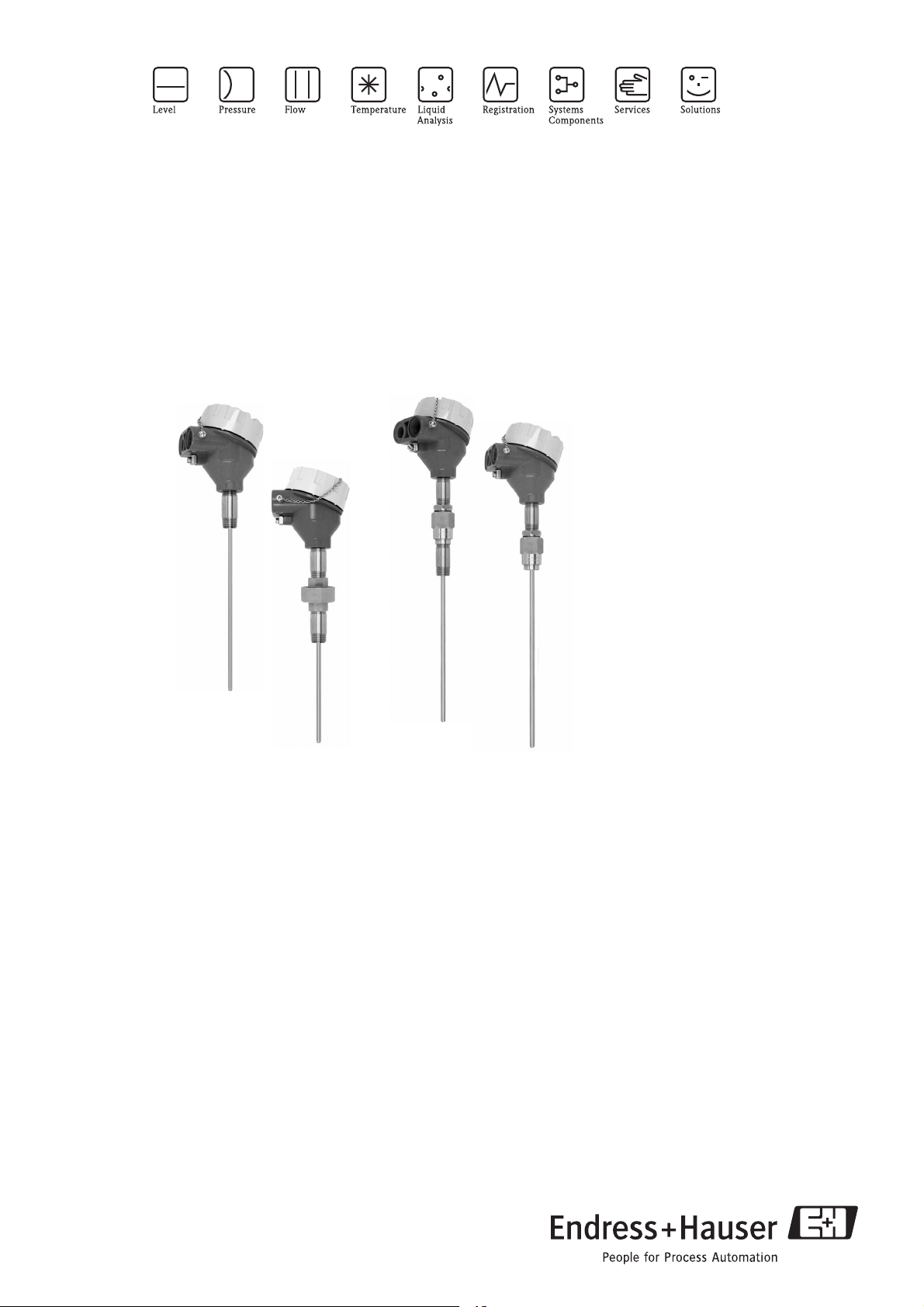
Technical Information
Omnigrad S -TR62
RTD thermometer EEx-d or EEx-ia certified, replaceable inset , complete
of niple and union to thermowell connection
PCP (4...20 mA), HART® or PROFIBUS-PA® electronics
Range of uses
The Omnigrad S TR62 is an RTD industrial thermometer,
developed for heavy duty and/or generic industrial applications.
In compliance to EN 50014/18 (ATEX certification) it is therefore particularly suitable also for hazardous areas.
When required, it’s also available with a transmitter(PCP,
HART® or PROFIBUS-PA®) into the housing.
The TR62 is available in several standard versions and different
configurations, can also be configured with specific dimensions
and characteristics depending on process requirements.
The installation on the plants, require separately order of the
thermowell (form pipe or from bar-stock).
