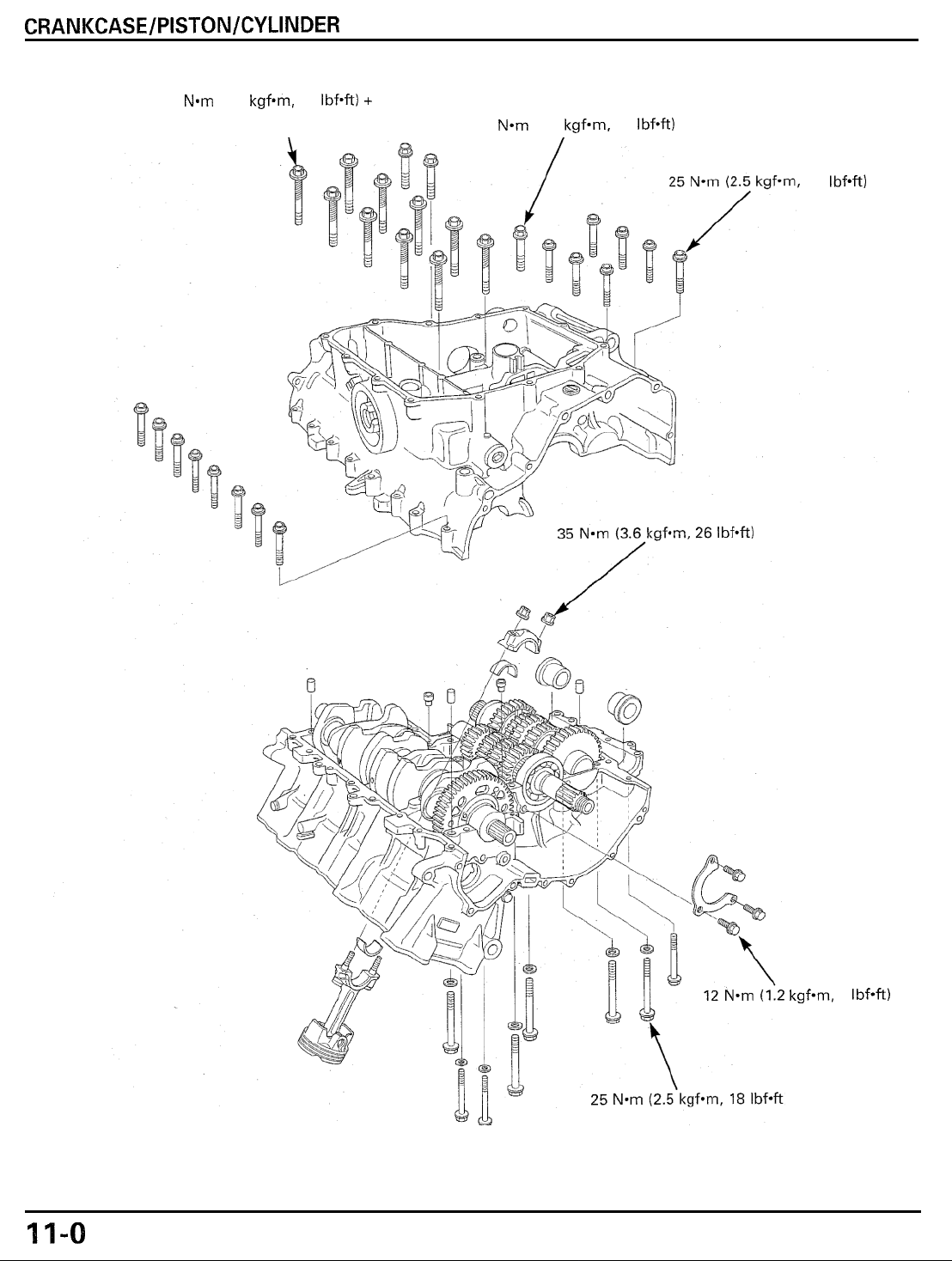
CRANKCASE/PlSTON/CYLlNDER
20
N-m
(2.0
kgf-m,
14
Ibf-ft)
\
+
150”
39
N*m
(4.0
kgfmm,
29
Ibf-ft)
18
Ibf*ft)
11-0
kgf-m, 9 Ibf-ft)
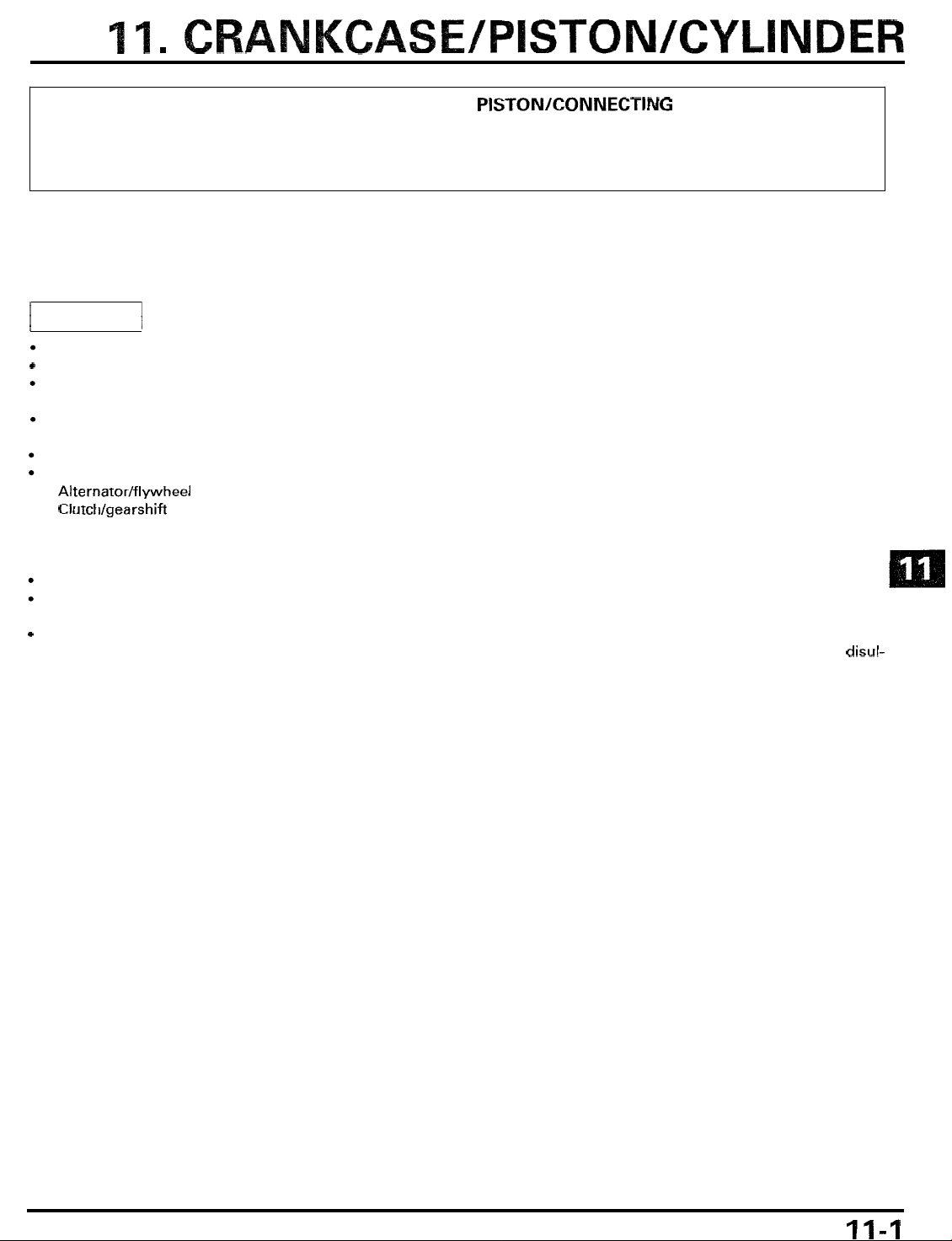
SERVICE INFORMATION 11-1 PISTON/CONNECTING ROD 11-4
TROUBLESHOOTING 11
CRANKCASE SEPARATION 11
SERVICE
INFORMATION
-
2 CRANKCASE COMBINATION 11-12
-
3
GENERAL
1
NOTICE
The main journal 9-mm bolts tightening method uses the Plastic Region Tightening Method (page 11-12).
