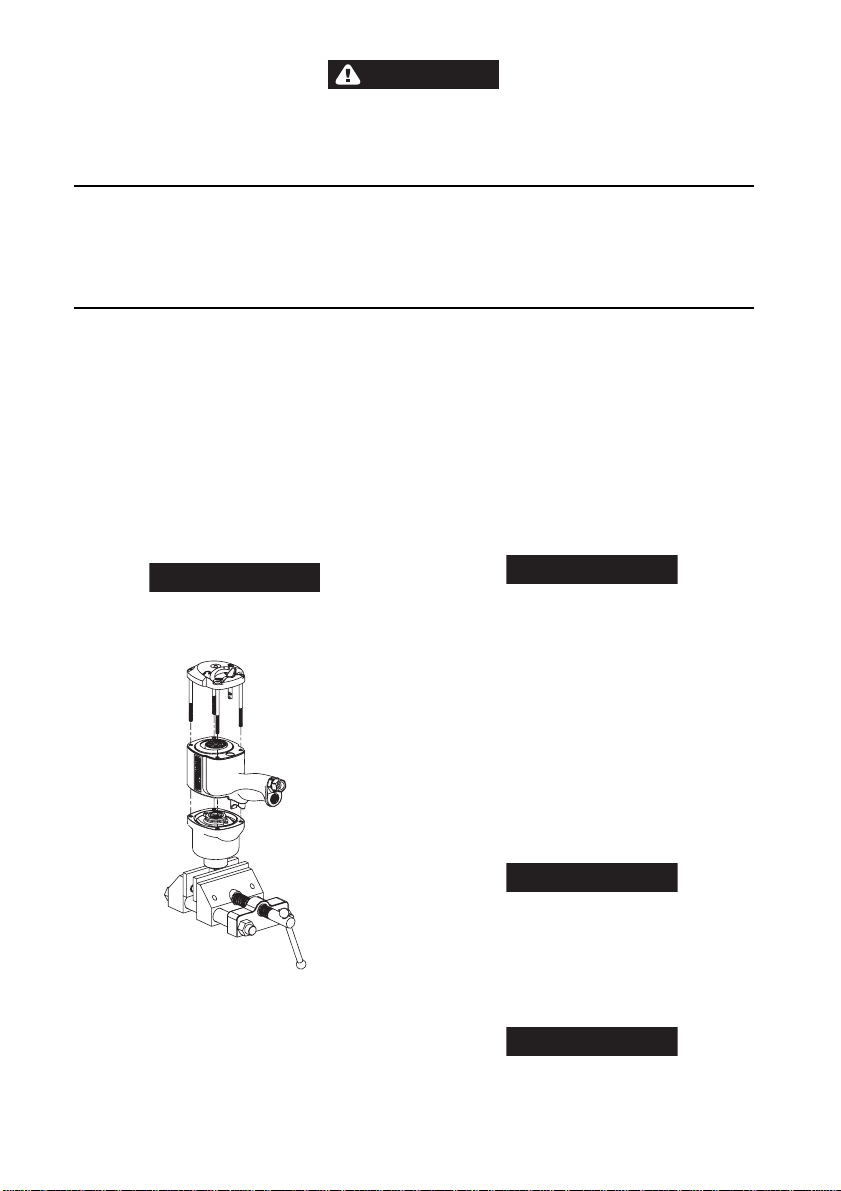
WARNING
Always wear eye protection when operating or performing maintenance on this tool.
Always turn off the air supply and disconnect the air supply hose before inst alling, removing or adjusting a ny accessory
on this tool, or before performing any maintenance on this tool.
Note: When reading the instructions, refer to exploded diagrams in Parts Information Manuals when applicable (see under
Related Documentation for form numbers).
Lubrication
Each time a Series 2925P1Ti and 2925P3Ti Impactool is
disassembled for maintenance and repair or replacement of
parts, lubricate the tool as follows:
1. Work approximately 12 to 15 cc of Ingersoll Rand
No. 170 Grease into the impact mechanism. Coat the
Anvil (40, 42 or 48) lightly with gre ase around the
Hammer Case Bushing (38). Inject approximately 2 to 4
cc of grease into the Grease Fitting (17).
