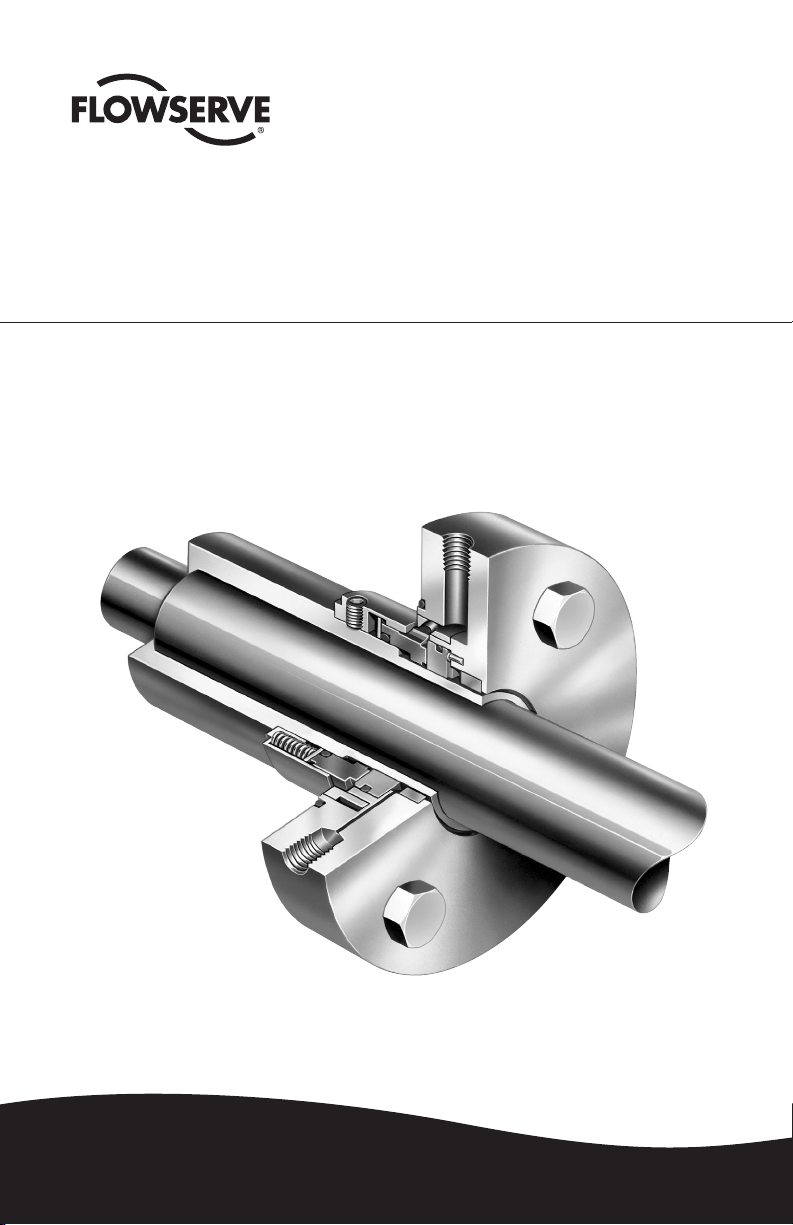
Installation
Instructions
BW Seals
General Service
Balanced Pusher Seal
Q, QB, QBQ, QBS, QBU, QBQ LZ
®
Q, QB Series
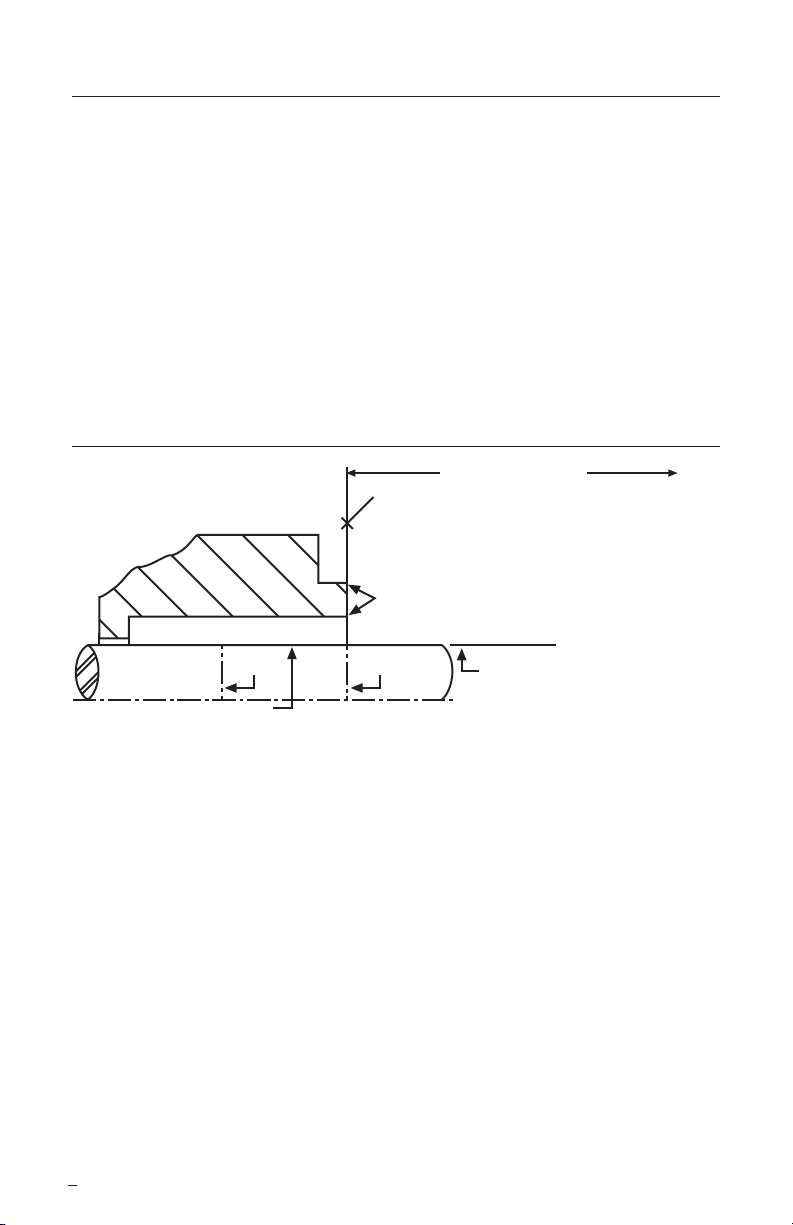
1 Equipment Check
1.1 Follow plant safety regulations:
• lock out motor and valves.
• wear designated personal safety equipment.
• relieve any pressure in system.
• consult plant MSDS les for hazardous material regulations.
1.2 Adjust the bearings, coupling, and impeller so that the shaft is in its operating
axial position. This shaft position must be used to check all seal setting (SS)
dimensions during installation. Disassemble equipment to allow access to seal
installation area.
1.3 Remove all burrs, nicks or scratches, and sharp edges from the shaft and sleeve
including sharp edges of keyways and threads. Replace worn shaft or sleeve. Make
sure the seal housing bore, face, and sealing uid ush taps are clean and free of
burrs and sharp edges that might damage gasket.
Seal Chamber Requirements Figure 1
To first obstruction
Face of seal housing to be square to the
axis of the shaft to within 0.0005 mm/mm
(0.0005 inch/inch) of seal chamber bore TIR
and have a 1.6 μm (63 μinch) R finish or better
Gland pilot can be at either of these
register locations, concentric to within
0.125 mm (0.005 inch) of shaft or
Seal housing bore to have 3.2 μm
(125
μ
inch) R finish or better
a
Scribe
Mark B
Sleeve or shaft finish to be
