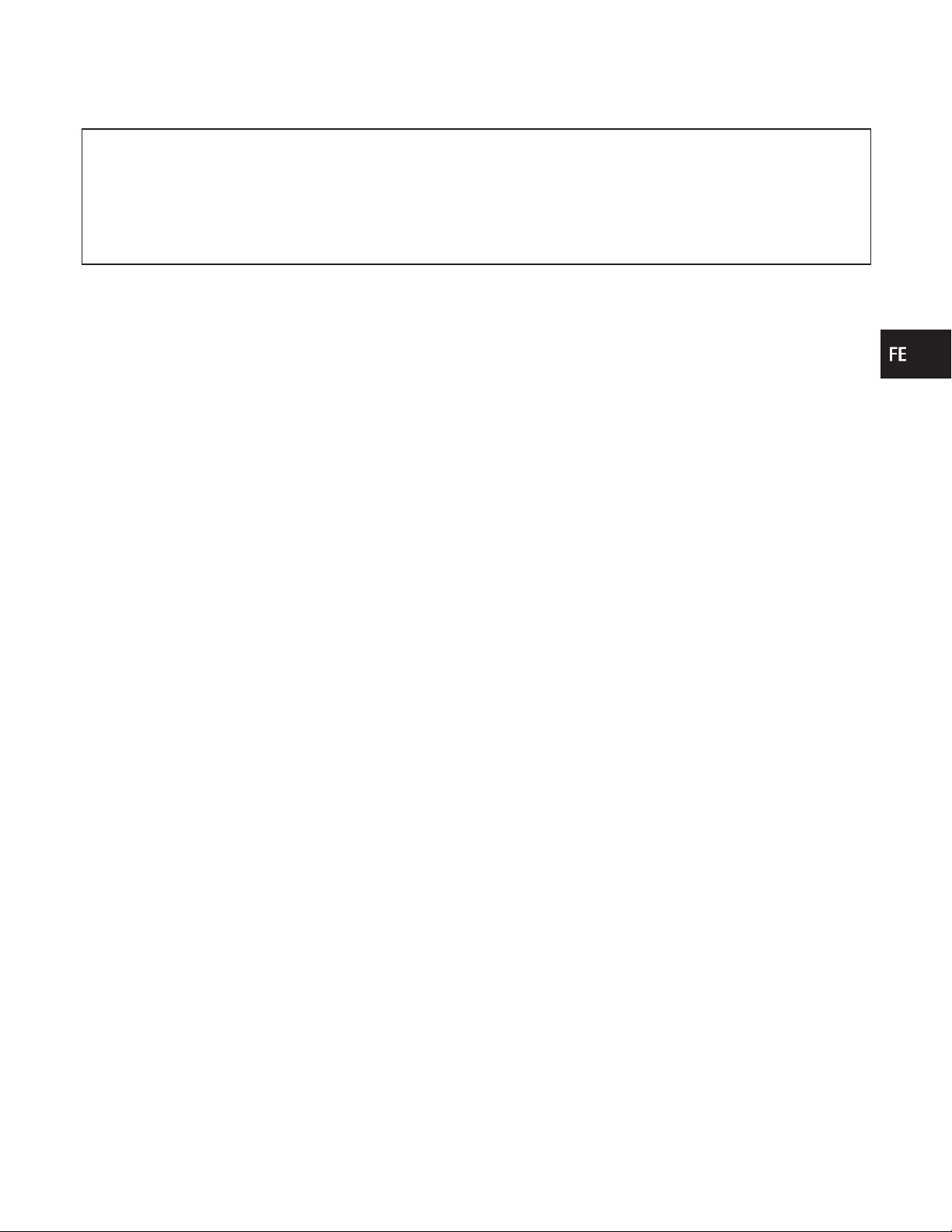
ACCELERATOR CONTROL, FUEL &
EXHAUST SYSTEMS
GI
MA
EM
CONTENTS
PREPARATION ...............................................................2
Special Service Tool ....................................................2
Commercial Service Tools ...........................................2
ACCELERATOR CONTROL SYSTEM...........................3
Removal and Installation.............................................3
REMOVAL
INSTALLATION
.................................................................3
..........................................................3
SECTION
INSPECTION AFTER INSTALLATION
