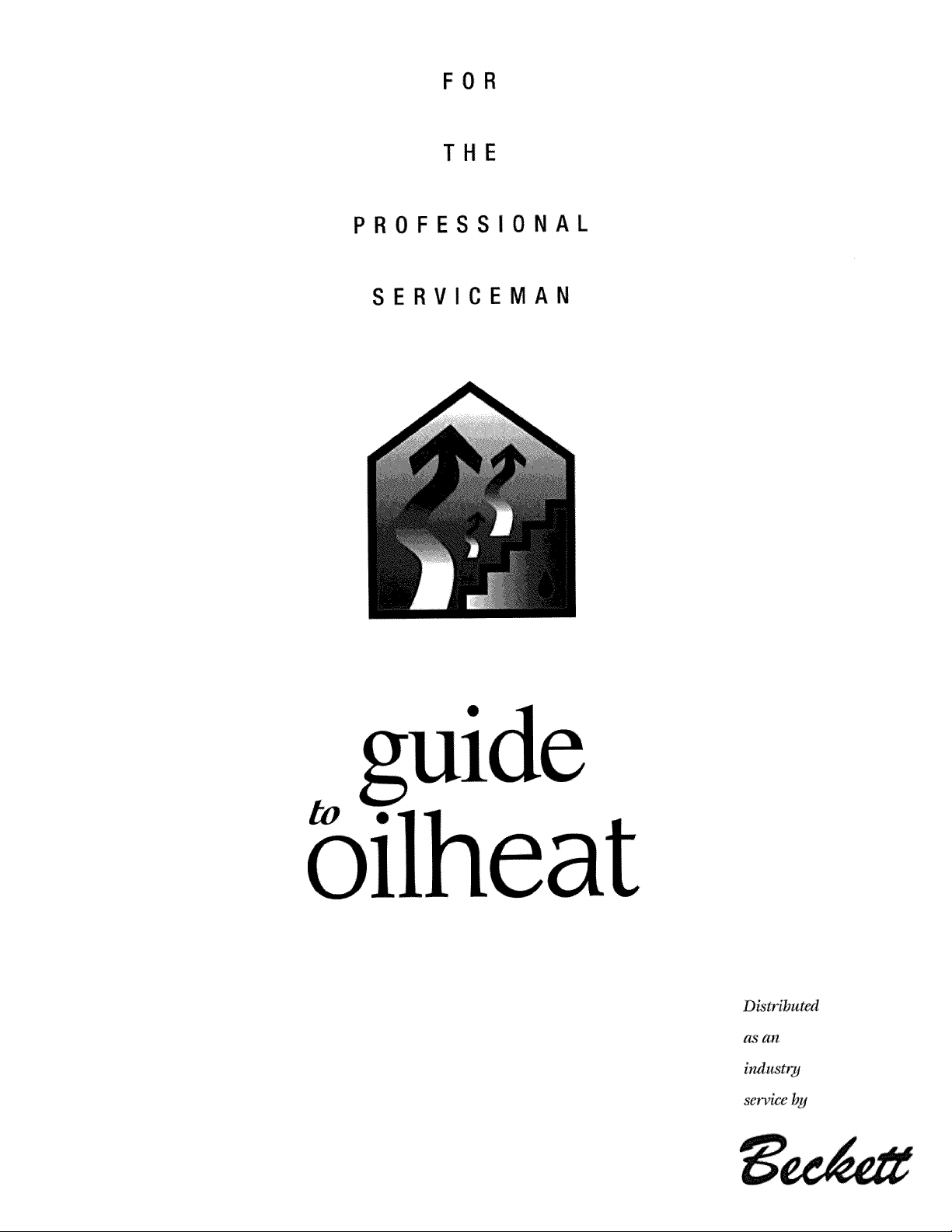
FOR
THE
PROFESSIONAL
SERVICEMAN
to
at
D_tt_buted
as (t,_z
iru4ustrtj
serviceb_
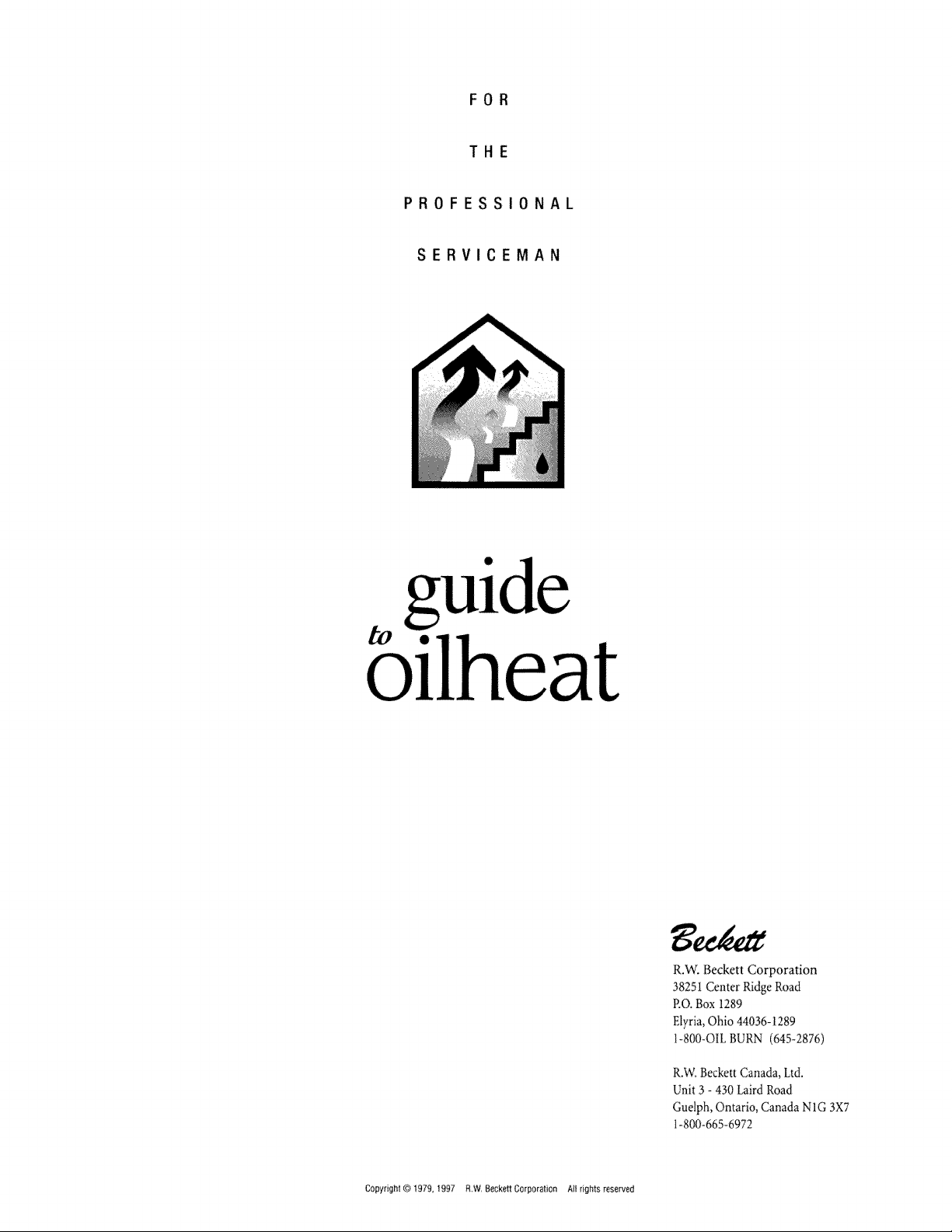
FOR
THE
PROFESSIONAL
SERVICEMAN
at
R/C,: Beckett Corporation
38251 Center Ridge Road
P.O. Box 1289
Elyria, Ohio 44036- !289
1-800_OIL BURN (645-2876)
R.W,BeckettCanada, Ltd.
Unit 3 - 430LairdRoad
Guelph, Ontario, Canada NIG 3X7
1-800-665-6972
Copyright @ 1979, i997 RW, BeckettCorporation All rights reserved
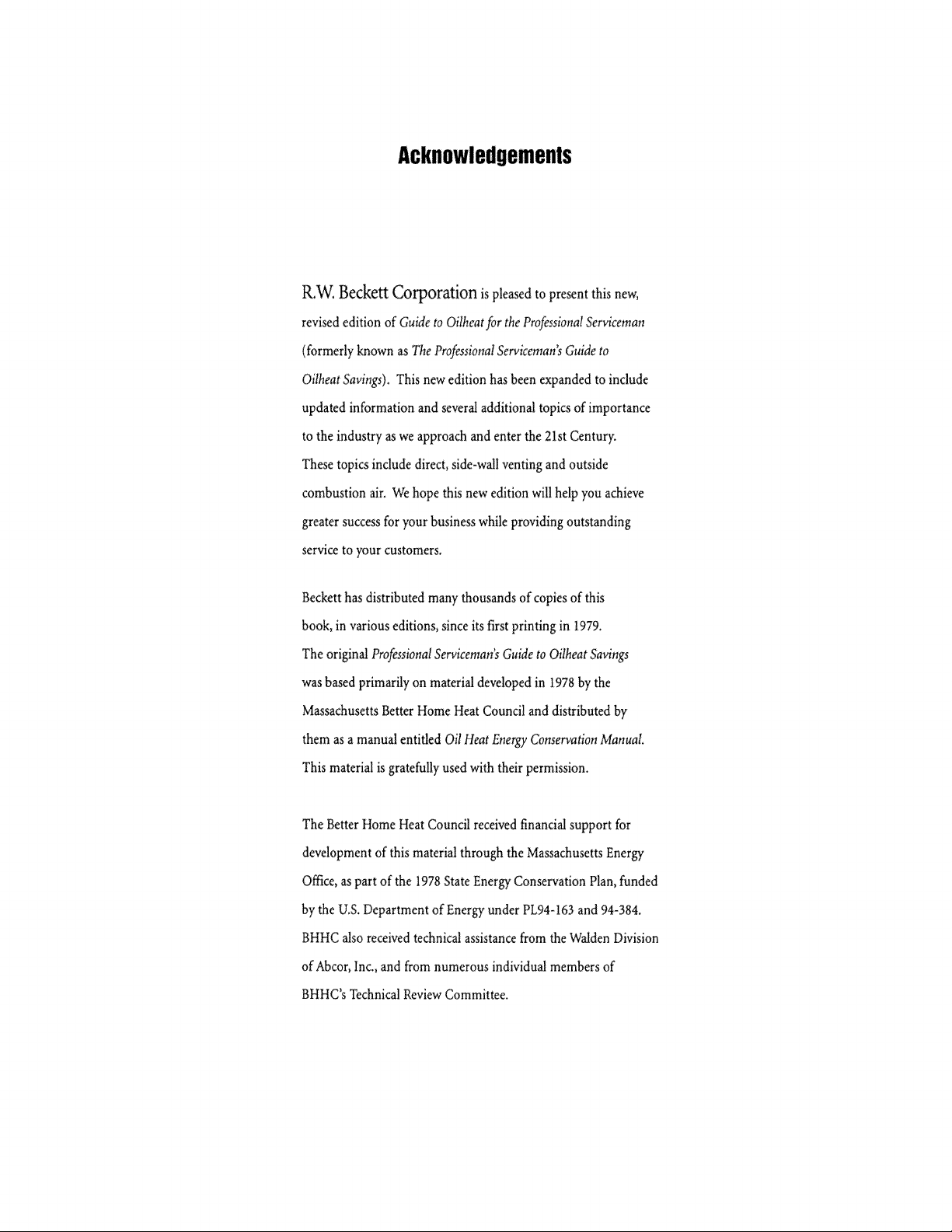
Acknowledgements
R.W.BeckettCorporation is pleased to presentthis new,
revised edition of Guideto Oilheatfor the ProfessionalServiceman
(formerly known as The ProfessionalServiceman's Guide to
Oilheat Savings). This new edition has been expanded to include
updated information and several additional topics of importance
to the industry as we approach and enter the 21st Century.
These topics include direct, side-wall venting and outside
combustion air. We hope this new edition willhelp you achieve
greater success for your business while providing outstanding
service to your customers.
Beckett has distributed many thousands of copies of [his
book, in various editions, since its first printing in 1979.
The original ProfessionalServiceman's Guide to Oilheat Savings
was based primarily on material developed in 1978 by the
Massachusetts Better Home Heat Council and distributed by
them as a manual entitled Oil Heat Energy ConservationManual.
This material is gratefully used with their permission.
The Better Home Heat Council received finandal support for
development of this material through the Massachusetts Energy
Office, as part of the 1978 State Energy Conservation Plan, funded
by the U.S. Department of Energy under PL94-163 and 94-384.
BHHC also received technical assistance from the Walden Division
of Abcor, Inc., and from numerous individual members of
BHHCs Technical Review Committee.
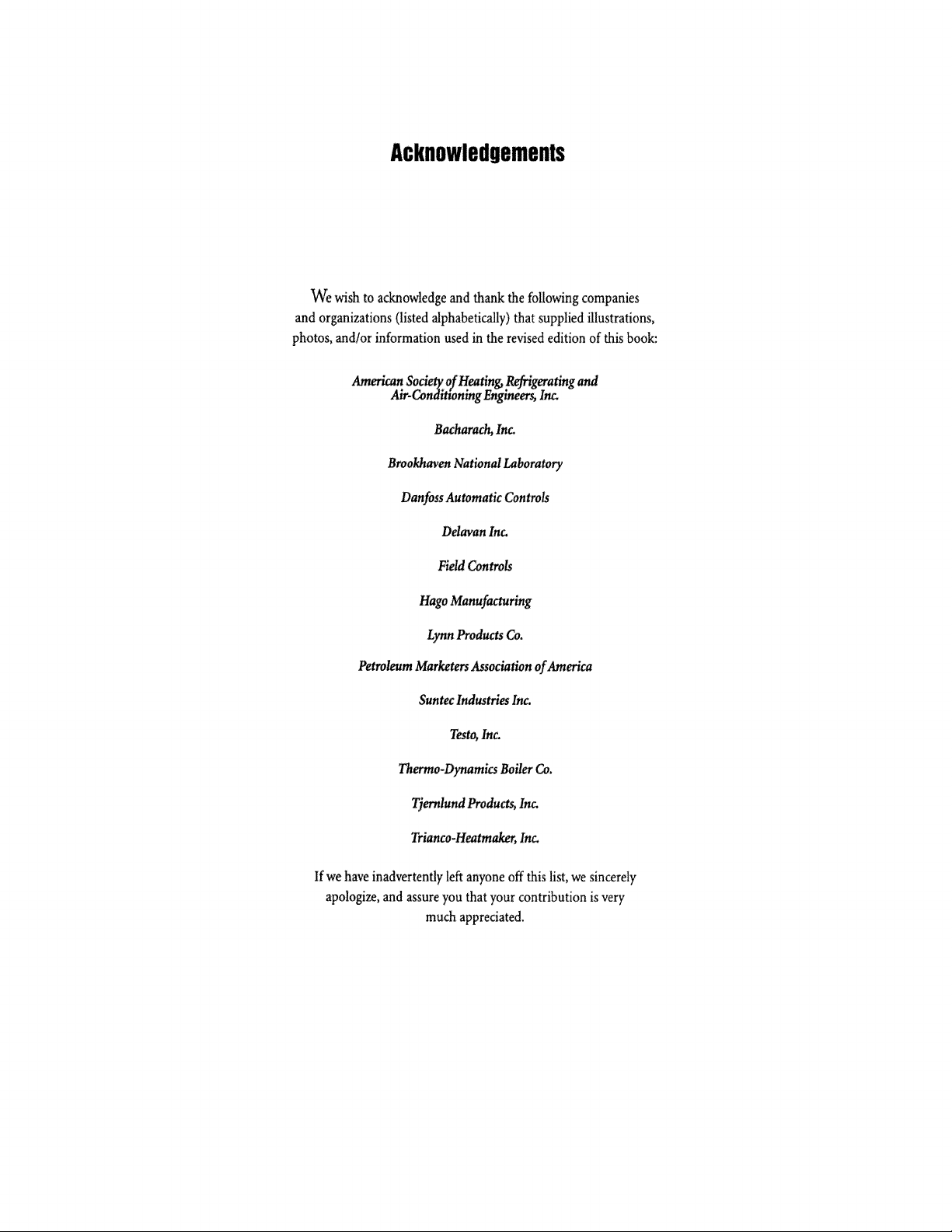
Acknowledgements
VCewishto acknowledgeandthank the followingcompanies
and organizations (listedalphabetically)that suppliedillustrations,
photos, and/or information used in the revisededitionof thisbook:
Bacharach,Inc.
