
Refrigerant
R410A
Floor Console/Under Ceiling Dual Type
INSTALLATION INSTRUCTION
SHEET
(PART NO. 9373244011)
WARNING
CAUTION
The basic installation work procedures are the same as conventional refrigerant (R22) models.
However, pay careful attention to the following points:
(1) Since the working pressure is 1.6 times higher than that of conventional refrigerant (R22) models, some of the piping and
installation and service tools are special. (See the table below.)
Especially, when replacing a conventional refrigerant (R22) model with a new refrigerant R410A model, always replace the
conventional piping and flare nuts with the R410A piping and flare nuts.
(2) Models that use refrigerant R410A have a different charging port thread diameter to prevent erroneous charging with
conventional refrigerant (R22) and for safety. Therefore, check beforehand. [The charging port thread diameter for R410A is
1/2 UNF 20 threads per inch.]
(3) Be more careful that foreign matter (oil, water, etc.) does not enter the piping than with refrigerant (R22) models. Also, when
storing the piping, securely seal the openings by pinching, taping, etc.
(4) When charging the refrigerant, take into account the slight change in the composition of the gas and liquid phases, and
always charge from the liquid phase side whose composition is stable.
Special tools for R410A
Tool name
Gauge manifold
Charge hose
Vacuum pump
Gas leakage detector
Copper pipes
It is necessary to use seamless copper pipes and it is desirable that the amount
of residual oil is less than 40 mg/10 m. Do not use copper pipes having a
collapsed, deformed or discolored portion (especially on the interior surface).
Otherwise, the expansion valve or capillary tube may become blocked with
contaminants.
As an air conditioner using R410A incurs pressure higher than when using
R22, it is necessary to choose adequate materials.
Thicknesses of copper pipes used with R410A are as shown in Table 1. Never
use copper pipes thinner than 0.8 mm (Nominal diameter is 1/4 in., 1/2 in.),
even when it is available on the market.
This mark indicates procedures which, if improperly performed, might lead to the death or serious injury of
the user.
This mark indicates procedures which, if improperly performed, might possibly result in personal harm to
the user, or damage to property.
This air conditioner uses new refrigerant HFC (R410A).
Contents of change
Pressure is high and cannot be measured with a conventional gauge. To prevent erroneous mixing of other
refrigerants, the diameter of each port has been changed.
It is recommended the gauge with seals –0.1 to 5.3 MPa (–76 cmHg to 53 kgf/cm2) for high pressure.
–0.1 to 3.8 MPa (–76 cmHg to 38 kgf/cm
To increase pressure resistance, the hose material and base size were changed.
A conventional vacuum pump can be used by installing a vacuum pump adapter.
Special gas leakage detector for HFC refrigerant R410A.
2
) for low pressure.
Table 1 Thicknesses of Annealed Copper Pipes
Thickness (mm)
Nominal
diameter (inch)
1/4
1/2
Outer diameter
(mm)
6.35
12.7
R410A [ref.] R22
0.80 0.80
0.80 0.80
STANDARD PARTS
The following installation parts are furnished. Use them as required.
INDOOR UNIT ACCESSORIES
Name and Shape
Cover plate (left)
Cover plate (right)
Tapping screw (ø4 × 10)
Installation template
Bracket (left)
Bracket (right)
Anchor bolt (M12)
Spring washer
Special nut
Wall bracket
Tapping screw (ø4 × 20)
Coupler heat insulator
(large)
Coupler heat insulator
(small)
Nylon fastener
Q’ty
1
1
2
For positioning the indoor
unit
1
For under ceiling type
For suspending the indoor
unit from ceiling
1
1
4
4
4
For suspending the indoor
unit on the wall.
2
For fixing the wall bracket.
6
For indoor side pipe joint
(Large pipe)
1
For indoor side pipe joint
(Small pipe)
1
For fixing the drain hose
1
Application
Name and Shape
Drain hose
Insulation (drain hose)
VT wire
Remote control unit
Battery (penlight)
Remote control unit holder
Tapping screw (ø3 × 12)
Q’ty
1
1
1
1
2
1
2
Application
Adhesive type 70 × 230
For fixing the drain hose
L 280 mm
Use for air conditioner
operation
For remote control unit
Use as remote control unit
holder
For remote control unit
holder installation
OUTDOOR UNIT ACCESSORIES
Name and Shape
Drain pipe
Drain cap
Q’ty
1
2
Application
For outdoor unit drain piping
work
[Heat & Cool model
(Reverse cycle) only]
OPTIONAL PARTS FOR INDOOR UNIT
Name and Shape Part No. Application
Joint pipe-A
9302812021
For indoor side pipe joint
INSTALLATION PROCEDURE
Install the room air conditioner as follows:
1
1. REMOVE THE INTAKE GRILLE
Open the intake grille and remove the three screws (Fig. 3).
