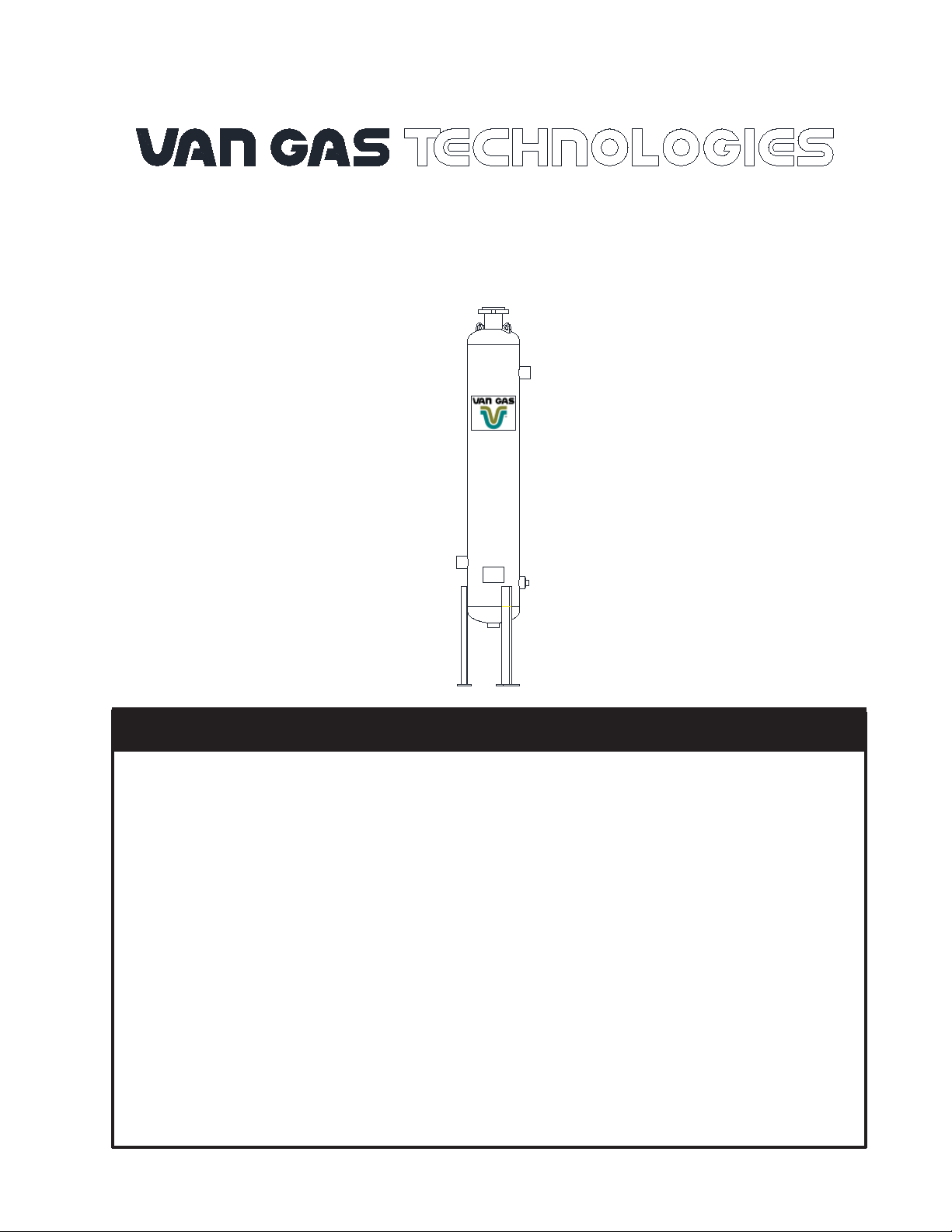
PN 32-0276
JANUARY 2011
INSTALLATION, OPERATION AND MAINTENANCE INSTRUCTIONS
FOR
PIPE LINE DEHYDRATOR FOR NATURAL GAS
PLD 8-7.2 thru PLD 36-7.2
REV B
WARNING
DO NOT REMOVE, REP AIR OR REPLACE ANY ITEM ON THIS VESSEL WHILE IT IS UNDER PRESSURE.
DO NOT OPERA TE IF THERE IS A LEAK IN VESSEL. IMMEDIA TELY T AKE VESSEL OUT OF SER VICE
AND CALL YOUR CERTIFYING AUTHORITY. IF THERE IS A LEAK, DEPRESSURIZE VESSEL, INSPECT ,
REPAIR AND OR REPLACE AS NECESSARY.
DO NOT OPERATE ABOVE MAXIMUM WORKING PRESSURE (MWP) AND OR ABOVE MAXIMUM
OPERATING TEMPERATURE (DEGREES OF).