Broo'yahavenNationalLaboratory
DanfossAutomaticControls
DelavanInc.
FieldControls
HagoManufacturing
LynnProductsCo.
PetroleumMarketersAssociationofAmerica
$untecIndustriesIra:.
Testo,Inc.
Thermo-DynamicsBoilerCo.
TjernlundProducts,Inc.
Trianco-Heatmak_r,Inc.
Ifwe haveinadvertentlyleftanyoneoffthis list,wesincerely
apologize,and assureyou that your contribution isvery
much appreciated.
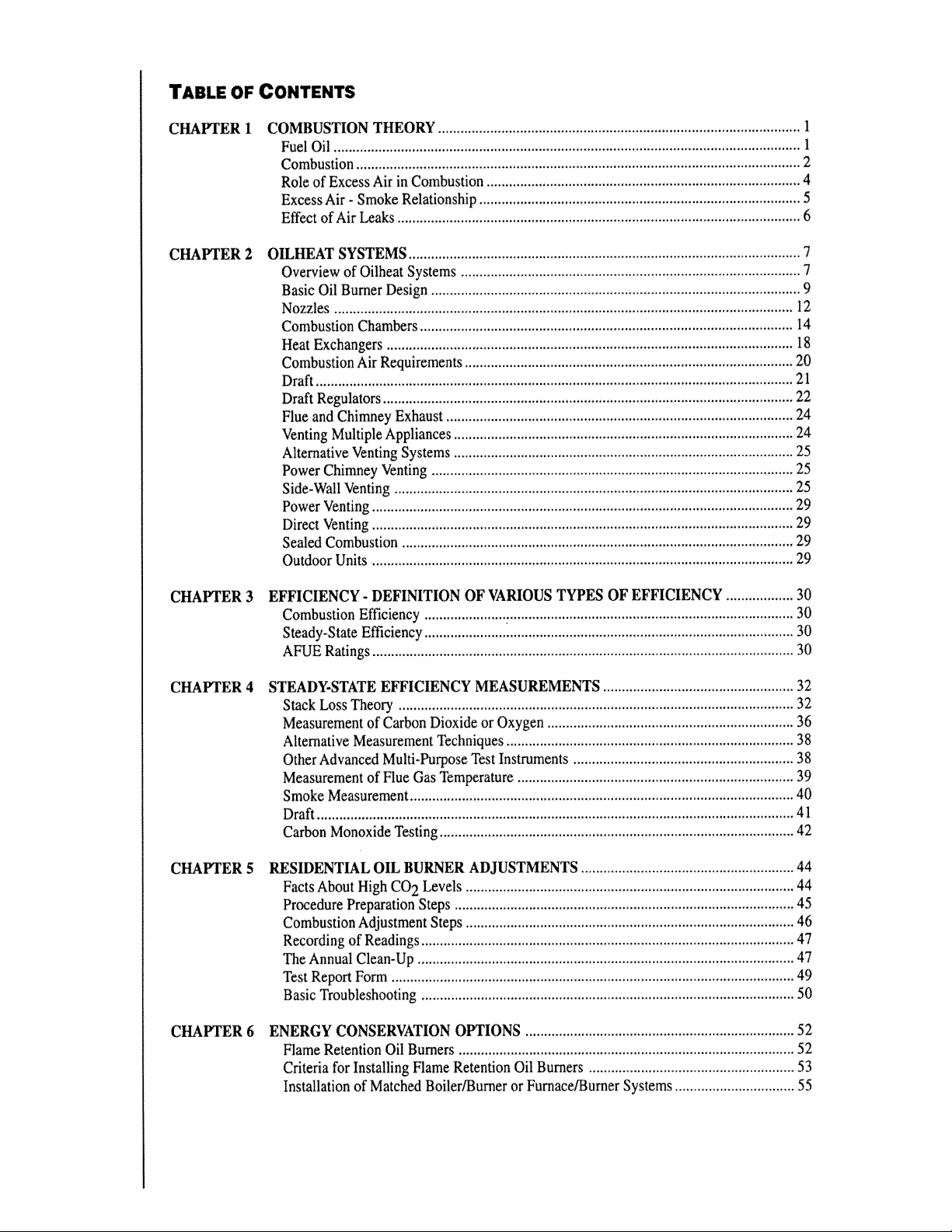
TABLE OF CONTENTS
CHAPTER 1
CtD_FrER 2
COMBUSTION THEORY ................................................................................................. 1
Fuel Oil ............................................................................................................................. 1
Combustion ....................................................................................................................... 2
Role of Excess Air in Combustion .................................................................................... 4
Excess Air - Smoke Relationship ....................................................................................... 5
Effect of Air Leaks ............................................................................................................ 6
OILHEAT SYSTEMS ......................................................................................................... 7
Overview of Oilheat Systems ........................................................................................... 7
Basic Oil Burner Design ................................................................................................... 9
Nozzles ........................................................................................................................... 12
Combustion Chambers .................................................................................................... 14
Heat Exchangers ............................................................................................................. 18
Combustion Air Requirements ........................................................................................ 20
Draft ................................................................................................................................ 21
Draft Regulators .............................................................................................................. 22
Flue and Chimney Exhaust ............................................................................................. 24
"ventingMultiple Appliances ........................................................................................... 24
Alternative "venting Systems ........................................................................................... 25
Power Chimney Venting ................................................................................................. 25
Side-Wall Venting ........................................................................................................... 25
PowerVenting ................................................................................................................. 29
Direct Venting ................................................................................................................. 29
Sealed Combustion ......................................................................................................... 29
Outdoor Units ................................................................................................................. 29
CHAPTER 3
EFFICIENCY - DEFINITION OF VARIOUS TYPES OF EFFICIENCY .................. 30
Combustion Efficiency ...................... ............................................................................. 30
Steady_State Efficiency ................................................................................................... 30
AFUE Ratings ................................................................................................................. 30
CHAPTER 4 STEADY-STATE EFFICIENCY MEASUREMENTS ................................................... 32
Stack Loss Theory .......................................................................................................... 32
Measurement of Carbon Dioxide or Oxygen .................................................................. 36
Alternative Measurement Techniques ............................................................................. 38
Other Advanced Multi-Purpose Test Instruments ........................................................... 38
Measurement of Flue Gas %mperature .......................................................................... 39
Smoke Measurement ....................................................................................................... 40
Draft................................................................................................................................ 41
Carbon Monoxide Testing ............................................................................................... 42
CHAPTER 5 RESIDENTIAL OIL BURNER ADJUSTMENTS ......................................................... 44
Facts About High CO 2 Levels ........................................................................................ 44
Procedure Preparation Steps ......................................................................................... 45
Combustion Adjustment Steps ........................................................................................ 46
Recording of Readings .................................................................................................... 47
The Annual Clean-Up ..................................................................................................... 47
Test Report Form ............................................................................................................ 49
Basic Troubleshooting .................................................................................................... 50
CHAPTER 6 ENERGY CONSERVATION OPTIONS ........................................................................ 52
Flame Retention Oil Burners .......................................................................................... 52
Criteria for Installing Name Retention Oil Burners ....................................................... 53
Installation of Matched BoileffBurner or Furnace/Burner Systems ................................ 55
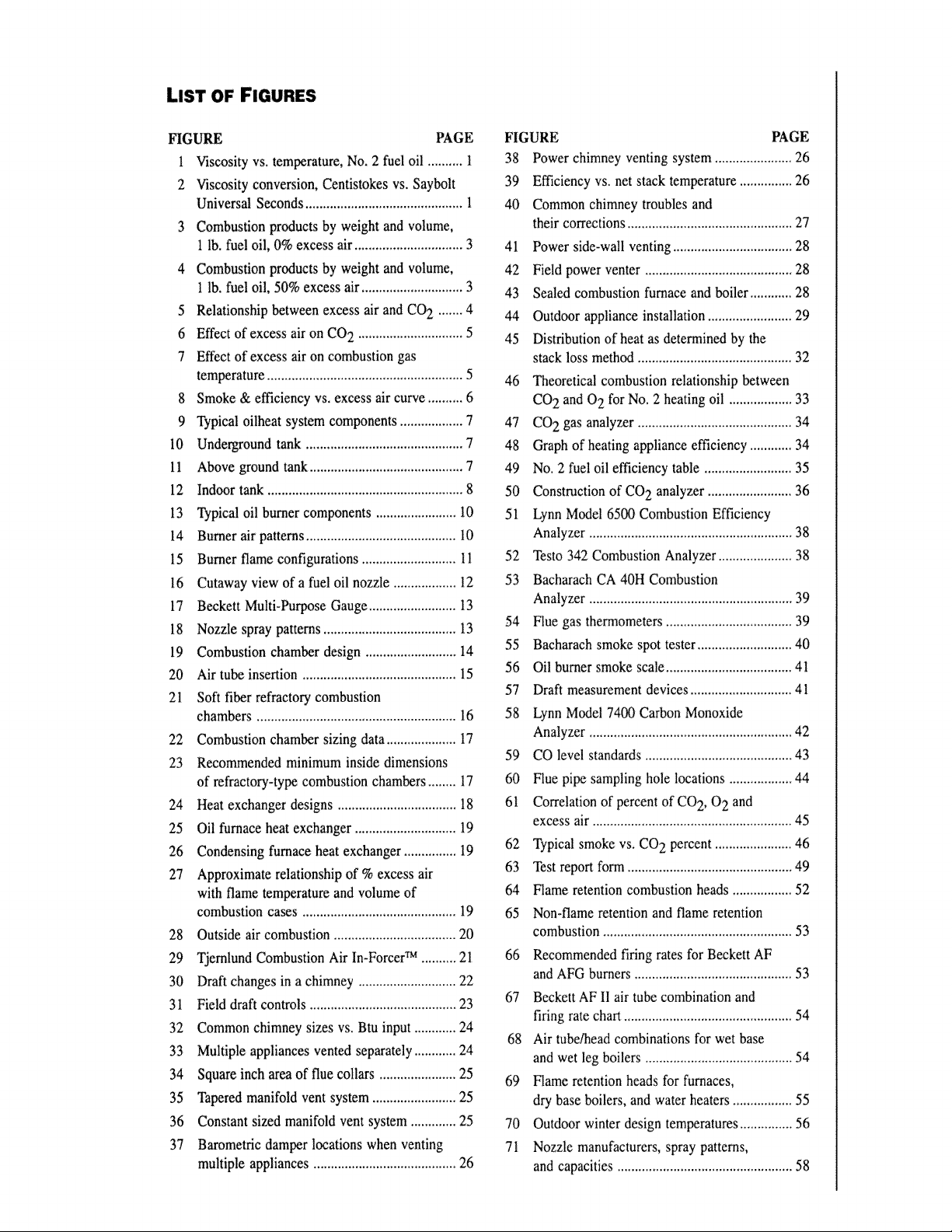
LIST OF FIGURES
FIGURE PAGE
1 Viscosity vs. temperature, No. 2 fuel oil .......... 1
2 "viscosityconversion, Centistokes vs. Saybolt
Universal Seconds............................................. 1
3 Combustion products by weight and volume,
1lb. fuel oil, 0% excess air...............................3
4 Combustion products by weight and volume,
1lb. fuel oil, 50% excess air.............................3
5 Relationship between excess air and CO2 .......4
6 Effect of excess air on CO2 ..............................5
7 Effect of excess air on combustion gas
temperature ........................................................ 5
8 Smoke &efficiency vs. excess air curve ..........6
9 Typical oilheat system components .................. 7
10 Underground tank .............................................7
11 Above ground tank............................................7
12 Indoor tank ........................................................8
13 Typical oil burner components ....................... 10
14 Burner air patterns ........................................... 10
15 Burner flame configurations ........................... 11
16 Cutaway view of a fuel oil nozzle .................. 12
17 Beckett Multi-Purpose Gauge......................... 13
18 Nozzle spray patterns ...................................... !3
19 Combustion chamber design .......................... 14
20 Air tube insertion ............................................ 15
21 Soft fiber refractory combustion
