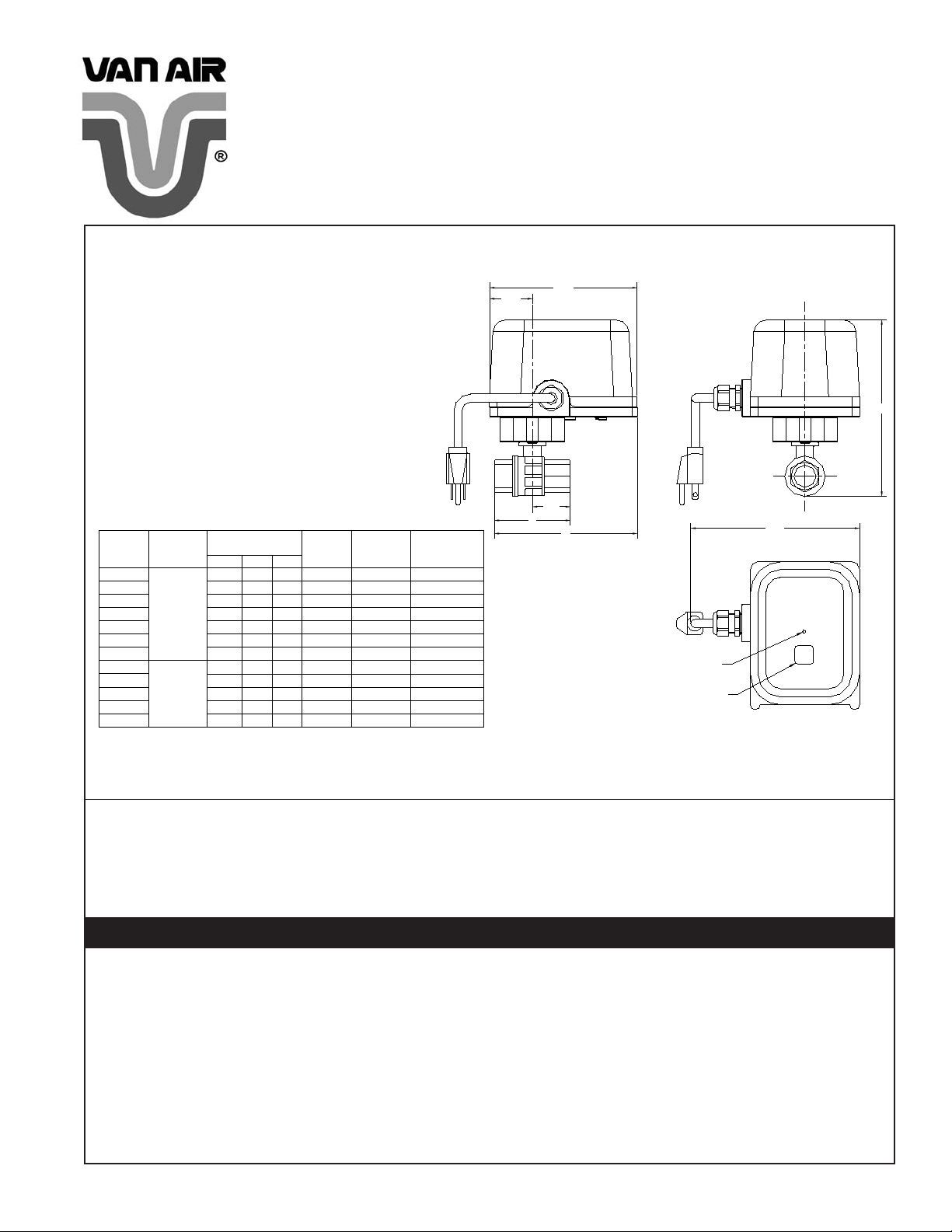
FIGURE 1
OCTOBER 2011
P/N 432-10036-D
INSTALLATION, OPERATION & MAINTENANCE INSTRUCTIONS
®
SENTINEL
MOTORIZED BALL VALVE WITH ADJUSTABLE CYCLE TIME
Model MDV400I
NOTES:
1. RATED PRESSURE: BRASS 600 PSIG COLD WOG.
2. VALVES ARE FULL PORT 2 PIECE BALL VALVES
3. AVAILABLE ELECTRICAL: -115VAC-1PH-50/60HZ, MAX CURRENT: 1.7 AMPS
(DC VOLTAGE UNITS ARE SUPPLIED WITH POWER CORD BUT WITHOUT PLUG)
4. ENCLOSURE RATING: NEMA 4
5. AMBIENT TEMPER A TURE OPERATING RANGE: 0 TO 120°F
6. VALVE INTERNAL MATERIALS:
BRASS VALVES; BALL-CHROME PLATED BRASS
316 SS VALVES; BALL-316SS
VALVE
SIZE
(NPT)
1/2"
3/4"
1"
1 1/2"
2"
2-1/2"
3"
1/2"
3/4"
1"
1 1/2"
2"
SS 900 PSIG COLD WOG
-230VAC-1PH-50/60HZ, MAX CURRENT: 0.9 AMPS
-12VDC, MAX CURRENT: 1.7 AMPS
-24VDC, MAX CURRENT: 0.9 AMPS
STEM-BRASS, NICKEL PLATED
SEAT-RTFE
STEM-316SS
SEATS-PTFE/TFM
VALVE
MATERIAL
BRASS
STAINLESS
STEEL
(316 SS)
* ACTUATOR TORQUE FOR THESE UNITS WITH DC VOLTAGE IS 300 IN/LBS.