2. Use Ingersoll Rand No. 50 Oil for lubricating the motor.
Inject approximately 1 to 2 cc of oil into the air inlet before
attaching the air hose.
Disassembly
General Instructions
1. Do not disassemble the tool any further than necessary
to replace or repair damaged parts.
2. Whenever grasping a tool or a part in a vise, always use
leather-covered or copper-covered vise jaws to protect
the surface of the part and help p reven t distor tion. This is
particularly true of threaded members and housings.
3. Do not remove any part which is a press fit in or on a
subassembly unless the removal of that part is necessary
for repair or replacement.
4. Do not disassemble the Impactool unless you have a
complete set of new gaskets and o-rings for repla cemen t.
Disassembly of the Hammer Case and Anvil
Assembly
NOTICE
Before disassembling this tool, clamp the anvil drive in
leather-covered or copper-covered vise jaws with the
Backcap (16) pointing upward. See Drawing TPD1918.
4. Remove the Hammer Case and impact mechanism
assembly from the vise. Remove the Hammer Frame
Washer (33) from the rear of th e H amm er Fra m e an d set
it aside on a clean bench.
5. Place the impact mechanism on a bench with the Anvil
pointing upward. Make sure that the Hammer Pins (36)
do not drop out of the Hammer.
6. Lift the Hammer Case off of the Anvil (40 or 48). If it is
unnecessary to disassemble the impact mechanism, set
it aside intact.
Disassembly of the Quick-Change Anvil
1. Clamp the handle of the tool in leather-covered or coppercovered vise jaws with the Quick-Change Anvil (42) upward.
2. Remove front Thrust Ring Lock (44) and Thrust Ring (45).
NOTICE
The Retaining Ball (47) will fall free once the Retaining
Sleeve (43) is removed.
3. Remove the Retaining Sleeve Spring (46), Retaining
Sleeve, Retaining Ball, and the rear Thrust Ring Lock.
4. Remove the four Backcap Bolts (14). While lightly tapping
on the end of the Anvil with a plastic hammer, lift off the
Hammer Case (39).
5. Remove and discard the Hammer Case Gasket (37).
6. Grasp the Hammer Frame (34) and carefully lift off entire
impact mechanism making certain not to drop the two
Hammer Pins (36). If it is necessary to disassemble the
impact mechanism, refer to Disassembly of the Impact
Mechanism. If it is unnecessary to disassemble the
impact mechanism, set it aside intact.
7. Remove the Rear Hammer Frame Washer (33).
Disassembly of the Impact Mechanism
1. Set the mechanism, driver end up, on the workbench.
NOTICE
Note the twin Hammers within the Hammer Frame. These
are identical but must be placed in the Hammer Frame in a
particular relationship. Using a felt tipped pen, mark the top
Hammer “T↑” and the bottom Hammer “B↑” with the arrows
(Dwg. TPD1918)
1. Unscrew and remove the four Backcap Bolts (14).
2. Lift the assembled Motor Housing (1) off of the Hammer
Case (39). Make sure that you hold the Backcap in
position on the Housing and that the motor does not
come out of the Housing.
3. Remove the Hammer Case Gasket (37) and re place with
a new one when assembling the Hammer Case to the
Housing.
EN-2 04584348_ed2
pointing upward. Mark both Hammers on the same end.
2. With the mechanism sitting upright on the workbench,
slowly rotate the Anvil in a clockwise direction until it
comes up solid.
NOTICE
If you continue to rotate the Anvil, it will cam the
Hammers out of engagement. Do not do this; merely
rotate the Anvil until it comes up solid.