DO NOT WELD OR GRIND VESSEL. IT WILL NOT BE SAFE TO OPERATE.
DO NOT OPERATE IF THE VESSEL HAS BEEN DAMAGED BY FIRE. TAKE OUT OF SERVICE
IMMEDIATELY AND NOTIFY YOUR CERTIFYING AUTHORITY.
ANY DAMAGE TO VESSEL CAN MAKE IT UNSAFE. INSPECT OUTSIDE AND INSIDE OF VESSEL
REGULARLY FOR CORROSION OR ANY DAMAGE (I.E., DENTS, GOUGES OR BULGES). IF
DAMAGED, TAKE OUT OF SERVICE IMMEDIATELY. CALL YOUR CERTIFYING AUTHORITY.
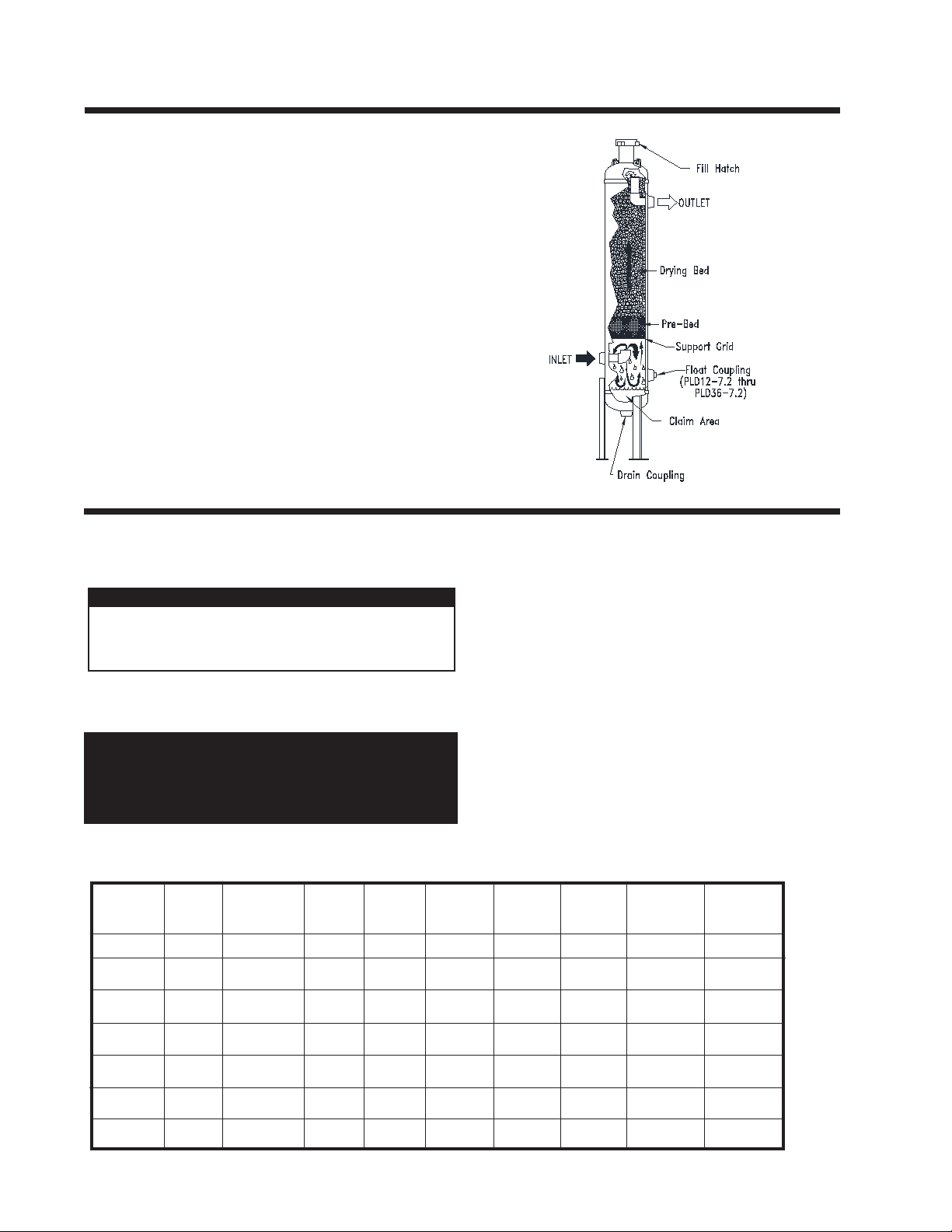
1.0 PURPOSE
A Pipeline Dehydrator removes the water vapor (humidity) present in the gas stream. The process cleans and dries the gas as it
fl ows through a vessel which is fi lled with a special drying agent
(desiccant). The dehydrator operates automatically. There are no
moving parts and no external source of power is required.
