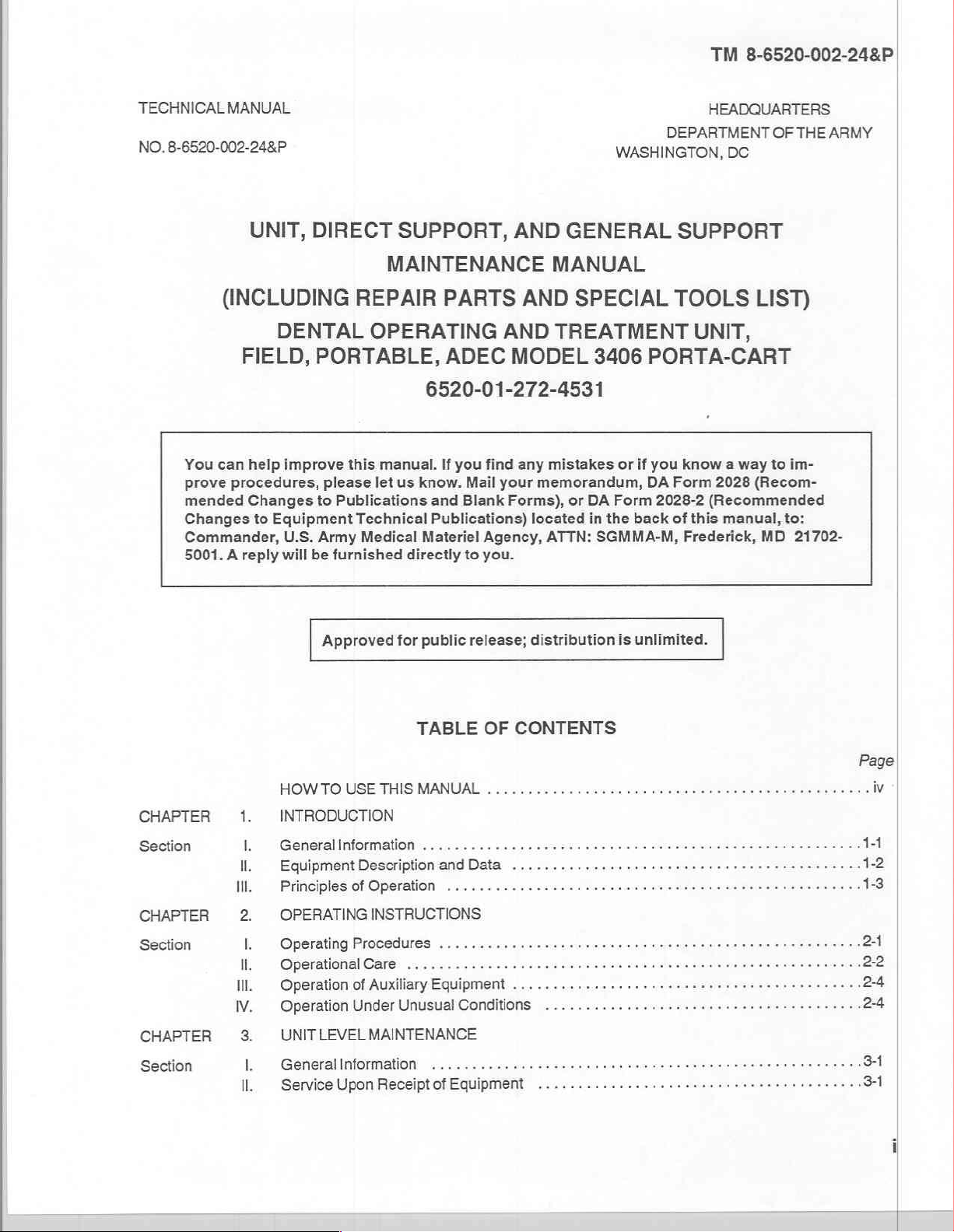
TM
8-6520-002-24&P
|
TECHNICAL
NO.
8-6520-002-248P
MANUAL
UNIT,
(INCLUDING
FIELD,
You
can
help
prove
procedures,
mended
Changes
Commander,
5001. A reply
Changes
to
DIRECT
DENTAL
PORTABLE,
improve
please
to
Publications
Equipment
U.S.
Army
will
be
furnished
SUPPORT,
MAINTENANCE
REPAIR
OPERATING
6520-01-272-4531
this
manual.
let
us
know.
Technical
Medical
Materiel
directly
AND
PARTS
AND
AND
ADEC
If
you
and
Blank
Publications)
to
find
Mail
Agency,
you.
MODEL
any
your
Forms),
GENERAL
MANUAL
SPECIAL
TREATMENT
3406
mistakes
memorandum,
or
DA
located
ATTN:
in
the
SGMMA-M,
HEADQUARTERS
DEPARTMENT
WASHINGTON,
DC
SUPPORT
TOOLS
UNIT,
PORTA-CART
or
if
you
know a way
DA
Form
2028
Form
2028-2
back
(Recommended
of
this
manual,
Frederick,
OF
THE
LIST)
to
im-
(Recom-
to:
MD
21702-
ARMY
CHAPTER
Section
CHAPTER
Section
CHAPTER
Section
1.
I.
И.
Il.
2.
ll
|.
Ill.
IV.
3.
|.
I.
o
Approved
HOW
TO
USE
INTRODUCTION
General
Equipment
Principles
OPERATING
Operating
Operational
Operation
Operation
UNITLEVEL
General
Service
Information
Description
of
Procedures
of
Under
Information
Upon
for
public
TABLE
THIS
MANUAL...
and
Operation
INSTRUCTIONS
......
Care
Auxiliary
MAINTENANCE
Receiptof
Equipment
Unusual
release;
OF
see
Data
........
еее
Conditions
Eguipment
distribution
is
CONTENTS
нение
..
................
...................
unlimited.
a
инея
as
ser
0...
