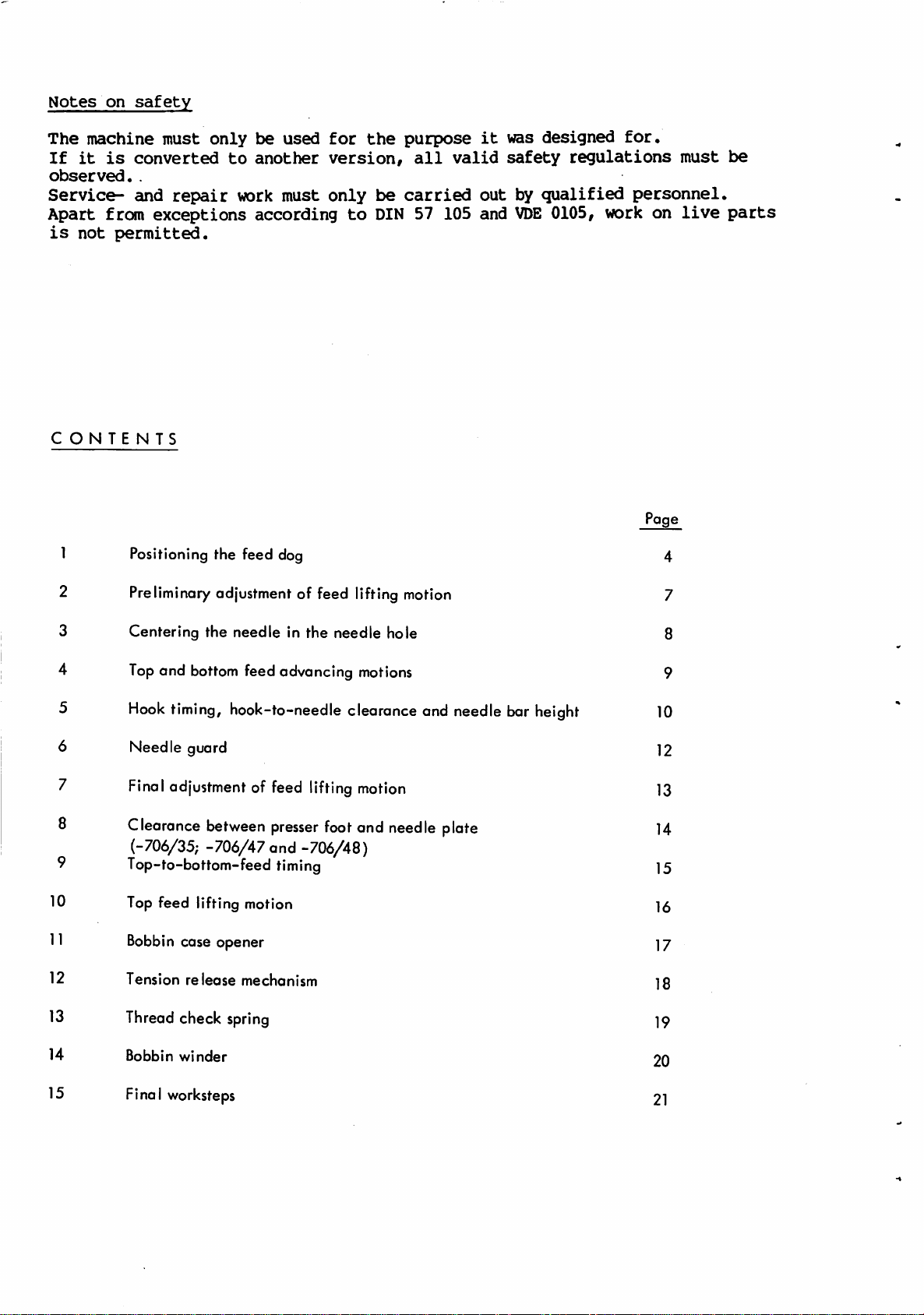
Notes
The
machine
If
it
observed.
