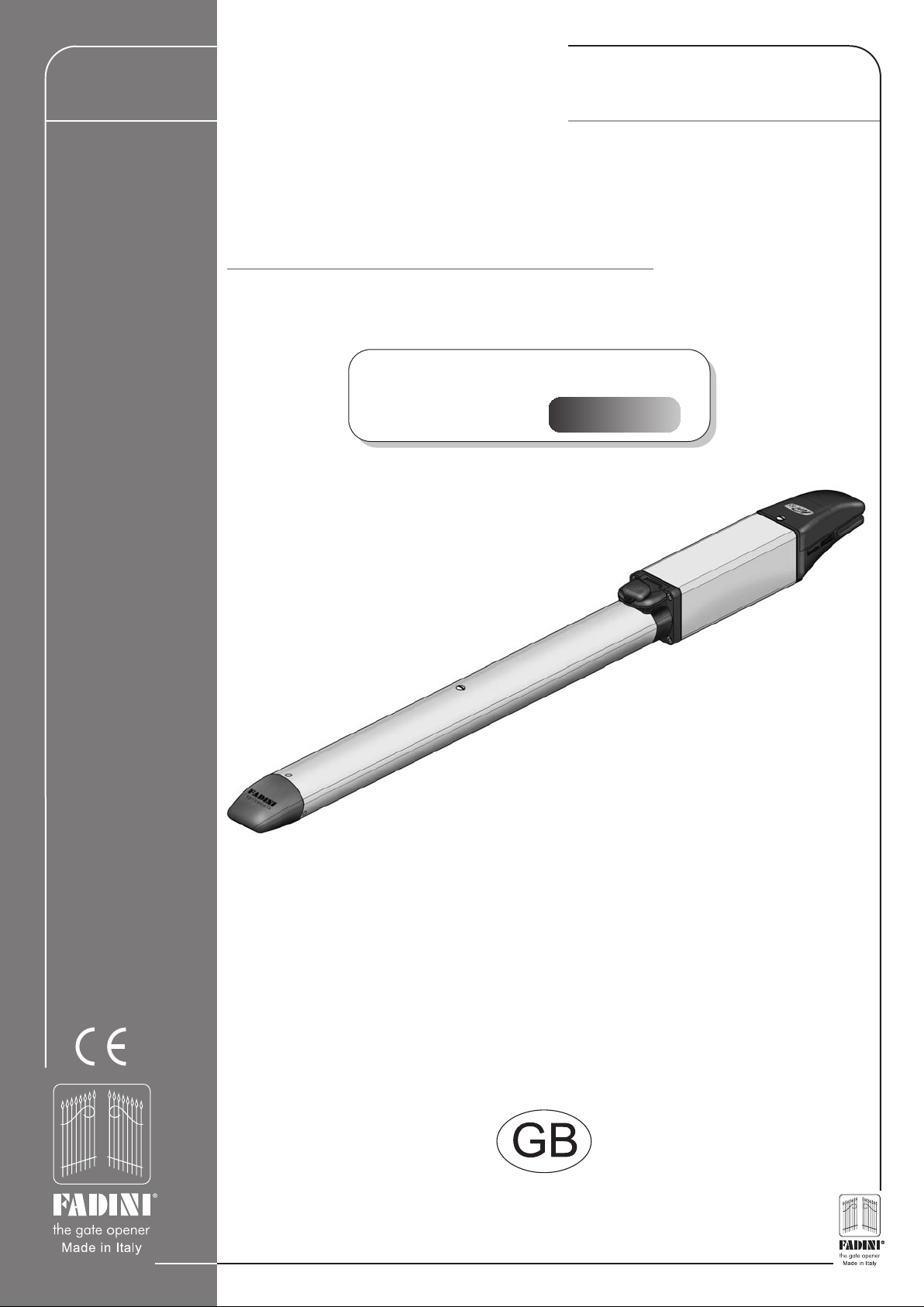
NUPI 66
Oil-hydraulic actuator for double swinging gates
Diameter øStroke 800 mm
Instructions manual
pages 9-16
9
