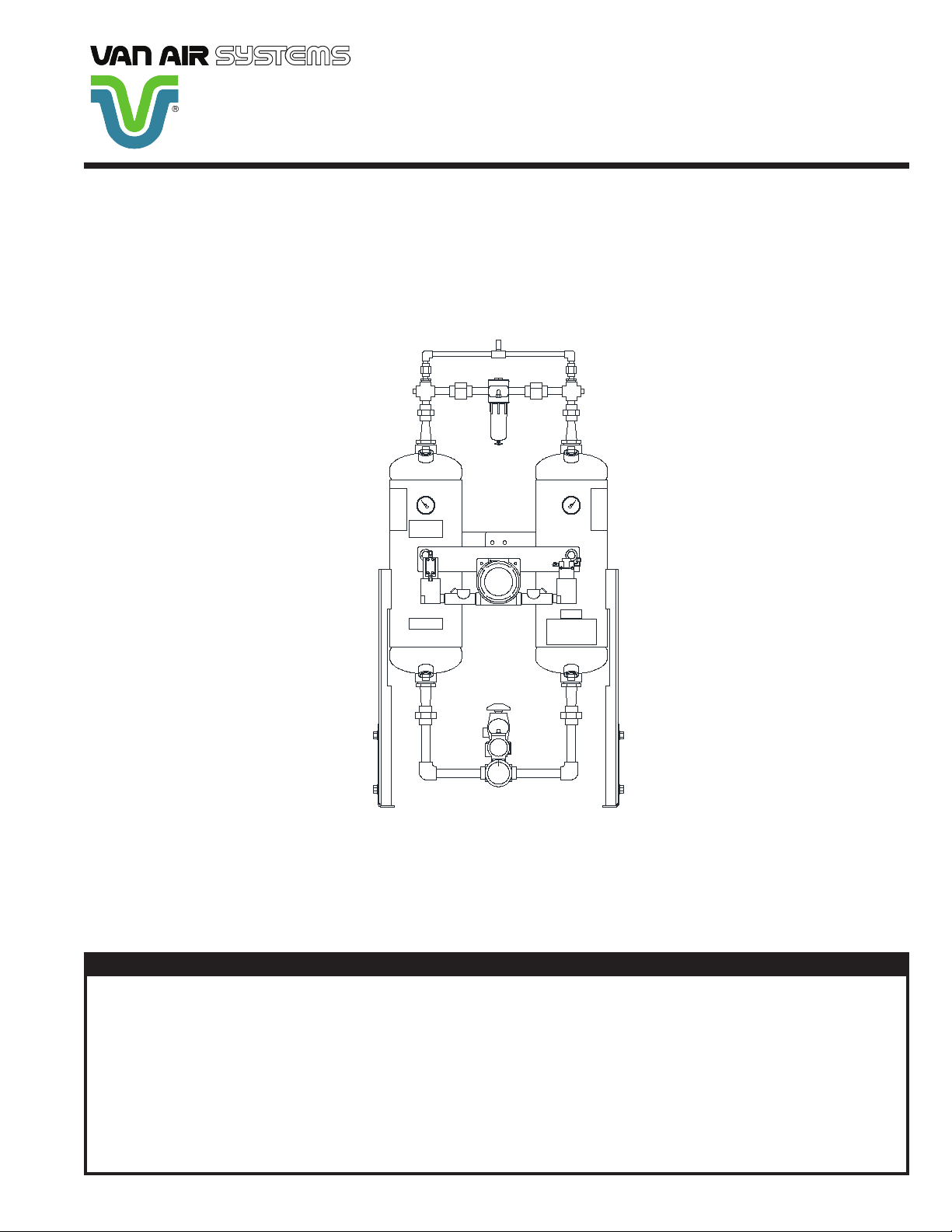
INSTALLATION, OPERATION & MAINTENANCE MANUAL
FOR
HEATLESS REGENERATIVE
COMPRESSED AIR DRYER SYSTEM
April 2014
Revision: A
2950 Mechanic Street
Lake City, PA 16423 USA
P: 800-840-9906
Fax: 814-774-3482
Email: info@vanairsystems.com
www.vanairsystems.com
MODEL: HLSXA55 115V
PART NO: 81-2368
WARNING
READ ALL INFORMATION IN THIS MANUAL BEFORE BEGINNING INSTALLATION OR OPERATION
OF THE DRYER. BEFORE STARTING INSTALLATION AND/OR MAINTENANCE PROCEDURES, TURN
OFF THE MAIN POWER TO THE DRYER AND COMPLETELY DEPRESSURIZE THE UNIT TO PREVENT
PERSONAL INJURY.
