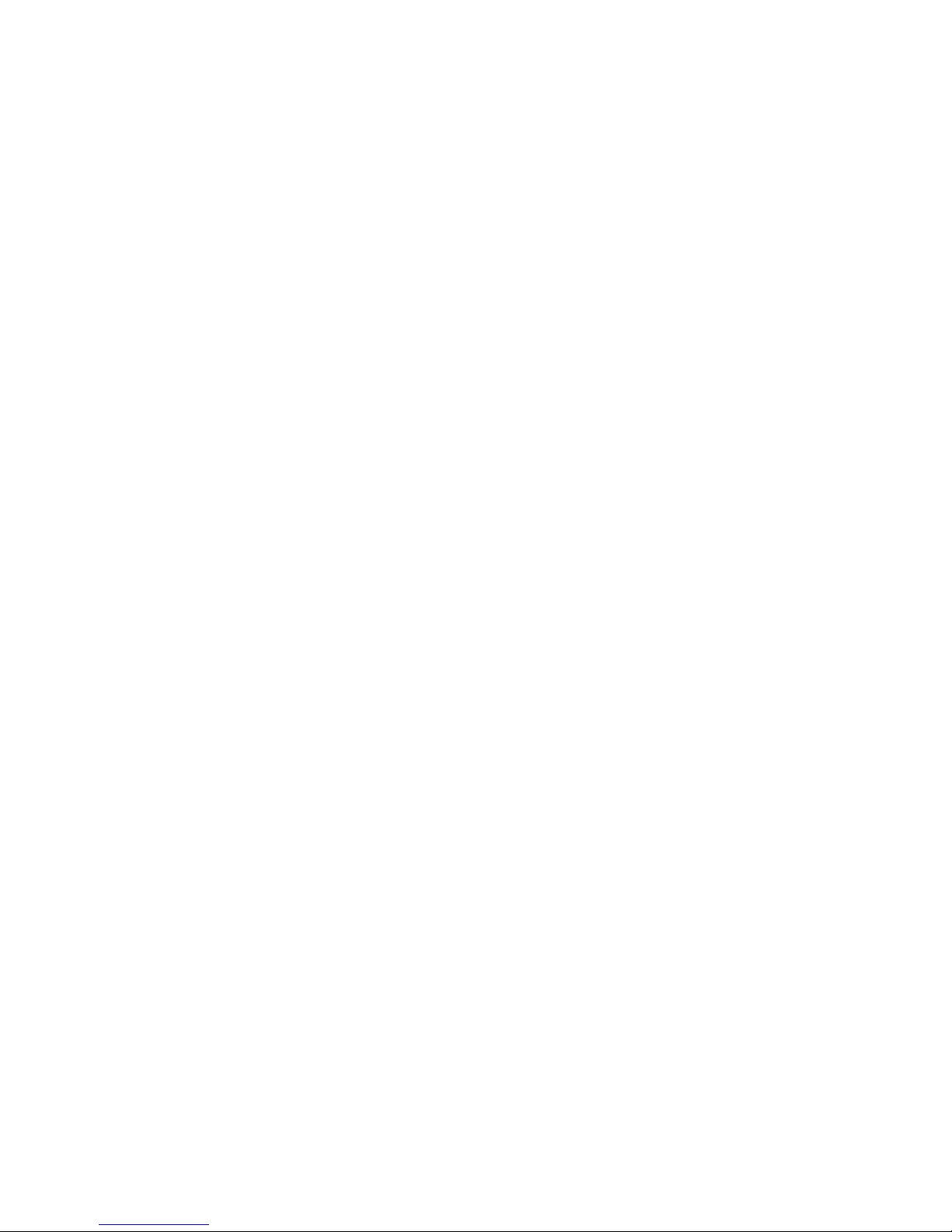
2
The information in this manual was, to the best of our knowledge,
correct when it went to press and Simrad or B&G cannot be liable for
any inaccuracies or omissions. There may also be differences
between the specifications in the manual and the product as a result
of ongoing development for which we accept no liability.
This precision engineered product was designed and manufactured in
the United Kingdom.