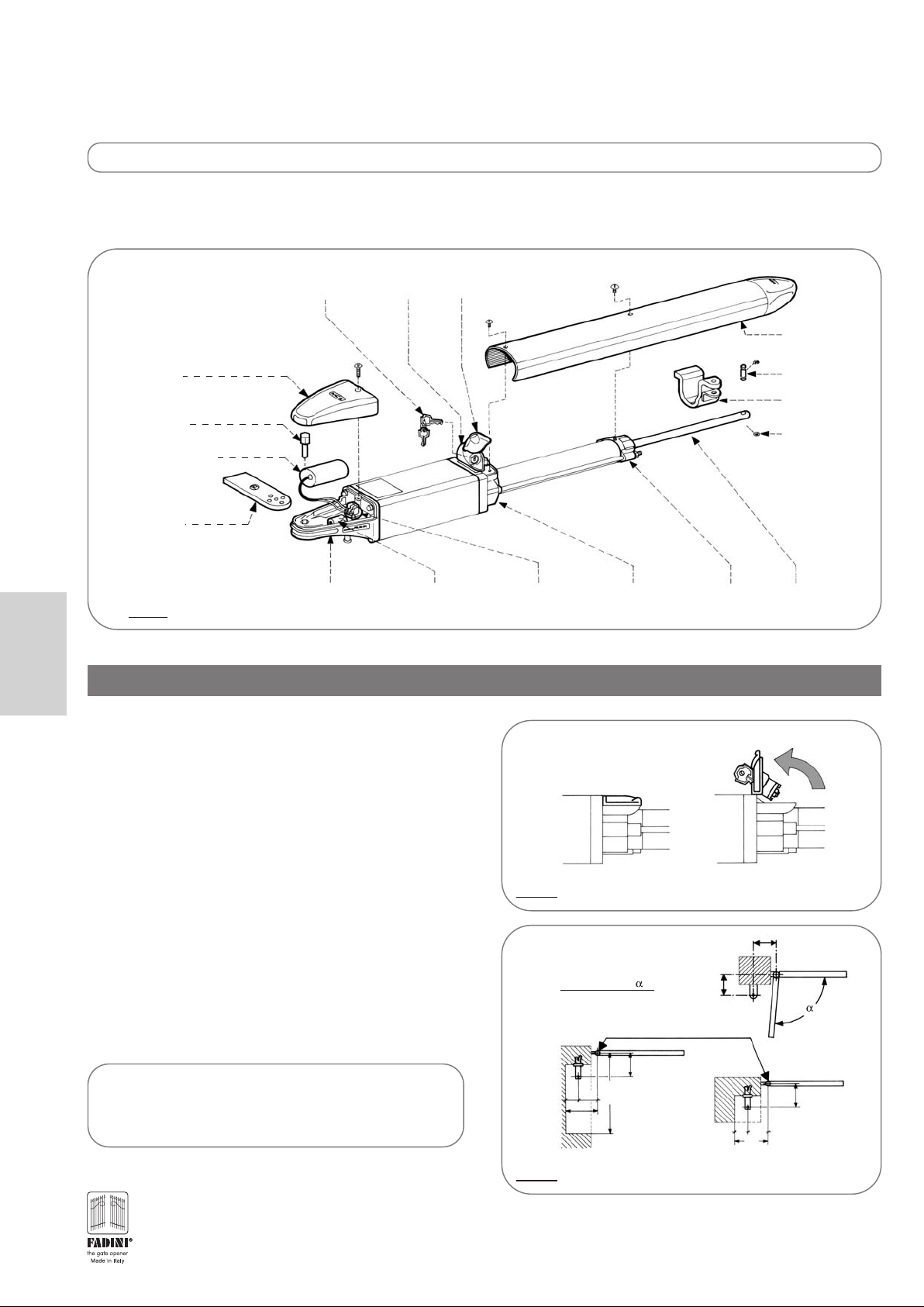
NUPI 66
FITTING INSTRUCTIONS
Important: Keep to the instructions outlined in the pages and diagrams that follow to achieve a perfect installation.
