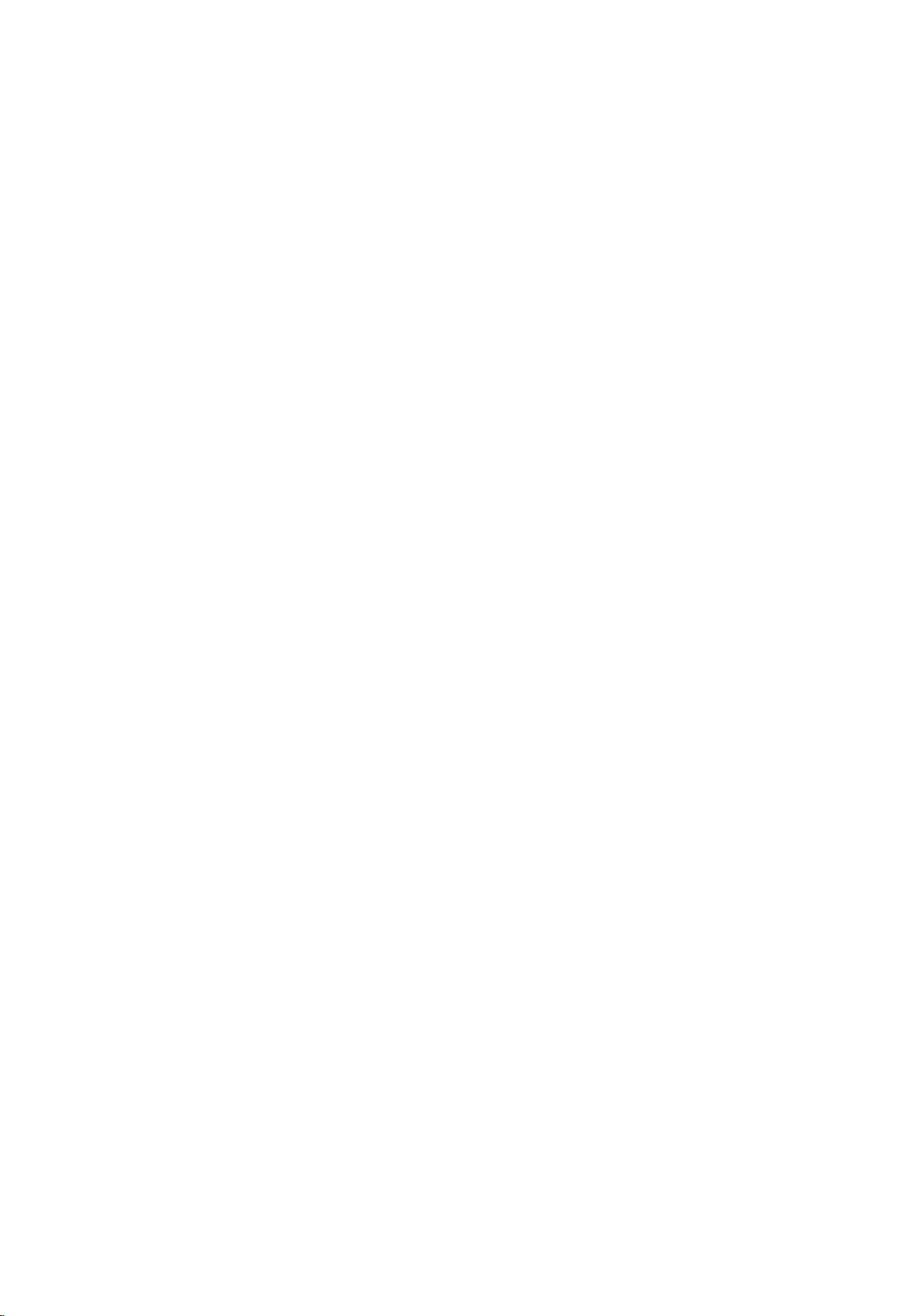
5.
SYSTEM
Parameter
5.1
Parameter
5.2
Parameter
5.3
Details
5.4
PARAMETER
Display
Setting
Table
of
Parameter
...
