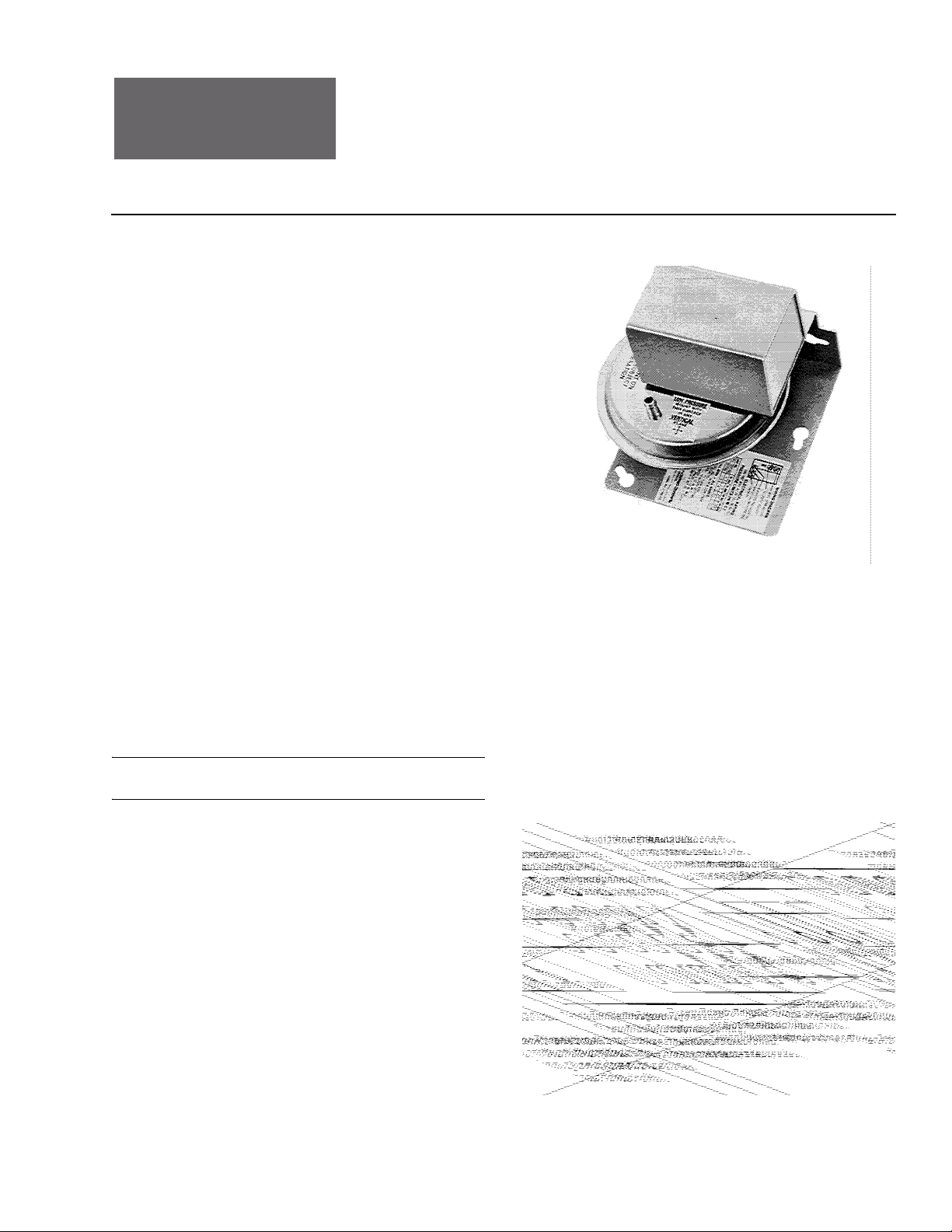
For use with Schneider Electric reversible control actuators
and for controlling differential pressures, static pressures or
air velocities in duct systems.
Other Applications:
• Static pressure control in hospital white rooms.
• Draft and exhaust damper control.
• Liquid level control in closed tanks.
All metal construction with conduit opening, for 13 mm (1/2")
conduit fitting. Has barbed connections for high and low
pressure connections for 9 mm (3/8") O.D. tubing. Unit has
SPDT floating contact, rated for 1.0 amps at 24 volts. Unit has
integral arc suppression. Ambient temperature range: -29 to
60°C (-20 to 140°F). Has coded screw terminals. Mounts with
diaphragm vertical on a vibration free surface. Dimensions:
130 mm (5-1/8") high, 120 mm (4-3/4") wide, and 111 mm
(4-3/8") deep.