FUEL SYSTEM................................................................4
Removal and Installation.............................................4
FUEL TANK
FUEL PUMP AND FUEL LEVEL SENSOR UNIT
EXHAUST SYSTEM ........................................................9
Removal and Installation.............................................9
...............................................................5
FE
.........................3
..........6
LC
EC
CL
MT
AT
TF
PD
AX
SU
BR
ST
RS
BT
HA
SC
EL
IDX
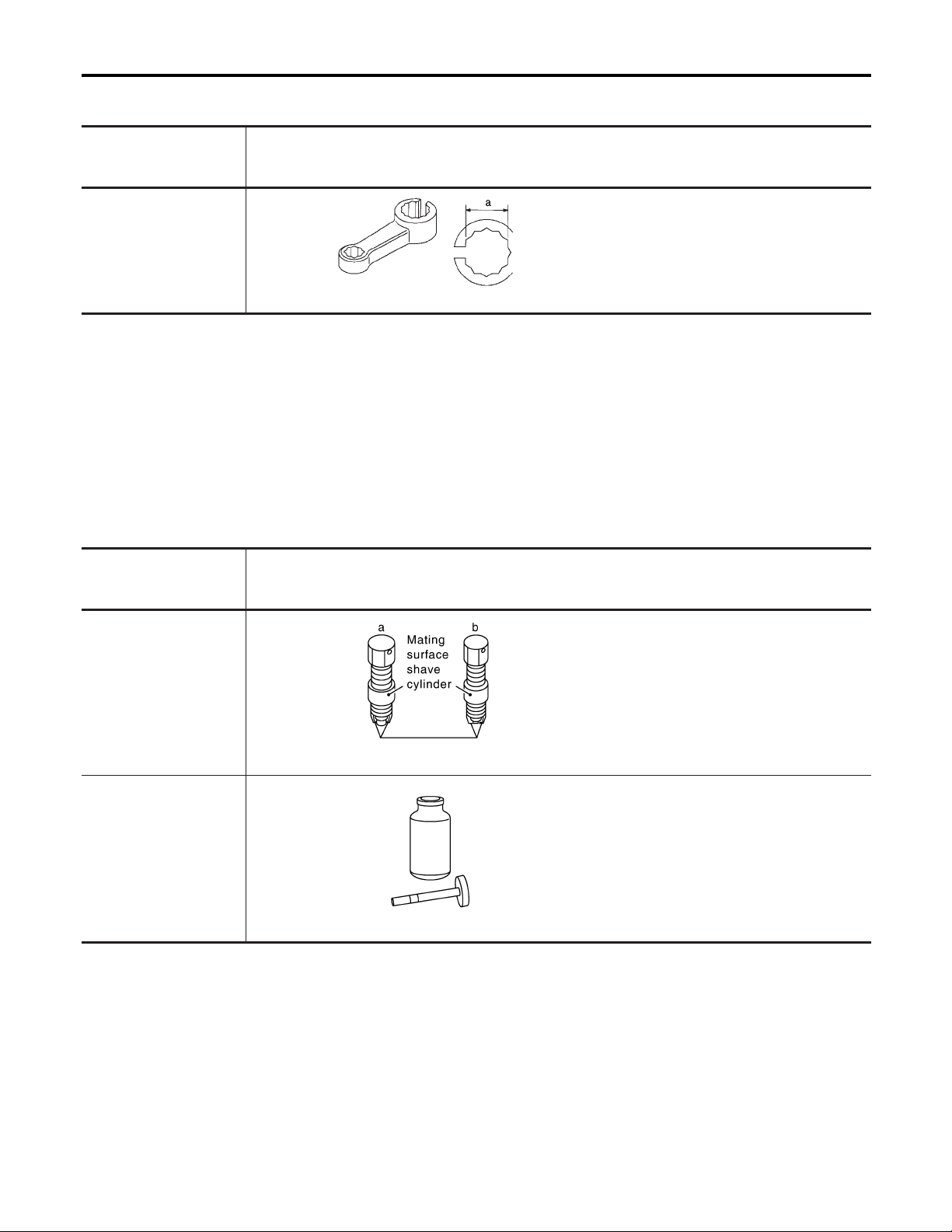
Special Service Tool
PREPARATION
Special Service Tool
The actual shapes of Kent-Moore tools may differ from those of special service tools illustrated here.
