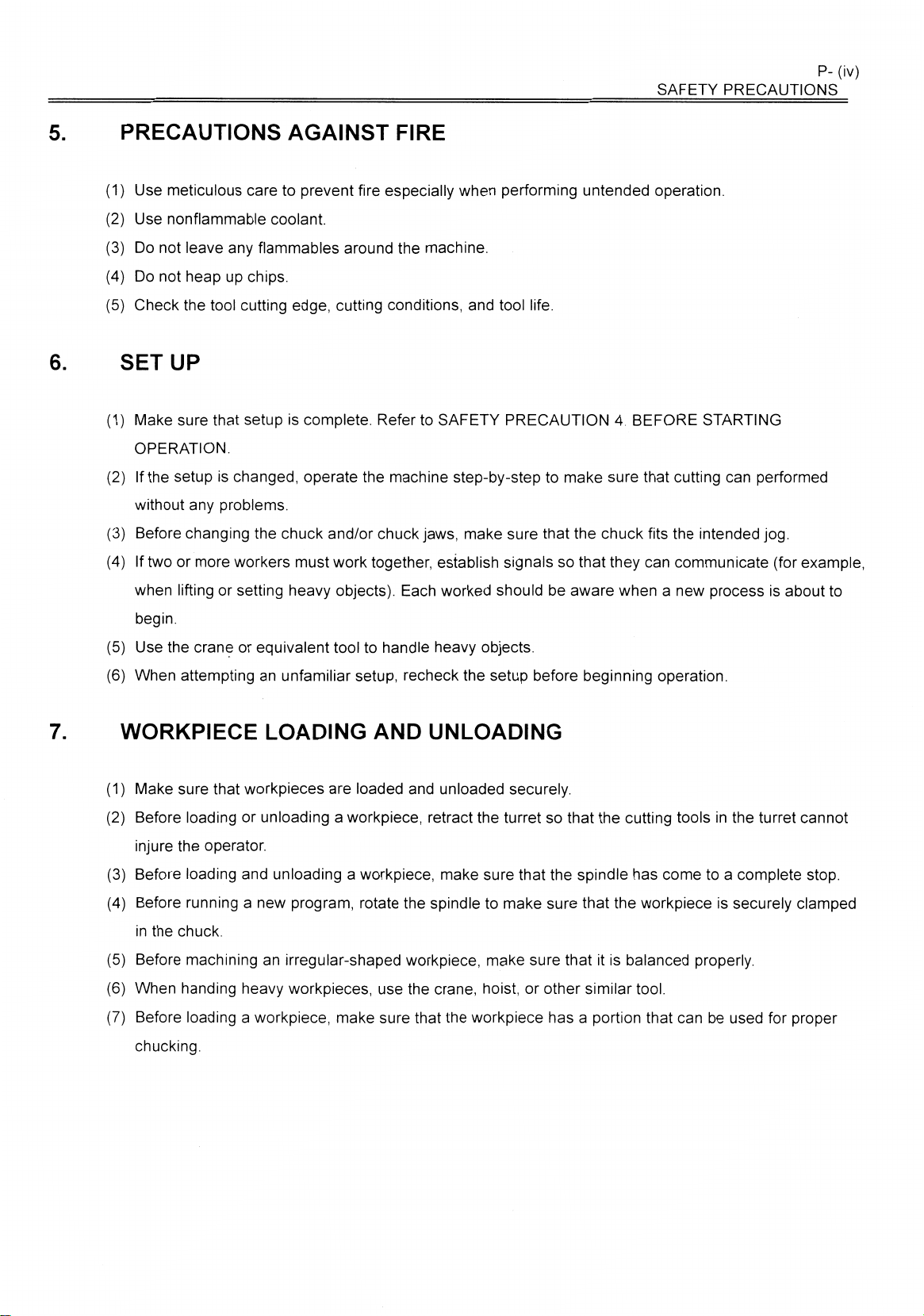
SAFETY
P-
PRECAUTIONS
(iv)
5.
6.
PRECAUTIONS
(1)
Use
meticulous
(2)
(3)
(4)
(5)
(1)
(2)
(3)
(4)
nonflammable
Use
Do
Do
Check
SET
Make
OPERATION.
If
without
Before
If
when
not
not
the
two
leave
heap
the
UP
sure
setup
any
changing
or
lifting
tool
that
is
problems.
more
or
any
up
changed,
workers
setting
AGAINST
care
to
coolant.
flammables
chips.
cutting
setup
the
edge,
is
chuck
heavy
prevent
cutting
complete.
operate
and/or
work
must
objects).
