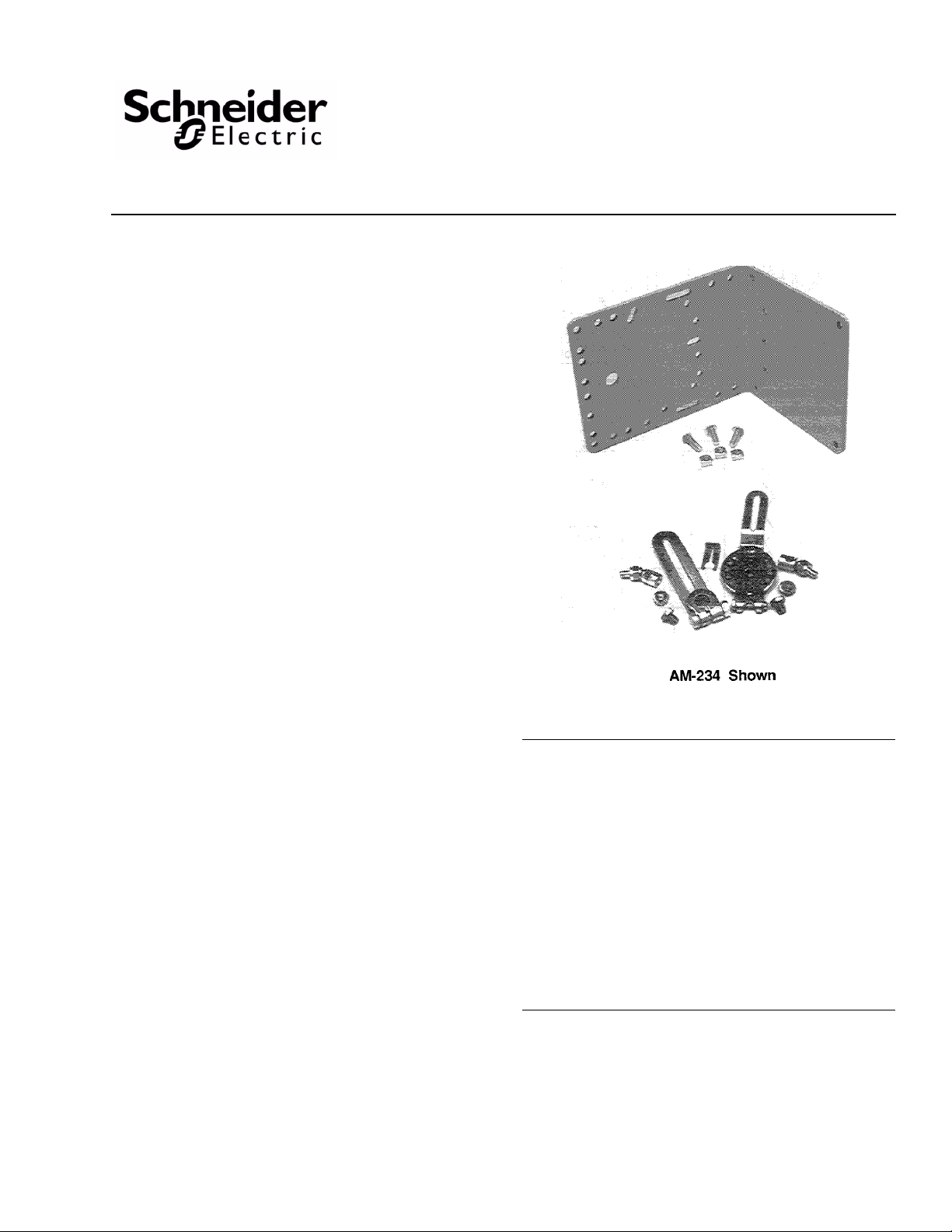
APPLICATION
Linkage for connection MM and MMR-400/500 Series
Modular Motors to dampers.