Please keep this manual in a safe place
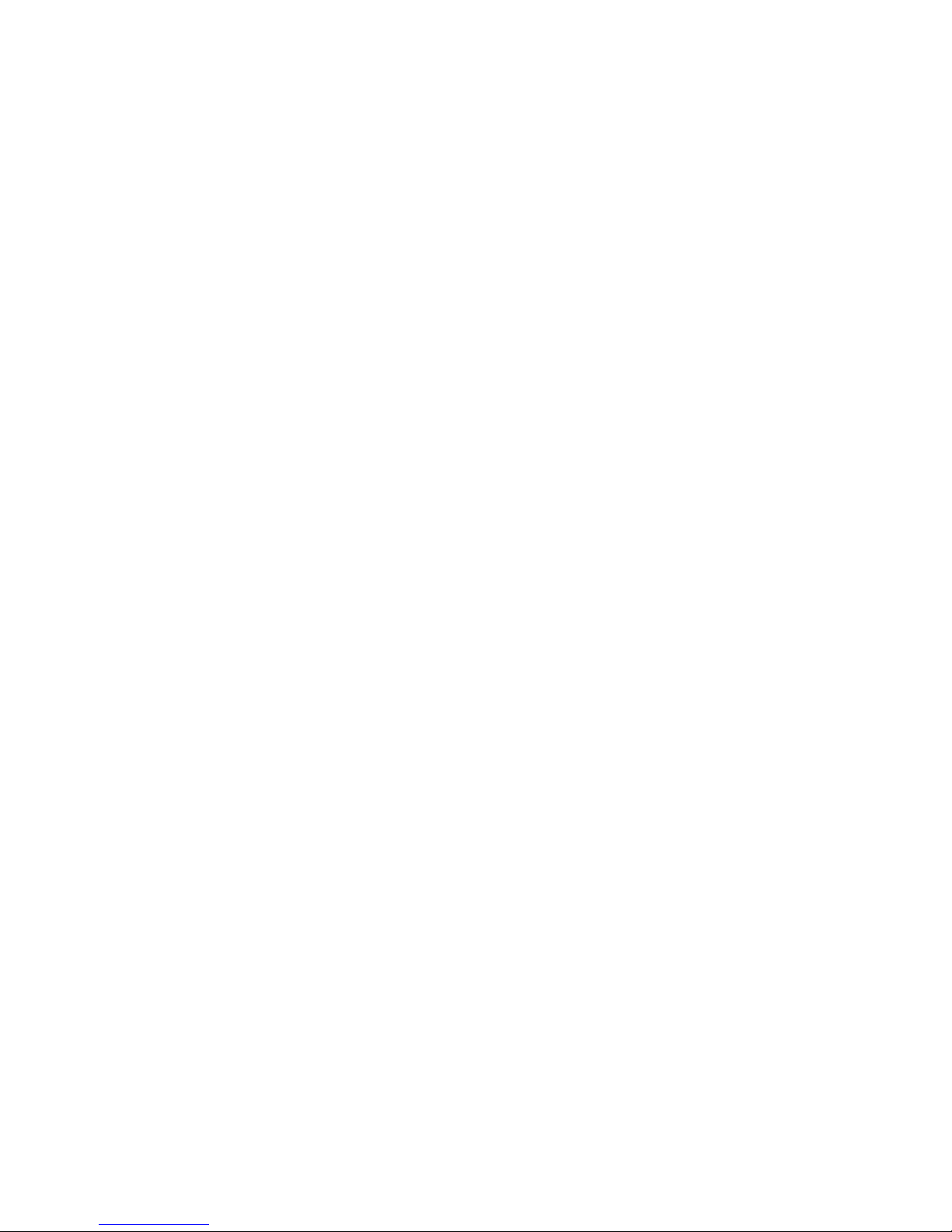
3
CONTENTS
Important Safety Information
Compliance Statement
Emergency Quick Release
Emergency Steering
Description
Performance
• Technical Data
Dimensions
Actuator Selection
Location
Tiller bolt
Mounting Foot
Quadrant
Considerations
Coil Connections
Maintenance
Servicing
Fault finding
Hydraulic Fluid
Commissioning
Dismounting the unit from its base
Dimensions for Mounting Foot
General Information
Contact Details
End of Life Disposal
Page 4
5
6
7
8
9
10
11
12
13
15
16
17
18
19
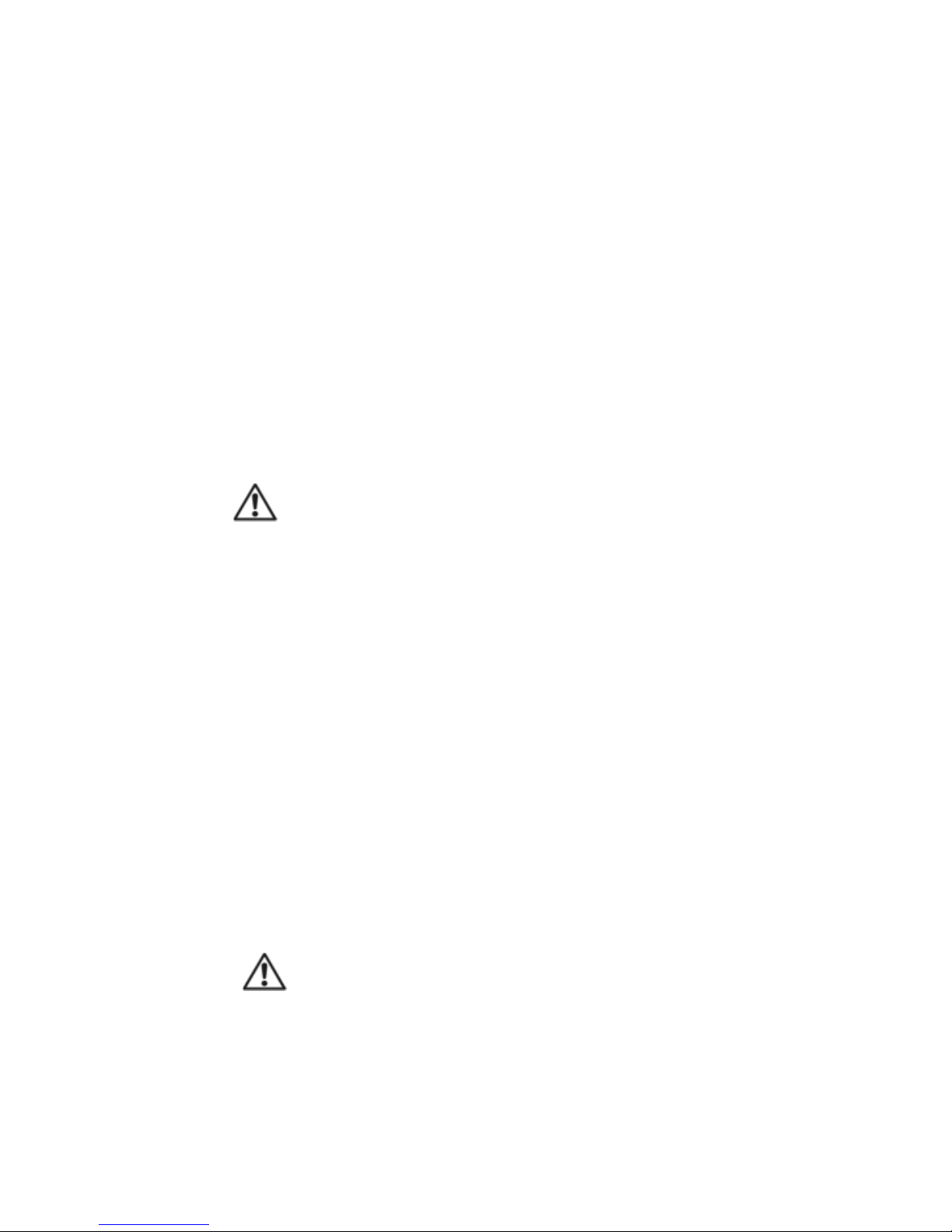
4
IMPORTANT SAFETY INFORMATION
Failure to install and maintain this equipment in accordance with the
instructions contained in this Manual could result in damage or injury.
This equipment must be installed and maintained by a person who is
qualified to do so. This equipment is only for use with marine autopilots
within the limitations stated in the following pages. Autopilot steering
systems are navigational aids and the user must still maintain a permanent watch.
This equipment meets the latest EMC (Electromagnetic Compatibility)
standards required for use in the marine environment.
In order to ensure conformance and to prevent interference with
electronic systems the unit must be properly bonded to earth and the
supply cables screened.
Caution!
In operation this unit can rotate the vessels wheel rapidly.
Keep clear of the wheel when this unit is engaged to avoid entrapment.
Beware of hot motor and solenoid components and the risk of
entrapment from moving parts.
Do not flash test.
COMPLIANCE STATEMENT
The RAM T1 & T2 complies with CE under directive 2014/30/EU. The
relevant Declaration of Conformity is available in the following websites
under model documentation section:
www.simrad-yachting.com or www.bandg.com
Complies with the requirements of level 2 devices of the Radio
communications (Electromagnetic Compatibility) standard 2017.
Warning!
The user is cautioned that any changes or modifications not expressly
approved by the party responsible for compliance could void the user’s
authority to operate the equipment.

5
EMERGENCY QUICK RELEASE
In the unlikely event of failure of the actuator a quick release R-Clip is fitted
to the tiller bolt which secures the actuator to the steering quadrant.
Pull the red tab to release the R-Clip and then manually lift the actuator
clear of the steering quadrant.