Service-
Apart
is
not
CONTENTS
on
safety
is
converted
.
and
from
exceptions
permitted.
must
repair
only
to
be
used
another
work
must
according
for
the
version,
only
be
to
DIN
purpose
all
valid
carried
57 105 and
it
out
was
designed
safety
by
qualified
VDE
0105, work on
for.
regulations
personnel.
Page
must
live
be
parts
11
12
10
1
2
3
4
5
6
7
8
Positioning the feed dog
Preliminaryadjustment of feed lifting
Centering the needle in the needle hole
Topand bottom feed advancing motions
Hook
timing,
hook-to-needle clearance and
Needle guard
Final adjustment of feed lifting
Clearance
between
presser
foot
motion
and
needle
motion
needle
plate
bar
height
4
7
8
9
10
12
13
14
(-706/35; -706/47and -706/48)
9
Top-to-bottom-feed timing
Top feed lifting motion
Bobbin
Tension
case opener
release
mechanism
15
16
17
18
13
14
15
Threadcheck
Bobbin
winder
Final worksteps
spring
19
20
21
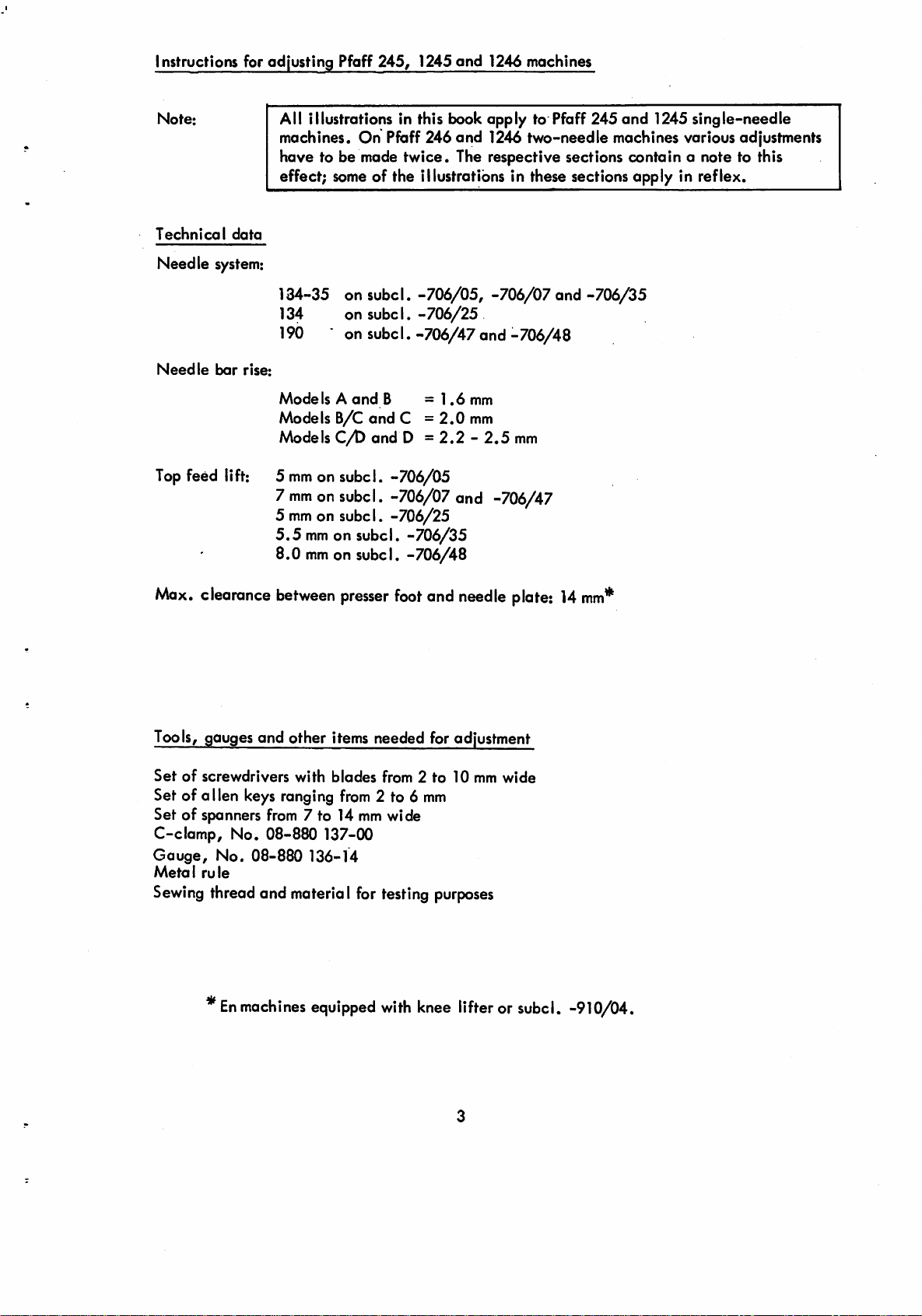
Instructions for adjusting Pfaff
245,
1245
and
1246 machines
Note:
Technical
Needle
Needle
Top
feed lift: 5
data
system:
bar
rise:
All illustrations in this book apply to Pfoff 245 and 1245 single-needle
machines. On Pfaff 246 and 1246 two-needle machines various adjustments
have to be mode
effect;
some
twice.
