
INSTALLATION INSTRUCTIONS
APRIL 2000
P/N: 432-10029
®
EHP SERIES FILTER ELEMENTS
PRODUCT PURPOSE & FUNCTION:
Van Air's EHP series elements provide long service life as well as ease of maintenance. Both particulate and coalescing
elements will operate efficiently for extended periods of time until a pressure drop of 10 PSID has occurred. The activated carbon
element (RD grade) must be changed to suit specific applications, or at least every 6 months.
STAINLESS
STEEL
ENDCAP S
THREADED
TOP
ENDCAP
INLET OUTLET
EHP-6, EHP-15/20
& EHP-50
FLOW DIRECTION THROUGH ELEMENT
(COALESCING)
IN/OUT
INLET
(PARTICULATE)
OUT/IN
OUTLET
EHP-35, EHP-70/75,
EHP-100/110 &
EHP-175/195
CHEMICAL
RESISTANT
POLYESTER
OUTER SOCK
STAINLESS
STEEL
ENDCAPS
EHP-275 & EHP-550
STAINLESS
STEEL OUTER
CORE (VISIBLE
ONLY ON RD
GRADE
ELEMENTS)
APPLICATION
Oil Removal (Liquids) AA Extra Coarse
Solid Particulate
Removal
Oil Vapor Removal RD Vapor Adsorbing 0.01µ 80 OUT/IN
ELEMENT
GRADE PURPOSE
FILTRATION GRADES
NOMINAL
PARTICULATE
REMOVAL
Coalescing
ACoarse
Coalescing
B General Purpos e
Coalescing
C High Efficiency
Coalescing
RAA Extra Coarse
Particulat e
RA Coarse Particula t e 5.00µ 225 OUT/IN
RB General Purpose
Particulat e
RC High Efficien cy
Particulat e
25.00µ 225 IN/OUT
5.00µ 225 IN/OUT
1.00µ 175 IN/OUT
0.01µ 125 IN/OUT
25.00µ 225 OUT/IN
1.00µ 225 OUT/IN
0.01µ 225 OUT/IN
MAXIMUM
INLET
TEMP. (°F)
WARNINGS
DO NOT REPLACE ANY ITEM ON VESSEL WHILE IT IS UNDER PRESSURE.
•
DO NOT OPERATE LEAKING FILTER TAKE THEM OUT OF SERVICE IMMEDIATELY.
•
DO NOT OPERATE FILTER ABOVE MAXIMUM WORKING PRESSURE AND/OR MAXIMUM OPERATING TEMP.
•
USE THE PROPER SAFETY PRECAUTIONS FOR THE GAS BEING PROCESSED.
•
ELEMENT
FLOW
DIRECTION
PRINTED IN THE USA ©2000 VAN AIR SYSTEMS INC. 2950 MECHANIC STREET, LAKE CITY, PA 16423 PAGE 1
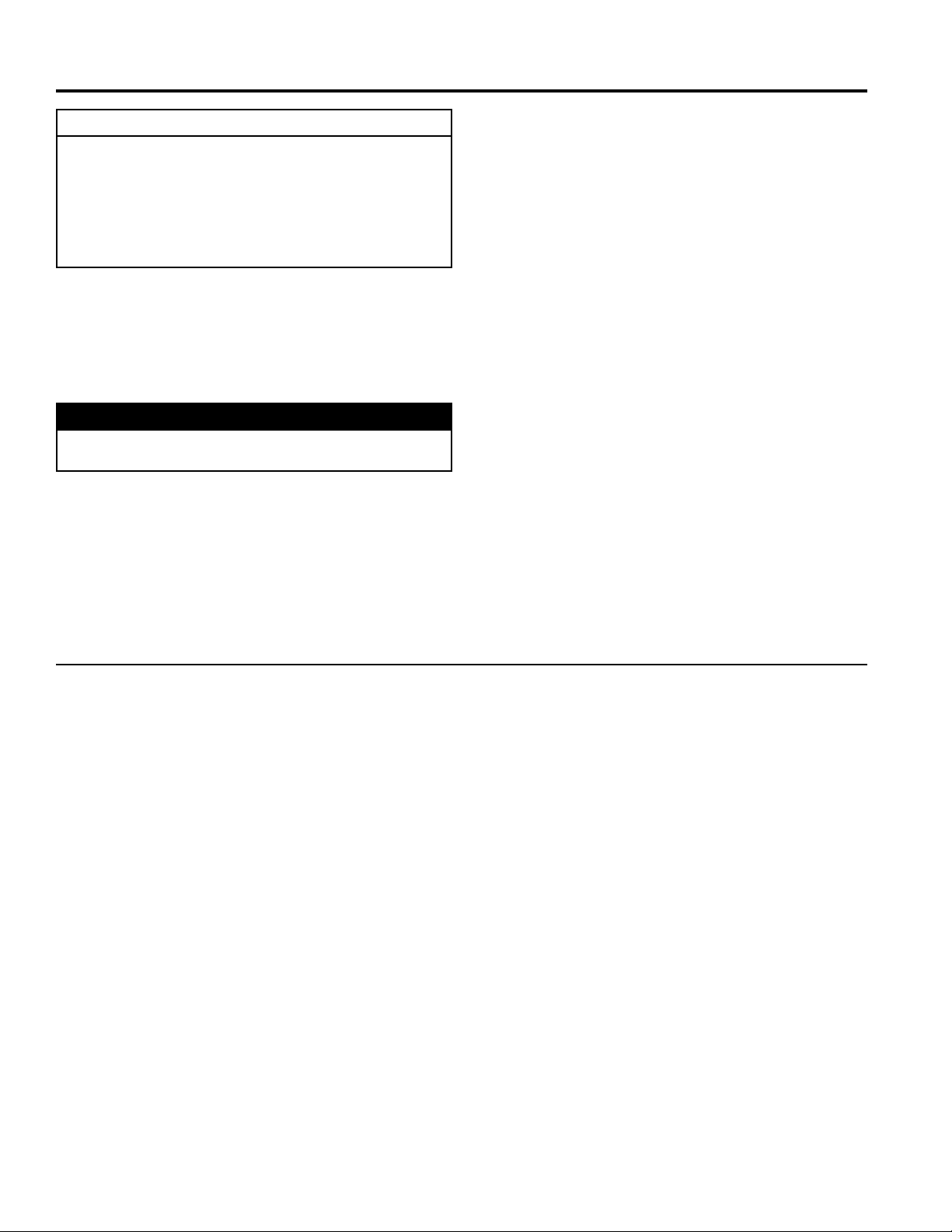
ELEMENT REPLACEMENT
NING
TO REDUCE ENERGY CONSUMPTION FROM EXCESSIVE
PRESSURE DROP AND MINIMIZE CHANCE OF CONTAMINANT CARRYOVER, INSTALL NEW ELEMENT WHEN
PRESSURE DROP REACHES 10 PSID (EXCEPT GRADE
