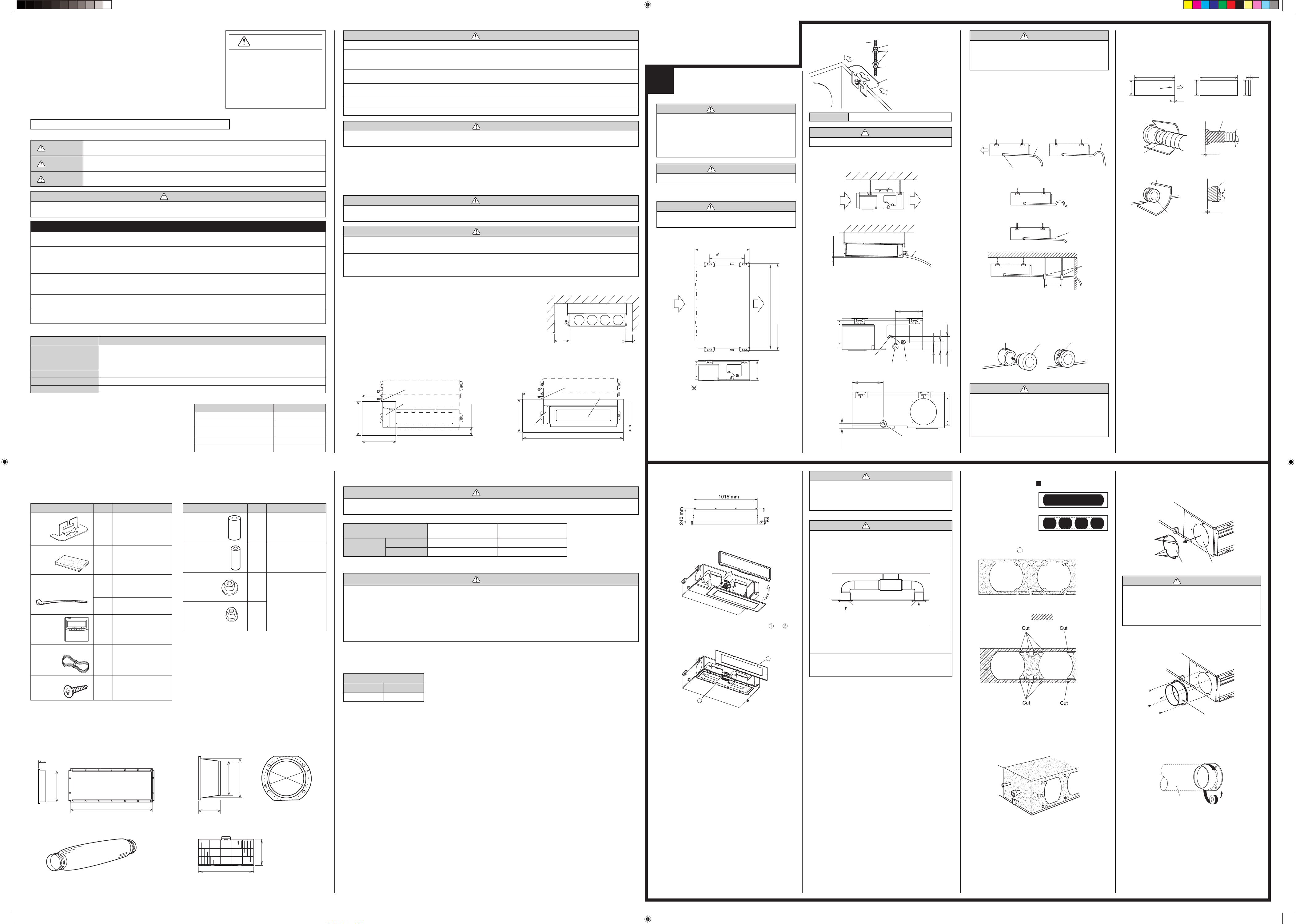
(Continued to the next page.)
CAUTION
Install the drain hose in accordance with the instructions in this installation instruction sheet and keep
the area warm enough to prevent condensation.
Problems with the piping may lead to water leaks.
Slide the unit in the arrow direction and fasten it.
2. LEVELING
Base vertical direction leveling on the unit (right and left).
Base horizontal direction leveling on top of the unit.
Give a slight tilt to the side to which the drain hose is connected.
The tilt should be in the range of 0 mm to 5 mm.
3. INSTALLING DRAIN HOSE
Install the drain hose according to the measurements given in the
following fi gure.
Drain pipe
ø 38 mm (O.D.)
The drain cap is attached
at the factory setting.
32 mm
240 mm
WARNING
Fasten the unit securely with special nuts A and B.
MODEL
24000
BTU/h model
30000/36000/45000
BTU/h model
Diameter
Liquid 6.35 mm (1/4 in.) 9.52 mm (3/8 in.)
Gas 15.88 mm (5/8 in.) 15.88 mm (5/8 in.)
Name and Shape Q’ty Application
Hanger
4
For suspending the
indoor unit from ceiling
Drain hose insulation
1
Insulates the drain
hose and vinyl hose
Binder
(Small)
1
For remote controller
and remote controller
cord binding
(Large)1For fi xing the drain
hose
Remote
controller
1
For air conditioner
operation
Remote controller cord
(*1)
1
For connecting the
remote controller
Tapping screw
(ø4 × 16)
2
For installing the
remote controller
(*1) Not supplied for ART series
STANDARD PARTS
The following installation parts are furnished. Use them as required.
INDOOR UNIT ACCESSORIES
OPTIONAL PARTS
When connecting the square duct and round duct, use the optional square fl ange or round fl ange and fl exible duct.
