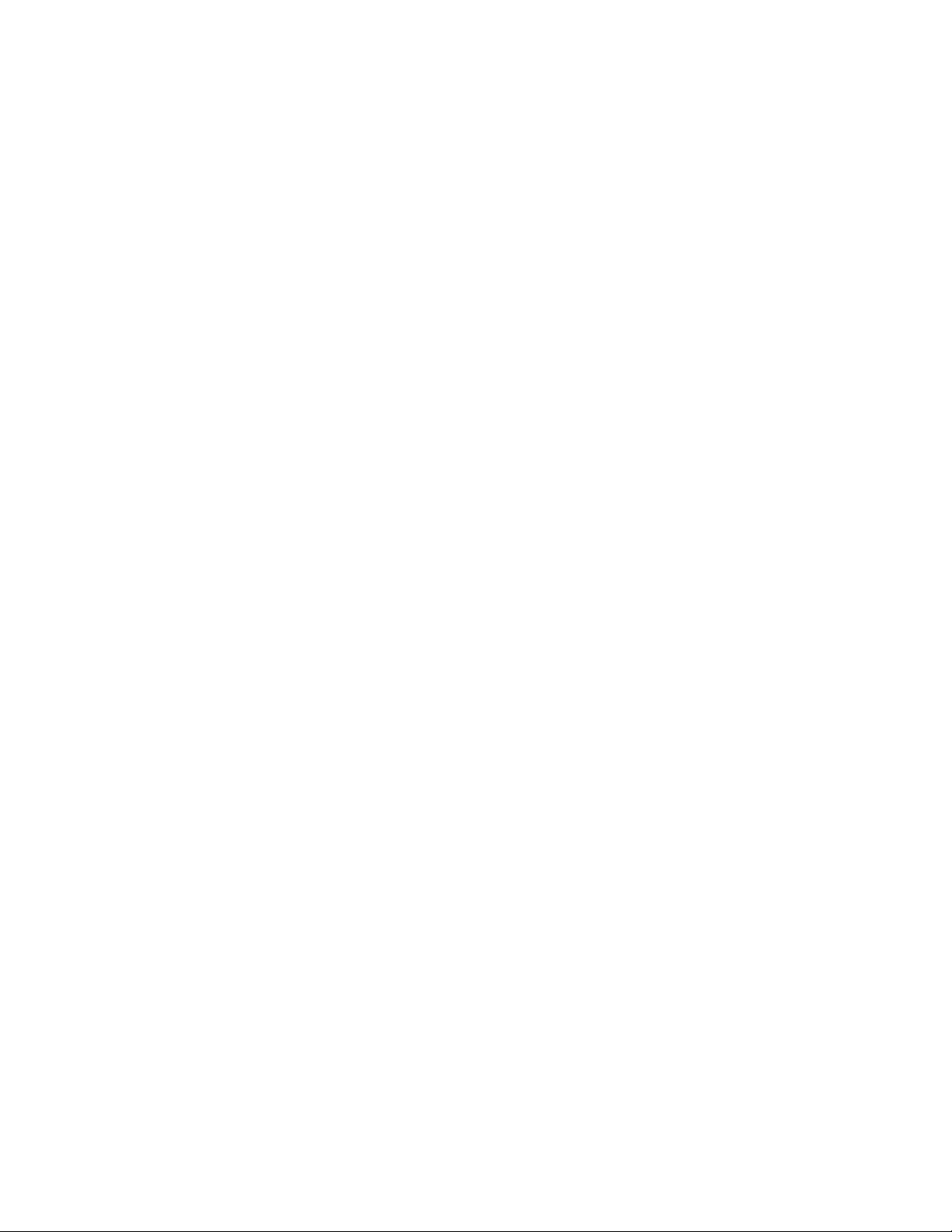
From the library of: Superior Sewing Machine & Supply LLC
CATAL
OG
NO.
129M
Fif
th
E
dition
CL
A
SSES
56
200
56300
56400
56500
56700
56900
®
Finest
Quality
Adjusting instructions and
illustrated parts list
,
..
,
u
Series
500
00 - Advan ced,
hig
h
spe
ed
, f
la
t b
ed
m
ac
hin
es
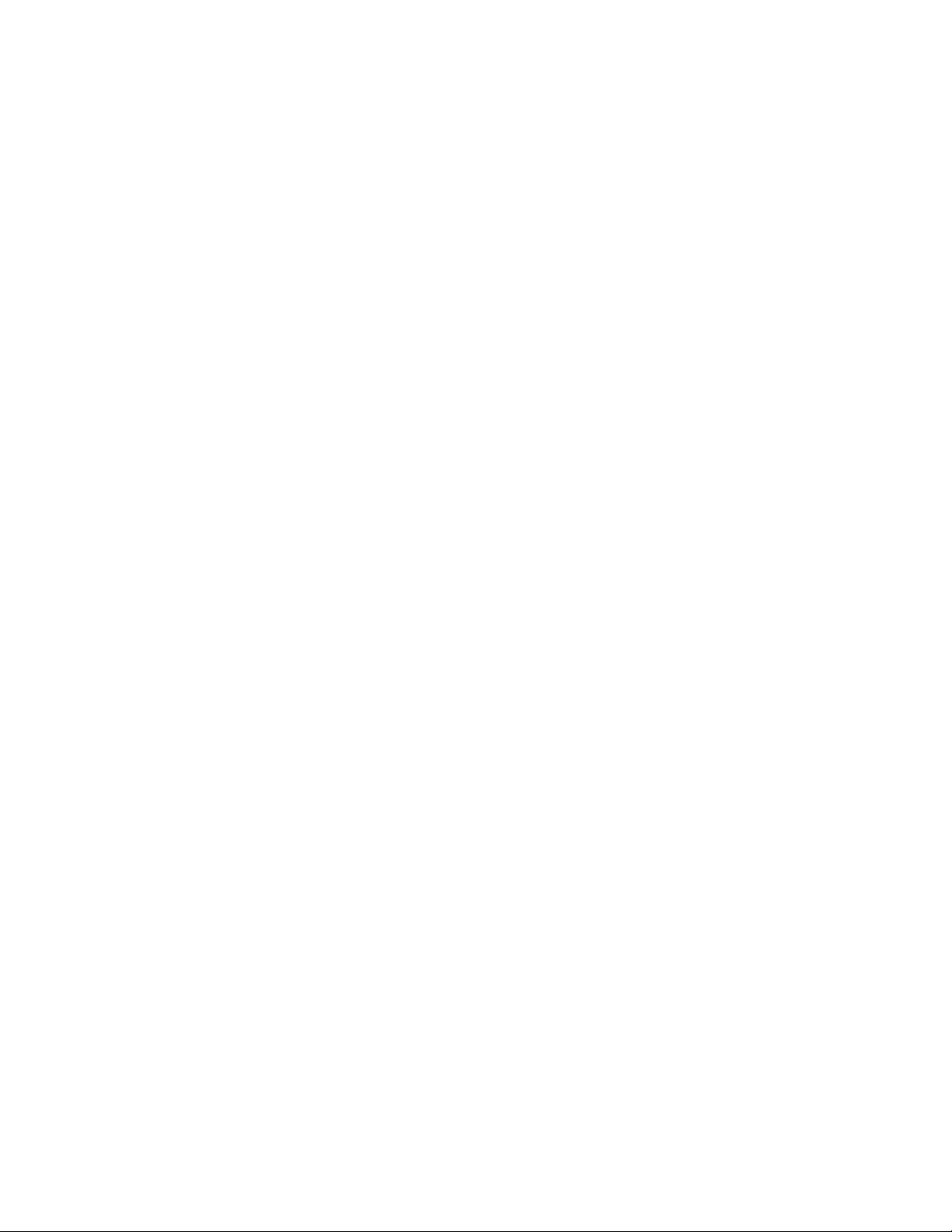
From the library of: Superior Sewing Machine & Supply LLC
56200
H
56200
K
56200
L
56200
R
56200
S
56200
W
56300
E
56300
F
56300
G
56300
H
56300
M
56300
N
CATALOG
NO.
129
M
ADJUSTING
INSTRUCTIONS
AND
ILLUSTRATED
PARTS
LIST
FOR
SERIES
50000
ADVANCED,
HIGH
SPEED
FLAT
BED
MACHINES
STYLES
56300
R
56300
U
56300
W
56300
X
56300
AH
56300
AL
56400
D
56400
P
56400
R
56400
S
56400
T
56400
W
Fifth Edition
©1965,
1982
By
Union
Special Corporation
Rights Reserved in
All
Countries
Printed in
U.S.A.
March,
1982
2
56400
X
56500
A
56500
B
56500
C
56500
J
56500
R
56500
U
56700
J
56900
H
56900
J
56900
P
56900
R
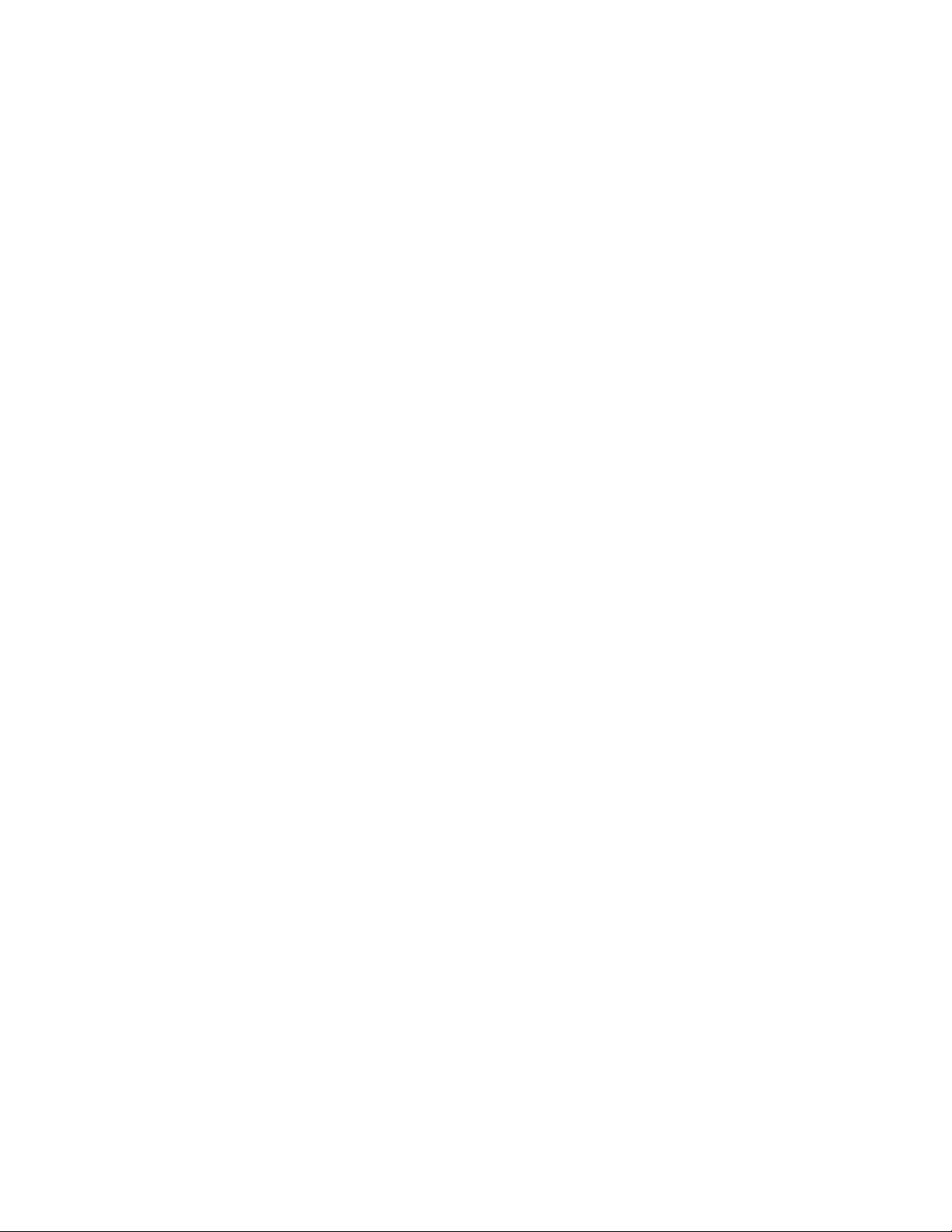
From the library of: Superior Sewing Machine & Supply LLC
IDENTIFICATION
OF
MACHINES
Each
UNION
SPECIAL
machine
carries
a Style
number,
which
on
these Classes of
mach-
ines,
is
stamped
into the
style
plate
affixed to the
right
front of
machine.
The
serial
number
is
stamped
in the casting
at
the
right
rear base of
machine.
CLASS
DESCRIPTION
(56200)
Advanced
high
speed,
low
or
medium
throw,
flat
bed
machines. Single needle, one
looper,
enclosed automatic lubricating system.
Maximum
reconmended
speed
6500
R.P.M.
Maximum
work
space to
right
of needle bar 8 1/4 inches
(209.6mm).
MACHINE
STYLES
56200
H
Low
throw
machine.
Typical application -
For
miscellaneous
seaming
oper-
ations
on
light
to
medium
weight
wash
and
wear
materials
where
chaining
and
a short
stitch
are required.
Seam
specification
401
SSa-1.
Type
101
GS
needle.
56200
K
Low
throw
machine. Typical application -
For
binding aprons
and
dresses
made
with
light
to
medium
weight materials.
Seam
specification
401
BSc-1.
Type
106
GLS
needle.
Uses
cut
edge
binding 3/4, 7/8,
1,
l
1/8,
1 1/4 inch
(19.0, 22.2, 25.4, 28.6,
31.8nm)
wide
and
produces a 7/32, 1/4, 9/32,
11/32, 13/32 inch (5.6,
6.4,
7.1,
8.7,
10.3mm)
finish,
respectively.
#56200
L
Medium
throw
machine.
Typical application -
For
binding mattress
ticks
made
with
medium
to
medium
heavy
weight materials.
Seam
specification
401
BSa-1.
Type
126
GS
needle.
Uses
selvage
edge
binding 5/8, 3/4, 7/8
inch (15.9, 19.0,
22.2mm)
wide
and
produces a 5/16, 3/8,
7/16
inch
(7.9,
9.5,
11.1mm)
finish,
respectively.
*56200
R
Low
throw
machine.
Typical application -
For
joining shoulders of
shirts
in
one
operation
made
with
light
to
medium
weight materials.
Seam
specifi-
cation
401
LSe-1.
Type
106
GLS
needle.
56200
S
Low
throw
machine.
Typical application -
For
miscellaneous operations
on
woven
materials, knitted drawer bands, knitted
shirt
fronts
made
with
light
to
medium
weight materials.
Seam
specification
401
SSa-1.
Type
108
GHS
needle.
56200
W
Medium
throw
machine.
Typical application -
For
seaming
cotton flannel
and
leather
palm
gloves.
Seam
specification
401
SSa-1.
Type
128
GAS
needle.
CLASS
DESCRIPTION
(56300)
Advanced
high
speed,
medium
or
high
throw,
flat
bed
machines. Single needle,
one
looper, enclosed automatic lubricating system.
Maximum
work
space to
right
of needle
bar 8
1/4
inches
(209.6mm).
#Discontinued -
Replaced
by
Style
56300
M.
*Discontinued -
In
most
instances, replacement parts are available.
