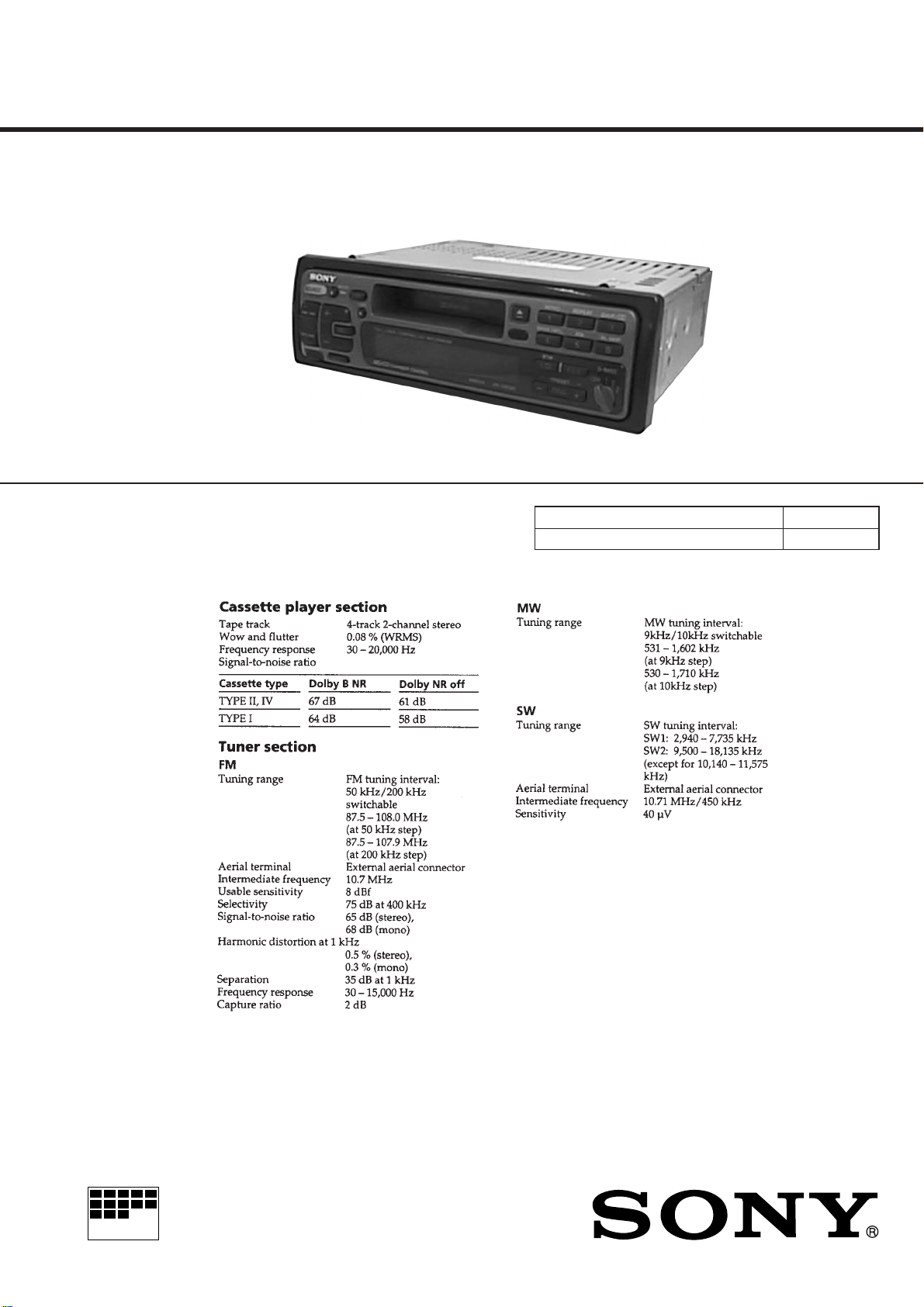
XR-C6100
SERVICE MANUAL
Dolby noise reduction manufactured under license
from Dolby Laboratories Licensing Corporation.
