
Application
The AV-29x linkages are used to field assemble
Schneider Electric gear train hazardous location
actuators to VB-7xxx series or select VB-9xxx series
valve bodies.
Features
• Die cast aluminum mounting bracket.
• Valve position indication provided as standard.
AV-291, AV-293, AV-295, and
AV-296
Valve Linkage for
Hazardous Location Gear Train Actuators
General Instructions
Applicable Literature
• EN-56-2 Apparatus for Use in Hazardous Locations,
F-
18451
• MAx-305 & MAx-318 Series MAx-405 through
MAx-
419 Series, Two-Position Actuators Genera
Instruc
tions, F-06491
• MC-351, 421, 431, MC-4311 Three-Wire, Two
Position
• MP-3xx and MP-4xx Series Reversible and
Proportional Electric
• Valve Products Catalog, F-27384
• EN-205 Water System Guidelines, F-26080
Actuators General Instructions, F-08366
Actuators, F-15479
l
Printed in U.S.A. 4/10 © Copyright 2010 Schneider Electric All Rights Reserved. F-27441-2
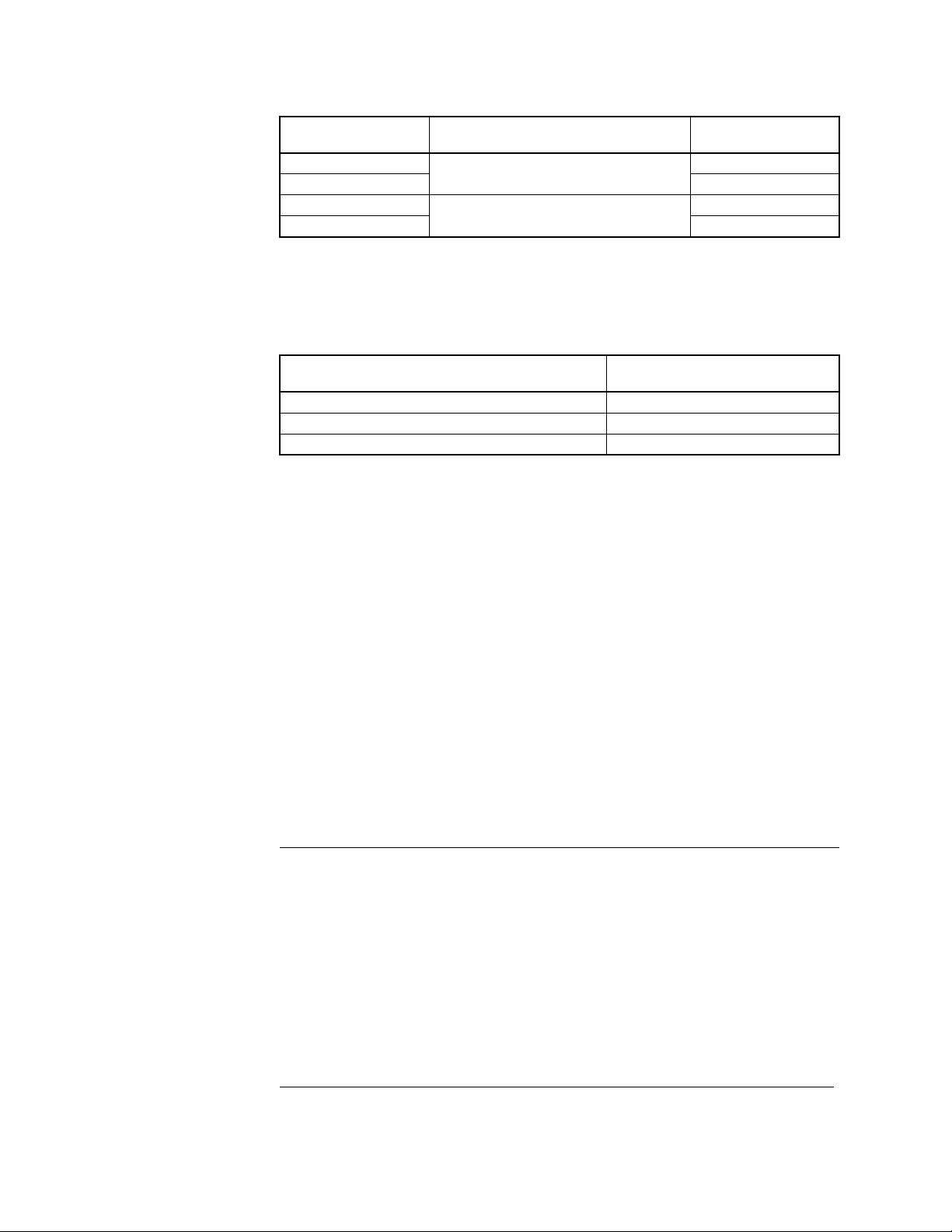
SPECIFICATIONS
Table-1 Model Chart.
