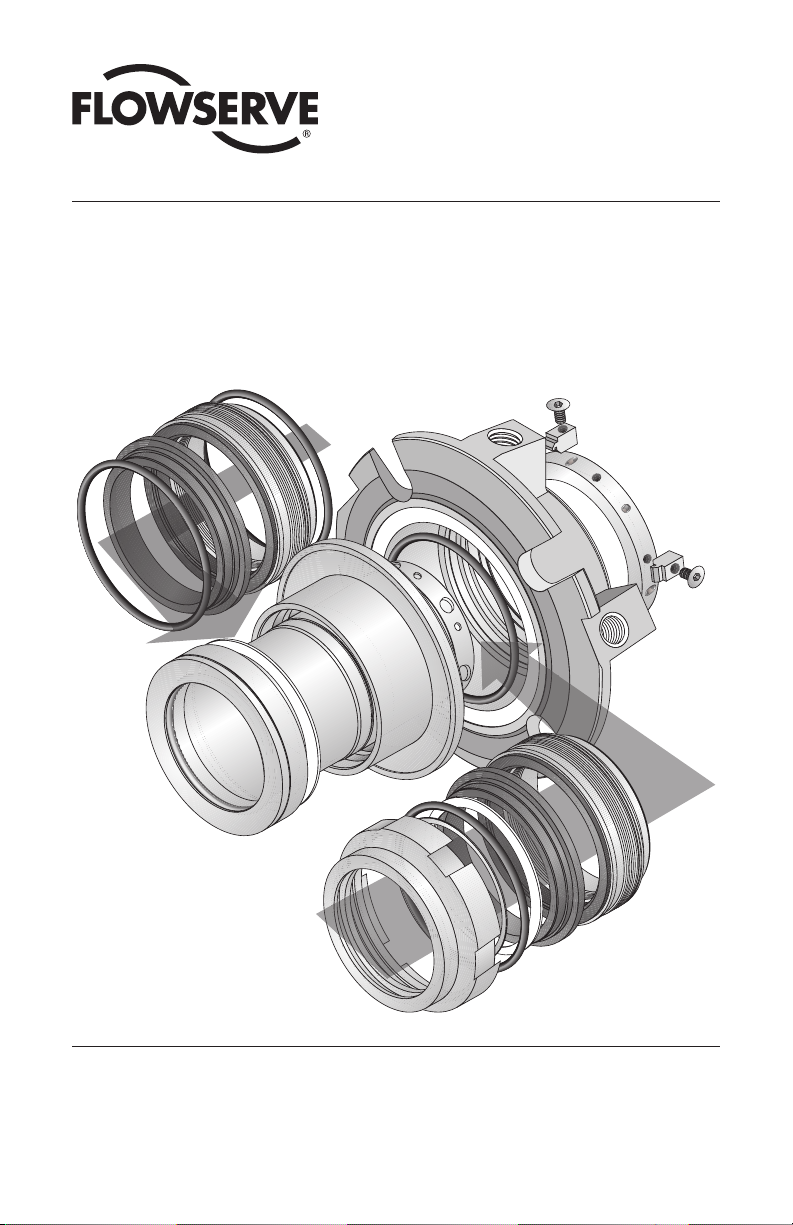
ISC
Flow Solutions Division
ISC2SS
Dual Stationary Bellows Seal
Repair Instructions
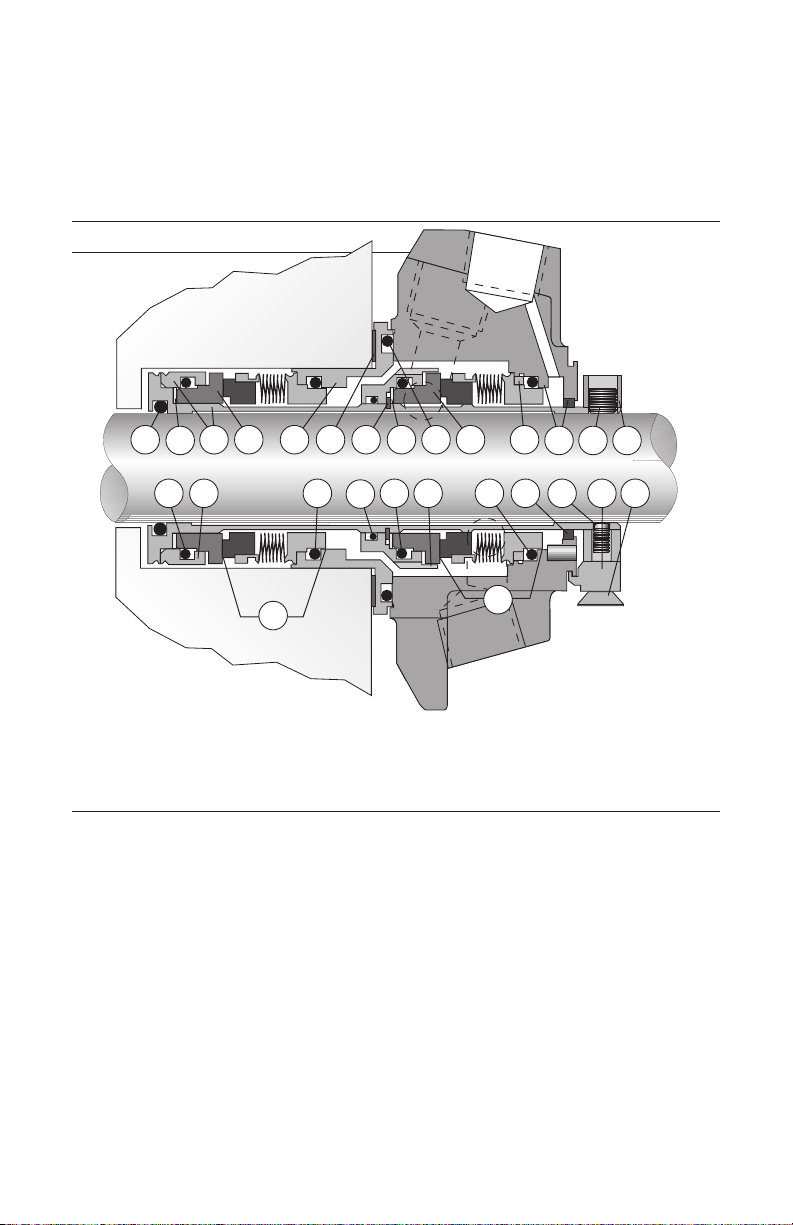
These instructions are written for trained, experienced technicians familiar with the basic
principles and tools involved in the installation, care and service of mechanical seals and seal
support systems. A complete reading of these instructions by personnel in contact with the
equipment is essential to safety. Incorrect installation, operation or maintenance can result in
personal injury or death to personnel and damage to the equipment.
1 Nomenclature
Figure 1
11
M1
6A
Table 1
34 Outboard Bellows Assembly
34A Inboard Bellows Assembly
3B Outboard Mating Ring
3C Inboard Mating Ring
6 Outboard Mating Ring O-ring
6A Inboard Mating Ring O-ring
P Outboard Bellows O-ring
P1 Inboard Bellows O-ring
G Gasket
G1 Inner Gland O-ring
1 Gland Assembly
B Carbon Bushing
1B Gland Drive Ring
1C Inner Gland
1C␣
3C
SL
10A P1
G
RR
11A 6
G1
3B
M
14
1B
P
B␣ 13A CT K
1
13
34
34A
Notes: - Inboard bellows assembly (34A) is interchangeable with outboard bellows assembly (34).
- Inboard mating ring (3C) is interchangeable with outboard mating ring (3B).
- Primary seal O-rings (P, P1, 6, 6A) are all the same size and cross section.
14 Rotor Carrier
RR Retaining Ring
CT Centering Tab
K Centering Tab Cap Screw