DO NOT REMOVE, REPAIR, OR REPLACE ANY ITEM ON THIS DRYER WHILE IT IS PRESSURIZED.
NEVER OPERATE THIS DRYER ABOVE THE RATED OPERATING CONDITIONS. OPERATION ABOVE
SPECIFIED CONDITIONS WILL RESULT IN DECREASED PERFORMANCE, POSSIBLE DAMAGE TO
THE UNIT AND/OR PERSONAL INJURY.
PAGE 1
www.vanairsystems.com
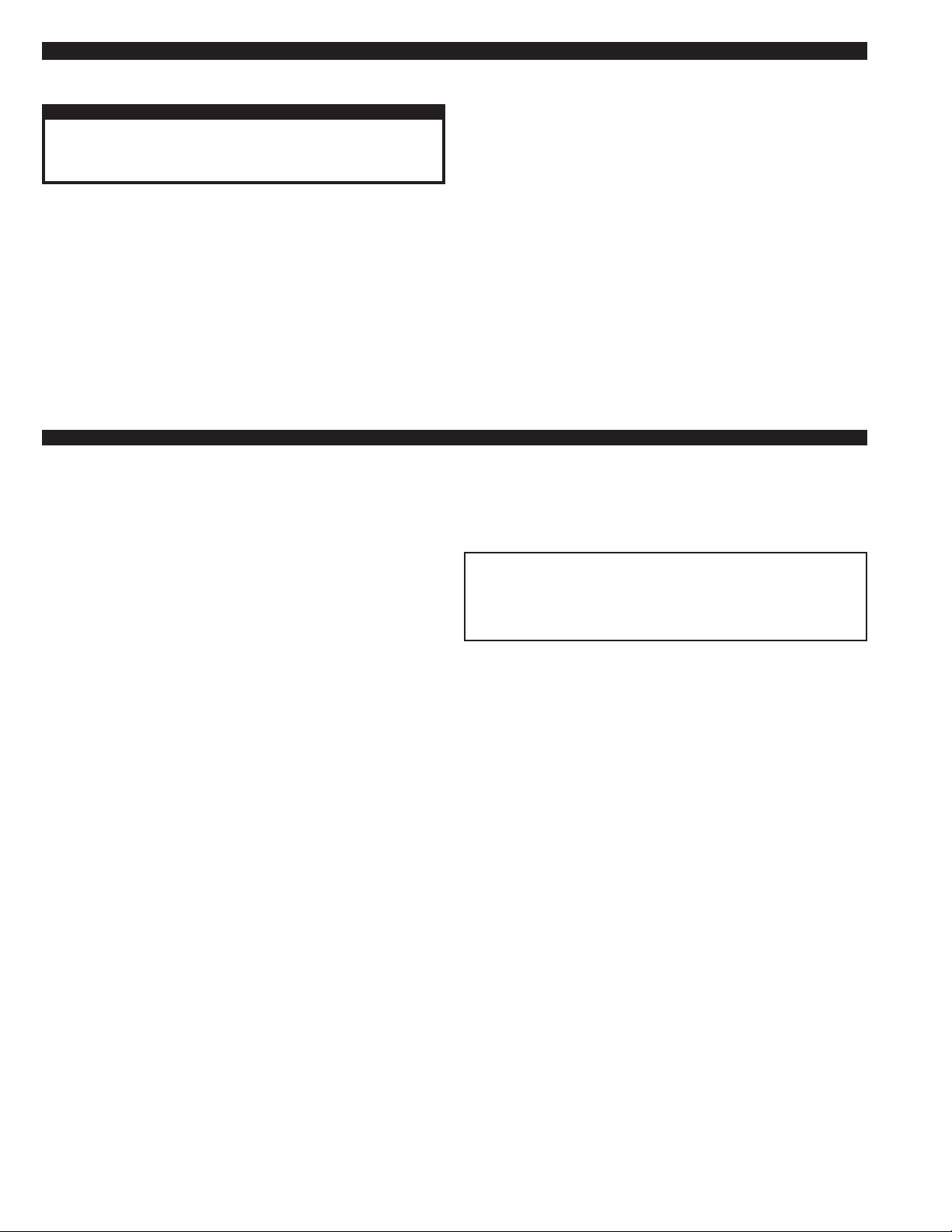
HANDLING SECTION 1
1.1 HANDLING INSTRUCTIONS
WARNING
DO NOT LIFT THE DRYER BY THE INLET PIPING (BELOW
VESSELS). THIS PIPING IS NOT DESIGNED TO SUPPORT THE
WEIGHT OF THE DRYER. PERSONAL INJURY AND/OR EQUIPMENT DAMAGE MAY RESULT.
