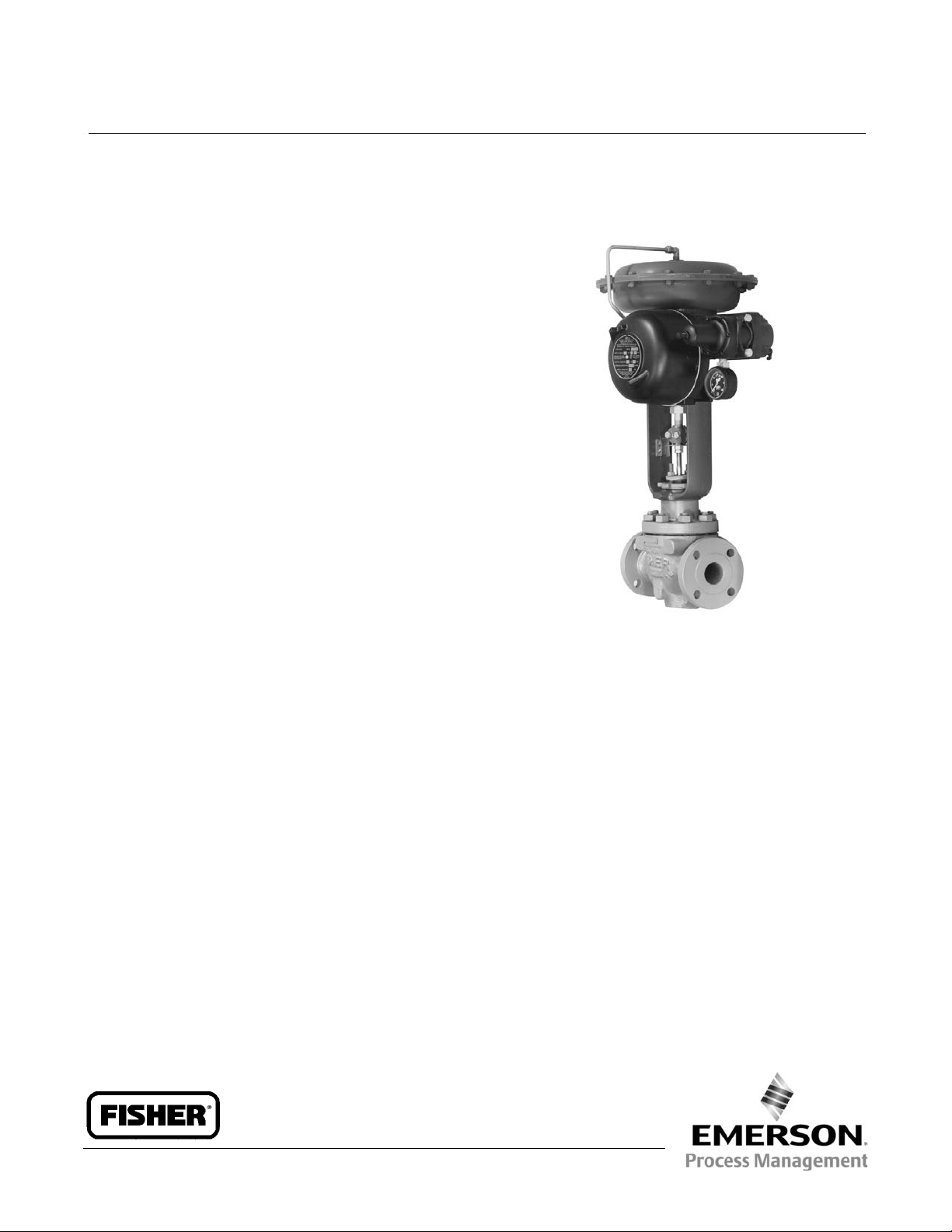
Product Bulletin
546NS Transducer
D103603X012
62.1:546NS
April 2015
Fisherr 546NS Electro‐Pneumatic Transducer
The Fisher 546NS transducer receives a direct‐current
input signal and use a torque motor, nozzle‐flapper,
and pneumatic relay to convert the signal to a
proportional pneumatic output signal. Nozzle
pressure, which operates the relay, is also piped to the
torque motor feedback bellows. This provides a
comparison between input signal and nozzle pressure
and reduces errors in nozzle pressure.
The transducer can be mounted on a pneumatic
diaphragm control valve actuator to provide accurate
operation of the valve. The integrated high‐capacity
pneumatic relay eliminates the need for additional
boosters or relays for operation of control valves.
The transducer also can be used to provide stable
operation when its output signal is transmitted to
small terminal volume chambers such as control
bellows in pneumatic valve positioners.
