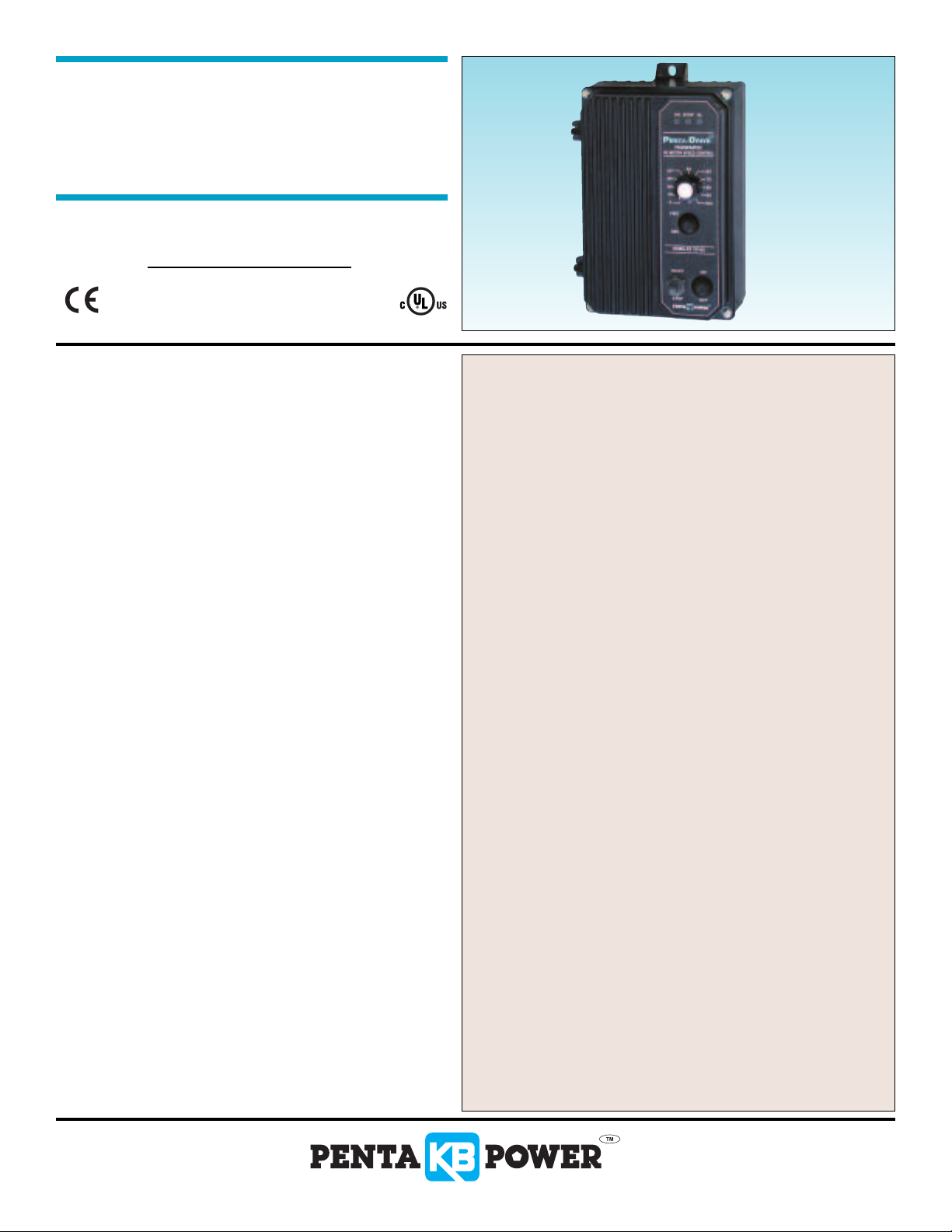
KBRC-240D
Full-Wave 4-Quadrant Regenerative Drive
for Speed & Torque Control of PM & Shunt DC Motors
NEMA-4X / IP-65
Rated for 1/10 - 1 HP (90 Volts DC) @115 Volts AC, 50/60 Hz
and 1/5 - 2 HP (180 Volts DC) @ 208/230 Volts AC, 50/60 Hz
W
ashdown and Watertight for Indoor and Outdoor Use
*
Conveyors • Feeders • Packaging Equipment
•
• Positioners • Textile Equipment • Indexers
TYPICAL APPLICATIONS
DATASHEET D-430
odel KBRC-240D
M
KB Part No. 8840
Black Case)
(
KB Part No. 8841
White Case)
(
STANDARD FEATURES
• Industrial Duty Die-Cast Aluminum Case: Available in black finish
(P/N 8840) and white FDA approved finish (P/N 8841).
Front Panel LEDs:Power On (ON), Stop (STOP) and Overload (OL).