a
Always use a new main journal 9-mm bolts (page 11-12).
The main journal 9-mm bolts is pre-coated with an oil additive for axial tension stability.
from the new 9-mm bolt surfaces.
Be sure to follow the tightening procedure on page 11-12 for crankcase bolt tightening.
This section covers crankcase separation for service of the crankshaft and pistons.
The following parts must be removed before separating the crankcase.
-
Alternator/flywheel (Section
-
Clutch/gearshift linkage (Section
-
Cylinder head (Section 8)
-
Engine (Section
-
Oil pump (Section
Mark and store the disassemble parts to ensure that they are installed in their original locations.
Mark and store the bearing inserts to be sure of their correct locations for reassembly.
installed, they will block the oil hole, causing insufficient lubrication and eventual engine seizure.
0
The connecting rod bearing inserts are select
code tables. After installing new bearings, recheck them with plastigauge to verify clearance. Apply molybdenum
fide oil
1
10)
7)
4)
to
the crank pin during assembly.
9)
Do
not remove the oil additive
If
the inserts are improperly
fit
and are identified by color codes. Select replacement bearings from the
disul-
11-1
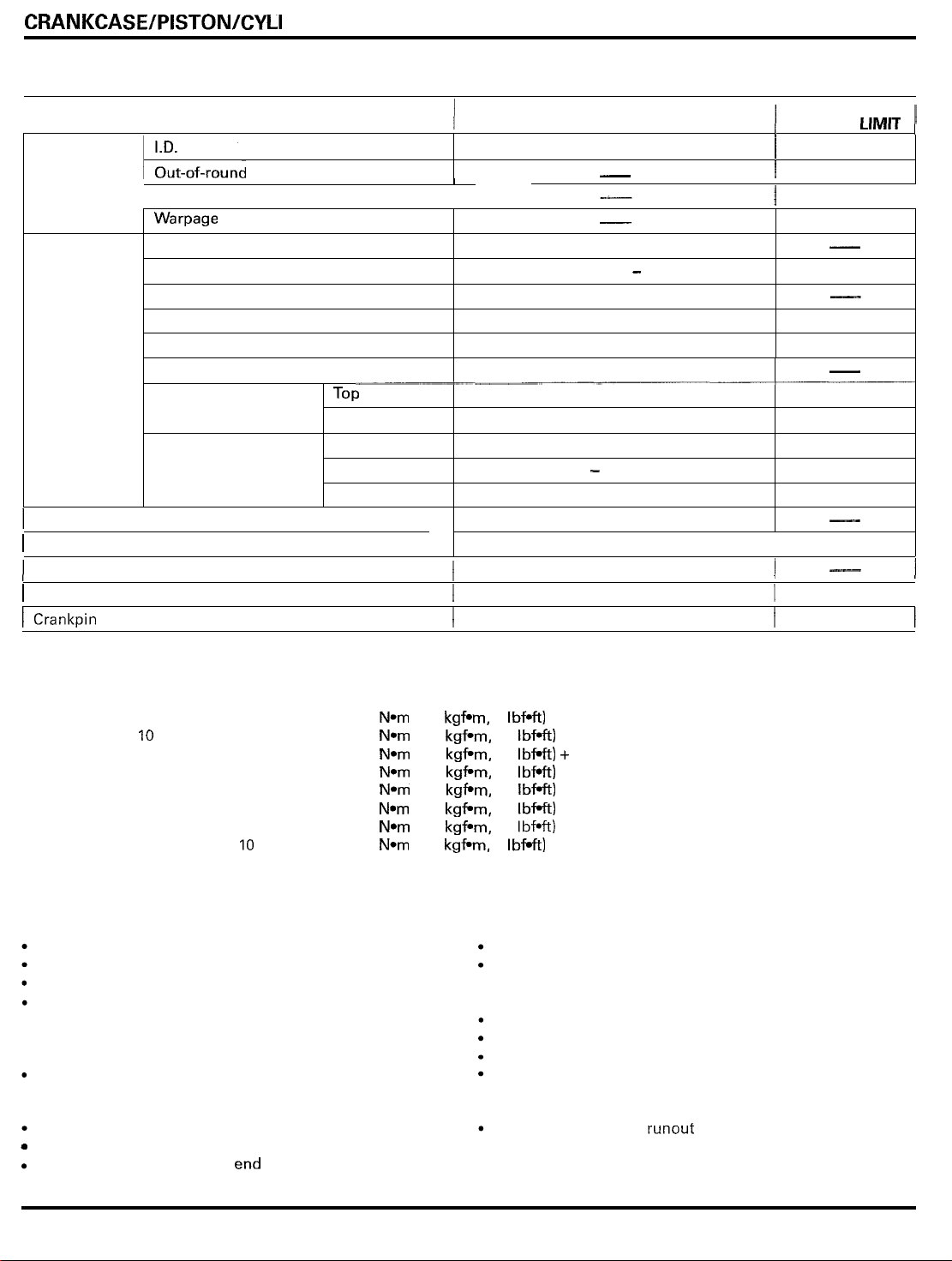
CRANKCASE/PISTON/CY LI N DER
SPECIFICATIONS
I
Cylinder
1
Et-of-round
I
1
Taper
Warpage
Piston, piston
rings
I
Cylinder-to-piston clearance
I
Connecting rod small end
1
Connecting rod-to-piston pin clearance
I
Connecting rod side clearance
I
Crankpin oil clearance
Piston mark direction
Piston
Piston
Piston pin bore
Piston pin
Piston-to-piston pin clearance
Piston ring
groove clearance
Piston ring end gap Top
ITEM
O.D.
O.D.
measurement point
I.D.
O.D.
-to-
ring TOP
I.D.
~~~
Second
Second
Oil (side rail)
Unit: mm (in)
STANDARD
75.000 - 75.015 (2.9528 - 2.9533)
I
"0"
mark facing toward the intake side
74.960 - 74.980 (2.9512 - 2.9520) 74.895 (2.949)
4
mm
(0.2
in) from bottom of skirt
17.002 - 17.008 (0.6694 - 0.6696)
16.994
-
17.000 (0.6691 - 0.6693)
0.002 - 0.014 (0.0001 - 0.0006)
0.030 - 0.065 (0.0012 - 0.0026)
0.015
-
0.045
0.28 - 0.38 (0.011 - 0.015) 0.5 (0.02)