41
.
41
41
44
54
DIAGNOSTIC
6.
Operating
6.1
Display
6.2
Details
6.3
Correspondence
6.4
TROUBLESHOOTING
7.
7.1
Troubleshooting
7.2
Troubleshooting
Alarm
7.3
7.4
Remedies
When
7.5
Troubleshooting
7.6
For
7.7
EXCHANGE
8.
Fuse
8.1
Exchange
8.2
8.3
Exchange
APPENDIX
FUNCTION
Procedure
Data
Signals
of
Display
Against
no
Alarm
Better
Understanding
PROCEDURES
Exchange
of
of
Table
between
Method
when
and
is
in
Power
Master
Alarms
Displayed,
(DGN)
of
Diagnostic
Diagnostic
by
Signal
I/O
Power
Countermeasures
Servo
Supply
PCB
is
but
System
of
Troubleshooting
Unit
Function
Function
Turned
NC
DGN
does
Number
On
not
and
Operate
Connector
Normally
Pin
Number
97
97
101
102
114
116
116
116
119
131
153
161
176
181
181
183
183
APPENDIX
1.1
1.2
1.3
1.4
APPENDIX
2.1
2.2
APPENDIX
3.1
3.2
3.3
3.4
3.5
3.6
CONNECTIONS
1.
Connection
Connection
Connection
Connection
RELATION
2.
When
the
When
a
Separate
3.
DETAILED
Input/Output
Adjustment
Voltage
OVP
Monitor
and
Changing
Changing
Portable
to
to
Bubble
ASR43
to
to
ASR33
BETWEEN
DIRECTIONS
Coder
Pulse
Type
DESCRIPTIONS
Terminals
and
Setting
Circuit
OCL
Functions
the
Stablizing
PC
the
Board
BETWEEN
Reader
Tape
Cassette
CABLE
OF
SERVO
is
Mounted
Coder
Pulse
and
Ratings
Unit
Unit
CONTROL
.
Adapter
CONNECTIONS
MOTOR
Inside
is
OF
.
.
the
Used
POWER
UNIT
AND
DC
Servo
STABILIZING
.
I/O
AND
DEVICE
ROTATING
Motor
UNIT
.
184
184
185
186
187
188
188
189
194
194
196
198
198
198
199

1.1
Table
Name
Master
Power
Programable
Additional
Additional
(ADD,
Keyboard
CRT
CRT
Magnetic
PCBs
Table
Name
1.1(b)
unit
unit
1.1(c)
of
PCB
supply
MEM)
and
of
PCB
PCB
controller
I/O
memory
PCB
cabinet
units
PCB
or
PCB
(PC2)
PCB
Unit
unit
20m
sequence
on
the
/Units
or
Control
(PCI)
above
of
Tape
Unit
PCB
drawing
list
Reader
PCB
drawing
or
unit
No.
A16B-1000-0010
A20B-1000-0410
A20B-0008-0630
A20B-0008-0640
A16B-1200-0220
A16B-1600-0042
A13B-0055-C001
A61L-0001-0076
A16B-1200-0370
not
are
all
(RS232C
specification
No.
specification
for
used
interface,
FS
2T-A
AC
Unit
specification
drawing
A02B-0058-B501
A
14B
(Option)
(Option
(Option)
MDI/CRT
A02B-0063-C001
CRT
A13-0055-C001
Option
FS
and
200V)
Unit
specification
drawing
No.
-0067-
unit
3T-C.
No.
BO
For
)
panel
for
PC-MODEL
02
PC-MODEL
D
H
Photoamplifier
RS232C
Additional
Table
Name
M
Table
series
interface
1.1(d)
of
1.1(e)
Unit
velocity
Multitap
Servo
Manual
Position
Position
power
PCB
Other
of
Name
input
transformer
pulse
coder
coder
PCB
supply
/Units
control
Units
Unit
transformer
generator
(6000rpm)
(4000rpm)
A20B-0007-0750
A20B-0008-0280
A14L-0066-0002
M
Series
of
PCB
drawing
Velocity
specification
No.