•
• PC Board LEDs: Power On (PWR ON), Overload (OL), Forward
Enable (FWD EN) and Reverse Enable (REV EN).
• Run Relay: Used to signal a warning or to shut down other equipment
if the control is put into “stop” or times out in TCL.
• Start/Stop Switch: Provides electronic start and stop functions.
• Barrier Terminal Blocks: Facilitates wiring of motor, AC line, Tach-
generator and run relay.
PROTECTION FEATURES
• AC Line Transient Protection: Provides protection to power devices
from AC line transients.
• Auto-Inhibit®: Allows rapid, safe cycling of the AC line.
• Motor Burnout Protection (I x t): Shuts down control if the motor is
overloaded for a predetermined amount of time.
• Regeneration Overspeed Protection: Prevents power bridge failure
in extreme overhauling conditions.
TRIMPOT ADJUSTMENTS
• Offset (OFFSET) • Reverse CL (REVCL)
• Reverse Accel (RACC) • IR Comp (IR)
• Forward Accel (FACC) • Response (RESP)
• Maximum Speed (MAX) • Dead Band (DB)
Forward CL
•
(FWDCL) •
imed CL
T
(TCL)
JUMPER SELECTABLE FEATURES
• J1/J2 (115V, 230V): Selects AC line input voltage.
• J3 (A90, A180, T7, T50): Selects motor voltage or tach feedback.
• J4 (1.7A, 2.5A, 5A, 7.5A, 10A): Selects motor current.
• J5 (10V, 15V): Selects analog input voltage.
• J6 (SPD, TRQ): Selects control mode.
J7 (S/L, NL):
•
•
J8 (TCL, NTCL):
J9 (RTS, CTS):
•
J10 (NC, NO):
•
1 (EN):
J1
•
Selects Linear or Non-Linear
Selects current limit mode.
Selects stopping mode.
Selects run relay output contacts.
Enable Jumper
.
Torque Mode.
OPTIONAL ACCESSORIES
• Forward-Stop-Reverse Switch (P/N 9485): Provides motor revers-
ing and regenerative braking.
• Power On/Off Switch (P/N 9486): Disconnects the AC line.
• Signal Isolator SIRC (P/N 8842): Provides isolation between a non-
isolated signal voltage source and the KBRC-240D.
• Auto/Manual Switch (P/N 9487): Selects signal input from either the
SIRC Signal Isolator or the Main Speed Potentiometer.
Note: * Requires CE RFI filter KBRF-200A
(KB P/N 9945) or equivalent.
DESCRIPTION
The KBRC-240D is a Full-W
IP-65 washdown and watertight enclosure. It is designed to operate 90 and
180 Volt Permanent Magnet and Shunt Wound DC motors in a bidirectional
mode. It provides 4-quadrant operation, which allows forward and reverse
torque in both speed directions. This allows the control to maintain constant
speed with overhauling loads and provides rapid instant reversing and
controlled braking. Because of its excellent performance, the control can
replace servo drives in many applications.
The KBRC-240D has a Regeneration Overspeed Protection Circuit,
which prevents failure of the power bridge in extreme overhauling conditions. Motor overload protection (I x t) will shut down control if the motor is
overloaded for a predetermined amount of time. The exclusive Auto-Inhibit
circuit allows safe, smooth starting during rapid cycling of the AC line.
Due to its user-friendly design, the KBRC-240D is easy to install and
operate. Tailoring to specific applications is accomplished via selectable
jumpers and trimpot adjustments. However, for most applications, no
adjustments are necessary.
The KBRC-240D can be operated from a two or three wire start/stop
circuit or can be started from the AC line. A set of dedicated normally open
or normally closed relay contacts are provided, which are activated via the
start/stop circuit. They can be used to turn on or off equipment or to signal
a warning if the control is put into Stop Mode or times out in TCL.
Main features of the KBRC-240D include Speed or Torque control
modes. In Linear Torque mode (S/L), speed and torque vary linearly as a
function of main speed potentiometer rotation or input signal. In Non-Linear
Torque mode (NL), the torque is varied by the main speed potentiometer or
input signal, and remains constant throughout the motor’s entire speed
range. In addition, Regenerate-to-Stop (R
ing modes are also provided.
Standard front panel features of the KBRC-240D include diagnostic
LEDs (for Power On, Stop and Overload), a Start/Stop Switch and a Main
Speed Potentiometer. Other features include Barrier Terminal Blocks (facilitates wiring of the AC line, motor, tach-generator and run relay), adjustable
trimpots (OFFSET
TCL), selectable jumpers (AC line voltage, motor voltage or tach feed
and
back, motor current, analog input voltage, control mode, torque mode, cur
rent limit mode, regeneration mode, run relay and enable) and LEDs (Power
On, Overload, Forward Enable and Reverse Enable).