The respective sections contain a note to this
of the illustrations in these sections apply in reflex.
134-35 on subcl. -706/05, -706/07 and -706/35
134 on subcl. -706/25
190
ModelsAand
Models B/C and C =
Models C/D and D =
7
5
5.5
8.0
• on subcl.-706/47 and-706/48
B
=1.6
mm
2.0
mm
2.2-2.5
mm
on subcl. -706/05
mmonsubcl.
mm
on subcl. -706/25
mm
on subcl. -706/35
mm
on subcl. -706/48
-706/07
and
mm
-706/47
Max.
clearance
between
presser
foot
and
needle
plate:14mm*
Tools, gauges and other items needed for adjustment
Setofscrewdrivers
Set of alien keys ranging
Set of spanners from 7 to 14
C-clomp, No. 08-880 137-00
Gauge,
Metal
Sewing
No.
rule
thread and material for testing
En
machines equipped with knee lifter or subcl. -910/04.
08-880
with
136-14
blades
from
mm
from 2to10 mm
2 to 6
mm
wide
purposes
wide
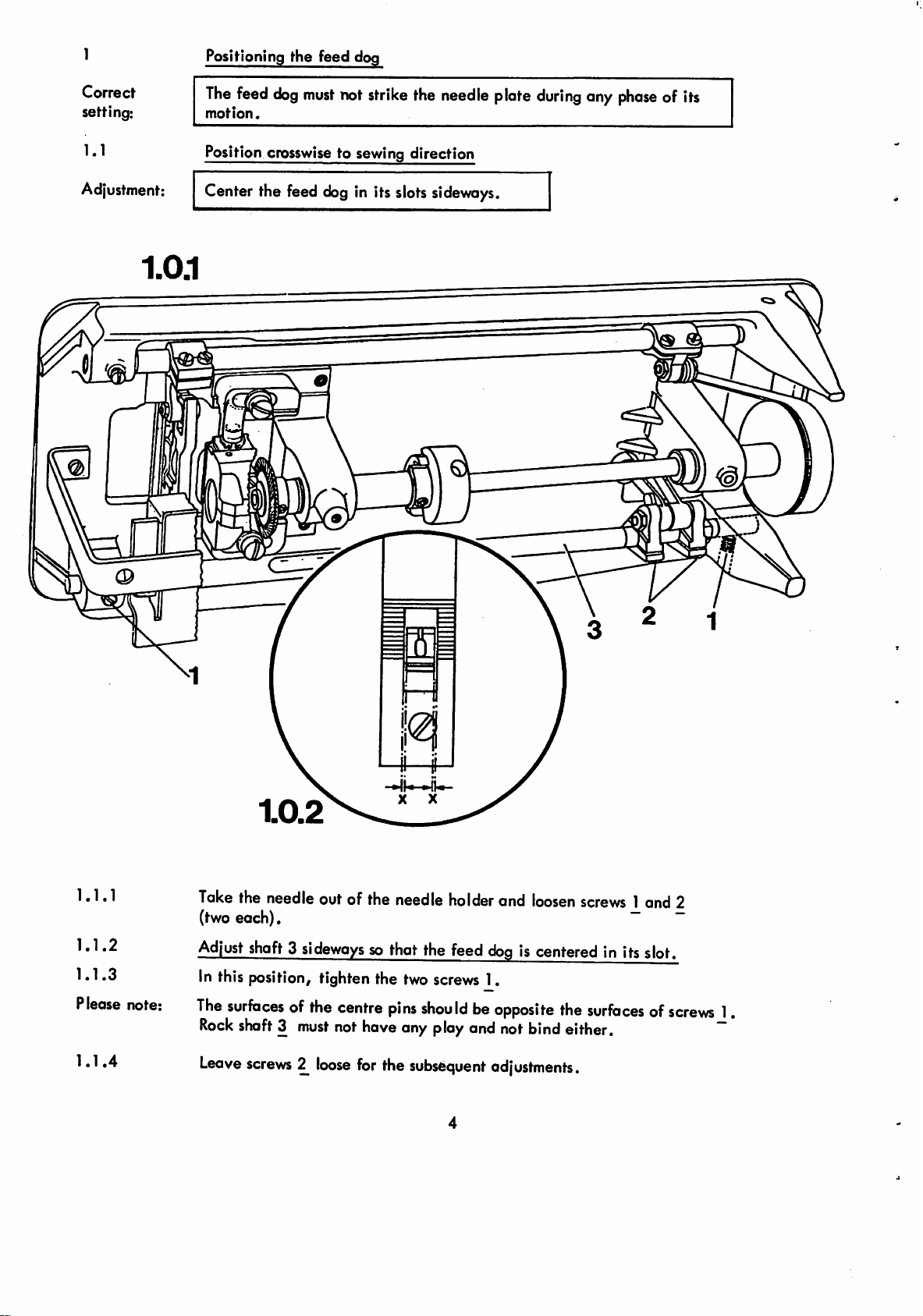
1
Positioning the feed dog
Correct
setting:
1.1
Adjustment:
The
feed
dog
must
not
strike
the
needle
motion.
Position crosswise to sewing direction
Center the feed
dog
in its
slots
sideways.
plate
during
any
phaseofits
1.1.1
1.1.2
1.1.3
Please
1.1.4
note:
Take
the
needle
(two each). ~ ~
Adjust
In this
The
Rock
Leave
shaft3sidewayssothat the
|X}sition,
surfacesofthe
shaft3must
screws^loose
outof the
tighten the
centre
not
have
for
the
needle
holder
feed
two
screws