Control
Unit
A20B-0009-0320
A13B-0073-B001
A13B-0074-B001
(Portable
Unit
specification
drawing
A06B-6047-H001
or
type)
No.
A06B-6047-H002
A06B-6047-H003
A06B-6047-H004
A06B-6047-H005
A06B-6047-H040
A06B-6047-1I041
Specification
drawing
No.
A80L-0001-0176
See
3.4
A860-0201-T001
A86L-00
26-000
00
2
In
A86L-0026-0001#102
6
?
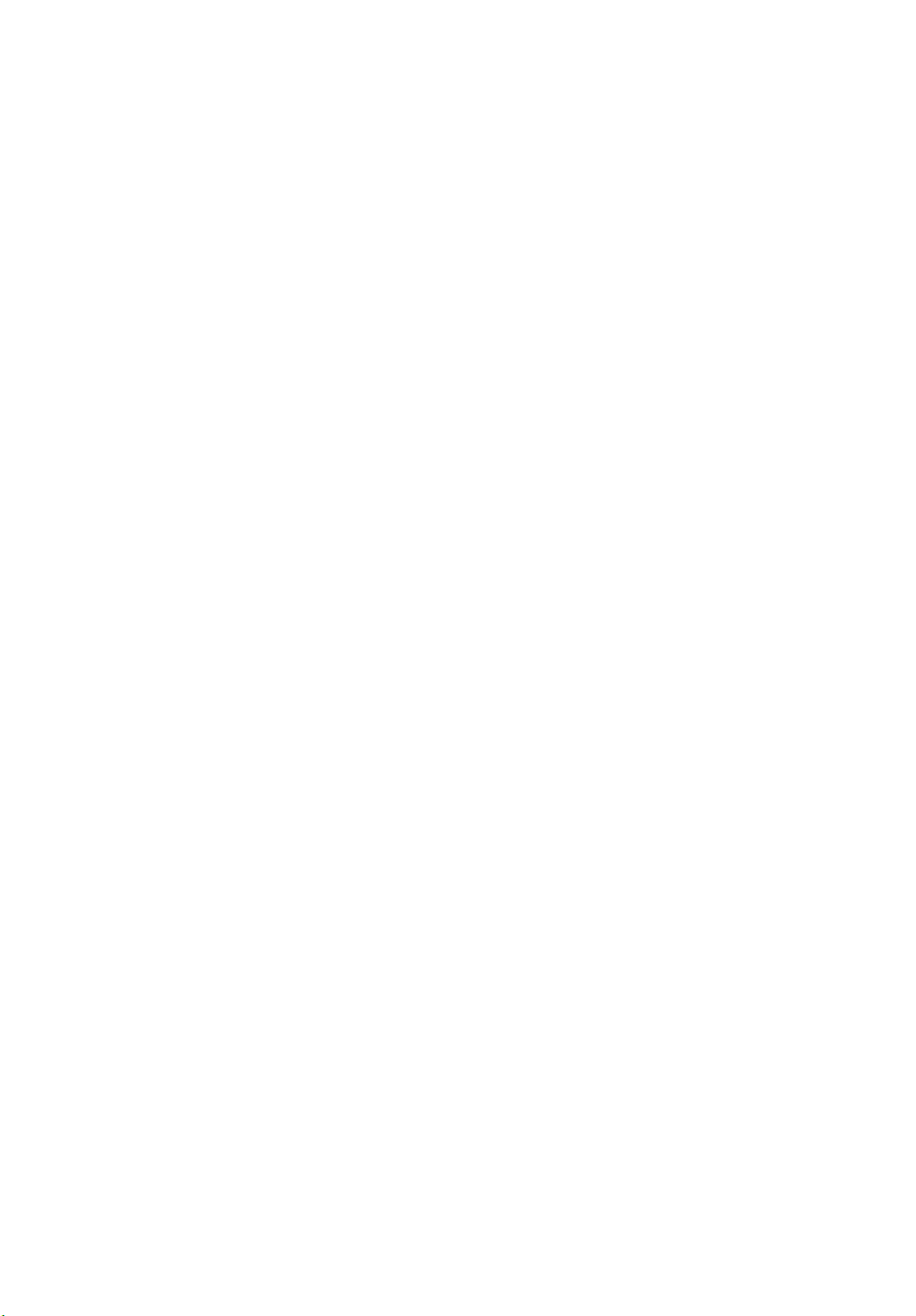
2.