renen
eee
ee
e
venerne
rr
eee
Page|
iv
2-1
ne
3-1
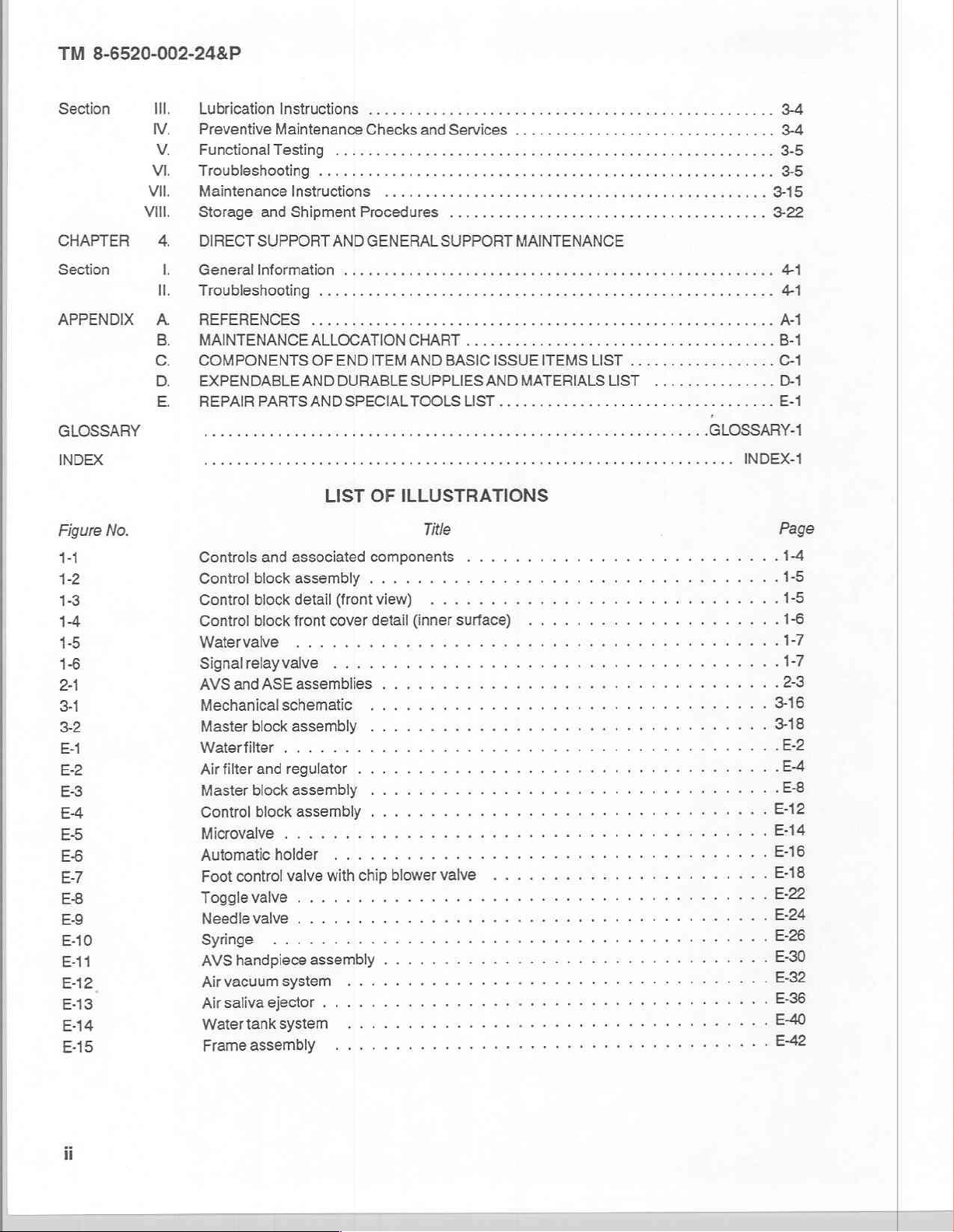
TM
8-6520-002-24&P
Section
CHAPTER
Section
APPENDIX
GLOSSARY
INDEX
Figure
No.
1-1
1-2
1-3
1-4
1-5
16
2-1
3-1
32
E-1
E-2
E-3
E-4
ES
E-6
E-7
E-8
E-9
E-10
E-11
E-12
E-13
E-14
E-15
11.
SEZ
Vil.
Vill.
4.
L
Il
A
B.
C.
D.
E
Lubrication
Preventive
Functional
Troubleshooting
Maintenance
Storage
DIRECT
General
Troubleshooting
REFERENCES
MAINTENANCE
COMPONENTS
EXPENDABLE
REPAIR
Controls
Control
Control
Control
Water
Signal
AVS
Mechanical
Master
Water
Air
filter
Master
Control
Microvalve
Automatic
Foot
Toggle
Needle
SYNGE:
AVS
Air
vacuum
Air
saliva
Water
Frame
Instructions
Maintenance
Testing
Instructions
and
Shipment
SUPPORT
Information
PARTS
and
associated
block
assembly
block
detail
block
front
valve
relay
valve
and
ASE
assemblies
schematic
block
assembly
filt@n
vic
and
regulator
block
assembly
block
assembly
holder
control
handpiece
valve
valve
valve
scan
system
ejector
tank
system
assembly
Checks
......
Procedures
AND
GENERAL
..
.
..
ALLOCATION
OF
END
AND
DURABLE
AND
SPECIAL
LIST
(front
cover
CHART
ITEM
AND
SUPPLIES
TOOLS
OF
ILLUSTRATIONS
components
view)
detail
cms
ancas»
with
chip
blower
rs
assembly
and
Services
SUPPORT
BASIC
Title
(inner
valve
...
..
ISSUE
AND
LIST
surface)
..
MAINTENANCE
ITEMS
MATERIALS
.....................
LIST
LIST
...
ss
41
.
41
„Aj
.B-1
Page
1-6
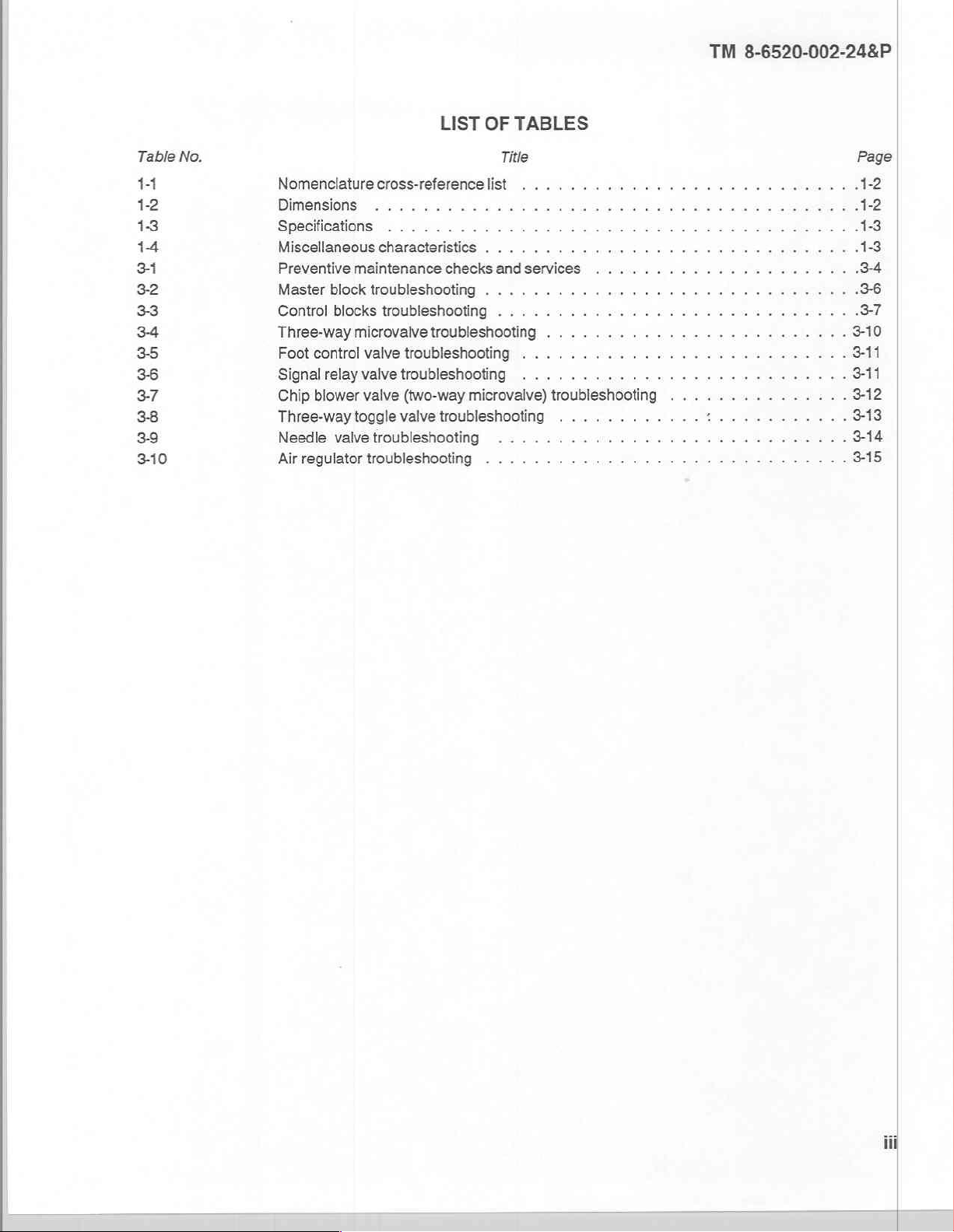
Table
No.