“DOLBY” and the double-D symbol a are trademarks of Dolby Laboratories Licensing Corporation.
SPECIFICATIONS
Saudi Arabia Model
Model Name Using Similar Mechanism NEW
Tape Transport Mechanism Type MG-25F-136
MICROFILM
– Continued on next page –
FM/MW/SW CASSETTE CAR STEREO
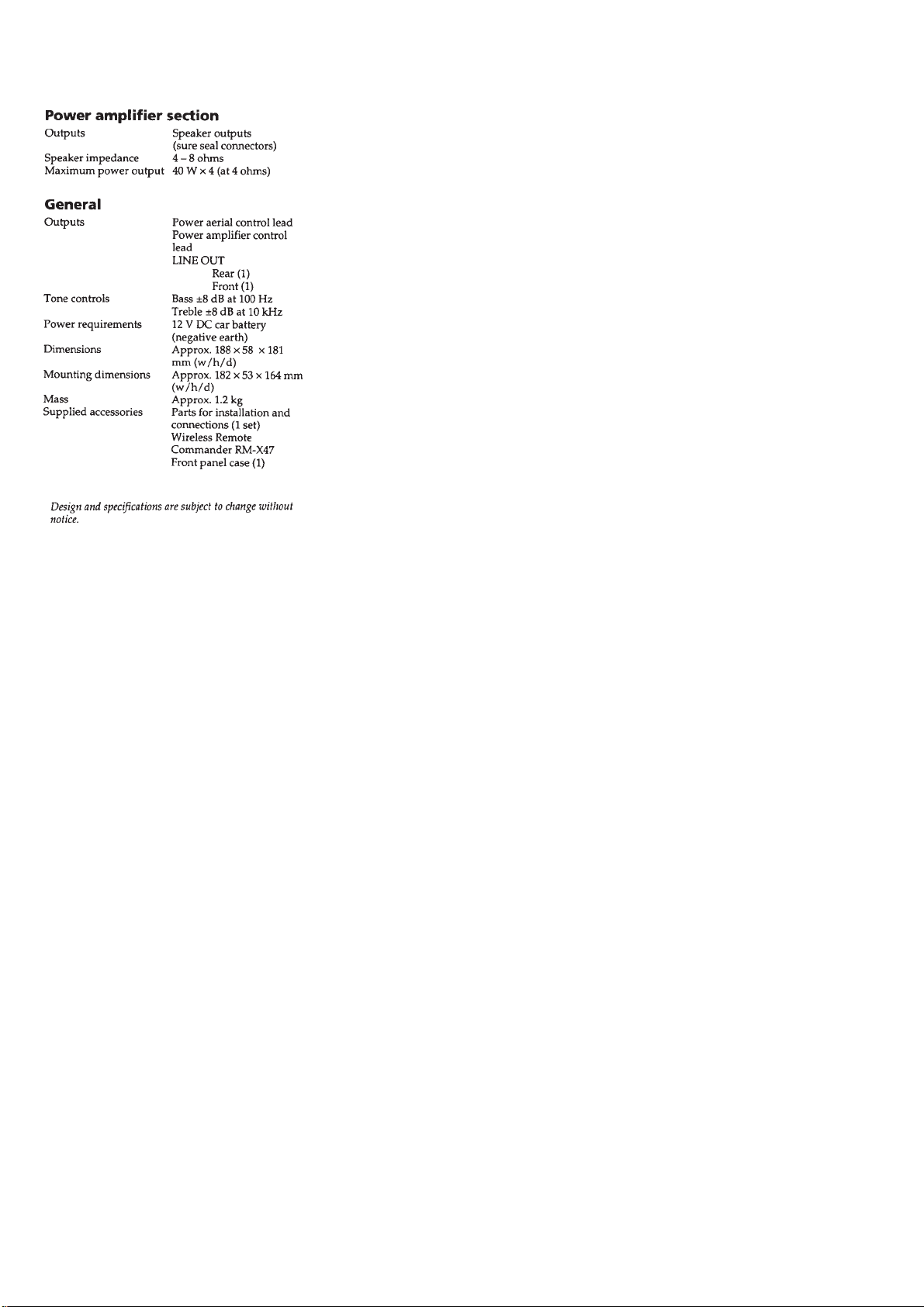
TABLE OF CONTENTS
1. GENERAL
Location of Controls ....................................................... 3
Installation....................................................................... 4
Connections ..................................................................... 5
2. DISASSEMBLY ......................................................... 8