NUPI 66 is an oil-hydraulic actuator locking in the closed gate position to operate gates that are not wider than 2.0 m. Fìxing to the gate
and gate post is by specially designed brackets. Peculiar with this operator is the absence of the high/low pressure valves, power is set
and controlled by the electronic control box ELPRO 7 RP (See the description as from page 12, Elpro 7 RP wiring diagram).
RELEASE
KEY
END COVER
HEXAGONAL
HEAD PIN
12.5 μF CAPACITOR
REAR PLATE
WITH HOLES
FOR FIXING
ADJUSTMENT
REAR BRACKET
BLOCK
English
FITTING NUPI 66
PIC. 1
This explains how to remove the operator cover and fix the
actuator. The first operation is to unlock the operator: push the
lock flap to one side, insert the key and turn it 90° clockwise. The
locking barrel can be tilted open and the operator is now released
(pic. 2). Unscrew the two screws that fix the operator cover and
remove it. Unscrew the screw that fixes the rear end cover and
remove it. The actuator is so ready for fixing operations.
RELEASE
DEVICE
RELEASE
FLAP COVER
FASTENER
COVER WITH
CAP
FIXING PIN
FRONT
FIXING
BENZING
RING
TERMINALSCABLE
RELEASE VALVE
BLOCK
CLOSED
CYLINDER
HEAD
UNLOCKED GATELOCKED GATE
PISTON
SHAFT
OPEN
• Special fitting
There can be cases where special fitting requirements are needed
to meet (gate hinges on the post edge line, brickwork to be
indented, special opening,...). NUPI 66 is supplied complete with
an adjustable rear fixing pIate: a pattern of fixing holes makes
the rear fixing extremely versatile to suit any gate. Refer to the
diagram on the right for fixing geometry (pic. 3).
ELECTRIC LOCK
An electric lock is recommended in installations where
each gate leaf exceeds 1.8 meters and is subjected to high
winds or are close boarded gates.
10
PIC. 2
GATE POST 150x150mm
AB
130 130 95°
130 120 100°
70 130
PIC. 3
RELEASING SYSTEM. DETAILS.
GATE MOVEMENT CENTRES
CLOSED
130
GATE
1˙210
200
A
B
CLOSED GATE
130
70 130
200
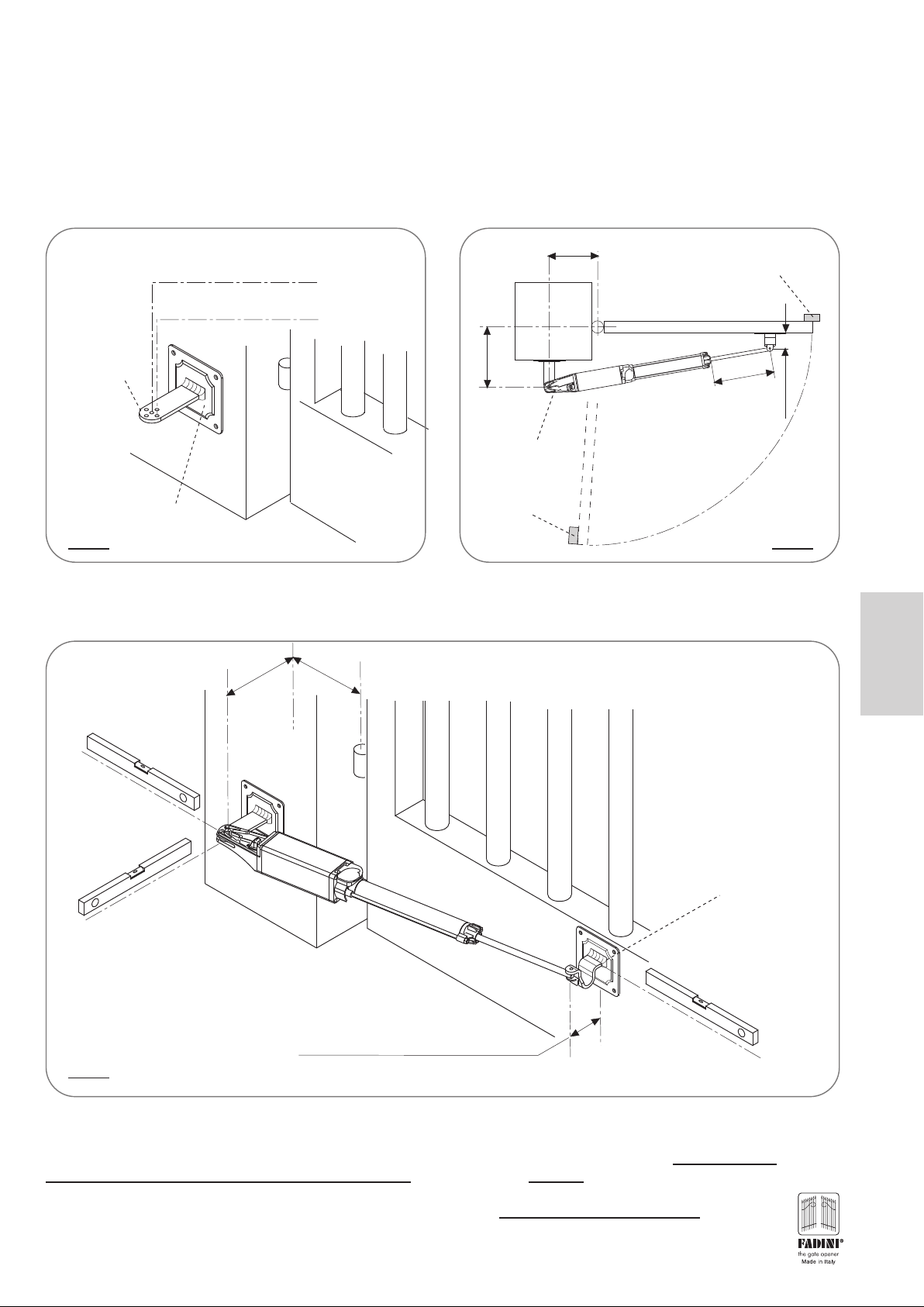
IMPORTANT: It is important to temporarily fix the operator rear casting using the center hole in the fixing plate and, once the installation