"Wet" natural gas enters the lower portion of the dryer where liquid
water and solid particles are separated by gravity and fall to the
bottom of the vessel. The gas moves upward through the prebed
and drying bed of Van Gas desiccant tablets. The tablets attract
and absorb moisture from the gas as it fl ows through the desiccant
bed. The tablets dissolve gradually as they absorb the moisture
and the liquid falls to the bottom of the vessel. The liquid run off in
the prebed creates an extended surface area capable of removing
additional moisture from the gas. This conserves the absorbent
desiccant tablets. The "dry" natural gas fl ows through the dryer
outlet.
The solution of dissolved desiccant and water that falls into the
claim area at the bottom of the vessel must be drained regularly to
prevent the vessel from fl ooding. An automatic drain valve can be
installed to prevent the vessel from fl ooding.
2.0 INSTALLATION
2.1 LOCATION
The ability of a dehydrator to dry natural gas is dependent on
the correct location of the unit. Temperature and pressure are
the keys to selecting the proper location.
IMPORTANT
ALWAYS PROCESS THE GAS THROUGH THE
DEHYDRA TOR A T THE LOWEST TEMPERA TURE
AND THE HIGHEST PRESSURE.
INLET GAS TEMPERATURE: Lower inlet gas temperatures will
result in a lower moisture content at the outlet of the dehydrator.
Locate the dehydrator at the point where temperature is the lowest.
CAUTION
The gas temperature should not exceed:
100°F for GASDRY PRIME
80°F for GASDRY PEAK
100°F for GASDRY MAX
MAXIMUM CAPACITIES - MSCFD
1,000 STANDARD CUBIC FEET PER DAY
MODEL
NO.
PLD 8-7.2
PART
NO.
80-1326
MAXIMUM
WORKING
PRESSURE
720 PSIG
100 PSIG
70
200 PSIG
132
300 PSIG
AFTERCOOLING: If the gas being processed has been compressed
mechanically, an aftercooler, fi nned tubing or extended run of piping
will usually be necessary to reduce the inlet gas temperature to the
dehydrator.
OPERATING PRESSURE: More gas can be processed through the
dehydrator at higher pressures. Locate the dehydrator at the highest
practical pressure, but do not exceed the maximum rated working
pressure of the dehydrator. Refer to the capacity chart located below .
CAPACITY: The chart below indicates the maximum fl ow rate
through the dehydrator for a 24 HOUR period. To calculate the
capacity for a rate per minute just multiply the MSCFD RATE (from
