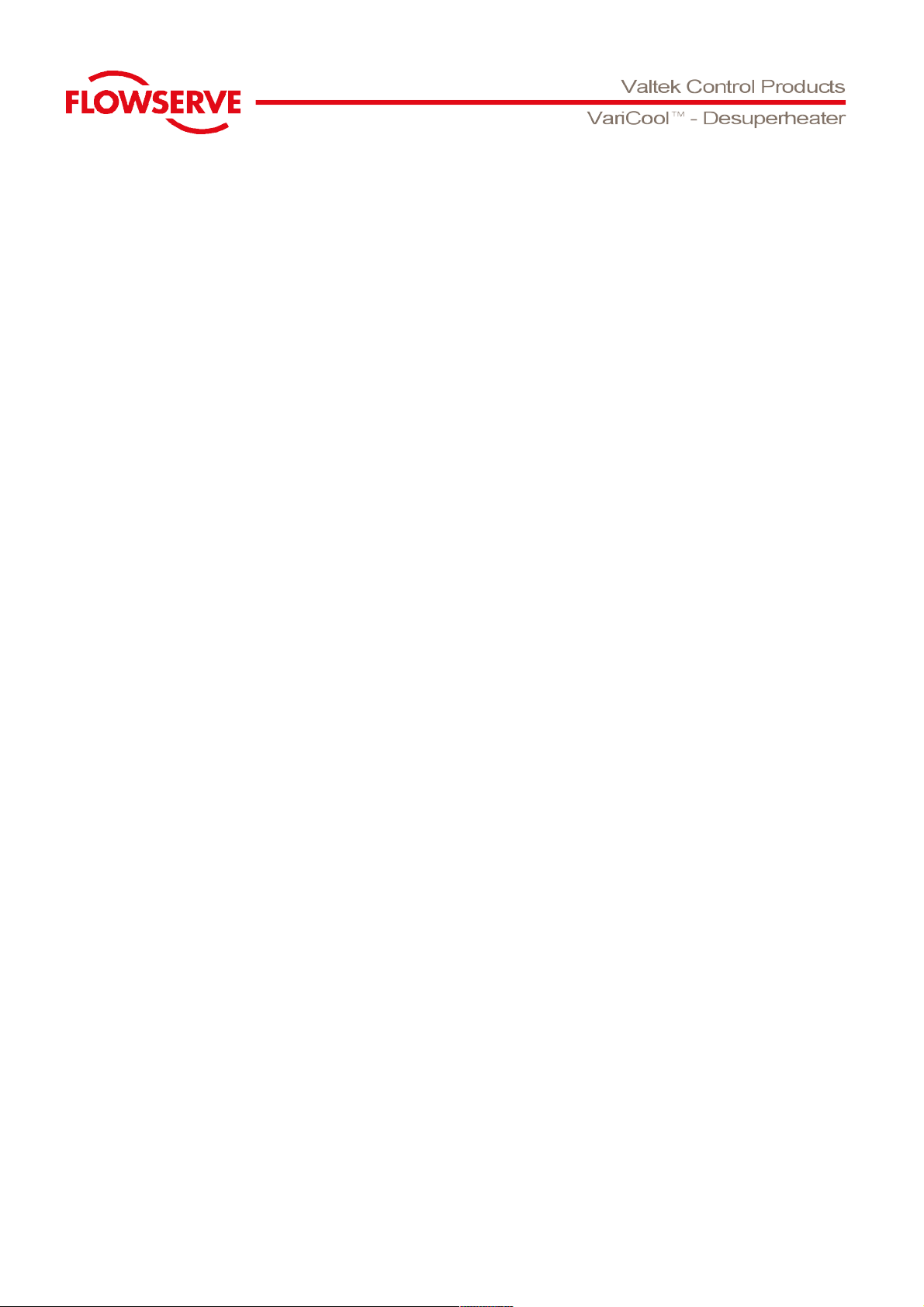
1
1.1
1.2
1.3
1.4
1.5
1.6
1.7
2
3
4
5
6
6.1
6.2
6.3
6.4
6.5
6.6
6.7
7
Operating instructions
Installation
Delivery status
Installation recommendation
Physical requirements
System requirements
Preparation for installation in the pipeline
Installation of the SCHMIDT valve
Commissioning
Maintenance
Trouble shooting
Repair
Assembly
Cleaning
Lubrication
Assembly component „Nozzle Body“
Assembly component „Plug“
Assembly component „Packing“
Assembly „VariCool“
Assembly „Finish“
Parts list
3
3
3
3
4
4
5
5
6
6
7 + 8
9
9
9
9
10
11
12
13
14
15