3. ASSEMBLY OF MECHANISM DECK........... 10
4. MECHANICAL ADJUSTMENTS ....................... 13
5. ELECTRICAL ADJUSTMENTS
Test Mode........................................................................ 13
Tape Deck Section .......................................................... 13
Tuner Section .................................................................. 14
6. DIAGRAMS
6-1. IC Pin Function Description ........................................... 17
6-2. Note for Printed Wiring Boards and
Schematic Diagram .........................................................20
6-3. Printed Wiring Board – MAIN Section –...................... 21
6-4. Schematic Diagram – MAIN Section (1/2) –................ 23
6-5. Schematic Diagram – MAIN Section (2/2) –................ 25
6-6. Printed Wiring Board – PANEL Section –.................... 27
6-7. Schematic Diagram – PANEL Section –....................... 29
7. EXPLODED VIEWS ................................................ 33
8. ELECTRICAL PARTS LIST ............................... 36
Flexible Circuit Board Repairing
• Keep the temperature of the soldering iron around 270 ˚C dur-
ing repairing.
• Do not touch the soldering iron on the same conductor of the
circuit board (within 3 times).
• Be careful not to apply force on the conductor when soldering
or unsoldering.
Notes on chip component replacement
• Never reuse a disconnected chip component.
• Notice that the minus side of a tantalum capacitor may be dam-
aged by heat.
– 2 –
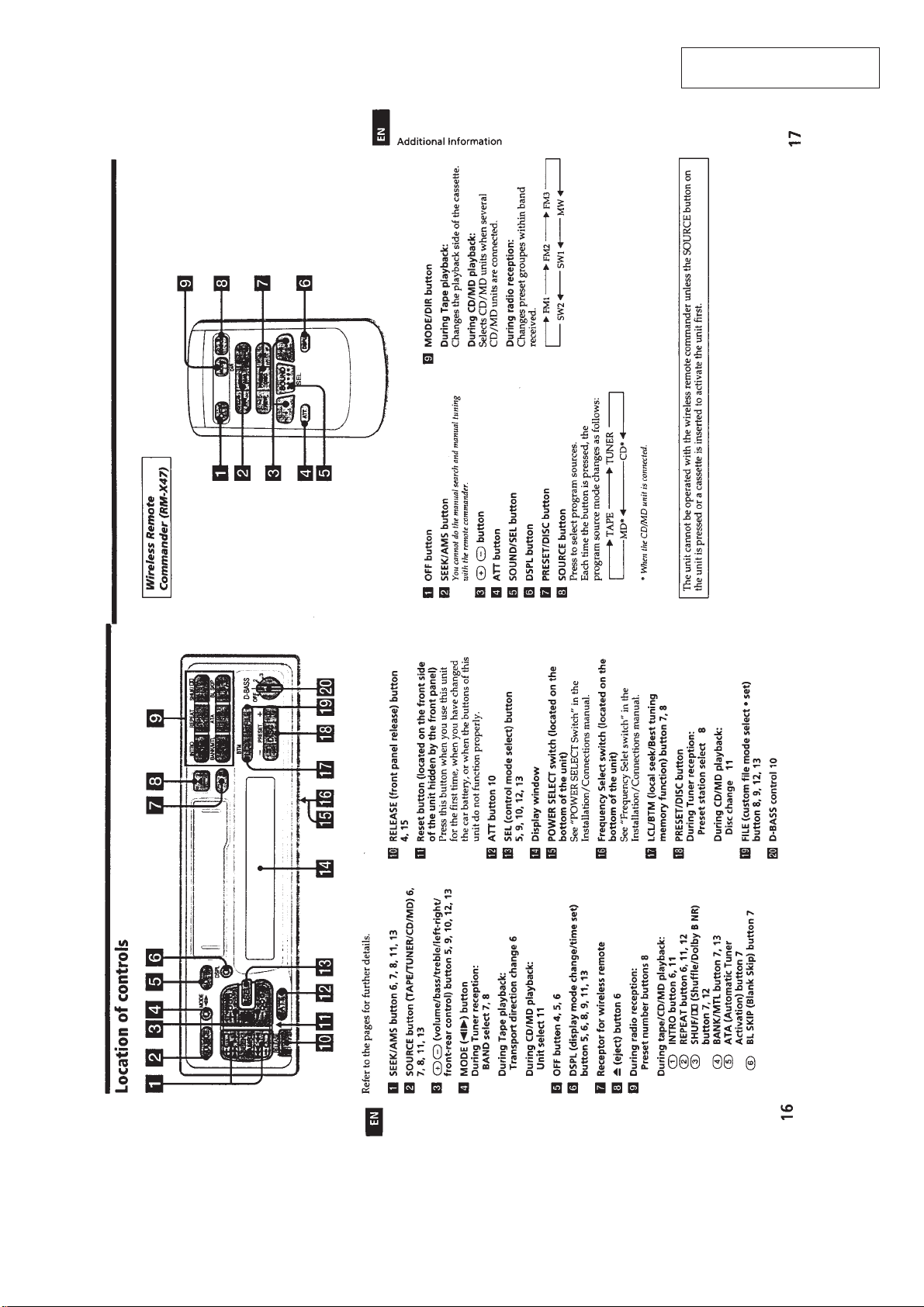
SECTION 1
GENERAL
This section is extracted from
instruction manual.
– 3 –
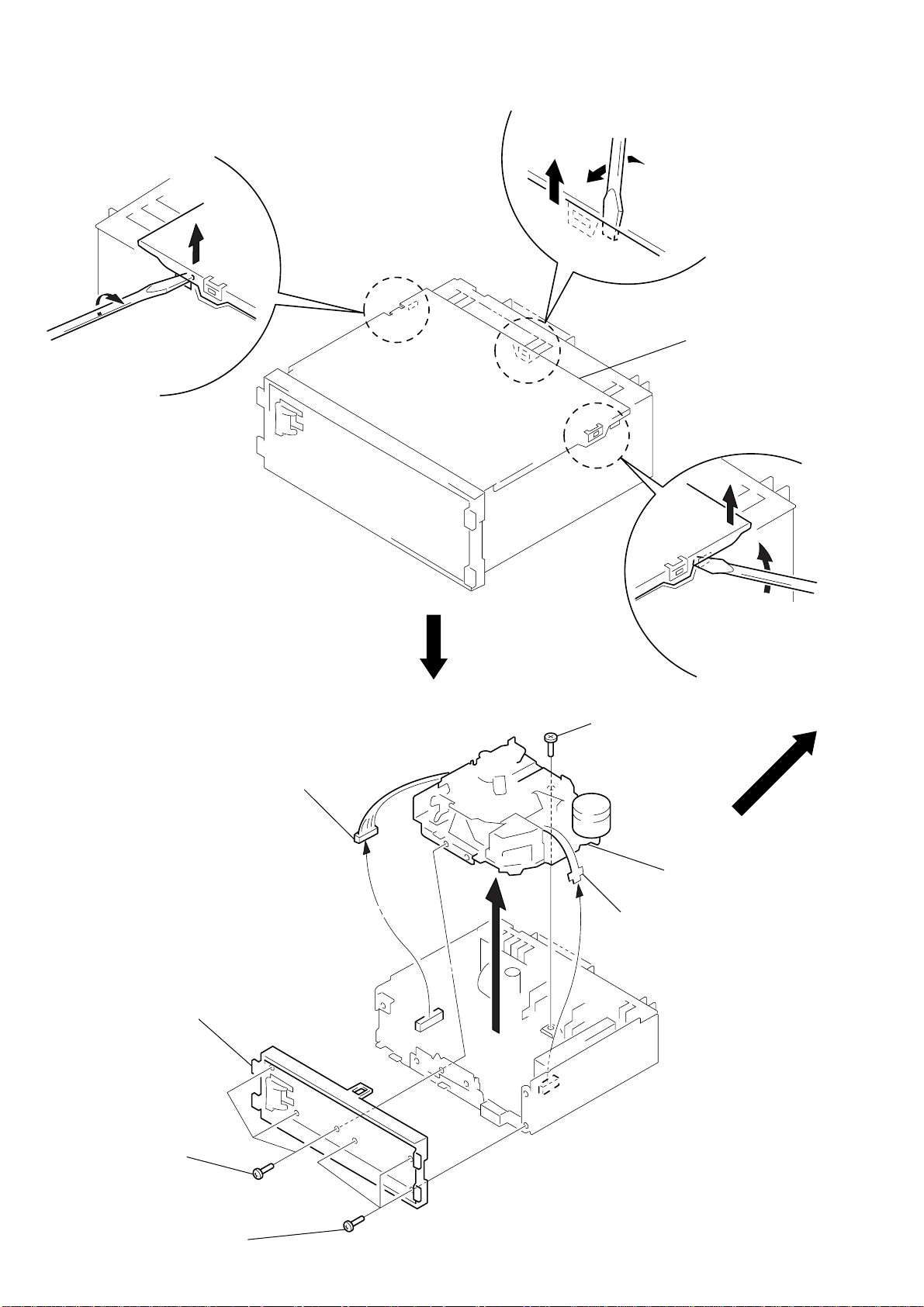
SECTION 2
DISASSEMBLY
Note: Follow the disassembly procedure in the numerical order given.
COVER ASS’Y
2
1
2
1
3
cover ass’y
2
SUB PANEL, MECHANISM DECK (MG-25F-136)
3
connector
(CN302)
5
screw
(PTT2.6
4
×
6)
6
mechanism dec
(MG-25F-136)
flexible flat cable
(CN301)
1
2
1
three screws
(PTT2.6