Lift the dryer by the outlet piping (above vessels).
When lifting the dryer, make sure that the chains or cables are clear of
all tubing and fragile components.
If outside storage is required, the unit MUST BE adequately covered to
prevent rain or snow from accumulating on the dryer. The unit must be
placed on a paved surface to keep it out of standing water and mud.
1.3 EQUIPMENT CHECK
Inspect the dryer for any damage that may have occurred during ship-
ment. Inspect all ttings, piping connections, fasteners, etc. for loose
connections. Also check gauges and lights for cracks or breakage.
IF DRYER HAS BEEN DAMAGED DURING SHIPMENT:
(1) NOTIFY CARRIER IMMEDIATELY AND FILE A CLAIM.
(2) CONSULT FACTORY BEFORE OPERATING THE DRYER.
1.2 STORAGE INSTRUCTIONS
The unit should be stored indoors and covered with a tarpaulin to
keep it clean. The location should be free from corrosive gasses and
extreme humidity, which will cause damage to the unit.
SAFETY SECTION 2
2.1 HANDLING
LIFT THE DRYER BY THE OUTLET PIPING (ABOVE THE VESSELS) AS THE OTHER COMPONENTS ARE NOT DESIGNED
TO SUPPORT THE WEIGHT OF THE DRYER.
LIFTING BY OTHER COMPONENTS MAY CAUSE PERSONAL
INJURY AND/OR EQUIPMENT DAMAGE.
2.2 INSTALLATION
BEFORE STARTING INSTALLATION PROCEDURES, TURN
OFF POWER TO THE AREA WHERE THE DRYER WILL BE INSTALLED. SERIOUS PERSONAL INJURY MAY RESULT IF THIS
SAFETY RULE IS NOT FOLLOWED.
DO NOT REMOVE, REPAIR, OR REPLACE ANY ITEM ON
DRYER WHILE IT IS PRESSURIZED.
THESE ASME CODE VESSELS MUST BE PROTECTED BY
PRESSURE RELIEF VALVES. Refer to OSHA 1910.169 Par.
b, Sub. Par (3) and ASME Boiler and Pressure Vessel Code,
Section VIII, Division 1, UG-125 through UG-136. Also comply with all state and local codes.
WHEN INSTALLING AND OPERATING THIS EQUIPMENT, COMPLY WITH THE NATIONAL ELECTRICAL CODE AND ALL APPLICABLE FEDERAL, STATE, AND LOCAL CODES.
2.3 OPERATION
DO NOT OPERATE DRYER IF EITHER OF THE VESSELS IS
LEAKING. IMMEDIATELY TAKE THE DRYER OUT OF SERVICE.
DO NOT OPERATE THIS DRYER ABOVE THE MAXIMUM RATED
WORKING PRESSURE.
