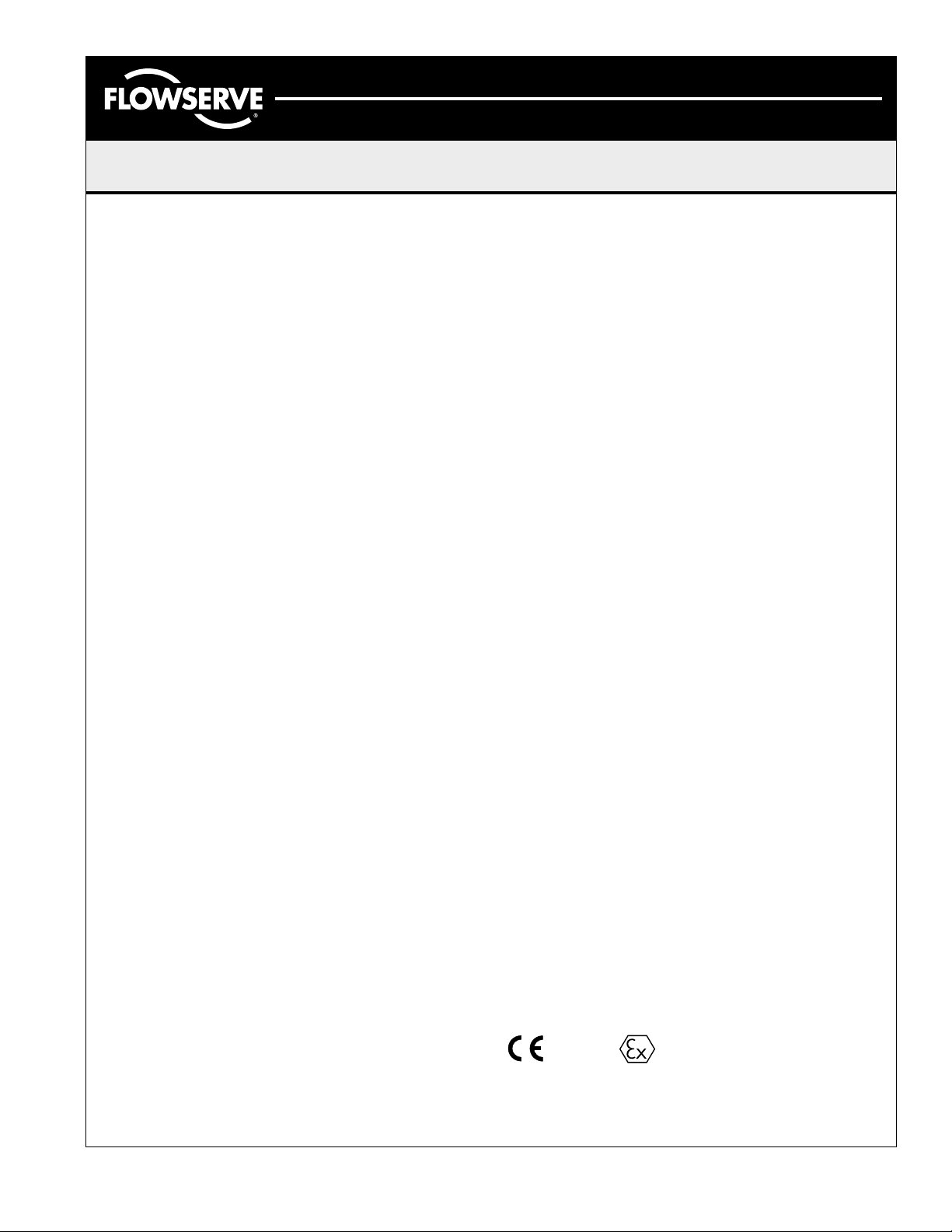
Automax Valve Automation Systems
Installation, Operation and Maintenance Instructions
Flowserve Corporation 1350 N. Mountain Springs Parkway 1978 Foreman Dr.
Flow Control Division Springville, Utah 84663-3004 Cookeville, TN 38501
www.flowserve .com Phone: 801 489 8611 Phone: 931 432 4021
UltraSwitch™ XL, GL, PL
Description
Automax UltraSwitch™ limit switch enclosures provide
local and remote position indication for automated
valves. They generally feature a Pharos™ visual indicator
with “red=closed” and “green=open” for intuitive local
position determination. The UltraSwitch™ is available
with a number of limit switch options for remote indication in a variety of electrical applications. They may also
be used as a junction box for direct installation of
solenoid valves.