LIST
OF
Title
TABLES
TM
8-6520-002-24&P
1-1
1-2
1-3
14
31
32
33
3-4
35
3-6
3-7
3-8
39
8-10
Nomenclature
Dimensions
Specifications
Miscellaneous
Preventive
Master
Control
Three-way
Foot
Signal
Chip
Three-way
Needle
Air
block
control
relay
blower
regulator
cross-reference
...........
characteristics
maintenance
troubleshooting . ..............................
blocks
microvalve
valve
valve
valve
toggle
valve
troubleshooting
troubleshooting . 2...
list
.........
.
checks
troubleshooting
troubleshooting
troubleshooting
troubleshooting
(tWo-way
valve
microvalve)
troubleshooting
............................
and
services
................
............
..............
..............
troubleshooting
........................
0.
ee
πο
ee
ee
eee
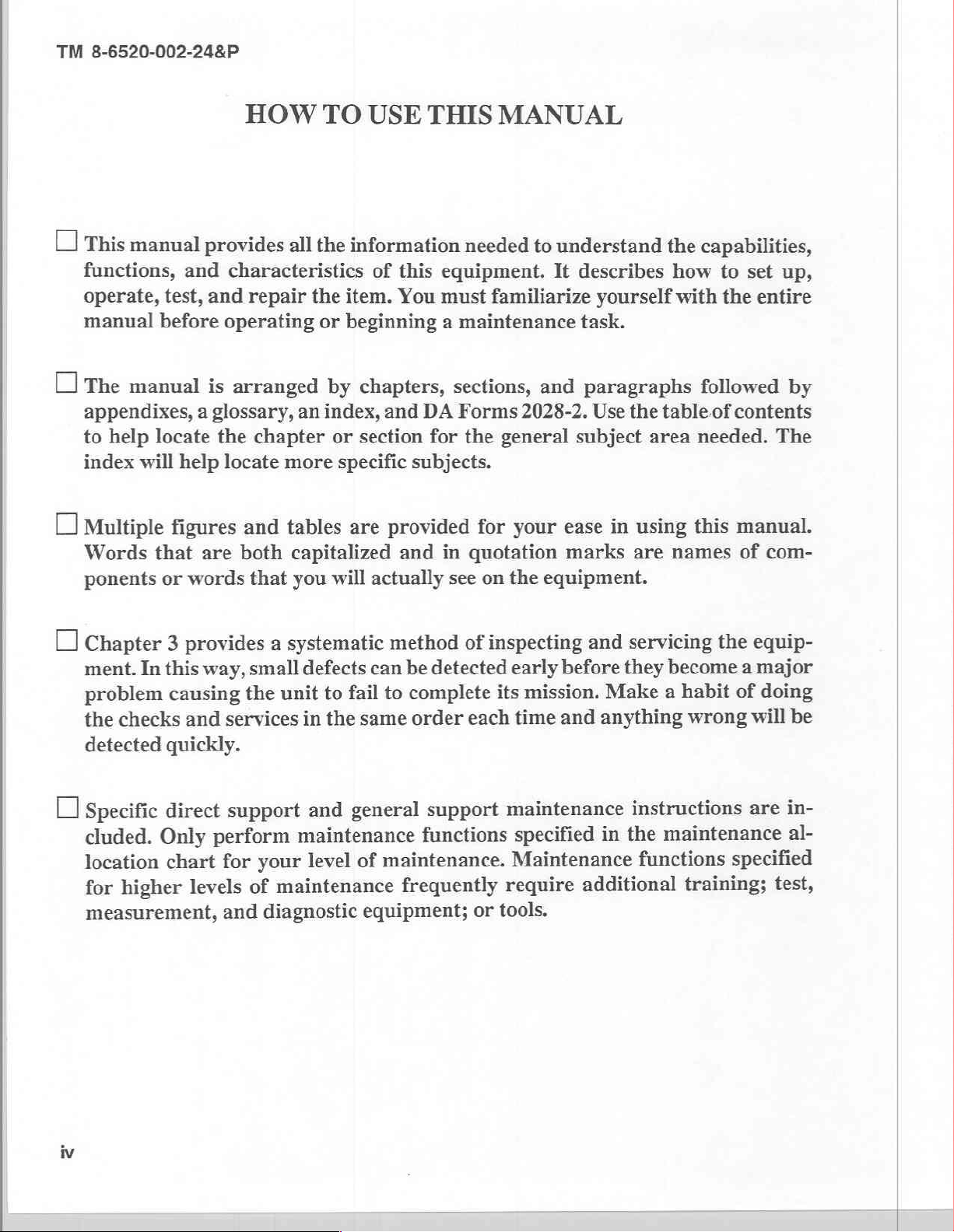
TM
8-6520-002-24&P
O
This
manual
functions,
operate,
manual
Lİ
The
manual
appendixes, a glossary,
to
index
O
Multiple
Words
help
locate
will
that
ponents
provides
and
test,
and
before
is
the
help
figures
are
or
words
characteristics
operating
arranged
locate
HOW
all
repair
chapter
more
and
tables
both
capitalized
that
you
TO
USE
the
information
of
the
item.
or
beginning a maintenance
by
chapters,
an
index,
or
section
specific
are
will
actually
THIS
this
equipment.
You
must
sections,
and
DA
Forms
for
subjects.
provided
and
in
see
needed
the
quotation
MANUAL
to
understand
It
familiarize
and
2028-2.
general
for
on
your
the
ease
marks
equipment.
describes
yourself
task.
paragraphs
Use
the
subject
in
area
using
are
the
capabilities,
how
table.of
to
with
the
followed
set
contents
needed.
this
manual.
names
of
up,
entire
by
The
com-
[]
Chapter 3 provides a systematic
ment.
problem
the
detected
Specific
O
cluded.
location
for
measurement,
In this
causing
checks
quickly.
direct
Only
chart
higher
way,
services
and
support
perform
for
levels
and
small
the
unit
maintenance
your
maintenance
of
diagnostic
defects
in
and
level
can
to
fail
same
the
general
of
equipment;
method
be
to
complete
order
of
inspecting
detected
its
each
support
functions
maintenance.
frequently
tools.
or
and
early
time
maintenance
specified
before
mission.