Decide the mounting position with the customer as follows:
INDOOR UNIT
(1) Install the indoor unit on a place having a suffi cient strength so that it withstand against
the weight of the indoor unit.
(2) The inlet and outlet ports should not be obstructed; the air should be able to blow all
over the room.
(3) Leave the space required to service the air conditioner.
(4) Install the unit where the drain pipe can be easily installed.
(5) Providing as much space as possible between the indoor unit and the ceiling will make
work much easier.
(6) If installing in a place where its humidity exceeds 80%, use heat insulation to prevent
condensation.
Maintenance hole dimension
It shall be possible to install and remove the control box. It shall be possible to install and remove the control box, fan
units and fi lter.
INSTALLATION
PROCEDURE
Install the air conditioner as follows:
NOTE: INSTALL THE DRAIN HOSE
• Install the drain hose with downward gradient (1/50 to
1/100) and so there are no rises or traps in the hose.
• Use general hard polyvinyl chloride pipe (VP25) [outside
diameter 38 mm] and connect it with adhesive (polyvinyl
chloride) so that there is no leakage.
• When the hose is long, install supporters.
• Do not perform air bleeding.
• Always heat insulate the indoor side of the drain hose.
• Cut the drain hose insulation at a position approximately
80 mm from the end with cutters, etc.
• Stick the large drain hose insulation at the drain hose installation
side.
• Stick the small drain hose insulation at the drain cap side.
(Left side)
(Left side)
(Right side)
1
INDOOR UNIT
INSTALLATION
ELECTRICAL REQUIREMENT
• Use conformed cord with Type 245 IEC57
• Install the disconnect device with a contact gap of at least 3 mm nearby the units.
(Both indoor unit and outdoor unit)
• Install all electrical works in accordance to the standard.
CONNECTING PIPE REQUIREMENT
• Use pipe with water-resistant heat insulation.
Flexible duct
Model name : UTD–RD202 (P/N 9074165004)
Round fl ange
Model name : UTD–RF204 (P/N 9093160004)
Long-life fi lter
Model name : UTD–LF25NA (P/N9079892004)
Square fl ange
Model name : UTD–SF045T (P/N 9098180007)
4. INTAKE DUCT CONNECTION
Follow the procedure in the following fi gure to the ducts.
The air inlet duct can be changed by replacing the intake grille
and fl ange.
For the bottom air intake, follow the procedure of → for
installation.
(The factory setting is back air intake.)
(1) Square duct
6. FRESH AIR INTAKE
(Processing before use)
(1) When taking in fresh air, cut a slit shaped cabinet in the left
side of the outer case with nippers.
Cut
Cut
Cabinet (iron plate) Square hole
5. OUTLET DUCT CONNECTION
Duct installation pattern ( CUT PART)
When using as a square duct
(1) Cut the slit seam with a cutter.
(2) Turn up the insulation around the points to be cut according
to the outlet port shape working points so that the insulation
does not stick out at the
part.
(3) Cut with nippers and remove the sheet metal.
(4) Since there is a slit in the insulation, use radio pliers, tweezers,
etc. to stretch the screw hole part used when installing the
round fl ange and square fl ange when connecting the duct.
(
2) Round duct outlet ×4
(This is the factory setting.)
Name and Shape Q’ty Application
Coupler heat
insulation (large)
1
For indoor side pipe
joint (gas)
Coupler heat
insulation (small)
1
For indoor side pipe
joint (liquid)
Special nut A
(large fl ange)
4
For suspending the
indoor unit from ceiling
Special nut B
(small fl ange)
4
WARNING
1 For the air conditioner to operate satisfactorily, install it as outlined in this installation instruction sheet.
2 Connect the indoor unit and outdoor unit with the air conditioner piping and cords available standards parts.
This installation instruction sheet describes the correct connections using the installation set available from
our standard parts.
3 Installation work must be performed in accordance with national wiring standards by authorized personnel
only.
4 If refrigerant leaks while work is being carried out, ventilate the area. If the refrigerant comes in contact with
a fl ame, it produces a toxic gas.
5 Do not use an extension cord.
6 Do not turn on the power until all installation work is complete.
• Be careful not to scratch the air conditioner when handling it.
• After installation, explain correct operation to the customer, using the operating manual.
• Let the customer keep this installation instruction sheet because it is used when the air conditioner is serviced
or moved.
SELECTING THE MOUNTING POSITION
CAUTION
This installation instruction sheet describes how to install the indoor unit only.
To install the outdoor unit, refer to the installation instruction sheet included with the outdoor unit.
WARNING
Install at a place that can withstand the weight of the indoor and outdoor units and install positively so that the
units will not topple or fall.
CAUTION
1 Do not install where there is the danger of combustible gas leakage.
2 Do not install the unit near heat source of heat, steam, or fl ammable gas.
3 If children under 10 years old may approach the unit, take preventive measures so that they cannot reach
the unit.
4 Take precautions to prevent the unit from falling.
CAUTION
Install heat insulation around both the gas and liquid pipes. Failure to do so may cause water leaks.
Use heat insulation with heat resistance above 120 °C. (Reverse cycle model only)
In addition, if the humidity level at the installation location of the refrigerant piping is expected to exceed 70%,
install heat insulation around the refrigerant piping. If the expected humidity level is 70-80%, use heat insulation that is 15 mm or thicker and if the expected humidity exceeds 80%, use heat insulation that is 20 mm or
thicker.
If heat insulation is used that is not as thick as specifi ed, condensation may form on the surface of the insula-
tion. In addition, use heat insulation with heat conductivity of 0.045 W/(m·K) or less (at 20 °C).