Fig. 3
Tapping screw
Remark: The main unit can be wired before the indoor unit is in-
2
A. FLOOR CONSOLE TYPE
1. DRILLING FOR PIPING
Select piping and drain directions (Fig. 4).
The piping and drain can be made in three directions as shown below.
Fig. 4
The drain hose can be connected to either the left or right side (Fig. 5).
Fig. 5
When the directions are selected, drill a 10 cm (4”) dia. hole on the wall so
that the hole is tilted downward toward the outdoor for smooth water flow.
When the pipe is led out from the rear, make a hole in Fig. 6, at the position shown.
Fig. 6
PREPARING INDOOR UNIT
INSTALLATION
Machine screw
Intake grille
stalled. Select the most appropriate installation order.
Tapping screw
INDOOR UNIT INSTALLATION
Drain hose
(Left side)
Wall
100 mm (4”)
Indoor side
6 mm (1/4”)
Outdoor side
Drain hose
(Right side)
When installing set to wall install the accessory wall bracket at the position shown in Fig. 7, and mount the set to it.
Fig. 7
65.5 cm (26”)
53 cm (21”)
4.5 cm (1-3/4”)
99 cm (39”)
50 cm (20”)
6.5 cm (2-1/2”)
10 cm (4”) hole
5 cm (2”) hole
12.5 cm (5”) 10 cm (4”)
24.5 cm
(
9-5/8”
)
Wall bracket
Side of set
6.5 cm (2-1/2”)
2. INSTALLING THE DRAIN HOSE
Select whether the drain hose will be connected to the left or right side
(Fig. 5).
Insert the drain hose into the drain pan, then secure the drain hose with a
nylon fastener (Fig. 8).
Fig. 8
Drain pan
Nylon fastener
Drain hose
Wrap the insulation (drain hose) around the drain hose connection
(Fig. 9).
Fig. 9
Drain hose
Be sure to arrange the drain hose so that it is leveled lower than the drain
hose connecting port of the indoor unit.
Fig. 10
Arrange the drain
hose lower than
this portion.
Do not install the unit so that the drain hose side is too
high. Height A should be less than 5 mm (Fig. 11).
Fig. 11
Drain pan
Insulation (Drain hose)
Drain hose
CAUTION
Drain hose
B. UNDER CEILING TYPE
Using the installation template, drill holes for piping and anchor bolts (for
holes) (Fig. 12).
Fig. 12
900 mm (35-7/16”)
Drilling position
for anchor bolt
200 mm
(7-7/8” )
1. DRILLING FOR PIPING
Select piping and drain directions (Fig. 13).
Fig. 13
Install the drain hose at the rear; it should not be installed
on the top or right side.
When the directions are selected, drill 80 mm (3-1/8”) and 50 mm (2”) or
150 mm (6”) dia. hole on the wall so that the hole is tilted downward toward the outdoor for smooth water flow.
Fig. 14
Indoor side Outdoor side
2. DRILLING HOLES FOR ANCHOR BOLTS AND
INSTALLING THE ANCHOR BOLTS
With a concrete drill, drill four 12.7 mm (1/2”) dia. holes (Fig. 15).
Fig. 15
Insert the anchor bolts into the drilled holes, and drive the pins completely
into the anchor bolts with a hammer (Fig. 16).
Fig. 16
Installation
template
Drilling position
for piping
Wall
ø 12.7 mm (1/2”)
To p
CAUTION
Rear (Install the
drain hose in this
direction.)
Right
6 mm (1/4”)
60 to 70 mm
Ceiling
Wall
(2-3/8” to 2-3/4”)
3. INSTALLING BRACKETS
Install the brackets with nuts, washers and spring washers (Fig. 17).
Fig. 17
Bracket (Left)
Spring
washer
Special nut
Bracket
Bracket (Right)
4. INSTALLING INDOOR UNIT
Reset the hex bolts as shown in Fig. 18.
Fig. 18
Hex bolt
Indoor unit
Apply the indoor unit to the brackets (Fig. 19).
8 to 13 mm
(5/16” to 1/2”)
Fig. 19
Bolt
Indoor unit
Now, securely tighten the hex bolts in both sides.
Bracket
5. INSTALLING THE DRAIN HOSE
Select whether the drain hose will be connected to the left or right side
(Fig. 5).
Insert the drain hose into the drain pan, then secure the drain hose with a
nylon fastener (Fig. 8).
Wrap the insulation (drain hose) around the drain hose connection
(Fig. 9).
Be sure to arrange the drain hose so that it is leveled lower than the drain
hose connecting port of the indoor unit (Fig. 20).
Fig. 20
Arrange the drain hose
lower than this portion.
When drain hose is arranged backward.
Secure the drain hose with the VT wire (Fig. 21).
Fig. 21
VT wire
hole
Pass the drain hose
through here.
Remove the hole cover.
