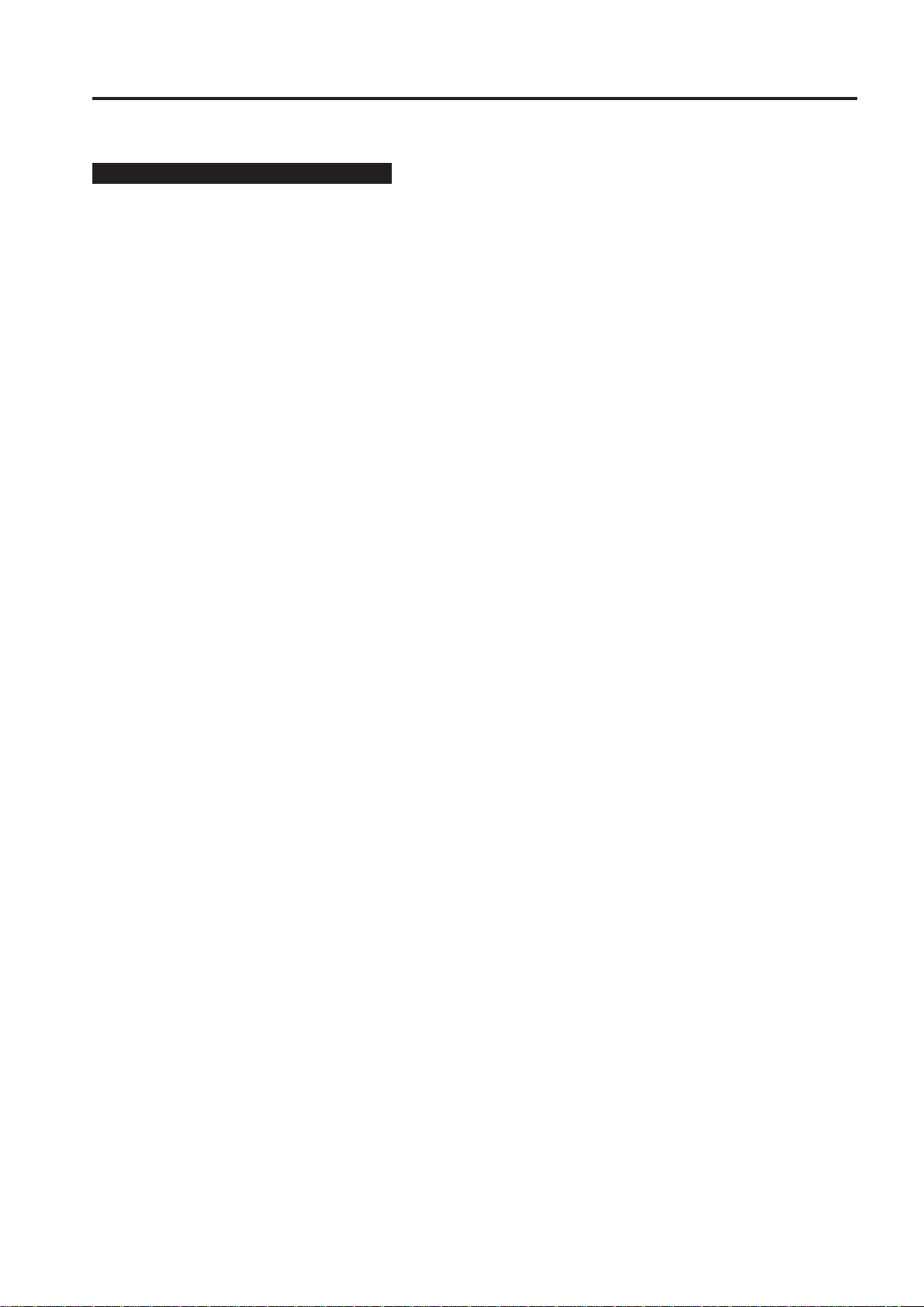
CONTENTS
CONTENTS
SAFETY AND IMPORTANT WARNING ITEMS
Refer to the 7075/7085 service handbook on page ...... vii
1. OUTLINE
PI-108 PRODUCT SPECIFICATIONS .................... 1-1
CENTER CROSS SECTION ................................... 1-2
DRIVE SYSTEM DIAGRAM .................................... 1-3
[1] Paper Feed Drive Section ........................... 1-3
[2] Sheet Tray Drive Section ............................ 1-3
2. UNIT EXPLANATION
PAPER FEED SECTION ......................................... 2-1
[1] Composition ................................................ 2-1
[2] Mechanisms ................................................ 2-1