and
Make a habit
anything
in
Maintenance
require
additional
servicing
they
become a major
the
wrong
instructions
maintenance
the
functions
training;
equip-
of
doing
be
will
in-
are
al-
specified
test,
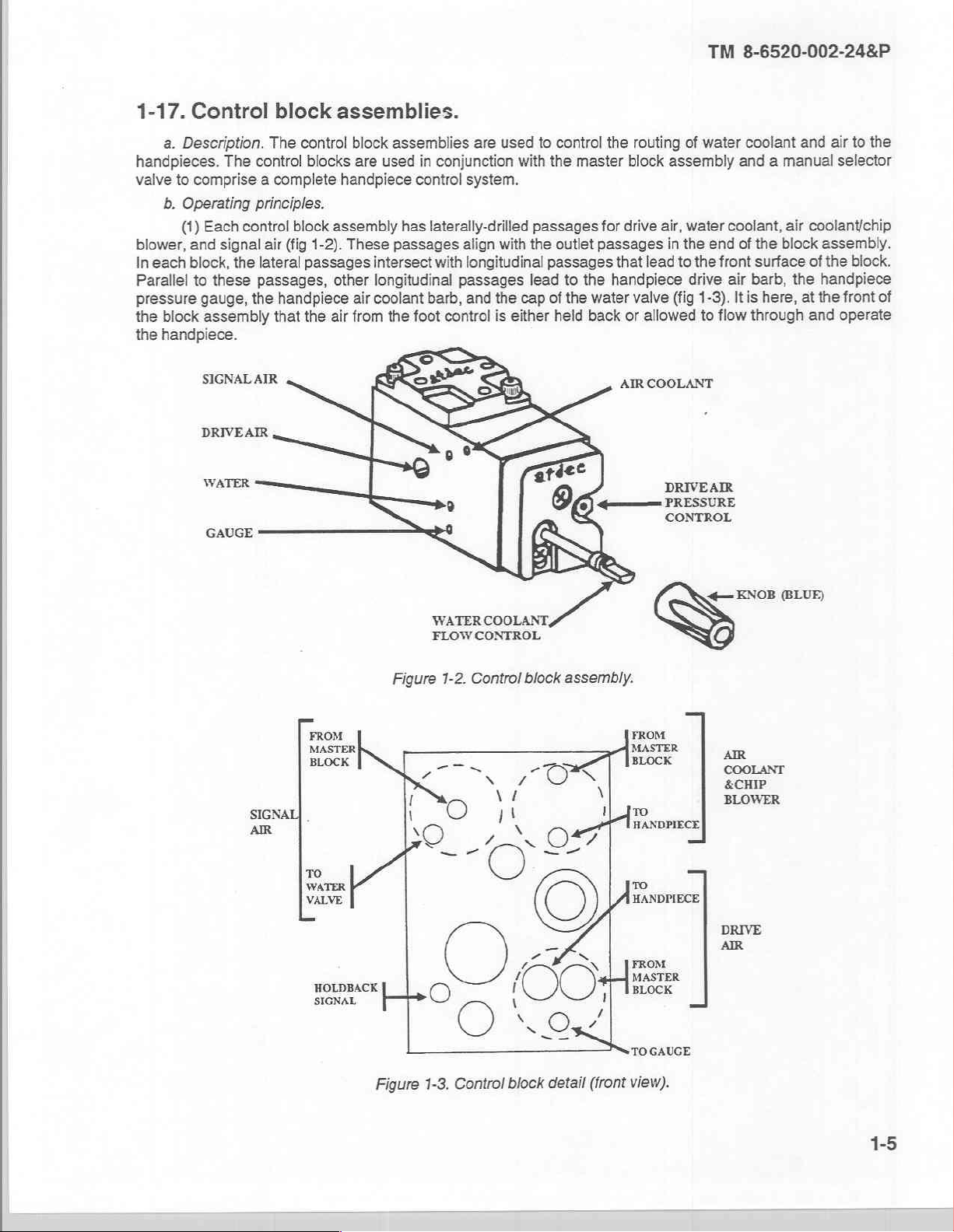
TM
8-6520-002-24&P
1-17.
handpieces.
valve
blower,
In
Parallel
pressure
the
the
Control
a.
Description.
to
comprise a complete
b.
Operating
(1)
Each
and
each
block,
to
these
gauge,
block
assembly
handpiece.
SIGNABAIR
DRIVEAIR
WATER
GAUGE
block
The
The
control
principles.
control
signal
air
(fig
the
lateral
passages,
the
handpiece
that
assemblies.
control
block
passages
the
blocks
handpiece
assembly
1-2).
These
other
air
block
are
air
from
assemblies
used
in
conjunction
control
has
laterally-drilled
passages
intersect
longitudinal
coolant
the
with
barb,
foot
passages
control
are
used
to
with
system.
passages
align with the
longitudinal
and
the
is
passages
lead
cap
of
either
control
the
master
outlet
to
the
the
water
held
back
the
routing
block
for
drive
passages
that
lead
handpiece
valve
or
allowed
AIR
COOLANT
—
of
water
assembly
air,
water
in
the
end
to
the
front
drive
(fig
1-3).
to
flow
DRIVEAR
PRESSURE
CONTROL
coolant and
and a manual
coolant,
of
air
Itis
air
the
block
surface
barb,
the
here,
through
at
air
to
the
selector
coolant/chip
assembly.
of
the
block.
handpiece
the
front
of
and
operate
FROM
MASTER
BLOCK
WATER
FLOW
Figure
M
I
SIGNAI
AIR
\
x
P
TO
WATER
VALVE
HOLDBACK
SIGNAL
|
>
O
1-2.
—
O
O
COOLANT,
CONTROL
Control
~
Xi
gı
x
O
00;
\
x
block
-
¿O
©
一
一
^
Os
assembly.
№
1
A
Tİ
HANDPIECE
7
x
x
1
/
TO
FROM
MASTER
BLOCK
To
HANDPIECE,
FROM
а
BLOCK
GAUGE
ペー
KNOB
AIR
COOLANT
&CHIP
BLOWER
DRIVE
AIR
(BLUF)
Figure
1-3.
Control
block
detail
(front
view).
1-5
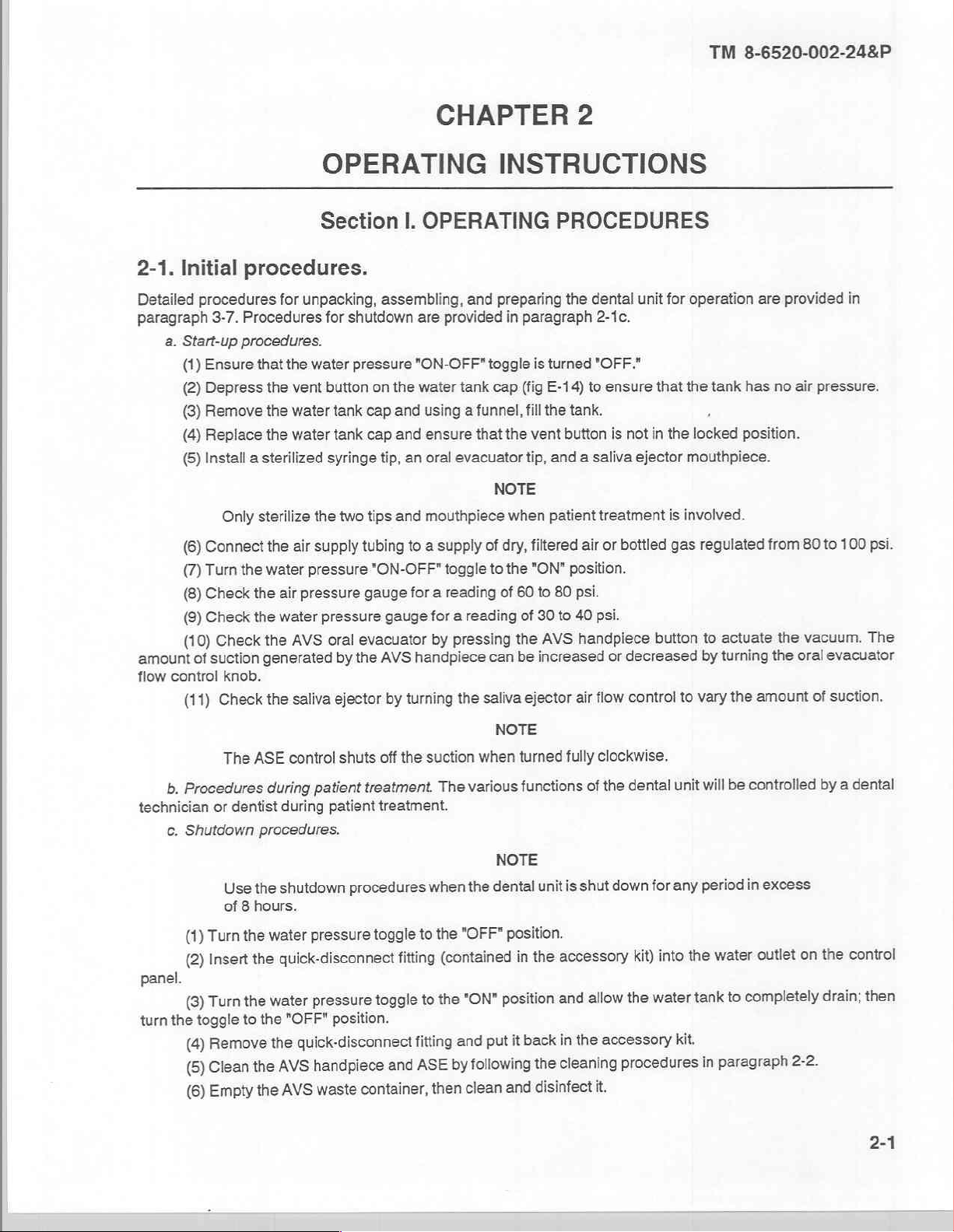
TM
8-6520-002-24&P
2-1.