3
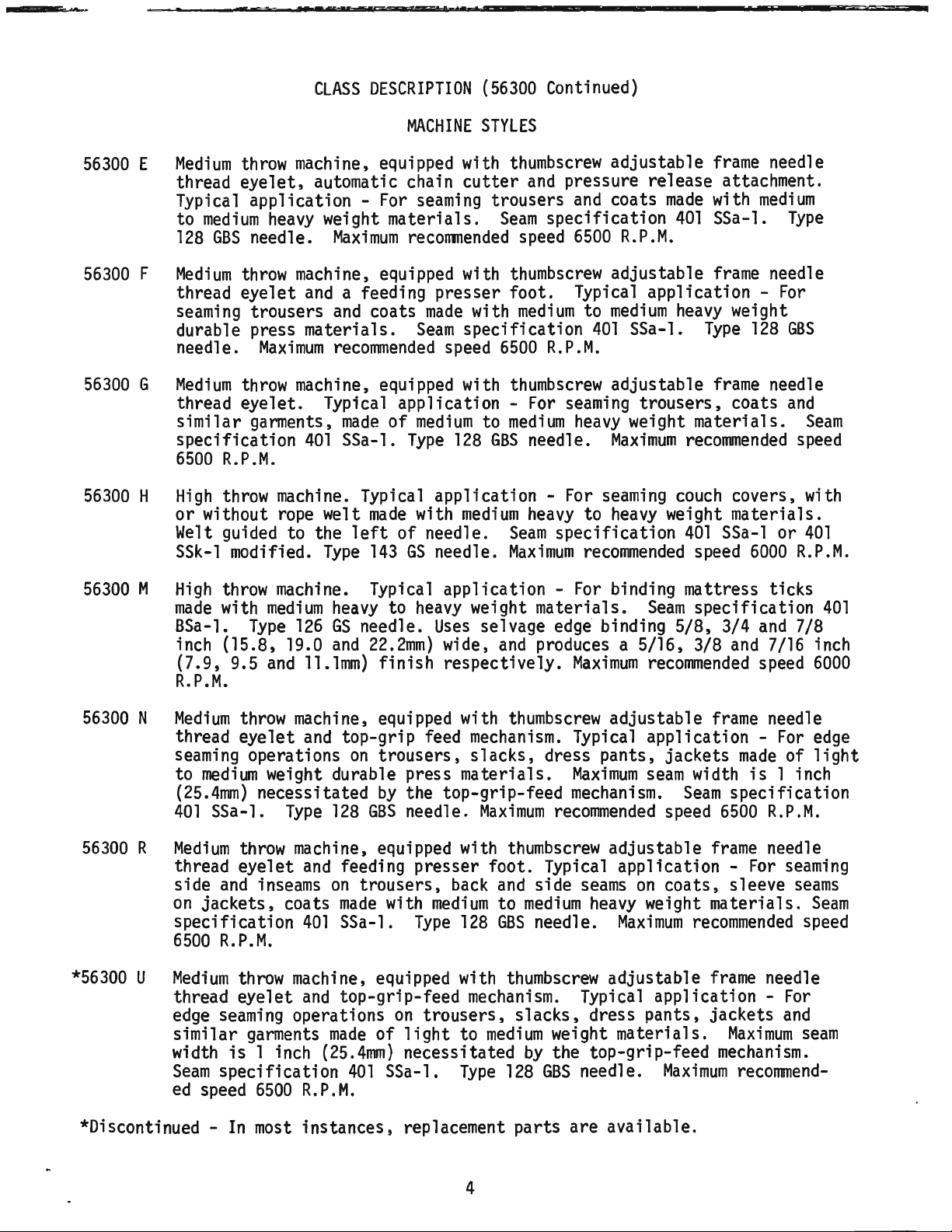
From the library of: Superior Sewing Machine & Supply LLC
CLASS
DESCRIPTION
(56300
Continued)
MACHINE
STYLES
56300
E
Medium
throw
machine, equipped with
thumbscrew
adjustable
frame
needle
thread
eyelet,
automatic chain
cutter
and
pressure release attachment.
Typical application -
For
seaming
trousers
and
coats
made
with
medium
to
medium
heavy
weight materials.
Seam
specification
401
SSa-1.
Type
128
GBS
needle.
Maximum
reconmended
speed
6500
R.P.M.
56300
F
Medium
throw
machine, equipped with
thumbscrew
adjustable
frame
needle
thread
eyelet
and
a feeding presser foot. Typical application -
For
seaming
trousers
and
coats
made
with
medium
to
medium
heavy
weight
durable press materials.
Seam
specification
401
SSa-1.
Type
128
GBS
needle.
Maximum
recommended
speed
6500
R.P.M.
56300
G
Medium
throw
machine, equipped with
thumbscrew
adjustable
frame
needle
thread
eyelet.
Typical application -
For
seaming
trousers,
coats
and
similar
garments,
made
of
medium
to
medium
heavy
weight materials.
Seam
specification
401
SSa-1.
Type
128
GBS
needle.
Maximum
recommended
speed
6500
R.P.M.
56300
H
High
throw
machine. Typical application -
For
seaming
couch
covers, with
or
without
rope
welt
made
with
medium
heavy
to
heavy
weight materials.
Welt
guided to the
left
of
needle.
Seam
specification
401
SSa-1
or
401
SSk-1
modified.
Type
143
GS
needle.
Maximum
recommended
speed
6000
R.P.M.
56300
M
High
throw
machine. Typical application -
For
binding mattress ticks
made
with
medium
heavy
to
heavy
weight materials.
Seam
specification
401
BSa-1.
Type
126
GS
needle.
Uses
selvage edge binding 5/8, 3/4
and
7/8
inch (15.8, 19.0
and
22.2mm)
wide,
and
produces a 5/16, 3/8
and
7/16
inch
(7.9, 9.5
and
11.1mm)
finish
respectively.
Maximum
recommended
speed
6000
R.P.M.
56300
N
Medium
throw
machine, equipped with
thumbscrew
adjustable
frame
needle
thread
eyelet
and
top-grip feed
mechanism.
Typical application -
For
edge
seaming
operations
on
trousers,
slacks,
dress pants, jackets
made
of
light
to
medium
weight durable press materials.
Maximum
seam
width
isl
inch
(25.4mm)
necessitated
by
the top-grip-feed
mechanism.
Seam
specification
401
SSa-1.
Type
128
GBS
needle.
Maximum
recommended
speed
6500
R.P.M.
56300
R
Medium
throw
machine, equipped with
thumbscrew
adjustable
frame
needle
thread
eyelet
and
feeding presser foot. Typical application -
For
seaming
side
and
inseams
on
trousers,
back
and
side
seams
on
coats,
sleeve
seams
on
jackets,
coats
made
with
medium
to
medium
heavy
weight materials.
Seam
specification
401
SSa-1.
Type
128
GBS
needle.
Maximum
recommended
speed
6500
R.P.M.
*56300
U
Medium
throw
machine, equipped with
thumbscrew
adjustable
frame
needle
thread
eyelet
and
top-grip-feed
mechanism.
Typical application -
For
edge
seaming
operations
on
trousers,
slacks,
dress pants, jackets
and
similar
garments
made
of
light
to
medium
weight materials.
Maximum
seam
width
isl
inch
(25.4mm)
necessitated
by
the top-grip-feed
mechanism.
Seam
specification
401
SSa-1.
Type
128
GBS
needle.
Maximum
recommend-
ed
speed
6500
R.P.M.
*Discontinued -
In
most
instances, replacement parts
are
available.
4
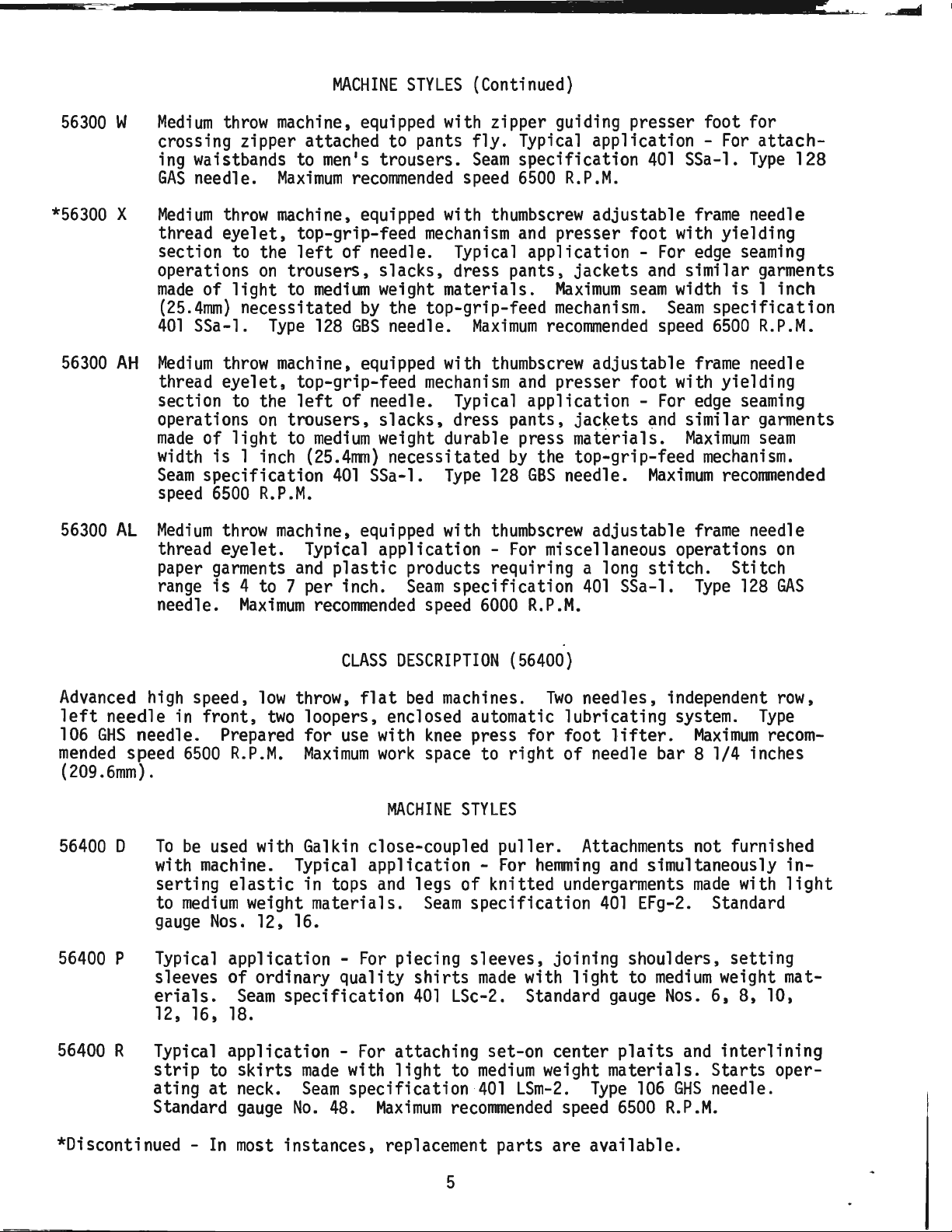
From the library of: Superior Sewing Machine & Supply LLC
MACHINE
STYLES
(Continued)
56300
W
Medium
throw
machine, equipped with zipper guiding presser foot for
crossing zipper attached to pants
fly.
Typical application -
For
attach-
ing waistbands to men's trousers.
Seam
specification
401
SSa-1.
Type
128
GAS
needle.
Maximum
recommended
speed
6500
R.P.M.
*56300
X
Medium
throw
machine, equipped with
thumbscrew
adjustable
frame
needle
thread
eyelet,
top-grip-feed
mechanism
and
presser foot with yielding
section to the
left
of needle. Typical application -
For
edge
seaming
operations
on
trousers, slacks, dress pants, jackets
and
similar garments
made
of
light
to
medium
weight materials.
Maximum
seam
width
isl
inch
(25.4mm)
necessitated
by
the top-grip-feed
mechanism.
Seam
specification
401
SSa-1.
Type
128
GBS
needle.
Maximum
recommended
speed
6500
R.P.M.
56300
AH
Medium
throw
machine, equipped with
thumbscrew
adjustable
frame
needle
thread
eyelet,
top-grip-feed
mechanism
and
presser foot with yielding
section to the
left
of needle. Typical application -
For
edge
seaming
operations
on
trousers, slacks, dress pants, jackets
~nd
similar garments
made
of
light
to
medium
weight durable press materials.
Maximum
seam
width
isl
inch
(25.4mm)
necessitated
by
the top-grip-feed
mechanism.
Seam
specification
401
SSa-1.
Type
128
GBS
needle.
Maximum
recommended
speed
6500
R.P.M.
56300
AL
Medium
throw
machine, equipped with
thumbscrew
adjustable
frame
needle
thread eyelet. Typical application -
For
miscellaneous operations
on
paper garments
and
plastic
products requiring a
long
stitch.
Stitch
range
is
4 to 7 per inch.
Seam
specification
401
SSa-1.
Type
128
GAS
needle.
Maximum
recommended
speed
6000
R.P.M.
CLASS
DESCRIPTION
(56400)
Advanced
high
speed,
low
throw,
flat
bed
machines.
Two
needles, independent
row,
left
needle
in
front,
two
loopers, enclosed automatic lubricating system.
Type
106
GHS
needle. Prepared for
use
with
knee
press for foot
lifter.
Maximum
recom-
mended
speed
6500
R.P.M.
Maximum
work
space to
right
of
needle bar 8 1/4 inches
(209.6mm).
MACHINE
STYLES
56400
D
To
be
used
with Galkin close-coupled
puller.
Attachments not furnished
with machine. Typical application -
For
hemming
and
simultaneously
in-
serting
elastic
in tops
and
legs
of
knitted undergarments
made
with
light
to
medium
weight materials.
Seam
specification
401
EFg-2.
Standard
gauge
Nos.
12,
16.
56400
P
Typical
sleeves
erials.
12, 16,
application -
For
piecing sleeves, joining shoulders,
setting
of
ordinary quality
shirts
made
with
light
to
medium
weight mat-
Seam
specification
401
LSc-2.
Standard
gauge
Nos.
6, 8, 10,
18.
56400
R Typical application -
For
attaching set-on center
plaits
and
interlining
strip
to
skirts
made
with
light
to
medium
weight materials. Starts oper-
ating
at
neck.
Seam
specification -
401
LSm-2.
Type
106
GHS
needle.
Standard
gauge
No.
48.
Maximum
recommended
speed
6500
R.P.M.
*Discontinued -
In
most
instances, replacement parts are available.
5
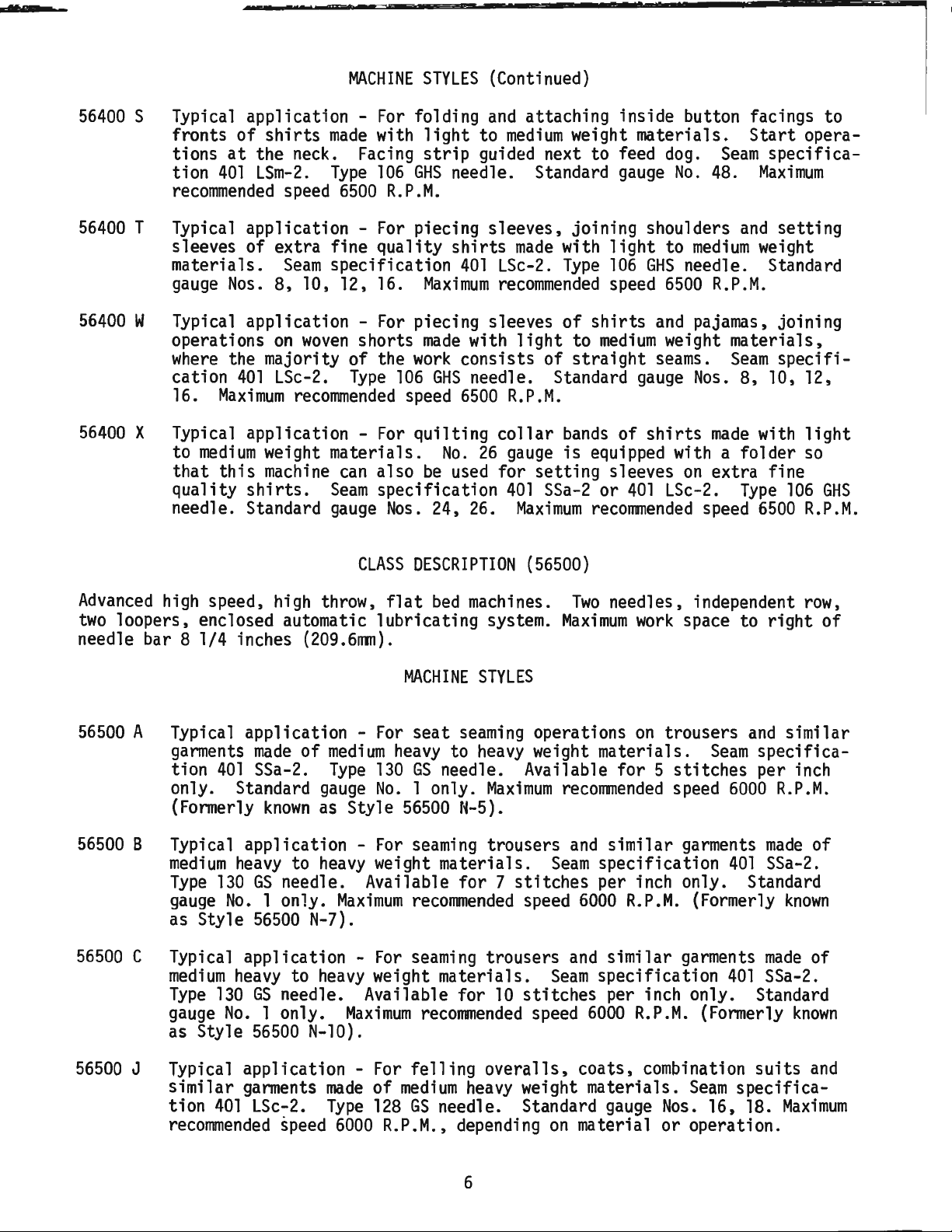
From the library of: Superior Sewing Machine & Supply LLC
MACHINE
STYLES
(Continued)
56400
S Typical application -
For
folding
and
attaching inside button facings
to
fronts
of
shirts
made
with
light
to
medium
weight materials.
Start
opera-
tions
at
the neck. Facing
strip
guided next
to
feed
dog.
Seam
specifica-
tion
401
LSm-2.
Type
106
GHS
needle. Standard
gauge
No.
48.
Maximum
recommended
speed
6500
R.P.M.
56400
T Typical application -
For
piecing sleeves, joining shoulders
and
setting
sleeves
of
extra fine
quality
shirts
made
with
light
to
medium
weight
materials.
Seam
specification
401
LSc-2.
Type
106
GHS
needle. Standard
gauge
Nos.
8,
10, 12, 16.
Maximum
recommended
speed
6500
R.P.M.
56400
W Typical application -
For
piecing sleeves
of
shirts
and
pajamas, joining
operations
on
woven
shorts
made
with
light
to
medium
weight
materials,
where
the majority
of
the
work
consists
of
straight
seams.