Drain hose
OK NO
Piping hole
Base (Bottom)
Intake grille
Cut the grille
Drain hose
VT wire
For authorized service personnel only.
WARNING
(1) For the room air conditioner to operate satisfactorily, install it as outlined in this installation instruction sheet.
(2) Connect the indoor unit and outdoor unit with the room air conditioner piping and cords available standards parts. This
installation instruction sheet describes the correct connections using the installation set available from our standard parts.
(3) Installation work must be performed in accordance with national wiring standards by authorized personnel only.
(4) If refrigerant leaks while work is being carried out, ventilate the area. If the refrigerant comes in contact with a flame, it
produces a toxic gas.
(5) Do not use an extension cord.
(6) Do not turn on the power until all installation work is complete.
••
• Be careful not to scratch the room air conditioner when handling it.
••
••
• After installation, explain correct operation to the customer, using the operating manual.
••
••
• Let the customer keep this installation instruction sheet because it is used when the air conditioner is serviced or moved.
••
SELECTING THE MOUNTING POSITION
WARNING
Install at a place that can withstand the weight of the indoor and outdoor units and install positively so that the units will not
topple or fall.
CAUTION
(1) Do not install where there is the danger of combustible gas leakage.
(2) Do not install near heat sources.
(3) If children under 10 years old may approach the unit, take preventive measures so that they cannot reach the unit.
Decide the mounting position with the customer as follows:
1. INDOOR UNIT
(1) Install the indoor unit level on a strong wall, floor, ceiling which is not sub-
ject to vibration.
(2) The inlet and outlet ports should not be obstructed : the air should be able
to blow all over the room.
(3) Install the unit near an electric outlet or special branch circuit.
(4) Do not install the unit where it will be exposed to direct sunlight.
(5) Install the unit where connection to the outdoor unit is easy.
(6) Install the unit where the drain pipe can be easily installed.
(7) Take servicing, etc. into consideration and leave the spaces shown in
Fig. 1. Also install the unit where the filter can be removed.
Fig. 1
••
• Floor console
••
Left
30 cm (12”) or more 30 cm (12”) or more
••
• Under ceiling
••
Left
15 cm (6”) or more 30 cm (12”) or more
Ceiling
Indoor unit
Ceiling
Right
Right
12.7 mm (1/2”) dia.
6.35 mm (1/4”) dia.
Outdoor unit
Indoor unit
2. OUTDOOR UNIT
WARNING
(1) Install the unit where it will not be tilted by more than 5˚.
(2) When installing the outdoor unit where it may exposed to strong wind, fasten it securely.
(1) If possible, do not install the unit where it will exposed to direct sunlight. (If necessary, install a blind that does not interfere with the air flow.)
(2) Install the outdoor unit in a place where it will be free from being dirty or getting wet by rain as much as possible.
(3) Install the unit when connection to the indoor unit is easy.
(4) During heating operation, drain water flows from the outdoor unit. Therefore, install the outdoor unit in a place where the drain water flow will not be
obstructed. (Reverse cycle model only)
(5) Do not place animals and plants in the path of the warm air.
(6) Take the air conditioner weight into account and select a place where noise and vibration are small.
(7) Select a place so that the warm air and noise from the air conditioner do not disturb neighbors.
(8) Provide the space shown in Fig. 2 so that the air flow is not blocked. Also for efficient operation, leave open three of the four directions front, rear, and both
sides.
Fig. 2
10 cm (4”)
or over
10 cm (4”)
or over
60 cm (2’)
or over
60 cm (2’)
or over
60 cm (2’)
or over
Indoor unit
CONNECTION PIPE REQUIREMENT
Table 2
Diameter
Small Large
6.35 mm (1/4 in.) 12.7 mm (1/2 in.) 15 m (49 ft) 8 m (26 ft)
••
• Use pipe with water-resistant heat insulation.
••
Maximum
length
CAUTION
Install heat insulation around both the gas and liquid pipes.
Failure to do so may cause water leaks.
Use heat insulation with heat resistance above
120 °C. (Reverse cycle model only)
In addition, if the humidity level at the installation location
of the refrigerant piping is expected to exceed 70%, install
heat insulation around the refrigerant piping. If the expected humidity level is 70-80%, use heat insulation that
is 15 mm or thicker and if the expected humidity exceeds
80%, use heat insulation that is 20 mm or thicker.
If heat insulation is used that is not as thick as specified,
condensation may form on the surface of the insulation.
In addition, use heat insulation with heat conductivity of
0.045 W/(m·K) or less (at 20 °C).
Maximum Height
(between indoor
and outdoor)
12.7 mm (1/2”) dia.
6.35 mm (1/4”) dia.
Outdoor unit
3
OUTDOOR UNIT INSTALLATION
1. OUTDOOR UNIT PROCESSING
WARNING
(1) Install the unit where it will not be tilted by more than 5˚.