SL Sleeve Assembly
10A Drive Ring
M Outboard Vibration Dampener
M1 Inboard Vibration Dampener
9 Sleeve Collar
13 Cup Point Set Screw
13A Quarter Dog Set Screw
11 Sleeve O-ring
11A Rotor Carrier O-ring
9
2
© Copyright 2000 Flowserve Corporation
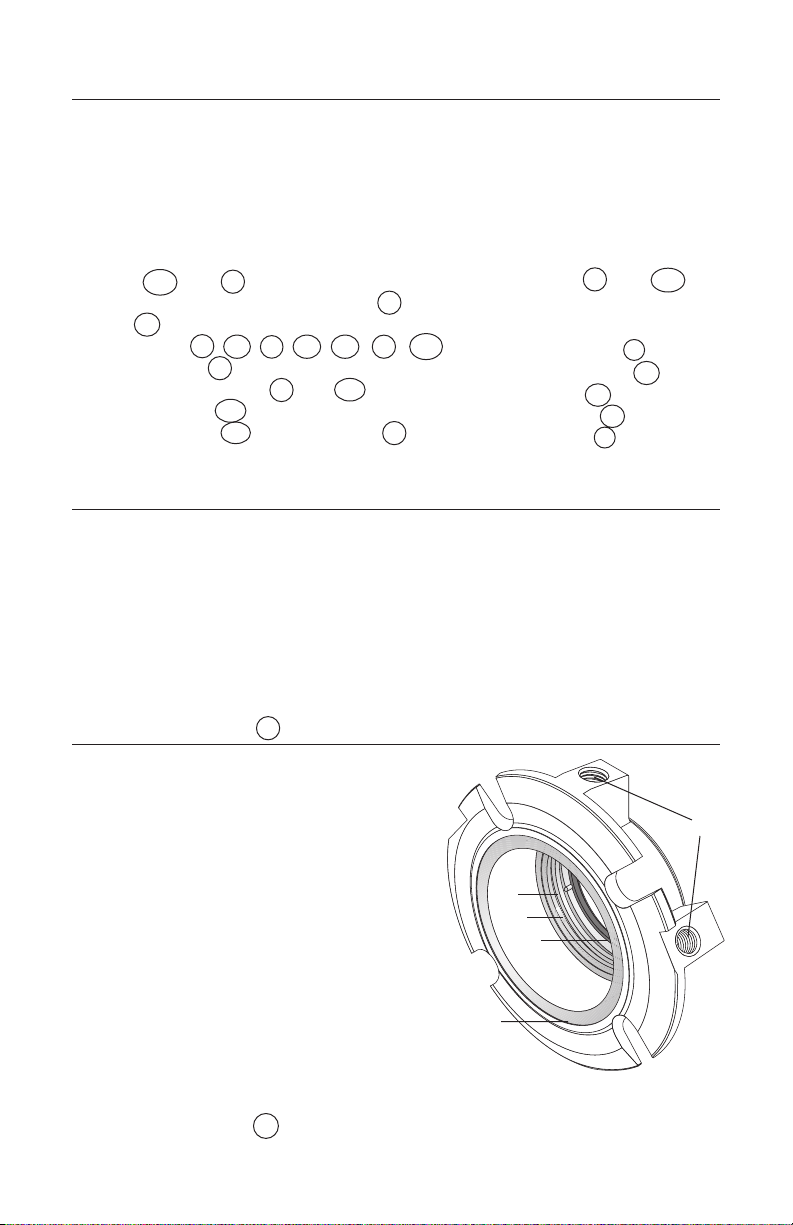
2 Disassembly
When disassembling seal, inspect for conditions which may have caused the
need for the seal to be removed from service. If seal was removed due to
premature failure, determine what conditions caused that failure and correct any
problems prior to returning the repaired seal to service. For assistance with seal
failure analysis, please contact your Flowserve representative.
Seal Parts that are always replaced
• Inboard and outboard bellows assemblies 34A and 34
• Inboard and outboard mating rings 3B
and 3C
• All O-rings P , P1 , 6 , 6A , G1 , 11 , 11A
• Gland gasket G
• Vibration dampeners M and M1
• Retaining ring RR
• Centering tabs CT and cap screws K
• Cup point and quarter dog
set screws 13 and 13A
Reconditionable Seal Parts
• Gland assembly 1
• Sleeve assembly SL
• Inner gland 1B
• Rotor carrier 14
• Sleeve collar 9
3 Inspection and Reconditioning
3.1 There are certain critical areas of each part where special attention should be
paid to the condition. If any of the areas listed in 3.2, 3.3 or 3.4 show signs of