Option: Non
ACCESSORIES
AP-301 Static probe for pressure .24 kPa (1" water)
AP-305 Static probe for pressures below .24 kPa
AT-208 Duct mounting bracket for probes other than
e
and up
(1" water)
AP-301 an
d AP-305
INSTALLATION
Caution: These units are for use with air or
non-combustible gases only.
PF-305, PF-306, PF-307, PF-308
Floating Differential Pressure
Electric Air Flow Switch
General Instructions
3. Mount the unit with mounting screws supplied. Note: The
diaphragm must be mounted in a vertical plane in a
location free from vibration. See Figure 3 for mounting
details.
4. Connect the probe(s) to the pressure taps using the 3/8"
O.D. plastic tubing su
5. Make all connections in accordance with job wiring
diagrams and in compliance with national and local
codes.
pplied.
Typical Actuators:
One Schneider Electric MP-300, -400, -2000 and -9700
series actuator directly. An AM-345 or AE-347 time delay
relay is required for use with the MP-9200, -9400, -9600, and
-9800 series actuator.
An SPDT floating switch action where “Common” makes to
“Normally Closed” on a decrease in differential pressure
between input ports, and to “Normally Open” on an increase
in differential between input ports.
1. Select appropriate probes from Table 1.
2. Install probe. See Figure 4. Sampling probes should be
located in areas of minimum air turbulence (6 to 8 duct
diameters downstream from fan outlet, elbows, tees,
ordampers). If this is not possible locate the probe tip as
close to the center of the duct as possible.
Figure-1 Typical Wiring.
Printed in U.S.A. 5/10 © Copyright 2010 Schneider Electric All Rights Reserved. F-17492-3
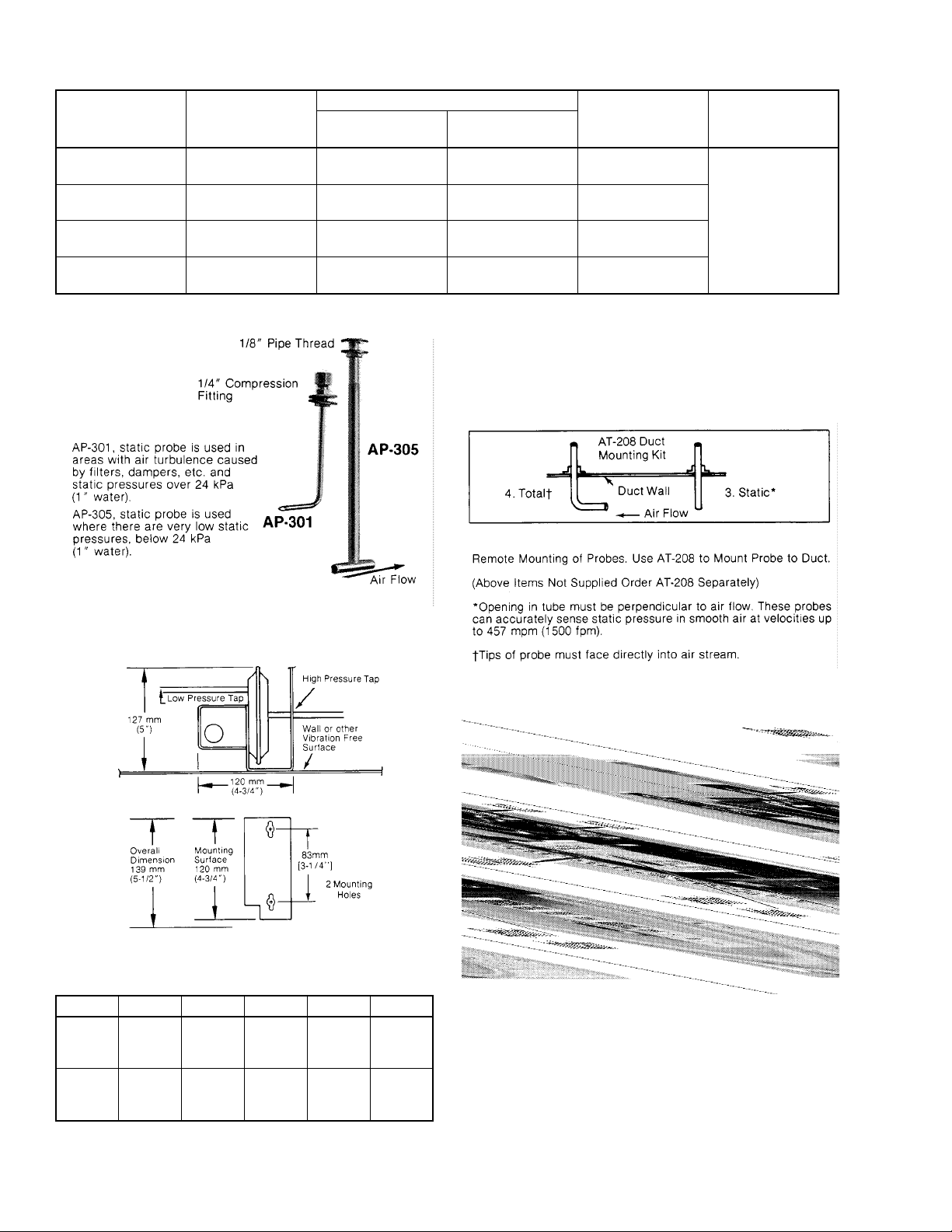
Table-1 Specification Table.