FIRE
especially
fire
around
the
conditions,
RefertoSAFETY
machine
the
jaws,
chuck
together,
Each
when
machine.
and
step-by-step
make
establish
worked
performing
tool
life.
PRECAUTION
make
to
sure
that
the
signals
should
so
be
that
aware
untended
4.
BEFORE
sure
chuck
they
when
operation.
that
cutting
fits
the
can
communicate
a
new
STARTING
can
performed
intended
process
jog.
(for
is
example,
about
to
7.
begin.
(5)
(6)
Use
When
crane
the
attempting
WORKPIECE
(1)
(2)
(3)
(4)
(5)
(6)
(7)
sure
Make
Before
injure
Before
Before
in
Before
When
Before
loading
the
loading
running
the
chuck.
machininganirregular-shaped
handing
loading
chucking.
operator.
or
that
workpieces
or
and
a
heavy
a
equivalent
an
unfamiliar
LOADING
are
unloading
unloading
program,
new
workpieces,
workpiece,
tool
handle
to
setup,
AND
loaded
a
workpiece,
a
workpiece,
rotate
use
make
sure
heavy
objects.
recheck
the
setup
UNLOADING
and
unloaded
make
crane,
the
the
sure
to
make
hoist,
workpiece
retract
the
spindle
workpiece,
the
that
before
securely.
so
turret
that
make
sure
other
or
that
the
sure
that
has
beginning
the
cutting
spindle
that
the
is
balanced
it
similar
a
portion
operation.
toolsinthe
cometoa
has
workpiece
tool.
that
can
complete
securely
is
properly.
be
used
turret
for
cannot
stop.
clamped
proper
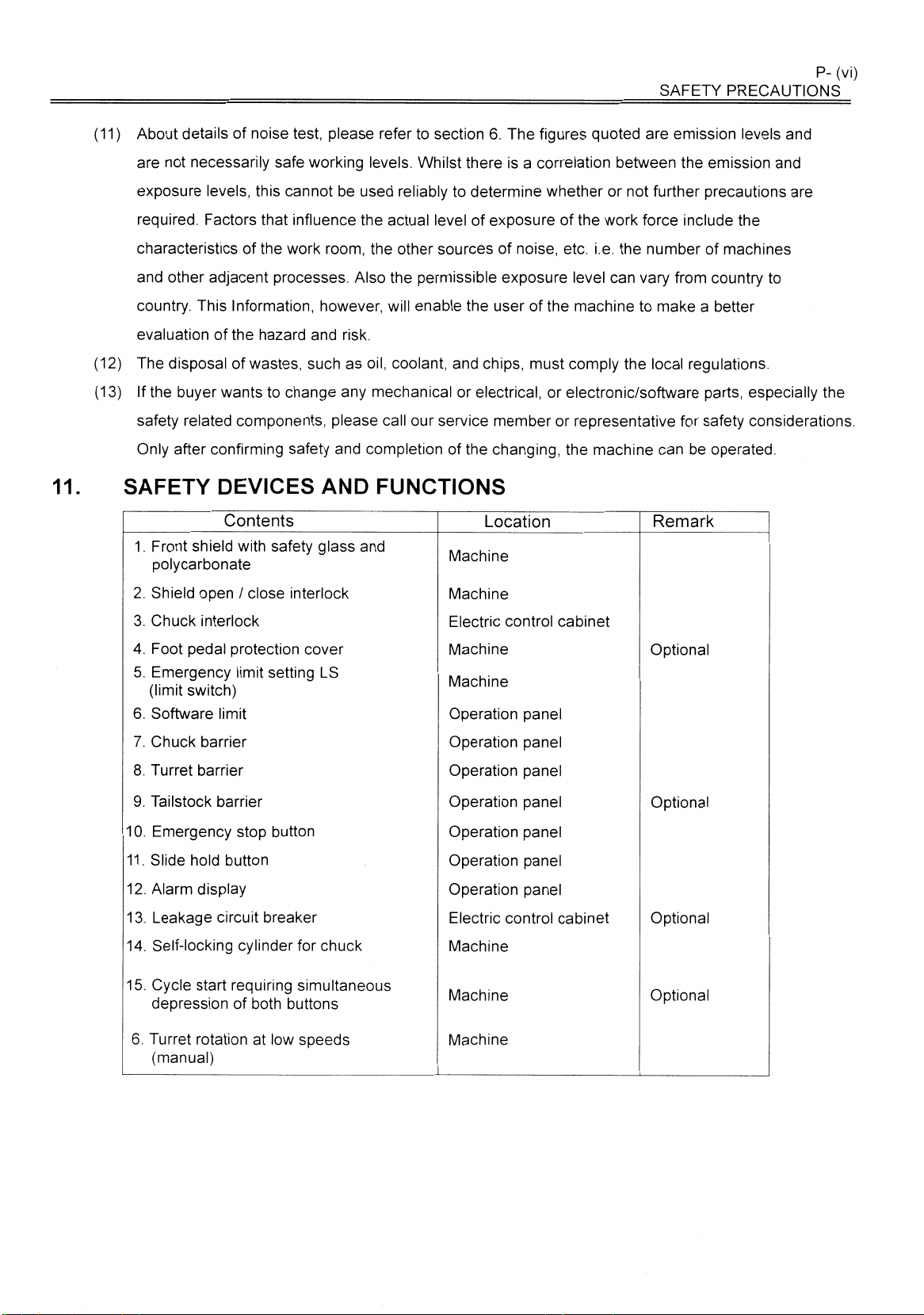
(11)
About
detailsofnoise
test,
please
refer
section6.The
to
figures
quoted