Optional accessories for the KBRC-240D include a Forward-StopReverse Switch, a Power On/Off Switch, a Signal Isolator and an
Auto/Manual Switch. Quick-connect terminals are provided for easy
installation of all accessories.
, RACC, FACC, MAX, FWDCL, REVCL, IR, RESP, DB
ave Regenerative Drive in a NEMA-4X/
TS) or Coast-to-Stop (CTS) stop-
-
-
®
Complete Line of Motor Drives
A
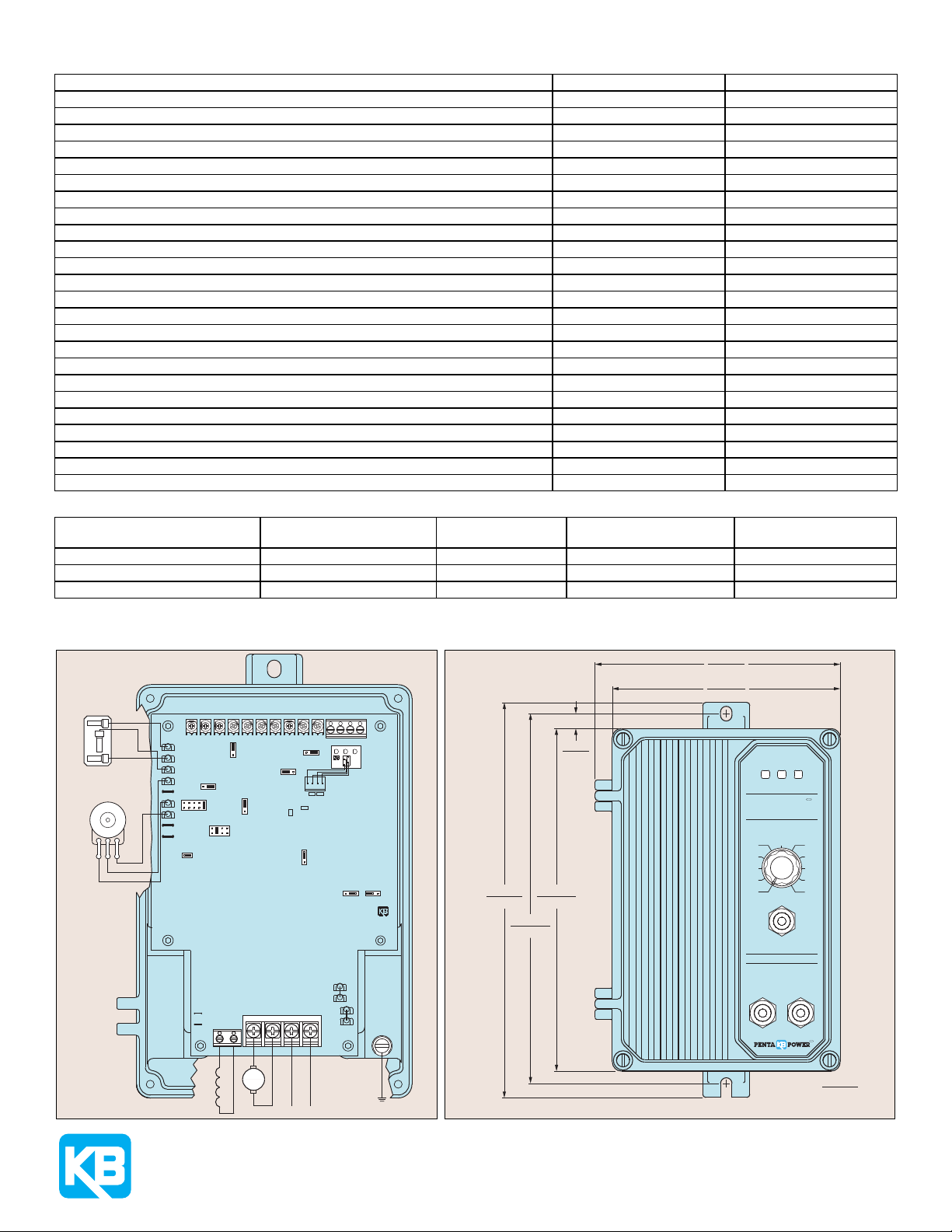
DATASHEET D-430
127
5.00
Maximum Depth
O
LSTOPON
REGENERATIVE
DC MOTOR SPEED CONTROL
60
70
90
80
100
50
40
30
1
0
20
0
R
EV
FWD
STOP
START
MANUAL
AUTO
NEMA-4X / IP-65
0.357
9.07
8.88
8.23
209
225
9.49
241
5
.89
150
5.47
1
39
KBRC-240D Shown with optional Forward-Brake-Reverse and Auto/Manual Switches
R
ecommended
Mounting Screw: 1/4" (M6)
PENTA-DRIVE
™
™
%
BLK
RED
WHT
STOP
CL
ON
B
G
R
Y
START/STOP
SWITCH
WHT
POTENTIOMETER
MAIN SPEED
ORG
VLT
GROUND
(EARTH)
AC LINE
+
+
FIELD
-
MOTOR
(SHUNT MOTORS ONLY)
L2A L2B
L2
M2 L1
TB1
M1
F-
F1
F2
TB2
F+
M
-
J1
KBRC
115V230V
J2
115V
L1A L1B
230V
FWD
EN
REV
EN
R
TS
J9
J11
E
N
C
TS
N
L
J
7
S
/L
A180
T50
T7
J3
A90
N
TCL
CON1
J8TCL
PWR ON
O
L
J
6
T
RQ SPD
5A
7.5A
10A
1.7A
2.5A
J4
L
ED BOARD
TB3
NO
N
C
J
10
15V
1
0V
J
5
STOPSIG STARTRETC OM +15VEN COM -15V
T+T-TCLDBIR RESPFWDCLFACC MAXRACCOFFSET REVCL RELAY
MODEL KBRC-240D (KB Part Nos. 8840 and 88411) – GENERAL PERFORMANCE SPECIFICATIONS
arameter
P
C Line Input Voltage (Volts AC, ±10%, 50/60 Hz)
A
rmature Voltage Range at 115 Volts AC Line (Volts DC)
A
rmature Voltage Range at 208/230 Volts AC Line (Volts DC)
A
ield Voltage at 115 Volts AC Line (Volts DC)
F
ield Voltage at 208/230 Volts AC Line (Volts DC)
F
ignal Following Input (Non-Isolated
S
ignal Following Linearity (% Base Speed)
S
ine Regulation (% Base Speed)
L
rmature Feedback Load Regulation (% Base Speed)
A
ach-Generator Feedback Load Regulation (% Set Speed)
T
aximum Load Capacity (% for 2 Minutes)
M
