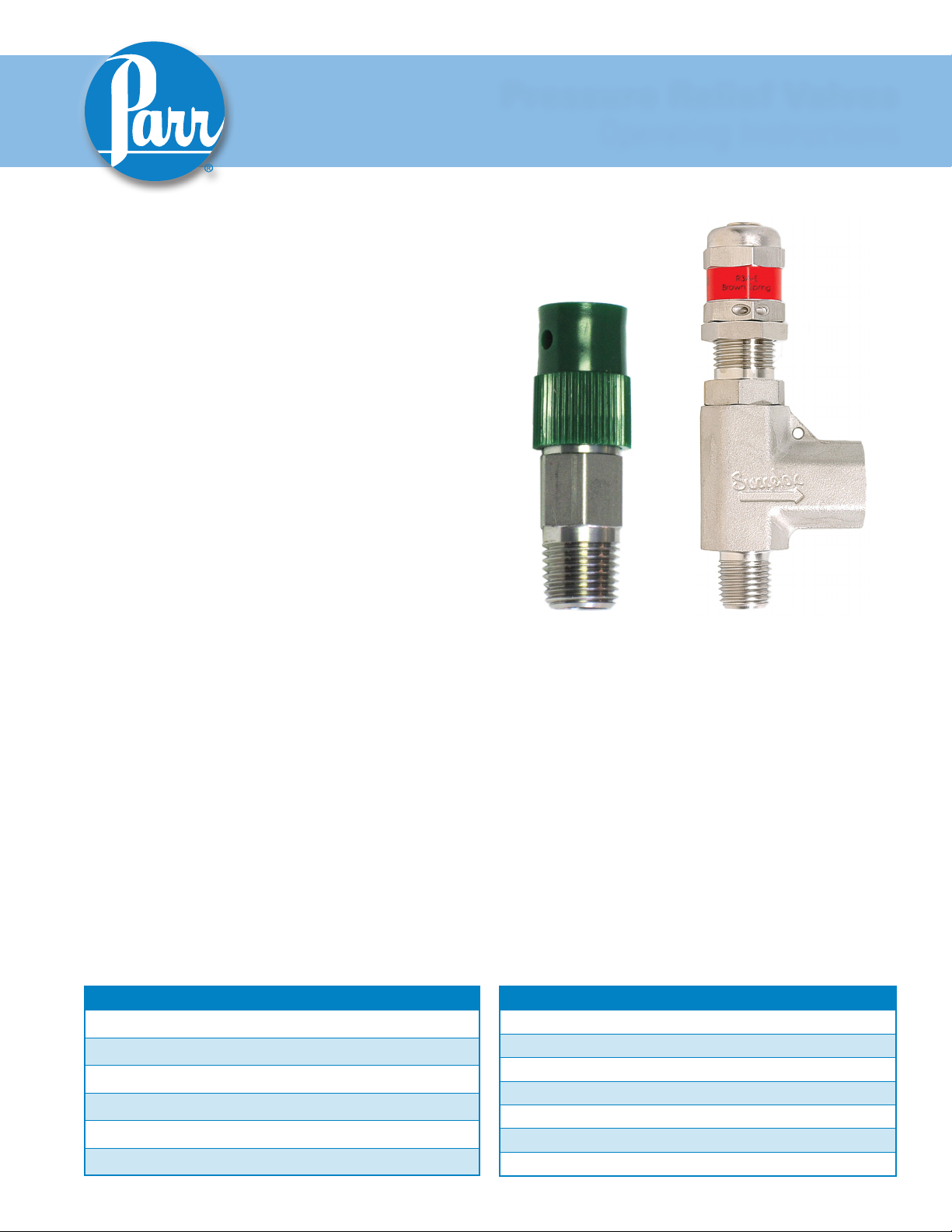
Supplemental Protection
Although a safety rupture disc offers excellent protection against overpressure, it may be desirable in some
installations to supplement the rupture disc with a
spring-loaded relief valve, pre-set to open at a pressure below the burst rating of the disk. Unlike rupture discs, relief valves can be slightly higher that the
routine operating pressure and, since the valve will
reseal once the pressure falls below the relief setting,
valuable reactants will often be saved by this protective feature. Also, adding a relief valve will provide
positive protection for the pressure gage when using
gages less than 1000 psi since small diameter rupture
discs are not reliable at these lower pressures.