NOTE
OPERATING CONDITIONS FOR PROPER PERFORMANCE OF
THIS DRYER ARE DIFFERENT FROM MAXIMUM OPERATING
CONDITIONS FOR THE VESSELS. BE SURE TO CHECK THE
DRYER OPERATING CONDITIONS. SEE SECTION 3.1
USE THIS DRYER FOR COMPRESSED AIR ONLY.
DO NOT OPERATE THIS DRYER IF EITHER VESSEL HAS
BEEN DAMAGED BY FIRE. TAKE OUT OF SERVICE IMMEDIATELY AND NOTIFY YOUR CERTIFYING AUTHORITY.
2.4 MAINTENANCE
DO NOT REMOVE, REPAIR, OR REPLACE ANY ITEM ON
THE DRYER WHILE IT IS PRESSURIZED. TURN OFF MAIN
POWER TO THE DRYER AND DEPRESSURIZE THE DRYER
COMPLETELY BEFORE STARTING MAINTENANCE PROCEDURES.
ALWAYS WEAR EYE PROTECTION, GLOVES AND A
RESPIRATORY PROTECTIVE DEVICE WHEN HANDLING THE
DESICCANT. DESICCANT DUST MAY CAUSE EYE AND
SKIN IRRITATION. AVOID BREATHING THE DUST AND
PROLONGED CONTACT WITH THE SKIN.
FIRST AID IN CASE OF EYE CONTACT WITH DESICCANT
DUST; IMMEDIATELY FLUSH THE EYES WITH PLENTY
OF WATER FOR AT LEAST 15 MINUTES. CONSULT A
PHYSICIAN.
IT IS CUSTOMER'S RESPONSIBILITY TO FILL ALL CONDUIT SEAL
FITTINGS (INCLUDING THE ONES TO THE SOLENOID VALVES)
WITH CHICO COMPOUND AND CHICO FIBER TO ENSURE THE
INTEGRITY OF THE EXPLOSION PROOF RATING.
PAGE 2
DO NOT WELD OR GRIND THE VESSELS. THEY WILL NOT
BE SAFE TO OPERATE. (Note: Any uncertified alteration to
the vessels VOIDS the ASME Code Certification.)
INSPECT OUTSIDE AND INSIDE OF VESSELS REGULARLY
FOR CORROSION AND DAMAGE (I.E. DENTS, GOUGES OR
BULGES). ANY DAMAGE TO THE VESSELS CAN MAKE
THEM UNSAFE TO USE. IF DAMAGED, TAKE OUT OF SERVICE IMMEDIATELY.
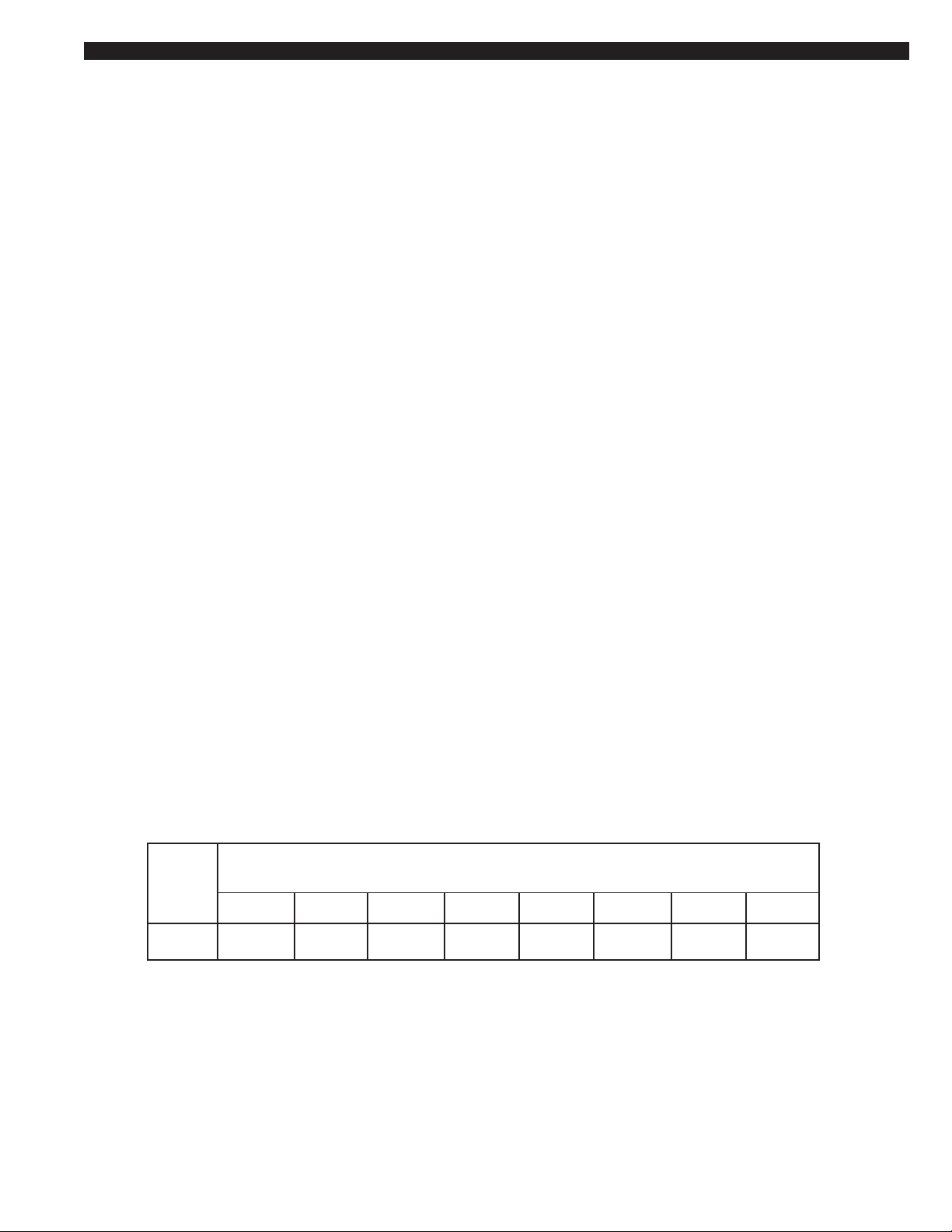
SPECIFICATIONS SECTION 3
3.1 DRYER SPECIFICATIONS