[3] Feed Control ............................................... 2-3
3. DISASSEMBLY/ASSEMBLY
PAPER FEED SECTION ......................................... 3-1
[1] Replacing a Paper-Feed Roller and Feed
Roller ........................................................... 3-1
[2] Replacing the Rubber, Double-Feed-
Prevention Roller ........................................ 3-3
1 OUTLINE
2 UNIT EXPLANATION
3 DIS./ASSEMBLY
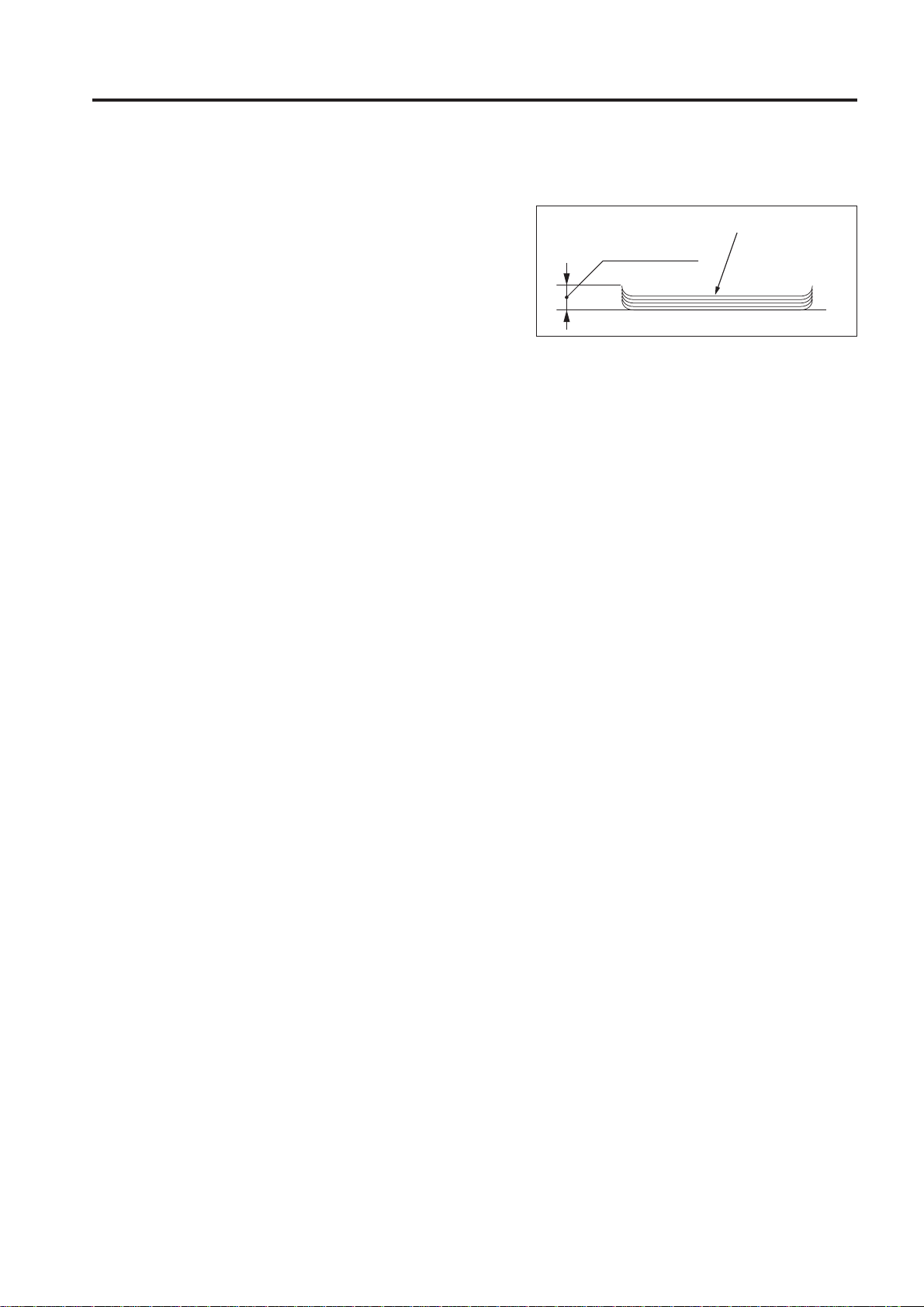
PI-108 PRODUCT SPECIFICATIONS
PI-108
[1] Type
Type:
Sheet feeder employing torque-limiter
separation
[2] Functions
Automatic sheet feed (online operation):
The PI-108 automatically feeds sheets into the
finisher in accordance with instructions from
the copier.
