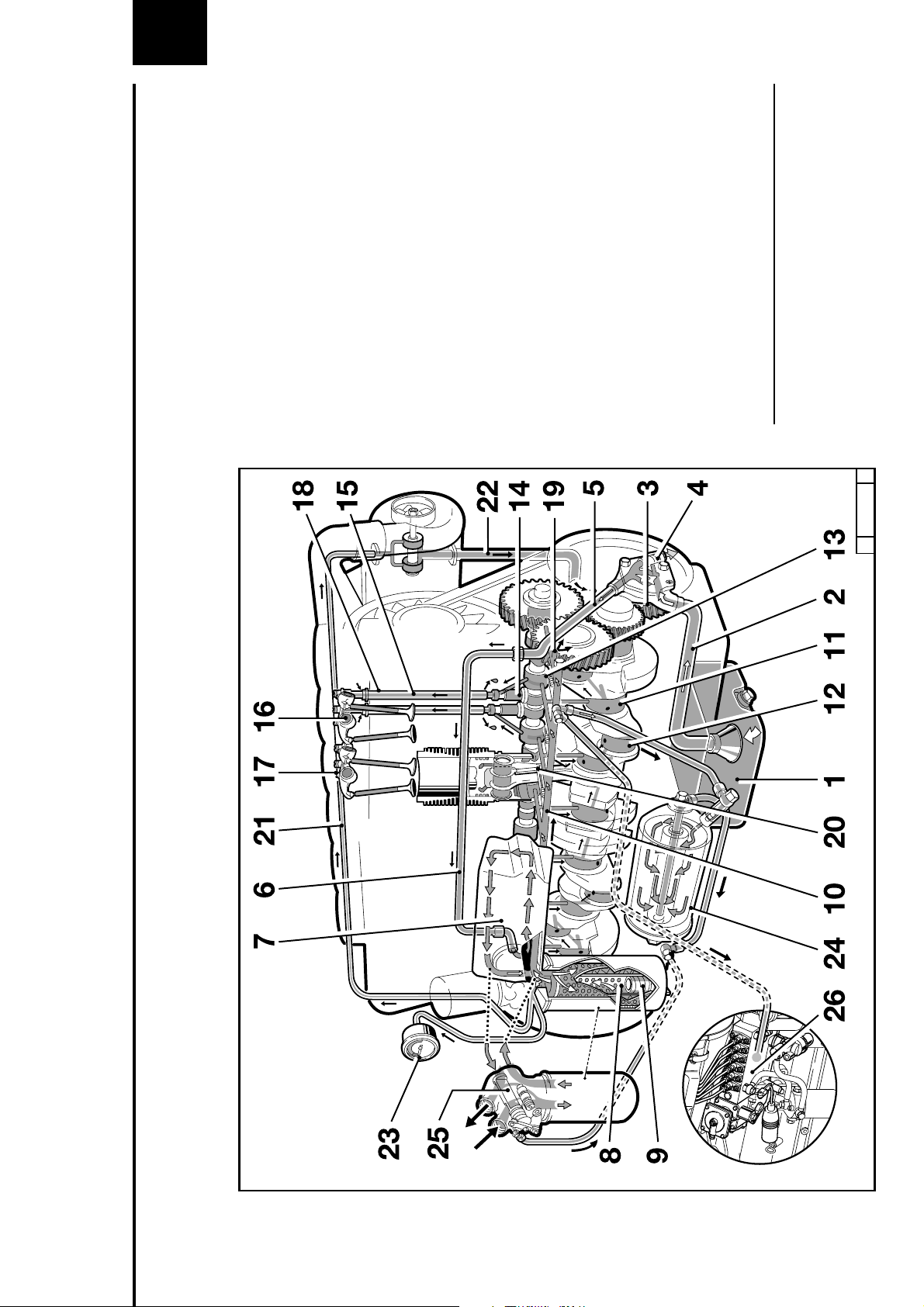
2
1 Oil pan
2 Intake line
3 Oil pump
arm)
4 Oil pressure regulating valve
5 Pressure oil line
6 Connection line to oil cooler
7 Block oil cooler
8 Lube oil filter
9 Safety valve
11 Crankshaft bearing
10 Main oil channel
12 Con-rod bearing
13 Camshaft bearing
14 Tappet (with impulse lubrication of rocker
rocker arm)
15 Pushrod (hollow, for oil intake to lubricate
16 Rocker arm bearings
cylinder head to crankcase)
17 Rocker arm lubrication
18 Pushrod protective tube (oil return from the
19 Throttle bore (to lubricate cogwheels)
© 2001
to crankcase
20 Spray nozzle for piston cooling
21 Oil line to lubricate turbocharger
22 Oil return line from exhaust turbocharger
23 Oil pressure gauge
24 Bypass lube oil fine filter
schematic
Please contact DEUTZ Service when
changing-over.