Seam
specifi-
cation
401
LSc-2.
Type
106
GHS
needle. Standard
gauge
Nos.
8,
10, 12,
16.
Maximum
recommended
speed
6500
R.P.M.
56400
X Typical application -
For
quilting
collar
bands
of
shirts
made
with
light
to
medium
weight materials.
No.
26
gauge
is
equipped with a folder
so
that
this
machine
can
also
be
used
for
setting
sleeves
on
extra fine
quality
shirts.
Seam
specification
401
SSa-2
or
401
LSc-2.
Type
106
GHS
needle. Standard
gauge
Nos.
24,
26.
Maximum
recommended
speed
6500
R.P.M.
CLASS
DESCRIPTION
(56500)
Advanced
high speed, high throw,
flat
bed
machines.
Two
needles, independent
row,
two
loopers, enclosed automatic
lubricating
system.
Maximum
work
space to
right
of
needle bar 8 1/4 inches (209.6rnn).
MACHINE
STYLES
56500
A Typical application -
For
seat
seaming
operations
on
trousers
and
similar
garments
made
of
medium
heavy
to
heavy
weight materials.
Seam
specifica-
tion
401
SSa-2.
Type
130
GS
needle. Available
for
5
stitches
per inch
only. Standard
gauge
No.
1 only.
Maximum
recornnended
speed
6000
R.P.M.
( Formerly
known
as
Style
56500
N-5).
56500
B Typical application -
For
seaming
trousers
and
similar
garments
made
of
medium
heavy
to
heavy
weight materials.
Seam
specification
401
SSa-2.
Type
130
GS
needle. Available
for
7
stitches
per inch only. Standard
gauge
No.
1 only.
Maximum
recommended
speed
6000
R.P.M.
(Formerly
known
as Style
56500
N-7).
56500
C Typical application -
For
seaming
trousers
and
similar
garments
made
of
medium
heavy
to
heavy
weight materials.
Seam
specification
401
SSa-2.
Type
130
GS
needle. Available
for
10
stitches
per inch only. Standard
gauge
No.
l only.
Maximum
recommended
speed
6000
R.P.M.
(Formerly
known
as Style
56500
N-10).
56500
J Typical application -
For
felling
overalls,
coats,
combination
suits
and
similar
garments
made
of
medium
heavy
weight materials.
Seam
specifica-
tion
401
LSc-2.
Type
128
GS
needle. Standard
gauge
Nos.
16, 18.
Maximum
recommended
speed
6000
R.P.M., depending
on
material or operation.
6
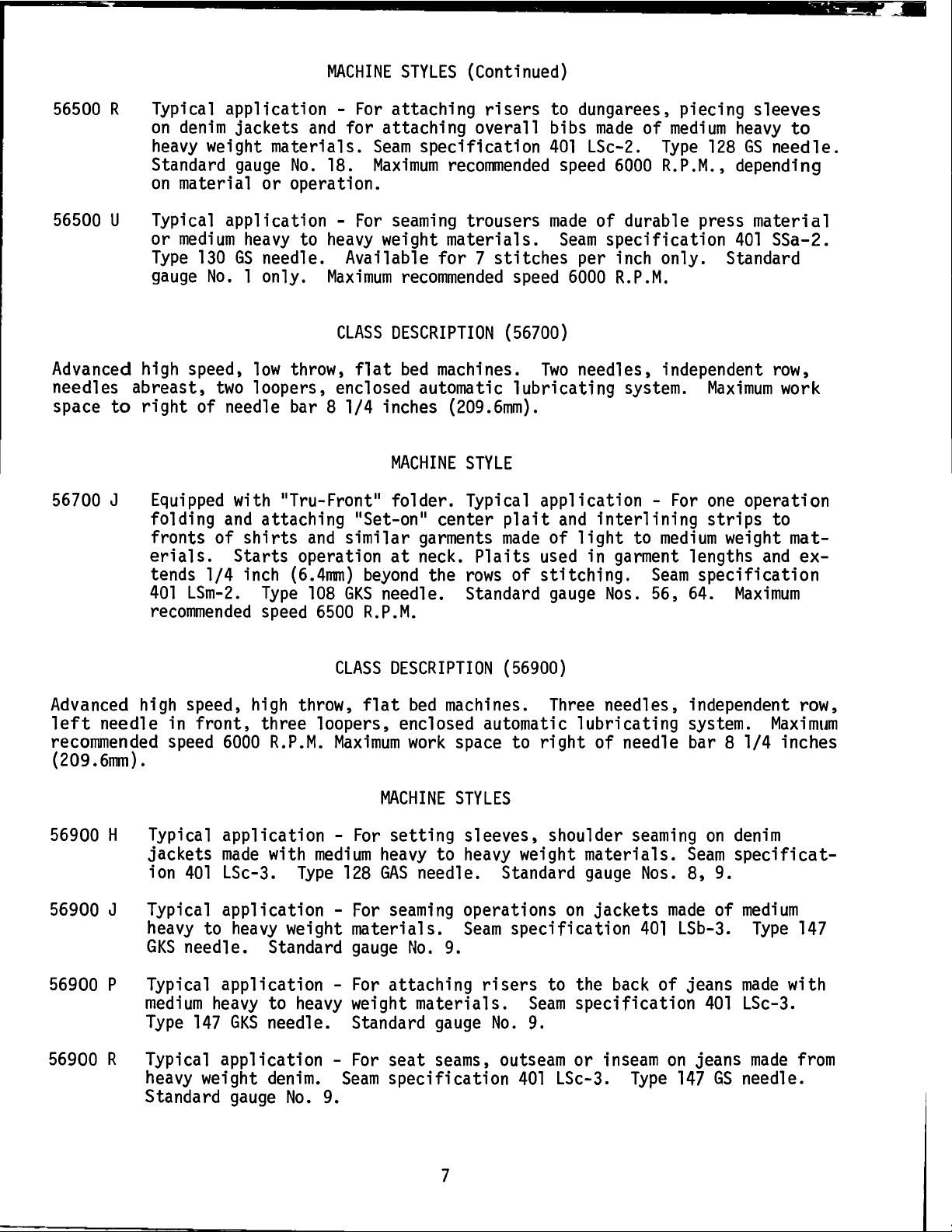
From the library of: Superior Sewing Machine & Supply LLC
MACHINE
STYLES
(Continued)
56500
R Typical application -
For
attaching
risers
to dungarees, piecing sleeves
on
denim
jackets
and
for attaching overall bibs
made
of
medium
heavy
to
heavy
weight materials.
Seam
specification
401
LSc-2.
Type
128
GS
needle.
Standard
gauge
No.
18.
Maximum
recommended
speed
6000
R.P.M.,
depending
on
material or operation.
56500
U Typical application -
For
seaming
trousers
made
of durable press material
or
medium
heavy
to
heavy
weight materials.
Seam
specification
401
SSa-2.
Type
130
GS
needle. Available for 7
stitches
per
inch
only. Standard
gauge
No.
l only.
Maximum
recommended
speed
6000
R.P.M.
CLASS
DESCRIPTION
(56700)
Advanced
high speed,
low
throw,
flat
bed
machines.
Two
needles, independent
row,
needles abreast,
two
loopers, enclosed automatic lubricating system.
Maximum
work
space
to
right
of needle bar 8 1/4 inches
(209.6mm).
MACHINE
STYLE
56700
J
Equipped
with
11
Tru-Front
11
folder. Typical application -
For
one
operation
folding
and
attaching
11
Set-on
11
center
plait
and
interlining
strips
to
fronts of
shirts
and
similar
garments
made
of
light
to
medium
weight mat-
erials.
Starts operation
at
neck.
Plaits
used
in
garment
lengths
and
ex-
tends 1/4 inch
(6.4mm)
beyond
the
rows
of stitching.
Seam
specification
401
LSm-2.
Type
108
GKS
needle. Standard
gauge
Nos.
56,
64.
Maximum
recommended
speed
6500
R.P.M.
CLASS
DESCRIPTION
(56900)
Advanced
high
speed,
high
throw,
flat
bed
machines.
Three
needles, independent
row,
left
needle in front, three loopers, enclosed automatic lubricating system.
Maximum
recommended
speed
6000
R.P.M.
Maximum
work
space to
right
of needle bar 8 1/4 inches
(209.6mm).
MACHINE
STYLES
56900
H Typical application -
For
setting sleeves, shoulder
seaming
on
denim
jackets
made
with
medium
heavy
to
heavy
weight materials.
Seam
specificat-
ion
401
LSc-3.
Type
128
GAS
needle. Standard
gauge
Nos.
8, 9.
56900
J Typical application -
For
seaming
operations
on
jackets
made
of
medium
heavy
to
heavy
weight materials.
Seam
specification
401
LSb-3.
Type
147
GKS
needle. Standard
gauge
No.
9.
56900
P Typical application -
For
attaching
risers
to the
back
of jeans
made
with
medium
heavy
to
heavy
weight materials.
Seam
specification
401
LSc-3.
Type
147
GKS
needle. Standard
gauge
No.
9.
56900
R Typical application -
For
seat
seams,
outseam
or
inseam
on
jeans
made
from
heavy
weight
denim.
Seam
specification
401
LSc-3.
Type
147
GS
needle.
Standard
gauge
No.
9.
7
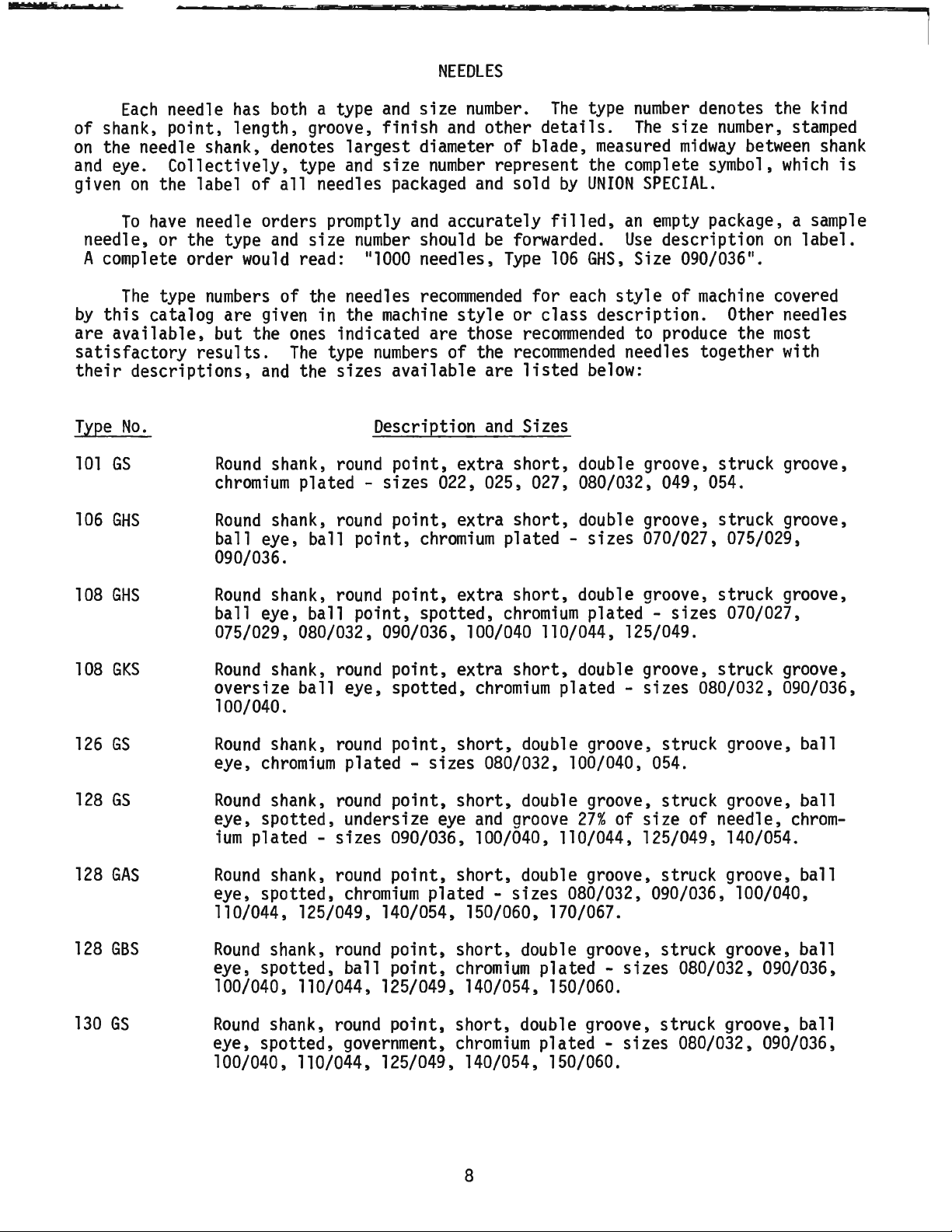
From the library of: Superior Sewing Machine & Supply LLC
NEEDLES
Each
needle
has
both a type
and
size
number.
The
type
number
denotes the kind
of shank, point, length, groove,
finish
and
other
details.
The
size
number,
stamped
on
the needle shank, denotes
largest
diameter of blade,
measured
midway
between
shank
and
eye.
Collectively,
type
and
size
number
represent the complete symbol,
which
is
given
on
the label
of
all
needles packaged
and
sold
by
UNION
SPECIAL.
To
have
needle orders promptly
and
accurately
filled,
an
empty
package, a
sample
needle, or the type
and
size
number
should
be
forwarded.
Use
description
on
label.
A complete order
would
read:
11
1000
needles,
Type
106
GHS,
Size 090/036
11
•
The
type
numbers
of
the needles
recommended
for
each
style
of
machine
covered
by
this
catalog are given in the
machine
style
or
class
description. Other needles
are
available,
but the
ones
indicated are those
recorrnnended
to produce the
most
satisfactory
results.
The
type
numbers
of the
recommended
needles together with
their
descriptions,
and
the sizes available are
listed
below:
Type
No.
101
GS
106
GHS
108
GHS
108
GKS
126
GS
128
GS
128
GAS
128
GBS
130
GS
Description
and
Sizes
Round
shank,
round
point,
extra
short,
double groove, struck groove,
chromium
plated - sizes 022, 025, 027, 080/032, 049, 054.
Round
shank,
round
point,
extra
short,
double groove, struck groove,
ball eye, ball
point,
chromium
plated -
sizes
070/027, 075/029,
090/036.
Round
shank,
round
point,
extra
short,
double groove, struck groove,
ball eye, ball point, spotted,
chromium
plated -
sizes
070/027,
075/029, 080/032, 090/036, 100/040 110/044, 125/049.
Round
shank,
round
point,
extra
short,
double groove, struck groove,
oversize ball eye, spotted,
chromium
plated - sizes 080/032, 090/036,
100/040.
Round
shank,
round
point,
short,
double groove, struck groove, ball
eye,
chromium
plated - sizes 080/032, 100/040,
054.
Round
shank,
round
point,
short,
double groove, struck groove, ball
eye, spotted, undersize
eye
and
groove
27%
of
size
of needle,
chrom-
ium
plated - sizes 090/036, 100/040, 110/044, 125/049, 140/054.
Round
shank,
round
point,
short,
double groove, struck groove, ball
eye, spotted,
chromium
plated -
sizes
080/032, 090/036, 100/040,
110/044, 125/049, 140/054, 150/060, 170/067.
Round
shank,
round
point,
short,
double groove, struck groove, ball
eye, spotted, ball point,
chromium
plated -
sizes
080/032, 090/036,
100/040, 110/044, 125/049, 140/054, 150/060.
Round
shank,
round
point,
short,
double groove, struck groove, ball
eye, spotted, government,
chromium
plated - sizes 080/032, 090/036,
100/040, 110/044, 125/049, 140/054, 150/060.