1. INSTALLING THE HANGERS
WARNING
Install the air conditioner in a location which can
withstand a load of at least fi ve times the weight of
the main unit and which will not amplify sound or
vibration.
If the installation location is not strong enough, the
indoor unit may fall and cause injuries.
CAUTION
For installation, refer to the technical data.
Hanging bolt installation diagram.
(Example)
(Top side)
(Left side)
The distance of
is adjustable according to the place of the
hanging bolts.
(MAX : 550 mm, MIN : 410 mm)
WARNING
When fastening the hangers, make the bolt positions uniform.
Bolt Strength 9.81 to 14.71 N·m (100 to 150 kgf·cm)
CAUTION
Always check that the drain cap is installed to the
unused drain port and is fastened with the nylon
fastener.
If the drain cap is not installed, or is not suffi ciently
fastened by the nylon fastener, water may drip during the cooling operation.
• When the unit is shipped from the factory, the drain port is on the
left side (control box side).
• When using the drain port on the right side of the unit, reinstall
the drain cap to the left side drain port.
CAUTION
When air is taken in from the bottom side, the operating sound of the product will easily enter the room.
Install the product and intake grilles where the affect
of the operating sound is small.
CAUTION
1 If an intake duct is installed, take care not to
damage the temperature sensor.
2 Be sure to install the air inlet grille and the air
outlet grille for air circulation. The correct temperature cannot be detected.
3 Grills must be fi xed so that man cannot touch
indoor unit fan, and cannot be removed by only
hand operation without tool.
4 Be sure to install the air fi lter in the air inlet. If the
air fi lter is not installed, the heat exchanger may
be clogged and its performance may decrease.
CAUTION
1 When removing the cabinet (iron plate), be care-
ful not to damage the indoor unit internal parts
and surrounding area (outer case).
2 When processing the cabinet (iron plate), be
careful not to injure yourself with burrs, etc.
(2) Install the round fl ange (option parts) to the fresh air intake.
(3) Connect the duct to the round fl ange.
(4) Seal with a band and vinyl tape, etc. so that air does not leak
from the connection.
CAUTION
Refer to the installation instruction sheet of the outdoor unit for description of the length of connecting pipe
or for difference of its elevation.
Connection cord (mm2)
MAX. MIN.
2.5 1.5
SPLIT TYPE AIR CONDITIONER
INSTALLATION
INSTRUCTION SHEET
(PART NO. 9374318285)
CAUTION
R410A
REFRIGERANT
Duct Type
This Air Conditioner contains and operates
with refrigerant R410A and Polyol Ester oil.
THIS PRODUCT MUST ONLY BE INSTALLED OR SERVICED
BY QUALIFIED PERSONNEL.
Refer to Commonwealth, State, Territory and local legislation,
regulations, codes, installation & operation manuals, before
the installation, maintenance and /or service of this product.
Copper pipes
It is necessary to use seamless copper pipes and it is desirable that the
amount of residual oil is less than 40 mg/10m. Do not use copper pipes
having a collapsed, deformed or discolored portion (especially on the interior
surface). Otherwise, the expansion valve or capillary tube may become
blocked with contaminants.
As an air conditioner using R410A incurs pressure higher than when using
conventional refrigerant, it is necessary to choose adequate materials.
Thicknesses of copper pipes used with R410A are as shown in the table.
Never use copper pipes thinner than that in the table even when it is
available on the market.
Thicknesses of Annealed Copper Pipes (R410A)
This air conditioner uses new refrigerant HFC (R410A).
The basic installation work procedures are the same as conventional refrigerant models.
However, pay careful attention to the following points:
1 Since the working pressure is 1.6 times higher than that of conventional refrigerant models, some of the
piping and installation and service tools are special. (See the table below.)
Especially, when replacing a conventional refrigerant model with a new refrigerant R410A model, always
replace the conventional piping and fl are nuts with the R410A piping and fl are nuts.
2 Models that use refrigerant R410A have a different charging port thread diameter to prevent erroneous
charging with conventional refrigerant and for safety. Therefore, check beforehand. [The charging port
thread diameter for R410A is 1/2 UNF 20 threads per inch.]
3 Be more careful that foreign matter (oil, water, etc.) does not enter the piping than with refrigerant models.
Also, when storing the piping, securely seal the openings by pinching, taping, etc.
4 When charging the refrigerant, take into account the slight change in the composition of the gas and liquid
phases, and always charge from the liquid phase side whose composition is stable.
Tool name Contents of change
Gauge manifold
Pressure is high and cannot be measured with a conventional gauge. To prevent erroneous mixing
of other refrigerants, the diameter of each port has been changed.
It is recommended the gauge with seals –0.1 to 5.3 MPa (–76 cmHg to 53 kgf/cm
2
) for high pressure.
–0.1 to 3.8 MPa (–76 cmHg to 38 kgf/cm2) for low pressure.
Charge hose To increase pressure resistance, the hose material and base size were changed.
Vacuum pump A conventional vacuum pump can be used by installing a vacuum pump adapter.
Gas leakage detector Special gas leakage detector for HFC refrigerant R410A.
Special tools for R410A
For authorized service personnel only.
DANGER
This mark indicates procedures which, if improperly performed, are most likely to result
in the death of or serious injury to the user or service personnel.
WARNING
This mark indicates procedures which, if improperly performed, might lead to the death
or serious injury of the user.
CAUTION
This mark indicates procedures which, if improperly performed, might possibly result in
personal harm to the user, or damage to property.
Indoor unit is an appliance not accessible to the general public.
