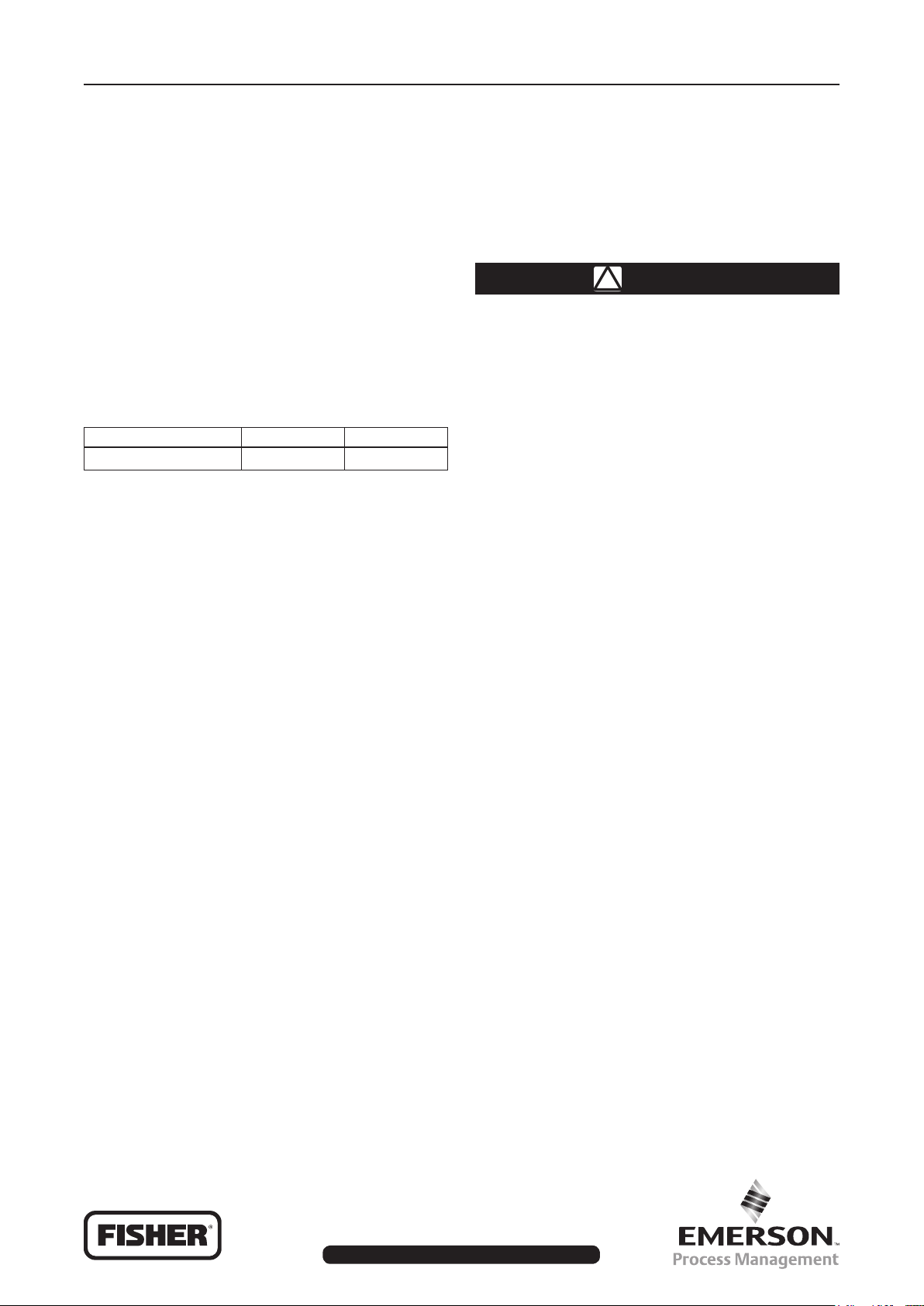
Installation Guide
English – October 2009
670 Series
Introduction
This installation guide provides instructions for
installation, startup, and adjustment. To receive a
copy of the instruction manual, contact your local
Sales Ofce or view a copy at www.emersonprocess.
com/regulators. For further information refer to: 670
Series Instruction Manual, form 965, D200109X012.
P.E.D. Categories
This product may be used as a safety accessory
with pressure equipment in the following Pressure
Equipment Directive 97/23/EC categories. It may
also be used outside of the Pressure Equipment
Directive using sound engineering practice (SEP)
per table below.