SAFETY
are
emission
P-
PRECAUTIONS
levels
and
(Vi)
11.
are
not
exposure
required.
characteristicsofthe
and
other
country.
evaluationofthe
(12)
The
disposal
If
(13)
the
safety
Only
buyer
related
after
SAFETY
1.
Front
polycarbonate
2.
Shield
3.
Chuck
necessarily
levels,
this
Factors
adjacent
Information,
This
hazard
wastes,
of
wants
components,
confirming
DEVICES
Contents
shield
with
/
open
interlock
close
safe
working
cannot
that
influence
work
processes.
and
such
to
change
safety
safety
interlock
be
used
the
room,
Also
however,
risk.
as
oil,
any
please
and
completion
AND
glass
and
levels.
the
mechanical
reliably
actual
other
the
will
enable
coolant,
our
call
Whilst
there
determine
to
level
of
sources
permissible
the
and
or
service
of
the
FUNCTIONS
Machine
Machine
Electric
is
a
exposure
noise,
of
exposure
user
of
chips,
must
electrical,
member
changing,
Location
control
correlation
whether
of
etc.
the
or
electronic/software
or
the
cabinet
between
or
not
the
work
i.e.
the
can
level
machine
comply
representative
the
machine
the
emission
further
force
precautions
include
the
numberofmachines
vary
to
local
make
can
country
from
a
better
regulations.
parts,
safety
for
be
operated.
especially
considerations.
Remark
and
are
to
the
4.
Foot
5.
Emergency
(limit
6.
Software
Chuck
7.
Turret
8.
Tailstock
9.
Emergency
10.
11.
Slide
12.
Alarm
13.
Leakage
14.
Self-locking
Cycle
15.
depression
6.
