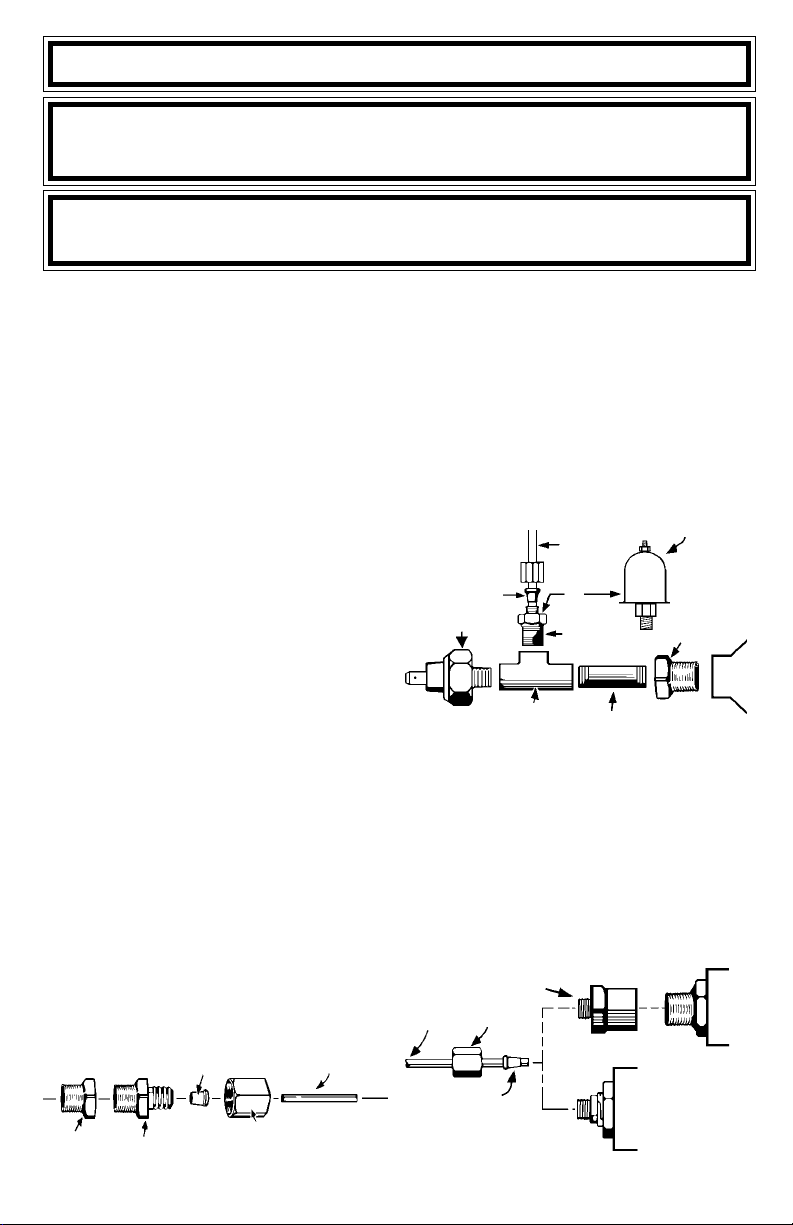
OIL PRESSURE GAUGE - INSTRUCTIONS
INDICADORES DE PRESION DE ACEITE/AIRE -
INSTRUCCIONES TENSIÓN 12 V
MANOMÈTRE DE PRESSION D'HUILE-
INSTRUCTIONS
WARNING: If your car is microprocessor (computer) controlled or has an electric cooling fan refer to
the section on the front cover titled MICROPROCESSOR CONTROLLED ENGINES.
Pressure gauges can measure the pressure
present in a system utilizing air or liquids. An electrical pressure gauge is simpler and more versatile for installation than a mechanical gauge but
is not quite as fast to respond to pressure
changes. The factory warning light sender can be
retained to operate the warning light with the use
of a T-Fitting which is commonly available at auto
parts stores and is manufactured by we.
PRECAUTIONS
1. Check the owners or service manual, or your
local dealer, to be sure that the normal pressure during cold-start and fully-warmed operation for your engine or air system are within
the gauge range.