Application
Injection control valve for direct steam cooling applications. In combination with a SCHMIDT
multispring or central spring pneumatic actuator, optionally also with an electrical linear or rotary
actuator, can be controlled. Suitable for a wide range of applications due to simple design and
adaptability to different processes.
1 VARICOOL operating instructions
1.1 Installation
The device may only be assembled and put into service by qualified personnel. Qualified
personnel are persons who are familiar with the assembly, commissioning and operation of
this product and have the respective qualifications to perform these activities.
1.2 Delivery status
The SCHMIDT injection nozzle valves are delivered with assembled and calibrated
actuators. They are provided with a protective coating, any shiny parts are greased and the
body openings are provided with blanking plugs. The greatest care must be taken against
knocks or sudden movements during loading and transport, as the lifting appliances must
be attached without pressure on the stem and the position indicator by means of a rope
sling below the actuator mounting flange. Any damage of the corrosion protection during
transport must be remedied immediately. At the construction site, the injection nozzle valves
must be protected against the effects of weather, grime and other damaging influences by
being placed on a firm base in a closed room until required for installation. The blanking
plugs attached for protection of the flange and interior of the control valve may only be
removed at the installation site.
1.3 Installation recommendation
The successful employment of the injection nozzle valve depends directly on a suitable
design of the converting station. As the function of the converting station depends greatly on
the consideration of the physical possibilities, it is recommended to observe the stated
standard values. Deviations may lead to considerable fluctuations in the control loop for
which the nozzle valve manufacturer rejects any liability whatsoever. In borderline cases, an
expensive conversion of the steam converting station should be expected. Even though the
complex physical processes may in individual cases justify a deviation from the standard
values, this requires, however comprehensive system knowledge and the express approval
of the manufacturer.

1.4 Physical requirements
• For an optimal operation, the steam speed should be 10 to 100 m/s / 30 to 300 ft/s
6
• To avoid condensate the set temperature should be 5 to 10 °C / 41 to 50 °F
above the saturated steam temperature.
• Max. operating temperature 530 °C / 986 °F
• Recommended cooling media temperature 120 °C / 248 °F
• Cooling media pressure 5 to 10 bar / 76 to 145 psi (see nozzle table) up to
max. 90 bar / 1300 psi above steam pressure.
• We recommend the installation of a strainer into the cooling media pipe
(mesh size 0,1mm / 0.004 inch)
• Minimum steam pipe diameter 150 mm / 6 inch
• Recommended straight pipe after injection nozzle valve: 0,1 x steam speed
min. 4 to 6 m / 13 to 20 ft
• The distance of the temperature sensor should be 0,2 x steam speed or min. 9 m / 30 ft
• The position of the temperature sensor is important for the measuring quality
Pay attention to the mounting instruction of the sensor supplier
1.5 System requirements
• System drawing with design recommendation Experience shows that deviations result in
considerable problems. A stratification of temperature zones is a frequent phenomenon
in large steam piping networks. We recommend the installation of 2 to 3 temperature
sensors with average value calculation.