323M
Pressure Relief Valves
Operating Instructions
Two Different Styles
Parr spring-loaded relief valves are offered in two different styles, both with 1/4” NPT mounting threads.
They are commonly installed in the side port of the
gage adapter or by adding a 155VB street tee below
the pressure gage and attaching the relief valve to the
side opening on the tee, but other arrangements can
be used as well.
A140VB2 Values for Low Pressures
A140VB2 relief valves are offered in five ranges for
use at low pressures up to 600 psi. Since small diameter rupture discs are not reliable at pressures below
1000 psi, adding a pre-set A140VB2 valve to a system
will protect low range pressure gages from accidental overpressure. The cracking pressure for A140VB2
valves is adjustable within the range prescribed for
each valve. To adjust the spring tension on the valve,
remove the green cap from the assembly. Remover
the outer locking screw with 5/32” Allen wrench.
Next, turn the inner 5/32” adjuster screw clockwise to
increase the cracking pressure, or counterclockwise
to lessen the cracking pressure. Replace the outer
locking screw until it comes in contact with the inner
screw. Place the green cap back onto the assembly.
Figure 1
A140VB2
Figure 2
A175VB
A175VB Valves for High Pressures
A175VB relief valves are offered in multiple ranges
for pressures 50-5000 psi. When the upstream pressure overcomes the force exerted by the spring in
these valves the poppet will open, allowing discharge
through a 1/4” NPT female opening to which extension
piping can be attached.
The cracking pressure in these valves is adjustable and
can be set by the user. To increase the cracking pressure: release the lock nut under the adjustment cap
clockwise to increase the compression on the spring.
Part No. Preset Psi Adj. Psi Bar
A140VB2PA 100 50-150 3.45-10.3
A140VB2P2 145 50-150 3.45-10.3
A140VB2P1 150 50-150 3.45-10.3
A140VB2PB 200 150-350 10.3-24.1