Turret
(manual)
pedal
switch)
limit
barrier
barrier
barrier
hold
display
circuit
start
rotation
protection
setting
limit
button
stop
button
breaker
cylinder
requiring
of
both
low
at
cover
LS
for
chuck
simultaneous
buttons
speeds
Machine
Machine
Operation
Operation
Operation
Operation
Operation
Operation
Operation
Electric
control
Machine
Machine
Machine
panel
panel
panel
panel
panel
panel
panel
cabinet
Optional
Optional
Optional
Optional
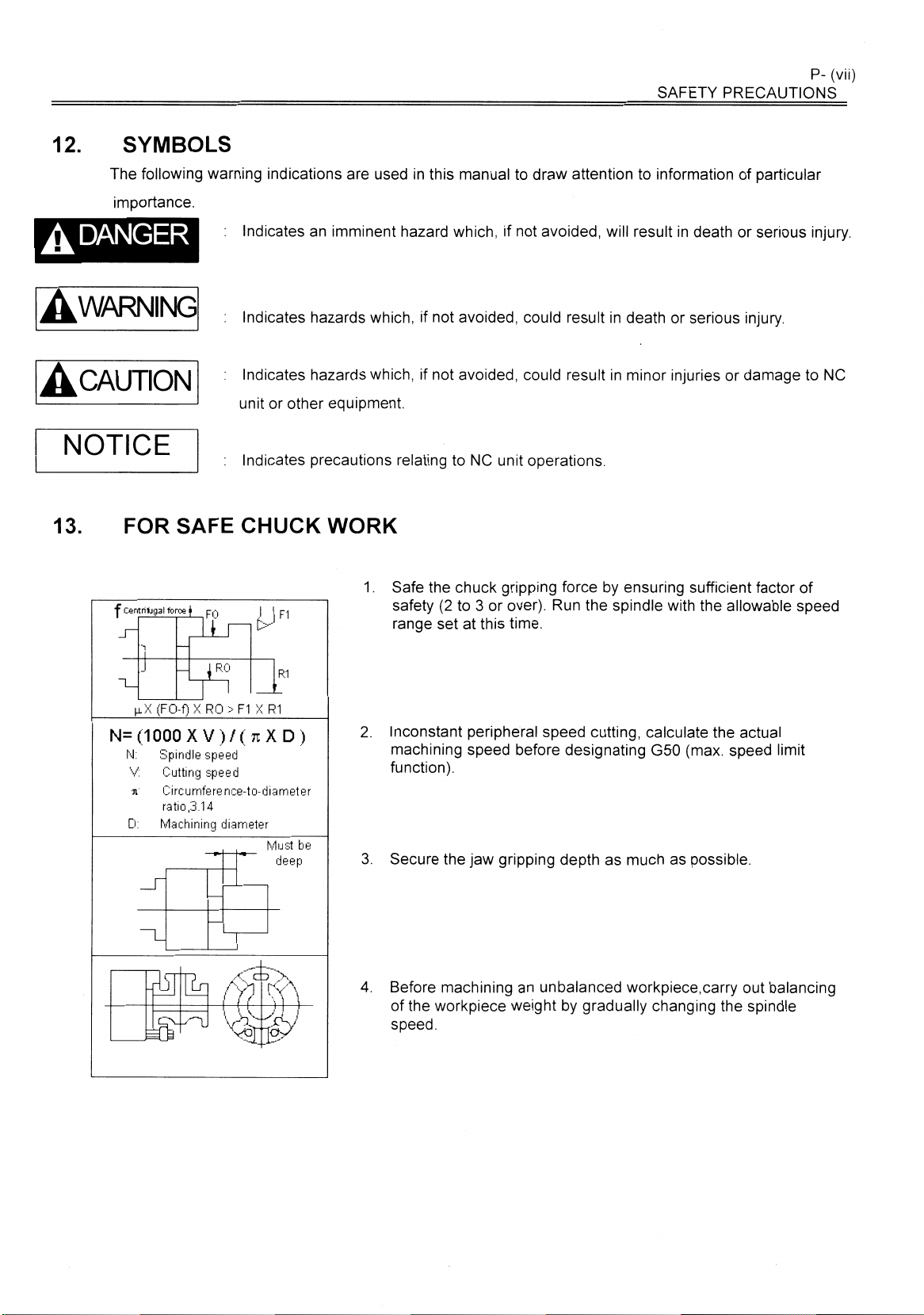
SAFETY
P-
PRECAUTIONS
(vii)
12.
A
|AWARNING|
ACAUTION
NOTICE
13.
SYMBOLS
The
following
importance.
DANGER
FOR
Cgritriliqal
SAFE
force
-i
warning
f
pQ
1R0
indications
Indicates
:
Indicates
Indicates
unitorother
Indicates
CHUCK
F1
R1
are
usedinthis
an
imminent
hazards
hazards
precautions
which,
which,
equipment.
WORK
.
1
hazard
if
if
relating
Safe
the
safety
range
which,
not
not
to
(2
set
manual
avoided,
avoided,
unit
NC
chuck
or
to
3
this
at
to
draw
not
if
avoided,
could
could
operations.
gripping
over).
time.
attention
will
resultindeath
in
result
force
by
Run
the
spindle
to
information
resultindeath
or
serious
minor
injuriesordamage
ensuring
sufficient
with
the
of
particular
or
serious
injury.
factor
allowable
injury.
NC
to
of
speed
N=
N:
M.X
(1000
V:
n
D:
(FO-f)
RO
X
F1
>
XV)/(JIXD)
Spindle
speed
Cutting
speed
Circumference-to-diameter
3.
14
ratio,
Machining
diameter
am
X
R1
Must
deep
be
2.