Each AM-230 kit contains:
One (1) AM-230 Motor crank arm assembly for connecting
e shafts of MM & MMR-400/500 Series
to squar
Modular Motor
One (1) Shaft retainer clip
One (1) General Instruction Sheet
Each AM-234 kit contains:
One (1) AM-230 Motor crank arm kit for connecting to
e shafts of MM & MMR-400/500 Series
squar
Modular Motor
One (1) AM-113 damper crank arm for 1/2" diameter
er shaft
damp
Two (2) AM-132 ball joint linkage connectors
One (1) AM-301 Motor mounting kit
Four (4) #10 x 3/4" round head sheet metal screws
Four (4) 1/4-20 x 3/4" hex head bolts (with washers and
One (1) General Instruction Sheet
Each AM-235 kit contains:
One (1) AM-230 Motor crank arm kit for connecting to
Three (3) AM-113 damper crank arms for 1/2" diameter
Four (4) AM-132 ball joint linkage connectors
One (1) AM-301 Motor mounting kit
Four (4) #10 x 3/4" round head sheet metal screws
Four (4) 1/4-20 x 3/4" hex head bolts (with washers and
One (1) General Instruction Sheet
Other Schneider Electric Components Required:
MM or MMR Modular Motor, MMC Control Module, and other
Other Schneider Electric Components That May Be Required:
AM-125-XXX Damper rod
AM-111 For 5/16" diameter damper shaft
AM-112 For 3/8" diameter damper shaft
AM-113 For 1/2" diameter damper shaft (included in AM-234
AM-115 For 7/16" diameter damper shaft
s)
nut
e shafts of MM & MMR-400/500 Series
squar
Modular Motor
er shaft
damp
s)
nut
equired accessories.
r
AM-235 kits)
and
PRE-INSTALLATION
Inspection
Visually inspect the package for damage. If damaged, notify
the appropriate carrier immediately. If undamaged, open the
package and visually inspect the device for obvious defects.
Return damaged or defective products.
AM-230 Series
Damper Linkage Kits
General Instructions
INSTALLATION
Caution:
1. Installer must be a qualified, experienced technician.
2. MM-400/500 Series and MMR-400/500 Series General
Instru
ction sheets contain specific information on
modular motor installation.
3. Avoid locations where excessive moisture, corrosive
