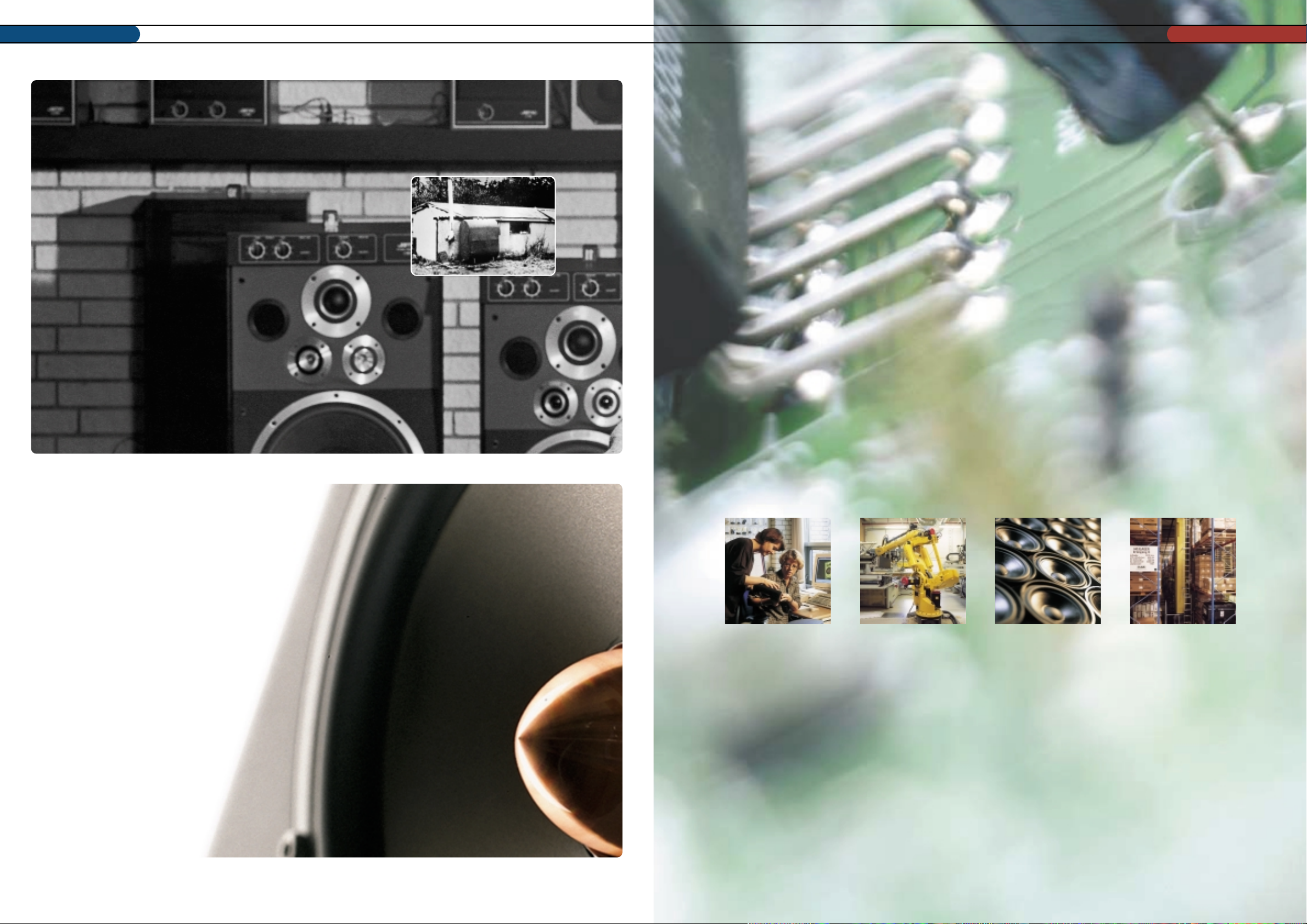
The story of Jamo begins in the Danish fishing village of Glyngøre.The year
is 1966, and Preben Jacobsen, a carpenter, decides to start building loud-
speakers in his little henhouse. He has a passion for good craftsmanship
and fine sound,and produces superbly designed loudspeakers with the
aid of the latest acoustic technologies. However, he is somewhat less
talented at selling so his brother-inlaw, Julius Mortensen, enters the
picture in 1968, bringing with him his export experience, gained in
the fishing industry.Jacobsen and Mortensen: Jamo.The stage is set
for an adventure to begin.