8
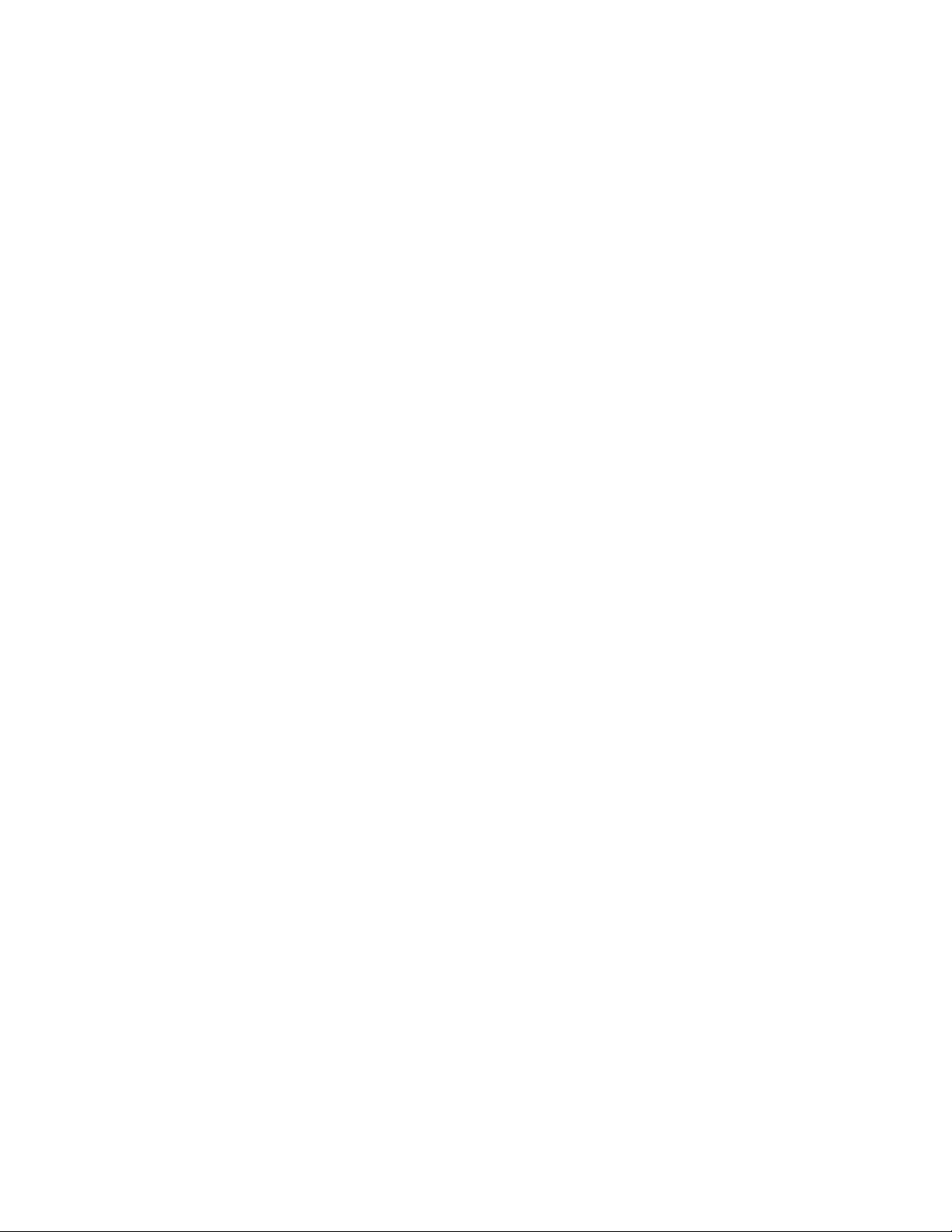
From the library of: Superior Sewing Machine & Supply LLC
NEEDLES
(Continued)
Description
and
Sizes
Type
No.
143
GS
Round
shank,
round
point,
No.
2 bag, double groove, struck groove,
spotted,
chromium
plated - sizes 140/054, 150/060, 170/067, 230/090.
147
GKS
Round
shank,
round
point, long, double groove, struck groove, over-
size ball eye, spotted, short point, standard
eye
and
grooves,
chromium
plated - sizes 090/036, 100/040, 110/044, 125/049, 140/054.
Selection of proper needle size
is
determined
by
size of the thread used.
Thread should pass freely through needle
eye
in order to
produce
a
good
stitch
formati
,'
on.
LUBRICATION
Use
a
straight
mineral oil with a Saybolt viscosity of
90
to
125
seconds
at
100
degrees
F.
This
is
equivalent to
Union
Special Corporation Specification
No.
175.
Before operating,
fill
machine
with
oil
at
plug screw
(A,
Fig. 1).
While
filling
machine
with
oil,
check
gauge
(B).
When
proper oil level
is
reached,
gauge
needle will
register
on
black
line
marked
11
FULL
11
•
Oil
must
be
added
when
gauge
needle
registers
on
black
line
marked
"LOW'.
Al-
though
the
machine
can
be
operated safely
when
gauge needle
registers
in the
"OPERATE"
zone,
it
is
recommended
to
always
check
oil
level before
operating,
to
be
sure
machine
is
filled
with
oil
to
the
"FULL"
mark.
CAUTION:
DO
NOT
over
fill
machine.
To
drain
oil,
remove
plug
screw
(C), or
low-
er
crank
chamber
cover
on
back
of
machine.
Oil
must
be
changed
every
2000
operating hours to
minimize wear.
On
new
machines, or a
machine
out of service
for
an
extended period of time; lubricate
machine
as follows:
Remove
head
cover, clean.out
lint,
then
di-
rectly
oil
needle bar link
and
needle bar.
Re-
place
head
cover
and
fill
machine
with
oil
to
proper
level.
Run
machine
at
low
RPM
to ensure
proper
lubrication
of
components
preventing
any
damage
which
may
occur
from
lack of
oil
distri-
bution.
9
Fig. 1
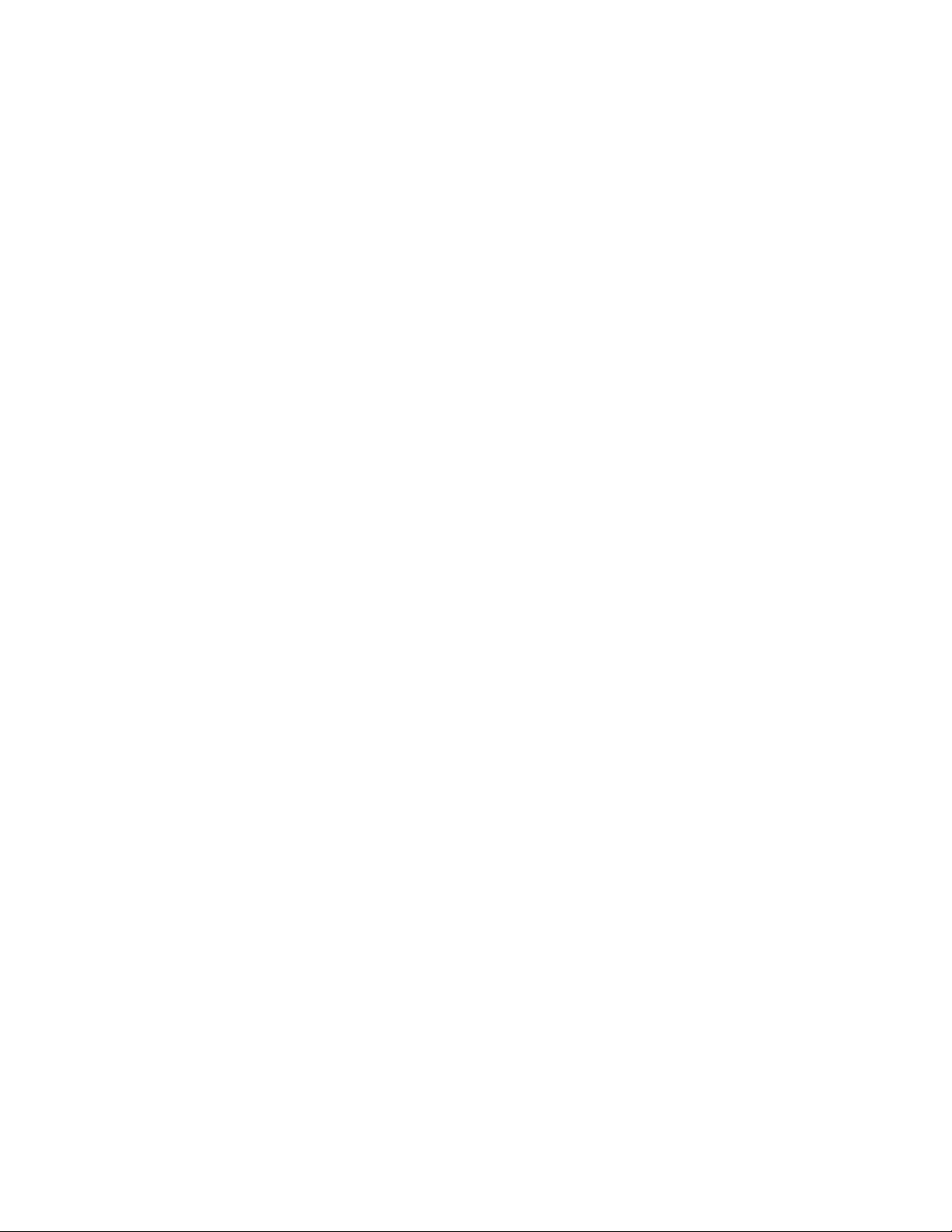
From the library of: Superior Sewing Machine & Supply LLC
CAUTION:
FIii
oll
reservoir
before
starting.
Machine
has
been
drained
before
shipping.
FIii main reservoir
here.
Fig. 2
THREADING
AND
OILING
DIAGRAM
FOR
ALL
STYLES
EXCEPT
56300
E,F,G,N,R,U,X,AH
and
AL
full
mark
on gauge.
Oil
has
been
drained
from
machine
before shipping
and
the reservoir
must
be
filled
before
starting
to operate. Maintain oil level in
"OPERATE"
zone;
add
oil
when
needle of
gauge
registers
on
the black
line
marked
"LOW".
Machine
is
automatically
lubricated
and
no
oiling other than
keeping
the
main
reservoir
filled
is
necessary.
Refer to instructions
under
11
LUBRICATION
11
and
"CHANGING
STITCH
LENGTH"
for additional
information.
Thread
machine
as
illustrated
above
for
all
Styles except
56300
E,F,G,N,R,U,X,
AH
and
AL.
10
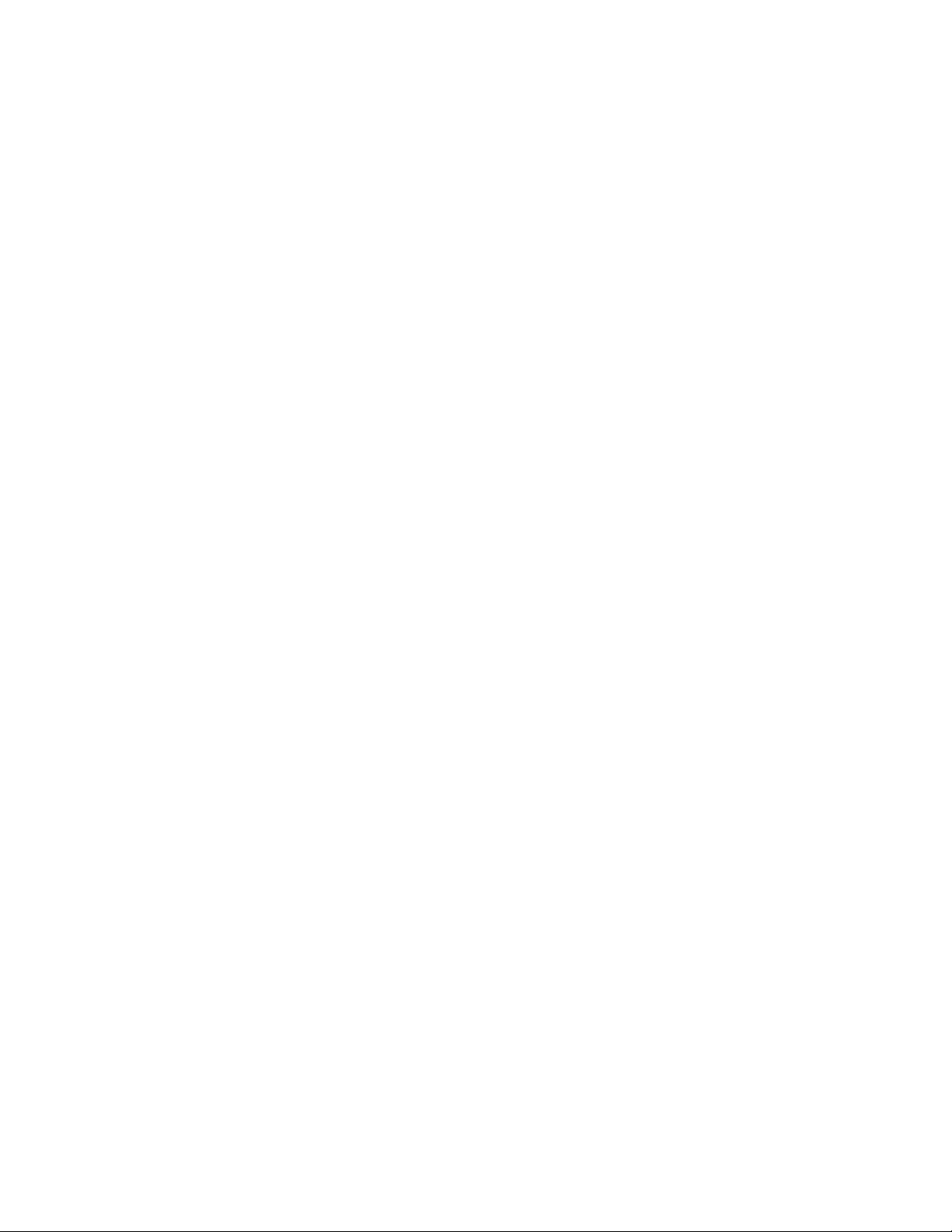
From the library of: Superior Sewing Machine & Supply LLC
CAUTION:
Fill
oll
reservoir
before
starting.
Machine
has
been
drained
before
shipping.
FIii main reservoir
here.
FIii reservoir
to
full mark on
gauge.
CAUTION: Be sure looper connection Is
up
before
sewing.
Fig.
2A
THREADING
AND
OILING
DIAGRAM
FOR
STYLES
56300
E,F,G,N,R,U,X,AH
and
AL
Oil
has
been
drained
from
machine
before shipping
and
the reservoir
must
be
filled
before
starting
to operate. Maintain oil level in
11
0PERATE
11
zone;
add
oil
when
needle of
gauge
registers
on
the black
line
marked
11
LOW
11
•
Machine
is
automatically
lubricated
and
no
oiling other than
keeping
the
main
reservoir
filled
is
necessary.
Refer to instructions under
11
LUBRICATION
11
and
"CHANGING
STITCH
LENGTH"
for additional
information.
Thread
machine
as
illustrated
above
for Styles
56300
E,F,G,N,R,U,X,AH
and
AL.
11

From the library of: Superior Sewing Machine & Supply LLC
ADJUSTING
INSTRUCTIONS
NOTE:
Instructions
stating
direction or location,
such
as
right,
left,
front or rear
of
machine,
are
given
relative
to operator's position
at
the
machine.
The
handwheel
rotates counterclockwise, in operating direction;
when
viewed
from
the
right
end
of
machine.
OIL
GAUGE
CALIBRATION
To
recalibrate oil
gauge,
follow instructions in sequence
as
listed:
- Place
machine
upright
on
a level surface.
-
Remove
plug
screw
(C,
Fig.
1)
and
tip
machine
forward
to drain
all
oil
from
reser-
voir.
-
Remove
lower
crank
chamber
cover
on
back
of
machine.
-
Fill
reservoir until
oil
is
even
with
bottom
of
knee
press shaft
bushing
(D).
-
Loosen
locknut
(E)
and
rotate calibrating
screw
(F)
as
required until
gauge
needle
registers
on
the black
line
marked
11
LOW
11
•
- Tighten locknut {E), then replace
plug
screw
(C)
and
lower
crank
chamber
cover.
- Fill
machine
with oil until
gauge
needle
registers
on
black line
marked
11
FULL
11
•
A
Fig. 3
Fig. 4
12
NEEDLE
BAR
ALIGNMENT
(TWO
AND
THREE
NEEDLE
MACHINES)
Insert
a
new
set
of needles (type
and
size required).
Turn
handwheel
to bring
needle bar
(A,
Fig.
3)
down
to ensure
that
needles center in needle holes of throat
plate
as
shown
in Fig.
3.
Adjustment
can
be
made
by
loosening
screw
(B)
slightly,
allowing needle bar to
be
turned
as
requir-
ed. Tighten
clamp
screw.
SYNCHRONIZING
LOOPER
AND
NEEDLE
MOTIONS
Insert looper into the looper rocker,
pushing
it
all
the
way
down
and
tighten
screw
against
flat
on
shank
of looper.
Turn
handwheel
in operating direction until
the point of the looper
(A,
Fig.
4)
moving
to the
left,
is
even
with the
left
side of
the
right
needle (B).
Note
the height of
the
eye
of the needle with respect to the
looper point
(See
Fig. 5).
Turn
the
hand-
wheel
in the reverse direction until the
point
of
looper again
moving
to the
left,
is
even
with the
left
side of right needle
(See
Fig. 5).
If
the height of the
eye
of
the needle with respect to the looper point
are the
same,
looper
and
needle
motions
are
synchronized - a variation of
.005
inch
(.127mm)
is
allowable.