Pipe outside diameter Thickness
6.35 mm (1/4 in.) 0.80 mm
9.52 mm (3/8 in) 0.80 mm
12.70 mm (1/2 in.) 0.80 mm
15.88 mm (5/8 in) 1.00 mm
19.05 mm (3/4 in.) 1.20 mm
DANGER
Never touch electrical components immediately after the power supply has been turned off. Electrical shock may
occur. After turning off the power, always wait 5 minutes or more before touching electrical components.
• Cover the drain cap with the drain hose insulation.
Remote sensor
Model name : UTD–RS100 (P/N 9072619004)
External control set
Model name : UTD–ECS5A (P/N 9077359004)
300 mm
500 mm
500 mm
Maintenance hole
Control box
100 mm
300 mm
500 mm
Control box
300 mm
or more
Maintenance hole
1550 mm
150 mm
or more
Intake panel
100 mm
AIR
740 mm
477 mm
AIR
270 mm
mm
1135
mm
1177
Hanging bolt M10
(Obtained locally)
Special nut A
Washer
(Obtained locally)
Special nut B
Hanger
Level meter
AIR
0-5 mm
Liquid pipe
Drain pipe
ø 38 mm (O.D.)
240 mm
Gas pipe
AIR
Drain hose
32 mm
Outlet
air flow
Drain
hose
Good Bad
Arrange the drain hose lower
than this portion.
Bad
Bad
1.5 to 2 m
66 mm
114 mm
Drain port
Drain cap Nylon fastener
Rise
Air bleeding
Trap
Supporter
170 mm
Drain hose
insulation
(large)
Drain hose
Drain hose insulation (small)
unit
Unit
450 mm
Cut line
80 mm
Drain cap
370 mm
170 mm
Drain hose
insulation
(large)
unit
0 mm
Unit
0 mm
80 mm
170 mm
Drain hose
Drain hose
insulation
(small)
40 mm
ø225 mm
2
1
Unit
Air Outlet Grille Air Inlet Grille
(Room)
204 mm
9374318285_B2.indd 19374318285_B2.indd 1 11/21/07 4:01:26 PM11/21/07 4:01:26 PM
1065 mm
ø200 mm
L 2 m
ø195 mm
ø205 mm
85 mm
239 mm
507 mm
ø235 mm
Duct
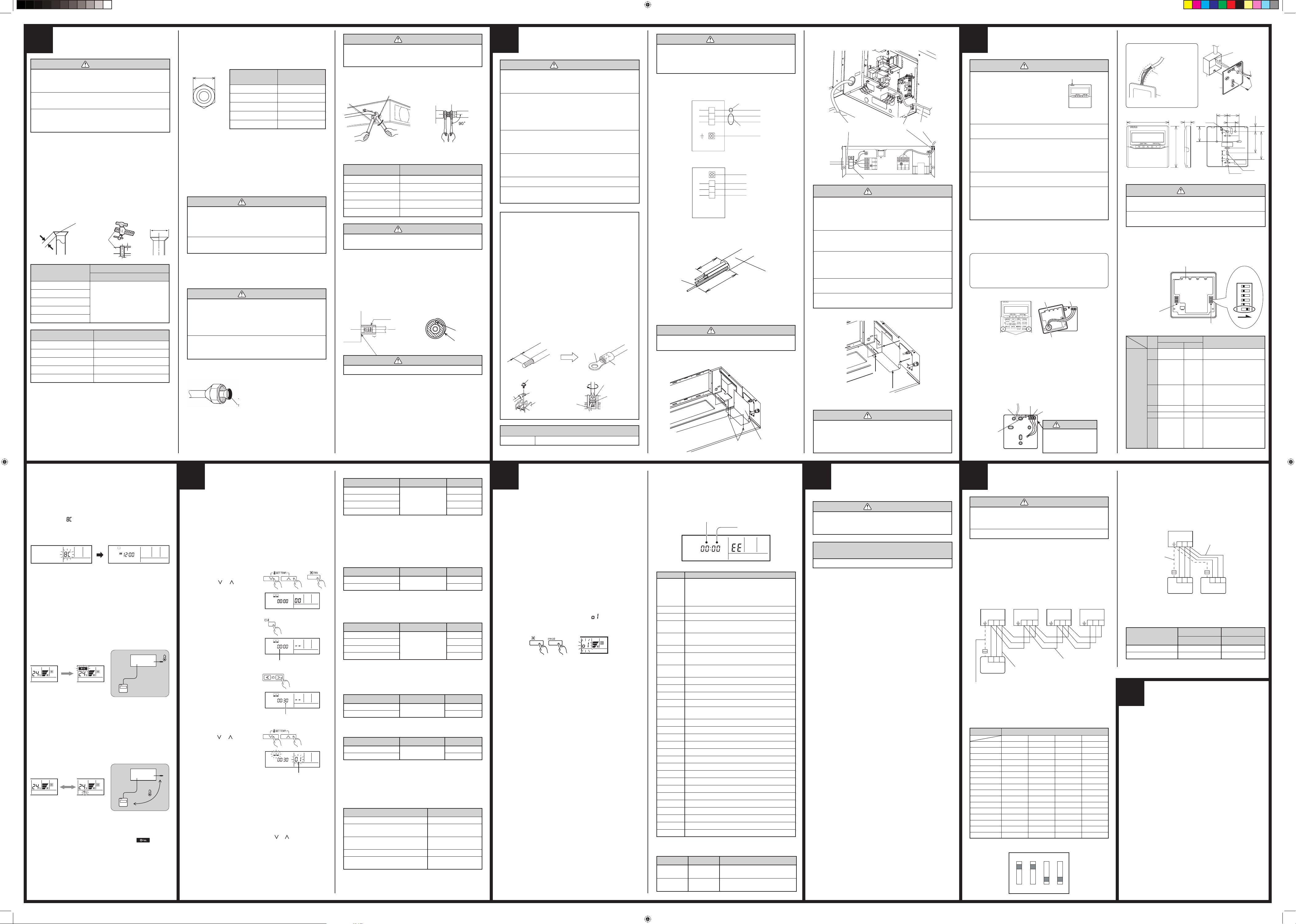
CAUTION
Use care not to mistake the power supply cord and
connection wires when installing.