Application areas
• Chemicals industry
• Energy industry
• Gas Processing industry
• Petrochemical industry
• General industrial services
Features and benefits
• Customized immersion length
• Aluminium housing, with protection grade from IP66 / IP 68
• PCP, HART® and PROFIBUS-PA®, (4...20 mA 2-wire transmitters)
• Thermoresistance insert insulated with mineral oxide cable
(MgO cable) diameter: 3 or 6 mm
• Pt100 sensing element with accuracy in class A or 1/3 DIN B
(IEC 60751)
• The Pt100 available are: wire-wound WW (-200...600°C) or
thin-film TF (-50...400°C)
• Single or double Pt100 to 2,3 or 4 wires connection
• ATEX II 1/2 GD EEx-ia IIC certification
• ATEX II 2 G EEx-d IIC certification
4 0
TI281T/02/en
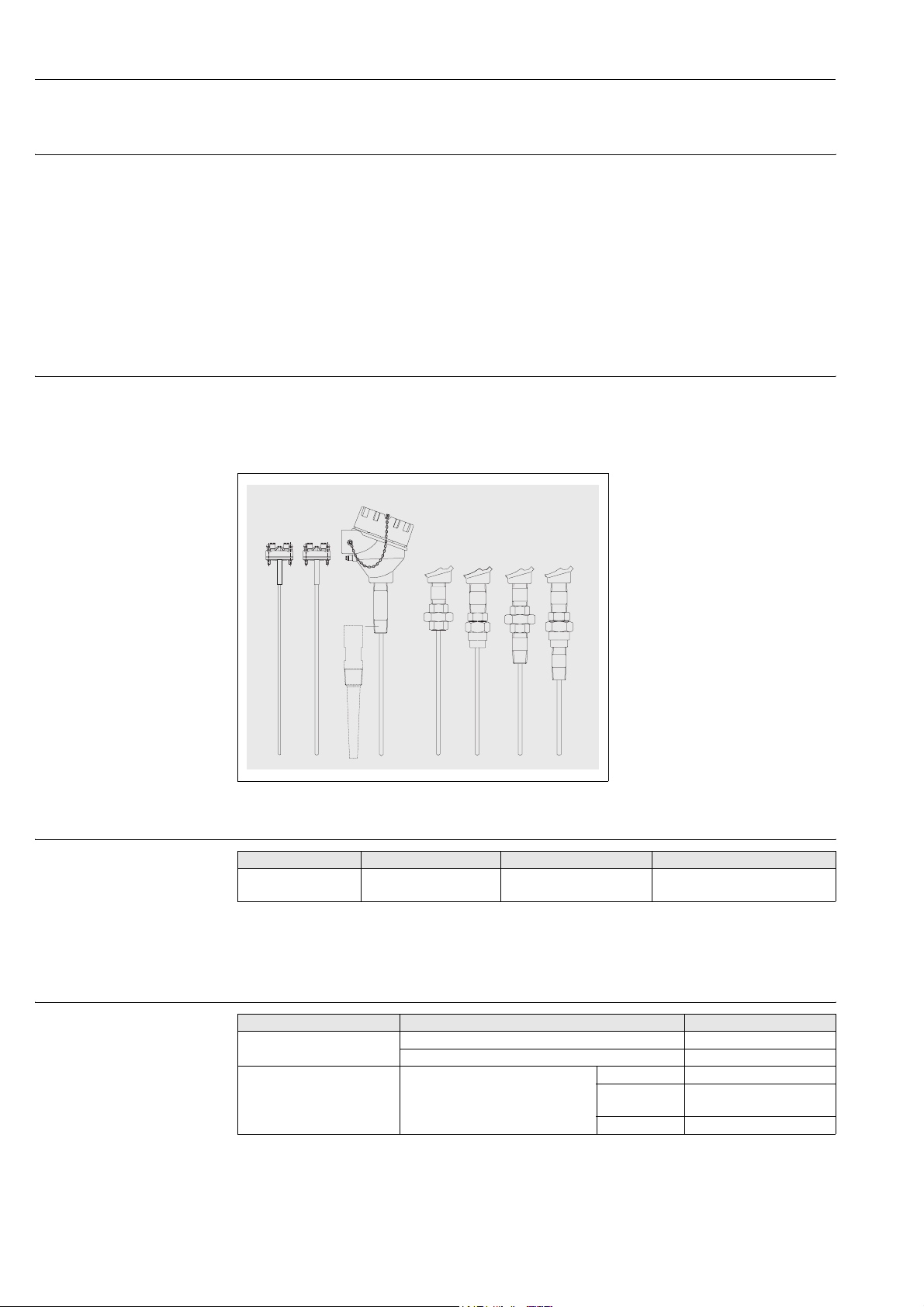
Omnigrad S -TR62
Function and system design
Measuring principle The RTD (Resistance Temperature Detector), is a sensor where the electrical resistance varies with the tem-
perature. The material of the RTD is Platinum (Pt) with a value of the resistance (R), referred to a nominal value
at the temperature of 0°C = 100,00 Ω (in compliance to rule DIN IEC 60751; it is called Pt100). The very
important is to define the RTD; it is defined with a standard "α" value measured between 0°C and 100°C.