0.8 μm (32 μinch) R or better
• Bearings must be in good condition
• Maximum lateral or axial movement of shaft (end play) = 0.25 mm (0.010 inch) TIR
• Maximum shaft runout at face of seal housing = 0.05 mm (0.002 inch) TIR
• Maximum dynamic shaft deflection at seal housing = 0.05 mm (0.002 inch) TIR
a
sleeve OD TIR
Scribe
Mark A
Shaft or sleeve OD
+0.000 mm (+0.000 inch)
-0.050 mm (-0.002 inch)
+0.000 mm (+0.000 inch) API 610/682
-0.025 mm (-0.001 inch) DIN/ISO
a
ANSI
1.4 Check requirements for shaft, sleeve, and seal housing. See Figure 1.
1.5 Check assembly drawing included with the seal for equipment dimensions,
seal design, materials of construction, and piping connections.
1.6 Check shaft or sleeve OD, box depth, box bore, and distance to the rst
obstruction to ensure that they are dimensionally the same as shown on the
seal assembly drawing.
1.7 Check gland pilot and bolt holes to ensure they are adaptable to the equipment
and are the same as shown on the assembly drawing.
1.8 Handle all seal parts with care, they are manufactured to precise tolerances.
The seal faces are of special importance. These two sealing faces are lapped at
to within two light bands (23.2 millionths of an inch).
Keep the seal faces perfectly clean at all times.
The images of parts shown in these instructions may differ visually from the actual
2
parts due to manufacturing processes that do not affect the part function or quality.