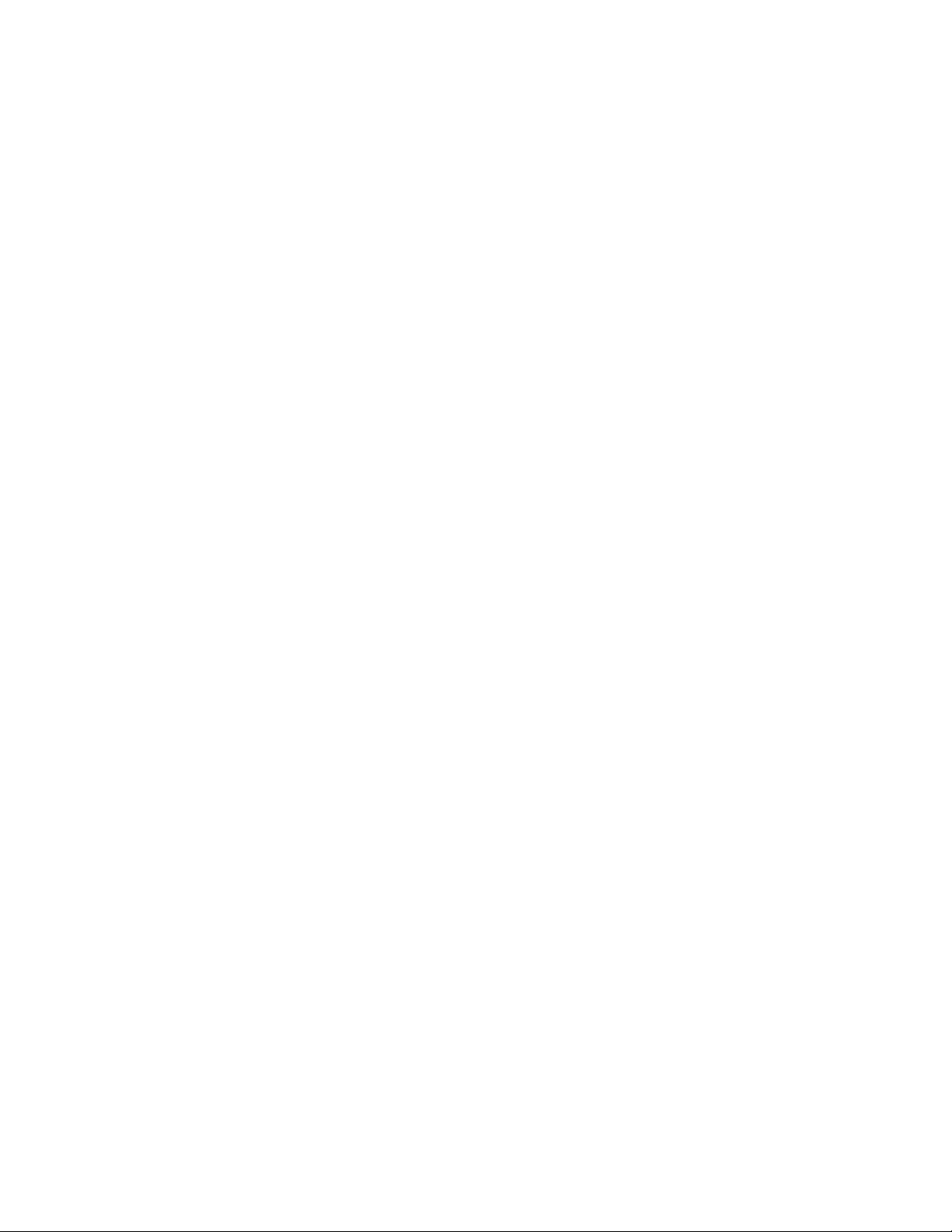
From the library of: Superior Sewing Machine & Supply LLC
SYNCHRONIZING
LOOPER
AND
NEEDLE
MOTIONS
(Continued)
If
the distance
from
the
eye
of the needle to the
point of
the
looper
is
greater
when
the
handwheel
is
turned in the operating direction, the looper
drive
lever
rocker
shaft
will
have
to
be
moved
slightly
towards the
rear.
Moving
the
shaft
to-
wards
the
front
acts the reverse.
NOTE:
The
1/64 inch
(.4mm)
dimension
shown
in
Fig. 5
is
for final
setting
of needle
bar height.
Adjust looper drive rocker lever
shaft
as
follows:
Loosen
screw
(C,
Fig.
4)
in looper
drive
lever
(D).
A
rod
of
.146-40 thd.
or
Union
Special
Screw
No.
22870
A
can
be
threaded
into
the looper drive lever rock-
er
shaft through the center of
thrust
adj-
usting screw (E).
Tap
or pull
slightly
as
required
to
position
shaft
for proper syn-
chronization. Tighten
screw
(C)
securely
and
remove
rod
or
screw
used
to position
shaft.
Loosen
lock nut
(F)
and
TORQUE
thrust
adjusting
screw
(E)
to 6 in.
lbs.
(7cm/kg);re-tighten lock nut
(F)
securely.
With
looper
at
extreme
right
end
of
its
travel,
check
location
of
the center-
line
of
right
looper connecting
rod
bear-
ing using
gauge
No.
21227
ex
for
all
Classes except
56700
which
uses
gauge
No.
21227
CX-56
for Style
56700
J-56
and
No.
21227
CX-64
for Style
56700
J-64.
Remove
nut
from
looper
lever
stud
(A,
Fig.
6)
and
place hole in
gauge
(B)
over threaded stud.
The
left
end
of
gauge
should locate against the
RIGHT
side of
looper rocker
cone
(C).
If
adjustment
is
neces-
sary,
loosen
clamp
screw
(D), reposition looper
drive
lever
(E)
as
required
and
retighten
screw
(D).
If
gauge
is
not available,
setting
can
be
checked with a scale.
"X"
dimension
is
from
centerline
of stud
(A)
to centerline
of
cone
(C)
which
should
be
4 1/16 inch
(103.2mm)
for
all
Classes except
56700.
Style
56700
J-56 should
be
a 3 5/8 inch
(92.
1nm)
and
Style
56700
J-64
should
be
3 9/16 inch
(90.6mm)
with looper
at
extreme
right
end
of
travel.
LOOPER
SETTINGS
Insert
a
new
needle, type
and
size
as
spec-
For
Proper
SYNCHRONIZATION of
Looper
& Needle
these
two
Dimensions
will
be
the
same
J
1/84'
1Hl
--==-
(.4mm)
-r
in
OPERATING
Direction
Fig. 5
Fig. 6
Fig. 7
Looper
in
FRONT of
Needle
In
REVERSE
Direction
ified.
If
the looper
ga
_
uge
is
5/32 inch (4.0nm), for example,
set
the looper
(A,
Fig. 7)
so
the distance
from
the center
of
the needle
(B)
to the point of the
looper is 5/32 inch
(4.0mm),
when
the looper
is
at
its
farthest
position to the
right.
13
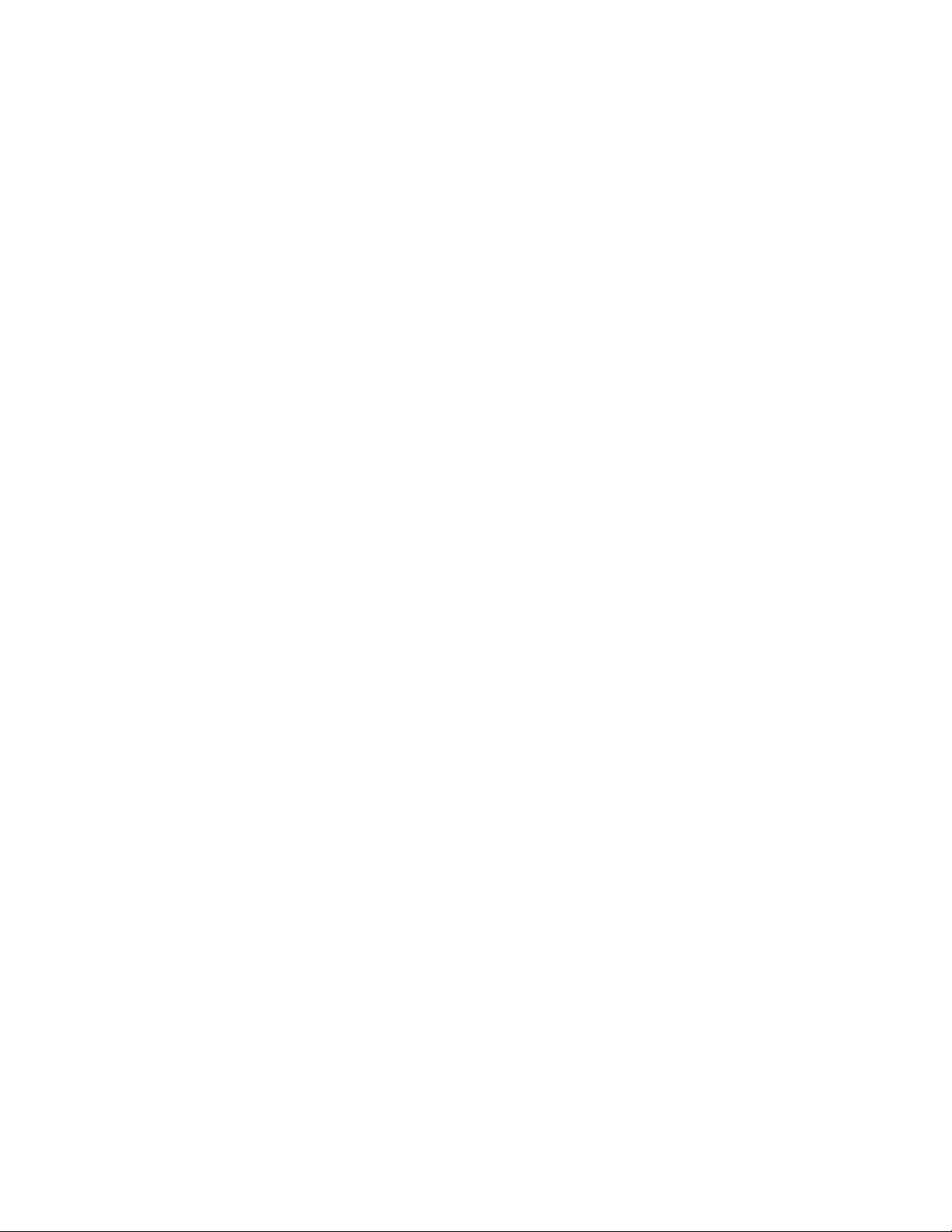
From the library of: Superior Sewing Machine & Supply LLC
LOOPER
SEITINGS
(Continued)
Looper
gauge
No.
21225-5/32
(C)
can
be
used
advantageously in
making
this
adjustment.
On
two
needle
machines
set
the
back
looper to the
right
needle
and
on
three needle
machines
set
the middle looper to the middle needle,
when
setting
the looper gauge.
Refer to chart for needle
Type,
looper
gauge
setting
and
looper
gauge
number.
If
adj-
ment
is
required, loosen nut
(D)
(it
has
a
left
hand
thread)
and
nut
(E)
on
connect-
ing
rod
(F), turn the connecting
rod
forward or
backward
to obtain the 5/32 inch
(4.0mm)
dimension. Retighten both nuts,
first
nut (E), then nut
(D).
Make
sure the
left
ball
joint
is
in
vertical
position
and
does
not bind
after
adjustment.
Machine
Styles
56200
H
56200
K,R
56200
L
56200
S
56200
W,
56300
W,AL
56300
E,F,G,N,R,
U,X,AH
56300
H
56300
M
56400
D
56400
P,R,S,T,W,X
56500
A,B,C,U
56500
J,R
56700
J
56900
H
56900
J
56900
P
56900
R
Needle
Type
101
GS
106
GLS
126
GS
108
GHS
128
GAS
128
GBS
143
GS
126
GS
106
GHS
106
GHS
130
GS
128
GS
108
GKS
128
GAS
147
GKS
147
GKS
147
GS
Looper
Gauge
Setting
1/8
Inch
(3.2mm)
1/8
Inch
(3.2mm)
5/32
Inch
(4.0mm)
1/8
Inch
(3.2mm)
5/32
Inch
(4.0mm)
5/32
Inch
(4.0mm)
5/32
Inch
(4.0mm)
5/32
Inch
(4.0mm)
1/8
Inch
(3.2mm)
1/8
Inch
(3.2mm)
5/32
Inch
(4.0mm)
5/32
Inch
(4.0mm)
1/8
Inch
(3.2mm)
5/32
Inch
(4.0ITITl)
7/32
Inch
{5.6mm)
5/32
Inch
(4.0ITITl)
7/32
Inch
(5.6mm)
Looper
Gauge
Number
21225-1/8
21225-1/8
21225-5/32
21225-1/8
21225-5/32
21225-5/32
21225-5/32
21225-5/32
21225-1/8
21225-1/8
21225-5/32
21225-5/32
21225-1/8
21225-5/32
21225-7/32
21225-5/32
21225-7/32
The
looper
is
set
correctly
if,
as
it
moves
to the
left
behind the needle,
its
point
(A,
Fig.
8)
clears
the
rear
of
needle
(B)
by
.002 inch (.05lmm).
Fig. 8
If
adjustment
is
necessary, loosen lock screw
(G,
Fig.
7)
and
turn stop
screw
(H)
as
required. Turning stop
screw
clock-
wise
sets
the looper to the
rear
and
turning
it
counterclock-
wise acts the reverse.
Holding
looper to the
front
while
making
this
adjustment
may
prove
helpful. Tighten lock
screw
when
setting
is
obtained
and
recheck the adjustment.
On
Style
56200
W,
looper needle guard (attached to looper)
should
be
set
to barely contact the
front
of needle without de-
flecting
as
looper
moves
to
left.
·
On
the
two
and
three needle machines,
insert
the other
needles
and
loopers.
The
same
looper - needle relationship
should
exist
without
any
adjustment, other than applying pres-
sure
on
the looper
at
front or
back
of blade, while
clamping
looper in looper rocker,
so
as to get the proper
in-line-of-
feed
setting.
14
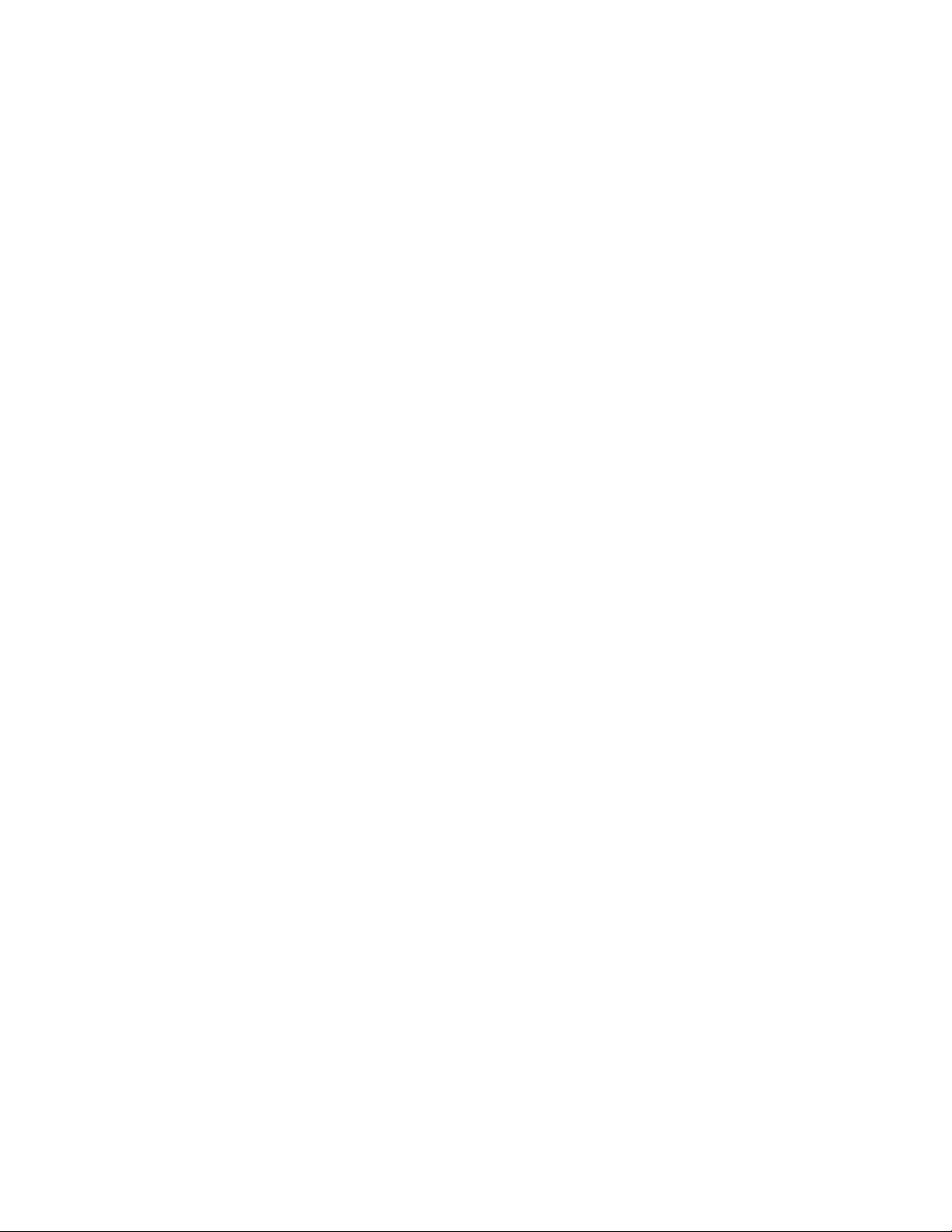
From the library of: Superior Sewing Machine & Supply LLC
NEEDLE
BAR
HEIGHT
The
height of the needle
is
correct
when
the
top
of
its
eye
is
1/64 inch (
.4mm)
below
the underside of the looper, with the looper
point
flush
with
the
left
side of the needle
as
shown
in Fig. 5.
On
Styles
56500
A,
Band
C the top of the needle eyes should
be
even
with the underside of the looper
when
the
looper
point
is
flush with the
left
side of
the needle.
If
adjustment
is
necessary, Fig. 9
loosen screw
(8,
Fig. 3)
and
move
needle bar
(A)
up
or
down
as
required
and
retighten screw.