(2) When installing the outdoor unit where it may exposed
to strong wind, fasten it securely.
• Set the unit on a strong stand, such as one made of concrete blocks to
minimize shock and vibration.
• Do not set the unit directly on the ground because it will cause trouble.
• Since the drain water flows out of the outdoor unit during heating op-
eration, install the drain pipe and connect it to an commercial 16 mm
hose. (Heat & Cool model (Reverse cycle) only)
• When installing the drain pipe, plug all the holes (• hole at one place)
other than the drain pipe mounting hole in the bottom of the outdoor
unit with putty so there is no water leakage. (Fig. 22) (Heat & Cool model
(Reverse cycle) only)
CAUTION
Installation in cold regions. Do not use the accessory drain
pipe and drain cap.
(If the drain pipe and drain cap are used, the drain water in
the pipe may freeze in extremely cold weather.)
Fig. 22
Hole
Drain cap
Hole
Drain cap
Bottom of outdoor unit
Drain pipe hole
Drain pipe
Drain hose
(commercial hose,
inside diameter 16 mm)
Bottom plate
Drain pipe
2. OUTDOOR UNIT CONNECTION CORD AND
PIPE CONNECTION PREPARATIONS
Remove outdoor unit terminal cover.
Fig. 23
* After removing the screws,
remove terminal cover.
Terminal cover
4
CONNECTING THE PIPING
WARNING
Do not use the existing (for R22) piping and flare nuts.
• If the existing materials are used, the pressure inside the
refrigerant cycle will rise and cause breakage, injury, etc.
(Use the special R410A materials.)
CAUTION
(1) Do not use mineral oil on flared part.
Prevent mineral oil from getting into the system as this
would reduce the lifetime of the units.
(2) Never use piping which has been used for previous
installations. Only use parts which are delivered with
the unit.
(3) While welding the pipes, be sure to blow dry nitrogen
gas through them.
CAUTION
The maximum lengths of this product are shown in table 3.
If the units are further apart than this, correct operation
can not be guaranteed.
1. LIMITATION OF REFRIGERANT PIPING LENGTH
Table 3
Max length (L)
Max height difference (H)
Fig. 24
Outdoor unit
20 m (66 ft)
8 m (20 ft)
Indoor unit
L
L
2. FLARING PROCESSING
(1) Cut the connection pipe to the necessary length with a pipe cutter.
(2) Hold the pipe downward so that cuttings will not enter the pipe and
remove the burrs.
(3) Insert the flare nut (always use the flare nut attached to the indoor
and outdoor units respectively) onto the pipe and perform the flare
processing with a flare tool.
Use the special R410A flare tool, or the conventional (for R22) flare
tool.
When using the conventional flare tool, always use an allowance adjustment gauge and secure the A dimension shown in table 4.
Fig. 25
L
Check if [L] is flared uniformly
and is not cracked or scratched.
Die
A
Pipe
(2) Install the outdoor unit wall cap (supplied with the optional installation
set or procured at the site) to the wall hole pipe.
(3) Connect the outdoor unit and indoor unit piping.
(4) After matching the center of the flare surface and tightening the nut
hand tight, tighten the nut to the specified tightening torque with a
torque wrench.
Fig. 27
Tighten with two wrenches.
Wrench (fixed)
Flare nut
Torque wrench
Indoor unit
pipe
Connection pipe
To prevent gas leakage,
coat the flare surface with
alkylbenzene oil (HAB).
Do not use mineral oil.
Table 5 Flare nut tightening torque
Table 4 Pipe outside diameter
Pipe outside
diameter
6.35 mm (1/4 in.)
12.7mm (1/2 in.)
Flare tool for
R410A, clutch type
0 to 0.5
0 to 0.5
A (mm)
Conventional (R22) flare tool
Clutch type Wing nut type
1.0 to 1.5 1.5 to 2.0
1.0 to 1.5 2.0 to 2.5
3. BENDING PIPES
(1) When bending the pipe, be careful not to crush it.
(2) To prevent crushing of the pipe, do not bend the pipe at a radius cur-
vature of 100 mm or over.
(3) If the copper pipe is bend the pipe or pulled to often, it will become
stiff. Do not bend the pipes more than three times at one place.
Flare nut
6.35 mm (1/4 in.) dia.
12.7 mm (1/2 in.) dia.
Do not remove the cap from the connection pipe before connecting
the pipe.
Tightening torque
14 to 18 N · m (140 to 180 kgf · cm)
50 to 62 N · m (500 to 620 kgf · cm)
CAUTION
Be sure to connect the large pipe after connecting the small
pipe completely.
5. HEAT INSULATION ON THE PIPE JOINTS
4. CONNECTION PIPES
(1) Centering the pipe against port on the indoor unit, turn the flare nut
with your hand (Fig. 26).
Be sure that the small pipe is completely installed before connecting
the large the pipe.