Initial
Detailed
procedures
paragraph
a.
Start-up
(1)
(2)
(3)
(4)
(6)
(6)
(7)
(8)
(8)
(10)
amount
flow
of
control
(11)
OPERATING
Section
procedures.
for
unpacking,
3-7.
Procedures
procedures.
Ensure
Depress
Remove
Replace
Install a sterilized
Connect
Turn
Check
Check
suction
Only
the
Check
knob.
Check
that the
sterilize
the
the
generated
the
vent
the
water
the
water
the
air
water
air
water
AVS
the
saliva
the
water
the
supply
pressure
pressure
pressure
for
shutdown
pressure
button
tank
cap and
tank
cap
syringe
two
tips
tubing
gauge
evacuator
oral
the
by
ejector
CHAPTER
|.
OPERATING
assembling,
are
"ON-OFF"
on
the
water
using a funnel,
and
ensure
tip,
an
oral
and
mouthpiece
to a supply
"ON-OFF"
for a reading
gauge
for a reading
by
handpiece
AVS
turning
by
INSTRUCTIONS
and
preparing
provided
toggle
tank
cap
that the
evacuator
NOTE
of
dry,
toggle
to
of
pressing
can
saliva
the
in
paragraph
is
turned
(fig
E-14)
fill
the
vent
tip,
and a saliva
when
patient
filtered
the
"ON"
60
to
80
of
30
AVS
the
increased
be
ejector
2
PROCEDURES
the
dental
unit
2-1c.
"OFF."
to
tank.
button
treatment
air
or
position.
psi.
to
40
psi.
handpiece
flow
air
ensure
or
that
is
not
in
ejector
bottled
button
decreased
control
for
operation
the
tank
the
locked
mouthpiece.
is
involved.
gas
regulated
to
by
vary
to
are
has
position.
from
actuate
turning
amount
the
provided
no
air
80
vacuum.
the
oral
the
of
in
pressure.
to
100
psi.
The
evacuator
suction.
Procedures
b.
technician
с.
Shutdown
Turn
(1)
Insert
(2)
panel.
Turn
(3)
turn
the
toggle
Remove
(4)
Clean
(5)
Empty
(6)
The
or
dentist
Use
of
8
the
the
to
ASE
control
during
during
procedures.
shutdown
the
shuts
patient
patient
hours.
pressure
water
quick-disconnect
the
pressure
water
the
"OFF"
position.
quick-disconnect
the
handpiece
AVS
the
waste
AVS
the
off
the
treatment.
treatment.
procedures
to
toggle
fitting
to
toggle
fitting
ASE
and
container,
suction
when
The
the
when
various
the
"OFF"
(contained
"ON"
the
and
following
by
clean
then
NOTE
turned
functions
NOTE
dental
position.
the
in
position
back
it
put
the
disinfect
and
fully
shut
is
unit
accessory
and
the
in
cleaning
clockwise.
dental
the
of
down
kit)
the
allow
accessory
procedures
it.
unit
any
for
into
water
kit,
will
period
water
the
tank
paragraph
in
controlled
be
excess
in
outlet
completely
to
on
2-2.
dental
a
by
control
the
drain;
then
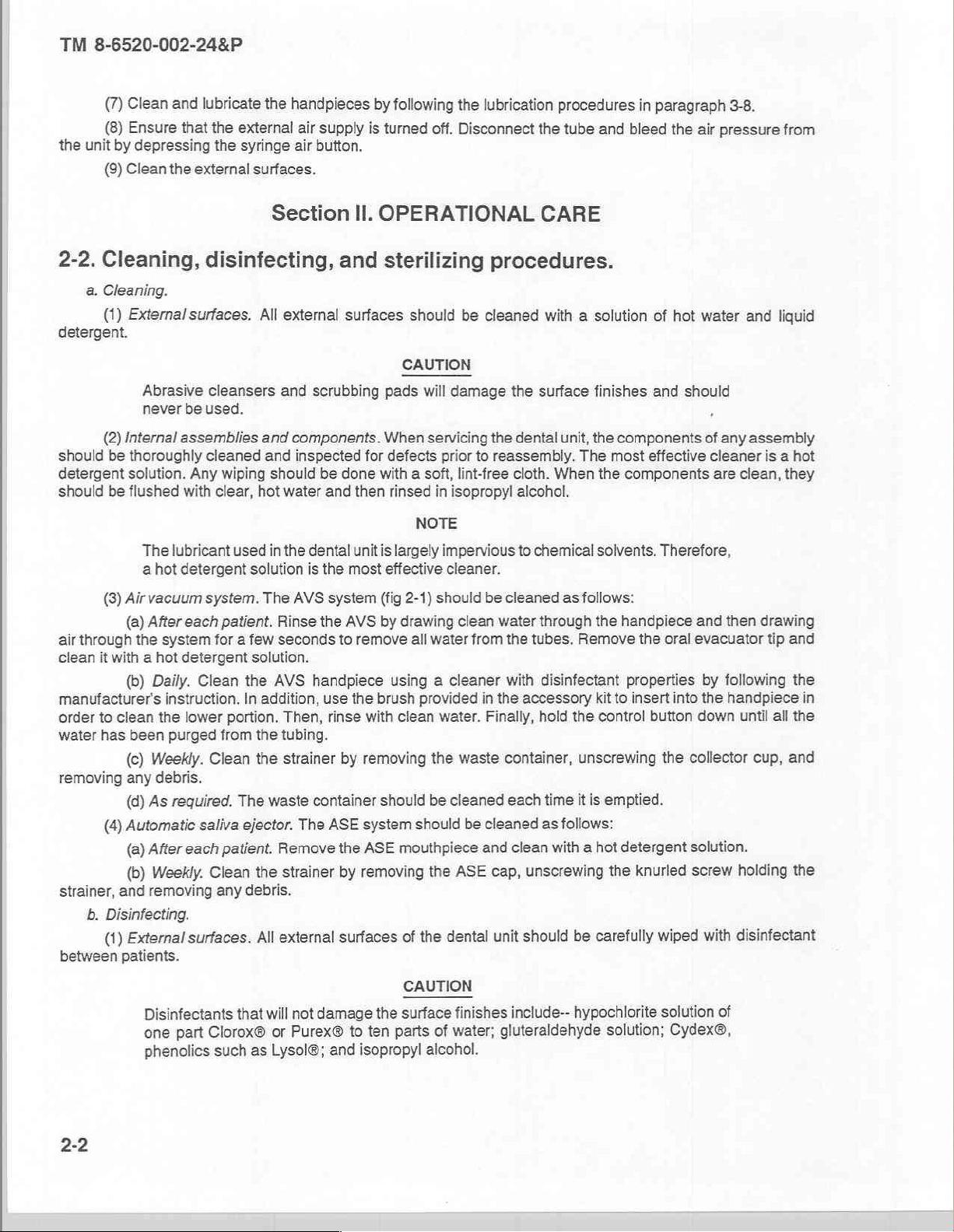
TM
8-6520-002-24&P
(7)
Clean
(8)
Ensure
the
unit
by
depressing
(9)
Clean
and
that
the
external
lubricate
the
the
the
external
syringe
surfaces.
handpieces
air
supply
air
button.
by
following
is
turned
the
off.
Disconnect
lubrication
procedures
the
tube and
in
paragraph
bleed
the
3-8.
air
pressure
from
2-2.
Cleaning,
a.
Cleaning.
(1)
External
detergent.
