
Installation Instruction
VBB/VBS Series Ball Valves
with Floating Actuators
Inspection
Inspect the package for damage. If package is damaged,
notify the appropriate carrier immediately. If undamaged, open
the package and inspect the device for obvious damage.
Return damaged products.
Requirements
Two-Way Valve: Flow A to AB Three-Way Valve: Mixing Only A
NOTICE
RISK OF EQUIPMENT DAMAGE
Read and understand these instru
•
servicing this product.
Do not install this product in haz
•
locations unless expressly permi
•
Turn off all power supplying equ
the product.
•
Make all connections in accorda
diagram.
Do not exceed the product’s technical ratings.
•
• Use copper conductors only. Make all connections in
accordance with the appropriate
•
Avoid installation locations expo
moisture, and/or corrosive or ex
Avoid electrical noise interferenc
•
conductors, electrical machinery
•
When making wiring connections within the actuator
put leads or connectors below the
•
This product is a class 2 (Limited V
device.
The installer is responsible for co
•
codes.
•
Check the Electrical terminals a
settings before powering up the
Failure to follow these instructions may cause equipment
damage.
ctions before installing or
ardous or classified
tted.
ipment before working on
nce with the electrical wiring
electrical wiring diagram.
sed to vibration, excessive
plosive vapours.
e. Do not install near large
, or welding equipment.
, do not
motor.
oltage Limited Energy)
nformance to all applicable
nd any configuration switch
actuator.
M112A0x or M122A0x
and/or B to AB.
M131A0x or M132A0x
If this product is used in a manner not specified by the manufacturer,
the protection provided by the product may be impaired.
No responsibility is assumed by Schneider Electric for any
consequences arising out of the use of this product.
Tools (not provided)
• Wrench/adjustable spanners: 24…42mm (1”…1-5/8”)
• Pipe wrench according to pipe size
• Volt-ohm multimeter
• Phillips Head screwdriver
© 2016 Schne ider Ele ctric. All rights rese rved. All trademar ks are ow ned by Sch neider Electr ic Indust ries S AS or its affi liated co mpanie s. April , 2016 tc
Docume nt Numbe r: F-27393-7
Training
• Installer must be a qualified, experienced technician
Other accessories
• As appropriate.
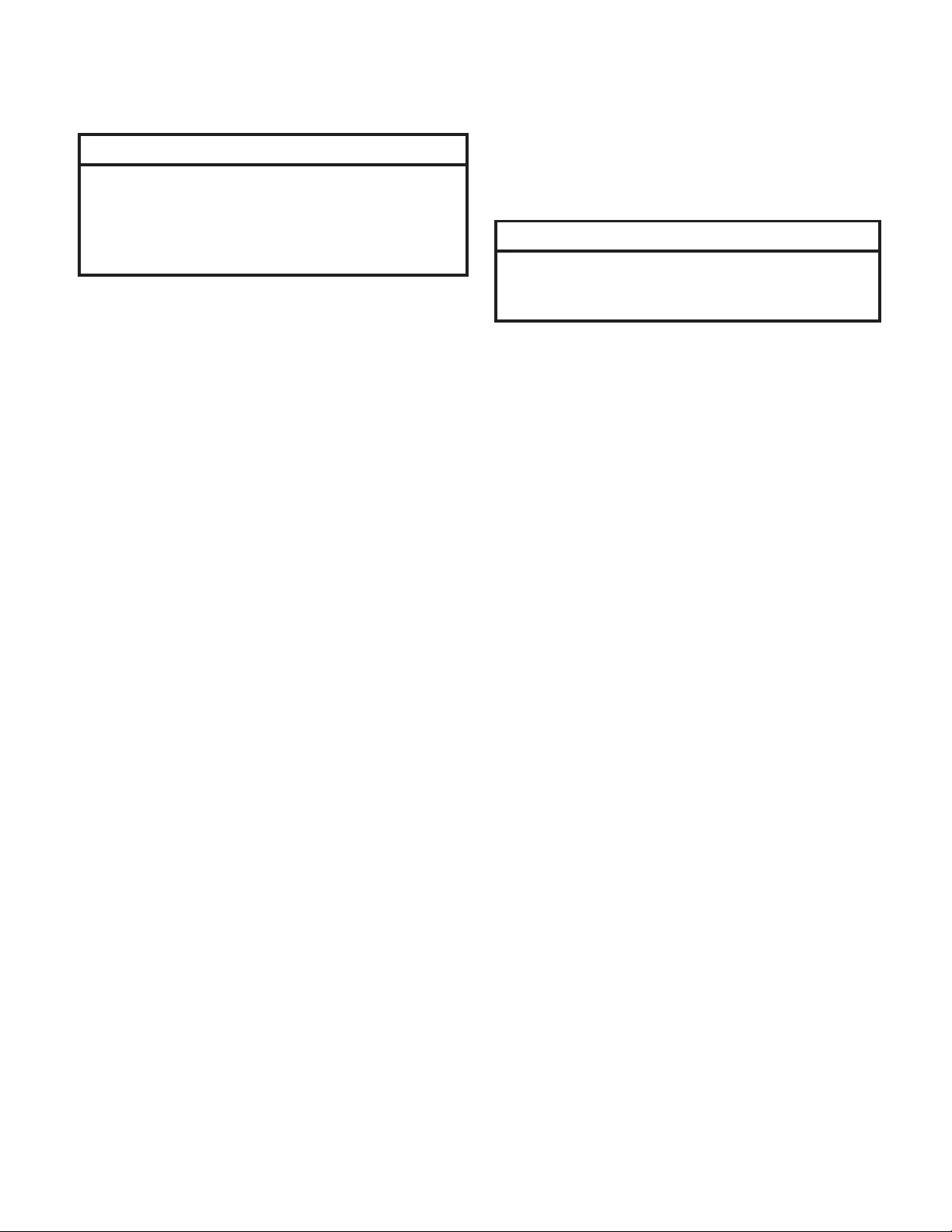
Selection Guide
Piping
NOTICE
RISK OF EQUIPMENT DAMAGE
•
Do not install in open systems using substantial make-up water.