wear, corrosion, or other defects that cannot be removed without affecting
the dimensional size of the surfaces by more than 0.001 to 0.002", then the
respective part should be replaced. If grit blasting is performed, it may be
necessary to polish the O-ring surfaces to achieve the required surface finish
(see 3.2A and 3.3A for the required surface finish). If any parts require
machining to correct damage, please contact your Flowserve representative
for dimensional requirements, or for any other questions regarding repair.
3.2 Gland Assembly 1 (Figure 2)
A Mating ring O-ring surface - Inspect for wear,
fretting, nicks, scratches, or corrosion.
Required surface finish
B Gasket surface - Remove the old gasket
and clean the gasket surface. Inspect for
nicks, scratches, or corrosion.
C Pipe taps and other threaded holes -
Inspect for damaged threads or corrosion.
Taps must be clean and free of debris and
corrosion. Re-tap as necessary.
D Bushing - Inspect for wear, breakage, or
loosened bond with gland. Replace using
Loctite®1 7471 Primer T and Loctite RCTM/640
or equivalent to adhere the bushing if any of
these conditions exist. A ten minute cure at 400°F
(204°C) is required to achieve full bond strength.
If worn or corroded, contact your Flowserve representative.
E Gland drive ring 1B - Inspect for wear or corrosion.
If worn or corroded, contact your Flowserve representative.