Installation
UltraSwitches may be installed with a variety of mounting
hardware. For best results, specify the NAMUR shaft
option and NAMUR mounting hardware (when possible).
These options allow direct coupling to actuators without
couplings, reducing deadband.
Simply bolt bracket to actuator and UltraSwitch™
to bracket, leaving bolts finger tight. For NAMUR
applications the UltraSwitch™ shaft features an integral
alignment pin. This pin must engage the tapped hole in
your actuator shaft. For non-NAMUR applications, make
sure to properly install a coupler between UltraSwitch™
and actuator. Once the UltraSwitch™ is installed with
fasteners loosely tightened, stroke your actuator
two or three times to align the bracket. Then tighten
all fasteners.
Special Hazardous Location Instructions
UltraSwitch™ XL Series enclosures are explosion proof
which allows them to be used in most Division 1 and 2
hazardous locations. You must install a conduit sealing
fitting within 18 inches of the enclosure to meet NEC
regulations. The AXL series does feature internal potting
wells. Units provided with factory-sealed leads do not
require external sealing fittings.
UltraSwitch™ PL and GL series enclosures are designed
to meet NEMA 4 specifications, but may be used in
Division 2 hazardous locations when supplied with
hermetically sealed magnetic proximity switches. For
Division 2 applications utilizing hermetically sealed
switches, conduit seals are not required. See nameplate
information to verify hazardous location suitability.
Wiring Instructions
UltraSwitch™ enclosures feature prewired switches. All
user connections are made at a numbered terminal strip.
A wiring diagram is located inside the cover and indicates
which terminal numbers correspond to switch contacts:
normally open, normally closed common, etc. Simply follow
the wiring diagram and electric code to connect switches
to your system.
switches, the top switch (top and third switches for
4-switch versions) should only be used to indicate the
clockwise position: the bottom switch (second and fourth
switches for 4-switch versions) should only be used to
indicate the counterclockwise position. Any deviation from
these settings may result in erratic indication.
Solenoids may also be wired through the UltraSwitch™
enclosure. At least two auxiliary terminals are included as
standard. A ground screw is also included. Simply wire the
solenoid to auxiliary terminals, then connect power leads to
the opposite terminal side. Be sure to properly ground the
solenoid at provided ground terminal. Note: PL series
enclosures are non-metallic: be sure to connect a ground
wire to this terminal. When two metal conduits are used
with the APL series, an external grounding strap must be