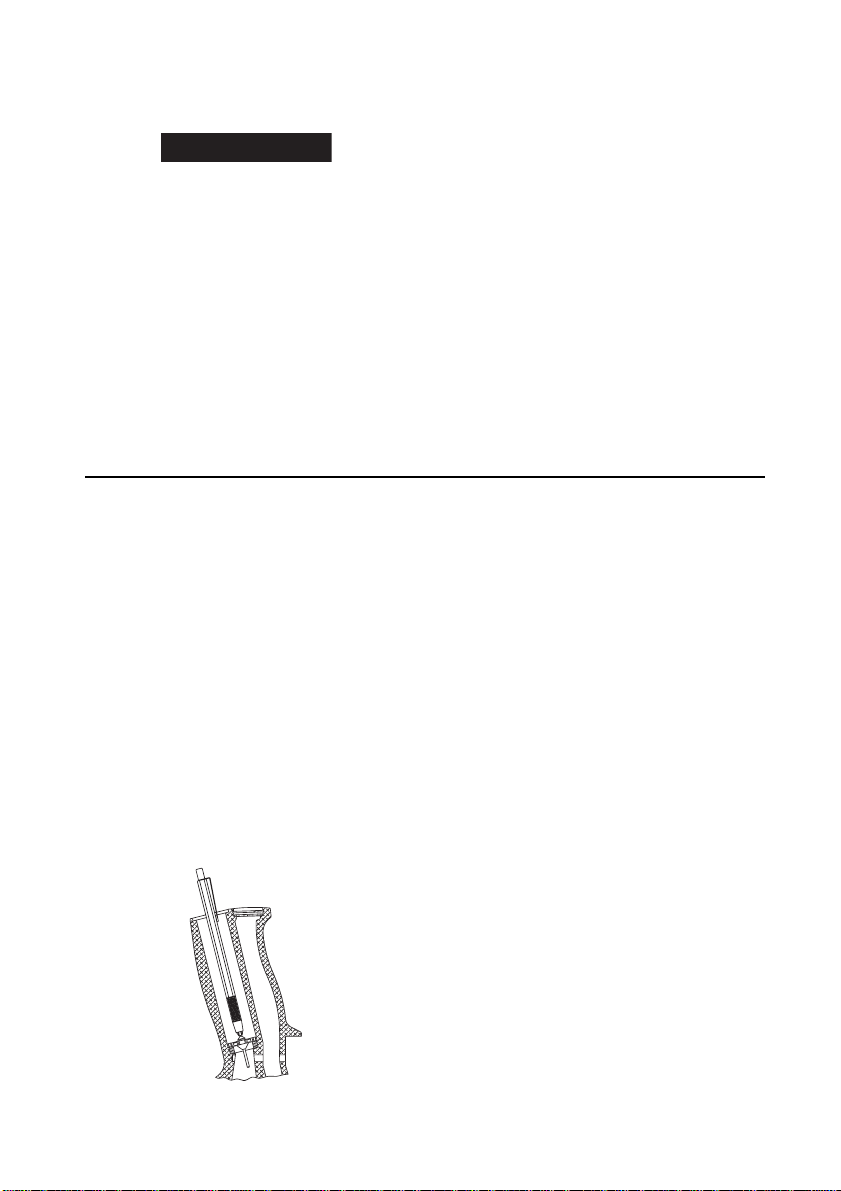
3. Hold the Hammer Frame firmly and, without disturbing
the Hammers, gently lift the Anvil, simultaneously rotating
it clockwise about 1/8 of a turn, from Hammer Frame.
4. With Anvil removed, lift out the two Hammer Pins.
NOTICE
The twin Hammers are now free to slide from the
Hammer Frame. Be careful not to drop them.
Disassembly of the Reverse Valve
1. Remove the four Backcap Bolts (14)
2. Lift the Backcap off of the rear of the Housing.
3. Discard the Backcap Gasket (15) and replace it with a
new one when assembling the tool.
4. Use a hooked tool to remove the Reverse Valve (32) from
the reverse valve bushing. Set the Reverse Valve aside
on a clean bench.
5. Remove and discard the Reverse Valve O-ring (31).
Replace it with a new one when assembling Reverse Valve.
6. Use a flat, thin blade screwdriver to remove the Reverse
Lever Retaining Ring (1 9) and Reverse Lever Spring (20)
from the Reverse Lever (18).
7. Remove the Reverse Lever from the Backcap.
Disassembly of the Motor
1. Remove the four Backcap Bolts.
Assembly
General Instructions
1. Always press on the inner ring of a ball-type bearing
when installing the bearing on a shaf t.