Fig. 26
Indoor unit side
H
Optional parts
H
CAUTION
Be sure to apply the pipe against the port on the indoor
unit correctly. If the centering is improper, the flare nut
cannot be tightened smoothly. If the flare nut is forced to
turn, the threads will be damaged.
(INDOOR SIDE ONLY)
Put coupler heat insulator on the joints (indoor side only) (Fig. 28).
Fig. 28
No gap
Coupler heat
insulator
(large)
Indoor unit
Coupler heat
insulator (small)
Be sure to overlap
the insulation
Large pipe Small pipe
No gap
Coupler heat
insulation
- Continued on back -
2 cm (3/4”) or more
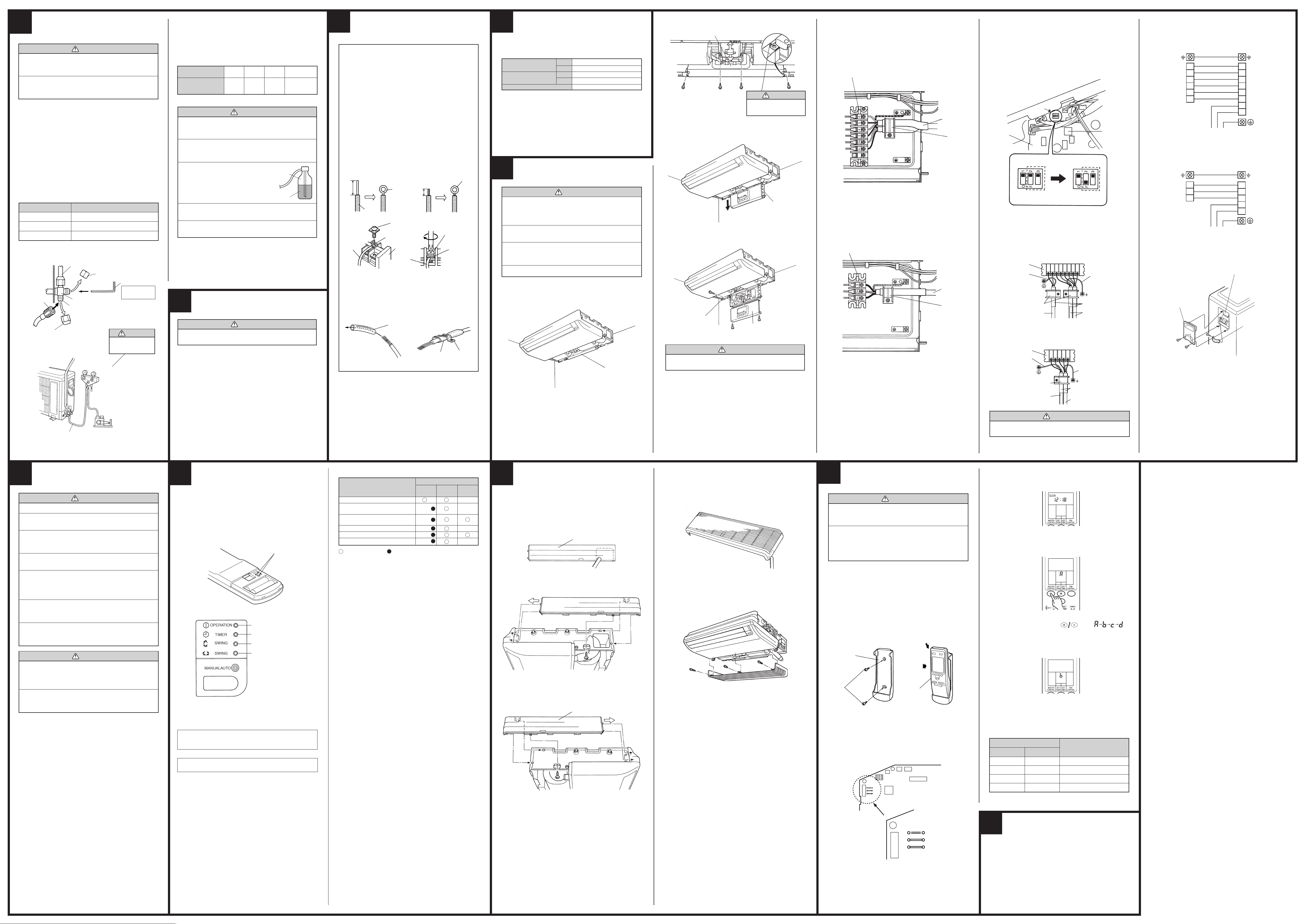
5
VACUUMING AND
ADDITIONAL CHARGE
CAUTION
(1) Do not purge the air with refrigerants but use a vacuum
pump to vacuum the installation! There is no extra refrigerant in the outdoor unit for air purging!