pins
shouldbeopposite
any
play
and
subsequent
and
loosen
screws
dogiscentered
1.
the
not
bind
either.
adjustments.
1and 2
in itsslot.
surfacesofscrews
1
""
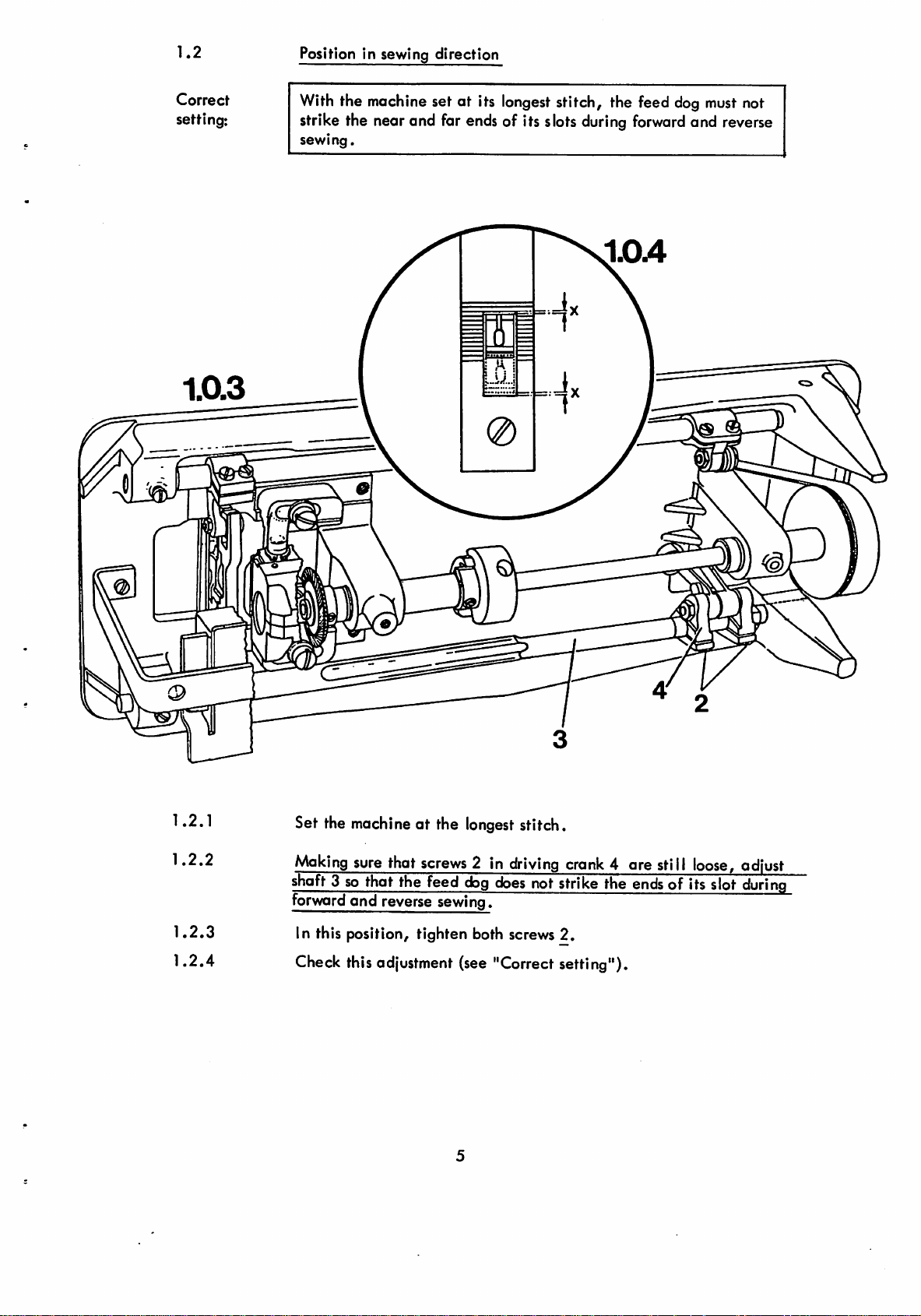
1.2
Position in sewing direction
Correct
setting:
With
the
machine
set at its
longest
stitch, the feed
strike the near and far ends of its slots
sewing.
0
during
forward
dog
must
and reverse
not
1.2.1
1.2.2
1.2.3
1.2.4
Set the machine at the longest stitch.
Making
shaft3 so that the feed
forward
In this position, tighten both screws 2.
sure
that
screws
2 in
dog
and reverse sewing.
driving
does
notstrike the
crank
Check this adjustment (see "Correct setting").