25 Connection option for oil heater **
26 Injection pump connected to lube oil circuit
** here the filter carrier must be exchanged.
© 35 583 0
BFL 914
2.3 Lube Oil Circuit Schematic Engine Description
2.3.2 Lube Oil Circuit Schematic
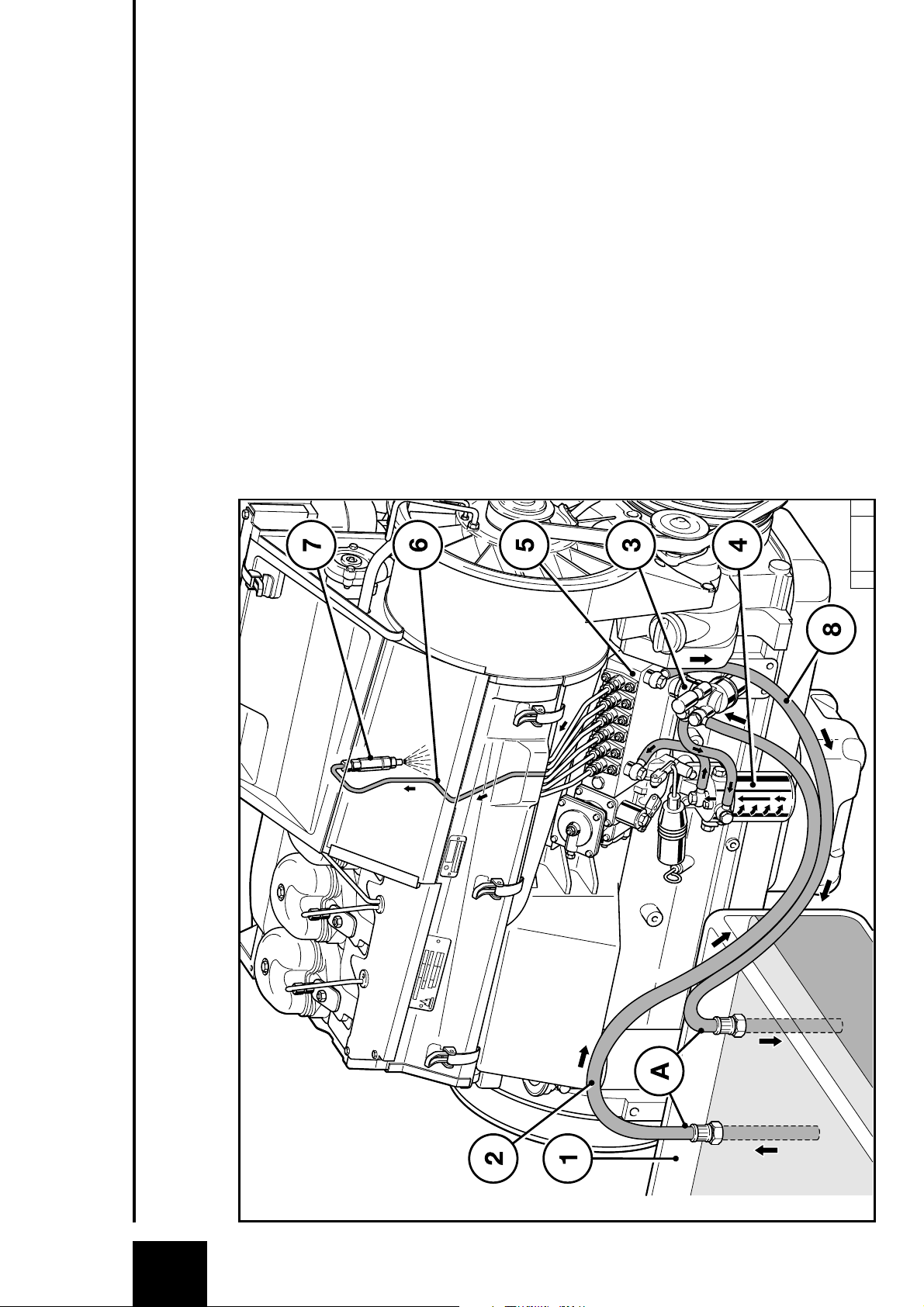
each other as possible
1 Fuel tank
2 Fuel line from tank to fuel pump
3 Fuel pump
4 Fuel change filter
5 Injection pump
6 Injection line