Features
n Vibration Resistance—High natural frequency of
torque motor moving parts results in negligible
vibration influence. Meets typical seismic
requirements for nuclear service.
n Easy Adjustment—Screwdriver adjustments for span
and zero are conveniently located and have arrows
indicating rotation to increase settings (as shown in
figure 1).
Fisher 546NS Transducer Mounted on
657 Pneumatic Diaphragm Actuator
W2115
n Field‐Reversible Action—No additional parts
required to reverse action.
n Simple Relay Removal—Integrated pneumatic relay
is mounted outside case and can be removed
without disturbing electrical or pressure
connections or impairing explosion safety.
www.Fisher.com
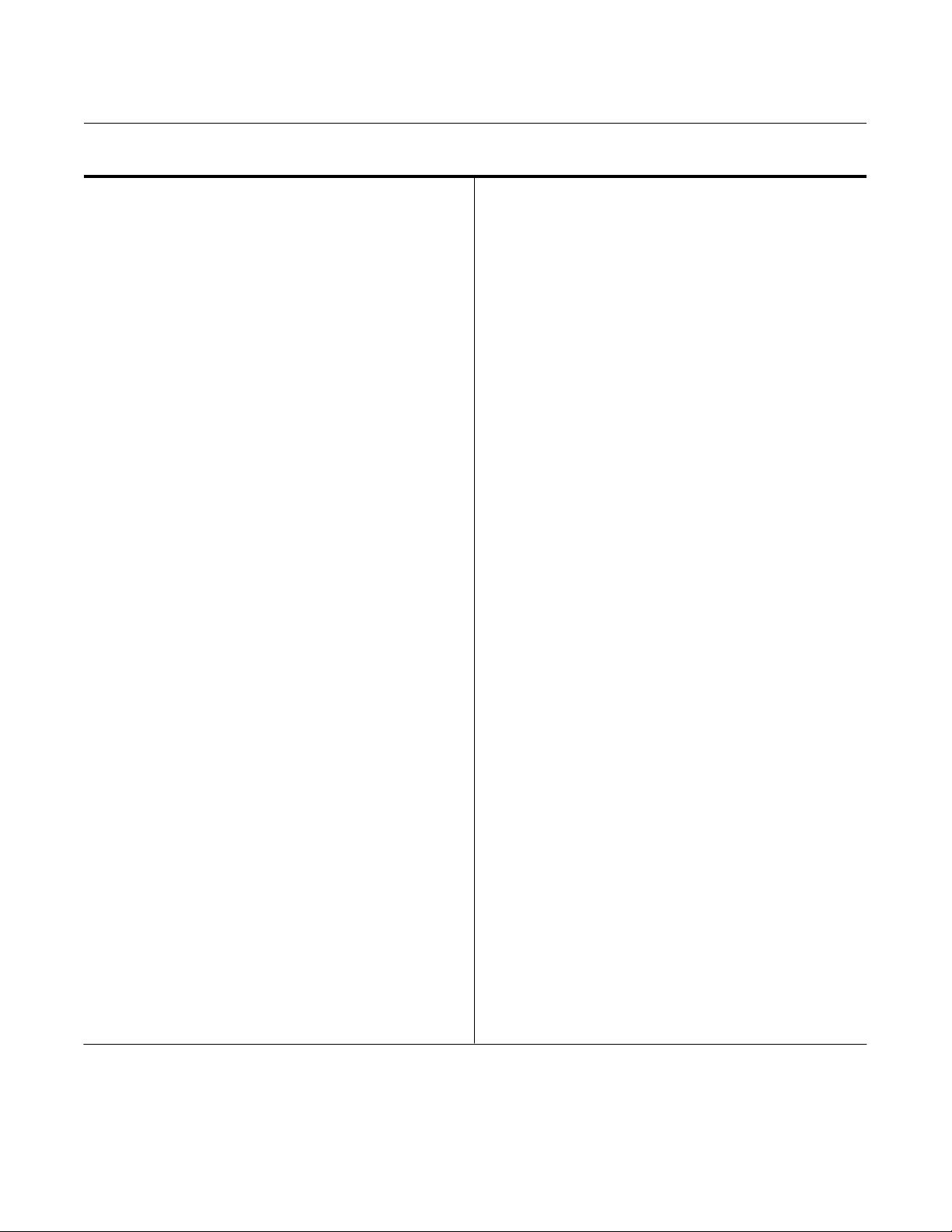
Product Bulletin
62.1:546NS
April 2015
Specifications
Available Configuration
Electro‐pneumatic signal transducer with
explosion‐proof case and cover, with EPDM
elastomers for use in elevated temperature and
radiation environments
The 546NS can be ordered
Fisher 67CFR filter regulator. The 51 mm (2 inch)
supply pressure gauge mounted on the regulator may
be
J 0 to 30 psig or J 0 to 60 psig range
Input Signals
J 4 to 20 mA DC, J 10 to 50 mA DC, or J two‐way
split range using either half of one of the standard
input signal spans
Internal Resistance of Torque Motor
4 to 20 mA DC Input Signal: 176 ±10 ohms
10 to 50 mA DC Input Signal: 90 ±10 ohms
J with or J without a
546NS Transducer
D103603X012
Performance
Actuator Loading Time: see figure 3
Reference Accuracy
Independent Linearity: ±0.50% of output signal span
Open Loop Gain: 26
Frequency Response: Gain is attenuated 3 dB at 20 Hz
with transducer output signal piped to a typical
instrument bellows with 305 mm (12 inch) of 1/4 inch
tubing
Electromagnetic Interference (EMI): Tested per IEC
61326‐1 (Edition 1.1). Meets emission levels for Class
A equipment (industrial locations) and Class B
equipment (domestic locations). Meets immunity
requirements for industrial locations (Table A.1 in the
IEC specification document). Immunity performance
shown in table 1.