(2) Use a vacuum pump for R410A exclusively. Using the
same vacuum pump for different refrigerants may damage the vacuum pump or the unit.
1. VACUUM
(1) Remove the cap, and connect the gauge manifold and the vacuum
pump to the charging valve by the service hoses.
(2) Vacuum the indoor unit and the connecting pipes until the pressure
gauge indicates –0.1 MPa (–76 cmHg).
(3) When –0.1 MPa (–76 cmHg) is reached, operate the vacuum pump
for at least 15 minutes.
(4) Disconnect the service hoses and fit the cap to the charging valve to
the specified torque.
(5) Remove the blank caps, and fully open the spindles of the 2-way and
3-way valves with a hexagon wrench (Torque : 6 to 7 N · m (60 to 70
kgf · cm).
(6) Tighten the blank caps of the 2-way valve and 3-way valve to the
specified torque.
Table 6
Tightening torque
Blank cap (2-way valve)
Blank cap (3-way valve)
Charging port cap
Fig. 29
Outdoor unit
Service hose
with valve core
Cap
20 to 25 N · m (200 to 250 kgf · cm)
25 to 30 N · m (250 to 300 kgf · cm)
10 to 12 N · m (100 to 120 kgf · cm)
Connecting pipe
Blank cap
3-way valve
Charging port
Use a clean gauge manifold and charging hose
for R410A exclusively.
Gauge manifold
t
Hexagon wrench
Use a 4 mm
hexagon wrench.
CAUTION
2. ADDITIONAL CHARGE
Refrigerant suitable for a piping length of 7.5 m is charged in the outdoor
unit at the factory.
When the piping is longer than 7.5 m, additional charging is necessary.
For the additional amount, see the table below.
Table 7
Pipe length
Additional
refrigerant
7.5 m
(25 ft)
None
(1) When moving and installing the air conditioner, do not
mix gas other than the specified refrigerant (R410A)
inside the refrigerant cycle.
(2) When charging the refrigerant R410A, always use an
electronic balance for refrigerant charging (to measure the refrigerant by weight).
(3) When charging the refrigerant, take
into account the slight change in
the composition of the gas and liquid phases, and always charge from
the liquid phase side whose composition is stable.
(4) Add refrigerant from the charging valve after the com-
pletion of the work.
(5) If the units are further apart than the maximum pipe
length, correct operation can not be guaranteed.
6
GAS LEAKAGE INSPECTION
After connecting the piping, check the joints for gas leakage with gas leak detector.
10 m
(33 ft)
37.5 g
(1.3 oz)
CAUTION
CAUTION
15 m
(49 ft)
112.5 g
(4.0 oz)
15 g/1 m
(0.53 oz/3.3 ft)
Gas
R410A
Liquid
7
HOW TO CONNECT WIRING
TO THE TERMINALS
A. For solid core wiring (or F-cable)
(1) Cut the wire end with a wire cutter or wire-cutting pliers, then strip
the insulation to about 25 mm (15/16”) of expose the solid wire.
(2) Using a screwdriver, remove the terminal screw(s) on the terminal
board.
(3) Using pliers, bend the solid wire to form a loop suitable for the
terminal screw.
(4) Shape the loop wire properly, place it on the terminal board and
tighten securely with the terminal screw using a screwdriver.
B. For strand wiring
(1) Cut the wire end with a wire cutter or wire-cutting pliers, then strip
the insulation to about 10 mm (3/8”) of expose the strand wiring.
(2) Using a screwdriver, remove the terminal screw(s) on the terminal
board.
(3) Using a round terminal fastener or pliers, securely clamp a round
terminal to each stripped wire end.
(4) Position the round terminal wire, and replace and tighten the ter-
minal screw using a screwdriver.
Fig. 30
A. Solid wire
Loop
Insulation
Strip 25 mm (15/16”)
Screw with
special washer
Round terminal
Wire
Terminal
board
Wire
HOW TO FIXED CONNECTION CORD AND
POWER CABLE AT THE CORD CLAMP
After passing the connection cord and power cable through the insulation tube, fasten it with the cord clamp.
Fig. 31
Insulation tube
Use VW-1, 0.5 to 1.0 mm thick, PVC tube as the insulation tube.
B. Strand wire
Strip 10 mm (3/8”)
Screw with
special washer
Round
terminal
Insulation tube Cord clamp
Round
terminal
8
ELECTRICAL REQUIREMENT
••
• Electric wire size and fuse capacity:
••
Table 8
Power supply cord (mm2)
Connection cord (mm2)
Fuse capacity (A)
••
• Install the disconnect device with a contact gap of at least 3 mm nearby
••
the units. (Both indoor unit and outdoor unit)
••
• Always make the air conditioner power supply a special branch circuit
••
and provide a special breaker.
••
• Always use H07RN-F or equivalent as the power supply cord and the
••
connection cord.
9
ELECTRICAL WIRING
MAX.
MIN.