2. Be sure the tubing kit for the mechanical
gauge is long enough for your application.
3. Follow the instructions carefully. A leak that
goes unnoticed may lead to serious engine
damage.
4. Do not use sealing tapes or compounds on
electrical senders. This will disturb their
grounding connection to the engine/system,
resulting in false low readings.
5. Be careful not to crimp the tubing while unrolling it. Do not use any section of tubing with
a crimp or kink in it. If the nylon tubing is a
little awkward to use because of being rolled,
heat it in boiling water and let the tubing cool
while it is unrolled.
INSTALLATION
Note: If you are planning to install an oil temperature gauge as well as an oil pressure gauge, read
the Note under INSTALLATION in TEMPERATURE-WATER/OIL INSTRUCTIONS.
For Mechanical Gauges:
1. If you are monitoring a fluid system, drain the
fluid level to a level below the warning light
sender location.
Diagram 1
ADAPTER
ENGINE FITTING
PARA NOMBRE, DOMICILIO Y TELEFONO DE IMPORTADOR: VER EMPAQUE.
FERRULE
HEX NUT
TUBING
2. Remove the warning light sender from the
engine and install the engine fitting in the same
location. If an adapter is required, first install
the adapter and then install the engine fitting.
3. Uncoil a few feet of tubing and slide the hex
nut and ferrule over the end of the tubbing
as in Diagram 1. Insert the tubbing into the
engine fitting, an then tighten the hex nut into
the engine fitting.
Diagram 2
NIPPLE
ELECTRICAL GAUGE
SENDER
ADAPTER
ENGINE
TO MECHANICAL GAUGE
HOSE
T-FITTING
OR
ENGINE
FITTING
FERRULE
WARNING LIGHT
SENDER
4. Optional T-Fitting (Diagram 2)- Install the nipple
into the T-Fitting and tighten the end of the
other nipple into the warning light sender location. Install an adapter fitting first if needed.
In one of the two remaining openings in the
T-Fitting, insert the engine fitting and then
follow Step 3 to connect the pressure tubing. Insert the warning light sender into the
remaining T-Fitting opening. Install an adapter
fitting first , if needed (we do not produce
metric fittings for the connection from a metric warning light sender to the T-Fitting).
Diagram 3
TUBING
1
HEX NUT ADAPTER
HEX NUT
FERRULE
COMPRESSION
FITTING GAUGE
1/8 NPT
GAUGE
BLOCK
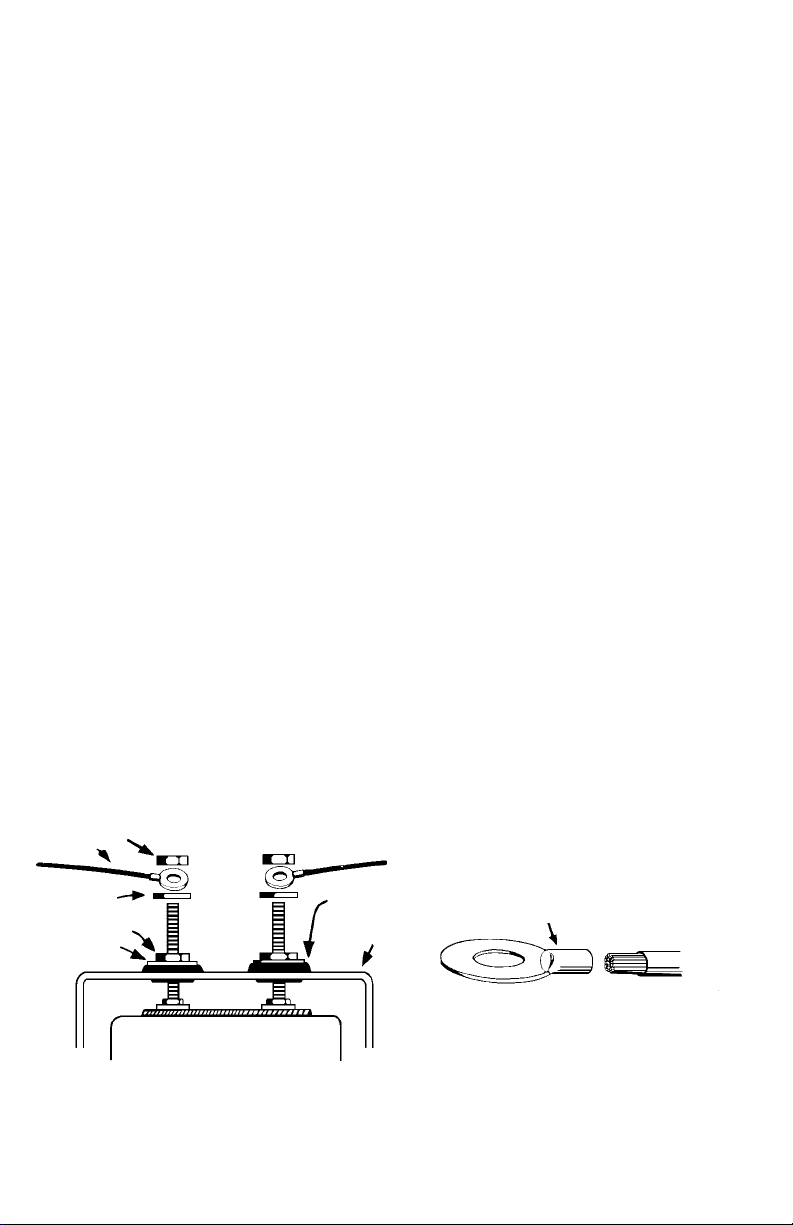
5. On some models, the hex nut adapter (Diagram3) is pre-installed on the back of the
gauge. If not, install the hex nut adapter onto
the gauge.
6. Route the remaining tubing through the fire
wall to the gauge mounting location. Leave
at least one 3 or longer loop in the tubing
before it enters the fire wall and protect the
tubing from rough edges of the fire wall hole.