This value is: α = 3.85 x 10
The temperature is measured indirectly by reading the voltage drop across the sensing resistor in the presence
of a constant current flowing through it using Ohm’s. The measuring current should be as small as possible to
minimise possible sensor selfheating; normally this current is around 1mA, no higher.
The resistance value measured for each degree is about = 0,391 Ohm/K; over 0°C it is opposite proportional
at the temperature. The standard RTD connection at the plant instrument can be to 2,3 or 4 wires to simple
or double RTD element.
Equipment architecture The construction of the Omnigrad S TR62 temperature sensor is based on the following standards:
• EN 50014/18 (assembly)
• Neck (ASME style: nipple and 3 elements coupling)
• IEC 60751 (insert).
-3
°C-1.
The housing is in painted aluminium
alloy; it is suitable to contain a transmitter and/or the ceramic block of the
inset; the “Ingress Protection” is: IP66
to IP68.
The neck is composed by one or two
nipples and 3 elements coupling. It is
the extension between the head and
the thermowell.
The replaceable insert 3 or 6 mm diameter, is composed by MgO cable (SS
316L sheath) with a sensing element
(Pt100 ohm/0°C) positioned at the
MgO cable tip.
The standard electrical connection is to
2, 3 or 4 wires for sensing element
(Pt100).
Material & Weight
Operating conditions
Fig. 1: TR62 with the various types of thermowell connections and end parts of the probe
Housing Insert Extension neck Weight
aluminium epoxy
coated
sheath in SS 316L/1.4404 SS 316/1.4401 or ASTM
A105
From 0,5 to 1.0 kg for standard
options
Performance
Operating condition or test Product type or rules Value or data of test
Ambient temperature housing (without head-mounted transmitter) -40÷130°C
housing (with head-mounted transmitter) -40÷85°C
Shock and vibration resistance
test
RTD Inset in according to the rule IEC
60751
Acceleration 3 g of peak
Frequency from 10Hz to 500Hz and
back
Time of the test 10 hours
2 Endress+ Hauser
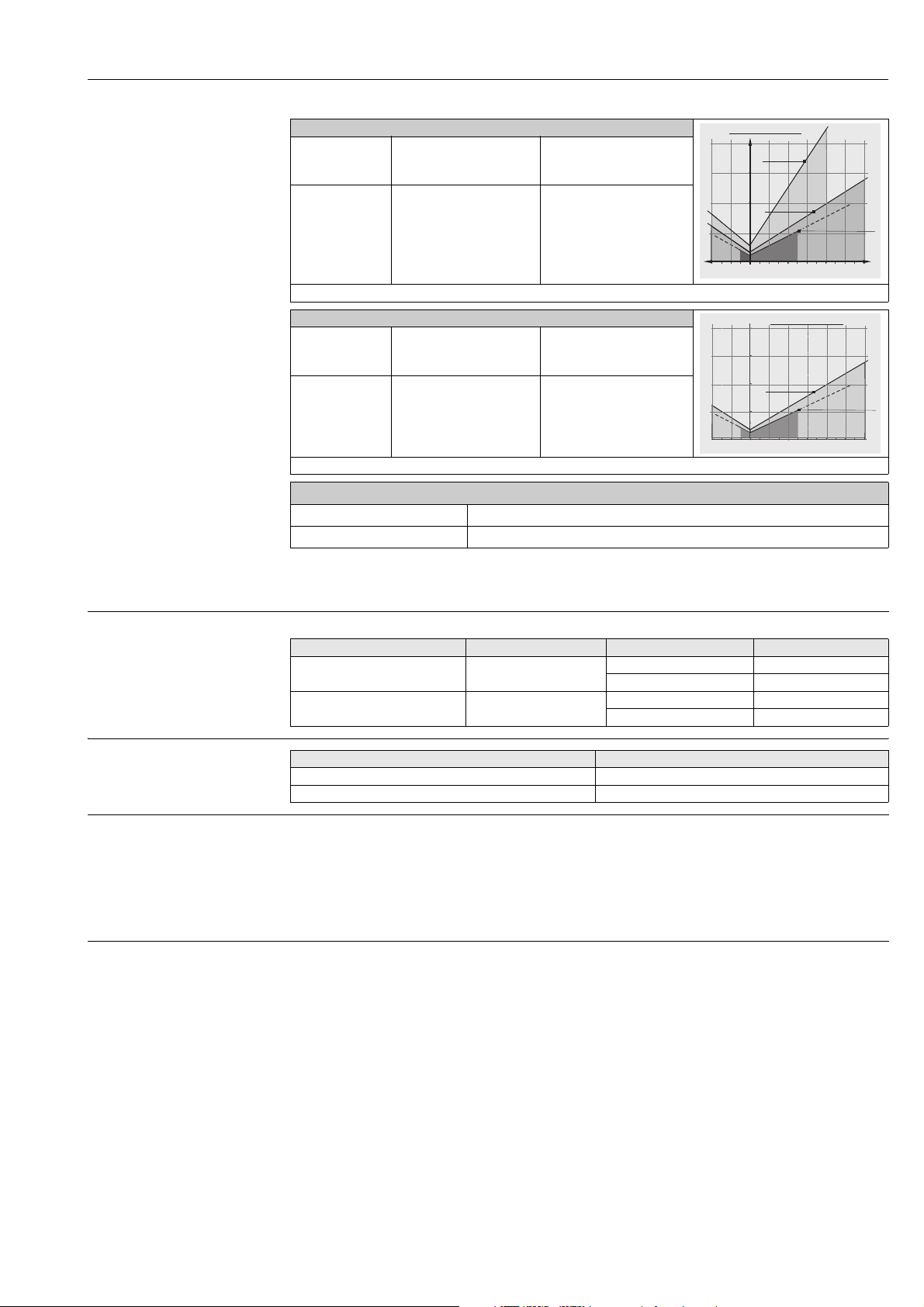
Omnigrad S -TR62
Accuracy
RTD maximum error type TF - Range: -50 to 400°C
Cl. A 3σ = 0.15+0.0020It|
3σ = 0.30+0.0050ItI
Cl. 1/3 DIN B 3σ = 0.10+0.0017It|
3σ = 0.15+0.0020ItI
3σ = 0.15+0.0020ItI
3σ = 0.30+0.0050ItI
= -50…250°C
= +250…400°C
= 0…100°C
= -50...0
= 100...250°C
= 250…400°C
DIN-IEC-EN 60751
2,0
Class B (°C)
1,5
1,0
Class A (°C)
Tolerance
0,5
-200 -100 0 100 200 300 400 500 600°C
Class 1/3 DIN B (°C)
±3σ = range including 99.7% of the readings. (|t|= absolute value of the temperature in °C).