urrent Ranges (Amps DC)
C
peed Range (Ratio)
S
perating Temperature Range (°C)
O
ffset Trimpot (OFFSET) Range (% Base Speed)
O
everse Acceleration Trimpot (RACC) Range (Seconds)
R
orward Acceleration Trimpot (FACC) Range (Seconds)
F
aximum Speed Trimpot (MAX) Range (% Base Speed)
M
orward Current Limit Trimpot (FWDCL) Range (% Range Setting)
F
3
Range (Volts DC)
)
Reverse Current Limit Trimpot (REVCL) Range (% Range Setting) 0 – 200 150
R Compensation Trimpot (IR) Range at 90 Volts DC Output (Volts DC at Full Load)
I
IR Compensation Trimpot (IR) Range at 180 Volts DC Output (Volts DC at Full Load) 0 – 30 10
eadband Trimpot (DB) Range (% Base Speed)
D
imed Current Limit Trimpot (TCL) Range (Seconds)
T
pecification
S
15 and 208/230
1
– ±90
0
2
– ±90
0 – ±180
0
,
00/50
1
00/100
2
– ±10, 0 – ±15
0
1 —
0.5
±
1
±
1
±
50
1
.7, 2.5, 5, 7.5, 10
1
0:1
5
– 45
0
– ±10
0
.2 – 15
0
.2 – 15
0
0 – 110
7
– 200
0
– 15
0
– ±3
0
– 15
0
actory Setting
F
2
– ±180
0
– ±15
0
1
1
0
ELECTRICAL RATINGS
AC Line Input Voltage ±10%, 50/60 Hz
(Single Phase Volts AC)
115
208/230
208/230
Notes: 1. KB Part No. 8841 is white FDAapproved finish., 2. Step-down operation: Motor may have reduced brush life. Consult motor manufacturer.
3. Requires an isolated signal. If a non-isolated signal is used, install the Signal Isolator SIRC (P/N 8842).
CONTROL LAYOUT & CONNECTION DIAGRAM
Maximum AC Line Input Current
(Amps AC)
15
15
15
Nominal Output Voltage
(Volts DC)
0 – ±90 11
0 – ±180
2
0 – ±90
MECHANICAL SPECIFICATIONS (Inches / mm)
Maximum Output Load Current
(Amps DC)
11
11
Maximum Horsepower Rating
HP, (KW)
1, (0.75)
2, (1.5)
1, (0.75)
30
—
—
—
—
—
—
—
0
1
—
—
0
1
1
00
50
—
.5
5
KB ELECTRONICS, INC.
12095 NW 39th Street, Coral Springs, FL 33065-2516 • (954) 346-4900 • Fax (954) 346-3377
Outside Florida Call
www.kbelectronics.com
TOLL FREE (800) 221-6570 • E-mail – info@kbelectronics.com
(A42104) – Rev
. B – 8/2003