7. Repeat Step 3 to attach the tubing to the
gauge.
8. Complete the mounting of the gauge.
9. Refill the fluid level, if drained, to its normal
level.
10. Start the engine and observe the fitting connections for leaks and the gauge for proper
operation.
For Electrical Gauges:
1. If you are mounting a fluid system, drain the
fluid level to a level below the warning light
sender location.
2. Remove the warning light sender from the engine and insulate the end of the sender wire if
a T-Fitting is not being used. Install the
gauges sender in the same location in the
engine block. If an adapter is required, first
install the adapter and then the gauges
sender.
3. Optional T-Fitting (Diagram 2) - Install the
nipple into the T-Fitting and tighten the other
end of the nipple into the warning light sender
location in the engine block. Install an adapter
fitting first if needed. In one of the two remaining openings in the T-Fitting, insert the gauge
sender. Insert the warning light into the remaining T-Fitting opening. Install the adapter
fitting first, if needed. (we do not produce
metric fittings for the connection from a metric warning light sender to the T-Fitting).
4. Run a length of 18-gauge insulated copper
wire from the gauges sender to the gauges
mounting location.
5. Connect the wire to the connection on top of
the gauge sender.
6. Facing the back of the gauge, the connection
post on the right is for +12 volts power, the
center post is for the ground connection and
left post is for the sender connection. After
you have mounted the gauge, connect the
sender wire to the left connection post as
shown in Diagram4. Do not over tighten.
7. Connect one end of another length of 18gauge insulated copper wire to the center connection post, as shown in Diagram 4, and the
other end of the wire to a good ground source.
8. Connect a third length of 18-gauge insulated
copper wire to the right connection post as
shown in Diagram 4, and the other end of the
wire should be connected to the fuse box
where the wire will receive +12 volts of power
whenever the ignition key is in the START,
ON or ACCESSORY position.
9. Refill the fluid level, if drained, to its normal
level.
10. Start the engine and observe the fitting connections for leaks and the gauge for proper
operation.
TROUBLESHOOTING
If your electrical gauge reads lower than you would
expect, check all electrical connections, particularly grounding connections. Any poor connection will increase resistance resulting in a false
low reading.
Diagram 4
NUT
WIRE
FLAT WASHER
NUT
WASHER
GAUGE
DO NOT LEAVE ANY HARDWARE
OUT OF THESE CONNECTIONS
GROMMET
CLOSED-EYE CONNECTOR
U-BRACKET
MAKE SURE CRIMP IS GOOD
2