EMERGENCY STEERING - PRIMARY STEERING FAILURE
If the primary steering fails it may be possible to steer the boat via the
autopilot controls.
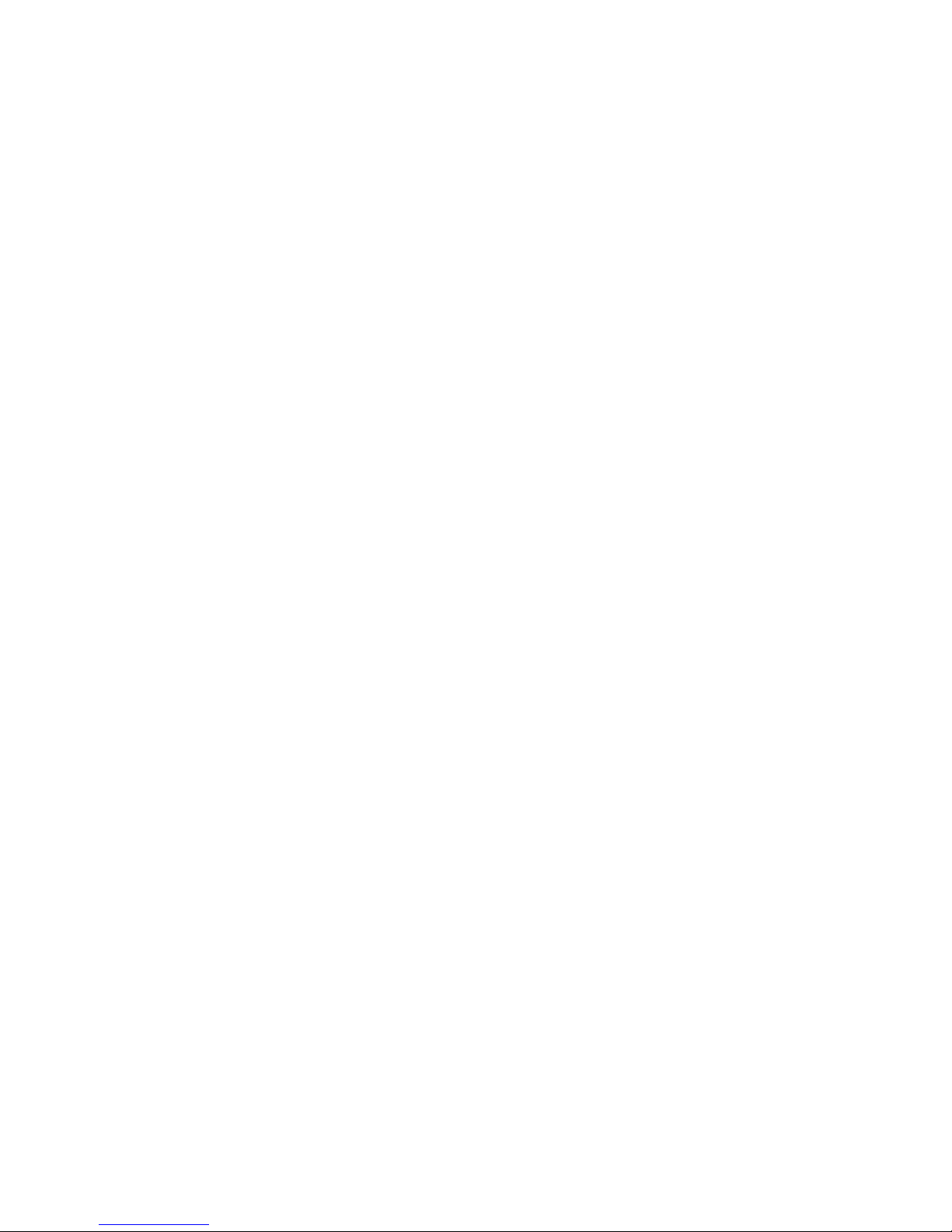
6
DESCRIPTION
The RAM T1/T2 Hydraulic linear actuator combines a cylinder, pump,
motor, clutch and reservoir in a pre-filled, sealed unit. Designed to be
used on vessels fitted with mechanical primary steering that can be back
driven.
When the clutch is disengaged the cylinder is free and moves with the
primary steering. To operate the unit in autopilot mode the course computer energises the clutch solenoid coil and runs the bi-directional motor
to extend and retract the ram.
Internal relief valves protect the unit and its mountings from rudder
strikes, grounding etc.
PERFORMANCE
Hard over time Typical max thrust
seconds at 5 kg kg
RAM T1 13 700
RAM T2 9 700