7 Injection valve
8 Fuel overflow pipe
A Distance: must be routed as far away from
© 35 582 0
Engine Description 2.4 Fuel System Schematic
2.4.1 Fuel System
2
© 2001
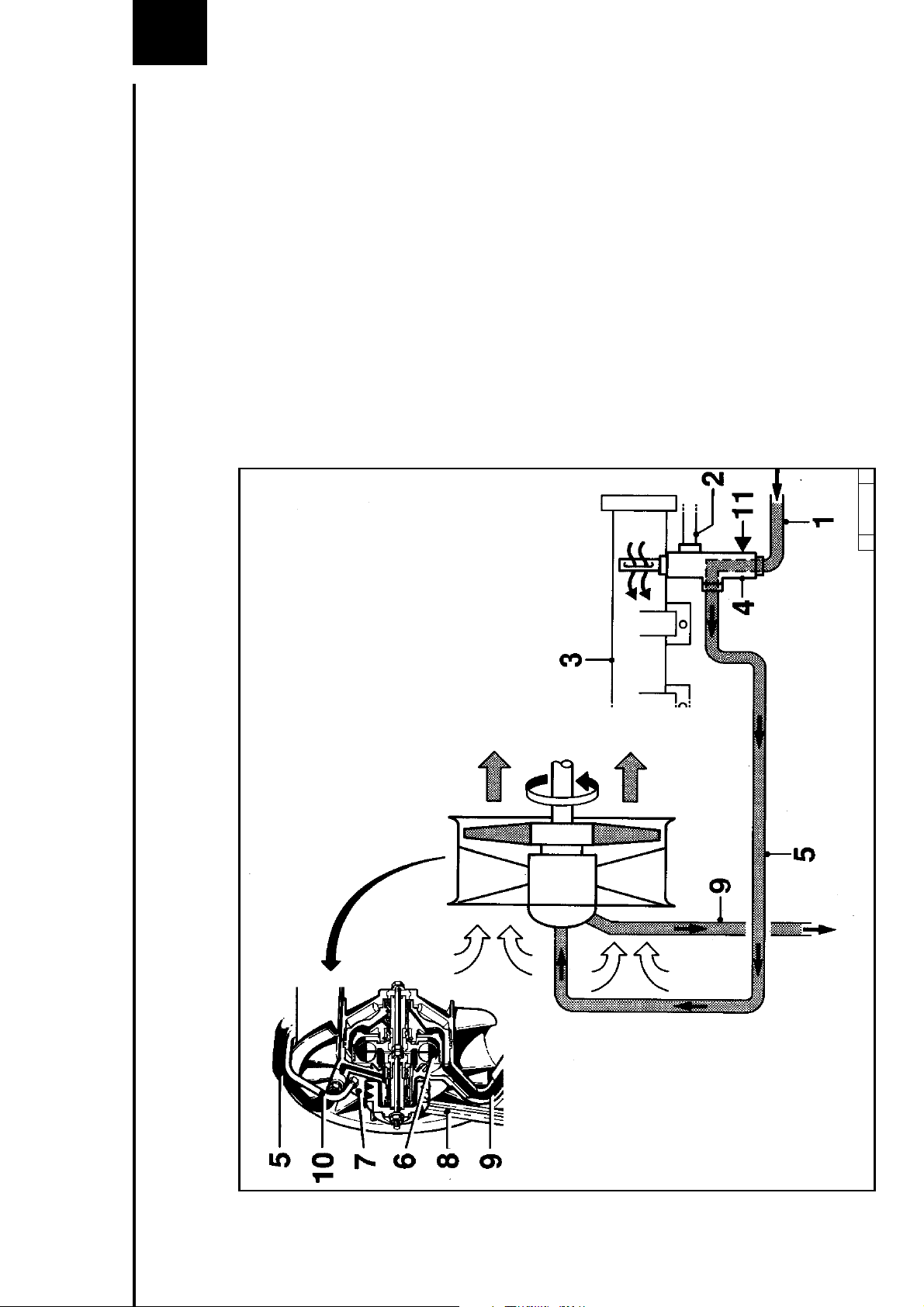
2
thermostat
1 Pressure oil line from engine to exhaust
2 Air line to exhaust thermostat
3 Exhaust manifold line
4 Exhaust thermostat
5 Control line to hydraulic coupling
6 Hydraulic coupling
7 Cooling fan
