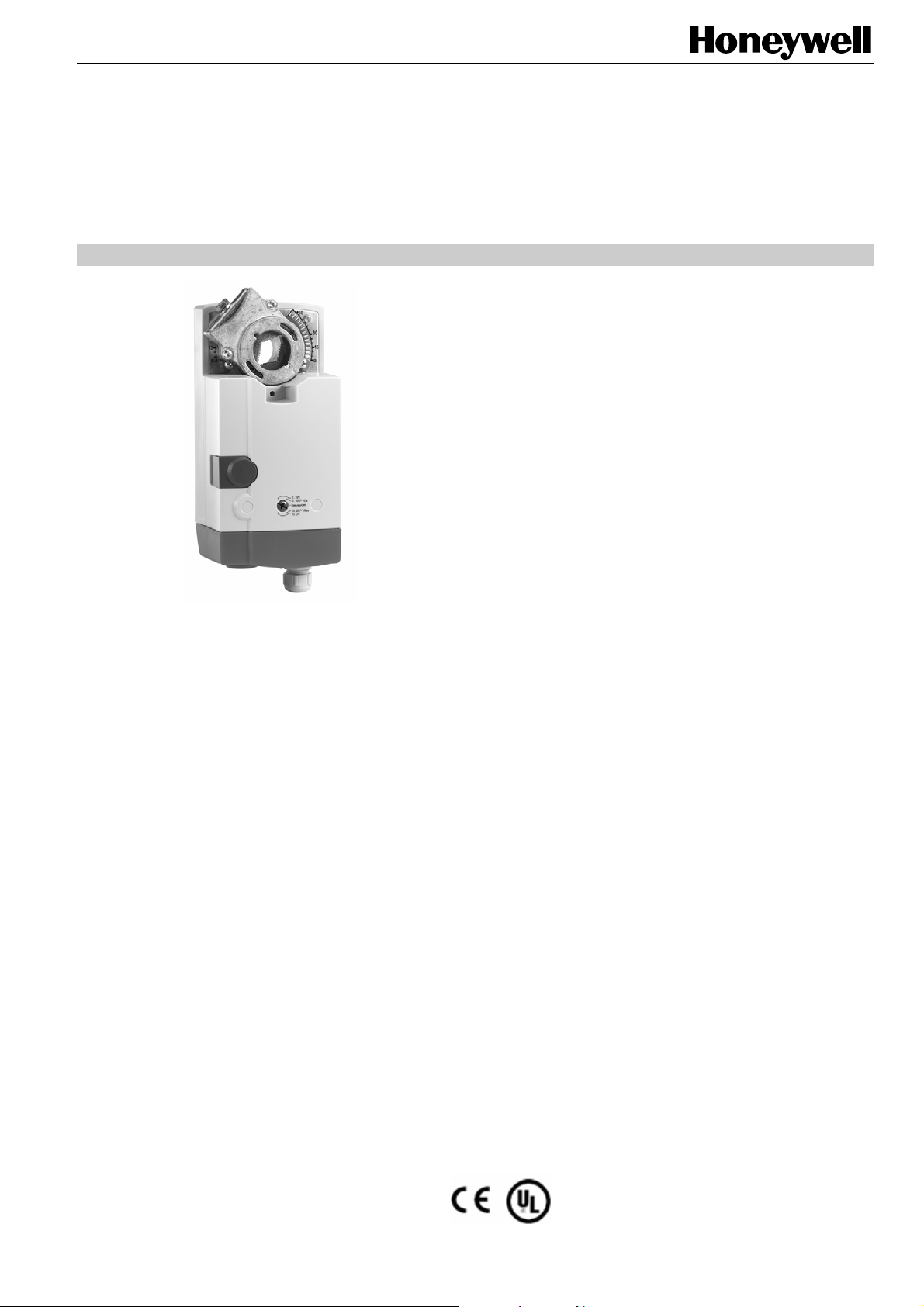
CN20, CN34 SERIES
NON-SPRING RETURN DIRECT-COUPLED DAMPER ACTUATORS
FOR MODULATING AND FLOATING / 2-POSITION CONTROL
PRODUCT DATA
SPECIFICATIONS
Supply voltage 24 Vac/dc ±15%, 50/60 Hz;
Nominal voltage 24 Vac/dc, 50/60 Hz;
All values stated hereinafter apply to operation under
nominal voltage conditions.