chambers ......................................................... 16
22 Combustion chamber sizing data.................... t7
23 Recommended minimum inside dimensions
of refractory-type combustion chambers ........ 17
24 Heat exchanger designs .................................. !8
25 Oil furnace heat exchanger ............................. 19
26 Condensing furnace heat exchanger ............... 19
27 Approximate relationship of % excess air
with flame temperature and volume of
combustion cases ............................................ 19
28 Outside air combustion ................................... 20
29 Tjernlund Combustion Air In-ForcerTM ..........21
30 Draft changes in a chimney ............................ 22
31 Field draft controls ..........................................23
32 Common chimney sizes vs. Btuinput ............ 24
33 Multiple appliances vented separately ............ 24
34 Square inch area of flue collars ......................25
35 Tapered manifold vent system ........................ 25
36 Constant sized manifold vent system .............25
37 Barometric damper locations when venting
multiple appliances .........................................26
FIGURE
38
Power chimney venting system ..................... 26
39
Efficiency vs. net stack temperature ............... 26
40
Common chimney troubles and
theircorrections ............................................... 27
41 Power side-wall venting.................................. 28
42 Field power venter .......................................... 28
43 Sealed combustion furnace and boiler ............ 28
44 Outdoor appliance installation ........................ 29
45 Distribution of heat as determined by the
stack loss method ............................................32
46 Theoretical combustion relationship between
CO2 and 0 2for No. 2 heating oil .................. 33
47 CO2 gas analyzer ............................................ 34
48 Graph of heating appliance efficiency ............ 34
49 No. 2 fuel oil efficiency table ......................... 35
50 Construction of CO2 analyzer ........................ 36
51 Lynn Model 6500 Combustion Efficiency
Analyzer .......................................................... 38
52 Testo 342 Combustion Analyzer .....................38
53 Bacharach CA 40H Combustion
Analyzer .......................................................... 39
54 Flue gas thermometers .................................... 39
55 Bacharach smoke spot tester........................... 40
56 Oil burner smoke scale.................................... 41
57 Draft measurement devices ............................. 41
58 Lynn Model 7400 Carbon Monoxide
Analyzer .......................................................... 42
59 CO level standards .......................................... 43
60 Flue pipe sampling hole locations ..................44
61 Correlation of percent of CO2, 02 and
excess air ......................................................... 45
62 Typical smoke vs, CO2 percent ...................... 46
63 Test report form ............................................... 49
64 Name retention combustion heads ................. 52
65 Non-flame retention and flame retention
combustion ...................................................... 53
66 Recommended firing rates for Beckett AF
andAFG burners ............................................. 53
67 Beckett AF II air tube combination and
firing rate chart ................................................ 54
68 Air tube/head combinations for wet base
and wet legboilers ..........................................54
69 Name retention heads for furnaces,
dry base boilers, and water heaters ................. 55
70 Outdoor winter design temperatures............... 56
7t Nozzle manufacturers, spray patterns,
and capacities ..................................................58
PAGE
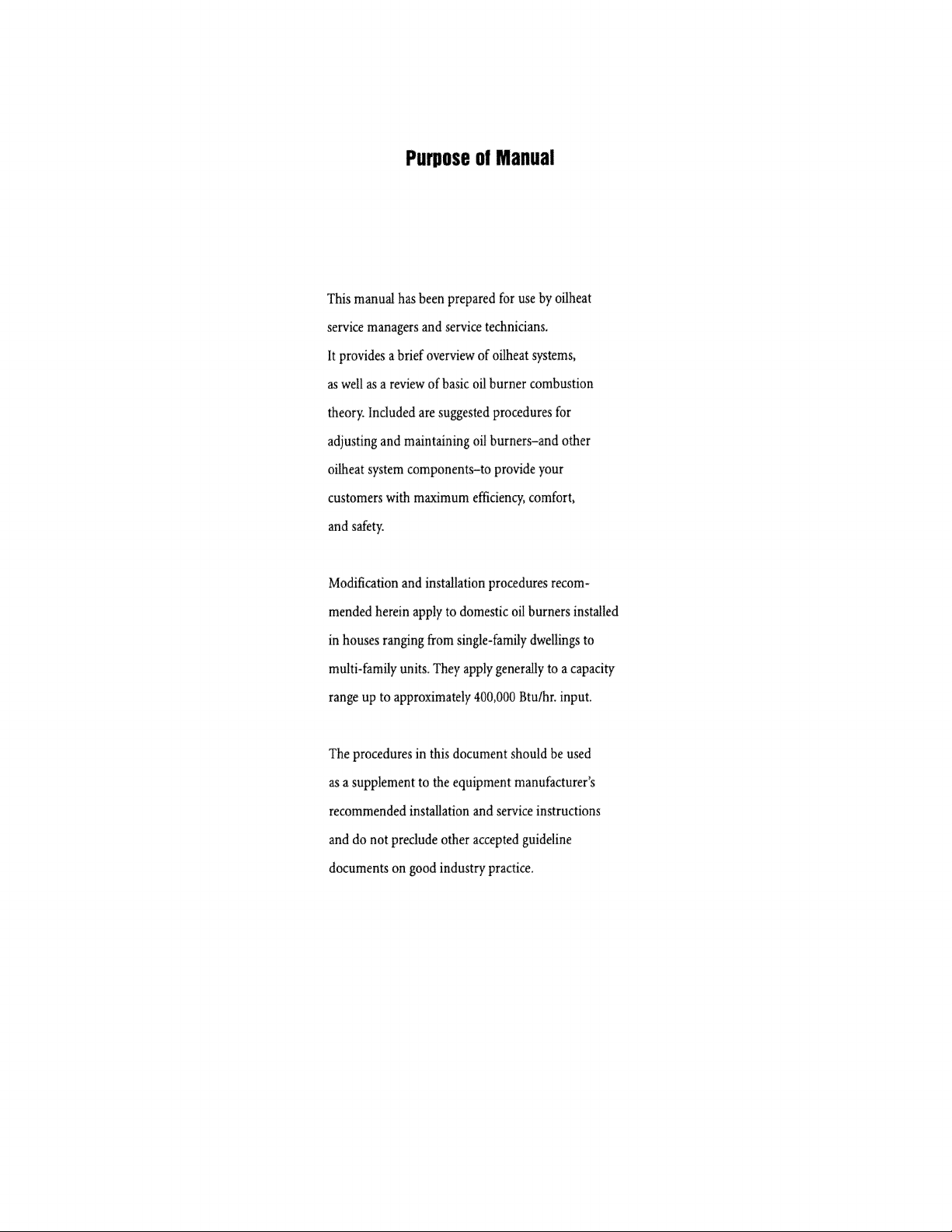
PurposeofManual
This manual has been prepared for use by oilheat
service managers and service technicians_
It provides a brief overview of oilheat systems,
as well as a review of basic oil burner combustion
theory. Included are suggested procedures for
adjusting and maintaining oil burners-and other
oilheat system components-to provide your
customers with maximum efficiency,comfort,
and safety.
Modification and installation procedures recom-
mended herein apply to domestic oil burners installed
in houses ranging from single-family dwellings to
multi-family units They apply generally to acapacity
range up to approximately 400,000 Btu/hr. input.
The proceduresin this documentshould beused
asa supplement to the equipmentmanufacturer's
recommendedinstallationand serviceinstructions
and do not precludeother acceptedguideline
documents on good industrypractice,
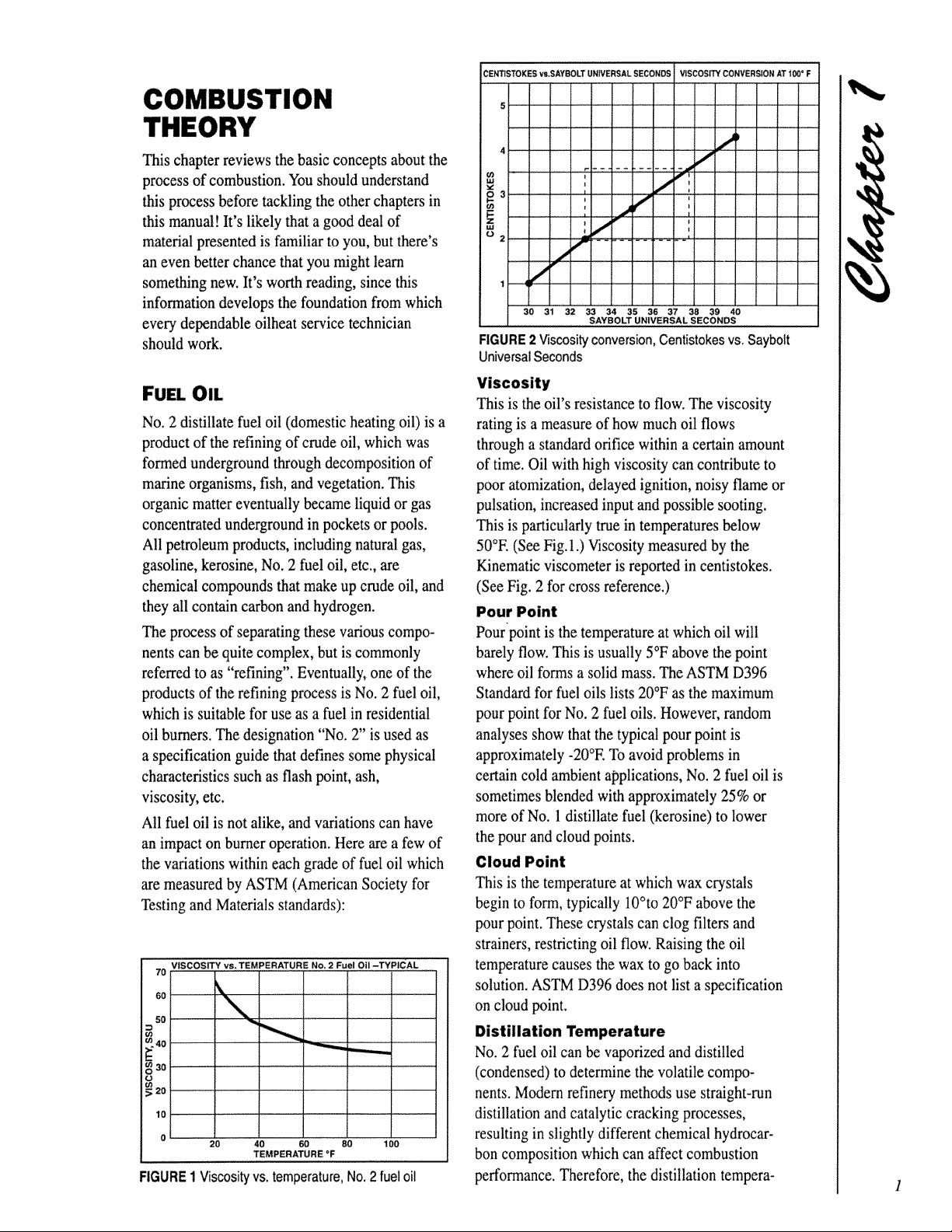
This chapter reviews the basic concepts about the
process of combustion. You should understand
this process before tackling the other chapters in
this manual! It's likely that a good deal of
material presented is familiar to you, but there's
an even better chance that you might learn
something new. It's worth reading, since this
information develops the foundation from which
every dependable oilheat service technician
should work.
CENT1STOKESvs.SAYSOLTUNWERSAL SECONDS VISCOSITy"CONVERSION ATi 00' F
5
iUJ _
02 _,. ............ ,
,/
1
3o 3"I _2 3'334 3s 36 37 _ 39 40
FIGURE 2 \_scosity conversion,Centistokesvs.Saybolt
UniversalSeconds
SAYBOLT UNIVERSAL SECONDS
FUEL OIL
No. 2 distillate fuel oil (domestic heating oil) is a
product of the refining of crude oil, which was
formed underground through decomposition of
marine organisms, fish, and vegetation. This
organic matter eventually became liquid or gas
concentrated underground in pockets or pools.
All petroleum products, including natural gas,
gasoline, kerosine, No, 2 fuel oil, etc., axe
chemical compounds that make up crude oil, and
they all contain carbon and hydrogen.
The process of separating these various compo-
nents can be quite complex, but is commonly
referred to as "refining". Eventually, one of the
products of the refining process is No. 2 fuel oil,
which is suitable for use as a fuel in residential
oil burners. The designation "No. 2" is used as
a specification guide that defines some physical
characteristics such as flash point, ash,
viscosity, etc.
All fuel oil is not alike, and variations can have
an impact on burner operation. Here are a few of
the variations within each grade of fuel oil which
are measured by ASTM (American Society for
Testing and Materials standards):
VISCOSITY vs. TEMPERATURE No, 2 Fuel Oil -TYPICAL
_0
30 -- _'%._%.
I0
20 40 60 80 100
TEMPERATURE _F
FIGURE 1 Viscosity vs. temperature, No. 2 fuel oil
This is the oil's resistance to flow. The viscosity
rating is a measure of how much oil flows
through a standard orifice within a certain amount
of time. Oil with high viscosity can contribute to
poor atomization, delayed ignition, noisy flame or
pulsation, increased input and possible sooting.
This is particularly true in temperatures below
50°E (See Fig, 1,) Viscosity measured by the
Kinematic viscometer is reported in centistokes.
(See Fig. 2 for cross reference.)
Pour Point
Pourpoint is the temperature at which oil will
barely flow. This is usually 5°F above the point
where oil forms a solid mass. The ASTM D396
Standard for fuel oils lists 20°F as the maximum
pour point for No. 2 fuel oils. However, random
analyses show that the typical pour point is
approximately -20°E To avoid problems in
certain cold ambient applications, No. 2 fuel oil is
sometimes blended with approximately 25% or
more of No. 1 distillate fuel (kerosine) to lower
the pour and cloud points.
Cloud Point
This is the temperature at which wax crystals
begin to form, typically 10°to 20°F above the
pour point. These crystals can clog filters and
strainers, restricting oil flow. Raising the oil
temperature causes the wax to go back into
solution. ASTM D396 does not list a specification
on cloud point.