MAX.
MIN.
3.0
2.0
2.5
1.5
15
CAUTION
(1) Match the terminal block numbers and connection cord
colors with those of the outdoor unit.
Erroneous wiring may cause burning of the electric
parts.
(2) Connect the connection cords firmly to the terminal
block. Imperfect installation may cause a fire.
(3) Always fasten the outside covering of the connection
cord with the cord clamp. (If the insulator is chafed,
electric leakage may occur.)
(4) Always connect the ground wire.
1. INDOOR UNIT SIDE
(1) Remove the electric component box.
Fig. 32
Electric component box
Fig. 33
Electric component box
Remove the four
tapping screws.
Do not remove the screws. If the
stays are removed, the electric
component box will fall.
CAUTION
(2) Pull out the electric component box.
Fig. 34
Electric component box
(3) Remove the electric component box cover.
Fig. 35
Base
Electric component box cover
Remove the three tapping screws.
CAUTION
Be careful not to pinch the lead wires between the electric
component box and base.
(4) Wiring
[Heat & Cool model (Reverse cycle)]
1 Remove the cord clamp.
2 Process the end of the connection cords to the dimensions shown in
Fig. 36.
3 Connect the end of the connection cord fully into the terminal block.
Fig. 36
Terminal block
Connection
cord
Cord clamp
4 Fasten the connection cord with a cord clamp.
5 Fasten the end of the connection cord with the screw.
[Cooling model]
1 Remove the cord clamp.
2 Process the end of the connection cords to the dimensions shown in
Fig. 37.
3 Connect the end of the connection cord fully into the terminal block.
Fig. 37
Terminal block
Connection
cord
Cord clamp
4 Fasten the connection cord with a cord clamp.
5 Fasten the end of the connection cord with the screw.
(5) Floor console/Under ceiling select switch
1 The electrical circuits for this were set for use as a ceiling type at the
factory.
2 The following changes must be made to the settings if the unit is to be
used as a floor type.
3 Changing the settings for the electrical circuits.
Switch 1 (SW1) on the printed circuit board inside the electric component box must be set as follows.
Fig. 38
SW1
Printed circuit
board
SW1 SW1
Under ceiling type Floor console type
Microcomputer
2. OUTDOOR UNIT SIDE
Fig. 39
[Heat & Cool model (Reverse cycle)]
NL1
(L)2(N)
NL1
(L)2(N)
3456
Ground wire length
65 mm or over
Control box
Insulation tube
Connection cord
3
Control box
Ground wire length
65 mm or over
Terminal block
Ground wire length
45 mm or over
Cord clamp
Power supply cord
[Cooling model]
Terminal block
Ground wire length
80 mm or over
Fig. 40
Heat & Cool model
(Reverse cycle)
Connection cord
Green/Yellow
6
5
4
3
2
(N)
1
(L)
Indoor unit
side terminal
Power supply
6
5
4
3
2
(N)
1
(L)
N
L
Outdoor unit
side terminal
Cooling model
Connection cord
Green/Yellow
3
2(N)
1(L)
Indoor unit
side terminal
Power supply Outdoor unit
3
2(N)
1(L)
N
L
side terminal
3. INSTALL THE TERMINAL COVER
Fig. 41
Terminal cover
Terminal block
Cord clamp
Vacuum pump
Service hose
10
POWER
WARNING
(1) The rated voltage of this product is 230V A.C. 50Hz.
(2) Before turning on the verify that the voltage is within
the 198V to 264V range.
(3) Always use a special branch circuit and install a spe-
cial receptacle to supply power to the room air conditioner.
(4) Use a circuit breaker and receptacle matched to the
capacity of the room air conditioner.
(5) The circuit breaker is installed in the permanent wir-
ing. Always use a circuit that can trip all the poles of
the wiring and has an isolation distance of at least
3 mm between the contacts of each pole.
(6) Perform wiring work in accordance with standards so
that the room air conditioner can be operated safely
and positively.
(7) Install a leakage circuit breaker in accordance with the
related laws and regulations and electric company
standards.
CAUTION
(1) The power source capacity must be the sum of the room
air conditioner current and the current of other electrical appliances. When the current contracted capacity
is insufficient, change the contracted capacity.
(2) When the voltage is low and the air conditioner is diffi-
cult to start, contact the power company the voltage
raised.
11
• Perform test operation and check items 1 and 2 below.
• For the operation method, refer to the operating manual.
• The outdoor unit may not run, depending on the room temperature.
In this case, the ‘TEST RUN’ signal is received during air conditioner
operation (use a metallic object to short the two metal contacts under
the battery compartment lid and send the ‘TEST RUN’ signal from the
remote control unit).
TEST RUNNING
Fig. 42
Short the two metal contacts under
the battery compartment lid.