2.
check
of
preventive
2.1
DAILY
(1)
MAINTENANCE
FS
3T-C
points
Maintenance
as
On
the
Preventive
0
Arrangement
Routine
°
Provision
°
following
The
Measuring
Instrument
AC
voltmeter
maintenance
and
much
other
maintenance
check
of
Tools
instruments
FS
2T-A
as
possible
hand,
user's
to
of
maintenance
and
adjustment
spare
maintenance
parts
are
run
needs
less
designed
from
sections
the
the
tools
Requirements
AC
power
measured
than
the
viewpoints
concerned
NC
machine
following
tools
are
recommandable
voltage
withatolerance
+2%.
to
facilitate
of
are
tool
items.
can
their
maintenance.
requested
under
.
be
of
a
good
adjustments
to
fully
condition
AC
power
Use
by
reducing
understand
for
a
long
voltage
periodical
the
concept
time.
measurement
DC
Oscilloscope
(2)
Tools
Cross-recessed
Conventionals
(3)
Chemicals
Tape
Cleaning
2.2
FS
tool
cabinet
periodically,
voltmeter
reader
of
3T-C
with
referring
cleaning
Cooling
and
built-in
(
)
+
(-)
screwdrivers:
System
FS
2T-A
to
Maximum
Tolerance:
(A
Frequency
higher,
screwdrivers:
solution
main
NC
employs
the
machine
digital
required)
(absolute
body
tool
2
Large,
a
division
heat
Less
voltmeter
bandwidth
channels
Large
do
not
exchanger
builder's
10
than
and
medium,
alcohol)
employ
V,
30V
+2%
be
may
5MHz
medium
and
and
any
instruction
power
DC
or
Adjustment
photoamplifier,
sizes
small
sizes
oil
filtei*,
air
or
an
air
filter.
manual.
etc.
voltage
Clean
of
tape
etc.
However,
the
measurement
reader
the
machine
cooling