fumes or vibration are present. AM-230 Series linkages
are intended for mounting only to the MM-400/500
Series and MMR-400/500 Series Modular Motors.
4. Damper rod (AM-125-XXX) should be:
a. Long enough for easy adjustment.
b. Short enough to be rigid, providing good damper
response.
Required Installation Items
• Tools (not provided):
Appropriate screwdriver and wrenches.
Printed in U.S.A. 6-10 © Copyright 2010 Schneider Electric All Rights Reserved. F-23377-5
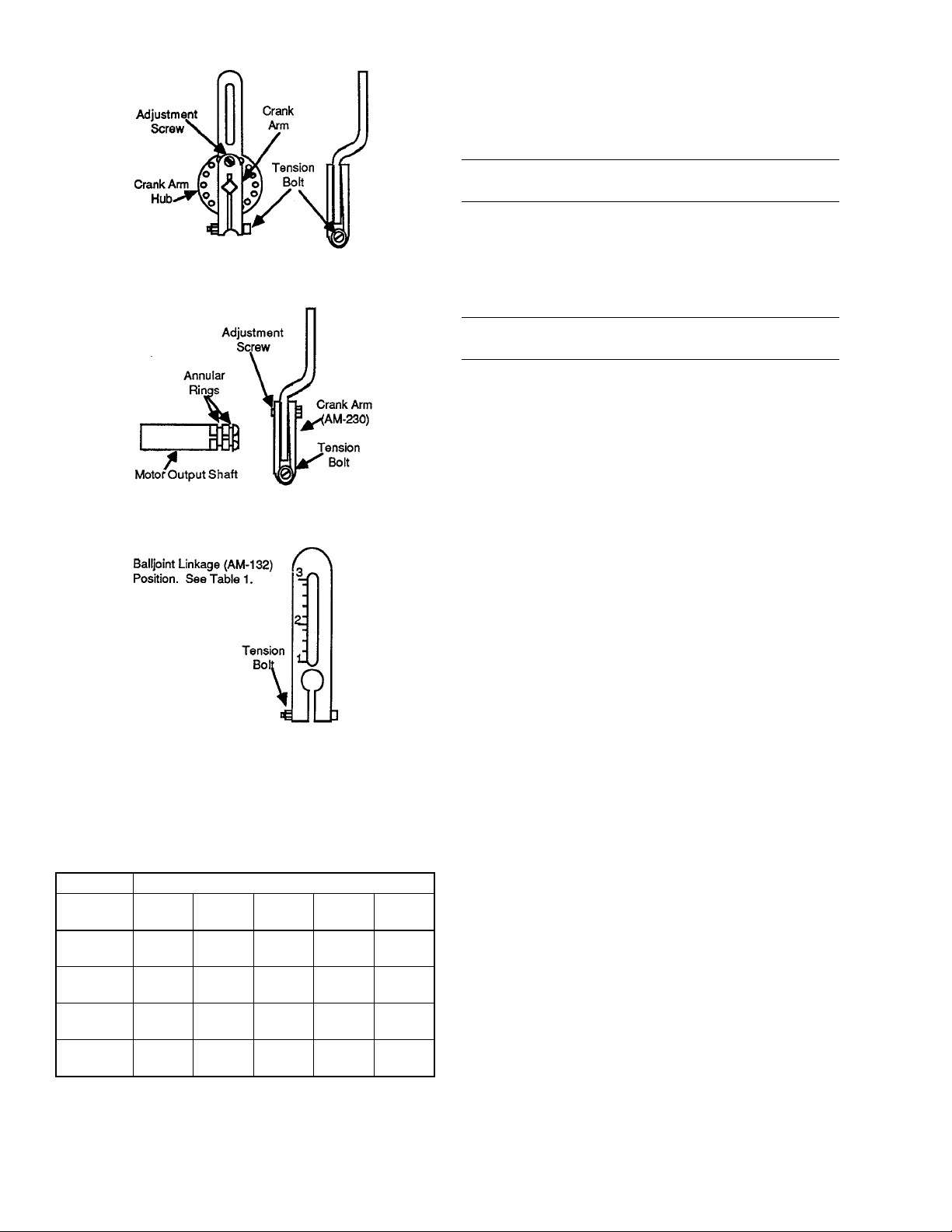
Figure-1 Crank Arm/Hub AM-230.
Figure-2 Crank Arm Mounting to Motor Output Shaft.
1. Align the modular motor output shaft to the shaft hole in the
motor crank arm/hub (AM-230) and insert the crank
arm/hub (AM-230) on the motor output shaft.
2. Finger tighten the motor crank arm/hub screws at this
phase of the installation.
Note: Do not install retainer clip until adjustments are
complete.
3. Insert the damper crank arm on the damper shaft
(AM-113 for 1/2" dia. shaft). Position the damper blades
in the position required with the motor in CCW
(counterclockwise) position (as viewed from the “Load” or
“Load, Normally Closed-CCW Spring Return” end).
Note: The crank arm must be firmly installed on the motor
output shaft and rest against the output shaft shoulder.
4. Finger tighten the damper crank arm screws only at this
point of the installation.
5. Install a ball joint linkage (AM-132) as close as possible
to motor output shaft.
6. Install a ball joint linkage (AM-132) at the positions shown
on the damper crank arm (see Figure 3) - adjust after
linkage is assembled and the motor is run through its
stroke.
Figure-3 Balljoint Linkage Position on Damper Crank Arm
AM-11X.
LINKAGE MOUNTING
Table-1 Position of Ball Joint on Damper Crank Arm.
(Ball Joint at minimum position on motor crank
arm.)
Damper Rotation
Motor
Rotation
75°
90°
110°
160°
Dimensions in inches (mm).
* not obtainable with standard AM-11X damper crank arm.
** Recommended damper rotation for two position control.
See Figures 1 through 4 and Table 1.
