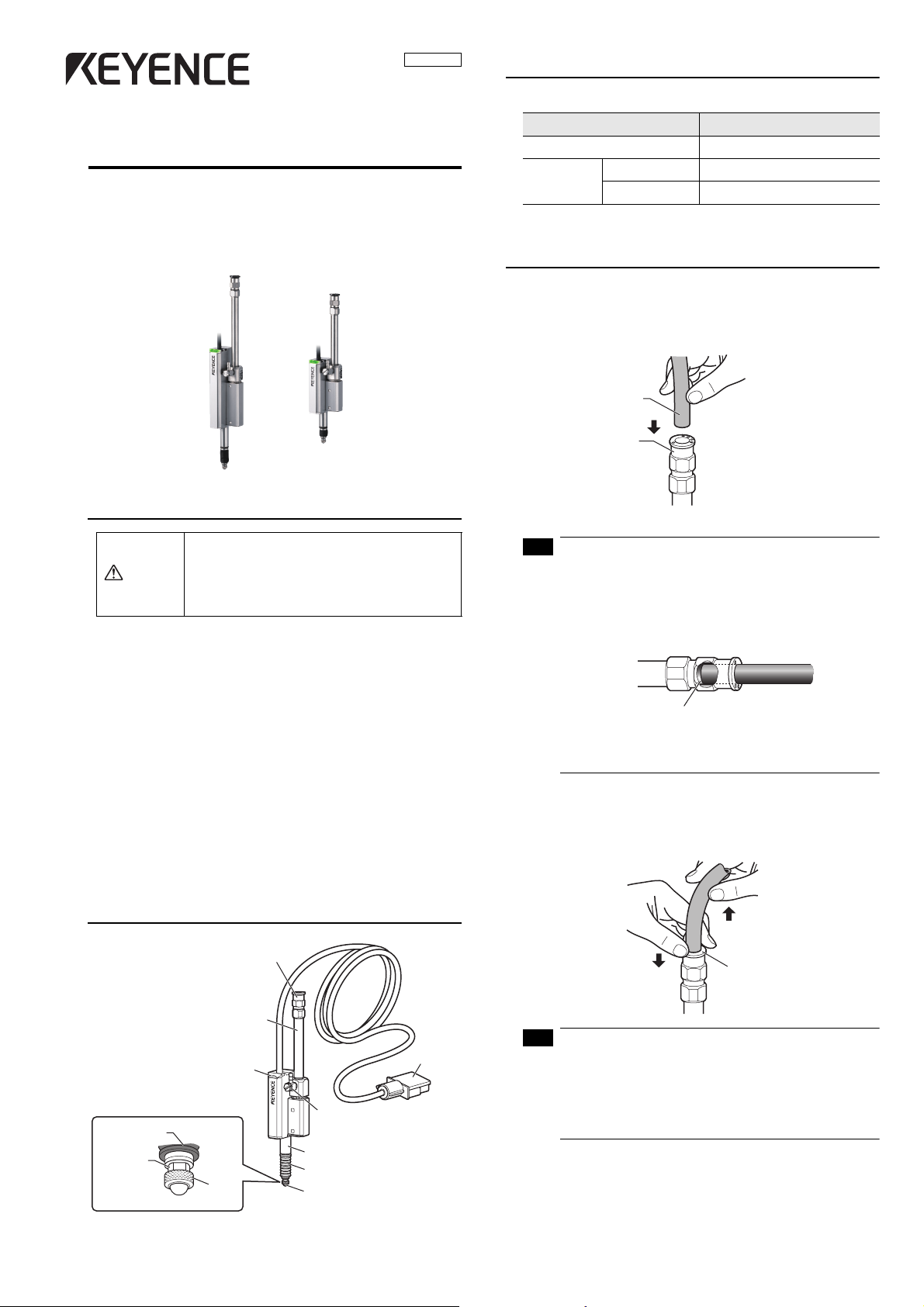
96M1757
GT Series - Digital Contact Sensors
Sensor Head (Air Push Models)
SupplementalManual
Read this manual before using.
After reading this manual, keep it in a safe place for quick reference.