Distillation Temperature
No. 2 fuel oil can be vaporized and distilled
(condensed) to determine the volatile compo-
nents. Modern refinery methods use straight-run
distillation and catalytic cracking processes,
resulting in slightly different chemical hydrocar-
bon composition which can affect combustion
performance. Therefore, the distillation tempera-
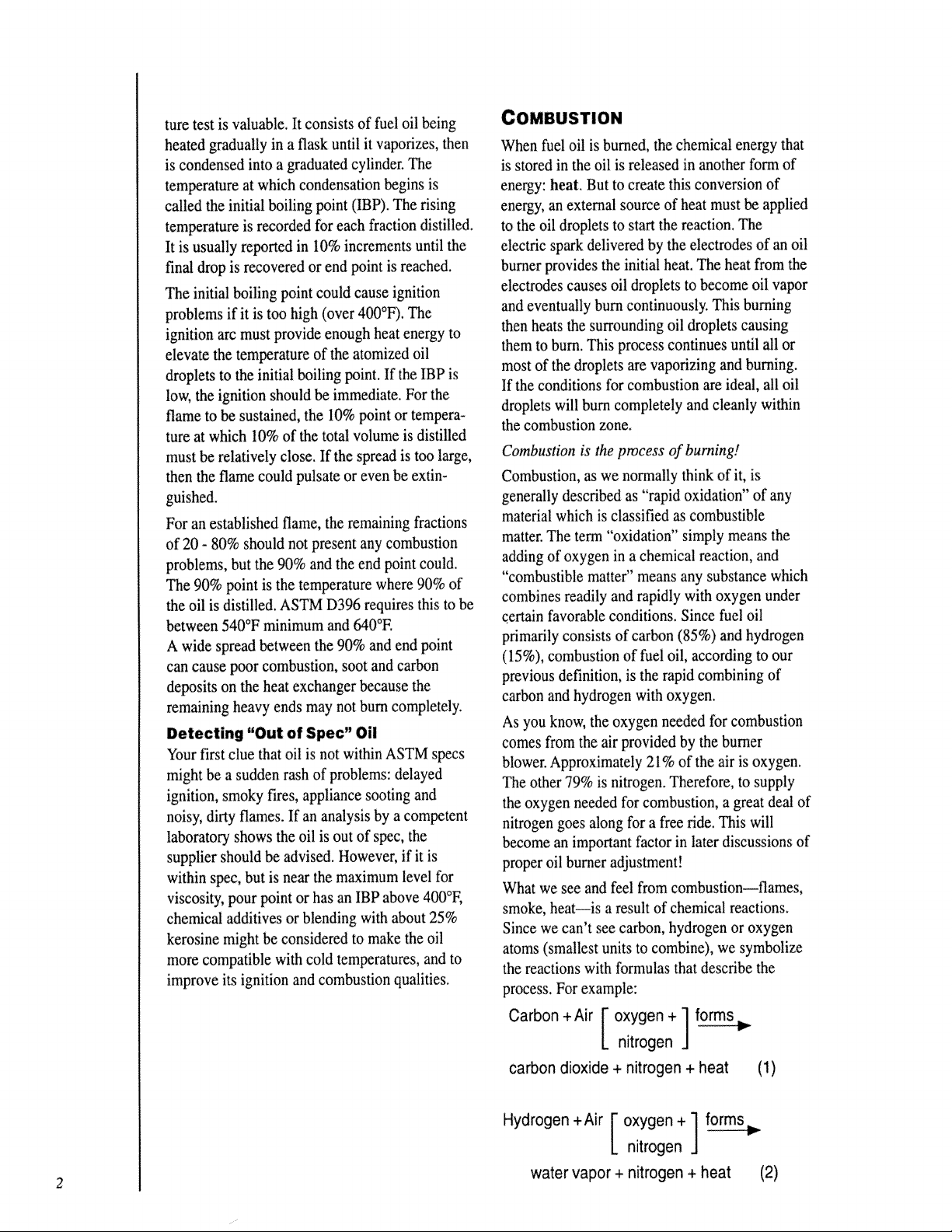
turetestisvaluable.It consistsoffueloilbeing
heatedgraduallyinaflaskuntilitvaporizes,then
iscondensedintoagraduatedcylinder.The
temperatureatwhichcondensationbeginsis
calledtheinitialboilingpoint(IBP).Therising
temperatureisrecordedforeachfractiondistilled.
Itisusuallyreportedin10%incrementsuntilthe
finaldropisrecoveredorendpointisreached.
Theinitialboilingpointcouldcauseignition
problemsif itistoohigh(over400°F).The
ignitionarcmustprovideenoughheatenergyto
elevatethetemperatureoftheatomizedoil
dropletstotheinitialboilingpoint.If theIBPis
low,theignitionshouldbeimmediate.Forthe
flametobesustained,the10%pointortempera-
tureatwhich10%ofthetotalvolumeisdistilled
mustberelativelyclose.If thespreadistoolarge,
thentheflamecouldpulsateorevenbeextin-
guished.
Foranestablishedflame,theremainingfractions
of20-80%shouldnotpresentanycombustion
problems,butthe90%andtheendpointcould.
The90%pointisthetemperaturewhere90%of
theoilisdistilled.ASTMD396requiresthistobe
between540°Fminimumand640°E
Awidespreadbetweenthe90%andendpoint
cancausepoorcombustion,sootaridcarbon
depositsontheheatexchangerbecausethe
remainingheavyendsmaynotburncompletely.
Detecting "Out of Spec" Oil
Your first clue that oil is not within ASTM specs
might be a sudden rash of problems: delayed
ignition, smoky fires, appliance sooting and
noisy, dirty flames. If an analysis by a competent
laboratory shows the oil is out of spec, the
supplier should be advised. However, if it is
within spec, but is near the maximum level for
viscosity, pour point or has an IBP above 400°E
chemical additives or blending with about 25%
kerosine might be considered to make the oil
more compatible with cold temperatures, and to
improve its ignition and combustion qualities.
COMBUSTION
When fuel oil is burned, the chemical energy that
is stored in the oil is released in another form of
energy: heat. But to create this conversion of
energy, an external source of heat must be applied
to the oil droplets to start the reaction. The
electric spark delivered by the electrodes of an oil
burner provides the initial heat. The heat from the
electrodes causes oil droplets to become oil vapor
and eventually burn continuously. This burning
then heats the surrounding oil droplets causing
them to bum. This process continues until all or
most of the droplets are vaporizing and burning.
If the conditions for combustion are ideal, all oil
droplets will burn completely and cleanly within
the combustion zone.
Combustion is the process of burning, p
Combustion, as we normally think of it, is
generally described as "rapid oxidation" of any
material which is classified as combustible
matter. The term "oxidation" simply means the
adding of oxygen in a chemical reaction, and
"combustible matter" means any substance which
combines readily and rapidly with oxygen under
certain favorable conditions. Since fuel oil
primarily consists of carbon (85%) and hydrogen
(15%), combustion of fuel oil, according to our
previous definition, is the rapid combining of
carbon and hydrogen with oxygen.
As you know, the oxygen needed for combustion
comes from the air provided by the burner
blower. Approximately 21% of the air is oxygen.
The other 79% is nitrogen. Therefore, to supply
the oxygen needed for combustion, a great deal of
nitrogen goes along for a free fide. This will
become an important factor in later discussions of
proper oil burner adjustment!
What we see and feel from combustion--flames,
smoke, heat--is a result of chemical reactions.
Since we can't see carbon, hydrogen or oxygen
atoms (smallest units to combine), we symbolize
the reactions with formulas that describe the
process. For example:
Carbon +Air oxygen + ] f_
nitrogen
carbon dioxide + nitrogen + heat (1)
Hydrogen +Air [ oxygen +
nitrogen ]
I.
J
watervapor + nitrogen +heat (2)
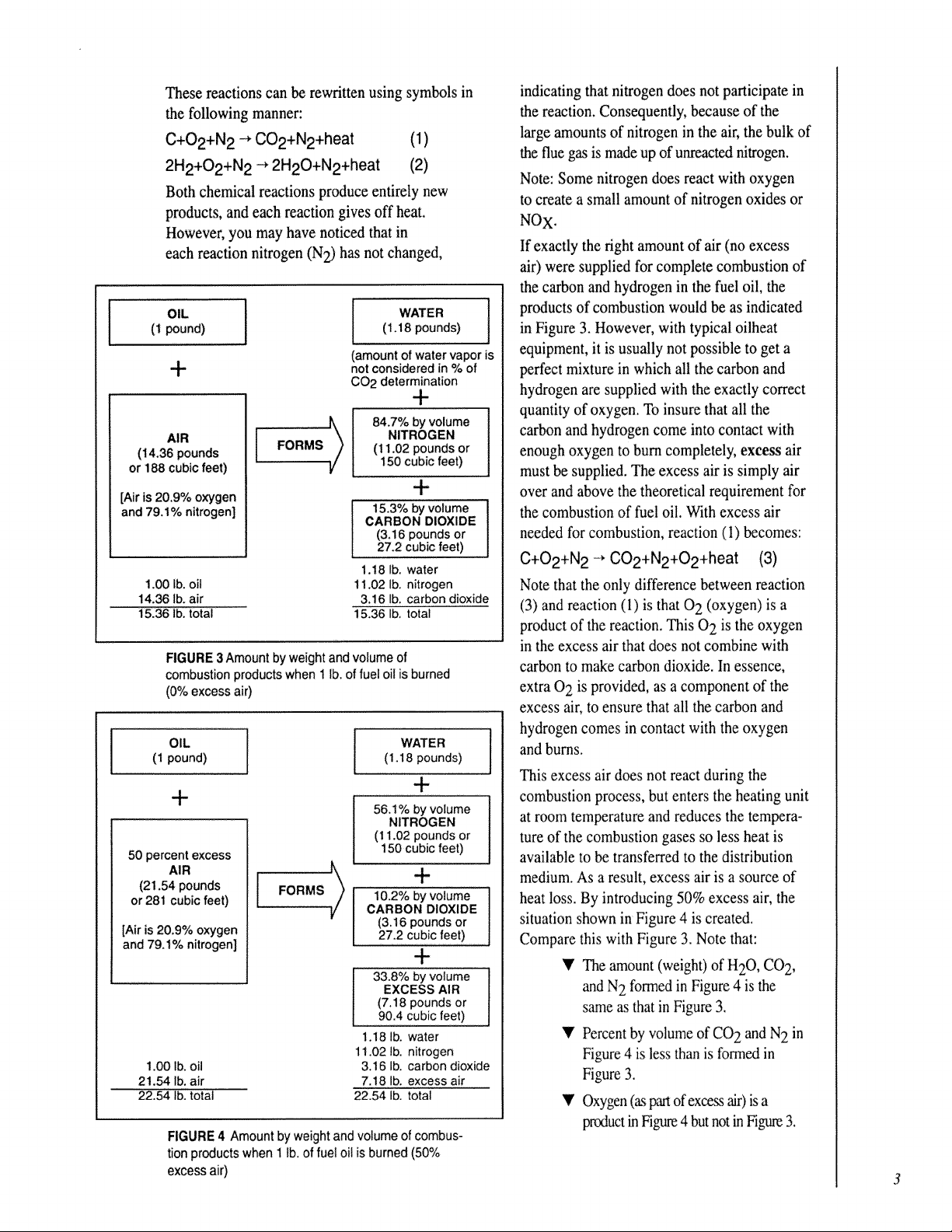
These reactions can be rewritten using symbols in
the following manner:
C+O2+N 2 -_ CO2+N2+heat (1)
2H2+O2+N 2 -_2H20+N2+heat (2)
Both chemical reactions produce entirely new
products, and each reaction gives off heat.
However, you may have noticed that in
each reaction nitrogen (N2) has not changed,
OIL
(t pound)
I
-t-
AIR
(14_36 pounds
or 188 cubic feet)
[Air is 20.9% oxygen
and 79.1% nitrogen]
1.00 lb. oil
14.36 lb. air
15.36 ib. total
FIGURE 3Amount byweightand volumeof
combustion products when 1 lb. offuel oil is burned
(0% excess air)
OIL
I
(1 pound)
-I-
50 pementexcess
AIR
(21.54 pounds
or281 cubicfeet)
[Airis 20,9%oxygen
and 79.1%nitrogen]
1,00 lb. oil
21.54 lb. air
22.54 lb. total
FIGURE 4 Amount by weight andvolume ofcombus-
tion products when 1 lb.of fuel oil is burned (50%
excess air)
I
[
1
FORMS > I
FORMS _)
(1.18 pounds)
I WATER
(amount of water vapor is
not considered in % of
CO2 determination
+
84.7% by volume
NITROGEN
(11.02 pounds or
150 cubic feet)
+
CARBON DIOXIDE
(3.16 pounds or
15.3% by volume
27.2 cubic feet)
1.18 lb. water
11.02 lb. nitrogen
3,16 lb. carbon dioxide
15.36 lb. total
WATER ](1.18 pounds)
+
56.1% by volume
NITROGEN
(11.02 pounds or
150 cubic feet)
+
10.2% byvolume ]
CARBON DIOXIDE
(3.16 pounds or
27.2 cubic feet)
+
33.8% by volume i
EXCESS AIR
(7.18 pounds or
90.4 cubic feet)
1.18 lb. water
11.02 lb. nitrogen
3.16 lb. carbon dioxide
7.18 lb. excess air
22.54 lb. total
indicating that nitrogen does not participate in
the reaction. Consequently, because of the
large amounts of nitrogen in the air, the bulk of
the flue gas is made up of unreacted nitrogen.
Note: Some nitrogen does react with oxygen
to create a small amount of nitrogen oxides or
NOx.
If exactly the right amount of air (no excess
air) were supplied for complete combustion of
the carbon and hydrogen in the fuel oil, the
products of combustion would be as indicated
in Figure 3. However, with typical oilheat
equipment, it is usually not possible to get a
perfect mixture in which all the carbon and
hydrogen are supplied with the exactly correct
quantity of oxygen. To insure that all the
carbon and hydrogen come into contact with
enough oxygen to burn completely, excess air
must be supplied, The excess air is simply air
over and above the theoretical requirement for
the combustion of fuel oil. With excess air
needed for combustion, reaction (1) becomes:
C+02+N 2 -* C02+N2+O2+heat (3)
Note that the only difference between reaction
(3) and reaction (1) is that 0 2 (oxygen) is a
product of the reaction. This 0 2 is the oxygen
in the excess air that does not combine with
carbon to make carbon dioxide. In essence,
extra 0 2 is provided, as acomponent of the
excess air, to ensure that all the carbon and
hydrogen comes in contact with the oxygen
and bums.
This excess air does not react during the
combustion process, but enters the heating unit
at room temperature and reduces the tempera-
ture of the combustion gases so less heat is
available to be transferred to the distribution
medium. As a result, excess air is a source of
heat loss. By introducing 50% excess air, the
situation shown in Figure 4 is created.
l
Compare this with Figure 3. Note that:
Y The amount (weight) of H20, CO2,
and N2 formed in Figure 4 is the
!
same as that in Figure 3.
• ' Percent by volume of CO2 and N2 in
Figure 4 is less than is formed in
Figure 3.
_' Oxygen (_ partof excess air) is a
pr_._ductin Figure 4 but not in Egtue 3.