Differential Pressure
Part Number
PF-305
PF-306
PF-307
PF-308
* Min. null is with 127 μm (.005 in.) contact gap. Max null is 635 μM (.025
contact gap.
Setpoint Range kPa
(in. of water)
-.12 to +.12
(-.5 to +.5)
.04 to .32
(.2 to 1.3)
.27 to .87
(1.1 to 3.5)
.79 to 2.48
(3.2 to 10)
At Minimum Setpoint
kPa (in. of water)
.01 to .03
(.06 to .14)
.01 to .03
(.05 to.13)
.01 to .03
(.06 to .17)
.02 to .09
(.12 to .4)
Adjustable Null S
At Maxi
Probes 3 and 4 (see Figure 4) can be constructed from 1/4
inch O.D., copper, brass, or aluminum tubing. The ends of the
probes should be cut square to the sides of the tube and
deburred. Total pressure probe must have the sensing end
bent at 90° approximately 25 to 76 mm (1 to 3 inches) from the
tip.
pan*
mum Setpoint
(in. of water)
.01 to .03
(.07 to .14)
.03 to .06
(.13 to .28)
.02 to .07
(.11 to .31)
.06 to .19
(.24 to .8)
Velocity Range M/S
PM) 21°C (70°F)
(F
Air
2 to 14
(400 to 2800)
9 to 23
(1800 to 4600)
22 to 38
(4200 to 7500)
37 to 71
(7200 to 14000)
Maximum Pressure
Differential 3 kPa
(12" Water)
INPUT
7 kPa (28” W
ater)
Figure-2 Optional Probes.
Figure-3 Mounting.
Table-2 Remote Mounting of Probe(s).
Static Veloc ity
High
Press.
Ta p
Low
Press.
Ta p
a
Pilot can be used instead of two probes.
b
Highest (absolute) pressure should be applied to high pressure tap.
Probe 3 Probe 4 Probe 4 Probe 3 Probe 4
b
— Pr
a
Total ΔStatic ΔTotal
obe 3 — Probe 3 Probe 4
Δ = ΔDifferential.
Figure-4
Figure-5
2 © Copyright 2010 Schneider Electric All Rights Reserved. F-17492-3

ADJUSTMENT
The locations for the setpoint and null span adjusting screws
are shown in Figure 5. Factory settings as below:
Model
PF-305 .02 (.1)
PF-306 .17 (.7)
PF-307 .47 (1.9)
PF-308 1.49 (6)
Setpoint kPa
(inches water)
Setpoint: Turn the setpoint screw CCW to increase if required.
Null Span: This is the pressure change in the duct without
switch.
All models are factory set at the maximum null span; refer to
Specification table. Turn the null adjustment screw CW to
decrease if required.
FIELD REPAIR
Field repair is not recommended. If the system does not
perform and the reason is traced to the control unit, it must be
replaced.
F-17492-3 © Copyright 2010 Schneider Electric All Rights Reserved. 3

On Octo be r 1s t, 2009, TAC became the Buil d ing s business of i ts pa ren t comp any Schneid er Electric. Thi s doc ument ref le cts the vi sual ide nt it y of Schn eid er Electr ic,
however there remains references to T AC as a corporate brand in the body copy. As each document is updated, the body copy will be cha nge d to reflect appropr iat e
corporate brand chan
Copyright 2010, Schneider Electric
All brand names, trademarks and registered
trademarks are the property of their respective
owners. Information contained within this
document is subject to change without notice.
F-17492-3
es.