0.40 - 0.55 (0.01 6 - 0.022) 0.7
-
0.7 (0.01 - 0.03)
0.2
0.020
-
0.055 (0.0008 - 0.0022)
1
0.016 - 0.040 (0.0006 - 0.0016)
1
0.05 - 0.20 (0.002 - 0.008)
I
0.030 - 0.052 (0.0012
-
-
(0.0006
-
0.0018)
-
0.0020)
I
SERVICE LIMIT
j
75.15 (2.959)
1
0.10 (0.004)
I
1
0.10 (0.004)
0.05 (0.002)
~
-
17.03 (0.670)
16.98 (0.669)
-
0.08 (0.003)
0.06
(0.002)
(0.03)
0.9 (0.04)
-
I I
I
1
-
0.30 (0.012)
0.062 (0.0024)
1
I
I
I
TORQUE VALUES
Mainshaft bearing set plate bolt
10
Crankcase bolt,
Connecting rod bearing cap nut
Upper crankcase sealing bolt
Lower crankcase sealing bolt,
mm
9
mm (main journal bolt)
8
mm
20
10
mm
mm
12
39
20
25
35
22
30
12
N*m
N*m
N*m
N*m
N*m
N*m
N*m
N*m
(1.2
(4.0
(2.0
(2.5
(3.6
(2.2
(3.1
(1.2
TROUBLESHOOTING
Cylinder compression is too
Blown cylinder head gasket
Worn, stuck or broken piston ring
Worn or damaged cylinder or piston
Bent valve, or bent and deteriorated valve seat
Cylinder compression is too high, or engine overheats or
knocks
Carbon deposits on the cylinder head and/or piston crown
Piston noise
Worn cylinder, piston and/or piston ring
*
Worn piston pin