DIMENSIONS
A
B
2.60
5.58
2.93
5.75
6.06
4.60
6.58
5.31
6.94
6.10
7.33
6.89
7.73
2.80
5.68
3.00
5.78
3.43
6.00
4.46
6.51
5.40
6.98
C
7.02
7.51
7.83
9.13
9.72
10.86
11.65
7.78
7.93
8.43
9.48
10.23
ACTUATOR
WEIGHT
10.65
12.96
11.65 150*
14.88
(LBS)
8.16
8.39
8.833.56
16.14
21.16
8.18
8.67
9.66
TORQUE
(IN/LBS)
150*
150*
150*
150*
300
600
600
150*
150*
150*
300
FLOW
COEFFICIENT
CV
19
34
52
143
205
475
780
38
71
110
350
600
1.72
6.00
C
B/2
B
A
POWER ON
LIGHT
PUSH-TO-TEST
BUTTON
6.81
POWER
PUSH
TEST
ON
TO
For optimum performance and safety, please read and understand all instructions before installation.
Personnel must use safe working practices and observe all applicable local and international regulations, safety, health and legal requirements when
installing and operating this product. Improper operation or maintenance of this product could be potentially dangerous resulting in an accident
causing injury or death. Van Air Systems cannot anticipate every possible circumstance which represents a potential hazard. The Warnings in this
manual cover the most common potential hazards and are therefore not all-inclusive. The installation and maintenance of this product must be in
strict accordance with this instruction manual or the warranty will be invalidated.
WARNINGS
DO NOT REMOVE OR REPLACE ANY PART OF THE PRODUCT WHILE IT IS UNDER PRESSURE. SERIOUS PER-
•
SONAL INJURY AND/OR DAMAGE TO THE PRODUCT MAY RESULT.
DO NOT OPERA TE THE PRODUCT IF THERE ARE ANY PRESSURE LEAKS. IF A LEAK IS PRESENT, THE PRODUCT
•
MAY BE UNSAFE TO OPERATE. REMOVE THE PRODUCT FROM SERVICE IMMEDIATELY.
DO NOT OPERATE THIS PRODUCT ABOVE ITS MAXIMUM OPERATING PRESSURE AND/OR TEMPERATURE.
•
WHEN INSTALLING THIS PRODUCT, BE SURE TO COMPLY WITH ALL LOCAL, STATE, INTERNATIONAL, AND/OR
•
GOVERNMENT LAWS, RULES, REGULATIONS AND CODES APPLICABLE TO YOUR INSTALLATION.
DO NOT INSTALL THIS PRODUCT IN A MANNER THAT DISCHARGES TOWARDS PEOPLE OR EQUIPMENT. SERI-
•
OUS INJURY AND/OR DAMAGE MAY RESULT.
PROPER DISPOSAL OF DRAINED LIQUIDS THROUGH THIS PRODUCT ARE THE RESPONSIBILITY OF THE USER.