Safety Precautions
Air Tube
The following tubing is recommended for all GT air push models:
Item Description
Recommended tubing material Nylon, Urethane
Tubing size
Outer diameter 4 mm
Inner diameter 2.5 mm
How to Attach/Detach the Air Tube
z
Attaching the air tube
Feed the tubing into the socket until it bottoms out (about 1/2").
The socket will ensure a tight seal around the tubing.
Air tube
Coupling socket
Connect this product to the GT-70A Series
sensor amplifier before using. Be sure to
CAUTION
z
Cylinder
•
This product uses a single-acting cylinder. The internal spring will
return the cylinder to its home position when air pressure is
removed. DO NOT supply air to the exhaust valve.
•
The cylinder is an integral part of the sensor. It cannot be removed.
z
Air
•
To ensure repeatable results, maintain regulated pressure to the air
cylinder.
•
Use of air cylinders, mist separators, dryers will ensure maximum
operating life.
z
Duct Assembly
•
The coupling socket and exhaust valve are integrated into the
sensor housing. They cannot be removed.
carefully read the instruction manual supplied
with the sensor amplifier and that it is fully
understood before using.
Names of Sensor Head Parts
Coupling socket
Note
•For best results, cut the end of the tube at a right
angle, ensure that the outer perimeter is not
damaged, and that it still maintains a circular cross
section.
•If the tube is not properly inserted, air leakage may
result (see figure below).
Tu be end
•After attachment, pull on the tube to make sure it is
secure.
z
Detaching the air tube
To detach the air tube, (1) press down on the release ring, (2) pull
out the tube.
(2)
(1)
Release ring
Dust boot
Spindle
Air cylinder
Operation indicator
Contact
Connector
Exhaust valve
Mounting fixture
Dust boot*
Contact
* Not mounted on GT-A10L/A22L.
Note
•Before detaching the tube, be sure to stop any air
flow.
•Press down on the release ring evenly from both
sides, and pull the tube out. Uneven pressure may
result in damage to the tube or damage to the
operation of the air cylinder.
1
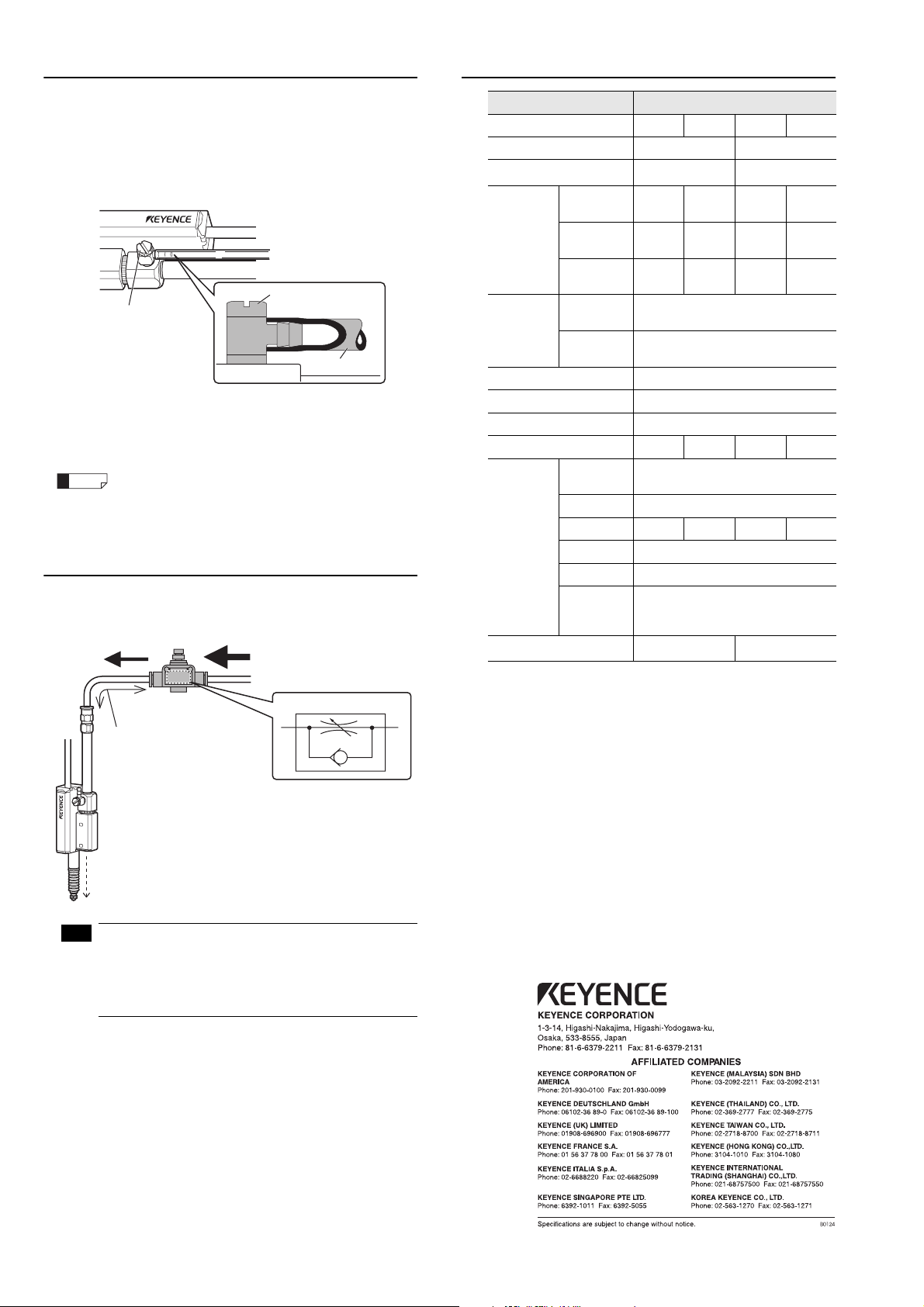
IP67 Enclosure Rating
Specifications