PRODUCT SIZE CATEGORIES FLUID TYPE
1/4 NPT SEP 1
Specications
Description (Regulator Type Number)
Type 670: Basic 1-gauge panel (Type 67R)
Type 670F: 1-gauge panel; regulator has lter
(Type 67AFR)
Type 670FG: 2-gauge panel; regulator has lter
(Type 67AFR)
Type 670FGV: 2-gauge panel with 3-way
changeover valve; regulator has lter
(Type 67AFR)
Type 670G: Basic 2-gauge panel (Type 67R)
Type 670GV: 2-gauge panel with 3-way or
4-way changeover valve (Type 67R)
Type 671: Basic 1-gauge panel (Type 912N)
Type 672V: Basic 1-gauge panel with 3-way
changeover valve (Type 67R)
Type 675: Basic 2-gauge panel (Type 67R)
Maximum Inlet Pressure
Types 670, 670F, 670FG, 670G, 671, and 675:
17,2 bar (250 psig)
Types 670FGV and 670GV: 3,4 bar (50 psig)
Maximum Outlet Pressure
Types 670, 670F, 670FG, 670G, and 675:
6,9 bar (100 psig)
Types 670FGV and 670GV: 3,4 bar (50 psig)
Type 671: 0,34 bar (5 psig)
Proof Test Pressure
All Pressure Retaining Components have been
proof tested per Directive 97/23/EC - Annex 1,
Section 7.4.
(1)
(1)
Maximum Emergency Outlet Pressure
Types 670, 670F, 670FG, 670G, and 675:
7,6 bar (110 psig)
Types 670FGV and 670GV: 3,8 bar (55 psig)
Type 671: 0,69 bar (10 psig)
(1)
Installation
WARNING
!
Only qualied personnel should install
or service a regulator. Regulators
should be installed, operated, and
maintained in accordance with
international and applicable codes and
regulations, and Emerson Process
Management Regulator Technologies,
Inc. instructions.
If the regulator vents uid or a
leak develops in the system, it
indicates that service is required.
Failure to take the regulator out of
service immediately may create a
hazardous condition.
Personal injury, equipment damage,
or leakage due to escaping uid
or bursting of pressure-containing
parts may result if this regulator is
overpressured or is installed where
service conditions could exceed the
limits given in the Specications
section, or where conditions exceed
any ratings of the adjacent piping or
piping connections.
To avoid such injury or damage,
provide pressure-relieving or pressurelimiting devices (as required by
the appropriate code, regulation,
or standard) to prevent service
conditions from exceeding limits.
Additionally, physical damage to the
regulator could result in personal
injury and property damage due to
escaping uid. To avoid such injury
and damage, install the regulator in a
safe location.
Clean out all pipelines before installation of the
regulator and check to be sure the regulator has
not been damaged or has collected foreign material
during shipping. For NPT bodies, apply pipe