On
two
and
three needle machines,
care should
be
taken not to disturb alignment of needle bar
when
moving
the needle
bar
either
up
or
down.
The
descending needles
must
be
deflected alike
on
the
back
of
the 1
oope
rs.
FEED
DOG
SETTINGS
Feed
dog
(A,
Fig.
9)
should
be
centered in throat
plate
(B)
with
equal
clearance
on
all
sides
and
ends
with
feed
travel
set
to desired
stitch
length.
At
highest point
of
travel,
tips
of feed
dog
teeth should extend the depth
of a tooth or approximate.ly
3/64 inch
(1.2mm)
above
throat
plate
and
parallel to
same.
Screw
(C)
should
be
set
to
support feed
dog
after
screw
(D)
has
been
loosened
which
secures feed
dog
in position.
On
Styles
56300
N,U,X,AH
the
tips
of the teeth
must
extend
1/32
inch
(.8mm)
above
the throat plate
and
the
"Grip
Feed"
presser foot feed
dog
must
line
with the
lower
feed
dog
left
to
right,
and
in-line-of-feed the
last
teeth
of the top
and
bottom
feeds should
match
tooth point to
point.
Fig.
10
Parallel
adjustment
can
be
made
by
loosening nut
(A,
Fig.
10)
and
turn
screw
(B)
clockwise
to
lower
front of feed
dog,
counterclockwise acts the reverse.
When
proper-
ly
set,
retighten nut
(A).
Right
to
left
adjustment
can
be
made
by
loosening
screws
(A,
Fig. 11)
and
slightly
move
feed rocker
(B)
on
feed rocker shaft
(C)
as
required,
then
retighten
screws.
Check
to en-
sure
that
feed rocker
arm
(D)
does
not bind
after
adjustment.
Forward
or rearward centering
of feed
dog
can
be
accomplished
by
loosening nut
(E,
Fig.
11),
move
feed rocker (B)
as
required
and
re-
tighten nut.
Fig.
11
15
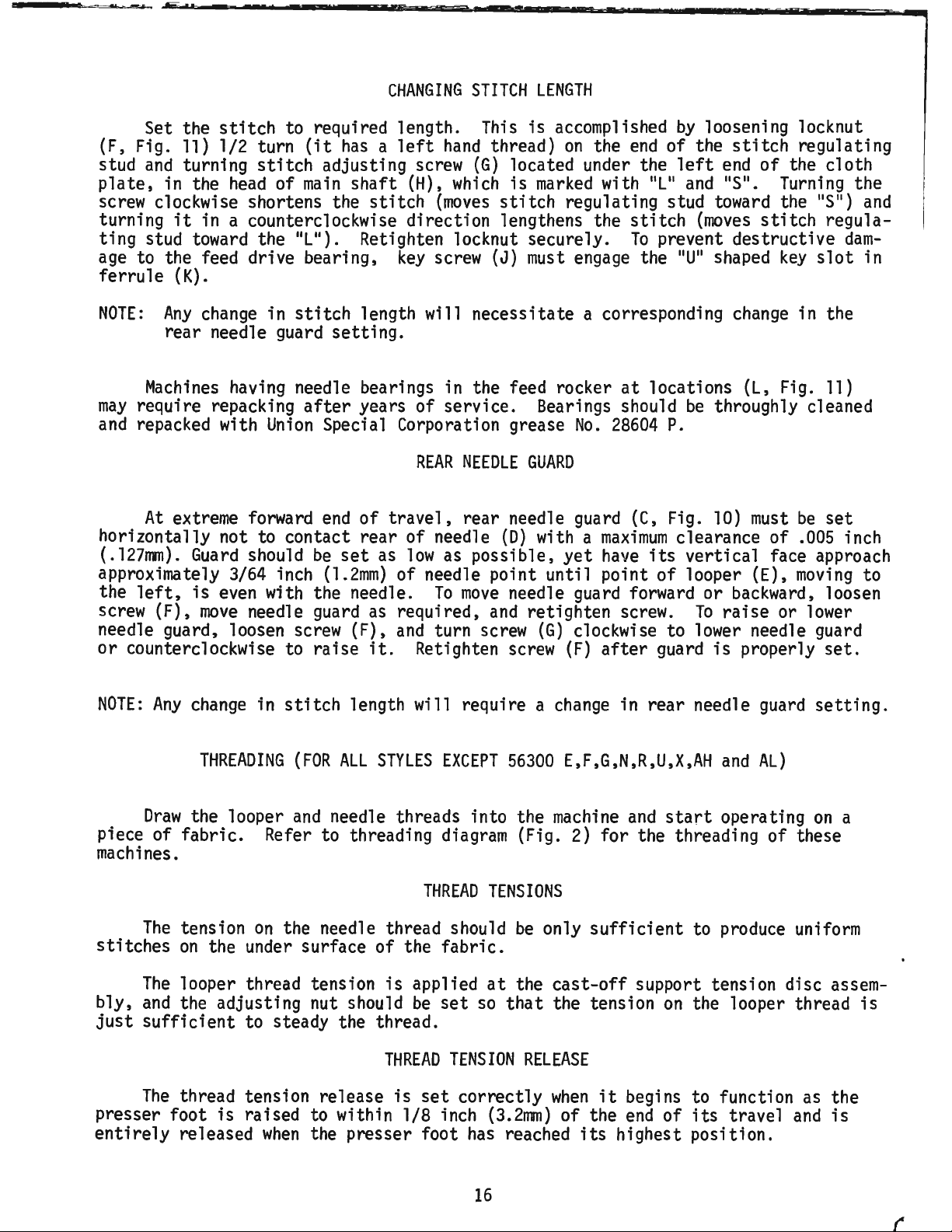
From the library of: Superior Sewing Machine & Supply LLC
CHANGING
STITCH
LENGTH
Set the
stitch
to required length.
This
is
accomplished
by
loosening locknut
(F, Fig.
11)
1/2 turn
(it
has
a
left
hand
thread)
on
the
end
of the
stitch
regulating
stud
and
turning
stitch
adjusting
screw
(G)
located under the
left
end
of the cloth
plate,
in the
head
of
main
shaft
(H),
which
is
marked
with
11
L
11
and
11
S
11
•
Turning
the
screw
clockwise shortens the
stitch
(moves
stitch
regulating stud
toward
the
11
S
11
)
and
turning
it
in a counterclockwise direction lengthens the
stitch
(moves
stitch
regula-
ting stud
toward
the
11
L
11
).
Retighten locknut securely.
To
prevent destructive
dam-
age
to the feed drive bearing,
key
screw
(J)
must
engage
the
11
U
11
shaped
key
slot
in
ferrule
(K).
NOTE:
Any
change
in
stitch
length will necessitate a corresponding
change
in the
rear needle
guard
setting.
Machines
having
needle bearings in the feed rocker
at
locations
(L,
Fig.
11)
may
require repacking
after
years of service. Bearings should
be
throughly cleaned
and
repacked with
Union
Special Corporation grease
No.
28604
P.
REAR
NEEDLE
GUARD
At
extreme
forward
end
of
travel,
rear needle
guard
(C,
Fig.
10)
must
be
set
horizontally not to contact rear of needle
(D)
with a
maximum
clearance of
.005
inch
(.12711111).
Guard
should
be
set
as
low
as possible,
yet
have
its
vertical face approach
approximately 3/64 inch
(1.2mm)
of needle point until point
of
looper (E),
moving
to
the
left,
is
even
with the needle.
To
move
needle
guard
forward or
backward,
loosen
screw
(F),
move
needle
guard
as
required,
and
retighten screw.
To
raise
or
lower
needle guard, loosen
screw
(F),
and
turn
screw
(G)
clockwise to
lower
needle guard
or
counterclockwise to raise
it.
Retighten
screw
(F)
after
guard
is
properly
set.
NOTE:
Any
change
in
stitch
length will require a
change
in rear needle
guard
setting.
THREADING
(FOR
ALL
STYLES
EXCEPT
56300
E,F,G,N,R,U,X,AH
and
AL)
Draw
the looper
and
needle threads into the
machine
and
start
operating
on
a
piece of fabric. Refer to threading
diagram
(Fig.
2)
for the threading of these
machines.
THREAD
TENSIONS
The
tension
on
the needle thread should
be
only
sufficient
to
produce
uniform
stitches
on
the under surface of the fabric.
The
looper thread tension
is
applied
at
the
cast-off
support tension disc
assem-
bly,
and
the adjusting nut should
be
set
so
that
the tension
on
the looper thread
is
just
sufficient
to steady the thread.
THREAD
TENSION
RELEASE
The
thread tension release
is
set
correctly
when
it
begins to function
as
the
presser foot
is
raised to within 1/8 inch
(3.2rrm)
of the
end
of
its
travel
and
is
entirely
released
when
the presser foot
has
reached
its
highest position.
16
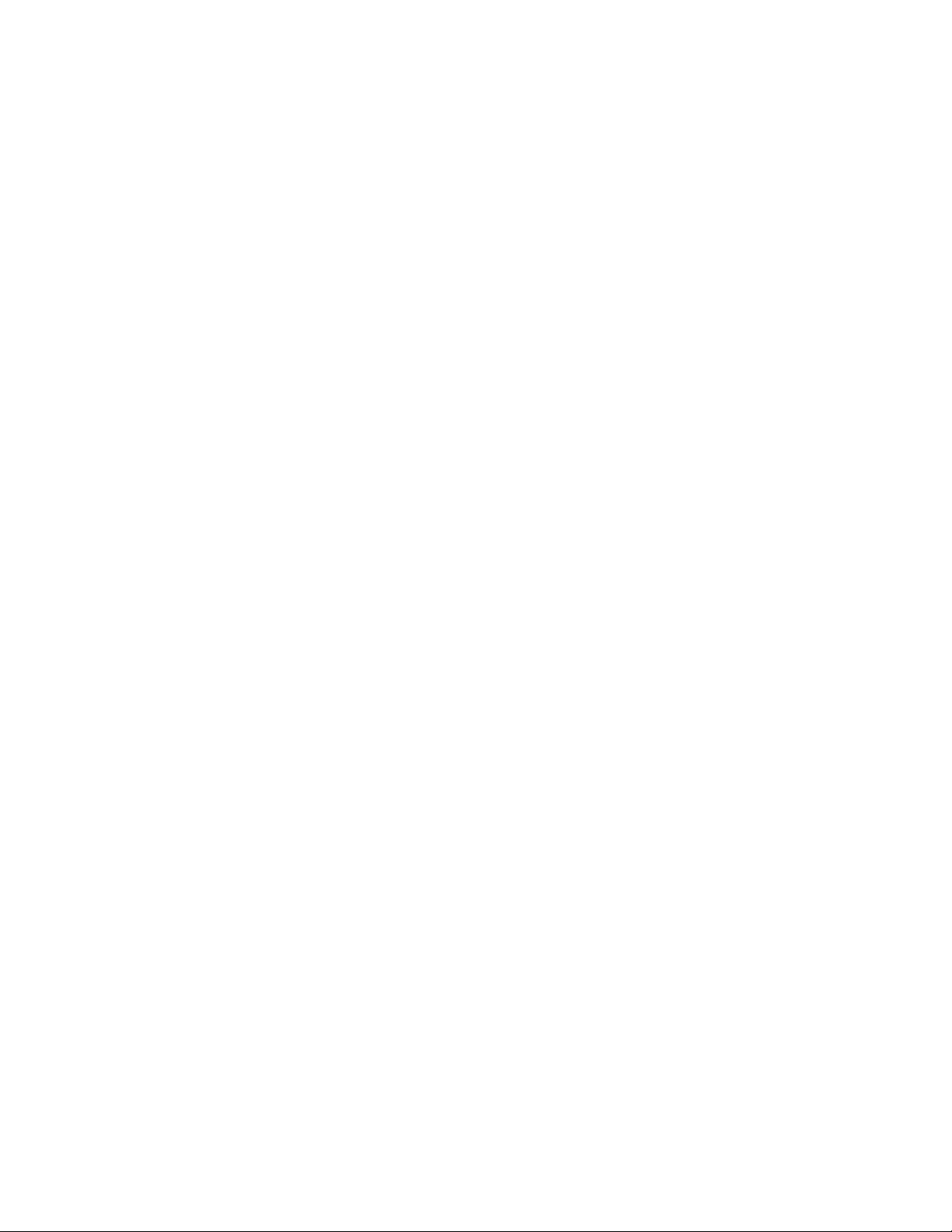
From the library of: Superior Sewing Machine & Supply LLC
THREAD
TENSION
RELEASE
(Continued)
If
adjustment
is
required, loosen tension release lever
screw
(A,
Fig. 12), located
at
the
back
of
machine
and
move
tension
disc
separator
as
required. Retighten screw. After
adjustment there should
be
no
binding
at
any
point.
PRESSER
BAR
HEIGHT
Height of presser bar
(A,
Fig.
13)
is
correct
when
pre-
sser
foot
can
be
removed
by
depressing foot
lifter
lever
(B,
Fig.
12).
There
should
be
approximately 1/16 inch
(1.6mm)
clearance
between
lower
surface of presser bar connection
and
guide
(B,
Fig.
13)
and
bottom
surface of
head
opeining in
bed
casting
when
foot
lifter
lever
is
released
and
presser foot
lying
flat
on
throat plate with feed
dog
below
throat
plate.
Fig.
12
'
A
Adjustment
can
be
made
by
turning
handwheel
to position needle bar
at
bottom
of
stroke.
Loosen
screw
(C,
Fig.
13)
and
while holding press-
er
foot
down
on
throat
plate,
position presser bar connect-
ion
and
guide
as
required to
attain
specified clearance
and
retighten
screw.
PRESSER
FOOT
PRESSURE
Regulate presser spring regulating
screw
(A,
Fig. 14)
so
that
it
exerts only
enough
pressure
on
the presser foot
to feed
the
work
uniformly
when
a
slight
tension
is
placed
on
the
fabric.
Turning
it
clockwise increases the pres-
sure, counterclockwise acts the reverse.
NEEDLE
THREAD
TAKE-UP
WIRE
AND
FRAME
EYELET
(FOR
ALL
STYLES
EXCEPT
56300
E,F,G,N,R,U,X,AH
and
AL)
Set needle thread take-up wire
(B,
Fig.
14),
so
that
its
upper surface
is
even
with the
top
of the holes in
needle bar thread eyelet
(C)
when
needle bar
has
completed
its
downward
stroke.
Lower
this
setting
for a smaller
needle thread loop, or raise
it
for a larger loop. Set
needle thread
frame
eyelet
(D)
so
that
the eyelet hole
is
3/4 inch
(19.0mm)
above
the attaching
screw
on
all
Styles except
on
Styles
56500
J,
56900
H,
J,
P
and
R the eyelet
is
to
be
set
5/8 inch
(15.9mm)
above
the attaching
screw
and
on
Style
56200
H the eyelet
is
to
be
set
l inch
(25.4mm)
above
the attaching screw.
NOTE:
For
the
above
setting
on
Styles
56300
E,F,G,N,R,U,X,AH
and
AL,
see
the following paragraphs.
THREADING
(FOR
STYLES
56300
E,F,G,N,R,U,X,AH
and
AL)
Refer to threading
diagram
(Fig.
2A)
for
the
manner
in
which
these
machines
are
threaded.
17
Fig.
13
Fig.
14
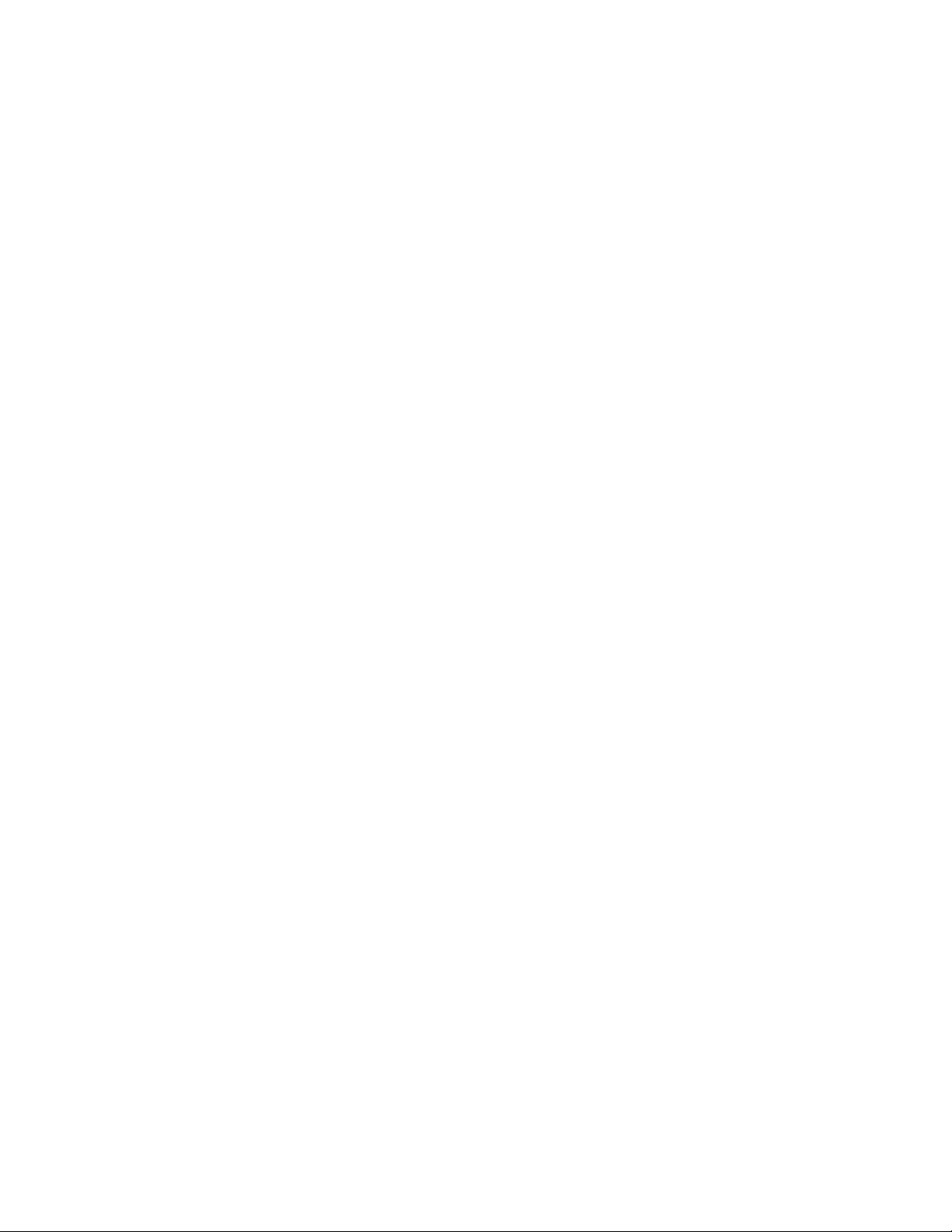
From the library of: Superior Sewing Machine & Supply LLC
NEEDLE
THREAD
TAKE-UP
WIRE
AND
FRAME
EYELET
FOR
(STYLES
56300
E,F,G,N,R,U,X,AH
and
AL)
Fig.