Manual sheet feed (offline operation):
User feeds sheets into finisher by operating
the PI-108 controls.
User can select from three finishing modes.
• Booklet mode (available only if mounted to the
FS-108BM/FS-211)
• Single-staple mode (staple at rear)
• Two-staple mode (flat stapling)
[3] Applicable paper
Plain paper
high-quality paper, recycled paper, etc.
2
(60g/m
Special paper
Printing paper
Paper sizes:
• Metric area
A3, B4, A4R, A4, B5, A5
Wide paper (Max. 314x445mm)
• Inch area
11x17, 8.5x14, 8.5x11R, 8.5x11, 5.5x8.5,
8x13
Wide paper (Max. 314x445mm)
Paper staking capacity:
Up to 250 sheets (when using 130g/m2 or
35 lbs equivalent paper), to max. height of
40mm
or 17 lbs to 90g/m2 or 24 lbs)
• OHP film
• Label paper
• Blueprint master paper
• 50 to 59g/m
paper
• 91 to 200g/m2 or 24 lbs to 45 lbs high-quality
paper
• Double-sided art paper
• Mat paper
• High-quality paper
2
or 13 lbs to 16 lbs high-quality
Paper curling:
Max. 10mm
5 sheets of copy paper
Amount of curl
[4] Machine Data
Power Source:
24VDC, 5VDC (supplied from finisher)
Maximum Power Consamption: Max. 25VA
Weight: Approx. 5kg
External dimensions:
Approx. 330(W) x 120(H) x 456(D) (mm)
[5] Maintenance
Maintenance: Same as the main body.
Service life: Same as the main body.
[6] Machine Operating Environment
Temperature: 10˚C to 30˚C(50˚F to 86˚F)
Humidity: 10% to 80% RH
Note: The information herein may subject to change
for improvement without notice.
1 OUTLINE
1 - 1
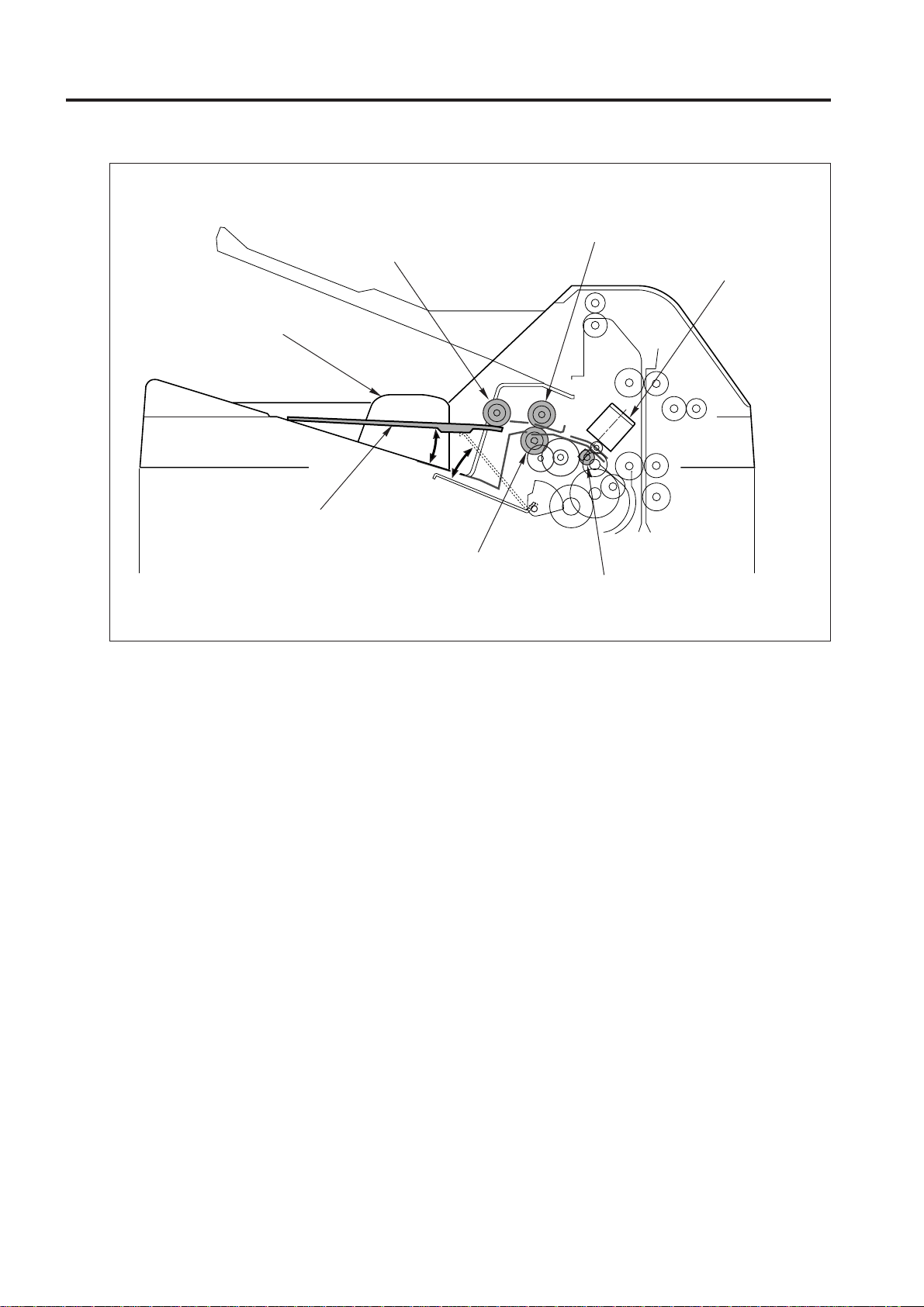