Ensure that the central nozzle and the atomisation cone correspond to the axis of the
piping. The cooling medium must always be injected in the direction of flow of the medium !
1.6 Preparation for installation in the pipeline
The sealing and functional check as well as the quality assurance checks carried out in the
factory ensure the version of the control valve fully corresponds with the version specified in
the supply contract. The model number and data required for operating the valve and drive
are noted on the nameplate. The achievable stroke can be read on the driving starting
pillar/yoke.
Before the installation, the pipelines must be carefully cleaned.
1.7 Installation of the SCHMIDT valve
Checklist:
• Does the name plate agree with the operating data of the system?
Non-agreement can lead to considerable damage of the injection nozzle valves, for
which the manufacturer accepts no liability !
• Is sufficient space available at the installation location for problem-free installation and
removal?
• Have the pipelines been cleaned before the installation?
Carefully remove any foreign bodies !
• Has the control valve been depreserved and cleaned before installation?
• Does the direction arrow attached to the body agree with the direction of flow?
• Do any unallowed voltages occur during installation and operation of the control valve?
Perpendicularity of the flange required !
• Does the spacing of the pipe ends correspond to the overall valve length?
If the aforementioned points are fulfilled, the control valve can be inserted in the pipeline
and screwed together with the connecting material ( seals, screws, nuts - provided by the
builder). Afterwards, the piping of the drive with the plant air in pneumatic actuators or the
wiring of the electrical actuators can be carried out according to the electrical block diagram
located in the removable drive hood or in the drive manufacturer documentation.

2 Commissioning
Increase the load on the operational parameters gradually and continuously.
Do not suddenly subject the control valve to full operational pressure and operational
temperature !
After the initial load ( trial run ), while the system is in a pressure-free and cool state:
tighten up the screw connections of the sealing components evenly across the diagonal.
Do not damage the high-quality stem surface !
It is forbidden to work between the pillar / yoke during operation because of the risk
of injury !
3 Maintenance
Clean the valve spindle with a soft cloth.
Do not damage the high-quality
spindle surface !
Depending on the amount of grime.
The spindle surface must always
retain its metallic shine !
Tighten up the valve spindle seal if any
leakages occur.
If any defects or faults occur, contact the manufacturer, his authorized repairers, customer
service or, in special cases, with the express permission of the manufacturer, the operating
company. Any repair activities on the part of third parties invalidate the warranty of the
manufacturer.
Service hotline:
0043 (0) 664 3418616

• no aux. energy supply (
pneumatic air or electrical power
) to actuator and accessories (
solenoid valve, filter reducing
station, positioner, limit switch
and special accessories )
• the fitted accessories do not
work
• the pneumatic actuator is
defective
• the electrical actuator is
defective
• excessive tightening of the
stuffing box packing
• Valve trim worn, stuck
• pneumatic actuators: check supply
line for leaks; check pressure (
usually 6 bar )
• electrical actuators: check power
supply (connections, circuit breakers,
voltage)
• see maintenance and operating
instructions of accessories
manufacturer
• contact customer service
departement or contract partner
• see maintenance and operating
instructions of actuator manufacturer
• loosen stuffing box packing nuts until
valve operates properly
Caution: make sure there are no leaks !
• contact customer service
departement or contract partner
• dirty spindle
• damaged spindle
• actuator not powerful enough
•
clean spindle with suitable cleaning
agent
• contact customer service department
or a contract partner
• compare actuator specs on the
rating plate with operation
specifications of the facility - if
incompatible, contact customer
service department or contract
partner
Spindle travel less than full
stroke
( 0 to 100% stroke )
• air supply pressure too low
• pneumatic actuators: bad hand
wheel position (hand wheel
emergency operation)
• electrical actuators: limit switch
misadjusted
• badly adjusted or defective
positioner
• foreign particles in valve seat,
damaged trim
• provide air at the pressure stated on
the rating plate
• take hand wheel to limit position
• readjust limit switch to actuator manu
facturer`s specifications
• readjust positioner to positioner
manu facturer`s specifications
• contact customer services
department or contract partner