Tool number
(Kent-Moore No.)
Tool name
KV10114400 (J38365)
Heated oxygen sensor
wrench
Description
Loosening or tightening rear heated oxygen sensor (For right bank)
a: 22 mm (0.87 in)
NT636
Commercial Service Tools
Tool number
(Kent-Moore No.)
Tool name
Description
NAFE0001
NAFE0007
Oxygen sensor thread
cleaner
(J-43897-18)
(J-43897-12)
Anti-seize lubricant (Per-
TM
matex
equivalent meeting MIL
specification MIL-A-907)
133AR or
Reconditioning the exhaust system
threads before installing a new heated
oxygen sensor. Use with anti-seize lubricant shown below.
a: J-43897-18 (18 mm dia.) for Zirconia
Heated Oxygen Sensor
b: J-43897-12 (12 mm dia.) for Titania
Heated Oxygen Sensor
NT778
Lubricating heated oxygen sensor thread
cleaning tool when reconditioning exhaust
system threads.
NT779
FE-2
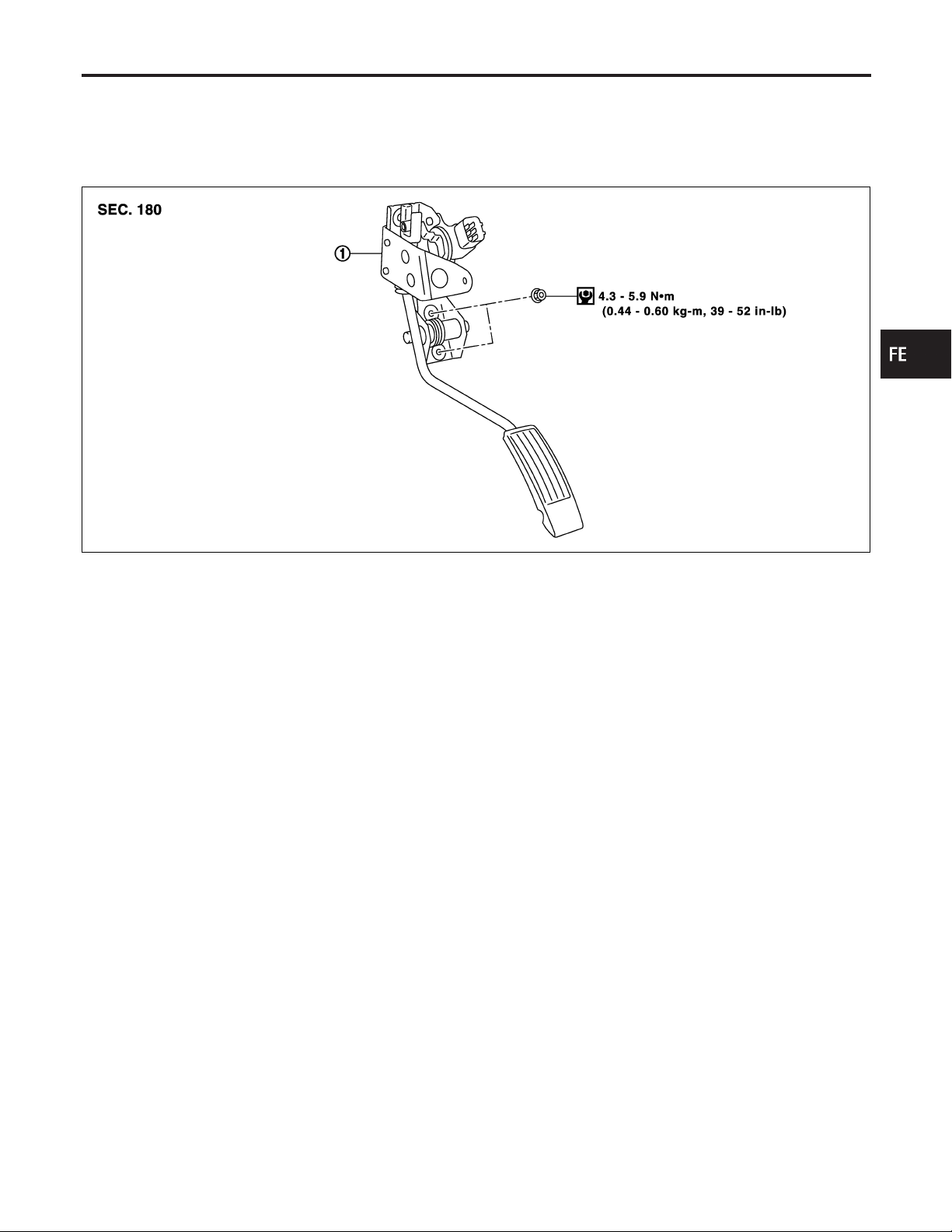
ACCELERATOR CONTROL SYSTEM
Removal and Installation
Removal and Installation
CAUTION:
I Check that throttle valve opens when accelerator pedal is fully depressed. Also check that it returns
to idle position when pedal is released when ignition switch is in “ON” position.
I Check accelerator control parts for improper contact with any adjacent parts.