3. CONNECTION PIPES
Indoor unit
(1) Detach the caps and plugs from the pipes.
CAUTION
1 To prevent breaking of the pipe, avoid sharp
bends.
Bend the pipe with a radius of curvature of 150
mm or over.
2 If the pipe is bent repeatedly at the same place,
it will break.
CAUTION
1 Do not use mineral oil on fl ared part. Prevent
mineral oil from getting into the system as this
would reduce the lifetime of the units.
2 While welding the pipes, be sure to blow dry
nitrogen gas through them.
3 The maximum lengths of this product are shown
in the table. If the units are further apart than
this, correct operation cannot be guaranteed.
CONNECTING THE
PIPE
Flare nut tightening torque
2
1. CONNECTION DIAGRAMS
Connection cord (to outdoor unit)
2. BENDING PIPES
The pipes are shaped by your hands. Be careful not to collapse
them.
Do not bend the pipes in an angle more than 90°.
When pipes are repeatedly bent or stretched, the material will
harden, making it diffi cult to bend or stretch them any more. Do
not bend or stretch the pipes more than three times.
(1) Remove the control box cover and install each connection
wire.
7
5
3
ELECTRICAL WIRING
Body
Be sure to overlap the
insulation
Coupler heat insulation
No gap
Coupler heat
insulation
4. HEAT INSULATION ON THE PIPE JOINTS
(INDOOR SIDE ONLY)
After checking for gas leaks, insulate by wrapping insulation
around the two parts (gas and liquid) of the indoor unit coupling,
using the coupler heat insulation.
After installing the coupler heat insulation, wrap both ends with
vinyl tape so that there is no gap.
3. INDOOR UNIT SIDE
2. CONNECTION CORD PREPARATION
Keep the earth wire longer than the other wires.
Power supply cord
or connection cord
20 mm
50 mm or mo
re
Earth wire
TEST RUNNING
6
STATIC PRESSURE
CHARACTERISTIC
1. FLARING
(1) Cut the connection pipe to the necessary length with a pipe
cutter.
(2) Hold the pipe downward so that cuttings will not enter the pipe
and remove the burrs.
(3) Insert the fl are nut (always use the fl are nut attached to the
indoor and outdoor units respectively) onto the pipe and
perform the fl are processing with a fl are tool.
Use the special R410A fl are tool, or the conventional fl are
tool.
CAUTION
1 Be sure to apply the pipe against the port on the
indoor unit correctly. If the centering is improper,
the fl are nut cannot be tightened smoothly. If
the fl are nut is forced to turn, the threads will
be damaged.
2 Do not remove the fl are nut from the indoor unit
pipe until immediately before connecting the
connection pipe.
(2) Centering the pipe against port on the indoor unit, turn the
fl are nut with your hand.
When the fl are nut is tightened properly by your hand, use a torque
wrench to fi nally tighten it.
CAUTION
Hold the torque wrench at its grip, keeping it in the
right angle with the pipe, in order to tighten the
fl are nut correctly.
Flare nut Tightening torque
6.35 mm (1/4 in.) dia. 16 to 18 N·m (160 to 180 kgf·cm)
9.52 mm (3/8 in.) dia. 30 to 42 N·m (300 to 420 kgf·cm)
12.70 mm (1/2 in.) dia. 49 to 61 N·m (490 to 610 kgf·cm)
15.88 mm (5/8 in.) dia. 63 to 75 N·m (630 to 750 kgf·cm)
19.05 mm (3/4 in.) dia. 90 to 110 N·m (900 to 1,100 kgf·cm)
CAUTION
Be sure to connect the gas pipe after connecting
the liquid pipe completely.
CAUTION
Must fi t tightly against body without any gap.
WARNING
1 Before starting work, check that power is not
being supplied to the indoor unit and outdoor
unit.
2 Match the terminal board numbers and con-
nection cord colors with those of the outdoor
unit.
Erroneous wiring may cause burning of the
electric parts.
3 Connect the connection cords firmly to the
terminal board. Imperfect installation may
cause a fi re.
4 Always fasten the outside covering of the
connection cord with the cord clamp. (If the
insulator is chafed, electric leakage may occur.)
5 Always connect the ground wire.
6 Install the remote controller wires so as not to
be direct touched with your hand.
(3) Install control box cover.
Pipe outside
diameter
Width across fl ats
of Flare nut
6.35 mm (1/4 in.) 17 mm
9.52 mm (3/8 in.) 22 mm
12.70 mm (1/2 in.) 26 mm
15.88 mm (5/8 in.) 29 mm
19.05 mm (3/4 in.) 36 mm
Pipe outside diameter
Dimension A (mm)
Flare tool for R410A, clutch type
6.35 mm (1/4 in.)
0 to 0.5
9.52 mm (3/8 in.)
12.70 mm (1/2 in.)
15.88 mm (5/8 in.)
19.05 mm (3/4 in.)
When using conventional fl are tools to fl are R410A pipes, the
dimension A should be approximately 0.5 mm more than
indicated in the table (for fl aring with R410A fl are tools) to achieve
the specifi ed fl aring. Use a thickness gauge to measure the
dimension A.