Power consumption
CN7220A2007 6 VA / 3 W
CN7234A2008 6 VA / 3 W
Ambient limits
Ambient operating limits -20...+60 °C (-5...+140 °F)
Ambient storage limits -40...+80 °C (-40...+175 °F)
Relative humidity 5...95%, non-condensing
Safety
Protection standard IP54 as per EN 60529
Protection class II as per EN 60730-1
Overvoltage category II
GENERAL
These direct-coupled damper actuators provide modulating
control for:
• air dampers,
• VAV units,
• air handling units,
• ventilation flaps,
• louvers, and
• reliable control for air damper applications with up to
2
4.6 m
/ 50 sq.ft. (20 Nm / 177 lb-in) or 7.8 m2 / 85 sq. ft.
(34 Nm / 300 lb-in) (seal-less dampers; air frictiondependent).
FEATURES
• Self-centering shaft adapter
• Access cover to facilitate connectivity
• Service/off for safe & easy servicing
• Rotation direction selectable by switch
• Declutch for manual adjustment
• Mechanical end limits
• Field-installable auxiliary switches
• Mountable in any orientation (no IP54 if upside down)
• Mechanical position indicator
• CE and UL certified
Lifetime
Full strokes 60000
Repositions 1.5 million
Mounting
Round damper shaft 10...27 mm (3/8...1-1/16")
Square damper shaft 10...18 mm (3/8...11/16");
45° steps
Shaft length min. 22 mm (7/8")
Control signal 0(2)...10 Vdc
0(4)...20 mA
Input impedance >100 kΩ [0...10 V]
500 Ω [0...20 mA]
Feedback signal
Limits ± 1 mA at 0...10 V
End switches (when included)
Rating 5 A (resistive) / 3 A (inductive)
Triggering points 5° / 85°
Torque rating
CN7220A2007 20 Nm (177 lb-in)
CN7234A2008 34 Nm (300 lb-in)
Runtime 95 sec (60 Hz) / 110 sec (50 Hz
or DC supply)
Rotation stroke 95° ± 3°
Dimensions see "Dimensions" on page 8
Weight (without cables) 1.35 kg (3 lbs.)
Noise rating 40 dB(A) max. at 1 m
Certification CE & UL
® U.S. Registered Trademark EN0B-0341CH33 R0803A
Copyright © 2008 Honeywell Inc. • All rights reserved

CN20, CN34 SERIES DAMPER ACTUATOR FOR MODULATING AND FLOATING CONTROL
MODELS
Model # Description
CN7220A2007
CN7234A2008
20Nm,24Vac/Vdc, Modulating and floating/2-position control, Non-Spring return, Voltage Feedback
Signal and without aux. Switch
34Nm,24Vac/Vdc, Modulating and floating/2-position control, Non-Spring return, Voltage Feedback
Signal and without aux. Switch
PRODUCT IDENTIFICATION SYSTEM
C – Direct Coupled Actuator
N – Fail Safe Function (Non-Spring Return)
61 – 24V Floating/2-position Control
72 – 24V Modulating and Floating/2-position Control
46 – 230V Floating/2-position Control
20 – 20 Nm (177 lb-in)
34 – 34 Nm (300 lb-in)
A – Standard Model
1 – No Feedback
2 – Voltage Feedback Signal
0 – No Internal Auxiliary Switches
2 – Two Internal Auxiliary Switches
XX – System Controlled Numbers
C N 72 20 A 2 0 XX
Fig.1. Product Identification System
OPERATION / FUNCTIONS
1
2
3
4
5
6
7 8
Fig. 2. Setting units and control elements
Legend for Fig.2:
1 Self-centering shaft adapter
2 Retainer clip
3 Rotational angle scales (0...90° / 90...0°)
4 Mechanical end limits
5 Declutch button
6 Anti-rotation bracket
7 Function Selection Switch
8 Access cover
Contents of Package
The delivery package includes the actuator itself, parts 1
through 8 (see Fig.2), the anti-rotation bracket screws, and
installation instruction.