system
11
-
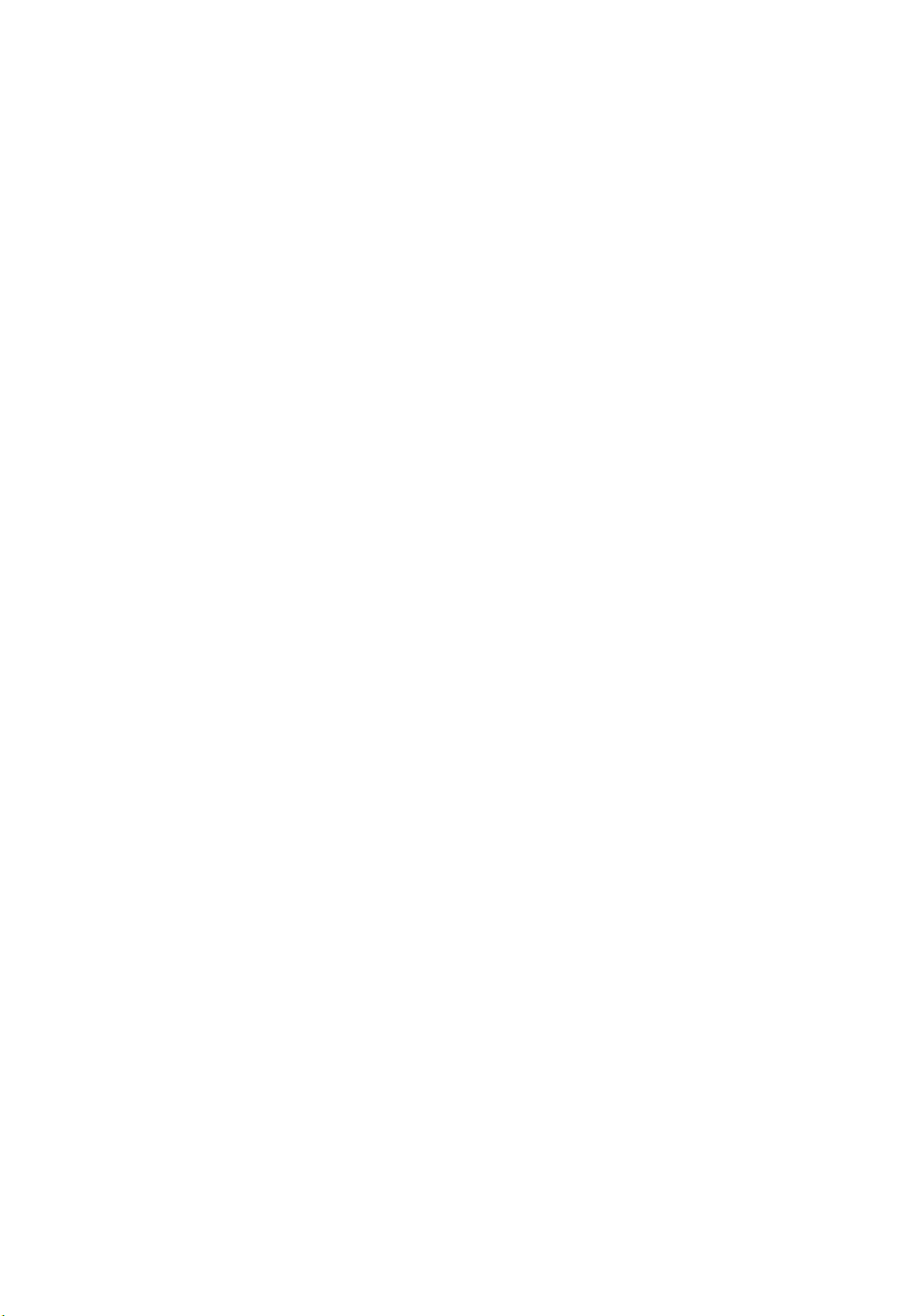
3.
3.
INSTALLATION
This
normally
This
By
section
after
observing
section
installing
finally
PROCEDURES
describes
it.
these
describes
the
procedures,
data
setting,
to
be
adjustment,
NC
can
recorded
be
as
and
checked
installation
check
procedures
appropriately
results.
for
operation
the
at
installation
NC
time.
3.1
(1)
Table
No.
1
2
3
4
5
6
Basic
Visual
(a)
(b)
(c)
3(a)
Paragraph
3.1
3.2
3.3
3.4
3.5
3.6
Check
inspection
Check
Check
Check
Installation
before
NC
NC
cables
Basic
Checking
transformer
Setting
Check
disconnected
Check
connected
Recording
Turning
for
dirt
for
internal
and
Procedures
Description
check
the
the
after
after
data
on
Power
and
damage
damage,
bundled
before
input
taps
taps
turning
turning
Supply
wires
turning
of
at
installation
in
looseness
for
power
M
series
on
power
on
power
appearance.
damage
on
supply
servo
time
of
power
of
transformer
supply
supply
PCB,
(exfoliation
supply
control
when
when
and
unit
and
motor
power
motor
power
disconnection
of
sheathing,
setting
cable
cable
of
etc.)
PCB.
the
has
has
been
been
(2)
Check
(a)
(b)
(c)
(d)
(e)
(f)
screw
Terminal
Tex'minal
Terminal
Terminal
Terminal
Check
terminals
board
board
board
board
board
terminal
for
of
power
of
tape
of
velocity
of
multitap
of
servo
boards
normal
reader
for
connections.
supply
unit.
conti'ol
input
transformer.
normal
unit.
unit.
transformer
mounting
16
-
(option)
condition
.
of
covers,
if
provided.