used to connect to them.
UltraSwitch™ XL and PL series enclosures include two 3/4"
conduit entries. GL series enclosures include two 1/2" entries.
Be sure to follow the National Electric Code regulations for
rigid conduit, or cable systems as applicable.
CAUTION: Substitution of components may impair suitability for Zone 2 Increased Safety.
Do not disconnect equipment unless power has been
switched off or the area is known to be non-hazardous.
Cleaning this housing by rubbing should be done in a nonhazardous area.
DEMKO 02 ATEX 130948X
0518 II 2 G EEx me II T4-T6
-40°C ≤ Tamb ≤ +55°C, T6
-40°C ≤ Tamb ≤ +70°C, T5
-40°C ≤ Tamb ≤ +80°C, T4
Note: for all magnetically tripped proximity
FCD AXAIMO0031-00 (LML0005-1) (AUTO-31) 7/04
©
2004, Flowserve Corporation, Printed in USA
Page 1 of 2
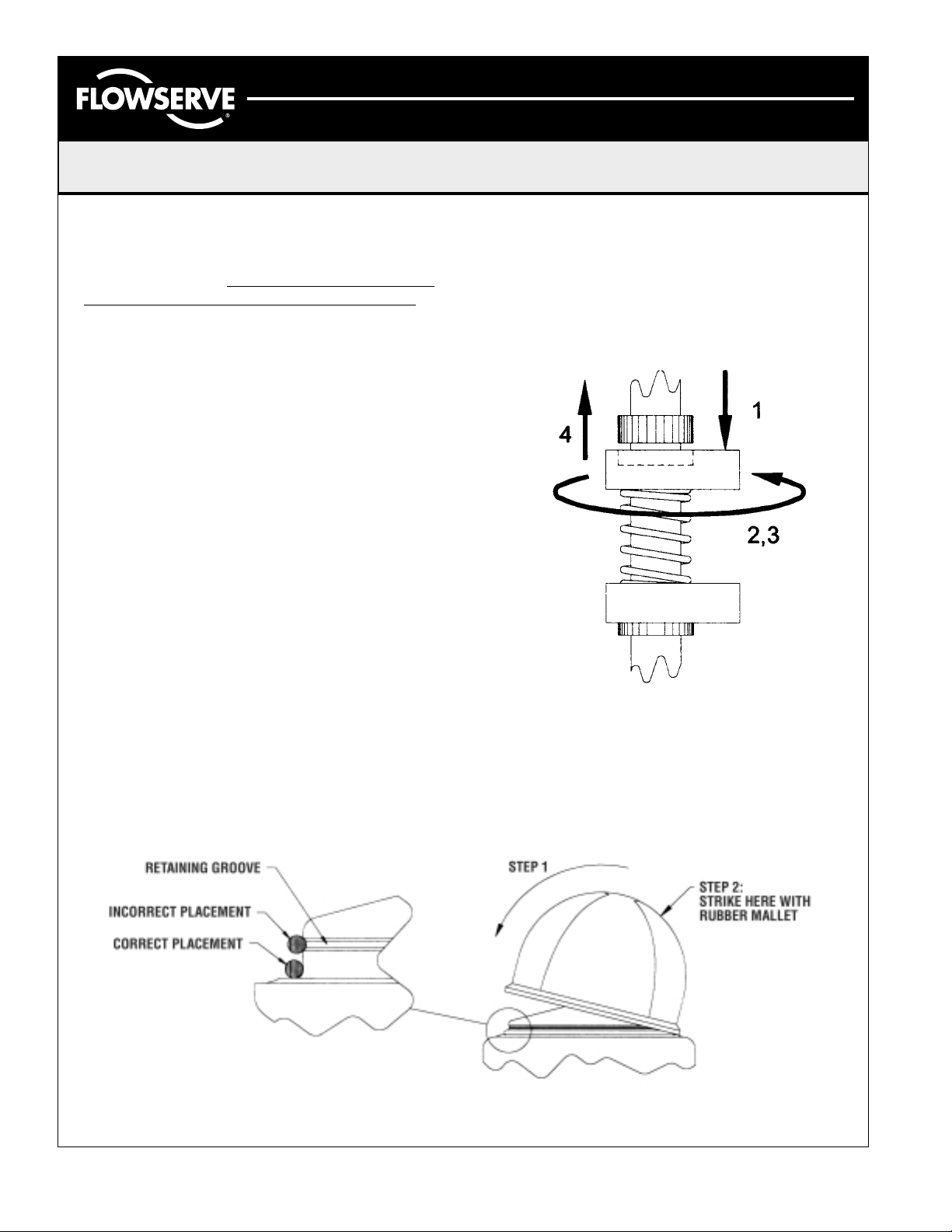
Automax Valve Automation Systems
Installation, Operation and Maintenance Instructions
Flowserve Corporation 1350 N. Mountain Springs Parkway 1978 Foreman Dr.
Flow Control Division Springville, Utah 84663-3004 Cookeville, TN 38501
www.flowserve .com Phone: 801 489 8611 Phone: 931 432 4021
Adjusting Limit Switches
UltraSwitch™ enclosures feature quick-set cams which
are used to trip the limit switches. These cams are easily
adjusted without tools.
Caution: disconnect power before
removing cover when installed in hazardous locations.
Remove cover and set aside. Rotate actuator/valve to full
clockwise (CW) position. Adjust cam(s) associated with CW
as follows:
1. Push or pull cam against spring to disengage it
from splines.
2. Rotate cam CW breaking contact with switch
(or moving magnet away from switch).
3. Continue rotating cam CW just until switch trips.
4. Release cam and reengage it with splines.
Rotate actuator/valve to full counterclockwise (CCW)
position. Adjust cam(s) associated with CCW as
described in steps 1 through 4, except rotate cam(s) CCW.
Note: factory setting is top switch = CW (closed), second
switch = CCW (open), third switch = CW, and fourth
switch = CCW.
Adjusting Pharos™ Position Indicator
Pharos visual indicators are easily adjusted to match
the dome’s clear windows to the rotor’s red and green
quadrants. Simply pry upward under dome “flange” with a
large, flat-bladed screwdriver to remove. Make sure o-ring
is fully seated against the flat dome sealing surface, not in
the dome retaining groove, as shown. Then install dome in
a tilted fashion, engaging one of the dome locking tabs in
the dome retaining groove. Make sure dome windows line
up with rotor quadrants. Finally, using a rubber mallet,
strike dome as shown to engage all locking tabs.
FCD AXAIMO0031-00 (LML0005-1) (AUTO-31) 7/04
©
2004, Flowserve Corporation, Printed in USA
Page 2 of 2