RTD maximum error type WW - Range: -200 to 600°C
Cl. A 3σ = 0.15+0.0020It| = -200…600°C
Cl. 1/3 DIN B 3σ = 0.10+0.0017It|
3σ = 0.15+0.0020ItI
3σ = 0.15+0.0020ItI
= -50...250°C
= -200...-50
= 250…600°C
-200 -100 0 100 200 300 400 500 600°C
2,0
1,5
1,0
Tolerance
0,5
DIN-IEC-EN 60751
Class A (°C)
Class 1/3 DIN B (°C)
±3σ = range including 99.7% of the readings. (|t|= absolute value of the temperature in °C).
Others errors
Transmitter maximum error See the corresponding documentation (codes at the end of the document)
Display maximum error 0.1% FSR + 1 digit (FSR = Full Scale Range)
The “4 wires” configuration, provided as a standard connection for the single Pt 100’s, excludes additional
errors in every condition. Generally in the “4 wires” configuration there is a higher guarantee of accurancy.
Response time Tests, with the RTD insert, in water at 0.4 m/s (according to IEC 60751); from 23 to 33°C step changes:
Insulation
Stem diameter of the insert Pt100 type t
6 mm TF / WW t
3 mm TF / WW t
(x)
50
t
90
50
t
90
Measurement Insulation type Result
Insulation resistance between terminals and probe sheath above 100 MΩ at 25°C
According to IEC 60751, test voltage 250 V above 10 MΩ at 300°C
Response time
3,5 s
8,0 s
2,0 s
5,0 s
Self heating Negligible when the E+H iTEMP® transmitters are employed.
Installation
The Omnigrad S TR62 thermometers can be installed on pipes or tanks by means of threaded or flanged thermowell connections. The immersion length must take into account all the parameters of the thermometer and
the process to measure. If the immersion is too low, an error may be generated in the temperature recorded
due to the lower temperature of the process fluid near to the walls and heat transfer, which takes place through
the sensor stem. The incidence of such an error can be not negligible if there is a big difference between the
process temperature and the ambient temperature.
To prevent measuring errors of this kind, it is advisable to use thermometer with a small diameter on well and
an immersion length (L) of at least 80÷100 mm.
In small section ducts the tubing’s axis must be reached and preferibly slightly exceeded by the tip of the probe
(see fig. 2A-2C).
Insulation of the outer part of the sensor reduces the effect produced by a low immersion. Alternatively, it is
also possible to adopt a tilted installation (see fig. 2B-2D).
For a best installation, in the industries, it's better to follow the rule: h ( d, L > D/2 + h.
Endress+Hauser 3