15
These
machine
styles
are equipped with addition-
al thread handling
and
con-
___:.i.,j~----
-
...__,
trol
parts,
so
the adjust-
ing sequence should
be
made
Fig.
14A
in the following
manner:
With
needle bar
at
the top of
its
stroke,
set
needle thread take-up wire
(A,
Fig.
14A)
so
its
lower extended surface
is
1 7/16 inch
(36.5mm)
above
centerline of
needle lever thread eyelet hole
and
3/4 inch
(19.0mm)
across the centerlines of
its
vertical surfaces
(See
Fig.
14A).
Fig.
16
Set looper thread guide eyelet
(A,
Fig.
15)
so
its
left
outer surface
is
3/4 inch
(19.0rrm)
from
the
left
side
of looper thread take-up (B),
(See
Fig. 15).
Adjust looper thread tension with nut
(B,
Fig.
14A)
to a
minimum
required for controlling the looper thread
(light).
Set the thread index eyelet
(C)
at
11
3
11
on
the
adjusting plate
(D).
Changing
the needle thread tension
only, with nut (E), balance the
stitch
so
that
when
6
inches
(152.4mm)
of
sewn
seam
are raveled back, the needle
thread
is
approximately as long as the looper thread.
Al
inch
(25.4mm)
difference in lengths
is
permissible.
NOTE:
Use
a
sample
of
the material to
be
sewn.
Maintaining
this
needle thread tension,
move
thread index eyelet
(C)
up
to
toward
11
L
11
to obtain a looser
seam
(longer needle loops)
and
toward
11
T
11
to obtain a
tighter
seam.
FEEDING
PRESSER
FOOT
Remove
the presser spring regulator
and
presser
spring. Adjust
long
stop
screw
(A,
Fig.
16)
in presser
bar guide
(B)
against
bed
casting
as
required to ensure a
clearance
between
the guide
and
top
of
presser bar bushing
(C), yet
so
that
guide
is
pulled
up
quickly
by
lifter
lever
link
(D)
when
foot treadle
is
activated. Tighten lock nut
(E)
on
stop screw.
18
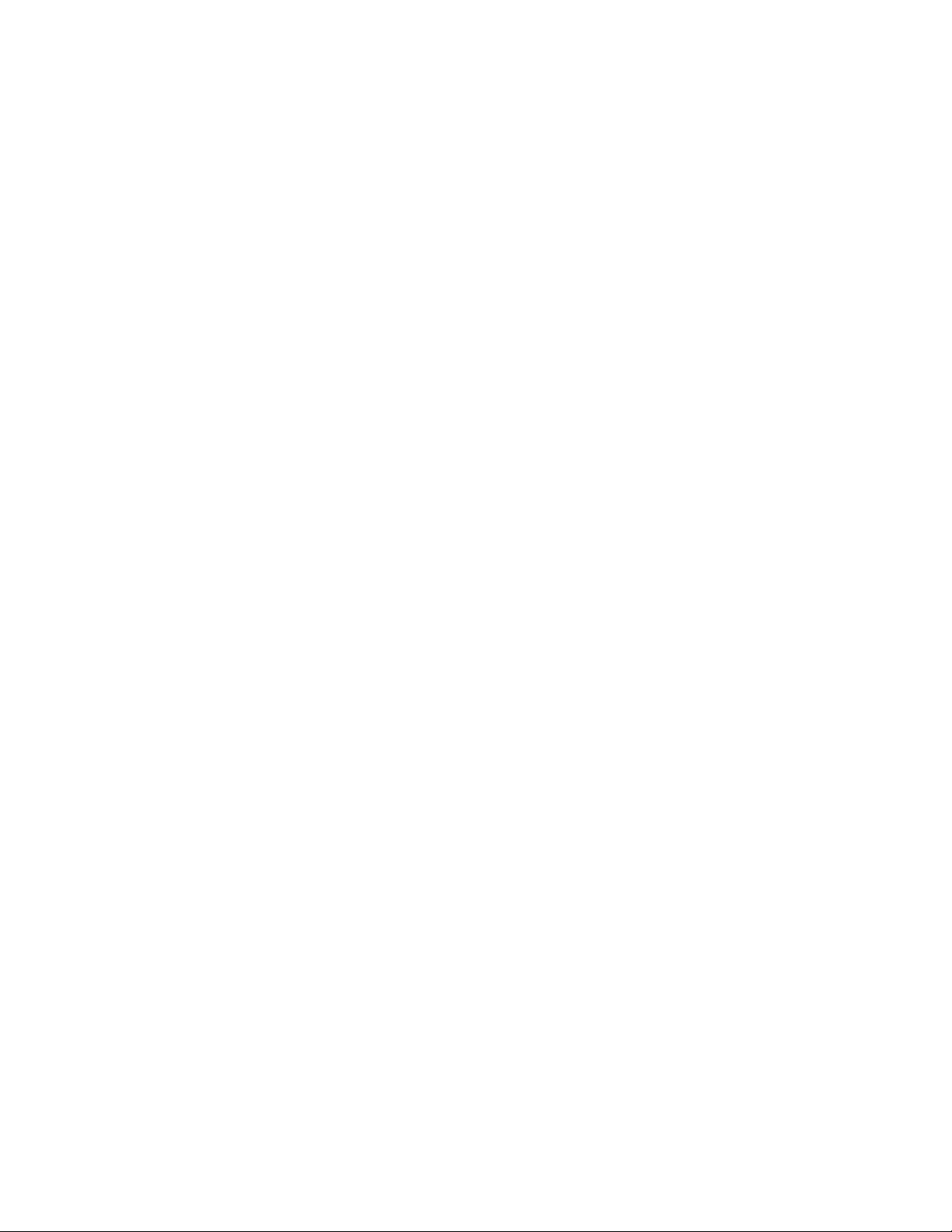
From the library of: Superior Sewing Machine & Supply LLC
FEEDING
PRESSER
FOOT
(Continued)
As
a preliminary
setting,
adjust spring regulator nut
(A,
Fig.
17)
on
feeding
presser
foot
so
the distance
from
the top of spring
(B)
to the
yoke
(C)
is
5/8 inch
(15.9mm),
(See
Fig. 17).
Assemble
the feeding presser
foot
to
presser bar.
With
presser foot resting
on
throat
plate
and
feed
dog
down,
press
down
on
spring
regulator
nut
{A,
Fig.
17)
until the
marks
on
presser
foot bottom line
up
with the centerline of needle,
while keeping the needle in the center of needle
slot,
tighten
set
screw
(D)
securing presser bar
guide
to
the presser bar,
making
sure stop
screw
in
presser
bar guide
is
resting
on
the
bed
casting.
Replace presser spring
and
presser spring reg-
ulator.
Turn
presser bar spring regulator
screw
down
until
the thread portion
is
level with the
head
casting.
NOTE:
Any
change
in the alignment of needle in
re-
lationship
to the
marks
on
the presser foot
bottom
probably
means
that
the stop
screw
of the presser bar
guide
was
not seated against
bed
c3sting before lock-
ing
set
screw.
When
the presser foot
is
lifted
off
the bare Fig.
17
throat
plate,
the foot should
move
back
only
slightly,
less
than 1/64 inch
(.4mm).
The
stop
screw
{E,
-Fig.
17)
on
the yoke,
which
is
set
at
the
factory,
can
be
readjusted
if
necessary, should
this
dimension
become
changed.
CHECK
Presser foot
at
back
of needle
slot
should cover
most
of throat plate land
when
resting
on
the bare throat
plate.
When
the presser foot
bottom
is
raised
by
material
so
that
the feeding foot
spring bottoms, the
back
of the needle
slot
should
clear
the needle.
The
main
press-
er
bar should not
lift
before the feeding foot spring bottoms.
The
purpose of the feeding foot
is
to
make
the top
and
bottom
ply of cloth feed
the
same
amount
without pulling
on
the
bottom
ply.
The
5/8 inch
{15.9mm)
setting
on
the feeding foot spring usually gives a
good
matching of
piles
and
a strong feeding
pull.
Reducing
this
pressure will tend to feed the top ply
more.
Increasing
this
pressure will tend to feed the
bottom
ply
more.
TORQUE
REQUIREMENTS
Torque
specifications given in
this
catalog are
measured
in
inch-pounds or
centimeter/kilograms.
All
straps
and
eccentrics
must
be
tightened to
19-21
in.
lbs.
(22-24cm/kg) unless otherwise noted.
All
nuts,
bolts,
screws,
etc
. , without torque
specifications
must
be
secured
as
tightly
as
possible, unless otherwise noted.
Special torque specifications for connecting rods,
links,
screws,
etc.,
are
shown
on
parts
illustrations.
19
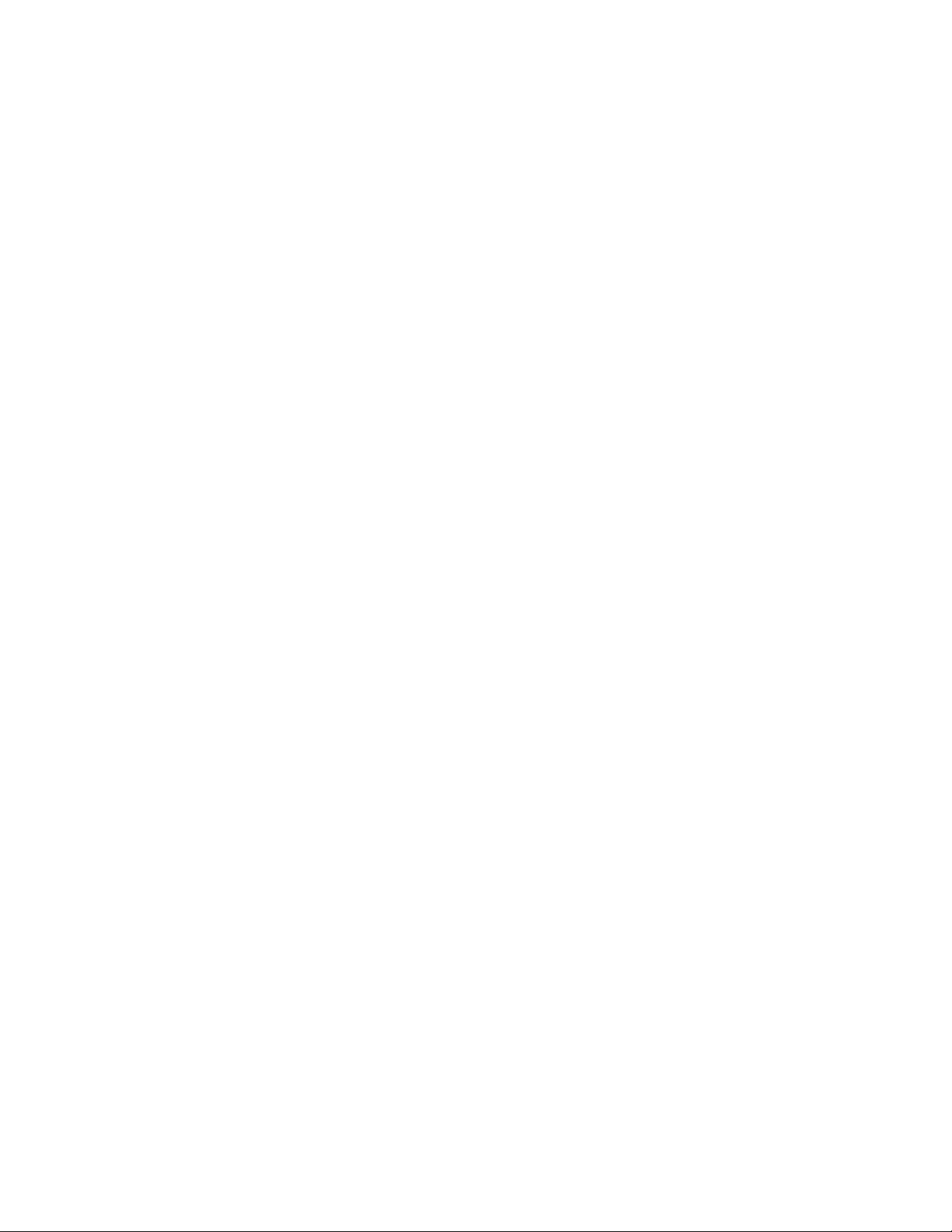
From the library of: Superior Sewing Machine & Supply LLC
•
Fig.
18
Fig. 19
.045"
( 1.14mm)
Fig.
20
SPECIAL
INSTRUCTIONS
NEEDLE
LEVER
When
adjusting needle lever or replac-
ing
related
parts,
follow instructions in
sequence
as
listed:
1.
Install
11
0
11
rings
(A,
Fig.
18)
onto
needle lever stud
(B)
and
thrust
collar
(C).
2.
With
needle lever
(D)
in
machine
and
positioned properly;
insert
stud (B)
through hole in needle lever until
its
shoulder contacts the needle lever
and
the
word
11
UP
11
on
stud
is
in the upright
position.
While
making
sure
no
binding
exists
in the needle bar
link,
secure
stud
(B)
with the front
set
screw
in
top of
machine
bed.
3.
Install
temper
load ring
(E)
and
com-
pression
cups
(F)
onto stud (B), then
push
ring
and
cups
through
opening
in
machine
bed.
4.
Install
thrust
collar
(C)
onto stud
(B)
being careful not to
damage
11
0
11
ring.
Compress
components
together
by
tighten-
ing
screw
(G)
until
washer
(H)
bottoms
against stud
{B).
Secure stud
(B)
in
position using the rear
set
screw
in top
of
bed.
5.
To
check
temper
load ring for proper
com-
pression,
remove
screw
(G)
from
stud (B)
and
loosen rear
set
screw
in
top
of
bed.
Thrust
collar
(C)
should spring out
.003
-
.007
inch (.08 -
.18mm).
Compress
load
ring in reverse order, then tighten
rear
set
screw.
6.
With
indented
11
UP
11
on
stud
(B)
in
upright
position,
install
bearing
oiler
(J)
so
its
hook
sets
in
oil
supply hole
(K)
of
stud.
When
hook
and
stud are secured in
their
proper positions, the proper
amount
of
oil
will
be
channeled to stud for lub-
ricating
needle lever
(D).
ALIGNING
MAINSHAFT
TO
CRANKSHAFT
As
viewed
looking
down
from
rear
of
machine, spot
screws
(A,
Fig.
19)
in
the
couplings
must
align with the spots in the looper drive crank
(B)
and
set
screws
(C)
must
align with the
flats
on
crankshaft
(D)
and
mainshaft (E). Mainshaft
must
be
positioned
laterally
with
.045
inch
(1.14mm)
clearance
between
the
right
side of
its
head
and
the
bed
casting as
shown
in Fig.
20.