Abrasive
never
(2)
internal
should
detergent
should
be
thoroughly
solution.
be
flushed
The
a
hot
(3)
Air
vacuum
(a)
After
air
through
clean
the
it
with a hot
(b)
system
Daily.
manufacturer's
order
to
clean
the
water
has
been
(c)
Weekly.
removing
strainer,
between
any
debris.
(d)
As required.
(4)
Automatic
(8)
After
(b)
Weekly.
and
removing
b.
Disinfecting.
External
(1)
patients.
disinfecting,
surfaces.
cleansers
be
used.
assemblies
cleaned
Any
wiping
with
clear,
lubricant
detergent
each
detergent
instruction.
lower
purged
each
used
solution
system. The
patient.
for a few
solution.
Clean
the
In
portion.
from
Clean
The
saliva
ejector.
patient.
Clean
any
debris.
surfaces.
Section
All
external
and
scrubbing
and
components.
and
inspected
should
hot
water
in
the
dental
is
AVS
Rinse
seconds
AVS
handpiece
addition,
Then,
the
tubing.
the
strainer
waste
container
The
Remove
the
strainer
external
All
Il.
and
surfaces
be
done
and
then
unitis
the
most
system
the
AVS
to
remove
use
the
rinse
by
ASE
the
by
surfaces
OPERATIONAL
sterilizing
should
CAUTION
pads
will
damage
When
servicing
for
defects
with a soft,
rinsed
largely
effective
(fig
by
using a cleaner
brush
with
removing
should
system
ASE
removing
prior
lint-free
in
isopropyl
NOTE
impervious
cleaner.
2-1)
should
drawing
all
clean
water
provided
clean
water.
the
waste
be
cleaned
should
mouthpiece
the
ASE
dental
the
of
CARE
procedures.
be
cleaned
the
surface
the
dental
to
reassembly.
cloth.
alcohol.
to
chemical
be
cleaned
water
through
from
the
tubes.
with
disinfectant
in
the
accessory
Finally,
be
cleaned
and
cap,
hold
container,
each
as
clean
unscrewing
should
unit
with a solution
finishes
unit,
the
components
The
most
When
the
components
solvents.
as
follows:
the
handpiece
Remove
the
properties
kit
to
insert
the
control
unscrewing
time
it
is
emptied.
follows:
with a hot
be
detergent
the
knurled
carefully
of
hot
water
and
should
of
effective
cleaner
Therefore,
and
oral
evacuator
by
into
the
button
down
the
collector
solution.
screw
with
wiped
and
any
assembly
is a hot
are
clean,
then
drawing
tip
following
handpiece
until
all
cup,
holding
disinfectant
liquid
they
and
the
in
the
and
the
Disinfectants
part
one
phenolics
that
Clorox®
such
will
or
as
Lysol®;
not
damage
Purex©
and
CAUTION
the
surface
parts
ten
to
isopropyl
finishes
water;
of
alcohol.
include--
hypochlorite
gluteraldehyde
solution
solution;
Cydex®,
of
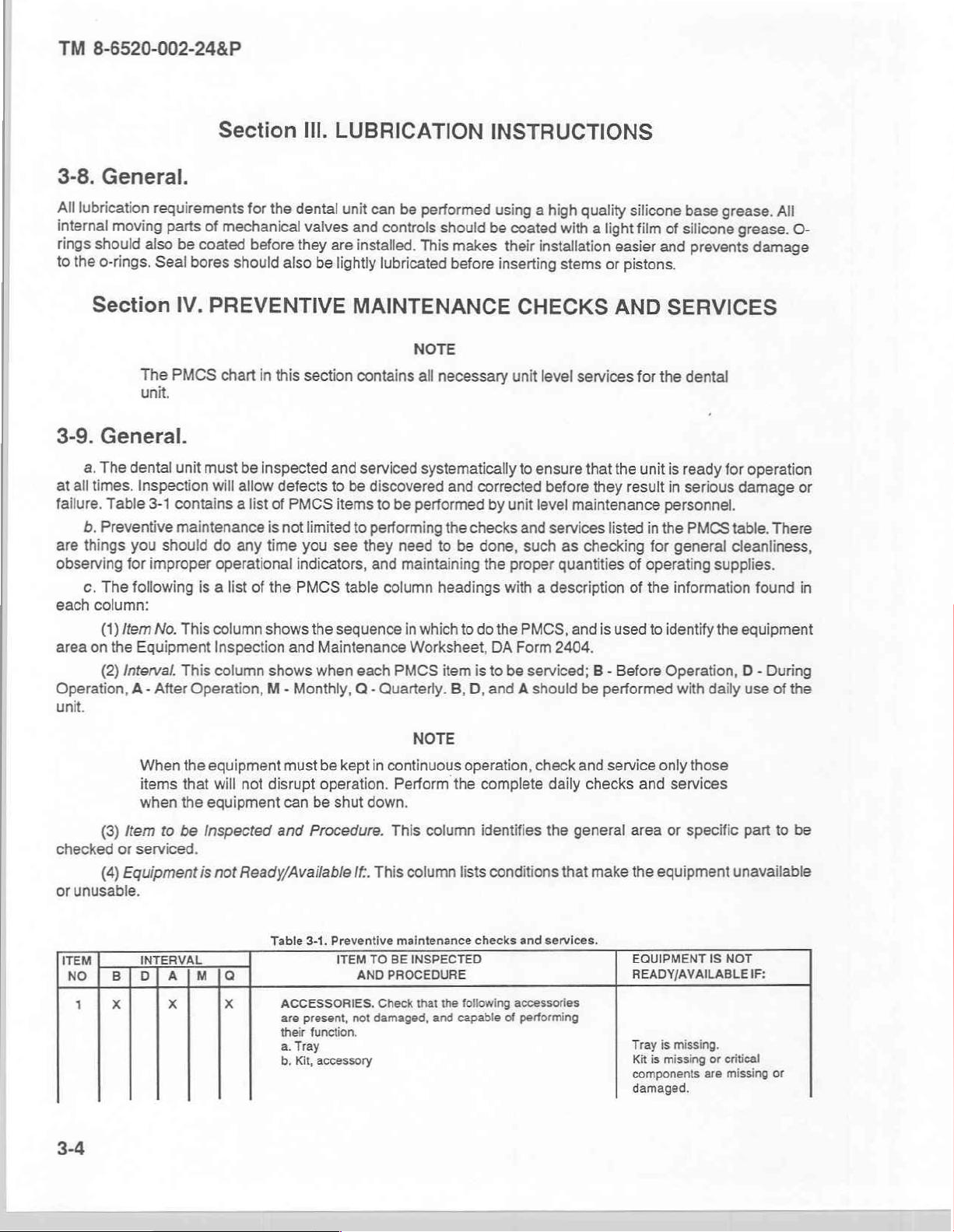
TM
8-6520-002-24&P
3-8.
General.
All
lubrication
internal
tings
to
should
o-rings.
the
moving
also
Section
The
unit.
3-9.
General.
a.
The
dental
at
all
times.
failure.
b.
are
things
observing
c.
each
area
on
Operation, A -
unit.
Inspection
Table
3-1
Preventive
you
for
The
following
column:
(1)
Item
the
Equipment
(2)
Interval.
Section
requirements
parts
of
mechanical
be
coated
should
bores
Seal
IV.
PREVENTIVE
PMCS
should
improper
No.
After
chart
unit
must
will
contains a list
maintenance
do
operational
is a list
This
column
Inspection
This
column
Operation, M -
for
the
before
in
this
be
inspected
allow
defects
of
is
any
time
of
the
shows
shows
III.