2. Always press on the outer ring of a ball-type bearing
when pressing the bearing into a bearing recess.
3. Whenever grasping a tool or part in a vise, always use
leather-covered or copper-covered vise jaws. Take extra
care with threaded parts or housings.
4. Always clean every part and wipe every part with a thin
film of oil before installation.
5. Apply a film of O-ring lubricant to all O-rings before final
assembly.
6. Check every bearing for roughness. Sealed or shielded
bearings should never be cleaned. Work grease
thoroughly into every open bearing before installation.
Assembly of the Throttle Mechanism
1. Install a new Throttle Valve Seat (2) by pushing it into
position in the Housing (1) with a 13/16” dowel.
2. Insert the short end of the stem of the Throttle Valve (5)
into the jaws of an expanding-type mechanical pencil.
Allow the jaws to retract around stem to secure it.
3. Install the Throttle Valve on the Valve Seat.
See Dwg. TPD1919.
2. Remove the Backcap, Motor Clamp Washer (21) and
Backcap Gasket from the Housing and set them aside o n
a clean bench. Discard the Backcap Gasket and replace
it with a new one when assembling the tool.
3. Lift the Housing from the Hamm er C a se. P l ace on e h and
over the rear of the Housing and tur n the Housing over so
that the assembled motor can slide and be guide out of
the Housing.
4. Place the assembled moto r on a clean bench with the
rotor spline facing upward.
5. Remove the Front End Plate (29) and Cylinder (27).
6. Remove the Rotor (25) from Rea r End Plate (23).
7. Remove the Vanes from the Rotor.
8. Inspect all motor parts including the Front Rotor
Bearing (30) and Rear Rotor B earing (2 2) an d rep lace a ll
worn or damaged parts.
Disassembly of the Throttle Mechanism
1. Unscrew and remove the Air Inlet Bushing (18).
2. Remove the Screen (7), Throttle Valve Spring (6) and
Throttle Valve (5).
3. If the Throttle Valve Seat (2) requires replacem en t, i nse r t
a hooked tool through the center of the Valve Seat.
Catching the backside of the Seat with the hook, pull the
Seat from the Housing.
4. Withdraw the Trigger Assembly (3) from Housing.
5. Remove the Retaining Ring (11), Exhaust Deflector (12)
and Muffler Element (10) from the Housing.
4. As an alternate assembly procedure, drop the Throt tle
Valve, long stem firs t, into the inlet p assage. If the throttle
Valve does not sit squarely on the Throttle valve Seat,
shake the Handle until it seats.
5. Install the Throttle Valve Spring (6), small end first, with
the inside diameter of the small first coil around the hub
of the Throttle Valve.
6. Coat the Inlet Bushing O-ring (9) with O-ring l ubricant and
install it on the Inlet Bushing (8).
7. Screw the Inlet bushing into the Housing until snug and
tighten to 50-55 ft. lbs. (68-75 Nm) torque.
8. Wipe the stem of the Trigger Assembly (3) with light
grease and insert the stem of the Trigger into the trigger
bore in the Housing until it snaps into place on the
Throttle Valve.
Assembly of the Motor
1. Pack the Front Rotor Bearing (30) and Rear Rotor
Bearing (22) with the recommended grease. Install the
Front Rotor Bearing in the Front End Plat e (29) and the ar
Rotor Bearing in the Rear End Plate (23).
2. Slide the assembled Rear End Plate and Rear Rotor
Bearing on the hub of the Rotor (25).
3. Set the assembled Rear End Plate and Rotor on a clean
surface with the spline of the Rotor pointing upward.
4. Insert the Vanes (26) in the vane slots on the Rotor.
5. Install the Front and Rear Cylinder Dowels (28) in the
Cylinder (27).
6. Slide the Cylinder over the R ot or and Vanes making sure
that the Rear Cylinder Dowel enters the notch in the
outside diameter of the Rear End Plate.
For Series 2925RBP1Ti and 2925RBP3Ti: Assemble
Cylinder with exhaust ports to LEFT of top dead center
(11 o’clock position). See Dwg. TPD1921.
(Dwg. TPD1919)
04584348_ed2 EN-3