4 ore still
ends
of its slot
loose,
adjust
during
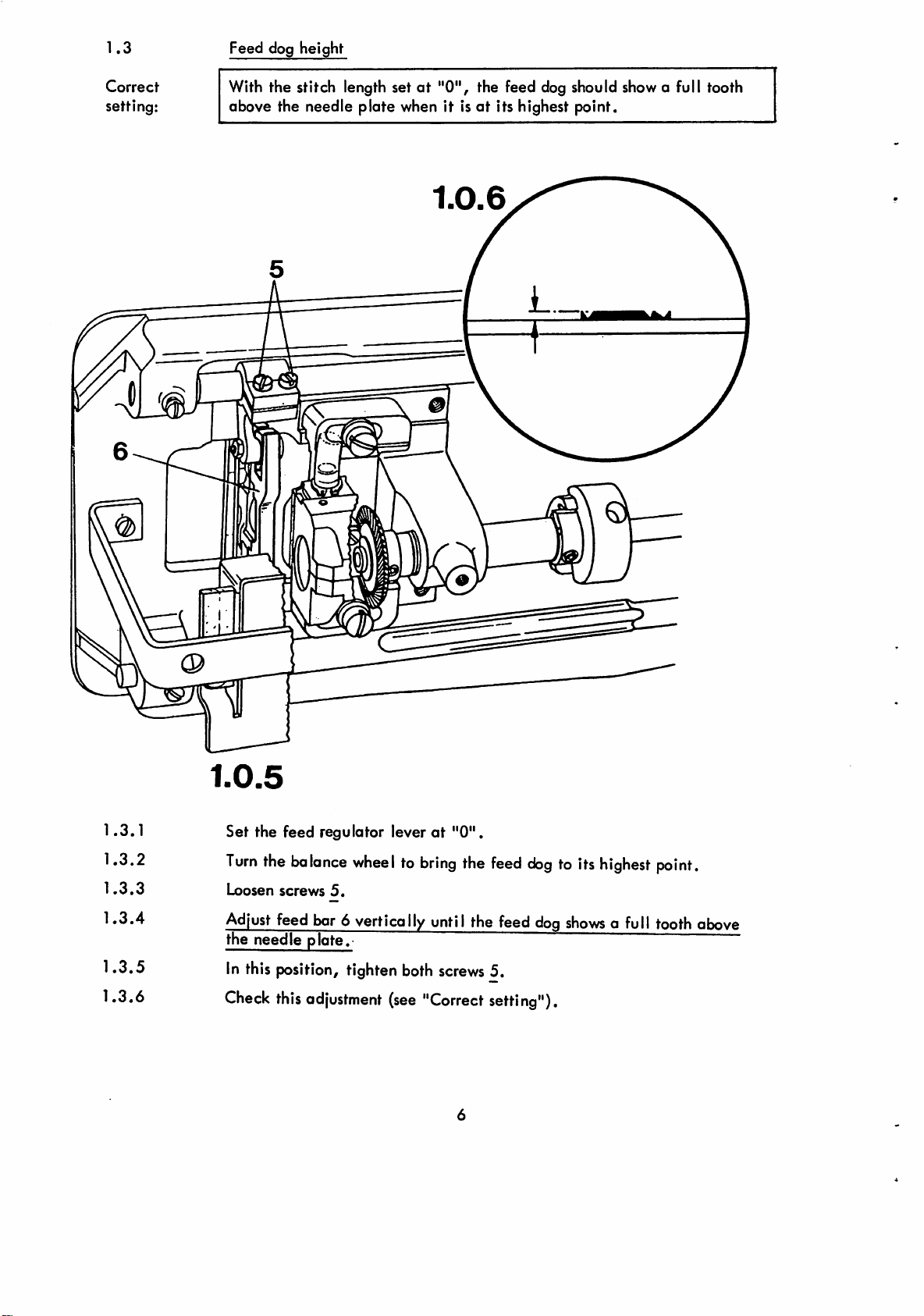
1.3
Feed dog height
Correct
setting:
With the stitch length setat"0",
above the needle plate when it isatits highest point.
the feed dog should show a full tooth
1.3.1
1.3.2
1.3.3
1.3.4
1.3.5
1.3.6
1.0.5
Set
the feed regulator leverat"0".
Turn
the
balance
Loosen
Adjust
the needle plate.
In this position, tighten both
Check
screws
feed bar 6 vertically until the feed
this
wheeltobring
5.
adjustment
(see
the
screws
"Correct
feed
dogtoits
dog
5.
setting").
highest
shows
a full tooth above
point.