1 Registered Trademark of Loctite Corporation
: 63 RMS
A
E
B
D
Figure 2
C
3
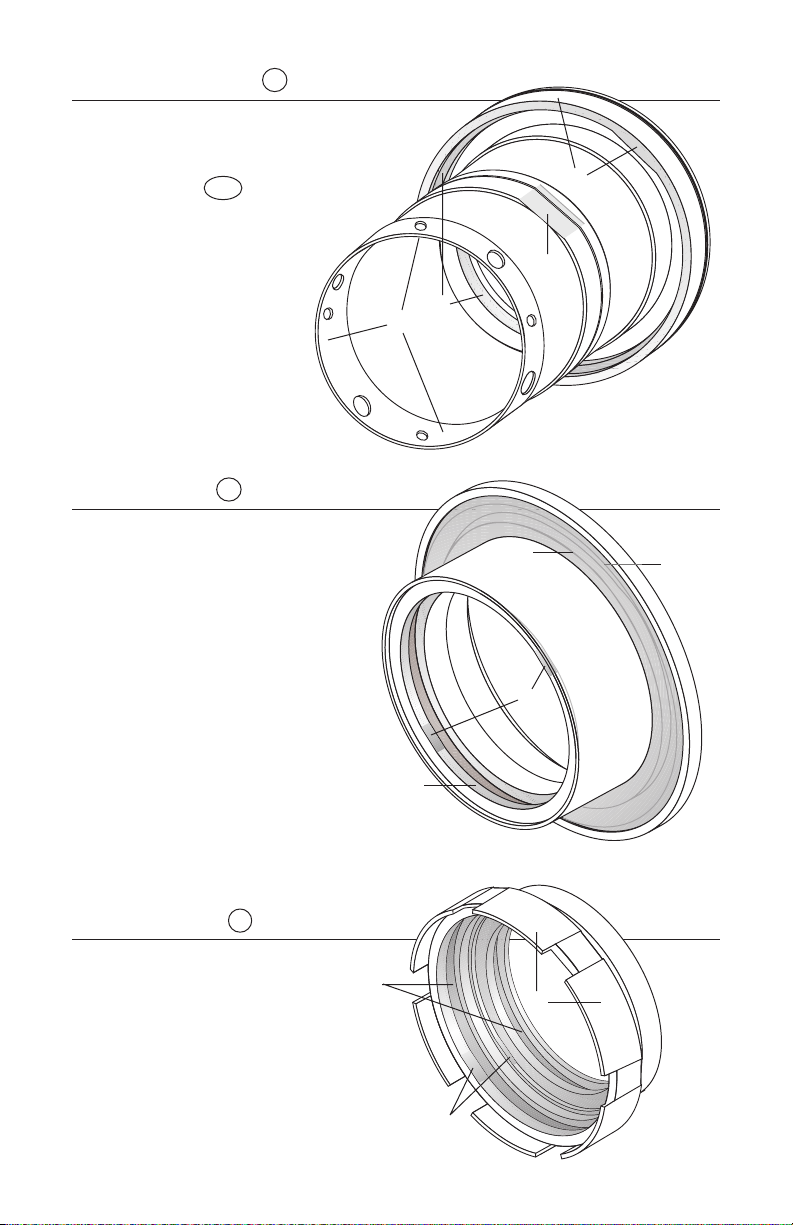
3.3 Sleeve Assembly SL (Figure 3)
A O-ring surfaces - Inspect for wear,
nicks, scratches, or corrosion.
Required surface finish
B Drive Ring 10A - Inspect for
wear or corrosion, especially
at drive flat surfaces on
ID of drive ring.
C Drive flats for rotor
carrier - Inspect for
wear, rounding of
edges of flats, or
corrosion.
D Drive end roundness
: 63 RMS.
No greater than
0.001" TIR
3.4 Inner Gland 1C (Figure 4)
A Mating ring O-ring surface - Inspect
for wear, fretting, nicks, scratches,
or corrosion.
finish:
B Gland O-ring surface - Inspect
for wear, nicks, scratches,
or corrosion.
finish:
63 RMS.
C Gasket surface - Remove
old gasket and clean surface.
Inspect for nicks, scratches,
or corrosion.
D Drive flats - Inspect for
wear or corrosion. If worn or
corroded, contact your Flowserve
representative.
Required surface
63 RMS
Required surface
Figure 3
B
C
A
D
Figure 4
C
D
A
B
3.5 Rotor Carrier 14 (Figure 5)
A O-ring surfaces - Inspect for
wear, nicks, scratches,
or corrosion.
surface finish
B Pumping vanes - Inspect for
wear, damage, or corrosion.
C Drive flats - Inspect for wear
or corrosion.
4
Required
: 63 RMS.
Figure 5
A
B
C