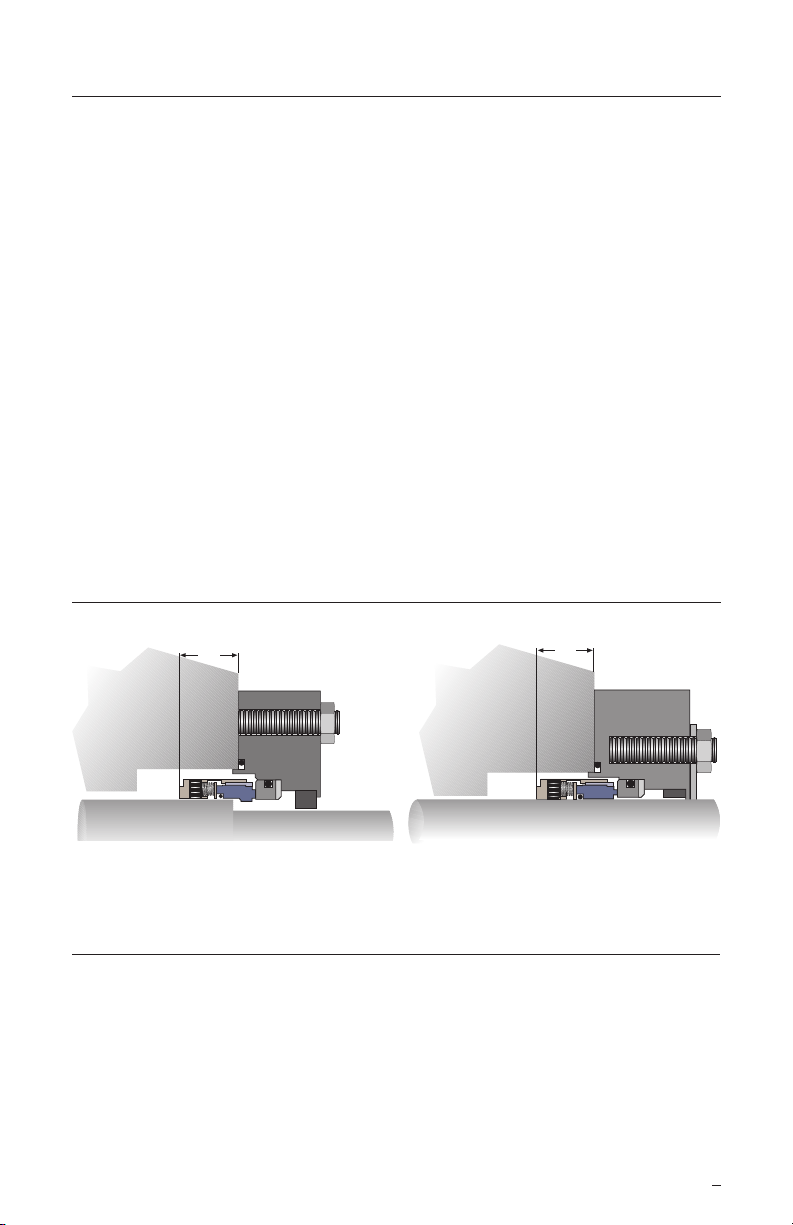
2 Assembly of Seal Components
2.1 Prepare rotating assembly for installation. The rotating assembly is comprised of
the spring holder, springs, retaining ring, set screws, rotating face and rotating face
gasket. Examine all parts - clean with alcohol or acetone as needed.
Caution: Consult material safety data sheets for proper handling of alcohol or acetone.
2.1.1 Install the set screws into the spring holder.
Caution: Set screws must not protrude into spring holder’s bore.
2.1.2 Install the springs in the spring pockets of the spring holder.
2.1.3 Align the retaining ring with the drive keys, compress the springs and rotate
the retaining ring so that the notches are no longer aligned with drive keys
to retain springs. Check springs to make sure none are bent over.
2.1.4 Install the rotating face gasket in the recess of the rear of the rotating face.
Lubricate the inside diameter of the rotating face gasket with silicone base
grease only, unless otherwise specied on seal drawing.
2.1.5 Press down rotating face gasket making sure it is retained in the groove
provided.
2.1.6 Install the rotating face in the spring holder with the slots in the face
aligning with the keys.
2.2 The rotating assembly can now be installed on the shaft or sleeve. Use caution
not to dislodge rotating face gasket. See Figure 2.
Installed Seal Assembly on Shaft or Customer’s Sleeve Figure 2
SS
SS
3 Seal Setting for Seal on Shaft or Customer’s Sleeve
For proper seal installation, you must obtain the correct seal assembly drawing for your
application.
3.1 Inspect pump shaft. Clean and remove any burrs, nicks, scratches, etc. which could
cause damage to gaskets when assembling seal.
3.2 Secure the seal assembly in place at its correct seal setting position (SS) by
tightening the rotating assembly set screws. See Figure 2. Refer to the seal
assembly drawing for correct seal setting dimension.
3