A140VB2PC 600 350-600 24.1-41.4
A140VB2PD 300 150-350 10.3-24.1
Parr Instrument Company www.parrinst.com
Part No. Adjustable Psi Bar
A175VB 750-1500 52-103
A175VB2 1500-2250 103-155
A175VB3 2250-3000 155-207
A175VB4 3000-4000 207-276
A175VB5 4000-5000 276-345
A175VB7 350-750 24-52
A175VB8 50-350 3.4-24.1
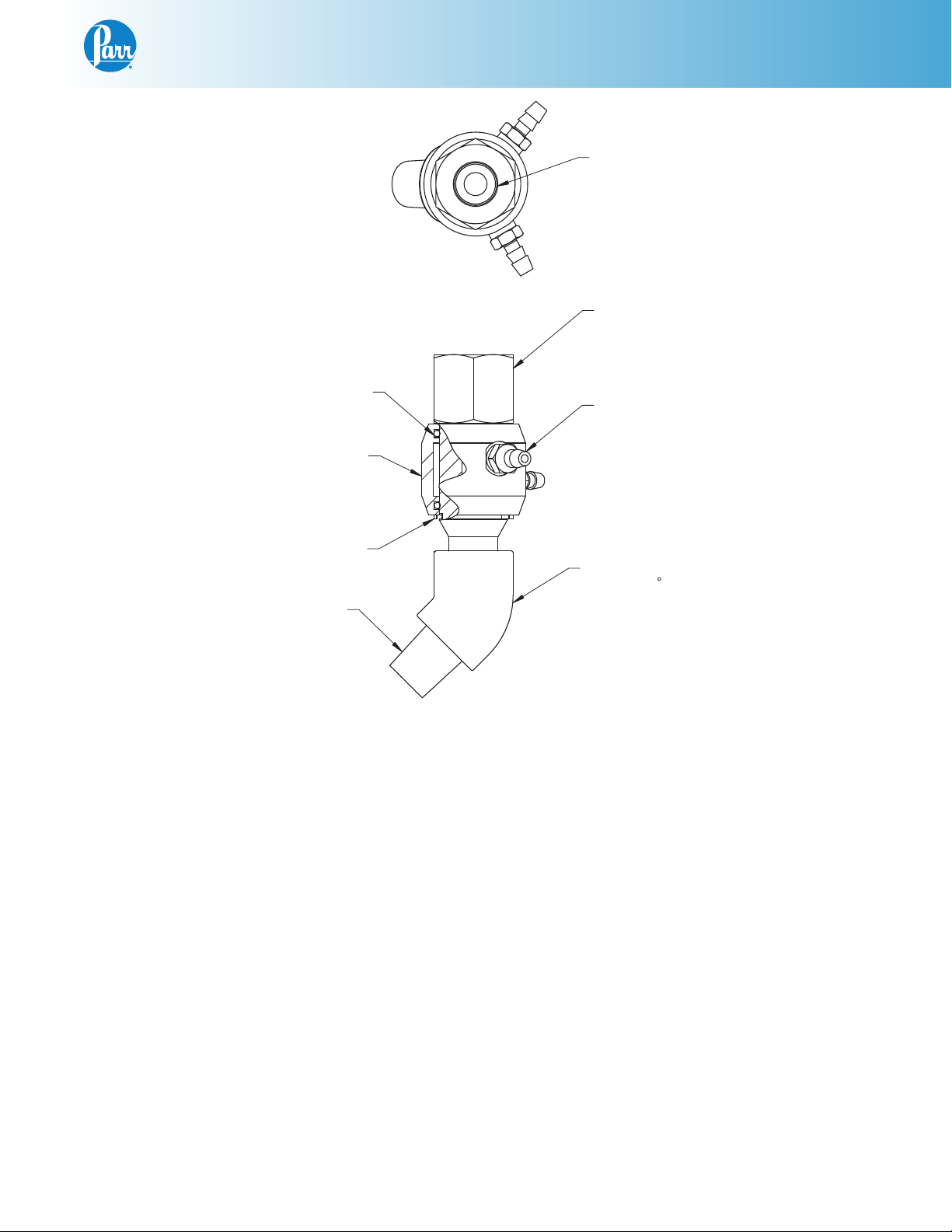
2X 827HC
O-RINGS
2683HC
COOLING SLEEVE
Pressure Relief Valves
1/4 NPT REF
1394HC3
COOLING BODY
2X 2714HC
HOSE NIPPLES
(SEE NOTE 1)
825HC
CLIP RING
1/4 NPT REF
Figure 3
A2599HC3
Cooling Body
The A2599HC3 cooling body assembly is provided
when a Parr pressure apparatus is intended to be operated above 350 °C. Cooling is necessary to limit the
temperature at the seals within the relief valve. To prevent overheating, a steady flow of cold water should
be fed during all vessel operations at temperatures
above 350 °C. Tubing connections for flowing water
are provided on each sleeve, and a 10 foot length of
tubing is furnished to connect to a water source.
154VB2
ELBOW 45
NOTE:
(1) FOR USE WITH JP0025TB06 TUBING
Servicing the Cooling Sleeve
The cooling sleeve has two O-rings which seal the
sleeve onto the cooling body. These O-rings will have
to be replaced after extended periods of service or
after excessive heating with no water flowing through
the sleeve. To replace the O-rings, remove the cooling
body from the elbow (see figure 3). After removing the
cooling body, rotate and pull off the cooling sleeve.
The O-rings can now be removed from the sleeve, be
careful not to scratch or damage the O-ring grooves.
Clean any accumulated lime deposits from the sleeve
and insert new O-rings into the grooves; then moisten
the O-rings and slide the cooling sleeve into place on
the cooling body.
323M R04 12/10/14
P
arr Instrument Company
211 53rd Street • Moline, Illinois 61265 USA 1-309-762-7716 • 1-800-872-7720 • Fax: 1-309-762-9453
E-mail: parr@parrinst.com • http://www.parrinst.com