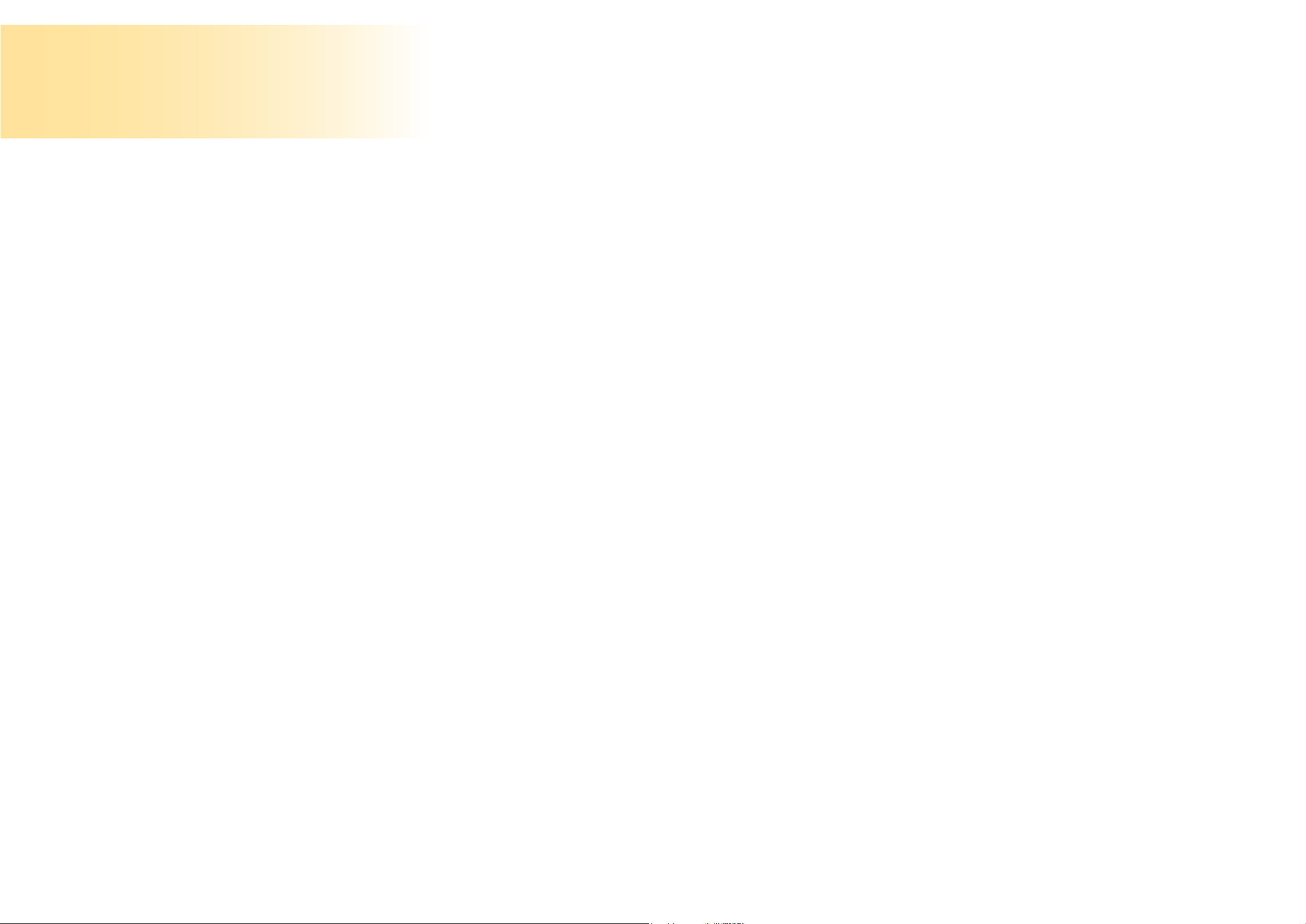
Why Calibrate?
• To comply with regulation
• To maximize process performance
• To maintain safety
• For quality control
Calibration of process
instrumentation is a necessary
function for two main reasons.
One, to comply with regulation;
and two, to maintain and control
process performance and product
quality.
