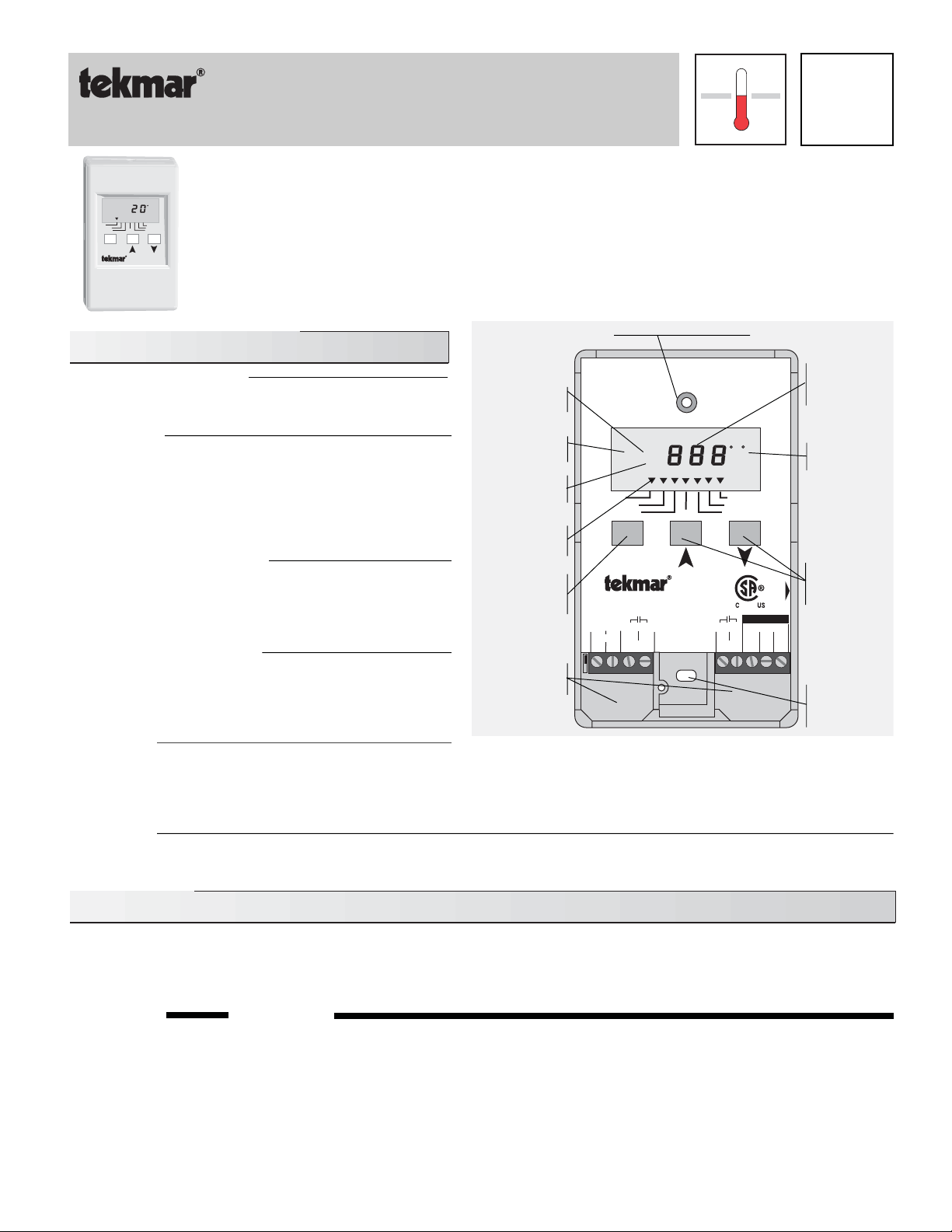
- Data Brochure
Difference Setpoint Control 155
D 155
06/10
The Difference Setpoint Control 155 is a microprocessor-based control that allows the transfer of heat from a source
to a storage tank whenever the temperature difference between the two is greater than the selected ΔT setpoint.
Additional setpoints are also included to help prevent the storage tank from overheating or the source from freezing.
F
ΔT
Source
Diff'l
Storage
Item
Difference Setpoint
Control 155
Both drainback and draindown systems can be used with this control.
Minimum
Maximum
ΔT •hours
Several displays provide a variety of useful information. The control can display the Maximum and Minimum
temperatures measured by both the Storage and Source sensors as well as the total heat transferred from the source
to the storage.