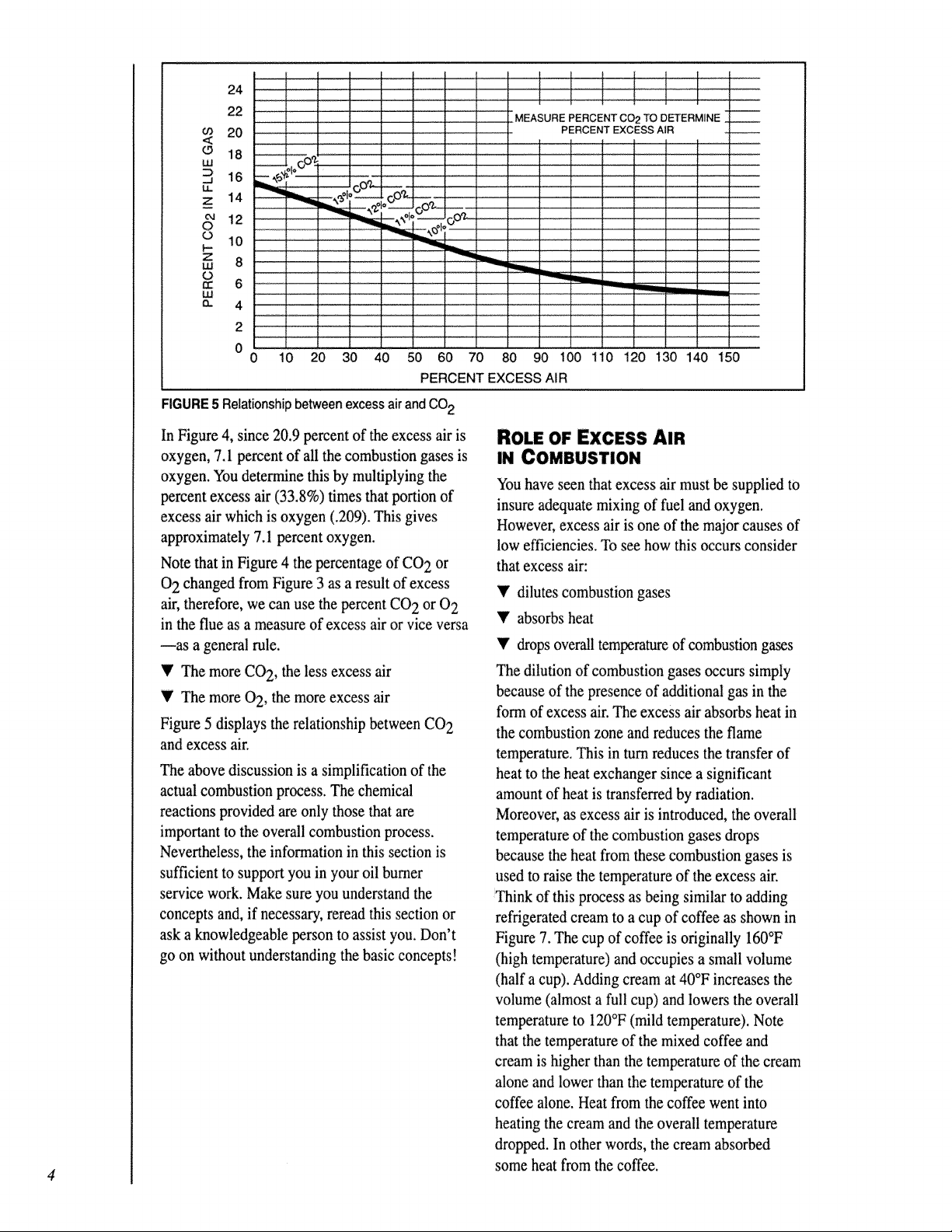
24
22
03
20
<
O
18
ILl
16
-J
It.
14
z
12
O
O
10
Z
8
LI.I
0
II
6
LU
I3u
4
2
0
0 i0 20 3o 4o so eo 7o 8o 90 i30 i40 1;50
FIGURE 5 Relationship between excessair and CO2
l
PERCENT EXCESS AIR
! ! I I ! !
MEASURE PERCENT CO2 TO D_ERMINE _
PERCENT EXCESS AIR
_" _IIii _._,m_mi " .iii--
In Figure 4, since 20.9 percent of the excess air is
oxygen, 7.1 percent of all the combustion gases is
oxygen. You determine this by multiplying the
percent excess air (33.8%) times that portion of
excess air which is oxygen (.209). This gives
approximately 7.1 percent oxygen.
Note that in Figure 4 the percentage of CO2 or
0 2 changed from Figure 3 as a result of excess
air, therefore, we can use the percent CO 2 or 0 2
in the flue as a measure of excess air or vice versa
las a general rule.
'_' The more CO 2, the less excess air
• ' The more 0 2, the more excess air
ROLE OF EXCESS AIR
IN COMBUSTION
You have seen that excess air must be supplied to
insure adequate mixing of fuel and oxygen.
However, excess air is one of the major causes of
low efficiencies. To see how this occurs consider
that excess air:
Y dilutes combustion gases
Y absorbs heat
• ' drops overall temperature of combustion gases
The dilution of combustion gases occurs simply
because of the presence of additional gas in the
form of excess air. The excess air absorbs heat in
Figure 5 displays the relationship between CO 2
and excess air.
The above discussion is a simplification of the
actual combustion process. The chemical
reactions provided are only those that are
important to the overall combustion process.
Nevertheless, the information in this section is
sufficient to support you in your oil burner
service work. Make sure you understand the
concepts and, if necessary, reread this section or
ask a knowledgeable person to assist you. Don't
go on without understanding the basic concepts!
the combustion zone and reduces the flame
temperature. This in turn reduces the transfer of
heat to the heat exchanger since a significant
amount of heat is transferred by radiation.
Moreover, as excess air is introduced, the overall
temperature of the combustion gases drops
because the heat from these combustion gases is
used to raise the temperature of the excess air.
Think of this process as being similar to adding
refrigerated cream to a cup of coffee as shown in
Figure 7. The cup of coffee is originally 160°F
(high temperature) and occupies a small volume
(half a cup). Adding cream at 40°F increases the
volume (almost a full cup) and lowers the overall
temperature to 120°F (mild temperature). Note
that the temperature of the mixed coffee and
cream is higher than the temperature of the cream
alone and lower than the temperature of the
coffee alone. Heat from the coffee went into
heating the cream and the overall temperature
dropped. In other words, the cream absorbed
4
some heat from the coffee.
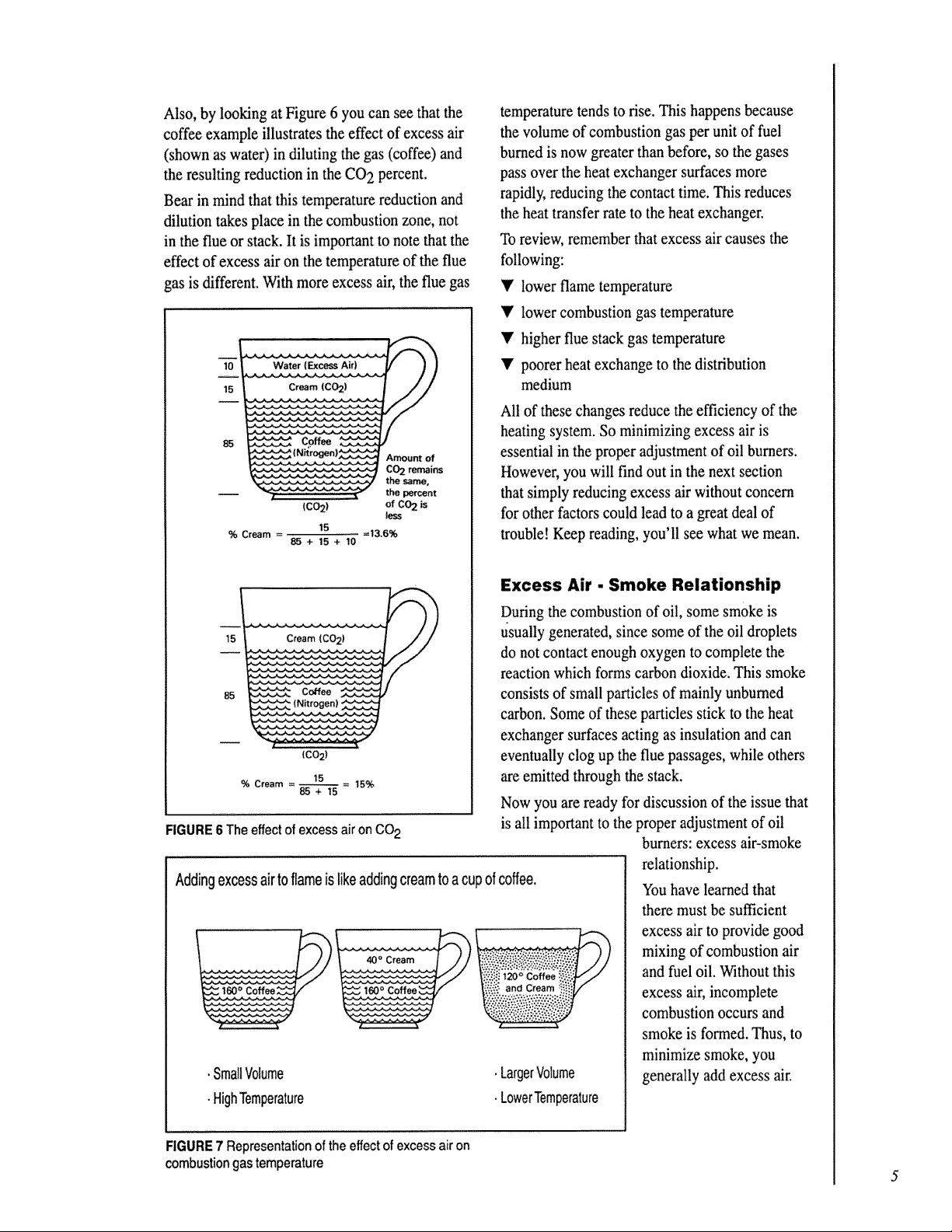
Also,bylookingatFigure6youcanseethatthe
coffeeexampleillustratestheeffectofexcessair
(shownaswater)indilutingthegas(coffee)and
theresultingreductionintheCO2percent.
Bearinmindthatthistemperaturereductionand
dilutiontakesplaceinthecombustionzone,not
intheflueorstack.Itisimportanttonotethatthe
effectofexcessaironthetemperatureoftheflue
gasisdifferent.Withmoreexcessair,thefluegas
10
15
85
Water (ExcessAir)
Cream 1CO21
_._ coffee
(C02)
% Cream =13.6%
15
85+15+10
Amount of
CO2 remains
the same,
the percent
of CO2is
less
temperature tends to rise. This happens because
the volume of combustion gas per unit of fuel
burned is now greater than before, so the gases
pass over the heat exchanger surfaces more
rapidly, reducing the contact time. This reduces
the heat transfer rate to the heat exchanger.
To review, remember that excess air causes the
following:
• ' lower flame temperature
Y lower combustion gas temperature
T higher flue stack gas temperature
T poorer heat exchange to the distribution
medium
All of these changes reduce the efficiency of the
heating system• So minimizing excess air is
essential in the proper adjustment of oil burners.
However, you will find out in the next section
that simply reducing excess air without concern
for other factors could lead to a great deal of
trouble! Keep reading, you'll see what we mean.
Excess Air. Smoke Relationship
During the combustion of oil, some smoke is
15
Cream (CO 2)
usually generated, since some of the oil droplets
do not contact enough oxygen to complete the
reaction which forms carbon dioxide. This smoke
85
.,,...,_ ( N t oge | _,,_,,...,,._
consists of small particles of mainly unburned
carbon. Some of these particles stick to the heat
exchanger surfaces acting as insulation and can
(C02)
% Cream 15%
15
85+15
eventually clog up the flue passages, while others
are emitted through the stack.
Now you are ready for discussion of the issue that
FIGURE 6 The effectof excess air on CO2
is all important to the proper adjustment of oil
Addingexcessairtoflameislikeaddingcreamtoacupofcoffee.
.SmallVolume
•HighTemperature
.LargerVolume
•LowerTemperature
burners: excess air-smoke
relationship.
You have learned that
there must be sufficient
excess air to provide good
mixing of combustion air
and fuel oil. Wqthout this
excess air, incomplete
combustion occurs and
smoke is formed. Thus, to
minimize smoke, you
generally add excess air.
FIGURE 7 Representation of theeffect of excess air on
combustion gas temperature
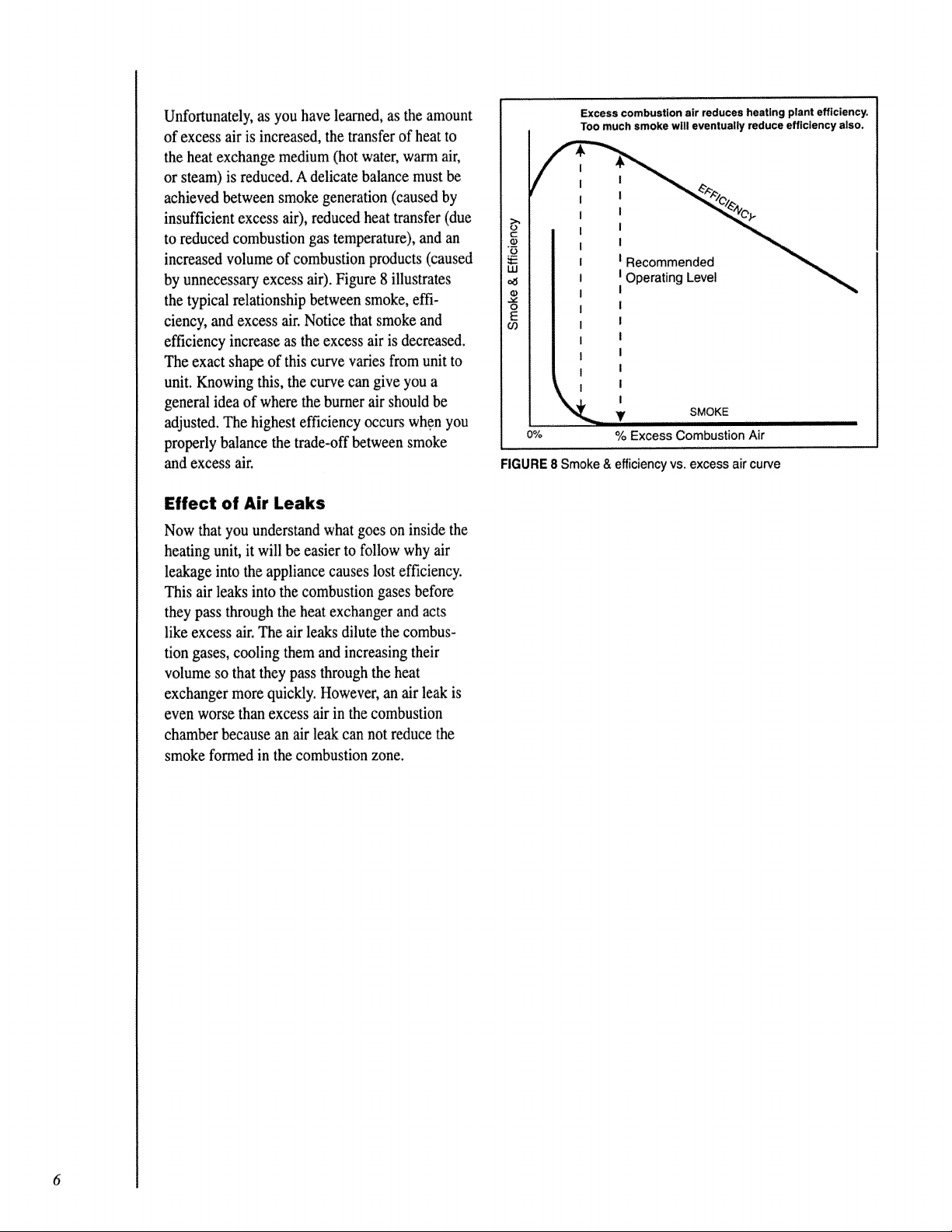
Unfortunately, as you have learned, as the amount
of excess air is increased, the transfer of heat to
the heat exchange medium (hot water, warm air,
or steam) is reduced. A delicate balance must be
achieved between smoke generation (caused by
insufficient excess air), reduced heat transfer (due
to reduced combustion gas temperature), and an
increased volume of combustion products (caused
by unnecessary excess air). Figure 8 illustrates
the typical relationship between smoke, effi-
ciency, and excess air. Notice that smoke and
efficiency increase as the excess air is decreased.