Worn connecting rod small end
hole
low,
or engine is hard to start
and piston pin
kgf*m, 9 Ibfaft)
kgf*m,
29
Ibf*ft)
kgf*m,
14
Ibf*ft)
+
kgf*m,
18
Ibfift)
kgf*m,
26
Ibfift)
kgf*m,
16
Ibf*ft)
kgf*m,
22
Ibf*ft)
kgf*m, 9 Ibf*ft)
Excessive smoke
Worn, stuck or broken piston ring
Worn valve stem seal
Excessive noise
Worn connecting rod big end bearing
Bent connecting rod
Worn crankshaft
Worn transmission bearing
Engine vibration
Excessive crankshaft runout
Apply a locking agent to the threads.
See page
150
"
Apply oil to the threads.
Apply
Apply
Apply
main
11-12.
a
locking agent to the threads.
a
locking agent to the threads.
a
locking agent to the threads.
journal bearing
11-2
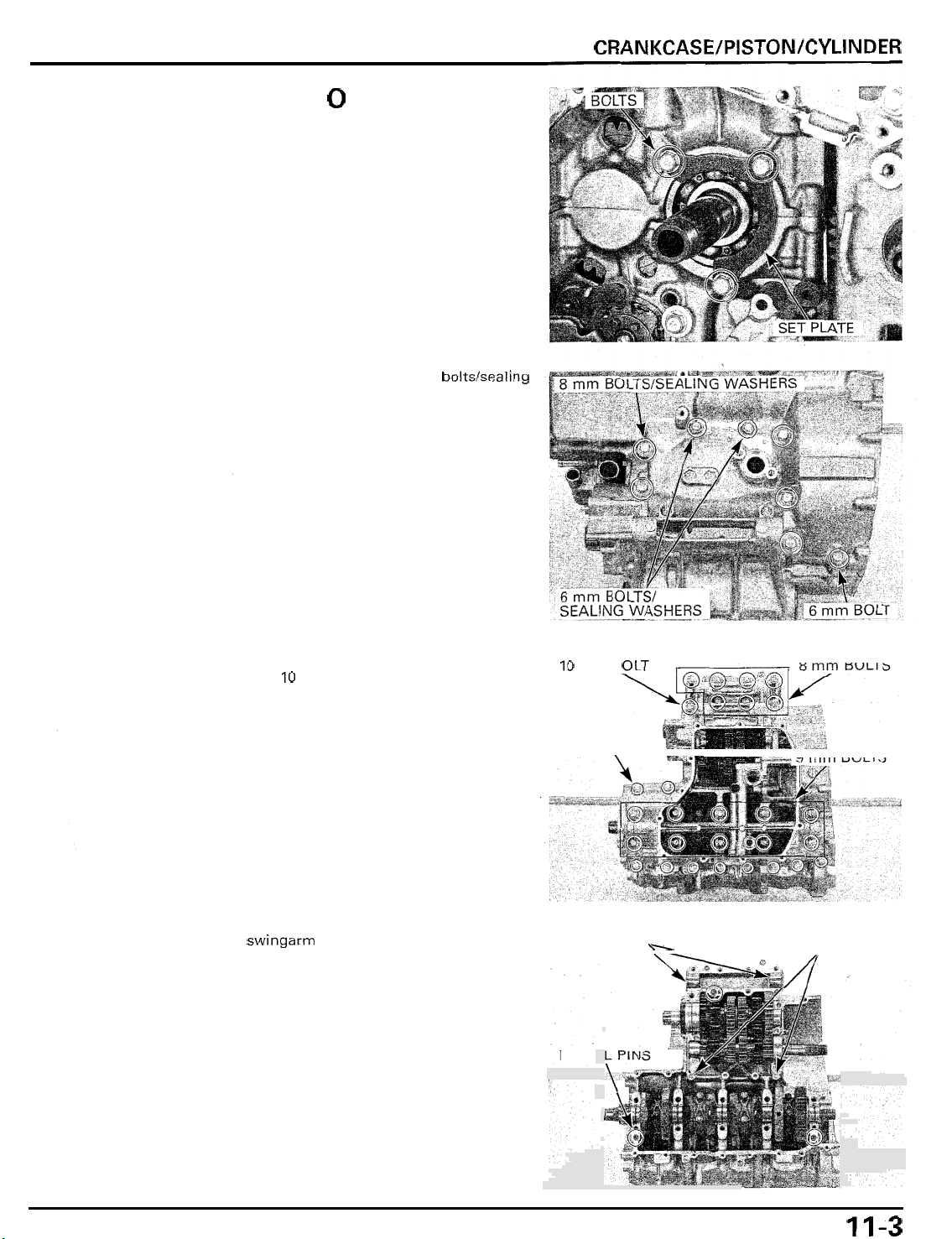
CRANKCASE/PISTON/CY LINDER
CRANKCASE S EPARATI
Refer to Service Information (page
necessary parts before separating the crankcase.
Remove the mainshaft bearing set plate bolts and
plate.
Remove the upper crankcase
washers and 6 mm bolt.
8
N
8
11-1)
mm
for removal
boltskealing
of
6
mm
Remove the lower crankcase
bolts (seven) and