Excessive valve seat leakage
• damaged sealing edges at
valve seat or plug
• foreign particles in seat area
• plug does not close fully
• contact customer services
department or contract partner
• contact customer services
department or contract partner
• refer to 3.1 to 3.5
Leaking stuffing box system
• compression force on packing
too low
• worn packing
• dirty spindle
• damaged spindle
• slightly re-tighten stuffing box packing
Caution: make sure the valve spindles
can still move !
• slightly re-tighten stuffing box packing
Caution: make sure the valve spindles
can still move !
• if the packing does not stop leaking,
contact customer service department
or contract partner
• clean spindle with suitable cleaning
agent
• contact customer services
department or contract partner
• pressing force on seal(s) too
low
• seal(s) defective
• properly re-tighten top or lid nuts
crosswise
• contact customer services
department or contract partner
• medium or flow related damage
• contact customer service department
or contract partner
• power supply to limit switch
interrupted
• limit switch misadjusted
• check power supply
( voltage, circuit
breakers, connections )
• readjust limit switch; operating
distance see limit switch data sheet
• see maintenance and operating in
structions of positioner manufacturer
If the problem is not solved by taking the above measures, contact the customer services
department or contract partner.

5. Repair
If a fault or defect occurs which, according to the list of measures before, requires the customer
services departement or contract partner to be contacted, the manufacturer`s guarantee shall
be rendered null and void - and the manufacturer released from any responsibility - unless the
customer services department or contract partner is duly notified.
Service hotline Austria:
+43 (0)664 341 8 616
6. Assembly
These procedure assumes that the Injection Nozzle Valve is completely disassembled. If it is
not, start the instructions at the appropriate step.
6.1 Cleaning
Carefully clean all valve parts before beginning assembly!
6.2 Lubrication
Lightly grease all guide pieces
For lubricant to be used, see table 1
LUBRICANT
Klüber Wolfracoat C – Item no.: 089032
Lightly grease all screw threads
For lubricant to be used, see table 2
LUBRICANT
Klüber Wolfracoat C – Item no.: 089032

6.3 Assembly component “Nozzle body”
• Fixation of the nozzle body (4.4)
• Insert the rotary disk (4.6) and profile
ring (4.7) into the nozzle body (4.4)
and then screw in the nozzle (4.5)
• Place the profile ring (1.2) on the
nozzle body (4.4)

6.4 Assembly component “Plug”
• Fixation of the plug (2.2)
• Screw the stem (2.4) into the plug (2.2)
• Drill both plug (2.2) and stem (2.4)
together
• Press the spring pin (2.3) into the
drilled hole
After pressing in the dowel pin, the plug
and stem must be aligned to one another !
• Insert the fuse carrier (2.14) in the plug
(2.2)
• Put the piston sleeve (2,13) onto the
plug (2.2)
• Screw the lock nut (2.25) onto the plug
(2.2) (for tightening torques, see page
9)
• The lock nut (2.25) must be secured by
welding spots against automatic
loosening !

6.5 Assembly component “Packing”
• Insert the guide sleeve (3.2) in the
body (1.1)
• Insert the packing (3.3) on the guide
bush (3.2)
• Screw the stud bolts (3.5) into the body
(1.1)
• Place the packing box (3.4) on the
packing (3.3)
• Place the disk (3.8) on the packing box
(3.4)
• Screw the hexagonal nuts softly (3.6)
onto the stud bolts (3.5)