OPERATION lamp (Red)
TIMER lamp (Green)
SWING lamp (Orange)
SWING lamp (Orange)
Operation can be checked by lighting and flashing of the display section
OPERATION and TIMER lamps.
Perform judgment in accordance with the following.
• Test running
When the air conditioner is run by pressing the remote control unit
test run button, the OPERATION and TIMER lamps flash slowly at
the same time.
• Error
The OPERATION, TIMER and SWING lamps operate as follows (Table 9) according to the error contents.
Table 9
(RED)
2 times
2 times
3 times
3 times
6 times
Error display
TIMER SWING
(GREEN)
(ORANGE)
—
—
—
—
Error contents
Indoor unit circuit board error
Indoor unit room temperature sensor
opened
Indoor unit room temperature sensor
short circuited
Indoor unit piping sensor opened
Indoor unit piping sensor short circuited
Indoor unit fan error
: Fast flashing : Slow flashing — : Off
OPERATION
CHECK ITEMS
(1) INDOOR UNIT
(1) Is operation of each button on the remote control unit normal?
(2) Does each lamp light normally?
(3) Do not air flow direction louvers operate normally?
(4) Is the drain normal?
(5) Is there any abnormal noise and vibration during operation?
(2) OUTDOOR UNIT
(1) Is there any abnormal noise and vibration during operation?
(2) Will noise, wind, or drain water from the unit disturb the neighbors?
(3) Is there any gas leakage?
• Do not operate the air conditioner in the test running state for a long
time.
• For the operation method, refer to the operating manual and perform
operation check.
12
MOUNT THE COVER PLATE
AND THE INTAKE GRILLE
1. MOUNT THE COVER PLATE (RIGHT)
(1) Cut a pipe exit hole in the right plate. This is only when the pipe exits
from the right side. (This operation is not required when the protrusion is on the top or rear.)
Fig. 43
Cover plate (Right)
(2) Join the cover plates (right) and mount with screws (Fig. 44).
Fig. 44
2. MOUNT THE COVER PLATE (LEFT)
(1) Join the cover plates (left) and mount with screws.
Fig. 45
Cover plate (Left)
3. MOUNT THE INTAKE GRILLE
(1) Cut the right side of the intake grille. This is only when the pipe exits
from the right side (Fig. 46).
Fig. 46
(2) Insert the hinges on the bottom of the intake grille into the holes in the
base assembly. Then mount the arms to the three areas on the top of
the intake grille (Fig. 47).
Fig. 47
13
REMOTE CONTROL UNIT
INSTALLATION
CAUTION
(1) Check that the indoor unit correctly receives the sig-
nal from the remote control unit, then install the remote
control unit holder.
(2) Select the remote control unit holder selection site by
paying careful attention to the following:
Avoid places in direct sunlight.
Select a place that will not be affected by the heat from
a stove, etc.
1. REMOTE CONTROL UNIT HOLDER
INSTALLATION
• Install the remote control unit with a distance of 7 m between the re-
mote control unit and the photocell as the criteria. However, when installing the remote control unit, check that it operates positively.
• Install the remote control unit holder to a wall, pillar, etc. with the tap-
ping screw (Fig. 48).
Fig. 48
Remote Control Unit
holder fixing
Remote control
unit holder
Tapping
screw
(small)
1 Set
2 Push
Remote
control unit
2. SWITCHING REMOTE CONTROL UNIT SIGNAL
CODES
• Air conditioner settings
Fig. 49
Indoor unit
Printed circuit board
Remote Control
Unit mounting
Cord clamp
Power supply cord
Insulation tube
Connection cord
CAUTION
When routing the ground wires, leave slack as shown in
the illustrations.
• Remote control unit settings
(1) Press the START/STOP button and display only the clock.
Fig. 50
(2) Press the MASTER CONTROL button continuously for more than five
seconds to display the current signal code.
Fig. 51
(3) Change the signal code with the button ( ).
Fig. 52
(4) Press the MASTER CONTROL button again to return to the clock
display and change the signal code.
• Confirm the setting of the remote control unit signal code and the printed
circuit board setting.
If these are not confirmed, the remote control unit cannot be used to
operate for the air conditioner.
Table 10
Jumper wire
JM2
Connect
Connect
Disconnect
Disconnect
JM3
Connect
Disconnect
Connect
Disconnect
Remote control unit
signal code
A (Primary setting)
B
C
D
JM1 (A)
JM2 (R1)
JM3 (R2)
14
Explain the following to the customer in accordance with the operating
manual:
(1) Starting and stopping method, operation switching, temperature ad-
justment, timer, air flow switching, and other remote control unit op-
erations.
(2) Air filter removal and cleaning, and how to use the air louvers.
(3) Give the operating and installation manuals to the customer.
(4) If the signal code is changed, explain to the customer how it changed
(the system returns to signal code A when the batteries in the remote
control unit are replaced).
CUSTOMER GUIDANCE
PART NO. 9373244011