The exact shape of this curve varies from unit to
unit. Knowing this, the curve can give you a
general idea of where the burner air should be
adjusted. The highest efficiency occurs when you
properly balance the trade-off between smoke
and excess air.
Effect of Air Leaks
Now that you understand what goes on inside the
heating unit, it will be easier to follow why air
leakage into the appliance causes lost efficiency.
This air leaks into the combustion gases before
they pass through the heat exchanger and acts
like excess air. The air leaks dilute the combus-
tion gases, cooling them and increasing their
volume so that they pass through the heat
exchanger more quickly, However, an air leak is
even worse than excess air in the combustion
chamber because an air leak can not reduce the
smoke formed in the combustion zone.
Excess combustion air reduces heating plant efficiency.
Too much smoke will eventually reduce efficiency also.
g-
LLI
<1 Operating Level
o
E
o')
k'_L SMOKE
o% % Excess Combustion Air
FIGURE 8Smoke & efficiency vs. excessair curve
Recommended
i i
6
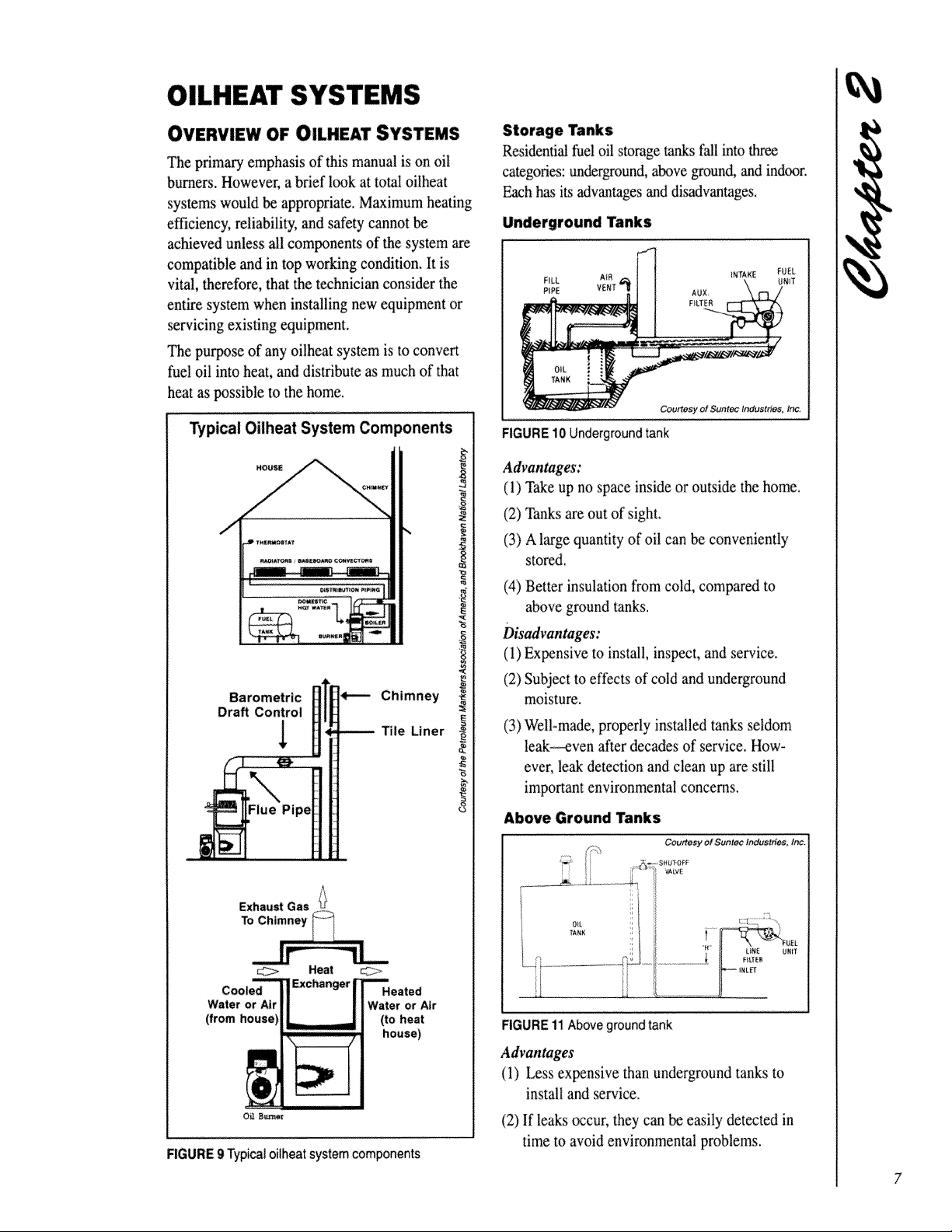
OILHEAT SYSTEMS
OVERVIEW OF OILHEAT SYSTEMS
The primapy emphasis of this manual is on oil
burners. However, abrief look at total oilheat
systems would be appropriate. Maximum heating
efficiency, reliability, and safety cannot be
achieved unless all components of the system are
compatible and in top working condition. It is
vital, therefore, that the technician consider the
entire system when installing new equipment or
servicing existing equipment.
The purpose of any oilheat system is to convert
fuel oil into heat, and distribute as much of that
heat as possible to the home.
Typical Oilheat System Components
HOU_
Storage Tanks
Residential fuel oil storage tan_ksfall into three
categories: underground, above ground, and indoor.
Each has i_ advantages and disadvantages.
Underground Tanks
Courtesy of Suntec tr_ustdes, In_
FIGURE10Undergroundtank
Advantages:
(1) Take up no space inside or outside the home.
(2) Tanks are out of sight,
(3) A large quantity of oil can be conveniently
stored.
Barometric _ Chimney
Draft Control
_, Tile Liner
_ Heat __;>
Cooled Exchan_ Heated
Water or Air Water or Air
(from house (to heat
house)
(4) Better insulation from cold, compared to
above ground tanks.
Disadvantages:
(1) ExNnsive to install, inspect, and service.
(2) Subject to effects of cold and underground
moisture.
(3) Well-made, properly installed tanks seldom
leak_ven after decades of service. How-
ever, leak detection and clean up are still
important environmental concerns.
Above Ground Tanks
Courtesy of Suntec Industries, Inc.
UNIT
FIGURE 11 Above ground tank
Advantages
(I) less expensive than underground tanks to
install and service.
RGURE 9 _pi_l oilheatsystem components
(2) If leaks occur, they can be easily detected in
time to avoid environmental problems.
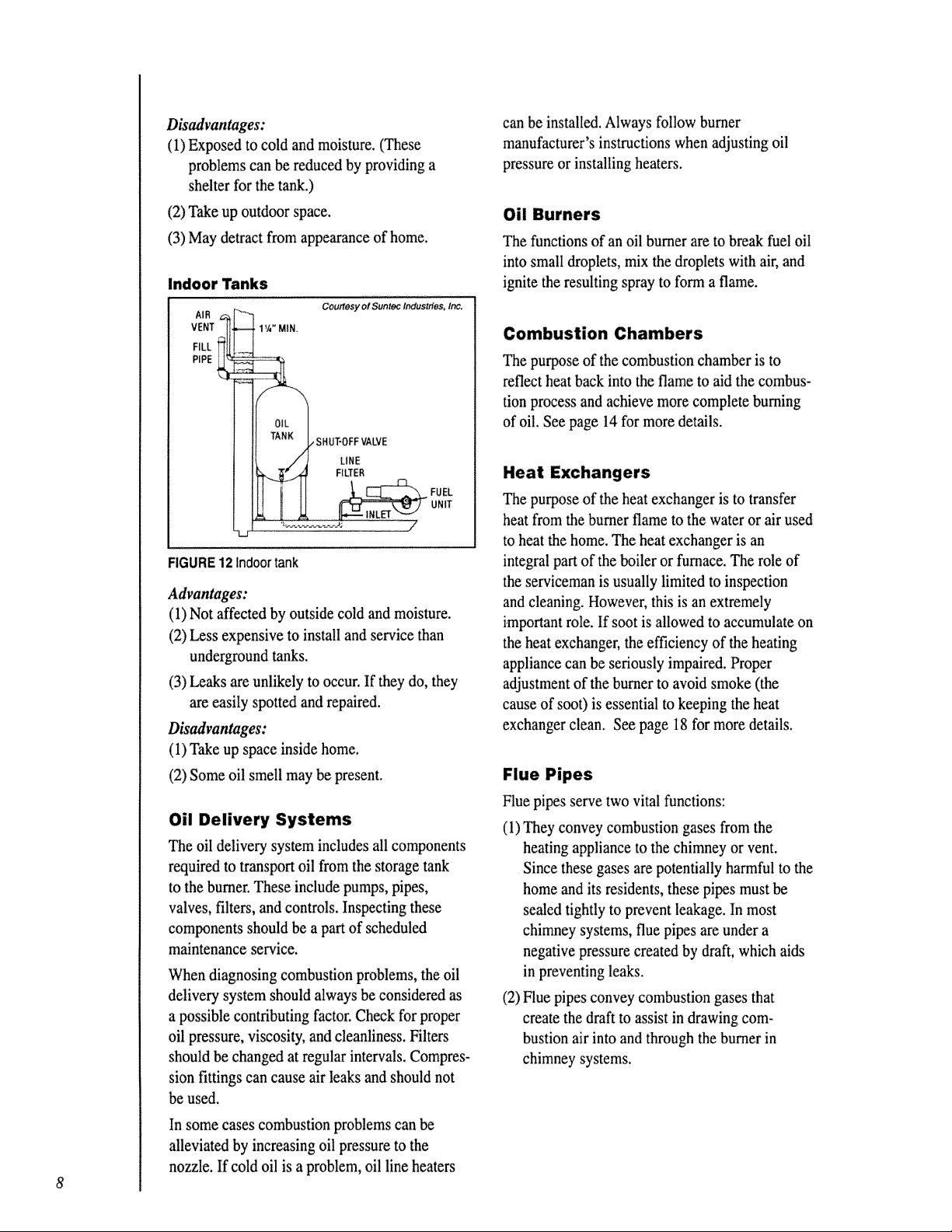
Disadvantages:
(1) Exposed to cold and moisture. (These
problems can be reduced by providing a
shelter for the _k.)
can be installed. Always follow burner
manufacturer's instvactions when adjusting oil
pressure or installing heaters.
(2)Take up outdoor space.
(3) May detract from appearance of home.
Indoor Tanks
Courtesy of Suntec Industries, Inc.
VENTll_
FIGURE 12 Indoor tank
• 1%" MIN.
_LK_ SHUT-OFFVALVE
LINE
Advantages:
(1) Not affected by outside cold and moisture.
(2) Less expensive to install and service than
underground tanks.
(3) Leaks are unlikely to occur. If they do, they
are easily spotted and repaired.
Disadvantages:
(1) Take up space inside home.
(2) Some oil smell may be present.
Oil Delivery Systems
The oil delivery system includes all components
required to transport oil from the storage tank
to the burner. These include pumps, pipes,
valves, filters, and controls. Inspecting these
components should be a part of scheduled
maintenance service.
When diagnosing combustion problems, the oil
delivery system should always be considered as
a possible contributing factor. Check for proper
oil pressure, viscosity, and cleanliness. Filters
should be changed at regular intervals. Compres-
sion fittings can cause air leaks and should not
be used.
Oil Burners
The functions of an oil burner are to break fuel oil
into small droplets, mix the droplets with air, and
ignite the resulting spray to form a flame.
Combustion Chambers
The purpose of thecombustion chamber is to
reflect heat back into the flame to aid the combus-
tion process and achieve more complete burning
of oil. See page 14for more details.
Heat Exchangers
The purpose of the heat exchanger is to transfer
heat from the burner flame to the water or air used
to heat the home. The heat exchanger is an
integral part of the boiler or furnace. The role of
the serviceman is usually limited to inspection
and cleaning. However, this is an extremely
important role. If soot is allowed to accumulate on
the heat exchanger, the efficiency of the heating
appliance can be seriously impaired. Proper
adjustment of the burner to avoid smoke (the
cause of soot) is essential to keeping the heat
exchanger clean. See page 18 for more details.
Flue Pipes
Flue pipes serve two vital functions:
(1) They convey combustion gases from the
heating appliance to the chimney or vent.
Since these gases are potentially harmful to the
home and its residents, these pipes must be
sealed tightly to prevent leakage. In most
chimney systems, flue pipes are under a
negative pressure created by draft, which aids
in preventing leaks.
(2) Flue pipes convey combustion gases that
create the draft to assist in drawing com-
bustion air into and through the burner in
chimney systems.
In some cases combustion problems can be
alleviated by increasing oil pressure to the
nozzle. If cold oil is a problem, oil line heaters
8
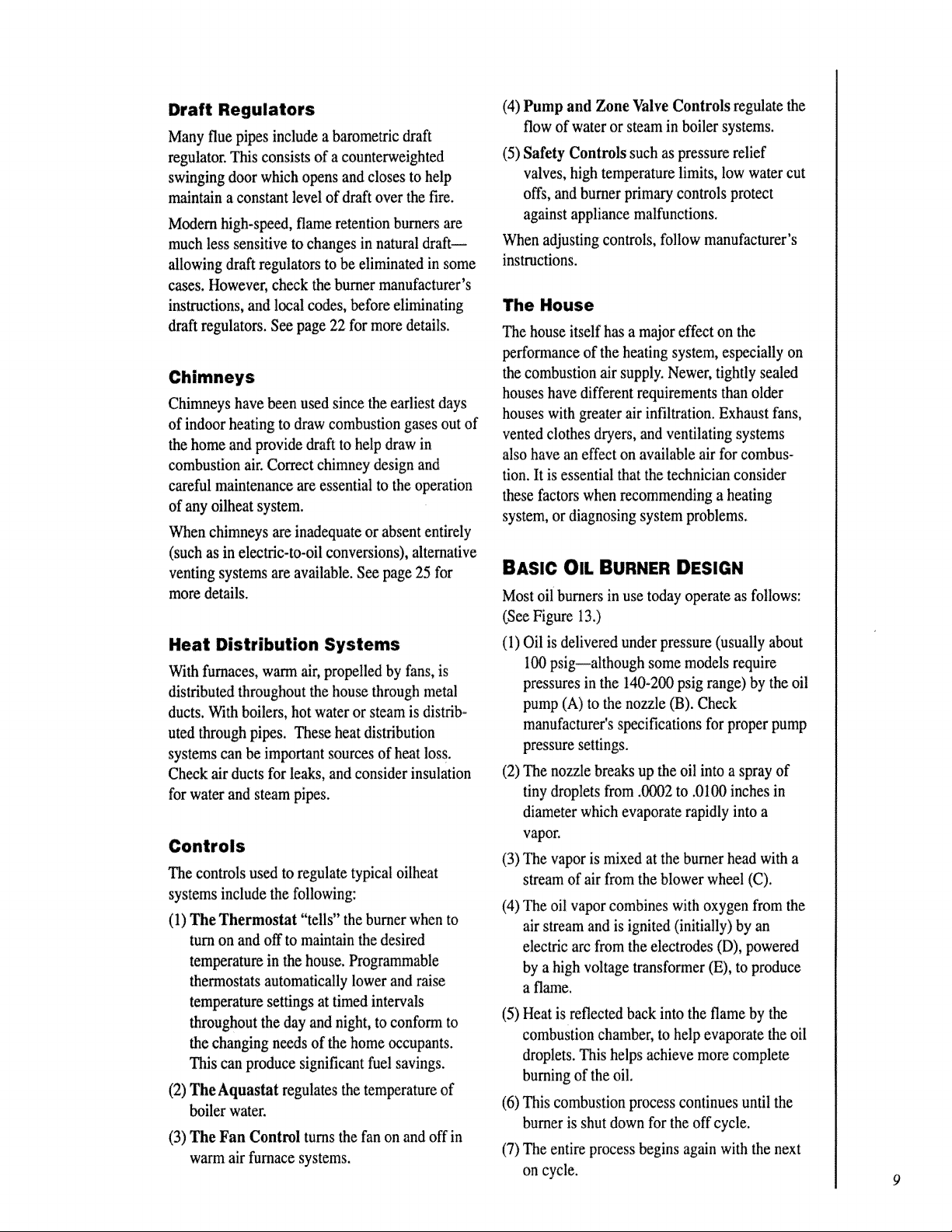
Draft Regulators
Many flue pipes include a barometric draft
regulator. This consists of a counterweighted
swinging door which opens and closes to help
maintain a constant level of draft over the fire.