LUBRICATION
dental
unit
valves
they
are
lightly
be
also
section
and
to
be
PMCS
not
and
items
limited
you
see
indicators,
PMCS
Monthly, Q -
table
the
sequence
Maintenance
when
can
be
performed
and
controls
installed.
lubricated
should
This
makes
before
MAINTENANCE
NOTE
contains
serviced
discovered
to
performing
they
and
each
all
necessary
systematically
and
to
be
performed
the
need
to
maintaining
column
Quarterly.
headings
in
which
Worksheet,
PMCS
item
be
to
B, D,
INSTRUCTIONS
using
a
high
be
coated
their
inserting
with
installation
stems
CHECKS
unit
level
services
to
ensure
corrected
by
checks
done,
the
do
the
DA
is
to
and A should
before
unit
level
maintenance
and
services
such
as
proper
with a description
be
quantities
PMCS,
Form
and
2404.
serviced; B -
quality
a
light
easier
or
silicone
film
pistons.
AND
for
that the
they
result
listed
checking
of
of
is
used
Before
be
performed
base
of
silicone
and
prevents
SERVICES
the
dental
unit
is
ready
in
serious
personnel.
in
the
PMCS
for
general
operating
the
information
to
identify the
Operation, D -
with
grease.
grease.
damage
for
operation
damage
table.
There
cleanliness,
supplies.
found
equipment
During
daily
use
All
of
O-
or
in
the
When
the
items
that
when
the
(3)
Item
to
be
Inspected
checked
or
ITEM
NO
or
serviced.
(4)
Equipment
unusable.
BIDIA
1
x
is
INTERVAL
| M |Q
x
equipment
Will
equipment
not
x
must
not
disrupt
can
and
Ready/Available
Table
ACCESSORIES.
are
their
a.
b.
be
kept
operation.
be
shut
Procedure.
If..
3-1.
Preventive
ITEM
AND
present,
not
function.
Tray
Kit,
accessory
NOTE
in
continuous
Perform
down.
This
This
column
maintenance
TO BE
INSPECTED
PROCEDURE
Check
that
damaged,
operation,
the
column
lists
the
following
and
capable
check
complete
identifies
conditions
checks
and services.
accessories
of
performing
and
daily
the
general
that
service
checks
make
only
those
and
services
area
or
specific
the
equipment
EOUIPMENT
READY/AVAILABLE
IS
-
Tray
is
missing.
Kit
is
missing
components
damaged.
or
are
part
to
be
unavailable
NOT
IF:
critical
missing
or
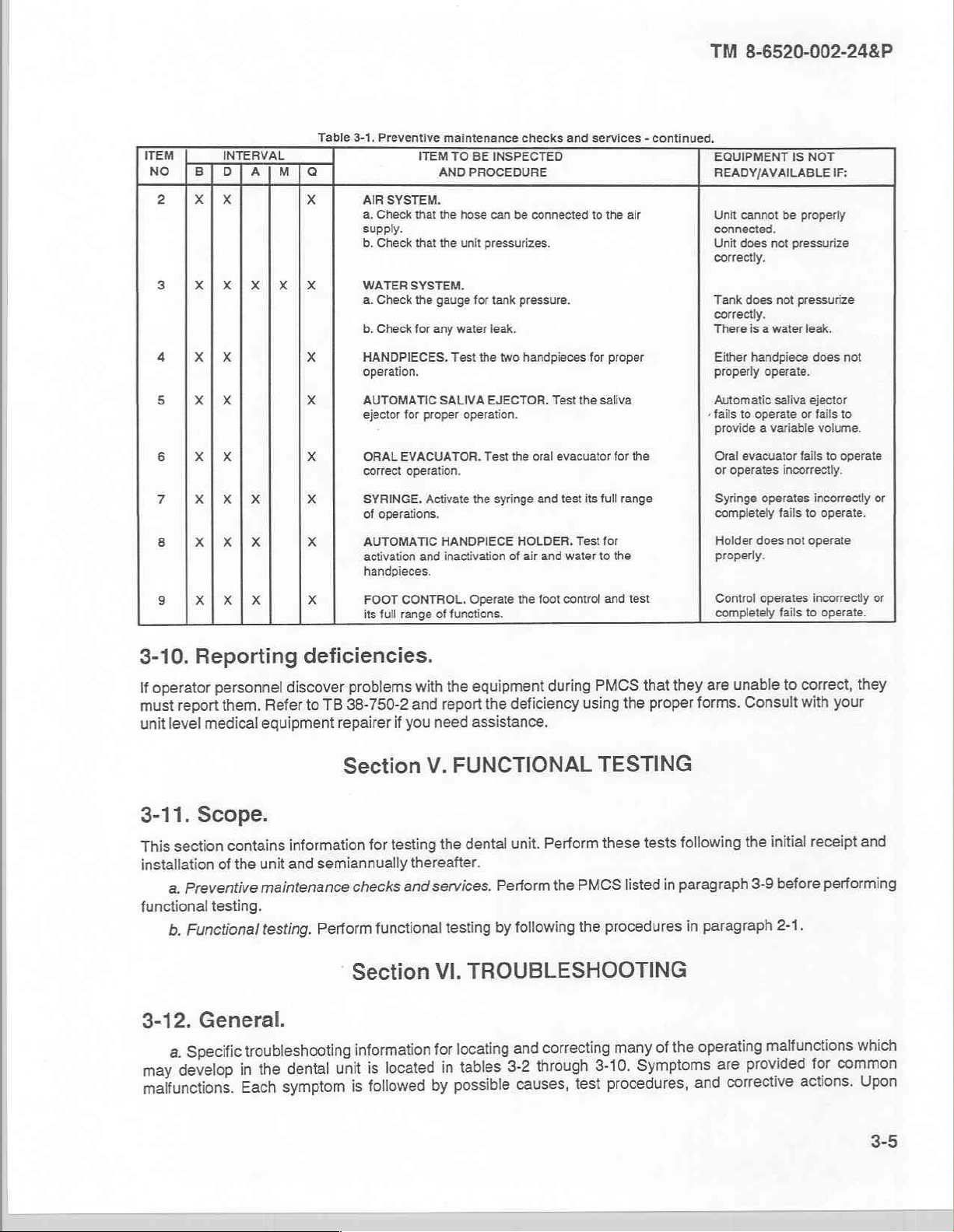
ITEM
no
2
[By]
|x|x
INTERVAL
D]A|M
Table
3-1.
Preventive
AIR
SYSTEM.
a.
Check
supply.
b.
Check
maintenance
ITEM
AND
that
the
that
the
TO
BE
INSPECTED
PROCEDURE
hose
can
be
unit
pressurizes.
checks
and
connected
services - continued.
to
the
air
TM
8-6520-002-24&P
EQUIPMENT
READY/AVAILABLE
Unit
cannot
connected.
Unit
does
correctly.
IS
NOT
IF:
be
properly
not
pressurize
4 X | X
5
X | X
6
X | X
了
X|X|X
3-10.
operator
If
report
must
unit
level
Reporting
personnel
them.
medical
Refer
equipment
deficiencies.
to
TB
problems
38-750-2
repairer
discover
WATER
a.
b.
HANDPIECES.
operation.
AUTOMATIC
ejector
ORAL
correct
SYRINGE.
of
AUTOMATIC
activation
handpieces.
its
SYSTEM.
Check
the
gauge
Check
for
any
water
Test
SALIVA
for
proper
EVACUATOR.
operation.
operations.
FOOT
Activate
and
CONTROL.
full
range
with
and
you
if
HANDPIECE
inactivation
of
functions.
the
report
need
operation.
for
tank
pressure.
leak.
the
two
handpieces
EJECTOR.
Test
the
oral
the
syringe
and
HOLDER.
of
air
and
Operate
the
foot
equipment
the
assistance.
during
deficiency
for
proper
Test
the
saliva
evacuator
test
water
control
its
full
Test
for
to
and
PMCS
using
for
range
the
the
test
that
the
Tank
‘There
+
fails
are
they
forms.
proper
does
not
correctly.
is a water
Either
handpiece
properly operate.