Required
Components
Valve Linkage
Model Number
AV-291
AV-293 300
AV-295
AV-296 300
VB-9313 2
Description
Complete Linkages
VB-7xxx 1/2” to 2”
VB-9xxx 2-1/2” to 3” bronze
-1/2” to 4” cast iron flanged
Stem Force
(lb.)
150
150
Temperature Restrictions
Verify that the fluid temperature of the media in the valve versus the ambient temperature at
the actuator does not exceed the ratings shown in Table-2.
Table-2 Restrictions on Maximum Ambient Te m pe r ature for Actuators.
Maximum Temperature of Media in the Valve
(Check Rating of Valve) °F (°C)
260 (126) 136 (57)
281 (138) 125 (52)
300 to 366 (149 to 185) 100 (37)
Maximum Ambient for Actuator
°F (°C)
Close-off Pressure Rating
Close-off pressure ratings are listed in Table-3. Check the appropriate table to verify that the
selected valve, valve linkage,
application.
The actuator with hazardous location housing, valve, and valve linkage should be purchased
separately. See Table-3 for selections.
and actuator provide adequate close-off pressure for your
INSTALLATION
Inspection Inspect the package for damage. If damaged, notify the appropriate carrier immediately.
If undamaged, open the package and inspect the device for obvious damage. Return
damaged products.
Requirements • Tools (not provided):
– Appropriate wrenches for stem extensions, lock nuts, packing nuts, and brackets
– Appropriate screwdriver for actuator mounting screws
– TOOL-37, 1-5/8" open-ended wrench with a ma
• Training: Installer must be a qualified, experienced technician
Caution:
• Install the unit in accordance with the National Electric Code Article 500 and all
applicable local codes.
• Avoid locations where excessive moisture, corrosive fumes, or vibration is present.
• Install all two-way valves so that they close against the flow. An arrow on the valve body
or a tag indicates the proper flow direction.
• Always install three-way mixing valves with two inlets and one outlet.
• Always install three-way diverting valves with one inlet and two outlets.
• The actuators can be mounted in any position above the centerline of the valve body.