20
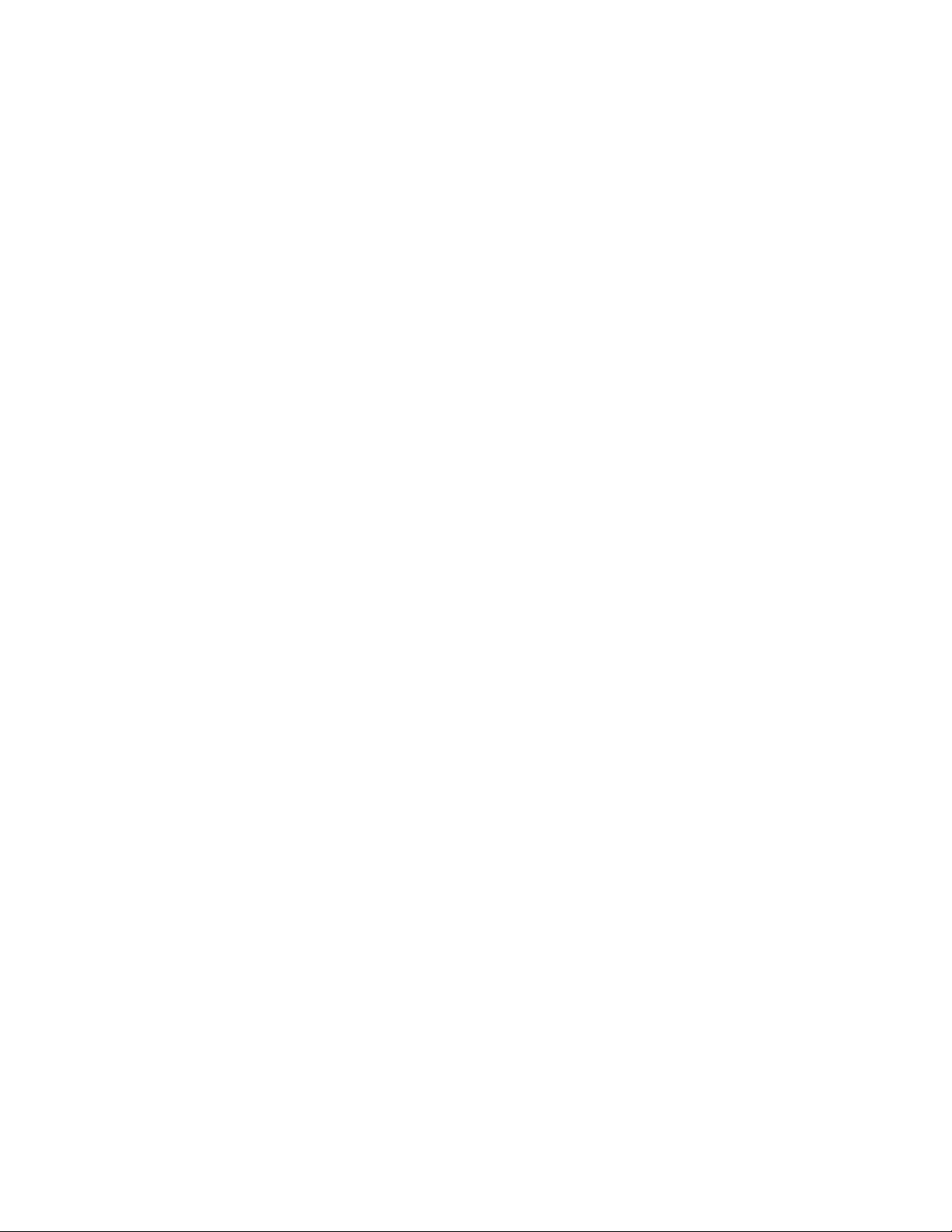
From the library of: Superior Sewing Machine & Supply LLC
ALIGNING
MAINSHAFT
TO
CRANKSHAFT
(Continued)
Looper
drive
Crank
(B,
Fig.
19)
must
be
positioned
laterally
with 1/32 inch
(.8mm)
clearance
between
it
and
mainshaft
(E)
as
shown
in Fig.
19.
Once
these
set-
tings are
made,
it
is
very
important
that
the couplings are tightened in the follow-
ing sequence for best performance.
Tighten spot
screws
(A)
temporarily, to the looper drive crank. Tighten
set
screws
(C) temporarily, to the crankshaft
and
mainshaft.
Torque
screws
(F)
to
19
-
__
21
in.
lbs.
(22-24cm/kg).
Loosen
spot
screws
(A)
and
set
screws
(C).
Re-tor-
que
screws
(F)
to
19-21
in.
lbs.
(22
-
24cm/kg), then, torque screws
(A
and
C)
to
19-21
in. lbs.
(22
-
24cm/kg).
The
oil
drip plate
(A,
Fig.
21)
located in the
oil
reservoir should
be
positioned with
its
tip
in the recessed
cut
out in the
bed
casting,
as
far to
the
left
as
possible without touching.
It
has
elongated
mounting
holes
and
can
be
adjusted
by
loosening
(2)
screws
(B)
in
top
of
the
oil
reservoir
back
cover
to position
as
required, retighten
screws.
•
Fig.
21
21
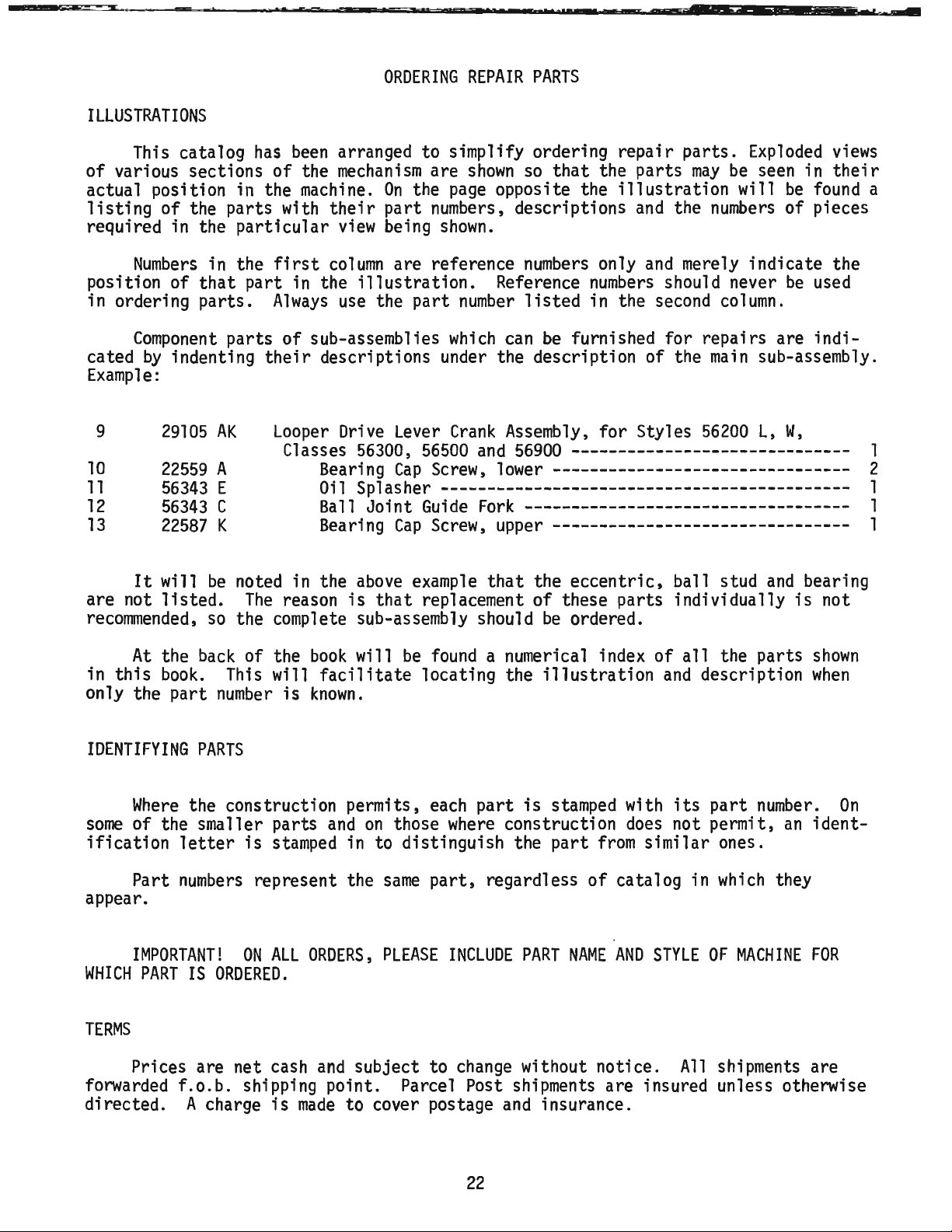
From the library of: Superior Sewing Machine & Supply LLC
ORDERING
REPAIR
PARTS
ILLUSTRATIONS
This catalog
has
been
arranged to simplify ordering
repair
parts.
Exploded
views
of
various sections
of
the
mechanism
are
shown
so
that
the parts
may
be
seen in
their
actual position in the
machine.
On
the
page
opposite the
illustration
will
be
found
a
listing
of the parts with
their
part
numbers,
descriptions
and
the
numbers
of
pieces
required in the
particular
view
being
shown.
Numbers
in the
first
column
are reference
numbers
only
and
merely indicate the
position of
that
part
in the
illustration.
Reference
numbers
should never
be
used
in ordering
parts.
Always
use
the
part
number
listed
in the
second
column.
Component
parts
of
sub-assemblies
which
can
be
furnished for repairs are
indi-
cated
by
indenting
their
descriptions under the description of the
main
sub-assembly.
Example:
9
10
11
12
13
29105
AK
22559
A
56343
E
56343
C
22587
K
Looper
Drive
Lever
Crank
Assembly,
for Styles
56200
L,
W,
Classes
56300,
56500
and
56900
------------------------------
1
Bearing
Cap
Screw,
lower--------------------------------
2
Oil
Splasher--------------------------------------------
1
Ball
Joint
Guide
Fork-----------------------------------
1
Bearing
Cap
Screw,
upper--------------------------------
1
It
will
be
noted in the
above
example
that
the
eccentric,
ball stud
and
bearing
are not
listed.
The
reason
is
that
replacement of these parts individually
is
not
recommended,
so
the complete sub-assembly should
be
ordered.
At
the
back
of the
book
will
be
found
a numerical index of
all
the parts
shown
in
this
book.
This
will
facilitate
locating the
illustration
and
description
when
only the part
number
is
known.
IDENTIFYING
PARTS
Where
the construction permits,
each
part
is
stamped
with
its
part
number.
On
some
of the smaller parts
and
on
those
where
construction
does
not permit,
an
ident-
ification
letter
is
stamped
in to distinguish the
part
from
similar ones.
Part
numbers
represent the
same
part,
regardless
of
catalog in
which
they
appear.
IMPORTANT!
ON
ALL
ORDERS,
PLEASE
INCLUDE
PART
NAME
AND
STYLE
OF
MACHINE
FOR
WHICH
PART
IS
ORDERED.
TERMS
Prices are net cash
and
subject to
change
without notice.
All
shipments are
forwarded
f.o.b.
shipping point. Parcel Post shipments are insured unless otherwise
directed. A charge
is
made
to cover postage
and
insurance.
22
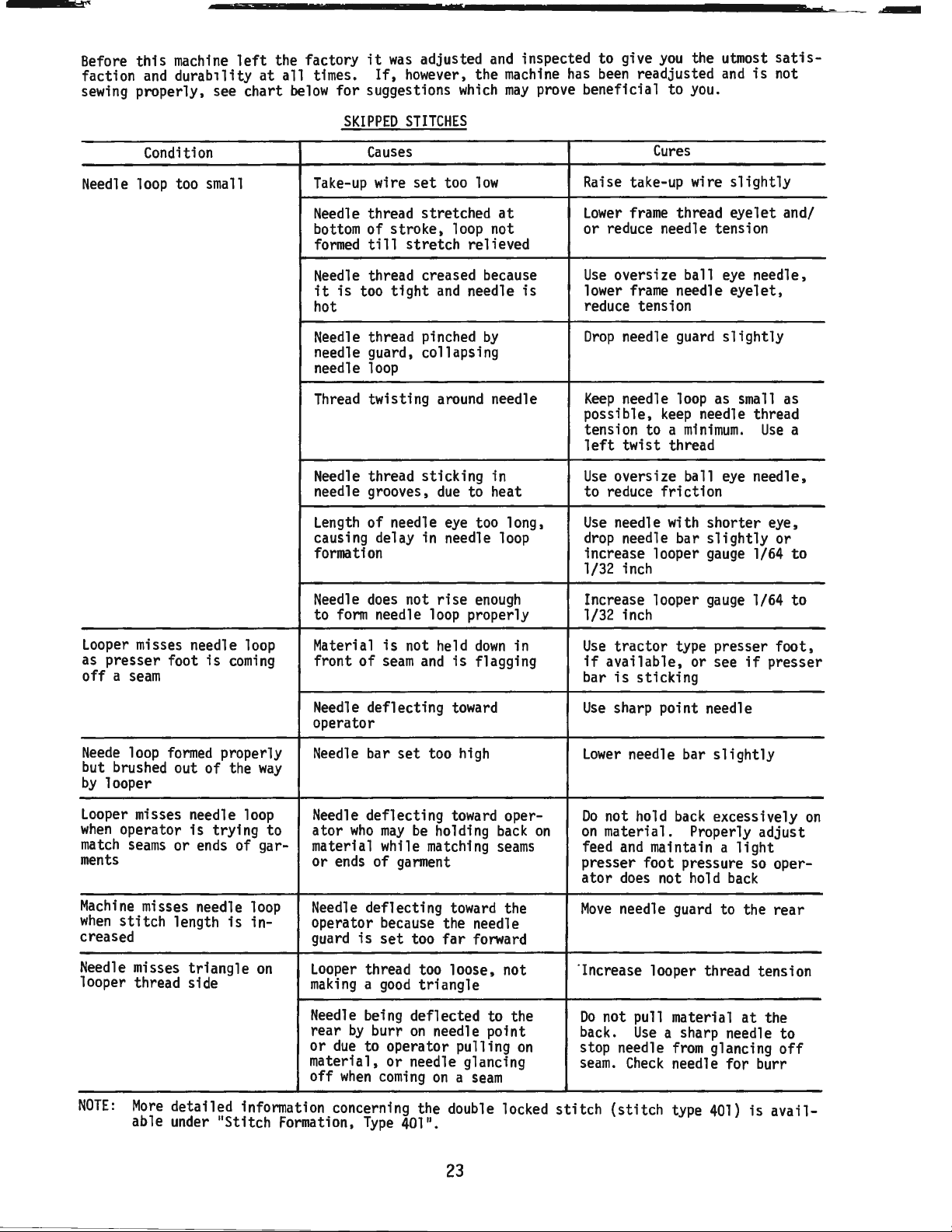
From the library of: Superior Sewing Machine & Supply LLC
Before
this
machine
left
the factory
it
was
adjusted
and
inspected to give
you
the utmost
satis-
faction
and
durability
at
all
times.
If,
however,
the
machine
has
been
readjusted
and
is
not
sewing
properly, see chart
below
for suggestions
which
may
prove
beneficial to
you.
SKIPPED
STITCHES
Condition
Causes
Cures
Needle
loop
too
small
Take-up
wire
set
too
low
Raise
take-up wire
slightly
Needle
thread stretched
at
Lower
frame
thread eyelet and/
bottom
of
stroke, loop not
or reduce needle tension
formed
till
stretch
relieved
Needle
thread creased because
Use
oversize ball
eye
needle,
it
is
too
tight
and
needle
is
lower
frame
needle eyelet,
hot
reduce tension
Needle
thread pinched
by
Drop
needle
guard
slightly
needle guard, collapsing
needle
loop
Thread
twisting
around
needle
Keep
needle
loop
as
small
as
possible,
keep
needle thread
tension to a
minimum.
Use
a
left
twist thread
Needle
thread sticking in
Use
oversize ball
eye
needle,
needle grooves,
due
to heat
to reduce
friction
Length
of needle
eye
too long,
Use
needle with shorter eye,
causing delay in needle
loop
drop
needle bar
slightly
or
formation
increase looper
gauge
1/64
to
1/32 inch
Needle
does
not
rise
enough
Increase looper
gauge
1/64 to
to
form
needle
loop
properly
1/32 inch
Looper
misses needle
loop
Material
is
not held
down
in
Use
tractor
type presser
foot,
as
presser foot
is
coming
front
of
seam
and
is
flagging
if
available, or see
if
presser
off
a
seam
bar
is
sticking
Needle
deflecting
toward
Use
sharp point needle
operator
Neede
loop
formed
properly
but brushed out of the
way
Needle
bar
set
too
high
Lower
needle bar
slightly
by
looper
Looper
misses needle
loop
Needle
deflecting
toward
oper-
Do
not
hold
back
excessively
on
when
operator
is
trying to
ator
who
may
be
holding
back
on
on
material.
Properly adjust
match
seams
or
ends
of gar-
material while
matching
seams
feed
and
maintain a
light
ments
or
ends
of
garment
presser foot pressure
so
oper-
ator
does
not
hold
back
Machine
misses needle
loop
Needle
deflecting
toward
the
Move
needle
guard
to the rear
when
stitch
length
is
in-
operator because the needle
creased
guard
is
set
too
far
forward
Needle
misses
triangle
on
Looper
thread too loose, not
"Increase looper thread tension
looper thread
side
making
a
good
triangle
Needle
being deflected to the
Do
not pull material
at
the
rear
by
burr
on
needle point
back.
Use
a sharp needle to
or
due
to operator pulling
on
stop needle
from
glancing
off
material,
or
needle glancing
seam.
Check
needle for burr
off
when
coming
on
a
seam
NOTE:
More
detailed information concerning the
double
locked
stitch
(stitch
type
401)
is
avail-
able
under
"Stitch Formation,
Type
401".
23