is completed, move the rear fixing to the inner hole.
IMPORTANT: it is necessary to firmly fix the gate stops to the ground in the open and closed gate positions (See pic. 5 on page 11 and
pic. 7 on page 12, parts 5 and 15) before installing the operator.
- A reinforcement plate (pic. 6) is recommended for the rear fixing, either to be embedded in the gate post, anchoring plates to be welded
to improve holding, or bolted to it so that the operator rear fixing can be welded to it in full respect of the geometry indicated below. See
distances A and B in pic.5 (distances are strictly referred to the center lines of the gate hinge and operator rear fixing)
Pierced
fixing plate
Reinforcement plate
Temporary installation axis to coincide
with center hole
Final installation axis to coincide with
inner hole
=130
B
Rear casting
Ground stop in
open gate
position
A=130
Closed gate
Ground stop in
closed gate position
260
=80
D
95°
PIC. 4 PIC. 5
- By means of a spirit level, make sure that the fixing plates are perfectly levelled, respect distance D for the front fixing, the gate in closed
position, ie. operator shaft driven 260 mm out.
A=130B=130
English
Spirit level
Never weld the front fixing
Spirit level
This distance to allow
1cm clearance between the cover
and the gate in open position
D=80
bracket directly to the gate. Use
a reinforcement plate. Remove
the operator before welding
Spirit level
PIC. 6
- At this stage NUPI 66 is fixed to the gate leaf. Note that it is locking when the release lid is closed; with the lid in the open
position the locking device is overridden and the gate can be pushed open by hand (pic.2 on page 10). The electrical connections
of the power supply cable to the terminal board are the next step. Remove the cable fastener. Connect
central terminal and the two live wires to the lateral terminals (pic. 9 on page 12) in parallel with the capacitor. Put back the
cable fastener.
On connecting the electronic control panel Elpro 7 RP, it is advised to set the
torque control switch to position 3
(pic. 10 on page 13 and pic. 11 on page 14).
the neutral to the
11