1. Accelerator pedal assembly
NAFE0008
SFE787A
GI
MA
EM
LC
EC
CL
MT
AT
TF
REMOVAL
1. Remove harness connector.
2. Remove mounting nut then remove accelerator pedal assembly.
CAUTION:
I Do not disassemble accelerator pedal or remove/install accelerator pedal position sensor.
I Do not drop or shock accelerator pedal assembly.
I Keep accelerator pedal assembly from getting wet.
INSTALLATION
Install in reverse order of removal.
INSPECTION AFTER INSTALLATION
I Check if accelerator pedal moves smoothly within its range.
I Check if accelerator pedal returns securely to its original position.
I Perform “Accelerator Pedal Released Position Learning” when removing the accelerator pedal position
sensor harness connector. Refer to EC-81, “BASIC SERVICE PROCEDURE”.
I For electrical inspection of accelerator pedal assembly, refer to EC-731, “DTC P2138 APP SENSOR”.
NAFE0008S01
NAFE0008S02
NAFE0008S03
PD
AX
SU
BR
ST
RS
BT
HA
SC
FE-3
EL
IDX
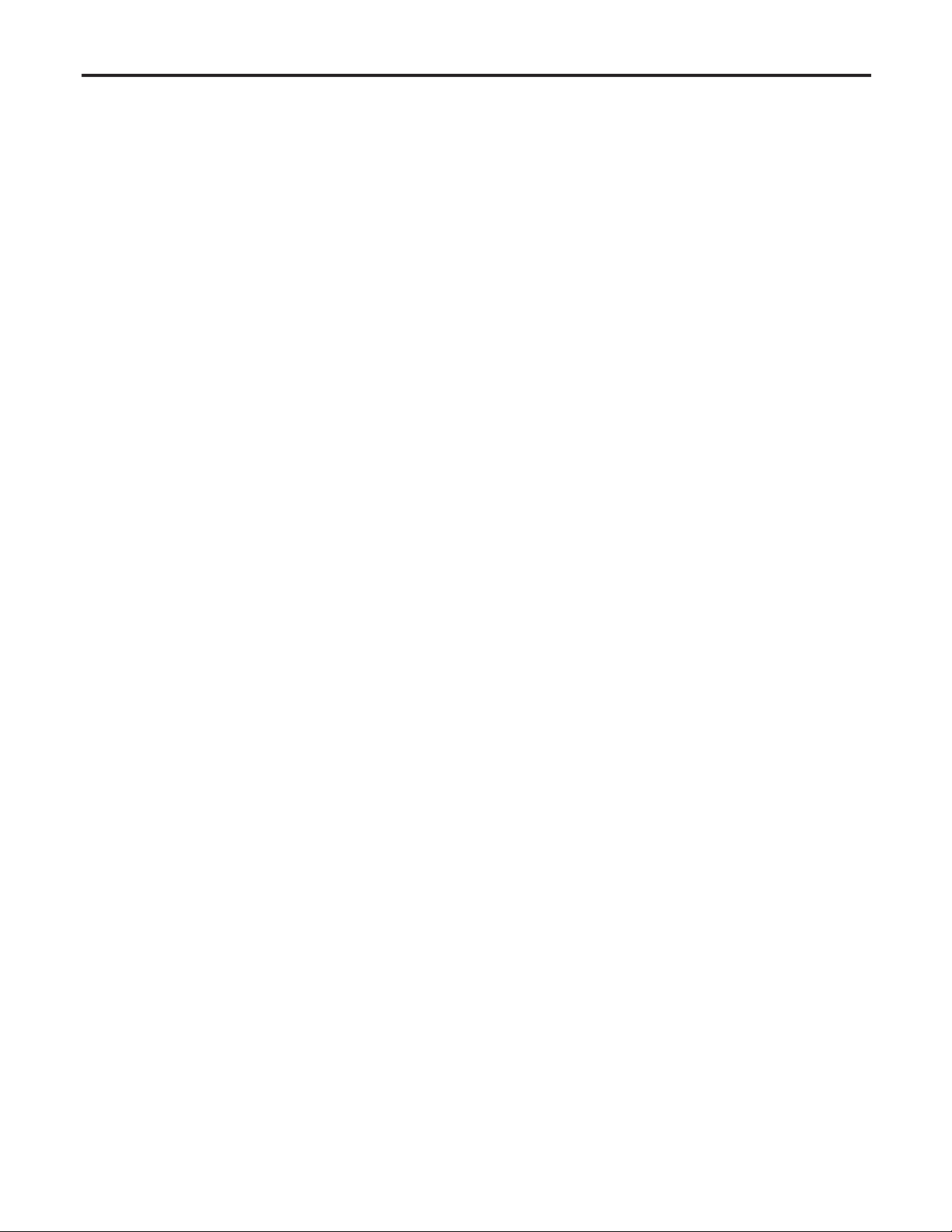
Removal and Installation
FUEL SYSTEM
Removal and Installation
NAFE0004
WARNING:
When replacing fuel line parts, be sure to observe the following:
I Put a “CAUTION: INFLAMMABLE” sign in workshop.
I Do not smoke while servicing fuel system. Keep open
flames and sparks away from work area.
I Be sure to work in a well ventilated area and furnish the
workshop with a CO
fire extinguisher.
2
CAUTION:
I Before removing fuel line parts, carry out the following
procedures:
a) Put drained fuel in an explosion-proof container and put
lid on securely. Keep the container in safe area.
b) Release fuel pressure from fuel line. Refer to MA-17,
“Changing Fuel Filter”.
c) Disconnect battery ground cable.
I Always replace O-ring with new ones.
I Do not kink or twist hose and tube when they are installed.
I Do not tighten hose clamps excessively to avoid damag-
ing hoses.
I When installing fuel check valve, be careful of its desig-
nated direction. Refer to EC-41, “EVAPORATIVE EMISSION SYSTEM”.
I For inspection of ORVR system parts, refer to EC-47, “ON
Board Refueling Vapor Recovery (ORVR)”.
I After installation, make sure there is no fuel leaks at con-
nections in the following steps.
a) Apply fuel pressure to fuel lines with turning ignition
switch ON (with engine stopped). Then check for fuel
leaks at connections.
b) Start the engine and rev it up and check for fuel leaks at
connections.
FE-4