Inconstant
machining
function).
3.
Secure
4.
Before
of
speed.
machining
the
workpiece
peripheral
speed
jaw
the
speed
before
gripping
unbalanced
an
weight
cutting,
designating
depth
as
by
gradually
calculate
(max.
G50
much
as
workpiece,
changing
the
actual
speed
possible.
carry
the
out
balancing
spindle
limit
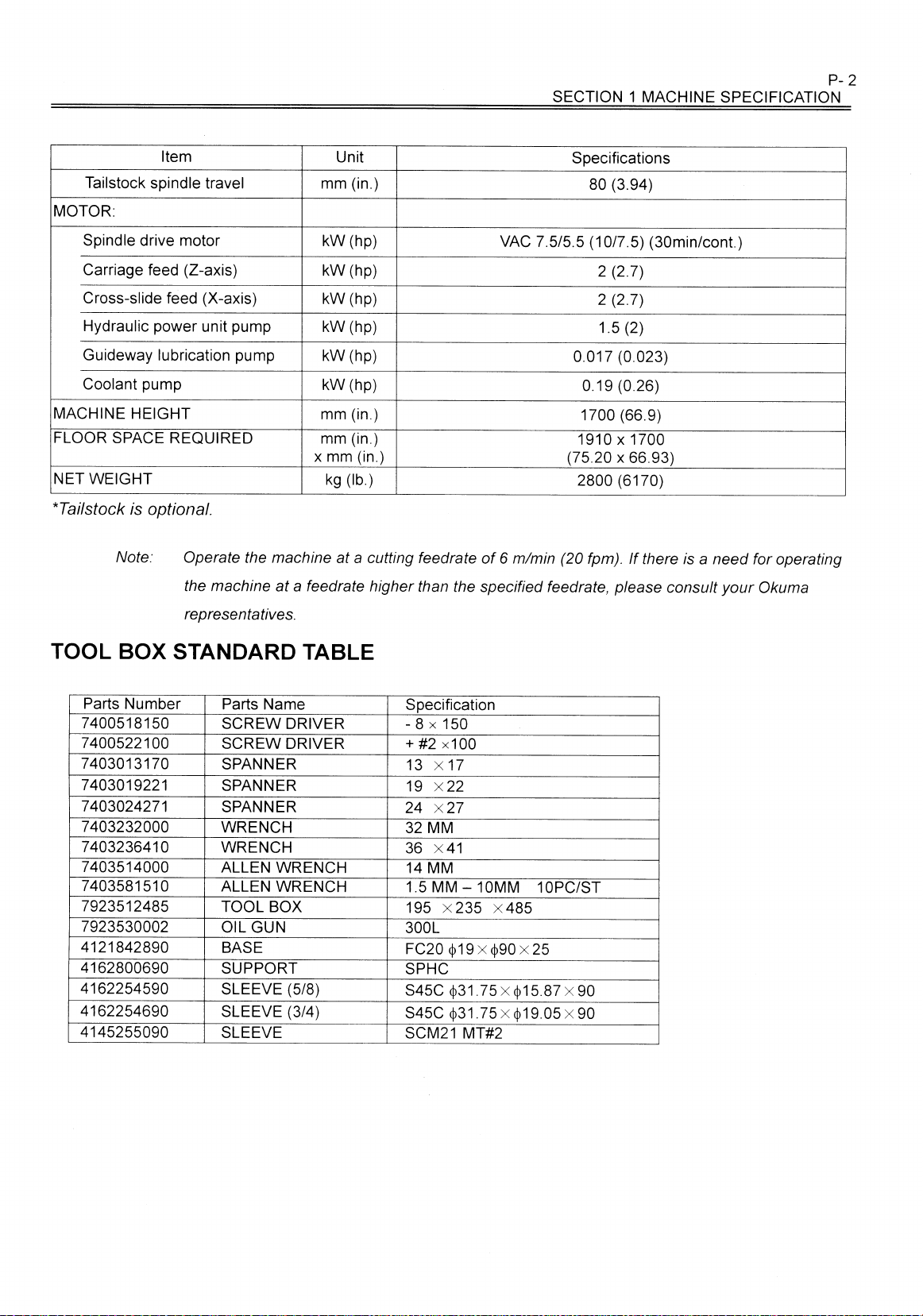
SECTION
MACHINE
1
P-2
SPECIFICATION
Tailstock
MOTOR:
Spindle
Carriage
Cross-slide
Hydraulic
Guideway
Coolant
MACHINE
FLOOR
NET
SPACE
WEIGHT
*Tailstock
drive
pump
HEIGHT
optional.