1. The pressure/temperature limits in this installation guide and any applicable standard or code limitation should not be exceeded.
www.emersonprocess.com/regulators
D200109XUS2
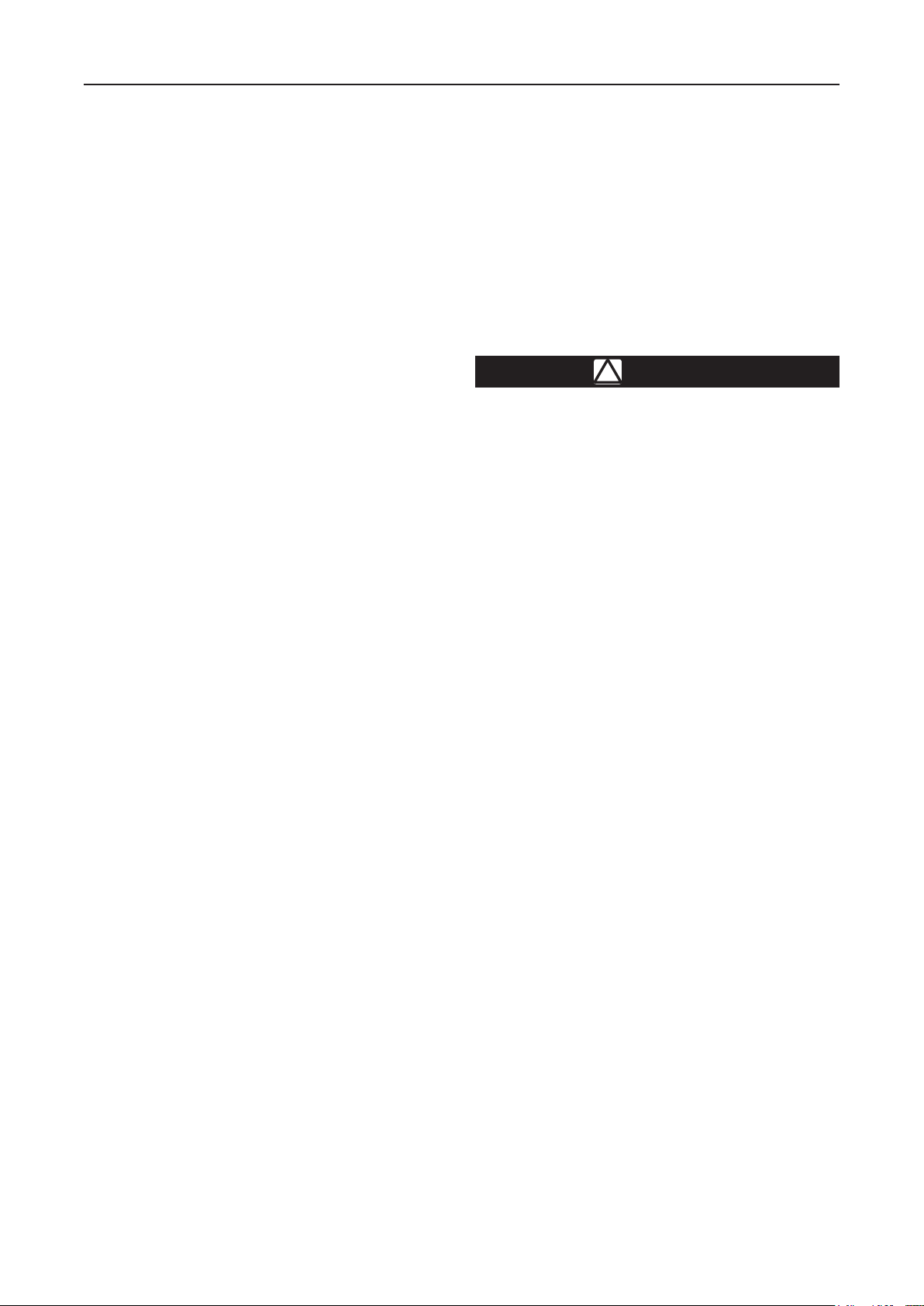
compound to the external pipe threads. For anged
bodies, use suitable line gaskets and approved
piping and bolting practices. Install the regulator
in any position desired, unless otherwise specied,
but be sure ow through the body is in the direction
indicated by the arrow on the body.
Note
It is important that the regulator be
installed so that the vent hole in the
spring case is unobstructed at all
times. For outdoor installations, the
regulator should be located away
from vehicular trafc and positioned
so that water, ice, and other foreign
materials cannot enter the spring
case through the vent. Avoid placing
the regulator beneath eaves or
downspouts, and be sure it is above
the probable snow level.
Overpressure Protection
The recommended pressure limitations are
stamped on the regulator nameplate. Some type of
overpressure protection is needed if the actual inlet
pressure exceeds the maximum operating outlet
pressure rating. Overpressure protection should
also be provided if the regulator inlet pressure
is greater than the safe working pressure of the
downstream equipment.
Regulator operation below the maximum pressure
limitations does not preclude the possibility of
damage from external sources or debris in the line.
The regulator should be inspected for damage after
any overpressure condition.
Startup
The regulator is factory set at approximately
the midpoint of the spring range or the pressure
requested, so an initial adjustment may be required
to give the desired results. With proper installation
completed and relief valves properly adjusted, slowly
open the upstream and downstream shutoff valves.
Adjustment
To change the outlet pressure, remove the closing
cap or loosen the locknut and turn the adjusting
screw clockwise to increase outlet pressure or
counterclockwise to decrease pressure. Monitor
the outlet pressure with a test gauge during the
adjustment. Replace the closing cap or tighten the
locknut to maintain the desired setting.
Taking Out of Service (Shutdown)
WARNING
!
To avoid personal injury resulting from
sudden release of pressure, isolate
the regulator from all pressure before
attempting disassembly.
Parts List
Key Description
1 Regulator
2 Gauge
3 Panel
4 Clamp Bar
5 Hex Nut
6 Machine Screw
7 Tubing
8 Fitting
9 Fitting
10 Nipple
11 Fitting
12 Tubing
13 Changeover Valve
15 Gauge Service Marking
16 Machine Screw
17 Fitting
18 Valve Dial
19 Machine Screw
20 Tubing
24 Bleed Orice and Screen Assembly
25 Serial Plate
26 Hex Nut
27 Fitting
28 Fitting