Operative Ambient Temperature Limits
-40 to 66_C (-40 to 150_F)
(4)
(5)
: ±0.75% of output signal span
(1)
Output Signals
Ranges:
J 0.2 to 1.0 bar (3 to 15 psig), J 0.4 to 2.0 bar
(6 to 30 psig)
Action: Field reversible between
J reverse
Supply Pressure
(1)
J direct and
Recommended: 0.3 bar (5 psi) higher than upper
range limit of output signal
Maximum: 3.5 bar (50 psig)
Average Steady‐State Air Consumption
(2)(3)
0.44 m3/hr (16.5 scfh) at 1.4 bar (20 psi) supply
pressure
Maximum Output Air Capacity
At 1.4 bar (20 psig) Supply Pressure:
3
12.9 m
At 2.4 bar (35 psig) Supply Pressure:
18.5 m
/hr (480 scfh)
3
/hr (690 scfh)
(2)
Electrical Classification
Hazardous Area:
CSA—Explosion‐proof, Dust Ignition-proof, Div 2
FM—Explosion‐proof, Dust Ignition‐proof,
Non‐incendive
Refer to tables 2 and 3 for specific approval
information
NEMA 3R, CSA Enclosure 3
NEMA 3R mounting orientation requires vent location
to be below horizontal.
Adjustments
Zero and Span Adjustments: Screwdriver adjustments
located inside case (see figure 1)
Connections
Supply Pressure: 1/4 NPT internal located on side of
case (located on filter‐regulator if a 67CFR is mounted
to transducer)
Output Pressure: 1/4 NPT internal located on side of
case
Vent: 1/4 NPT internal with screen located on relay
Electrical: 1/2 NPT internal located on bottom of case
-continued-
2
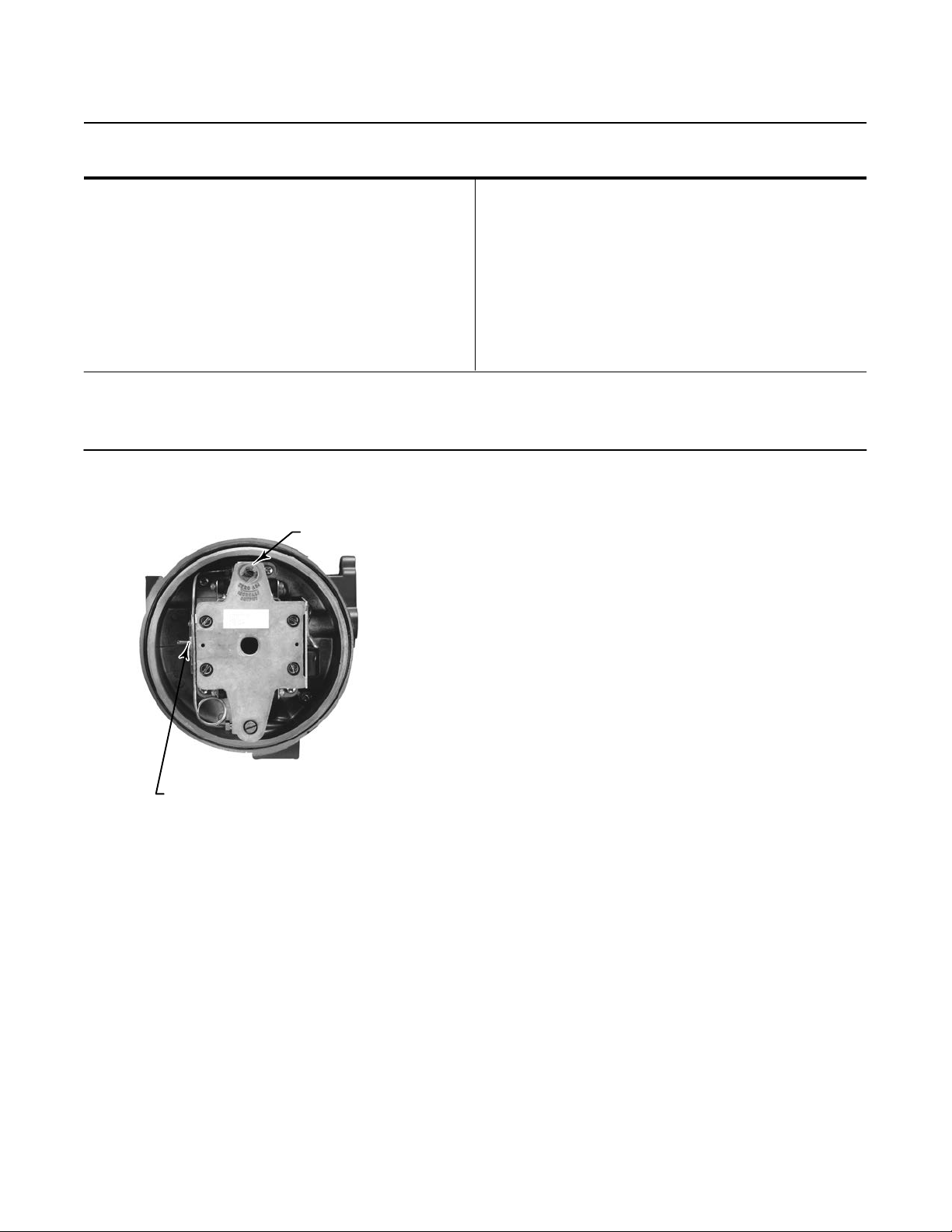
Product Bulletin
546NS Transducer
D103603X012
62.1:546NS
April 2015
Specifications (continued)
Construction Materials
Case and Cover: Aluminum
O‐Rings: EPDM
Flame Arrestors: Stainless steel
Supporting Bracket/Torsion Member: Stainless steel
Magnets: Alloy steel
Nozzle: Stainless steel
Feedback Bellows: Brass
Relay Body: Aluminum
Relay Restriction: Aluminum/Stainless steel
NOTE: Specialized instrument terms are defined in ANSI/ISA Standard 51.1 - Process Instrument Terminology.
1. The pressure/temperature limits in this document and any applicable standard or code limitation should not be exceeded.
2. Normal m
3. Average flow rate determined at 12 mA and 0.6 bar (9 psig) output.