8 Cooling fan drive
9 Oil return line to crankcase
10 Ventilation line
11 Adjusting screw with special seal ring
© 2001
© 26 120 1
2.5 Engine cooling Engine Description
2.5.1 Amount of cool air regulated by exhaust thermostat
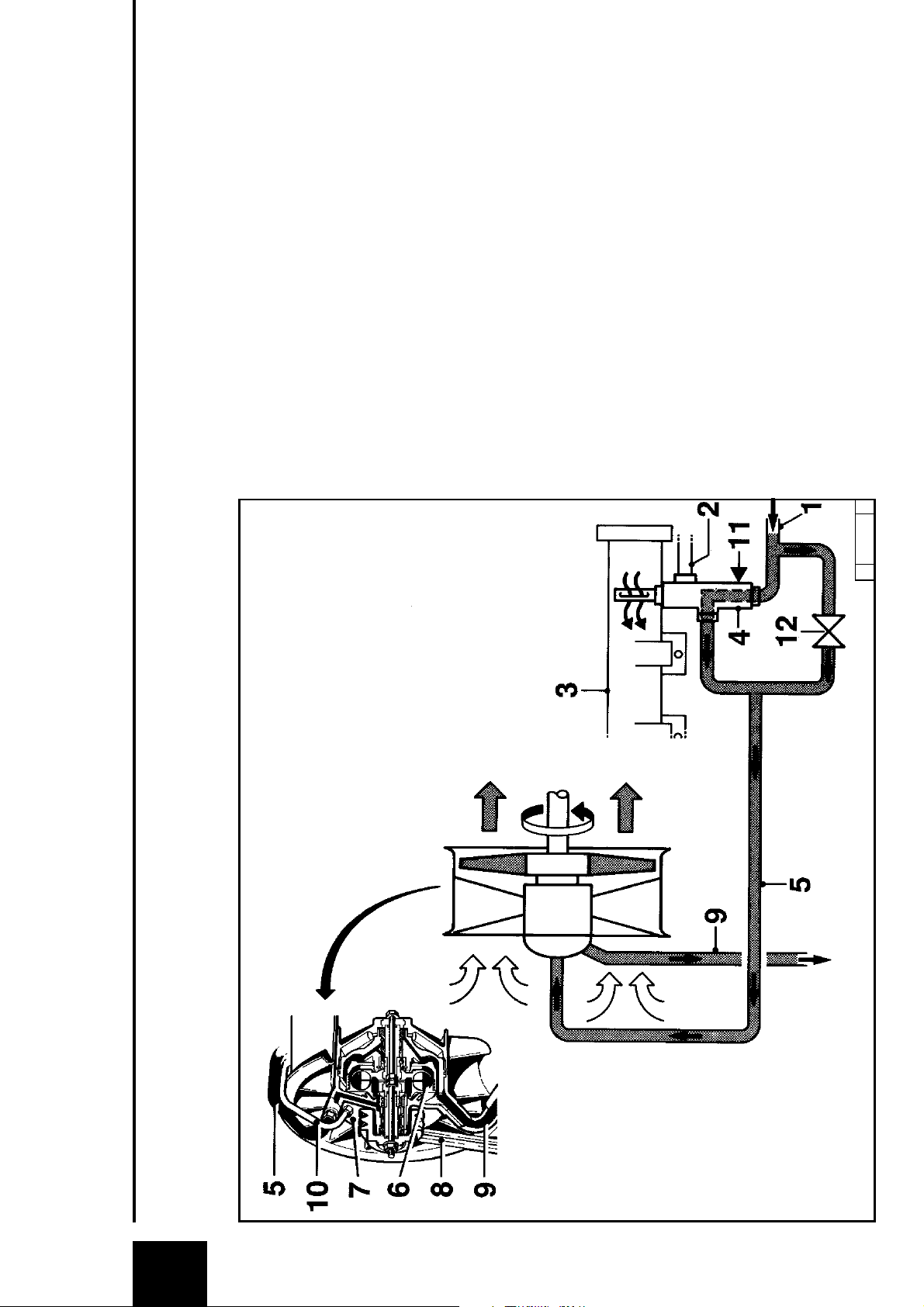
thermostat
1 Pressure oil line from engine to exhaust
2 Air line to exhaust thermostat
3 Exhaust manifold line
4 Exhaust thermostat