DIMENSIONS ..... ................See SECTION 3.2
VESSELS (desiccant towers)
Construction ................... Manufactured to ASME CODE, Section VIII, Div. 1.
Vessels stamped "UM" designator.
Design Pressure ............. 300 PSIG
Design Temperature ....... -20OF TO 200OF
PIPING
Threaded ttings: ANSI B16.11
Threaded unions: ANSI B16.11
Pipe: Carbon steel, Schedule 40
VALVES
Inlet ............................... 4-Way ball valve w/ actuator (Qty. 1)
Outlet .............................. Check valves (Qty. 2)
Purge .............................. Ball valve w/ actuator N.C. (Qty. 1)
Purge Metering .............. Needle valve (Qty. 1)
CONTROL AIR FILTER
Construction ................... Aluminum housing
ELECTRICAL
Voltage ...........................115V/1PH/60HZ
CONTROL BOX
NEMA 4/7 CD
Explosion Proof (Class 1, Div 1, Groups C & D)
DESICCANT
Material ........................................... Activated Alumina, 1/8" (2-5 MM) Bead type
Quantity Per Tower: ........................ See SECTION 3.2
OPERATING CONDITIONS
Inlet Operating Pressure ................ MIN 80 PSIG ...........MAX 250 PSIG
Inlet Operating Temperature ........... MIN 40OF ................MAX 120OF
Ambient Operating Temperature .... MIN 40OF ................MAX 120OF
PROCESS GAS
Compressed Air
RATED INLET CONDITIONS
Inlet Air Pressure ............................ 100 PSIG
Inlet Air Temperature ...................... 100°F
Relative Humidity (saturation) ........ 100% RH
RATED FLOW CAPACITIES
Flow capacities at various pressures
MODEL
HLSXA55
80 PSIG
45
100 PSIG55125 PSIG
61
150 PSIG66175 PSIG71200 PSIG75225 PSIG
SCFM
80
250 PSIG
84
PAGE 3