is
Note:
Item
spindle
feed
power
motor
(Z-axis)
feed
travel
(X-axis)
unit
lubrication
REQUIRED
Operate
the
machine
representatives.
pump
pump
the
x
machine
a
at
feedrate
Unit
(in.)
mm
kW(hp)
kW(hp)
kW(hp)
kW
(hp)
kW
(hp)
kW
(hp)
mm
(in.)
mm
(in.)
mm
(lb.)
kg
at
a
(in.)
cutting
higher
feedrate
than
the
VAC
of
6
m/min
specified
Specifications
5/5.5
7.
0.017
0.19
1700
1910
(75.20
2800
(20
feedrate,
(3.94)
80
(10/7.5)
2
(2.7)
2
(2.7)
1.5(2)
(0.023)
(0.26)
(66.9)
x
x66.93)
(6170)
fpm).
please
(30min/cont.)
1700
If
there
is
consult
a
need
your
operating
for
Okuma
TOOL
Parts
7400518150
7400522100
7403013170
7403019221
7403024271
7403232000
7403236410
7403514000
7403581510
7923512485
7923530002
4121842890
4162800690
4162254590
4162254690
4145255090
BOX
Number
STANDARD
Parts
Name
SCREW
SCREWDRIVER
SPANNER
SPANNER
SPANNER
WRENCH
WRENCH
ALLEN
ALLEN
TOOL
OIL
BASE
SUPPORT
SLEEVE
SLEEVE
SLEEVE
WRENCH
WRENCH
BOX
GUN
TABLE
DRIVER
(5/8)
(3/4)
Specification
-
x
8
150
#2
+
x100
13
X
17
19
22
X
X
24
27
32
MM
36
X
41
MM
14
1.5MM-10MM
195
X
235
300L
FC20
SPHC
S45C
S45C
SCM21
x
9
4>1
(|>31
.75
<|>31.
MT#2
tj)90
75
X485
\
(|)1
x<t)1
10PC/ST
x
25
5.87
9.05x90
xgp
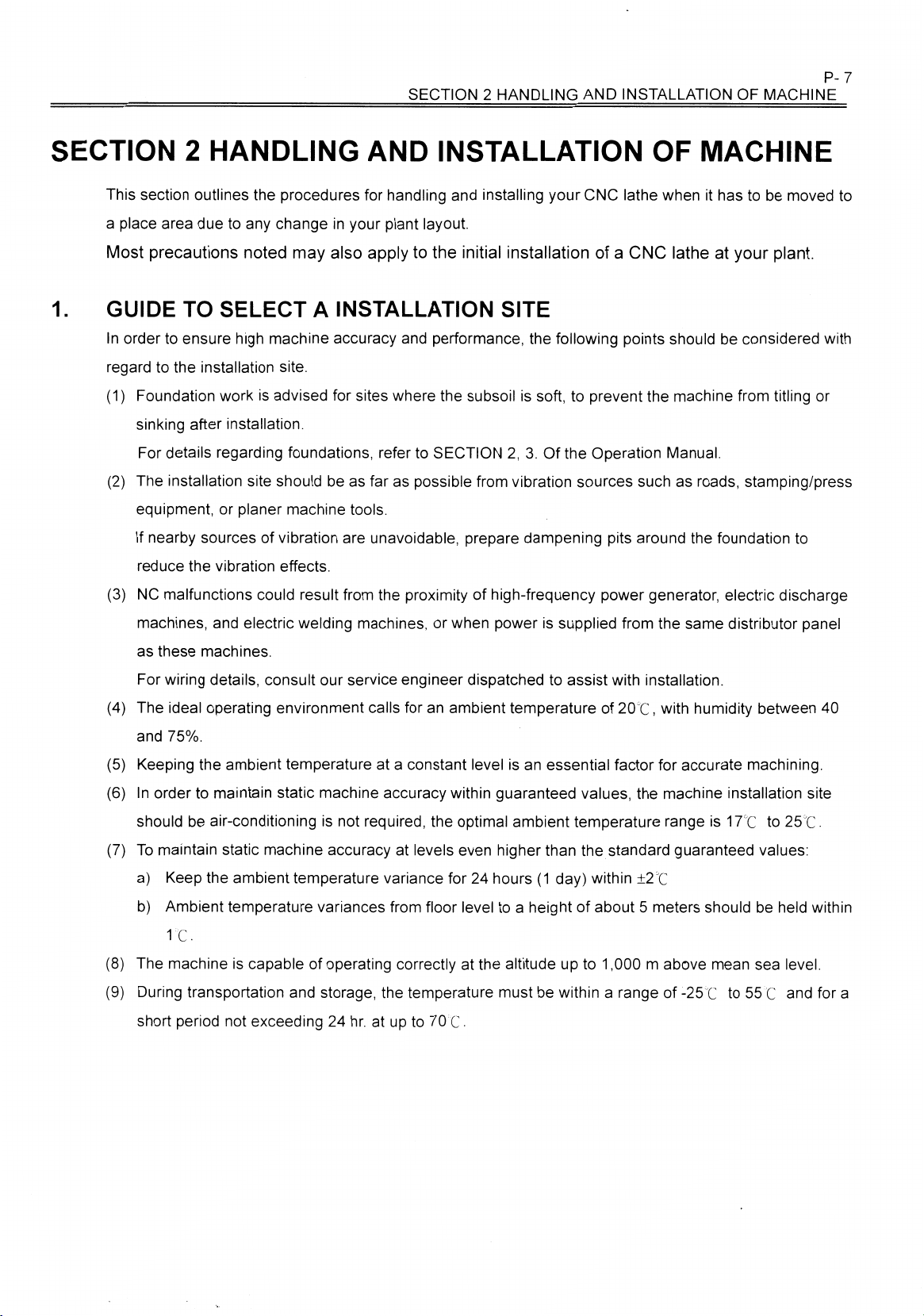
SECTION
HANDLING
2
AND
INSTALLATION
OF
MACHINE
P-7
SECTION
This
section
1.
a
Most
GUIDE
In
regard
(1)
(2)
(3)
area
place
precautions
order
to
to
Foundation
sinking
For
details
The
equipment,orplaner
If
nearby
reduce
NC
malfunctions
2
HANDLING
outlines
due
to
the
any
noted
TO
SELECT
ensure
the
installation
high
installation
workisadvised
installation.
after
regarding
site
sources
the
vibration
of
could
procedures
change
may
A
machine
site.
foundations,
should
machine
vibration
effects.
result
your
in
also
AND
handling
for
plant