• Insert the plug (2.2) in the nozzle body
(4.4)
• Place the LR nut (1.6) onto the nozzle
body (4.4)
• Fixation of the body (1.1)
• Insert the stem (2.4) in the body (1.1)
• Connect the body (1.1) and nozzle
body (4.4) with one another by turning
the LR nut (1.6) (for tightening torques,
see .....)
After assembly, the LR nut (1.6) must be
secured by welding spots against
automatic loosening !
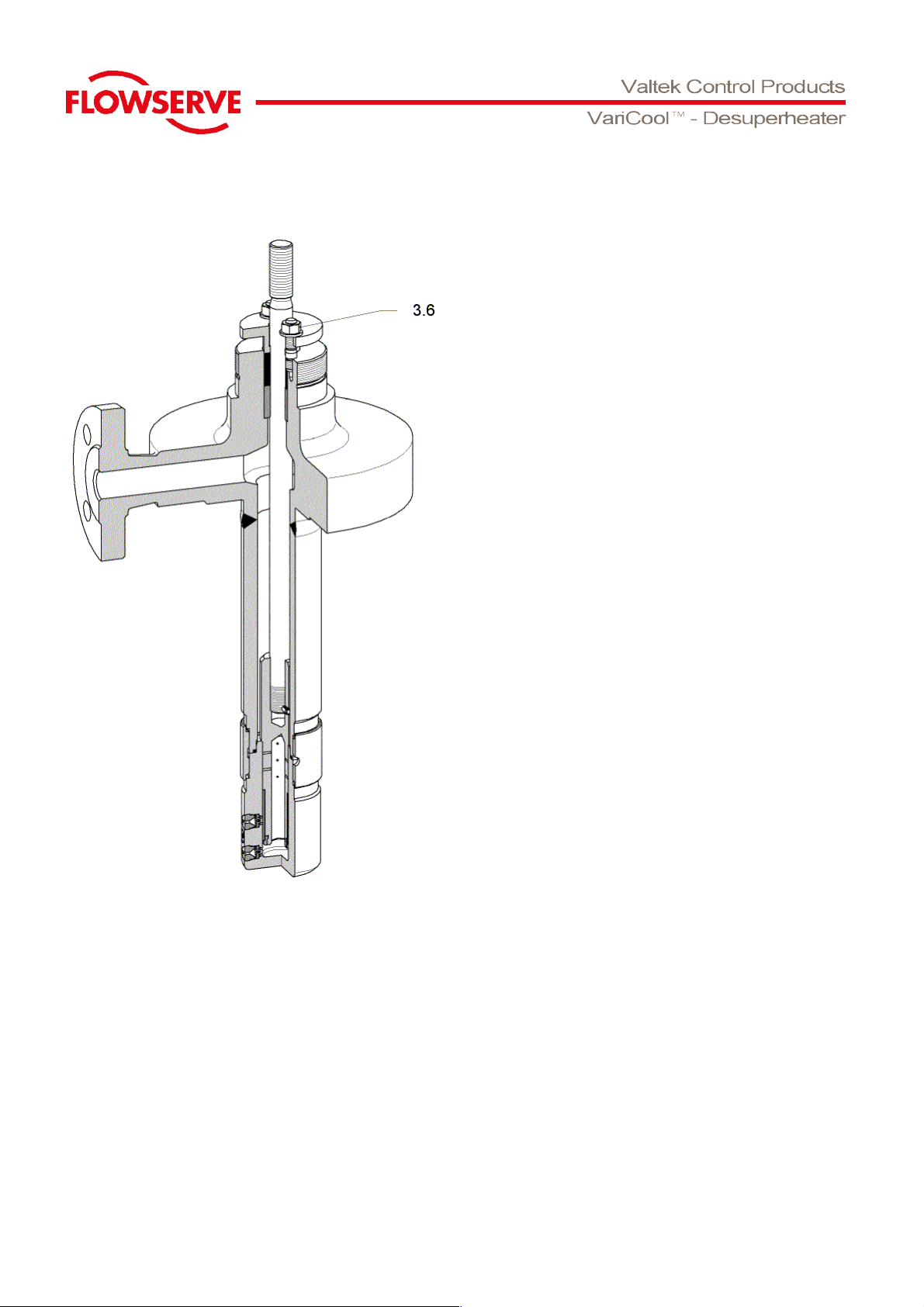
• Tighten the hexagonal nuts (3.6) evenly
The stem must move smoothly !

Protection
against torsion
K plug, stem, piston sleeve
S nozzle-set
D seal-set

SAEEIMV901 03.08
Flowserve (Austria) GmbH
Control Valves – Villach Operation
Kasernengasse 6
9500 Villach
Austria
Phone +43 (0) 42 42 / 41 1 81 - 0
Fax +43 (0) 42 42 / 41 1 81 - 50 or 51
E-mail villach_operation@flowserve.com
www.flowserve.com
www.flowserve-villach.com