• Follow proper water treatment practices and system
procedures.
Failure to follow these instructio
damage.
These valves must be piped according to the water flow
diagram below. Two-Way valve flow should go A to AB. Threeway valves should be applied only as mixing valves (see
diagram).
Best Practice Guidelines
It is recommended to fit a strainer upstream of the valve to
increase reliability and to follow water treatment guidelines as
detailed in VDI 2035.
Recommendations
The pipework system should be flushed prior to the operation.
Installation Notes
• Verify there is no overhead water source that may drip
onto valve actuator. In normal service, some condensation
may occur on or around the valve. A drip pan may be
necessary or the valve body may be insulated.
• Do not cover the actuator or obstruct the manual operator
lever.
• Reference product label and Product Datasheet F-27895
for additional product specifications.
It is the responsibility of the installer or product specifier to
verify media compatibility of the valves construction materials
with the supplier of water treatment/heat transfer solution.
Installing the Valve Body
Apply PTFE tape to the male pipe thread. Hand screw the pipe
into the valve, turning it as far as it will go. Use a wrench to
fully tighten the valve to the pipe. Do not over tighten or strip
the threads.
Installing the Actuator on the Valve Body
1. Turn the valve stem so the slot on top of the stem is
pointing towards the large keyed post.
2.
Do one of the following:
• For a spring return actuator, press the red lever down
and rotate the manual operating lever to align the stem
hole with the valve stem. Then slide the red lever up to
lock the manual lever in place.
• For a non-spring actuator, press and hold the red
release button on the top of the actuator and rotate
the manual operating lever to align the stem hole with
the valve stem, then release the red button.
3. Align the valve body with the actuator so the stem lines up
with the large stem hole and the large keyed post lines up
with the post hole on the bottom of the actuator.
4. Firmly press the valve and actuator together to lock into
place.
ns may cause equipment
The first time the valve is operated electrically, the manual
operating lever of the actuator will move to the automatic
position. The manual operating lever can be used to allow
flushing of the system after installation.
Removing the Actuator
NOTICE
RISK OF EQUIPMENT DAMAGE
Do not use the valve body to manually open the actuator.
•
Failure to follow this instruction
the actuator
NOTE: Make sure the valve stem rotates freely before and
after installing the actuator. If the stem does not operate freely
it may indicate that the stem was damaged and may require
that the valve be replaced.
1. Press and hold the valve release lever inward, towards the
valve.
2. Lift the actuator from the valve.
3.
After the piping is under pressure, check the valve body
and the connections for leaks.
4. After the valve and actuator are installed, power the
actuator and check the operation by varying the control
signal. On spring return models, the valve should return to
its normal position when power is removed.
.
Theory of Operation
This series of floating valve actuator assemblies is designed
to make incremental adjustments to flow based on the control
signal input. This actuator is not intended for continuous use in
zero dead band control systems.
In order prevent a false spring return, a solenoid is used
to disengage the gear for spring return. When power is
removed for more than two seconds, spring return valve
assemblies return to their normal position. Non-spring return
valve assemblies remain at their last position when power is
removed. The spring return feature should not be used for
routine, normal operation.
Spring Return and Non-Spring Return actuators with time-out
will automatically limit the running time of the actuator. The
Time-out feature automatically cuts off the control signal to
the valve after three minutes of continuous operation. Upon
change in control signal direction, the actuator will resume
operation. The controller or thermostat used to operate the
Non-Spring Return Floating actuator must be configured to
turn off the control signal after being continuously on for three
minutes.
NOTE: Do not use the manual operator while power is applied
to the actuator. If the actuator is manually positioned while
power is applied, the calibration cycle must be completed
again for the actuator to function properly. To recalibrate the
actuator, cycle power off for more than 6 seconds.
will result in damage to
April , 2016 tc © 2016 Schne ider Ele ctric. All rig hts rese rved. All trademar ks are ow ned by Sch neider Electr ic Indust ries S AS or its affi liated co mpanie s.
Document Number: F-27393-7