For steam applications where the ambient temperature approaches the limit of the
actuator, the valve stem should be mounted 45° from vertical. When selecting a
location, allow sufficient room for accessories and for service of the product.
ximum thickness of 3/16"
2 © Copyright 2010 Schneider Electric All Rights Reserved. F-27441-2
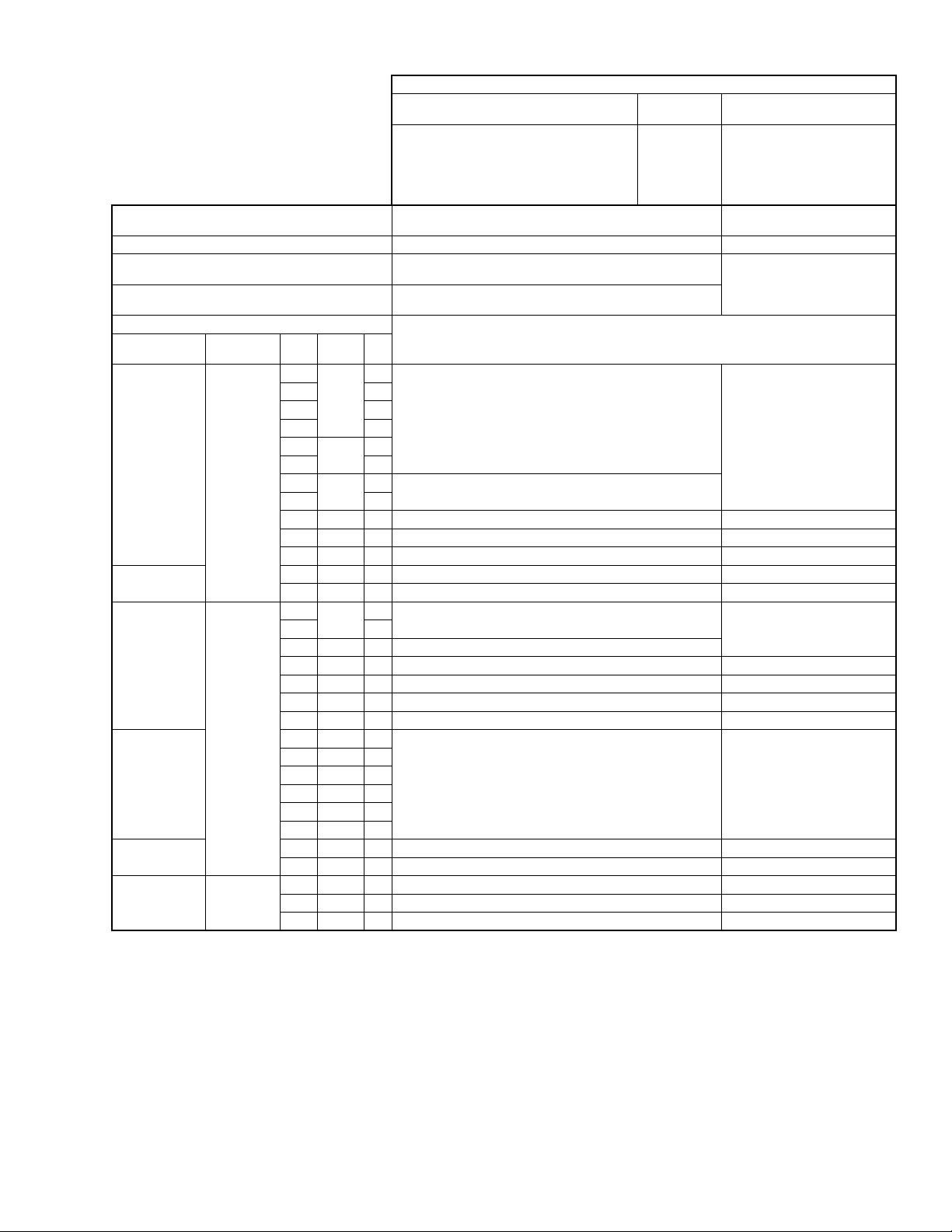
Table-3 Linkage Selection and Valve Close-Off Pressure Ratings for VB-7x xx and VB-9x1x Valve Bodies.
TYPICAL ACTUATOR PART NUMBERS
Spring Return No Normal
MA8-318, MA8-318-500
MA8-418, MA8-418-500
MP6-361, MP6-367
MP6-371, MP6-377, MP6-379,
MP6-465 MP7-4651
MP6-470, MP6-475, MP7-4751
Minimum Torque/Travel Required
Linkage for 1/2" to 2” VB-7xxx Series Valves AV-291 AV-293
Linkage for 2-1/2" to 3" VB-9xxx Series Bronze Body
Linkage for 2-1/2" to 4" VB-9313 Cast Iron Body
VALVE BODY INFORMATION CLOSE-OFF PRESSURE PSI (kPa)
Valve Body
t Number
Par
VB-7213-0-4-P
VB-7214-0-4-P
VB-7215-0-4-P
VB-7253-0-4-P
VB-7273-0-4-P
VB-9213-0-4-P
VB-9215-0-4-P
VB-7313-0-4-P
VB-7314-0-4-P
VB-7315-0-4-P
VB-7323-0-4-P
VB-9313-0-4-P
VB-9315-0-4-P
VB-9313-0-5-P
a
See Table-4 to set stem and cam position.
Description P
2-Way
3-Way
3-Way
125 lb
F
langed
Code
1
2 1.3
3 2.2
4 4.4
5
6 7.5
7
8 14
9 1-1/4" 20 90 (621) 200 (1379)
10 1-1/2" 28 65 (448) 140 (965)
11 2" 40 35 (241) 80 (552)
12 2-1/2" 65 20 (137) 50 (345)
13 3" 85 12 (83) 34 (234)
2
6 3/4" 7.5 220 (1517)
8 1" 14 150 (1034) 250 (1724)
9 1-1/4" 20 100 (689)
10 1-1/2" 28 60 (414) 140 (965)
11 2" 41 33 (228) 80 (552)
10 1-1/2” 28
11 2” 40
12 2-1/2" 67 20 (137) 50 (345)
13 3" 91 12 (83) 34 (234)
12 2-1/2" 74 20 (137) 50 (345)
.
13 3" 101 12 (83) 34 (234)
14 4" 170
4 1/2” 4.4
6 3/4” 7.5
8 1” 15
9 1-1/4” 20
lves
Va
Va
lves
Size Cv
0.4
1/2"
5.5
3/4"
10
1"
2.2
1/2"
50 lb.-in., 180° Rotation,
Plunger
150 lb.
AV-295 AV-296
–
250 (1724)
150 (1034)
250 (1724)
250 (1724) 250 (1724)
6 (41) 17 (117)
Posi
tion
MP6-421 MC6-351
a
No Normal Position
MC6-421
MC6-431
MP6-381
MP6-485
MC7-4311
175/220 lb.-in., 180° Rotation,
300 lb. Plunger
250 (1724)
250 (1724) 4 4.4
200 (1379)
F-27441-2 © Copyright 2010 Schneider Electric All Rights Reserved. 3