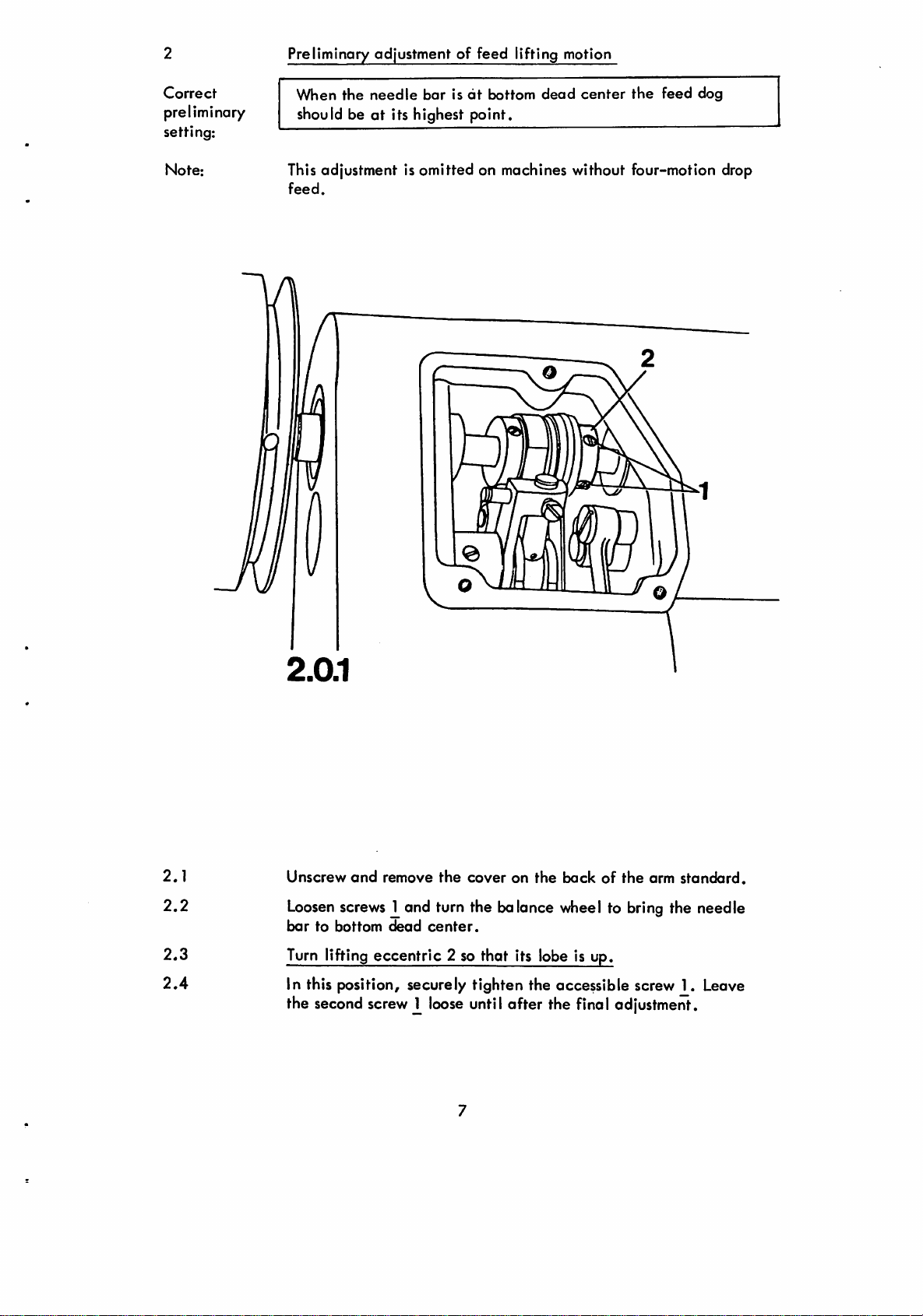
Preliminary adjustment of feed lifting motion
Correct
preliminary
setting:
Note:
When
the
needle
barisdt
bottom
dead
center
the
feed
dog
should beatits highest point.
This adjustment is omitted on machines without four-motion drop
feed.
2.1
2.2
2.3
2.4
©
Unscrew
Loosen
bartobottom
Turn lifting
and
screws
remove
the
coveronthe
bockofthe
arm
and turn the balance wheel to bring the needle
dead
center.
eccentric
2 so that its lobe is up.
standard.
In this position, securely tighten the accessible screw 1. Leave
the
second
screw^loose
until
after the
final
adjustment.