40° 50° 60° 75° 90°**
2-11/16
(68)
3-1/8
(79)
3-9/16
(90)*
4-5/16*
(110)
2-3/16
(56)
2-1/2
(64)
2-7/8
(73)
3-1/2*
(89)
1-13/16
(46)
2-1/8
(54)
2-7/16
(62)
2-15/16
(75)
1-1/2
(38)
1-3/4
(44)
2 (51)
2-7/16
(62)
1-5/16
(33)
1-1/2
(38)
1-3/4
(44)
2-1/16
(52)
Two Position Damper Ball Joint Position on Damper
Crank Arm (See Figure 3 and Table 1)
Set the ball joint on the damper crank arm as indicated in
Table 1. the damper will be completely open or completely closed if required by a two position controller.
Proportional Damper Ball Joint Position on Damper
Crank Arm (See Figure 3 and Table 1)
Set the ball joint on the damper crank arm (see T able 1).
A damper set to open at 60° will allow approximately
96% of the maximum air flow through the damper. Further damper opening will pass little, if any, additional air.
Motor shaft rotation of 160° and a maximum damper
shaft rotation of 60° will provide the best possible air flow
control by the damper.
7. Assemble the pushrod to the ball joints. Finger tighten the
ball joint setscrews.
ADJUSTMENTS
See Figure 5.
1. Position the damper midstroke.
2. Slide the motor crank arm off the output shaft.
3. With the motor output shaft in line with the motor crank
arm rotate the motor crank arm around the motor output
shaft axis and the damper crank arm around the damper
shaft until both crank arms are perpendicular to the
imaginary line between the motor and damper shafts.
4. Tighten the set screws on the damper crank arm and ball
joint.
5. With the motor crank arm still off the output shaft:
a. Rotate the motor crank arm CW (clockwise) through
the remainder of the motor stroke.
2 © Copyright 2010 Schneider Electric All Rights Reserved. F-23377-5

Figure-4 Typical Motor Mounting and Damper Linkage.
Note: Clockwise reference to the motor output shaft rotation
is as seen from the “Load” or “Load, Normally Closed - CCW
Spring Return” end of the motor.
b. Rot ate the motor crank arm CCW to the position that
corresponds to the start of the stroke (the motor
de-energized position).
Complete steps a and b several times to confirm that the
damper and linkage will operate freely.
6. With the crank arm position corresponding to the CCW
end (the motor de-energized position), slip the motor
crank arm on the motor output shaft.
Note: It may be necessary to re-position the crank arm/hub
by removing the adjustment screw and inserting it in another
hole on the hub.
7. Insert retainer clip between crank arm and crank hub
(See Figure 6).
Note: The adjustment screw must be loose to provide
clearance for retainer clip insertion.
8. Tighten the motor crank arm adjustment screw.
9. Tighten the motor crank arm tension bolt.
CHECKOUT
1. Power the motor and run it through its complete stroke:
a. If linkage binding occurs, release one of the
connectors to prevent damage.
b. Make certain that any extra length of pushrod does
not foul and stall the motor.
c. Note that the motor rotates and linkage/damper
moves smoothly through-out the stroke
Caution: If crank arm does not provide proper travel, reset
connecting link in linkage connector. NEVER ATTEMPT TO
TURN THE MOTOR SHAFT WITH A WRENCH OR A
CRANK. This will cause internal damage.
2. Tighten all nuts and screws after making all adjustments.
3. Linkage assembly and adjustment is now complete.
MAINTENANCE
Regular maintenance of the total system is recommended to
assure sustained optimum performance.
FIELD REPAIR
None. Replace damaged components with functional linkage.
F-23377-5 © Copyright 2010 Schneider Electric All Rights Reserved. 3

On October 1st, 2009, TAC became the Buildings business of its parent com pany Schnei der Electric . This doc ument reflects the visual identity of Schneider Electric,
however there remains references to TAC as a corporate brand in the body copy. As each document is updated, the body copy will be cha nged to refl ect appropri ate
Figure-5 Typical Damper Linkage Position - Motor Crank Arm
Position May Change Due to Damper Location.
Figure-6 Retaining Clip Location.
corporate brand changes.
Copyright 2010, Schneider Electric
All brand names, trademarks and registered
trademarks are the property of their respective
owners. Information contained within this
document is subject to change without notice.
F-23377-5