RUN MODES
The function selection switch (see Fig 3) is used to place the
actuator into any one of five different modes:
• 2-10V, modulating control; floating/2-position control, cw
run
• 0-10V/Dir, modulating control; floating/2-position control,
cw run
• Service/Off, actuator stop running
• 10-0V/Rev, modulating control; floating/2-position control,
ccw run
EN0B-0341CH33 R0803A 2

CN20, CN34 SERIES DAMPER ACTUATOR FOR MODULATING AND FLOATING CONTROL
• 10-2V, modulating control; floating/2-position control, ccw
run
Fig.3. Function selection switch
Power-Off Behavior
If power is removed, the actuator retains its position.
Service/Off
If the function selection switch is set to the "Service/Off"
position, all rotary movement is cancelled, and all control
signals are ignored, thus allowing the actuator to be safely
manually operated.
Floating/2-Position Run Mode
If the function selection switch has been set to one of the four
positions (2-10V, 0-10V/Dir, 10-0V/Rev, 10-2V) – and the
actuator is wired as Floating/2-position mode (see A2 and A3)
– then as soon as operating power is applied, the actuator will
run clockwise or counterclockwise.
Table 1. Shaft adapter behavior in the floating mode
Control signal at Function selection switch settings
Terminal 3 Terminal 4 2...10V 0...10V /Dir Service / Off 10...0V /Rev 10...2 V
open open stops stops stops stops stops
open 24 Vac/dc CCW CCW stops CW CW
24 Vac/dc open CW CW stops CCW CCW
Table 2. Shaft adapter behavior in the 2-position mode
Control signal at Function selection switch settings
Terminal 3 Terminal 4 2...10V 0...10V /Dir Service / Off 10...0V /Rev 10...2 V
24 Vac/dc open CW CW stops CCW CCW
24 Vac/dc 24 Vac/dc CCW CCW stops CW CW
Table 3. Shaft adapter behavior in the modulating mode
Control signal at Function selection switch settings
Terminal 3 Terminal 4 2...10V 0...10V /Dir Service / Off 0...10V /Rev 10...2 V
Open
< min. control signal plus 0.24V
between min. control signal plus 0.24V
and max. control signal minus 0.24V
> max. control signal minus 0.24V
open -- -- stop -- --
24 Vac/dc
open -- -- stop -- --
24 Vac/dc
open proportional proportional stop proportional proportional
24 Vac/dc
open -- -- stop -- --
24 Vac/dc
Modulating Run Mode
If the function selection switch has been set to one of the four
positions (2-10V, 0-10V/Dir, 10-0V/Rev, 10-2V) – and the
actuator is wired as modulating mode (see A1) – as soon as
operating power is applied, the actuator will run according to
the control signals applied. If terminal 5 is also wired, the
actuator will output the voltage feedback signal(0/2-10V)
proportional to actuator’s actual position. Alternatively, if
terminal 4 is wired and powered on, actuator will override the
control signal and immediately come to a position of 0% of
max. stroke.
Table 1 describes the actuator behavior (stops, rotates CCW,
or rotates CW) for the floating mode in relation to the control
signals applied to terminals 3 and 4 and to the function
selection switch setting.
Table 2 describes the actuator behavior (stops, rotates CCW,
or rotates CW) for the 2-position mode in relation to the
control signals applied to terminals 3 and 4 and to the function
selection switch setting.
Table 3 describes the actuator behavior (stops, rotates CCW,
rotates CW, runs in proportional position, or runs to 0% of
max. stroke) for the modulating mode in relation to the control
signals applied to terminals 3 and 4 and to the function
selection switch setting.
0% (most
left)
0% (most
left)
0% (most
left)
0% (most
left)
0% (most
left)
0% (most
left)
0% (most
left)
0% (most
left)
stop
stop
stop
stop
0%(most
right)
0%(most
right)
0%(most
right)
0%(most
right)
0% (most
right)
0% (most
right)
0% (most
right)
0% (most
right)
3 EN0B-0341CH33 R0803A