Pipe outside diameter Dimension B (mm)
6.35 mm (1/4 in.) 9.1
9.52 mm (3/8 in.) 13.2
12.70 mm (1/2 in.) 16.6
15.88 mm (5/8 in.) 19.7
19.05 mm (3/4 in.) 24.0
0
-0.4
CAUTION
1 Tighten the indoor unit connection cord (to the
outdoor unit) and power supply indoor and
outdoor unit terminal board connections fi rmly
with the terminal board screws. Faulty connection may cause a fi re.
2 If the indoor unit connection cord (to the outdoor
unit) and power supply are wired incorrectly, the
air conditioner may be damaged.
3 Wire the indoor unit connection cord (to the
outdoor unit) by matching the numbers of
the outdoor and indoor units terminal board
numbers as shown in terminal label.
4 Ground both the indoor and outdoor units by
attaching a ground wire.
5 Unit shall be grounded in compliance with the
applicable local and national codes.
RECOMMENDED RANGE OF
EXTERNAL STATIC PRESSURE
30Pa to 150Pa
CAUTION
If the applicable static pressure does not match the
static pressure mode, the static pressure mode may
be changed to another mode automatically.
CHECK ITEMS
(1) Is operation of each button on the remote control unit nor-
mal?
(2) Does each lamp light normally?
(3) Do not air fl ow direction louvers operate normally?
(4) Is the drain normal?
(5) Is there any abnormal noise and vibration during operation?
ü Do not operate the air conditioner in the running state for a
long time.
[OPERATION METHOD]
ü For the operation method, refer to the operating manual.
(1) If the operation lamp is on, press the Start/Stop button to turn
it off.
(2) Press the Master Control Button and Fan Control Button at
the same time for more than two seconds to start the test
operation.
The operation lamp will light up and “
” will be displayed
on the set temperature display.
* Perform the test operation for 60 minutes.
(3) Press the start/stop button to stop the test running.
[Troubleshooting at the remote control LCD]
This is possible only on the wired remote control.
[SELF-DIAGNOSIS]
If an error occurs, the following display will be shown.
(“EE” will appear in the set room temperature display.)
Error code Error contents
01
13
26
27
Indoor signal error
00
Wired remote controller abnormal
02
Indoor room temperature sensor error
04
Indoor heat exchanger temperature sensor
(middle) error
28
Indoor heat exchanger temperature sensor
(inlet) error
09
Float switch operated
0C
Outdoor discharge pipe temperature sensor
error
06
Outdoor heat exchanger temperature sensor
(outlet) error
0A
Outdoor temperature sensor error
15
Compressor temperature sensor error
1d
2-way valve temperature sensor error
1E
3-way valve temperature sensor error
29
Outdoor heat exchanger temperature sensor
(middle) error
20
Indoor manual auto switch abnormal
2A
Power supply frequency detection error
17
IPM protection
18
CT error
1A
Compressor location error
1b
Outdoor fan error
1F
Connected indoor unit abnormal
1c
Outdoor unit computer communication error
12
Indoor fan abnormal
0F
Discharge temperature error
24
Exessive high pressure protection on cooling
2c
4-way valve abnormal
16
Pressure switch abnormal
2b
Compressor temperature error
19
Active fi lter abnormal
25
PFC circuit error
If “CO” appears in the unit number display, there is a remote
controller error.
SPECIAL INSTALLATION
METHODS
8
CAUTION
1 When setting DIP switches, do not touch any
other parts on the circuit board directly with
your bare hands.
2 Be sure to turn off the main power.
1. GROUP CONTROL SYSTEM
ü A number of indoor units can be operated at the same time
using a single remote controller.
ü Depending on the model, some indoor units cannot be con-
nected for group control.
ü Some functions may become unusable, depending on the
combination of the indoor units that are connected in a group.
(1) Wiring method (indoor unit to remote controller)
(2) DIP switch setting (Indoor unit)
Set the unit number of each indoor unit using DIP switch on the
indoor unit circuit board. (See following table and fi gure.)
DIP switch is normally set to make unit number No. 0.
Indoor unit
Unit number DIP SWITCH No.
1234
0 OFF OFF OFF OFF
1 ON OFF OFF OFF
2 OFF ON OFF OFF
3 ON ON OFF OFF
4 OFF OFF ON OFF
5 ON OFF ON OFF
6 OFF ON ON OFF
7 ON ON ON OFF
8 OFF OFF OFF ON
9 ON OFF OFF ON
10 OFF ON OFF ON
11 ON ON OFF ON
12 OFF OFF ON ON
13 ON OFF ON ON
14 OFF ON ON ON
15 ON ON ON ON
Example : No. 3
CUSTOMER GUIDANCE
9
Explain the following to the customer in accordance with the
operating manual:
(1) Starting and stopping method, operation switching, tempera-
ture adjustment, timer, air fl ow switching, and other remote
control unit operations.
(2) Air fi lter removal and cleaning.
(3) Give the operating and installation manuals to the customer.
FUNCTION SETTING
Setting Setting Value
Static pressure
Cooler room temperature
correction
Heater room temperature
correction
Auto restart
Indoor room temperature sensor
switching function
Setting the Static Pressure
Determine the wind volume in each mode i.e., applicable
range of static pressure, refering to [7] STATIC PRESSURE
CHARACTERISTICS. (The unit is factory-set to “00”.)
Setting the Cooler Room Temperature Correction
ü Depending on the installed environment, the room temperature
sensor may require a correction. The settings may be selected
as shown in the table below. (The unit is factory-set to “00”.)
Setting the Heater Room Temperature Correction
ü Depending on the installed environment, the room temperature
sensor may require a correction. The settings may be changed
as shown in the table below. (The unit is factory-set to “00”.)