chart ) by 0.6944 example:
A PLD 12-7.2 operating at 100 PSIG has a maximum MSCFD rate
of 132. To fi gure the SCFM multiply 132 MSCFD x 0.6944 which
equals 92 SCFM
NOTE: This is the MAX instantanious fl ow that
can be processed through the dehydrator without
deterioration of the drying performance.
193
400 PSIG
254
500 PSIG
315
600 PSIG
377
720 PSIG
450
PLD 12-7.2
PLD 16-7.2
PLD 20-7.2
PLD 24-7.2
PLD 30-7.2
PLD 36-7.2
PAGE 2
80-1328
80-1330
80-1332
80-1334
80-1466
80-1308
720 PSIG
720 PSIG
720 PSIG
720 PSIG
720 PSIG
720 PSIG
132
207
332
471
747
1191
248
387
621
881
1398
2230
363
567
910
1291
2049
3269
479
748
1200
1701
2700
4307
594
928
1489
2112
3350
5346
709
1108
1778
2522
4001
6385
848
1325
2126
3014
4783
7631
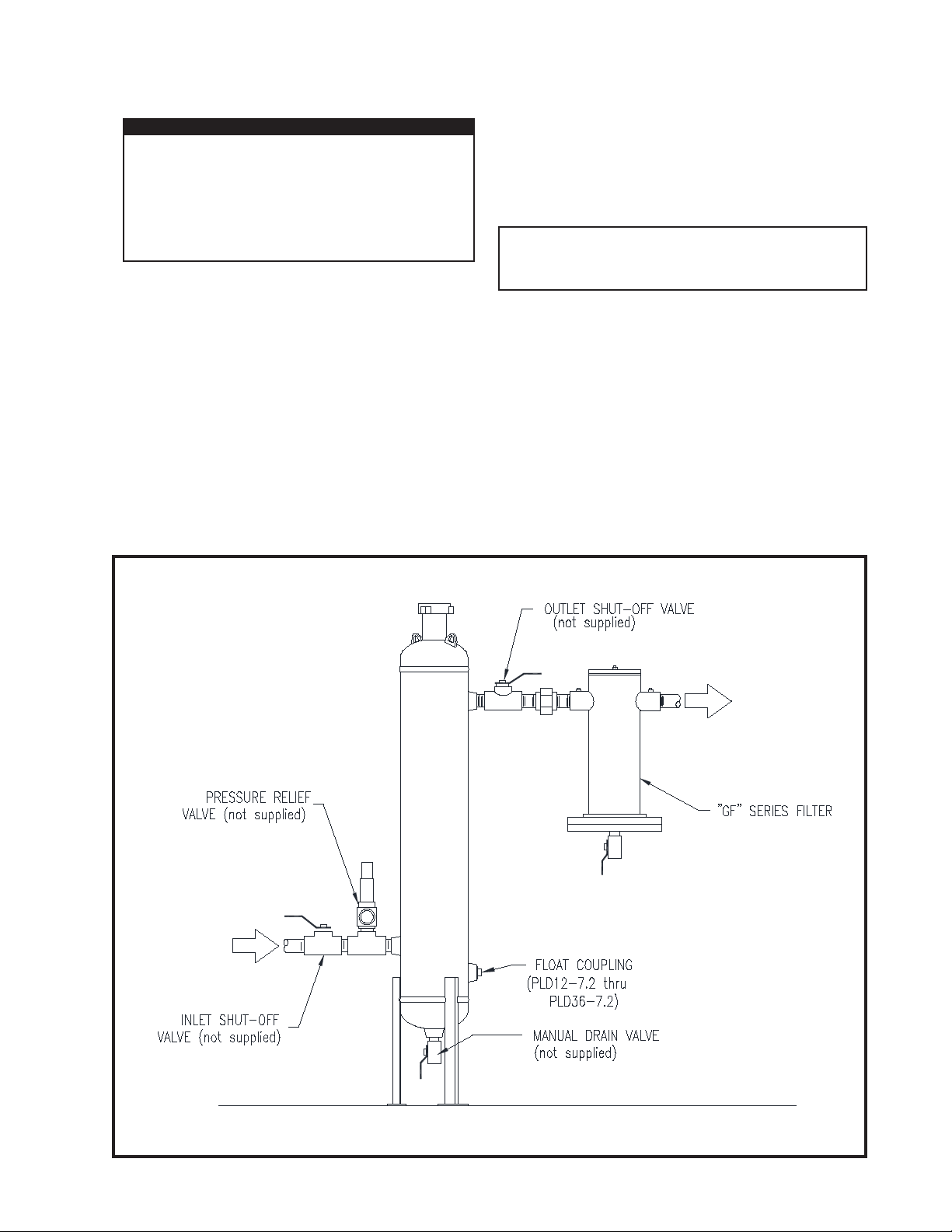
2.2 PIPING AND ANCILLARY EQUIPMENT
2.3 INLET AND OUTLET PIPING
IMPORTANT
COMPLY WITH ALL FEDERAL, STATE, AND
LOCAL REGULATIONS CONCERNING
INSTALLATION OF NATURAL GAS SYSTEMS.
COMPLIANCE TO AND KNOWLEDGE OF ALL
REGULATIONS IS THE RESPONSIBILITY OF
THE INSTALLER.
Make sure that the temperature of gas is not over the maximum
for the desiccant being used. If gas temperature is too high, cool it
prior to the dehydrator.
Mount the dehydrator on a level surface capable of supporting the
weight of the vessel, such as a cement pad or a skid.
Install a pressure relief valve in the up-stream piping (relief
valve not furnished). A relief valve must be installed to
conform with the ASME Boiler and Presssure Vessel Codes,
Section VIII, Division 1 UG-125, Paragraph (1) and OSHA
standards. Also comply with all applicable Federal, State,
and Local codes.
FIGURE 2-A RECOMMENDED INSTALLATION
Two shut-off valves should be installed (not furnished with
dehydrator)-one at dryer inlet and another at dryer outlet. See
Figure 2-A Recommended Installation.
Connect the inlet and outlet piping as shown in Figure 2-A.
NOTE
Inlet and outlet shut-off valves will make start-up
and addition of desiccant easier.
2.4 AFTERFILTER
Van Gas "GF" Series Filters can be installed downstream of the
dehydrator to remove particulate contamination from the natural
gas. Contact Van Gas for details.
2.5 DRAIN VALVE
Install a drain valve (not furnished with dehydrator) in the drain
coupling at the bottom of the tower (except on PLD8-7.2). A fl oat/
auto drain valve system is available. Contact Van Gas for details.
PAGE 3