PI-108
CENTER CROSS SECTION
1 OUTLINE
Paper feed roller
Width regulation plates
Sheet tray
Feed roller
Sheet tray motor (M201 )
Double-feed prevention roller
Conveyance roller
1 - 2
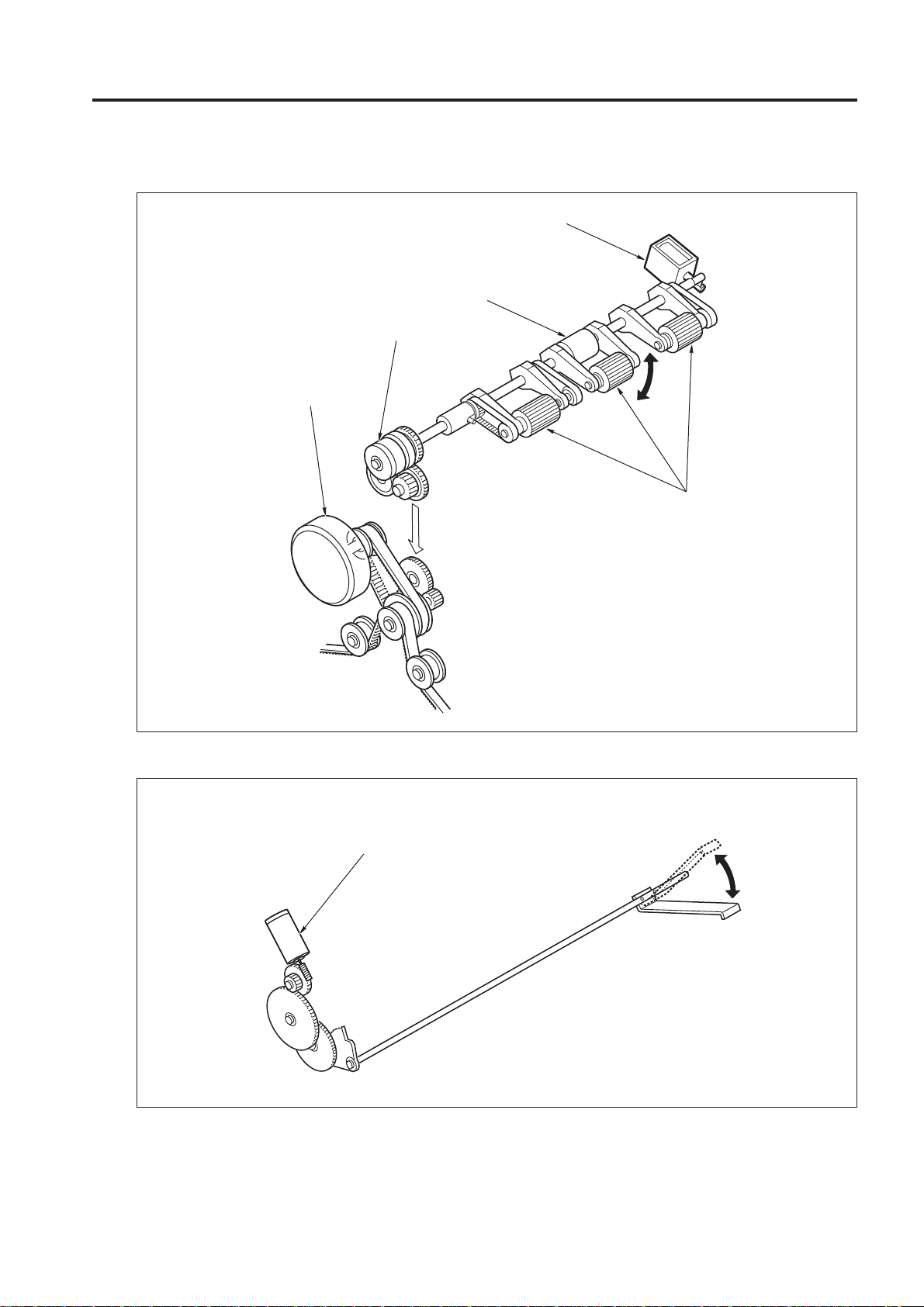
DRIVE SYSTEM DIAGRAM
PI-108
[1] Paper Feed Drive Section
Paper feed clutch (MC201)
FNS conveyance motor (M1)
1 OUTLINE
Paper-feed solenoid (SD201)
Feed roller
Paper feed roller
[2] Sheet Tray Drive Section
Sheet tray motor (M201)
1 - 3
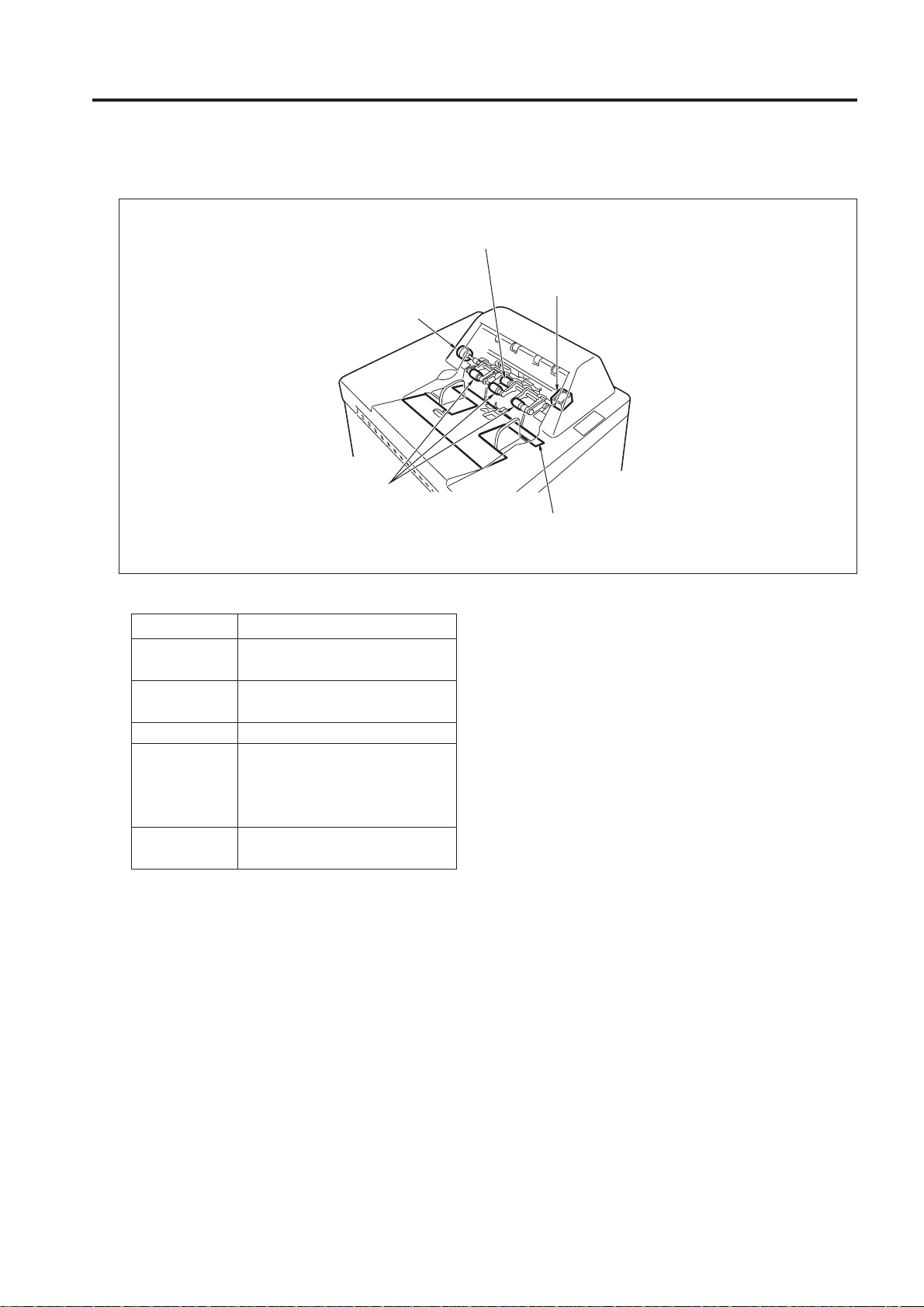
PAPER FEED SECTION
[1] Composition
Conveyance MC (MC201)
Paper feed roller
PI-108
Feed Roller
Paper feed SD (SD201)
2 UNIT EXPLANATION
Sheet tray
[2] Mechanisms
Mechanism
*1 Paper feed
Double-feed
prevention
Conveyance
Paper lift
Sheet size