Setting Other Functions
ü The following settings are also possible, depending on the
operating conditions. (The unit is factory-set to “00”.)
Auto Restart
Indoor Room Temperature Sensor Switching Function (Wired
remote controller only)
ü If setting value is “00”, room temperature is controlled by the
indoor unit temperature sensor.
ü If setting value is “01”, room temperature is controlled by either
indoor unit temperature sensor or remote control unit sensor.
Setting Record
ü Record any changes to the settings in the following table.
Setting Description Function Number Setting Value
Yes
40
00
No 01
Setting Description Function Number Setting Value
Standard
31
00
Lower control 01
Slightly warmer control 02
Warmer control 03
Setting Description Function Number Setting Value
Standard
30
00
Lower control 01
Setting Description Function Number Setting Value
Normal
21
00
High static pressure 1 01
High static pressure 2 02
High static pressure 3 03
Setting Description Function Number Setting Value
No
42
00
Yes 01
After completing the FUNCTION SETTING, be sure to turn off
the power and turn it on again.
1. STATIC PRESSURE MODE
It is necessary to set up a static pressure mode for each usage
of static pressure.
Determine the applicable range of static pressure in each mode
and wind volume, referring to the TECHNICAL MANUAL.
2. MODE SETTING
It is possible to change the setting of static pressure mode. Refer
to [5] FUNCTION SETTING.
HOW TO CONNECT WIRING TO THE
TERMINALS
For strand wiring
(1) Use crimp-type terminals with insulating sleeves as shown
in the fi gure below to connect to the terminal block.
(2) Securely crimp the crimp-type terminals to the wires using
an appropriate tool so that the wires do not come loose.
(3) Use the specifi ed wires, connect them securely, and fasten
them so that there is no stress placed on the terminals.
(4) Use an appropriate screwdriver to tighten the terminal
screws.
Do not use a screwdriver that is too small, otherwise, the
screw heads may be damaged and prevent the screws
from being properly tightened.
(5) Do not tighten the terminal screws too much, otherwise,
the screws may break.
(6) See the table below for the terminal screw tightening
torques.
CAUTION
Do not bundle the remote controller cord, or wire
the remote controller cord in parallel, with the
indoor unit connection wire (to the outdoor unit)
and the power supply cord. It may cause erroneous
operation.
ü Use a 4-core wire cord.
(2) After wiring is complete, secure the remote controller cord,
connection cord, and power cord with the cord clamps.
4
REMOTE CONTROLLER
SETTING
1.
INSTALLING THE REMOTE CONTROLLER
Open the operation panel on the front of the remote controller,
remove the two screws indicated in the following fi gure, and then
remove the front case of the remote controller.
When installing the remote controller, remove the connector
from the front case. The wires may break if the connector is
not removed and the front case hangs down.
When installing the front case, connect the connector to the
front case.
Front case
(back side)
Rear case
Connector
Screws
When remote controller cord is embedded
(1) Embed the remote controller cord and box.
(2) Pass the remote controller cord through the hole in the rear
case and connect the remote controller cord to the remote
controller terminal board specifi ed in the fi gure.
(3) Clamp the remote controller cord sheath with the binder as
shown in the fi gture.
(4) Cut off the excess binder.
(5) Install the rear case to the wall, box, etc., with two screws.
Connection cord
(to outdoor unit)
Cord clamp
Remote
controller cord
Cord clamp
45 mm
Adjust the position of the screws for control box cover according
to the installation.
CAUTION
When connecting the
remote controller wires,
do not overtighten the
screws.
Binder
(Small)
Hole
1. Red
2. White
3. Black
CAUTION
1 Install the remote controller wires so as not to
be direct touched with your hand.
2 Do not touch the remote controller PC board
and PC board parts directly with your hands.
2.
SETTING THE DIP SWITCHES
Set the remote controller DIP switches.
Front case (back side)
Do not use this
DIP switch 2
DIP switch 1
[Example]
NO.
SW state
Detail
OFF ON
DIP
switch 1
1
´
Cannot be used. (Do not
change)
2
´
Dual remote controller setting
*Refer to 2. DUAL REMOTE
CONTROLLERS in 3
SPECIAL INSTALLATION
METHODS.
3
Follow the
selection in
FUNCTION
SETTING
Invalidity
Filter reset operation and filter
display
4
´
Cannot be used. (Do not change)
5
´
Cannot be used. (Do not change)
6
´ Invalidity
Validity
Memory backup setting
*Set to ON to use batteries for the
memory backup. If batteries are
not used, all of the settings stored
in memory will be deleted if there
is a power failure.
(´ Factory setting)
3.
TURNING ON THE POWER
1. Check the remote controller wiring and DIP switch settings.
2. Install the front case.
* When installing the front case, connect the connector to the
front case (in 1 REMOTE CONTROLLER SETTING).
3. Check the indoor and outdoor unit wiring and circuit board
switch settings, and then turn on the indoor and outdoor
units. After “ ” has fl ashed on the set temperature display
for several seconds, the clock display will appear in the center
of the remote controller display.The clock display will appear
in the center of the remote controller display.
4.
SETTING THE ROOM TEMPERATURE
DETECTION LOCATION
The detection location of the room temperature can be selected
from the following two examples. Choose the detection location
that is best for the installation location.
A. Indoor unit setting (factory setting)
The room temperature is detected by the indoor unit temperature
sensor.
(1) When the THERMO SENSOR button is pressed, the lock
display fl ashes because the function is locked at the factory.
B. Indoor unit/remote controller setting (room temperature
sensor selection)
The temperature sensor of the indoor unit or the remote controller
can be used to detect the room temperature.
(1) Enable the room temperature sensor selection in FUNCTION
SETTING, which will be described later.