• New Solar Sensor 085 immersion type sensor included!
Hole for mounting screw
Sequence of Operation
Powering up the control
After the Difference Setpoint Control 155 is powered up,
the LCD segments are turned on for 3 seconds.
ΔT Setpoint
The control measures the difference between the Source
and the Storage temperatures (ΔT). When this ΔT is
greater than the ΔT setpoint, Relay 1 is turned on to
transfer heat from the source to the storage. If the ΔT drops
below the ΔT setpoint less the ΔT differential, Relay 1 is
turned off.
Maximum Storage Setpoint
If the Storage temperature rises above the Maximum
Storage setting, Relay 1 is turned off. This relay remains off
until the Storage temperature drops below the Maximum
Storage setting less its differential.
Minimum Source Setpoint
If the Source temperature drops below the Minimum Source
setting, Relay 1 is turned off. This relay remains off until the
Source temperature rises above the Minimum Source
setting plus its differential.
Relay 1
operation
Programming
mode indicator
Relay 2
operation
identifiers
Item selection
and display
button
Wiring Chamber
and terminals
Item
Meets Class B:
Canadian ICES
FCC Part 15
Made in Canada
tektra 906-08
PRGM
ΔT
Source
Storage
Item
Difference Setpoint
Control 155
34
21
Power
C –
R +
Relay 1
Drainback l Draindown
Power: 24 V (ac) ± 10% 50/60 Hz 3 VA
24 V (dc) ± 10% 0.03A
Relay: 240 V (ac) 10 A 1/3hp
1
2
HEAT
Diff’l
Signal wiring
must be rated
at least 300V
Minimum
Maximum
ΔT • hours
5
Relay 2
FC
6
Com
H11161E
No power
No Power
8
7
Src
Stor
9
Date Code
Display for
temperatures
and setpoints
°C or °F
indicators
Programming
and display
buttons
Hole for
mounting
screw
Draindown
When the DIP switch is set to draindown, Relay 2 is closed until the Source temperature drops below the Minimum Source setting.
If Relay 2 is connected to a drain valve, the heat transfer fluid can be drained from the source when Relay 2 is opened. Once the
Source temperature rises above the Minimum Source setting plus the Minimum Source Differential, Relay 2 is closed and the control
continues with ΔT setpoint operation. See the Application Brochures A 155 for the correct wiring of Relay 2.
Drainback
If the DIP switch is set to drainback, Relay 2 is turned on (closed) for 3 minutes whenever Relay 1 is turned on. Relay 2 is typically
connected to a booster pump to overcome gravity head and prime a siphon.
Installation
Caution
Step One Getting ready
Note: Carefully read the Sequence of Operation section in this brochure to ensure that you have chosen the proper control and understand
: Improper installation and operation of this control could result in damage to the equipment and possibly even
personal injury. It is your responsibility to ensure that this control is safely installed according to all applicable codes
and standards. This electronic control is not intended for use as a primary limit control. Other controls that are
intended and certified must be placed into the control circuit.
Check the contents of this package. If any of the contents listed are missing or damaged, please refer to the Limited Warranty
and Product Return Procedure on the back of this brochure and contact your wholesaler or tekmar sales agent for assistance.
Type 155 includes:
• One Difference Control 155 • One Universal Sensor 071, One Solar Sensor 085
• Data Brochures D 155, D 070, D 085, D 001
• Application Brochure A 155
Other information available:
• Essay E 001
its functions within the operational requirements of your system.

Step Two
Mounting
The control is mounted in accordance with the instructions in the Data Brochure D 001.
Step Three
Rough-in wiring
All electrical wiring terminates in the two wiring chambers at the bottom front of the control. If the control is to be mounted on
an electrical box, the wiring can be roughed-in at the electrical box prior to installation of the control (see Brochure D 001).
Standard 18 AWG solid wire is recommended for all low voltage wiring to this control.
Power should not be applied to any of the wires during the rough-in wiring stage.
• Install the Source Sensor 085 and Storage Sensor 071 according to the instructions in Data Brochure D 085 and D 070, and run
the wiring back to the control. Do not connect the wires to the terminals yet.
• EITHER: Install a 24 V (ac) Class 2 transformer with a minimum 5 VA rating and run the wiring from the transformer to the control.
A Class 2 transformer must be used.
OR: Install a 24 V (dc) source and run the wiring back to the control.
• Run wiring back to the control from the devices connected to Relay 1 and Relay 2.
Do not connect either of the transformer secondary wires to ground.