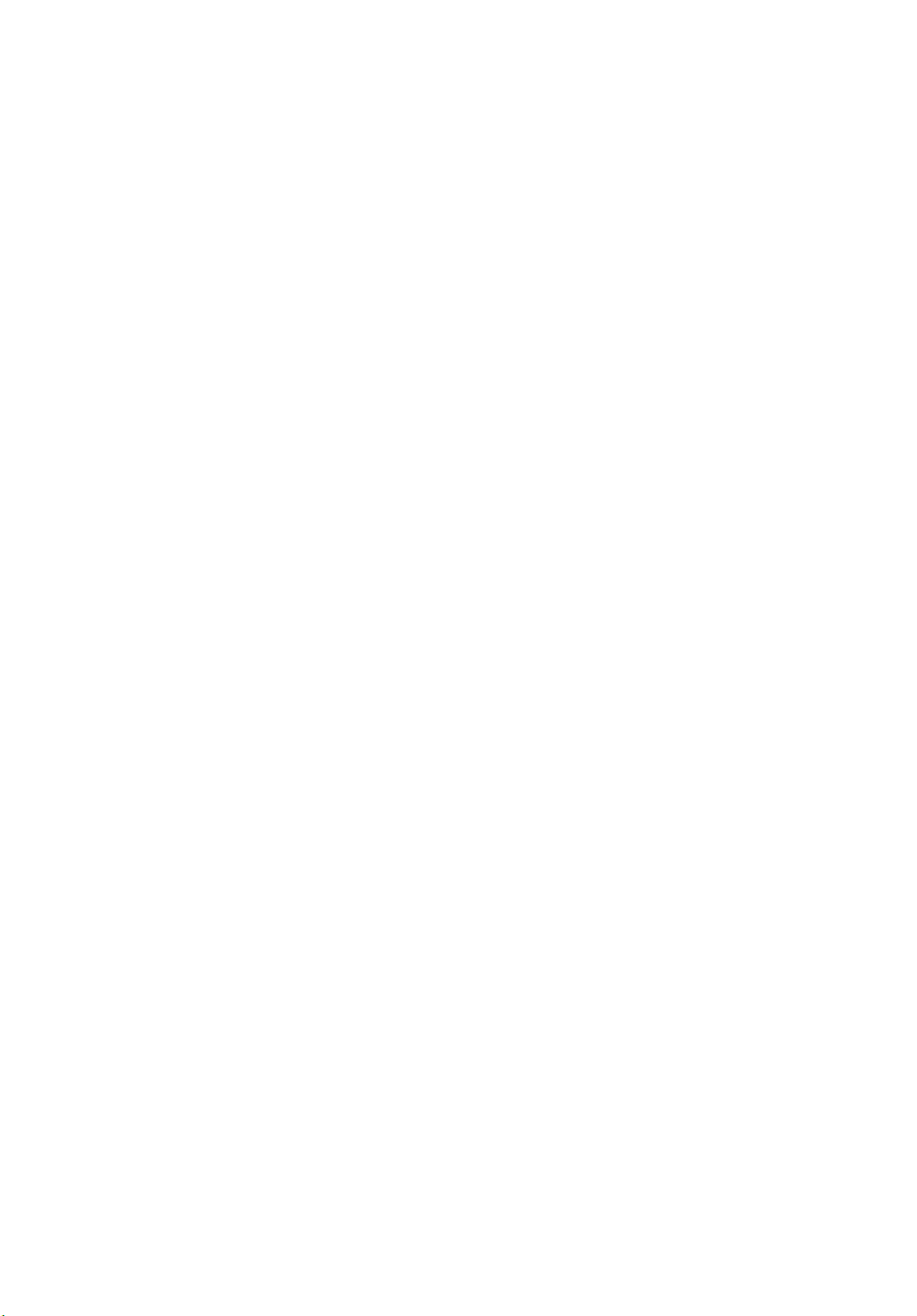
3.1
(5)
(6)
(7)
(8)
Check
(a)
(b)
(c)
Check
Check
(a)
(b)
(c)
(d)
Check
Power
Make
sure
(a)
(b)
(c)
(d)
(e)
(f)
(g)
(h)
(i)
(j)
connectors
Check
Check
Check
of
setting
the
if
Master
Power
Option
Velocity
EROM,
if
supply
sure
that
power
Between
Between
Between
Between
Between
Between
Between
Between
Between
Between
if
if
if
setting
PCB
supply
that
clamp
the
clamp
PCB
control
unit
5V
24V
15V
-15V
5V
5V
5V
24V
24V
15V
for
clamp
plug
PCB
RAM,
check
power
supplies
and
and
and
and
and
and
and
and
and
looseness
screws
screws
plug
unit
LSI,
supply
OV
OV
OV
and
24V
15V
-15V
15V
-15V
-15V
claw
are
OV
is
PCB
HONDA
of
of
of
option
securely
etc.