apply
INSTALLATION
and
layout.
the
initial
to
INSTALLATION
accuracy
for
as
be
tools.
are
from
and
sites
where
refer
to
far
possible
as
unavoidable,
the
proximity
performance,
the
SECTION
installing
installation
SITE
the
subsoil
prepare
of
is
2,
3.
from
vibration
dampening
high-frequency
your
following
soft,
the
Of
CNC
ofaCNC
to
prevent
Operation
sources
pits
power
OF
MACHINE
lathe
when
it
hastobe
lathe
at
shouldbeconsidered
points
the
machine
Manual.
as
such
around
generator,
roads,
the
foundation
moved
plant.
your
from
titling
stamping/press
to
electric
discharge
to
with
or
(4)
(5)
(6)
(7)
(8)
(9)
machines,
as
these
For
wiring
The
and
Keeping
In
ordertomaintain
should
To
maintain
a)
b)
The
During
short
and
machines.
details,
ideal
operating
75%.
the
ambient
be
air-conditioning
static
the
Keep
Ambient
1
C.
machine
transportation
period
not
electric
ambient
temperature
is
capable
welding
consult
environment
temperature
static
machine
temperature
and
exceeding
our
service
machine
is
not
accuracy
variances
of
operating
storage,
24
hr.
machines,
engineer
calls
for
a
at
constant
accuracy
required,
levels
at
variance
from
correctly
the
temperature
atupto
or
an
the
floor
70
ambient
for
C.
when
power
dispatched
level
guaranteed
within
optimal
higher
even
24
hours
level
to
the
at
must
is
supplied
assist
to
temperature
isanessential
values,
ambient
a
altitude
than
(1
day)
height
be
within
temperature
the
of
up
to
from
with
of
20°C
factor
standard
within
about
1,000
a
range
the
same
installation.
,
humidity
with
for
accurate
the
machine
range
guaranteed
±2'C
5
meters
above
m
of
-25
distributor
between
machining.
installation
is
17°Cto25"C.
values:
shouldbeheld
mean
sea
level.
to
55
C
and
C
panel
40
site
within
for
a