sub panel
×
6)
1
three screws
(PTT2.6
×
6)
– 8 –
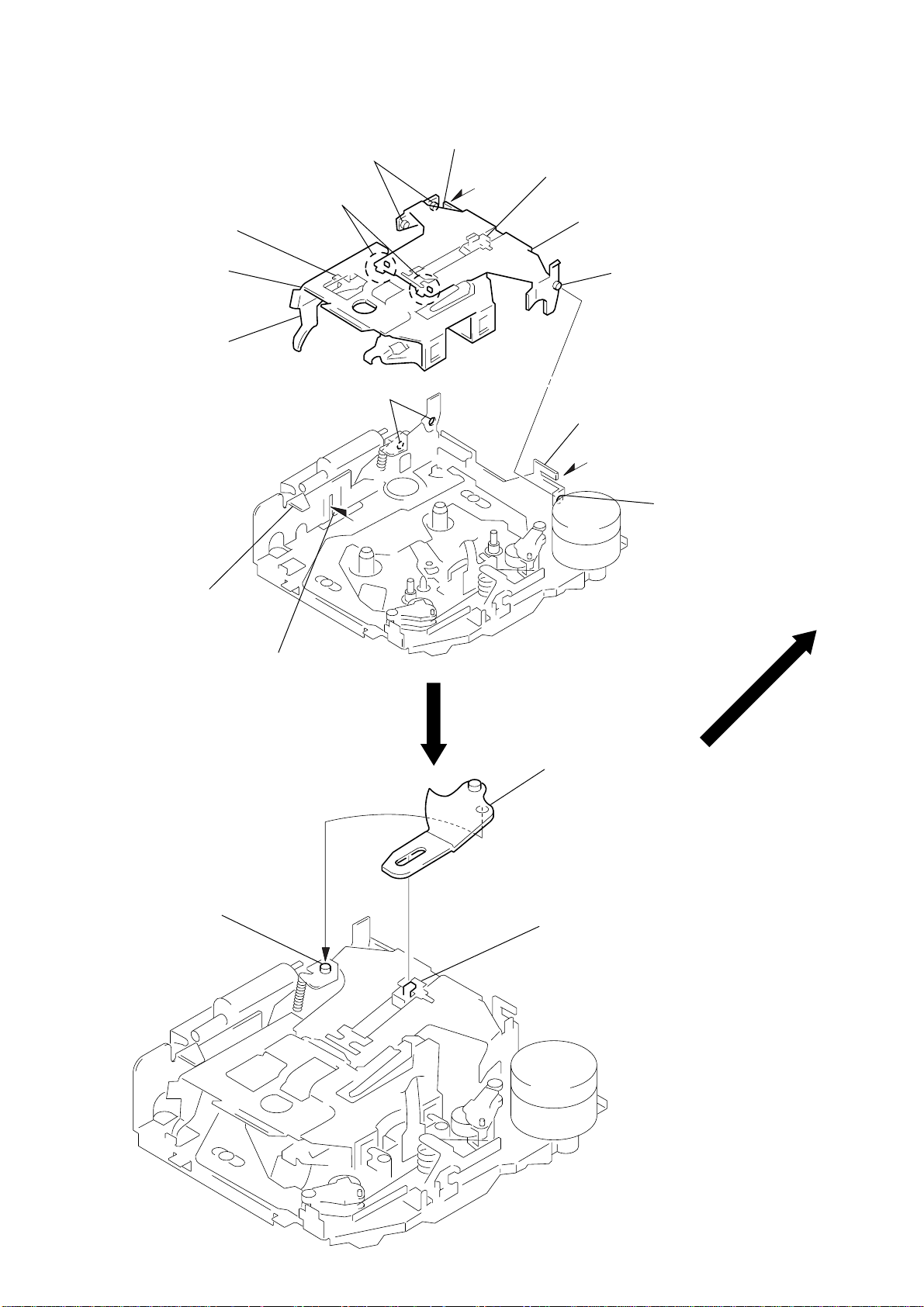
SECTION 3
ASSEMBLY OF MECHANISM DECK
Note: Follow the assembly procedure in the numerical order given.
HOUSING
4
Fit claw on B part.
3
Put the housing
under
A
part.
2
Install the hanger onto
two claws of the housing.
housing
5
Fit projection on C part.
C
part
7
Holder the hanger by bending the claw.
1
Install the catch to the hanger.
hanger
6
Fit projection on D part.
8
Hold the hanger by
bending the claw.
D
part
ARM (SUCTION)
A
part
projection
B
part
2
Move the arm (suction) in the arro
direction and fit on projection.
1
Fit the arm (suction) on the shaft.