4. Performance values are obtained using a 546 transducer with a 4 to 20 mA DC input signal and a 0.2 to 1.0 bar (3 to 15 psig) or a 0.4 to 2.0 bar (6 to 30 psig) output signal. Ambient temperature
is 24_C (75_F). A transducer with other input or output signals may exceed these values.
5. Reference accuracy includes the effects of non-linearity, hysteresis, and deadband per SAMA Standard PMC 20.1-1973.
3
/hr-‐Normal cubic meters per hour (0_C and 1.01325 bar, absolute). Scfh‐‐Standard cubic feet per hour (60_F and 14.7 psia).
Relay Diaphragm: EPDM/Nomex
Relay Valve Plug and Seat Ring: Brass
Mounting
Mounting parts are available for
actuator mounting,
mounting, or
J pipestand (2 inch nominal)
J surface mounting
Approximate Weight
4.1 kg (9 lb)
R
.
J control valve
Figure 1. Zero and Span Adjustments (Cover
Removed)
W5391
SPAN ADJUSTMENT
ZERO ADJUSTMENT
Principle of Operation
Refer to figure 2, and assume that the transducer is
direct acting. As the DC milliamp signal increases, so
does the magnetic field around the coils. This results in
an increased magnetic attraction between the
armature and the pole pieces. The armature rotates
slightly clockwise to cover the nozzle, increasing
pressure in the nozzle, the upper chamber of the relay,
and the feedback bellows. Increased nozzle pressure
and increased pressure in the upper chamber of the
relay cause the relay supply port to open, increasing
the output pressure to the actuator and the control
valve. At the same time, the increased pressure in the
feedback bellows acts to move the armature back to
the equilibrium position. In this way, the new nozzle
pressure is compared to the DC input signal by the
force balance principle.
As the DC input signal decreases, magnetic attraction
is reduced and the armature rotates slightly in the
counterclockwise direction to uncover the nozzle.
Decreased nozzle pressure and decreased pressure in
the upper chamber of the relay cause the relay exhaust
port to open and allow output pressure to bleed to
atmosphere. Pressure to the control valve is reduced
until equilibrium is attained.
Reverse‐acting transducers operate in a similar
manner except that when the DC input signal
increases, pressure to the actuator and control valve
decreases.
3