unit
not
power
are
securely
terminals
grounded
connectors
connector
PCB
mounted
is
to
loosen.
into
mounted
are
not
each
of
master
(BUNDY)
the
setting
onto
grounded
other.
is
IC
PCB
are
fitted
pin
socket
by
tightened.
normally.
the
in
of
using
following
master
an
ohmmeter.
units.
PCB.
Make
in
j)
J
/
/
/
~/ni
/ /
h
/
//
//
/
//
//
y
//////////
A
4
A
4
A
4
4
4
4
4
4
/////,
///
4
4
7
7,
7
7
7
R
4
4
s
4
1=1
paK
o
OPB_//
////////Z//////TT//
Measuring
Points
POWER
//////////////
in
UNIT
Power
)
/
/
n
/
////
Supply
}
n
i
n
/
/
/
/
/
/
/
/
/
/
/
/
/
/
/
/
/
/
/
/
/
/
///
//
TPll
+
5
-\-
5
o
0
0
CP32
o
o
o
AN
+15V
-15
OV
EN
(
ENABLE
(ptM-cr
a
f
V
0
V
)
)
u
c
i
i
1
Unit
18
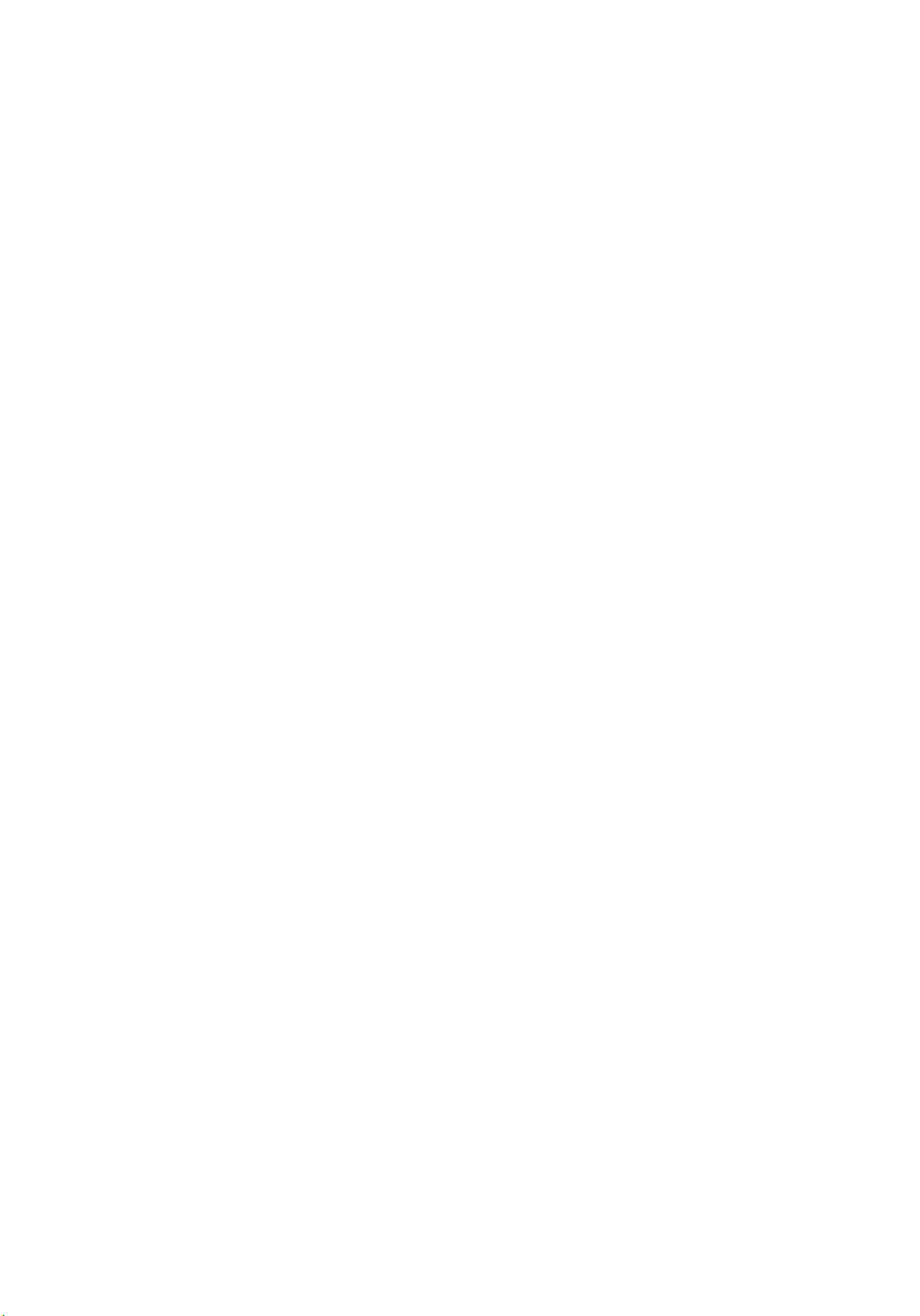
For
rotating
follows.
(a)
(b)
(c)
(d)
Exchange
Exchange
Exchange
Exchange
motor
the
the
the
power
tachogenerator
in
terminal
terminal
cables
the
positions
positions
A1
direction
B
and
signals
A2
for
for
TSAa
signals
signals
with
by
each
and
(+)
command,
PCAa
*PCAa
other.
TSBa
and
with
and
connect
PCBa
*PCBa
each
with
other.
the
with
DC
each
each
(Note
servo
other.
other.
1)
motor
3.5
as
1)
Note
2)
Note
Example)
Velocity
5
This
should
tachogenerator
(X
is
X
When
the
following
unit
control
7