To m a i n t a i n an IP67 enclosure rating for GT-A10/A22, the following
must be satisfied:
•
Firmly connect tubing with 2.5 mm inner diameter to the exhaust
port until it bottoms out.
•
Ensure that the tube end is free of dirt or water.
Screw
Exhaust valve
Air tube
•
Tighten the screw of the exhaust valve with a torque of 0.5 to
y
0.6 N
m. If the screw is loose, the IP67 rating cannot be
guaranteed.
Tip
By loosening the screw of the exhaust valve, you can
change the exhaust port angle.
Adjustment of Spindle Movement Speed
To a d ju s t t h e spindle movement speed, install the optional speed
controller (OP-82133) between the cylinder and the air supply.
Air supply
Speed controller
(OP-82133)
Within 0.5 m recommended
Indication symbol
Item Specifications
Model GT-A10 GT-A10L GT-A22 GT-A22L
Detecting range 10 mm 22 mm
Repeatability
Operating
*2
force
Environmental
resistance
*1
When installed
facing down
When installed
sideways
When installed
facing up
Ambient
temperature
Relative
humidity
3 µm 8 µm
1.0N 0.3N 1.5N 0.35N
0.9N 0.25N 1.4N 0.3N
0.8N 0.2N 1.3N 0.25N
0 to +55°C
35 to 85%RH
Fluid to use Dry air
Pressure range 0.35 to 0.5 MPa
Max pressure 1.0 MPa
Enclosure ratings IP67 - IP67 -
Main unit
cover
SUS430
Indicator Polyarylate
Dust boot NBR - NBR -
Material
Contact SUS304
Cable PVC
Aluminum alloy,
Polyacetal,
Nickel plated brass
Approx. 150 g Approx. 180 g
Weight
Air cylinder
assembly
*3
*1 The read value at the detection center under an ambient
temperature of 23°C and a response time of 100 ms.
*2 The operating force (typical value) at the center of the
movable range of the installed sensor head when supplying
air. Note that the detectability varies according to the
mounted condition of the dust boot. Do not mount the dust
boot on GT-A10L/A22L.
*3 Includes the connector cable (2 m).
Adjusting the speed.
Note
•To ensure proper operation, install the speed
controller within 0.5 m of the cylinder.
•Install the speed controller in the direction indicated
by the above figure. The speed controller will not
operate if installed in the reverse direction.
© KEYENCE CORPORATION, 2006
2
0017-1 96M1757
Printed in Japan