RD). INSTALL NEW RD ELEMENTS WHEN HYDROCARBON VAPORS ARE FIRST DETECTED DOWNSTREAM OR
AT LEAST EVERY 6 MONTHS.
Close inlet and outlet shutoff valves (and open bypass valve
1.
if provided), or lock out all compressed air supply to filter
housing.
Depressurize filter by loosening the drain plug, but do not
2.
remove the drain plug. Leave drain cracked open until all
pressure is out of filter housing and bowl is removed.
IMPORTANT
WARNING
DO NOT UNSCREW FILTER BOWL FROM HEAD UNTIL
VESSEL IS COMPLETELY DEPRESSURIZED.
Follow the filter instruction manual included with filter housing
3.
to disassemble the filter.
Remove used element and discard.
4.
Remove new element from packaging. Check to make sure
5.
that o-ring is properly positioned in endcap and has been
lightly greased.
Grasp clean element by bottom endcap and install it in the filter
6.
head.
Check o-ring in filter head. Replace if worn or damaged.
7.
Clean and lubricate threads on bowl with light grease. This will
8.
facilitate removal of bowl at next servicing.
Follow filter instruction manual to reassemble the filter.
9.
Tighten the drain plug then slowly open inlet and outlet shutoff
10.
valves. Close bypass valve (if provided). Filter is now in
service.
Monitor differential pressure regularly and replace element as
11.
indicated.
Drain coalescing filters every shift.
•
Check differential pressures weekly on coalescing and
•
particulate filters (AA, A, B, C, RA, RB, RC, and HT grades).
When differential pressure reaches 10 psid, install clean
elements. On adsorbing filters (grade RD), install clean
elements when hydrocarbon vapors are first detected
downstream or every six months, whichever comes first.
MAINTENANCE
For correct replacement element model numbers see: label
•
on filter housing, bottom element endcap and/or page 3.
When changing out element, inspect housing o-ring for
•
nicks and/or cracks. If any nicks and/or cracks are present,
replace o-ring.
PAGE 2 ©2000 VAN AIR SYSTEMS INC. 2950 MECHANIC STREET, LAKE CITY, PA 16423 PRINTED IN THE USA