Step Four
Testing and connecting the wiring
Caution These tests are to be performed using standard testing practices and procedures and should only be carried out by properly
trained and experienced persons. A good quality electrical test meter, capable of reading from at least 0 — 200 Volts, and
at least 0 — 2,000,000 Ohms, is essential to properly test this control. At no time should voltages in excess of 27 V (ac or
dc) be measured at any of the wires connected to the control.
Test the sensors
• This test must be performed
power is applied to the control and
before
the sensors are connected to the terminal strip.
before
Test the sensors according to the instructions in the enclosed Data Brochure D 085 and D 070.
Test the power supply
• Ensure exposed wires are not grounded or in contact with other wires, then turn on the power supply. If a 24 V (ac) transformer
is used, make sure the voltmeter is set to AC. With the voltmeter leads connected to the secondary side of the transformer, you
should measure between 21 and 27 V (ac). If a DC power supply is used, make sure the voltmeter is set to DC. Connect the positive
lead from the voltmeter to the positive terminal on the DC source and the negative lead from the voltmeter to the negative terminal
on the DC source. The voltmeter should measure between 21 and 27 V (dc).
• Turn off the power and complete the electrical connections to the terminal strip of the control.
Power and output connections
The installer should test to confirm that no voltage is present at any of the wires.
• EITHER: Connect the 24 V (ac) power supply to terminals
Power C- and R+
OR: Connect the negative (-) lead from the 24 V (dc) source to the Power C- terminal
Connect the positive (+) lead from the 24 V (dc) source to the Power R+ terminal
Note: The control will not operate if the DC leads are reversed.
• Connect the Relay 1 controlled device to terminals
• Connect the Relay 2 controlled device to terminals
Relay1
Relay 2
(3 and 4)
(5 and 6)
Sensor connections — Caution, voltage is never applied to these terminals
• Connect the Source Sensor
• Connect the Storage Sensor
085 to terminals
071 to terminals
Com Sen and Src Sen
Com Sen and Stor Sen
(7 and 8)
(7 and 9)
(1 and 2)
1C-2R+34
Power
24 V
power
supply
10A
Relay 1
Relay 1 closes to
transfer heat
from the source
to the storage
10A
6
5
Relay 2
Relay 2 closes to
satisfy drainback
or draindown
requirements
Do not apply
power here
89
7
Com
Src
Sen
Sen
Source
Sensor
085
Stor
Sen
Storage
Sensor
071
Settings
PROGRAMMING
PRGM
ΔT
Source
Storage
Item
Press and Release
all three buttons at the
same time to begin
programming. The first
item displayed is the
“ΔT setpoint”.
PRGM
ΔT
Source
Storage
Item
Press and Release
the “Item” button to
change the display to
the “Maximum Storage
Setpoint”.
F
Use the arrow
Minimum
keys to set the
Maximum
Diff'l
ΔT • hours
“ΔT setpoint”.
F
Use the arrow
Minimum
keys to set the
Maximum
Diff'l
ΔT • hours
Item
Item
“Maximum
Storage
Setpoint”.
PRGM
ΔT
Source
Storage
Item
Press and Release
the “Item” button to
change the display to
the “ΔT Differential”.
PRGM
ΔT
Source
Storage
Item
Press and Release
the “Item” button to
change the display to
the “Maximum Storage
Differential”.
F
Minimum
Maximum
Diff'l
ΔT • hours
F
Minimum
Maximum
Diff'l
ΔT • hours
Item Item Item
Use the arrow
keys to set the
“ΔT Differential”.
Item Item
Use the arrow
keys to set the
“Maximum
Storage
Differential”.
PRGM
ΔT
Source
Storage
Item Item
Press and Release
the “Item” button to
change the display to
the “Minimum Source
Setpoint”.
PRGM
ΔT
Source
Storage
Item
Press and Release
the “Item” button to
change the display to
“°F” or “°C”.
F
Use the arrow
Minimum
keys to set the
Maximum
Diff'l
ΔT • hours
Minimum
Maximum
Diff'l
ΔT • hours
F
“Minimum
Source
Setpoint”.
Use the arrow
keys to switch
between “°F”
and “°C”.
PRGM
ΔT
Source
Storage
Press and Release
the “Item” button to
change the display to
the “Minimum Source
Differential”.
Note: The control automatically
exits programming when
the buttons are left alone
for 20 seconds.
F
Minimum
Maximum
Diff'l
ΔT • hours
2
Use the arrow
keys to set the
“Minimum Source
Differential”.