OUR HISTORY
In the years since then, Jacobsen's little henhouse has grown
to become a 30,000 m2/ 300,000 sq.ft state-of-the-art factory
while Jamo is now Europe's biggest manufacturer of loudspeakers. At the same time, customer demands have
become more individual and challenging.Which is lucky for
us because developing new solutions is a daily source of
inspiration in our work. Much has changed, but the soul
and the driving force behind Jamo is still the same:
we want to develop and build products that make a
difference to people’s lives, that connect on an
emotional level.
A chain is only as strong as its weakest link.
That’s why designing loudspeakers is not just a
question of selecting the best possible components
and materials, but also ensuring that they provide
the best solution when combined.
OUR PRODUCTION
The first step in the construction process is to set up an
advanced 3D computer model to provide a foundation for
both further design work and the programming of the
computer-controlled part of the production process. The
actual production environment brings together some of the
world’s most advanced robot machines and a team of vastly
experienced carpenters who take great pride in their craftsman-
ship. It is no coincidence that Jamo’s headquarters lies in a region
that is home to a large part of Denmark’s world renowned furniture
production industry. For Jamo, production and quality control are
simply two sides of the same coin all the way from the control of raw
materials to the painstaking final inspection of every single finished
loudspeaker. That’s your guarantee that the sound, finish, accessories,
packaging – in short, every aspect of a Jamo product – will totally match
your expectations.
What is good sound? There’s no simple answer to that
question because good sound is a highly subjective
experience. Not only do we respect that fact – we
consciously base our work upon it. This is clearly
expressed in the promise that lies at the foundation of our
work and our success: Jamo will create sound solutions
that make a difference to the individual. This promise is
built into all Jamo’s products. You can hear it in our
unrivalled sound quality. And you can see it in the stylish
finish that characterises every single detail.
OUR PROMISE
Jamo’s products are based on the Danish design tradition of
simplicity and functionality. We care about the complete
solution, not just the sound. In this catalogue, we hope you
will notice both the details and the harmonious integrity
that characterises Jamo products. They have been carefully
developed, designed and manufactured to provide you with
a unique experience. Or in other words: Jamo will make a
difference to you.
Product development
This is based on market
feedback, to ensure that
we have a good sense of
our customers’ wishes and
requirements. Jamo’s
innovative acoustic,
electronic and mechanical
engineers are responsible
for product development –
but the development
process is never concluded
until our experienced
panel of listeners has
approved the new product.
Construction
Everything is first modelled
in 3D computer software,
to make it easier to check
that the various
components, wooden
elements, etc., fit together.
This also means that
design optimisation is
possible at a much earlier
stage of the development
process. Such advanced 3D
applications, however, are
no replacement for our
experienced model
carpenters, who then
produce a perfect, full size
prototype.
Quality control
This begins with entry
point checking, during
which all of the raw
materials are subjected to
test sampling. Similarly,
samples of all production
components are tested
during the production
process.Then comes a final
inspection of every
product before it leaves
the factory. Moreover,
products are selected
every week from the
finished goods warehouse
and subjected to an
additional 100% quality
check of their sound,
finish, packaging,
accessories etc.
Warehouse
This is fully automated and
based on the latest
technology.Everything is
controlled by bar codes
and computers – right
from the time that the
orders are keyed into the
system until they are
delivered directly from
Glyngøre to outlets all over
Europe. For overseas
deliveries, Jamo makes use
of its finished goods
warehouses in Chicago
and Shanghai.
2 3