Modern high-speed, flame retention burners are
much less sensitive to changes in natural draft
allowing draft regulators to be eliminated in some
cases. However, check the burner manufacturer's
instructions, and local codes, before eliminating
draft regulators. See page 22 for more details.
Chimneys
Chimneys have been used since the earliest days
of indoor heating to draw combustion gases out of
the home and provide draft to help draw in
combustion air. Correct chimney design and
careful maintenance are essential to the operation
of any oilheat system.
When chimneys are inadequate or absent entirely
(such as in electric-to-oil conversions), alternative
venting systems are available. See page 25 for
more details.
Heat Distribution Systems
With furnaces, warm air, propelled by fans, is
distributed throughout the house through metal
ducts. With boilers, hot water or steam is distrib-
uted through pipes. These heat distribution
systems can be important sources of heat loss.
Check air ducts for leaks, and consider insulation
for water and steam pipes.
Controls
The controls used to regulate typical oilheat
systems include the following:
(1) The Thermostat "tells" the burner when to
turn on and off to maintain the desired
temperature in the house. Programmable
thermostats automatically lower and raise
temperature settings at timed intervals
throughout the day and night, to conform to
the changing ne_edsof the home occupants.
This can produce significant fuel savings.
(2) TheAquastat regulates the temperature of
boiler water.
(3) The Fan Control turns the fan on and off in
warm air furnace systems.
(4) Pump and Zone "/hive Controls regulate the
flow of water or steam in boiler systems.
(5) Safety Controls such as pressure relief
valves, high temperature limits, low water cut
offs, and burner primary controls protect
against appliance malfunctions.
When adjusting controls, follow manufacturer's
instructions.
The House
The house itself has a major effect on the
performance of the heating system, especially on
the combustion air supply. Newer, tightly sealed
houses have different requirements than older
houses with greater air infiltration. Exhaust fans,
vented clothes dryers, and ventilating systems
also have an effect on available air for combus-
tion. It is essential that the technician consider
these factors when recommending a heating
system, or diagnosing system problems.
BASIC OIL BURNER DESIGN
Most oil burners in use today operate as follows:
(See Figure 13.)
(1) Oil is delivered under pressure (usually about
100 psig--although some models require
pressures in the 140-200 psig range) by the oil
pump (A) to the nozzle (B). Check
manufacturer's specifications for proper pump
pressure settings.
(2) The nozzle breaks up the oil into a spray of
tiny droplets from .0002 to .0100 inches in
diameter which evaporate rapidly into a
vapor.
(3) The vapor is mixed at the burner head with a
stream of air from the blower wheel (C).
(4) The oil vapor combines with oxygen from the
air stream and is ignited (initially) by an
electric arc from the electrodes (D), powered
by a high voltage transformer (E), to produce
a flame.
(5) Heat is reflected back into the flame by the
combustion chamber, to help evaporate the oil
droplets. This helps achieve more complete
burning of the oil.
(6) This combustion process continues until the
burner is shut down for the off cycle.
(7) The entire process begins again with the next
on cycle.
9
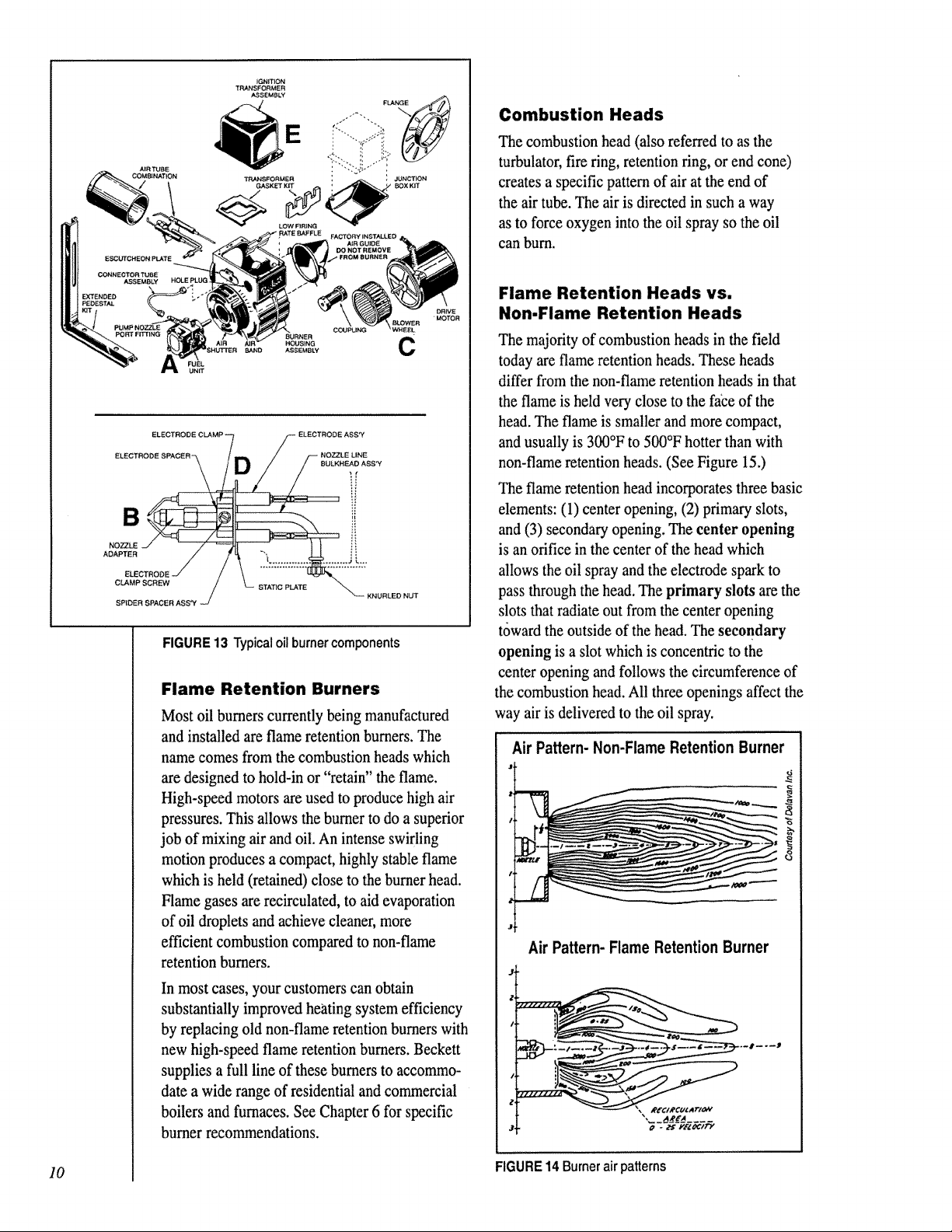
Combustion Heads
The combustion head (also referred to as the
turbulator, fire ring, retention ring, or end cone)
creates a specific pattern of air at the end of
the air tube. The air is directed in such a way
as to force oxygen into the oil spray so the oil
can burn.
Flame Retention Heads vs.
Non-Flame Retention Heads
NOZZLE
ELE
CLAMP SCREW _ STA_dC PLATE _\
SPtDER SPACER ASS'Y J _- KNURLED NUT
FIGURE 13 Typicaloilburner components
Flame Retention Burners
Most oil burners currently being manufactured
and installed are flame retention burners. The
name comes from the combustion heads which
are designed to hold-in or "retain" the flame.
High-speed motors are used to produce high air
pressures. This allows the burner to do a superior
job of mixing air and oil. An intense swirling
motion produces a compact, highly stable flame
which is held (retained) close to the burner head.
Flame gases are recirculated, to aid evaporation
of oil droplets and achieve cleaner, more
efficient combustion compared to non-flame
retention burners.
c
The majority of combustion heads in the field
today are flame retention heads. These heads
differ from the non-flame retention heads in that
the flame is held very close to the face of the
head. The flame is smaller and more compact,
and usually is 300°F to 500°F hotter than with
non-flame retention heads. (See Figure 15.)
The flame retention head incorporates three basic
elements: (1) center opening, (2) primary slots,
and (3) secondary opening. The center opening
is an orifice in the center of the head which
allows the oil spray and the electrode spark to
pass through the head. The primary slots are the
slots that radiate out from the center opening
toward the outside of the head. The secondary
opening is a slot which is concentric to the
center opening and follows the circumference of
the combustion head. All three openings affect the
way air is delivered to the oil spray.
Air Pattern- Non-Flame Retention Burner
_3
"6
Air Pattern-FlameRetentionBurner
In most cases, your customers can obtain
substantially improved heating system efficiency
by replacing old non-flame retention burners with
new high-speed flame retention burners. Beckett
supplies a full line of these burners to accommo-
date a wide range of residential and conur_ercial
boilers and furnaces. See Chapter 6 for specific
burner recommendations.
10 FIGURE14Burnerairpatterns
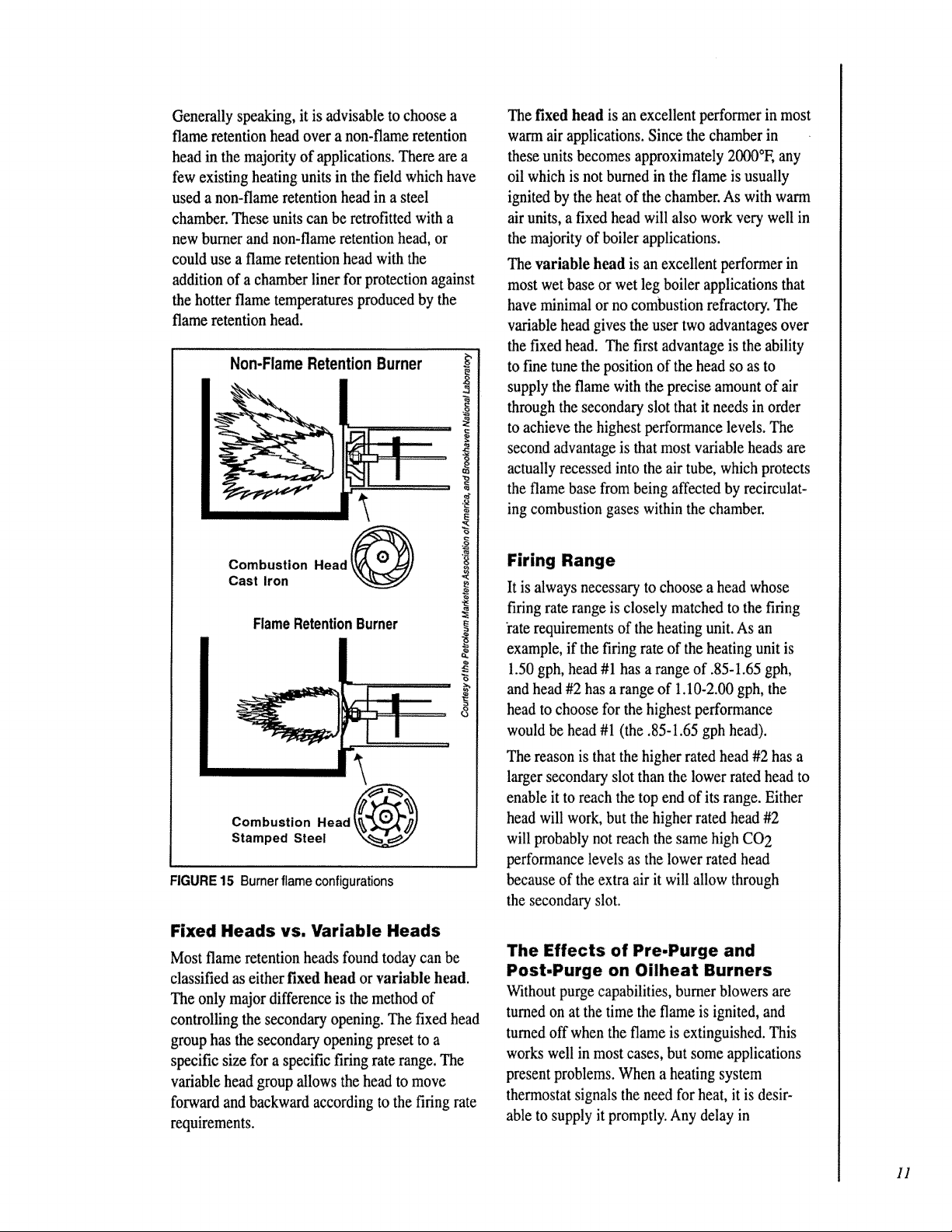
Generally speaking, it is advisable to choose a
flame retention head over a non-flame retention
head in the majority of applications. There are a
few existing heating units in the field which have
used a non-flame retention head in a steel
chamber. These units can be retrofitted with a
new burner and non-flame retention head, or
could use a flame retention head with the
addition of a chamber liner for protection against
the hotter flame temperatures produced by the
flame retention head.
Non-Flame Retention Burner
The fixed head is an excellent performer in most
warm air applications. Since the chamber in
these units becomes approximately 2000°E any
oil which is not burned in the flame is usually
ignited by the heat of the chamber. As with warm
air units, a fixed head will also work very well in
the majority of boiler applications.