5 Control line to hydraulic coupling
6 Hydraulic coupling
7 Cooling fan
8 Cooling fan drive
9 Oil return line to crankcase
11 Adjusting screw with special seal ring
10 Ventilation line
12 Solenoid valve
© 26 121 2
2.5.2 Amount of cool air regulated by exhaust thermostat and soleno-
Engine Description 2.5 Engine cooling
id valve
2
© 2001
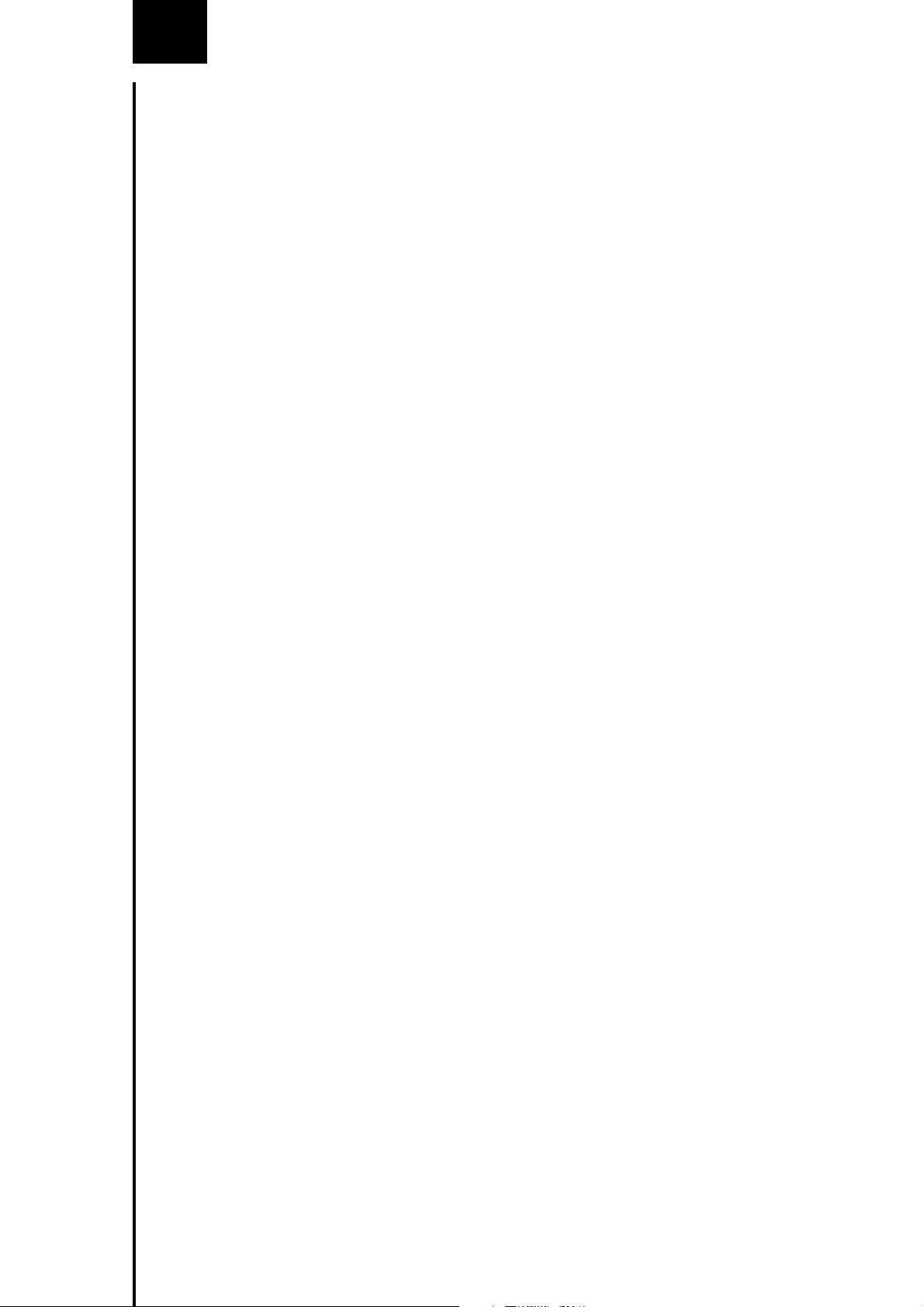
3
Engine Operation
© 2001
3.1 Commissioning