•
PAGE 1
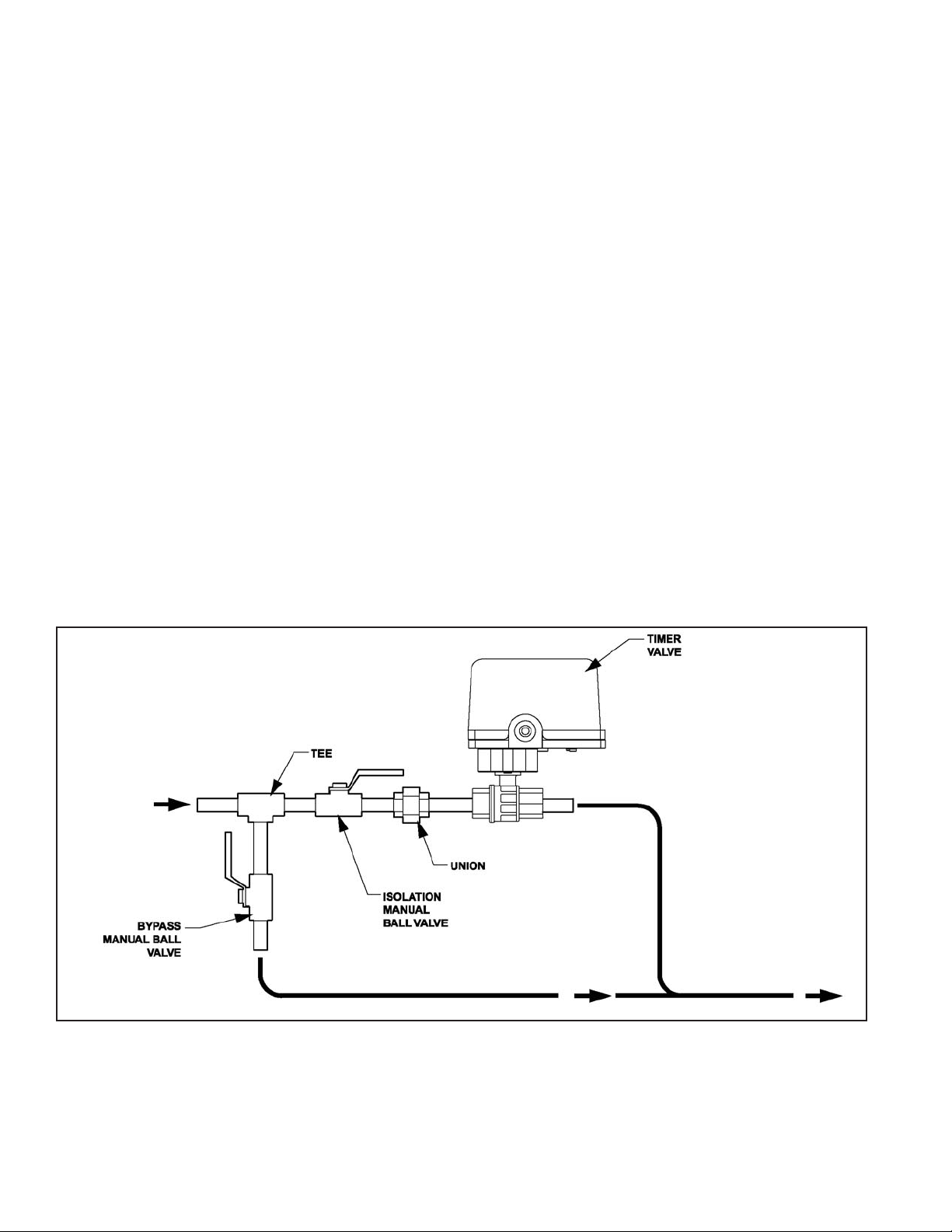
1.0 DESCRIPTION OF NORMAL OPERATION:
1.1 This product consists of a quarter turn ball valve mated to an electric actuator with a fully adjustable timer
controller. The product is designed for mounting in a pipe-line requiring adjustable set closed times and
adjustable set open times. A common application is draining fl uids from compressed air system components
such as separators, fi lters, airlines and receiver tanks. The timer is set at the factory to open the valve for
10 seconds every 2 hrs.
2.0 INSTALLATION INSTRUCTIONS: (Reference Figure 2)
2.1 Carefully unpack the valve from its shipping box or boxes. Check for visible signs of damage immediately fi le a
claim with the carrier if damage is found. Do not install a damaged valve or actuator. Note: 2” valves and larger
will be shipped in two boxes, one containing the valve and one containing the actuator. Smaller valves are
shipped with actuator installed.
2.2 2” valves and larger will require installing the actuator after installing the valve in the line (See Figure 3).
2.3 Make sure that all pressure is removed from the line where the valve is to be installed. Make precautions to
ensure the line remains free of pressure during the installation process.
2.4 Check the line for obstructions and clean as required.
2.5 Make sure all components and parts you are installing meet the temperature and pressure ratings of your
system. (piping, manual valves, fi ttings, or electrical parts are not included)
2.6 Install a tee onto the line with the outlet facing down. Install a nipple and manual ball valve on the tee facing
down. This is for bypassing the timer valve if it is not operational for any reason.
2.7 Install an isolation valve on the remaining opening. Close both manual valves and install a nipple and union on
the isolation valve.
2.8 Install the valve after the union and install all additional piping downstream of the valve and bypass valve per
your local requirements.
2.9 Locate a suitable power source and verify it meets the requirements of your valve (see valve label). Wire the
valve using the cord included or conduit taking all precautions necessary to meet all required electrical codes for
your location. Verify your timer valve is in the closed position and that timing is per your needs.
2.10 Review steps 2.1 through 2.9 to verify no steps were skipped.
2.11 Slowly pressurize the system. Once the system is fully pressurized, slowly open the isolation valve and check
the system for leaks. In the event a leak is discovered, remove pressure from the system and repair before
proceeding.
2.12 Your valve is now installed and ready for operation.
FIGURE 2 RECOMMENDED INSTALLATION
CAUTION: DO NOT INSTALL MORE THAN ONE FLOW SOURCE PER VALVE. MULTIPLE SOURCES WILL HAVE VARIED
PRESSURES RESULTING IN HIGHEST TO LOWEST CONTAMINATION.
PAGE 2