6
A2X
A
or
Z.
DC
connection.
M
8
IX
7
be
.
servo
1
14
PCZX
ID
done
OH
*PCZX
2
a.
15
only
motor
O
IX
16
PCAX
3
9_
H2X
when
is
4
+
V
5
0
1
1
17
*POAX
<J5>
J
o
model
+
PCD
5
1
X
A
pcax
CL
u»czx
N
Ov
~h
n
DC
axis
»
PCAX
1L
Op
P
Ov
r~i
servo
+
+
OH
the
built-in
5M,
the
5
G
7
+
5V
5
V
1
1
8
1
*PCBX
X
3
1
2
1
9
20
1
Ou
is
C
5
J
5
R
1
DC
Model
V
V
X
*PCU>
+
OH2X
servo
motor
reversely
I)
+PCAX
_L_
J£
5
V
S
T
motor
5M
E
is
connected
F
I’CZX
M
used
inside
by
the
the
C
A
0
IX
A
A
X
2
C
D
(3)
Axis
(a)
(b)
(c)
(d)
motion
Apply
parameters
Check
values
parameters
Operate
axis
by
overtravel
an
Move
make
maximum
check
10mm
if
is
the
sure
CMR
the
normally
No.
the
JOG
axis
that
feedrate.
from
position
34
limit
feed
alarm
by
an
MDI,
and
DMR.
control
3000.
and
35.
switch
withalow
detected.
is
JOG
alarm,
and
feed
check
The
mounted
override,
or
such
loop
manual
as
servo
on
an
the
if
gain
the
excessive
27
is
loop
and
rapid
-
axis
set
gain
machine
make
traverse
moves
properly
multiplier
tool
sure
error,
10mm
securely.
or
not.
intentionally,
that
the
while
changing
etc.
is
is
not
The
set
axis
produced
parameter
for
while
stops
the
If
each
override,
not,
moving
moving
even
examine
No.
axis
when
at
37
by
the
and
the