Regulation is vital to ensure plant
and process safety and calibration
is now mandatory throughout the
process industry. Regulation is
also especially important where
traceability is vital to ensure the
quality of sensitive products such
as in the pharmaceutical sector
Calibration for process and
product quality control is
something that improves the
bottom line. Product quality must
be maintained and monitored
to eliminate any wastage issues
or customer litigation. Process
performance must be monitored
to ensure eciency of operation
as well as plant safety.
But what is calibration?
Basically, calibration involves the
comparison of two instruments or
measuring devices, one of which
is of known accuracy, to establish
the accuracy, or otherwise, of
the device to be calibrated.
Calibration is necessary because
all measuring devices drift over
time and calibration is carried out
to ensure we are measuring to
the accuracy required, accuracy
set on installation or accuracy set
later to some agreed value.
Optimize Your Calibration
Regime
When to calibrate is often
asked. Some calibrate
strictly to manufacturers’
recommendations. Some calibrate
on a regular frequency basis, such
as annual shut-down. Historically,
such calibration sometimes
involved taking the measuring
device out of service and sending
it to a calibration lab. Here
calibration tests are carried out
by instruments which are veried
to national standards and labs
are audited by national standards
authorities.
Today’s laboratory calibration
equipment oers easy
communication with software
and can provide 100% automated
calibration of pressure
transducers and transmitters.
However, this is not a perfect
solution because, naturally,
instruments can drift between
these calibration intervals. An
obvious answer to this is to
calibrate more frequently, but this
entails increased time and cost,
both in lost production and in
calibration resource.
Fortunately, today’s calibration
management software can
analyse collected calibration
data and determine the optimum
calibration frequency for each
instrument or measuring device,
based on a set of programmable
operating scenarios and safety
margins. But more of that later!
Communicate and
Calibrate
Commissioning and conguration
of instrumentation is a very
important part of a plant
technician’s working life – and
this requires communication
with the instrument. Most of
the instrumentation in today’s
plants are analogue, operating
on a 4-20 mA basis. Many new
plants, especially in the Far
East, are eldbus-based and use
digital signals. However, most of
the analogue-wired plants now
use the HART communication
protocol for commissioning and
conguration. Essentially this
converts the digital signal to an
analogue output for transmission
on the plants 4-20 mA system.
HART enabled instruments have
several features that signicantly
reduce the time required to
commission or congure a
HART network or loop. HART
instruments are tagged and
contain conguration data. HART
devices also have a loop test
feature, to ensure that the device
is connected properly to support
devices such as indicators,
recorders and DCS displays. In
addition, the analogue value can
be compared with the digital
value as a further integrity check.
HART devices can also be
calibrated to ensure that the
digital value it reads is converted
into the correct analogue
output. This is an essential step
as it is often easy to make the
mistake that because a device is
measuring, it is in fact measuring
correctly. It is also important
to remember that just because
a device is digital, this does
not mean that it doesn’t need
calibration.
And it is important to realize
that a communicator is not a
calibrator and a calibrator is not a
communicator. Many of the handheld devices on the market are
in fact communicators, without
the ability to calibrate. And no
communicator has the ability to
calibrate pressure.
Automating the
Calibration Process
Naturally, calibration is an
important aspect of maintenance
and if calibration data is analysed
correctly, it can help maintain and
improve compliance, eciency,
quality and safety. However,
managing the calibration of
1000s of plant instruments
and then analyzing all the data
to a level required for trend
evaluation is not a simple task.
Even today, a surprising number
of organisations still use pen
and paper to record calibration
results. This can mean that an
instrument engineer can spend
as much as 50% of his time
working on documentation and
paperwork, preparing calibration
instructions, making notes of
calibration results in the eld and
documenting and archiving data.
Apart from the valuable time
involved, paper-based recording
also brings with it the chances of
transcription mistakes.
Today’s advanced portable
calibrators can store a vast
amount of data and can even
be used to create and review
calibration certicates and
custom reports, which can be
electronically signed o. This data
can subsequently be transferred
to a PC when convenient for
printing and archiving. Calibration
management software is available
to automate the calibration
process by stepping through the
test points, calculating errors and
reporting Pass/Fail conditions.
Calibration management
software can produce reports
as mentioned but also schedule
work and even analyse device
trends.