The variable head is an excellent performer in
most wet base or wet leg boiler applications that
have minimal or no combustion refractory. The
variable head gives the user two advantages over
the fixed head. The first advantage is the ability
to fine tune the position of the head so as to
supply the flame with the precise amount of air
through the secondary slot that it needs in order
to achieve the highest performance levels. The
second advantage is that most variable heads are
actually recessed into the air tube, which protects
the flame base from being affected by recirculat-
ing combustion gases within the chamber.
Combustion Head 0
Cast Iron
FlameRetentionBurner
FIGURE 15 Burner flame configurations
Fixed Heads vs. Variable Heads
Most flame retention heads found today can be
classified as either fixed head orvariable head.
The only major difference is the method of
controlling the secondary opening. The fixed head
group has the secondary opening preset to a
specific size fora specific firing raterange. The
variable head group allows thehead to move
forward and backward according to the firing rate
requirements.
Firing Range
It is always necessary to choose a head ',,chose
firing rate range is closely matched to the firing
'rate requirements of the heating unit. As an
example, if the firing rate of the heating unit is
1.50 gph, head #1 has a range of .85-1.65 gph,
and head #2 has a range of 1.10-2.00 gph, the
head to choose for the highest performance
would be head #1 (the .85-1.65 gph head),
The reason is that the higher rated head #2 has a
larger secondary slot than the lower rated head to
enable it to reach the top end of its range. Either
head will work, but the higher rated head #2
will probably not reach the same high CO2
performance levels as the lower rated head
because of the extra air it will allow through
the secondary slot.
The Effects of Pre-Purge and
Post-Purge on Oilheat Burners
Without purge capabilities, burner blowers are
turned on at the time the flame is ignited, and
turned off when the flame is extinguished. This
works well in most cases, but some applications
present problems. When a heating system
thermostat signals the need for heat, it is desir-
able to supply it promptly. Any delay in
11
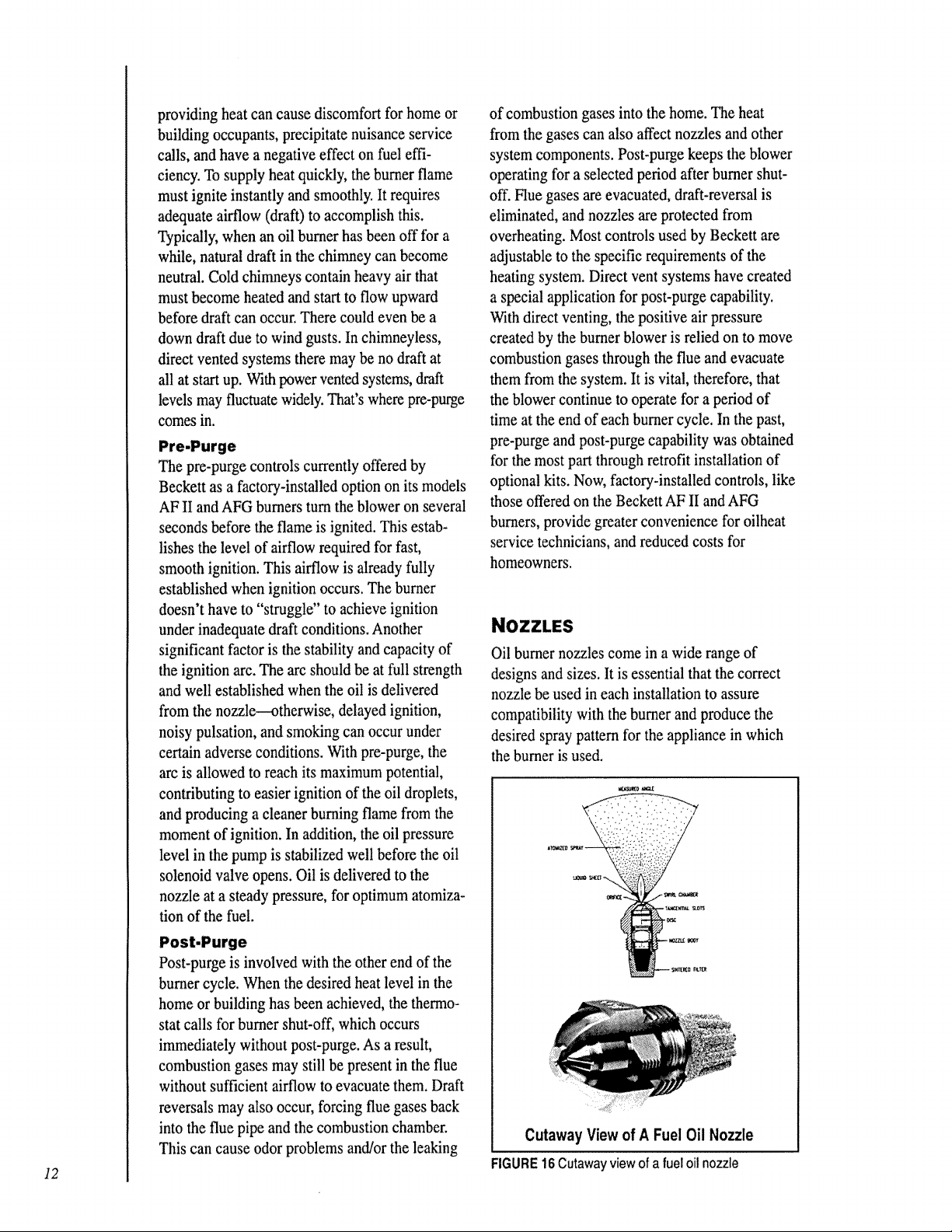
providing heat can cause discomfort for home or
building occupants, precipitate nuisance service
calls, and have a negative effect on fuel effi-
ciency. To supply heat quickly, the burner flame
must ignite instantly and smoothly. It requires
adequate airflow (draft) to accomplish this.
Typically, when an oil burner has been off for a
while, natural draft in the chimney can become
neutral. Cold chimneys contain heavy air that
must become heated and start to flow upward
before draft can occur. There could even be a
down draft due to wind gusts. In chimneyless,
direct vented systems there may be no draft at
all at start up. With power vented systems, draft
levels may fluctuate widely. That's where pre-purge
comes in.
The pre-purge controls currently offered by
Beckett as a factory-installed option on its models
AF II and AFG burners turn the blower on several
seconds before the flame is ignited. This estab-
lishes the level of airflow required for fast,
smooth ignition. This airflow is already fully
established when ignition occurs. The burner
doesn't have to "struggle" to achieve ignition
under inadequate draft conditions. Another
significant factor is the stability and capacity of
the ignition arc. The arc should be at full strength
and well established when the oil is delivered
from the nozzle--otherwise, delayed ignition,
noisy pulsation, and smoking can occur under
certain adverse conditions. With pre-purge, the
arc is allowed to reach its maximum potential,
contributing to easier ignition of the oil droplets,
and producing a cleaner burning flame from the
moment of ignition. In addition, the oil pressure
level in the pump is stabilized well before the oil
solenoid valve opens. Oil is delivered to the
nozzle at a steady pressure, for optimum atomiza-
tion of the fuel.
of combustion gases into the home. The heat
from the gases can also affect nozzles and other
system components. Post-purge keeps the blower
operating for a selected period after burner shut-
off. Flue gases are evacuated, draft-reversal is
eliminated, and nozzles are protected from
overheating. Most controls used by Beckett are
adjustable to the specific requirements of the
heating system. Direct vent systems have created
a special application for post-purge capability.
With direct venting, the positive air pressure
created by the burner blower is relied on to move
combustion gases through the flue and evacuate
them from the system. It is vital, therefore, that
the blower continue to operate for a period of
time at the end of each burner cycle. In the past,
pre-purge and post-purge capability was obtained
for the most part through retrofit installation of
optional kits. Now, factory-installed controls, like
those offered on the Beckett AF II and AFG
burners, provide greater convenience for oilheat
service technicians, and reduced costs for
homeowners.
Oil burner nozzles come in a wide range of
designs and sizes. It is essential that the correct
nozzle be used in each installation to assure
compatibility with the burner and produce the
desired spray pattern for the appliance in which
the burner is used.
12
Post-purge is involved with the other end of the
burner cycle. When the desired heat level in the
home or building has been achieved, the thermo-
stat calls for burner shut-off, which occurs
immediately without post-purge. As a result,
combustion gases may still be present in the flue
without sufficient airflow to evacuate them. Draft
reversals may also occur, forcing flue gases back
into the flue pipe and the combustion chamber.
This can cause odor problems and/or the leaking
Cutaway View of A Fuel Oil Nozzle
FIGURE16Cutawayviewofa fueloilnozzle
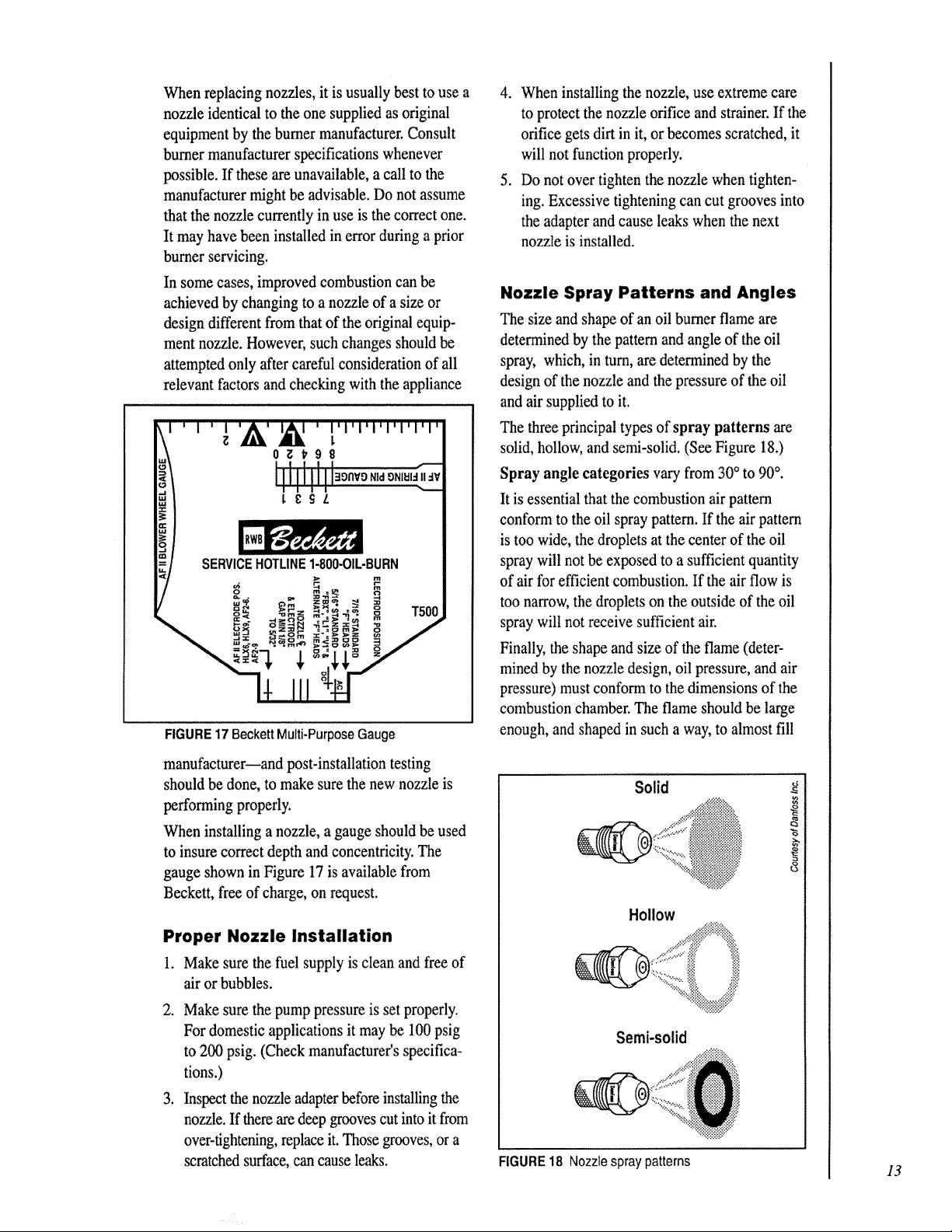
When replacing nozzles, it is usually best to use a
nozzle identical to the one supplied as original
equipment by the burner manufacturer. Consult
burner manufacturer specifications whenever
possible. If these are unavailable, a call to the
manufacturer might be advisable. Do not assume
that the nozzle currently in use is the correct one.
It may have been installed in error during a prior
burner servicing.
In some cases, improved combustion can be
achieved by changing to a nozzle of a size or
design different from that of the original equip-
ment nozzle. However, such changes should be
attempted only after careful consideration of all
relevant factors and checking with the appliance
SERVICEHOTLINE1-800-OIL,BURN
FIGURE 17 Beckett Multi-Purpose Gauge
4. When installing the nozzle, use extreme care
to protect the nozzle orifice and strainer. If the
orifice gets dirt in it, or becomes scratched, it
will not function properly.
5. Do not over tighten the nozzle when tighten-
ing. Excessive tightening can cut grooves into
the adapter and cause leaks when the next
nozzle is installed.
Nozzle Spray Patterns and Angles
The size and shape of an oil burner flame are
determined by the pattern and angle of the oil
spray, which, in turn, are determined by the
design of the nozzle and the pressure of the oil
and air supplied to it.
The three principal types of spray patterns are
solid, hollow, and semi-solid. (See Figure 18.)
Spray angle categories vary from 30° to 90°.
It isessential that the combustion air pattern
conform to the oil spray pattern. If the air pattern
is too wide, the droplets at the center of the oil
spray will not be exposed to a sufficient quantity
of air for efficient combustion. If the air flow is
too narrow, the droplets on the outside of the oil
spray will not receive sufficient air.
Finally, the shape and size of the flame (deter-
mined by the nozzle design, oil pressure, and air
pressure) must conform to the dimensions of the
combustion chamber. The flame should be large
enough, and shaped in such a way, to almost fill
manufacturer--and post-installation testing
should be done, to make sure the new nozzle is
performing properly.
When installing a nozzle, a gauge should be used
to insure correct depth and concentricity. The
gauge shown in Figure 17 is available from
Beckett, free of charge, on request.
Proper Nozzle Installation
1. Make sure the fuel supply is clean and free of
air or bubbles.
2. Make sure the pump pressure is set properly.
For domestic applications it may be 100 psig
to 200 psig. (Check manufacturer's specifica-
tions.)
3. Inspect the nozzle adapter before installing the
nozzle. If there are deep grooves cut into it from
over-tightening, replace it. Those grooves, or a
scratched surface, can cause leaks.
Solid
Semi-solid
FIGURE 18 Nozzle spray patterns
Q
"6
13