– 10 –
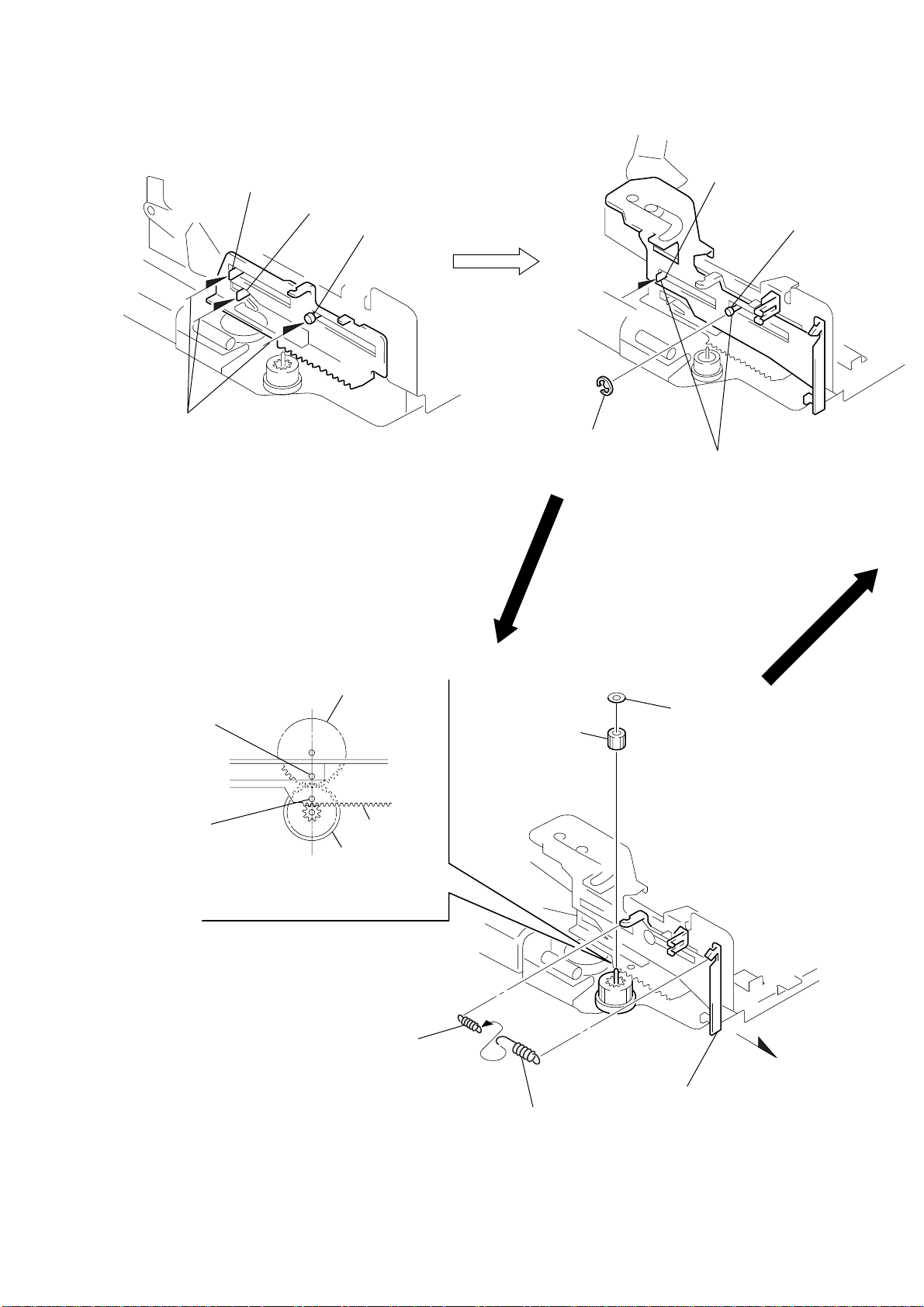
LEVER (LDG-A) / (LDG-B)
shaft
A
shaft
1
Fit the lever (LDG-A) on
shafts
A
– C and install it.
B
shaft
C
3
type-E stop ring 2.0
shaft
A
Fit the lever (LDG-B) on
2
shafts
A
install it.
and B and
shaft
B
GEAR (LDG-FT)
hole
hole
gear (LDG-D)
lever (LDG-A)
gear (LDG-FB)
4
Align hole in the gear (LDG-D)
with hole the lever (LDG-A).
2
tension spring (LD-2)
5
gear (LDG-FT)
1
2
tension spring (LD-1)
6
polyethylene washer
3
Move the lever (LDG-B)
in the arrow direction.
– 11 –