3.2 Starting
3.3 Monitoring Operation
3.4 Shutting off
3.5 Operating Conditions
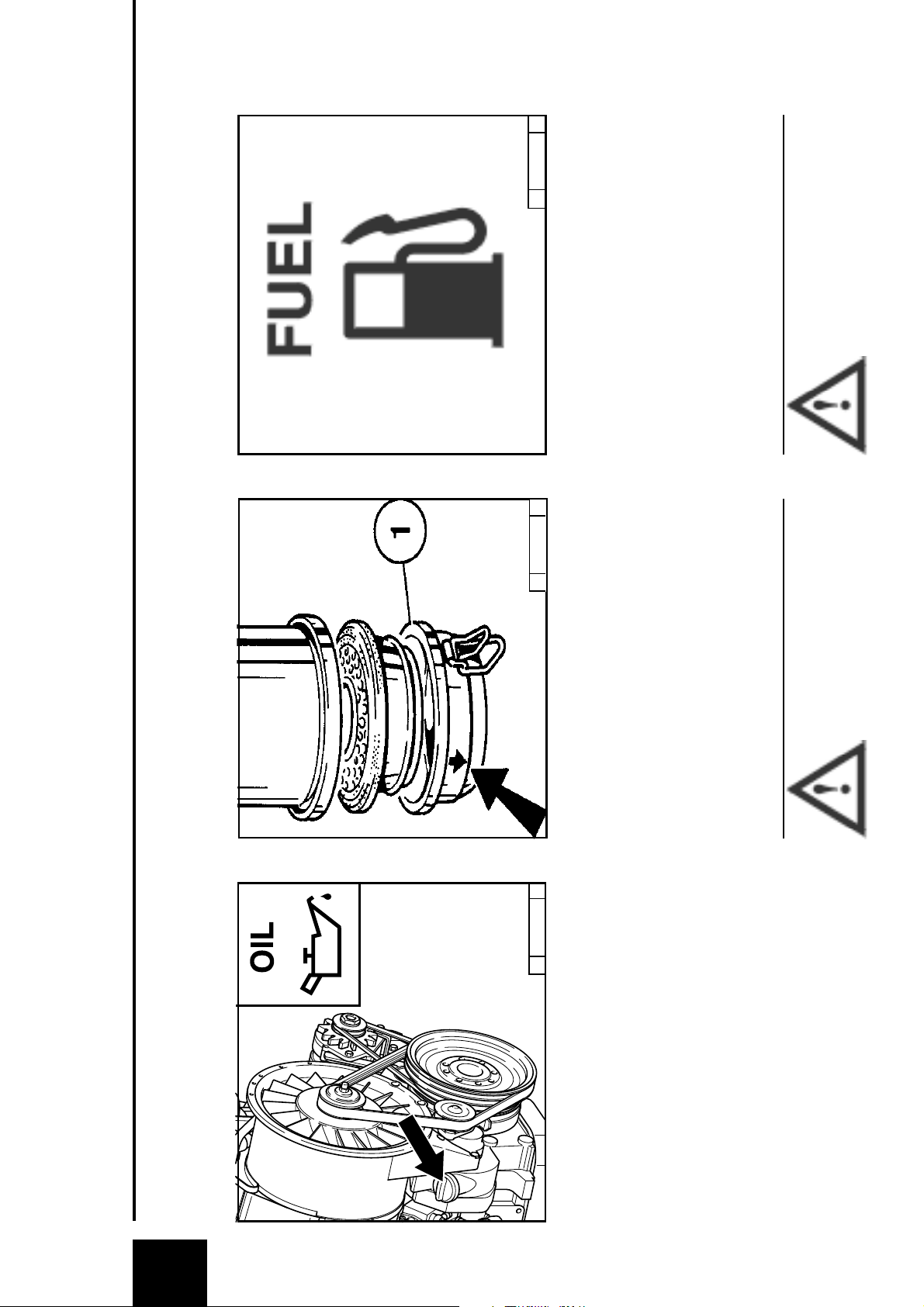
© 26 398 0
Never fill the tank while the en-
gine is running.
Ensure cleanliness!
Do not spill fuel!
3.1.3 Pour in Fuel
Engine Oil
Use only commercial-grade diesel fuel. For
© 24 980 2
Fill oil cup 1 of the oil bath air cleaner with oil
fuel grade, see 4.2. Use summer or winter-
grade fuel, depending on the ambient tempera-
ture.
Do not fill the precleaner dust
collector (if fitted) with oil.
up to the arrow.
For oil grade and viscosity, see 4.1.
Engine Operation 3.1 Commissioning
3.1.1 Pour in Engine Oil 3.1.2 Oil Bath Air Filter with
3
© 35 201 0
As a rule, engines are delivered without oil.
Pour lube oil into the oil filler neck (arrow).
For oil grade and viscosity, see 4.1.
© 2001