detection
Method
Paper feed roller (3)
Feed roller (1)
Double-feed-prevention roller
(1)
Conveyance roller
Sheet tray
Sheet tray motor (M201)
+ Tray upper/lower limit
detection sensor
Sheet size detection sensor
+ Sheet size VR
2 - 1
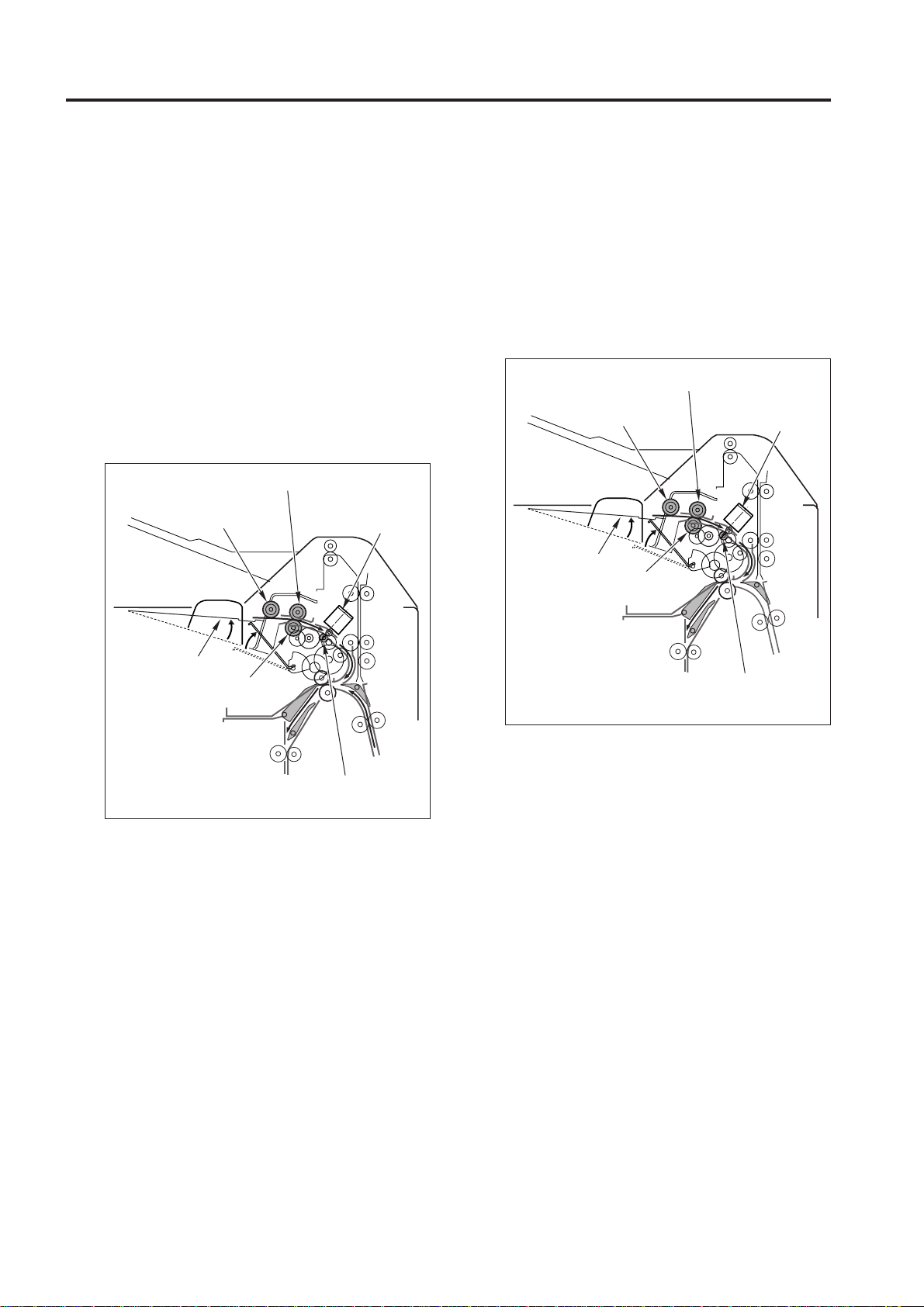
PI-108
*1: Sheet feeding processes
a. Automatic Sheet Feeding (online operation)
Sheet tray motor (M201) raises the sheet tray.
Paper feed solenoid (SD201) and paper-feed MC
(MC201) goes on, causing the paper-feed, feed,
and double-feed-prevention rollers to turn. This
action feeds sheets, one by one, into the stacker
section. The rollers are driven by FNS conveyance motor (M1) via a timing belt.
Sheets are stacked as cover sheets onto paper
from the copier, and the results are then proc-
2 UNIT EXPLANATION
essed by the FNS (single staple, double staple,
or booklet generation).
Paper feed roller
Feed roller
Sheet tray motor
(M201)
b. Manual Sheet Feeding (offline operation)
Sheet tray motor (M201) raises the sheet tray.
Paper feed (SD201) and paper-feed MC (MC201)
goes on, causing the paper-feed, feed, and double-feed-prevention rollers to turn. This action
feeds all of the sheets from the sheet tray into
the stacker section. The FNS carries out the required finishing (single stapling, double stapling,
or booklet generation).
Feed roller
Paper feed roller
Sheet tray
Double-feed
prevention roller
Sheet tray motor
(M201)
Sheet tray
Double-feed
prevention roller
Conveyance roller
Conveyance roller
2 - 2