Loosen the ten lower crankcase
cross pattern in two to three steps, then remove the
bolts.
Separate the lower crankcase from the upper
crankcase.
Remove the
oil
orifices.
10
mm
bolt.
swingarm pivot collars, dowel pins and
bolts (ten),
9
mm
bolts in a criss
8
mm
10
mm
B
-
6
mm
BOLTS
\
COLLARS
DOWE
\\
I
8
mm
OIL
ORIFICES
BOLTS
11-3
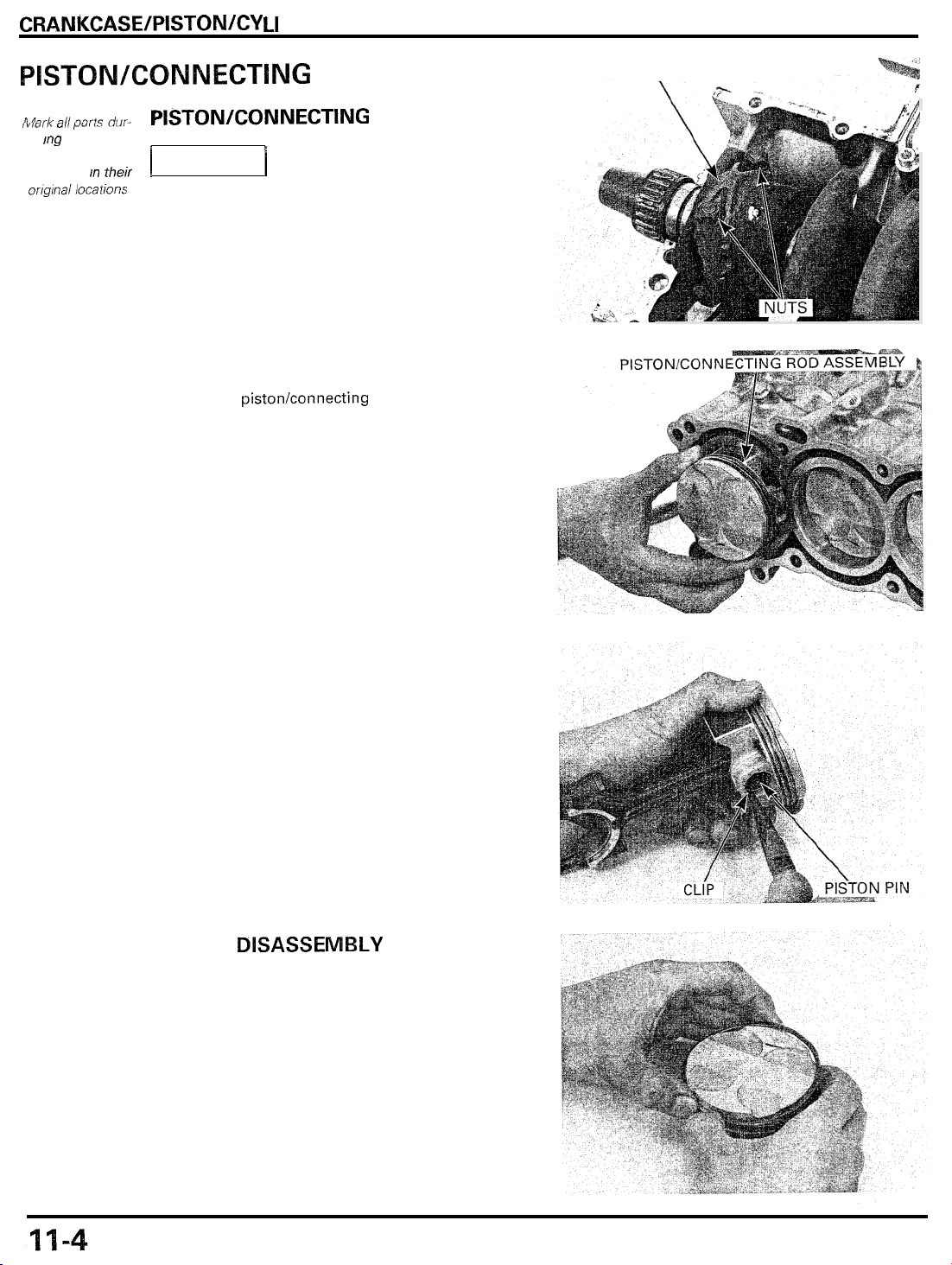
CRANKCASE/PISTON/CY Ll NDER
PISTON/CONMECTING
,yIL(II,
",,
pu,
/ng removal
they can
replaced
or~g/naiiocat/ons
in
.'ISTON/CONNECTING
so
be
I
ther
NOTICE
Do
not interchange the bearing inserts. They must be
installed in their original locations or the correct bear
ing oil clearance may not be obtained, resulting in
engine damage.
Remove the nuts and connecting rod bearing cap.
Remove the
top of the cylinder.
1
pistonkonnecting rod assembly from the
ROD
ROD
BEARING CAP
REMOVAL
-
Do
not damage
the piston rings
during removal.
PISTON
Remove the piston pin clip with pliers.
Press the piston pin out of the piston and remove the
piston from the connecting rod.
PISTON
Remove the piston rings.
REMOVAL
DISASSE