(2) Press the THERMO SENSOR button for 5 seconds or more to
select the temperature sensor of the indoor unit or the remote
controller.
NOTES
If the function to change the temperature sensor is used as shown
in examples A (other than example B), be sure to lock the detection
location. If the function is locked, the lock display
will fl ash
when the THERMO SENSOR button is pressed.
Indoor unit
Operation Method
(1) Press the set temperature
buttons ( ) ( ) and fan
control button simultaneously
for more than 5 seconds to
enter the function setting
mode.
(2) Press the SET BACK button
to select the indoor unit
number.
(3) Press the set time buttons to
select the function number.
value stops fl ashing.
If the setting value display changes or if “- -” is displayed
when the fl ashing stops, the setting value has not been set
correctly.
(An invalid setting value may have been selected for the indoor
unit.)
(6) Repeat steps 2 to 5 to perform additional settings.
Press the set temperature buttons ( ) ( ) and fan control
button simultaneously again for more than 5 seconds to cancel
the function setting mode.
In addition, the function setting mode will be automatically
canceled after 1 minute if no operation is performed.
(7) After completing the FUNCTION SETTING, be sure to turn
off the power and turn it on again.
ü This procedure changes to the function settings used to control
the indoor unit according to the installation conditions. Incorrect
settings can cause the indoor unit malfunction.
ü After the power is turned on, perform the “FUNCTION SETTING”
according to the installation conditions using the remote
controller.
ü The settings may be selected between the following two: Func-
tion Number or Setting Value.
ü Settings will not be changed if invalid numbers or setting values
are selected.
Unit number of INDOOR UNIT
Function number
(4) Press the set temperature
buttons ( ) ( ) to select
the setting value.
The display fl ashes as shown
to the right during setting
value selection.
(5) Press the SET button to
confi rm the setting.
Press the SET button for a
few seconds until the setting
Setting value
2. DUAL REMOTE CONTROLLERS
ü Two separate remote controllers can be used to operate the
indoor units.
ü The timer and self-diagnosis functions cannot be used on the
slave units.
(1) Wiring method (indoor unit to remote controller)
(2) Remote controller DIP switch 1 setting
Set the remote controller DIP switch 1 No. 2 according to the
following table.
Number of remote
controllers
Master unit Slave unit
DIP SW 1 No. 2 DIP SW 1 No. 2
1 (Normal) OFF -
2 (Dual) OFF ON
Remote controller cord
Indoor unit
When ground wire
is necessary
Master unit Slave unit
Remote controller
[Example]
Hole
Hole × 3
Hole × 2
Unit : mm
Unit number Error code Content
C0 1d
Incompatible indoor unit is
connected
C0 1c
Indoor unit ↔ remote controller
communication error
Tightening torque
M4 screw 1.2 to 1.8 N·m (12 to 18 kgf·cm)
WARNING
Use crimp-type terminals and tighten the terminal
screws to the specifi ed torques, otherwise, abnor-
mal overheating may be produced and possibly
cause heavy damage inside the unit.
Wired remote controller cord
* Ground the remote controller ip it has a ground wire
CAUTION
1 In order to detect the room
temperature correctly when
using the temperature sensor
of the remote controller, do not
install the remote controller in a
place where it will be exposed
Temperature sensor
to direct sunlight or directly below the air outlet
of the indoor unit.
2 Do not touch the remote controller PC board
and PC board parts directly with your hands.
3 Do not wire the remote controller cord and the
bus wire together with or parallel to the connection cables, transmission cords, and power
supply cords of the indoor and outdoor units.
It may cause erroneous operation.
4 When installing the bus wire near a source of
electromagnetic waves, use shielded wire.
5 Do not set the DIP switches, either on the air
conditioner or the remote controller, in any way
other than indicated in this sheet or the manual
that is supplied with the air conditioner. Doing
so may result in an accident.
Ground the remote controller if
it has a ground wire.
Wrap the connector
and remote controller
wires with vinyl tape
or some other type of
insulation as shown
in the fi gure.
Remote controller
Remote
controller cord
Connector
Screws
Rear case
Box
Indoor unit 0 Indoor unit 1 Indoor unit 2 Indoor unit 3
Bus wire
Remote
controller cord
When ground wire is necessary
Check if [L] is flared uniformly
and is not cracked or scratched
Die
A
Pipe
L
Width across flats
B
o prevent gas leakage, coat the flar
urface with alkylbenzene oil (HAB
Do not use mineral oil
Holding
spanner
Torque wrench
Unit
side
Wire
mm
01 pirtS
Screw with
special washer
Crimp-type terminal
Terminal
board
Terminal block
Wire
Crimp-type
terminal
Sleeve
Screw with
special washer
Crimp-type
terminal
3
enil lo
noC
rt
2
1
roodnI
tin
u
ed
is
3
2
1
u roodnI
tin
d
is
e
*
Black
hW
Red
l
ni
ewo
e
r
P
t
e
i
Control box cover
Screw
SET BACK
120
0
2
1
17
3.54
30 33.5
23
8
5.4
5.215.4
6
4.5
OFF
1
2
3
4
5
6
ON
ON
3
.
51
5.
3
5.38
6
SUMOTUWETH FR
SA
9374318285_B2.indd 29374318285_B2.indd 2 11/21/07 4:01:34 PM11/21/07 4:01:34 PM
A
B
SET BACK
SUMOTUWETH FR
SA
SUMOTUWETH FR
SA
SA
SUMOTUWETH FR
FAN MODE
Test run display
Unit number
SUMOTUWETH FR
Error code
SA
EX. Self-diagnosis
123
123
123 123 123
ON
1234
1 2 3
1 231 23