Automatic
to
provide a variable
Oral
evacuator
or
operates
Syringe
completely
Holder
properly.
Control
completely
unable
Consult
pressurize
leak.
does
saliva
operate
operates
does
operates
ejector
or
fails
volume.
fails
incorrectly.
incorrectly
fails
to
not
operate
incorrectly
fails
to
correct,
to
with
to
operate
operate.
operate.
your
not
to
or
or
they
3-11.
This
installation
functional
3-12.
may
maifunctions.
Scope.
section
of
Preventive
a.
testing.
Functional
b.
General.
Specific
a.
develop
contains
the
Section
information
unit
and
semiannually
maintenance
testing.
troubleshooting
the
in
Each
Perform
dental
symptom
unit
V.
testing
for
thereafter.
checks
Section
information
is
and
functional
located
is
followed
FUNCTIONAL
Perform
dental
the
services.
testing
VI.
locating
for
tables
in
possible
by
unit.
Perform
following
by
TROUBLESHOOTING
correcting
and
through
3-2
causes,
the
PMCS
the
test
TESTING
tests
these
in
listed
procedures
of
many
Symptoms
3-10.
procedures,
following
paragraph
paragraph
in
operating
the
are
corrective
and
receipt
initial
the
before
3-9
2-1.
malfunctions
provided
actions.
and
performing
which
common
for
Upon
3-5
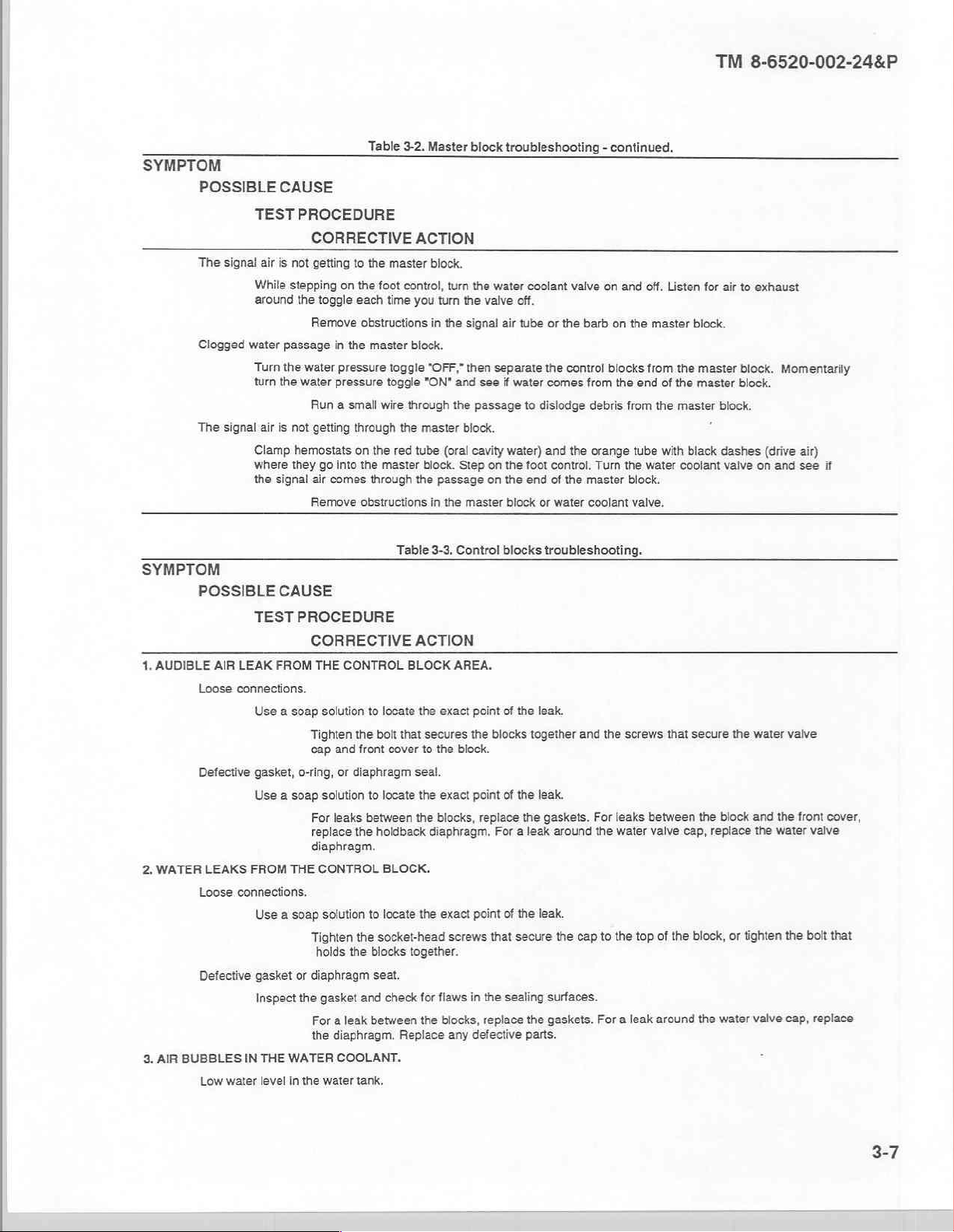
SYMPTOM
POSSIBLE
The
Clogged
The
TEST
signal
air
While
around
water
Turn
turn
signal
air
Clamp
where
the
CAUSE
PROCEDURE
CORRECTIVE
is
not
getting
to
stepping
passage
the
the
is
not
they
signal
on
the
the
toggle
each
Remove
in
the
water
pressure
water
pressure
Run a small
getting
through
hemostats
go
into
air
comes
Remove
on
Table
3-2.
Master
ACTION
the
master
block.
foot
control,
time
obstructions
master
toggle "OFF,"
toggle
wire
the
the red
the
master
through
obstructions
turn
you
tum
the
in
the
signal
block.
then
"ON"
and
through
the
master
block.
tube
(oral
block.
Step
the
passage
in
the
master
block
troubleshooting - continued.
the
water
coolant
valve
off.
air
tube
separate
see
if
water
passage
cavity
water)
on
the
on
the
block
valve
or
the
the
control
comes
to
dislodge
and
the
foot
control,
end
of
the
or
water
barb
from
debris
orange
Turn
master
coolant
on
and
off.
on
the
master
blocks
from
the
end
from
tube
the
water
block.
valve.
Listen
block.
the
master
of
the
master
the
master
with
black
coolant
TM
for
air
block.
block.
È
dashes
valve
8-6520-002-24&P
to
exhaust
block.
Momentarily
(drive
air)
on
and see
if
SYMPTOM
POSSIBLE
1,
AUDIBLE
Loose
Defective
2.
WATER
3.
AIR
LEAKS
Loose
Defective
BUBBLES
Low
CAUSE
TEST
PROCEDURE
AIR
LEAK
FROM
connections.
Use a soap
gasket,
o-ring,
Use a soap
FROM
THE
connections.
Use a soap
gasket
or
Inspect
IN
THE
WATER
water
level
in
Table
CORRECTIVE
THE
CONTROL
solution
to
locate
Tighten
the
cap
solution
For
replace
diaphragm.
CONTROL
solution
Tighten
holds
diaphragm
the
gasket
For a leak
the
the
water
bolt
and
front
cover
or
diaphragm
to
locate
leaks
between
the
holdback
BLOCK.
to
locate
the
socket-head
the
blocks
seat.
and
check
between
diaphragm.
COOLANT.
tank,
3-3.
Control
ACTION
BLOCK
AREA.
the
exact
that
secures
to
seal.
the
the
the
together.
for
the
Replace
the
the
block.
exact
blocks,
diaphragm,
exact
screws
flaws
in
blocks,
any
blocks
troubleshooting.
point
of
the leak.
blocks
together
point
of
the
leak.
replace
the
For a leak
point
that
the
replace
defective
gaskets.
around
of
the leak.
secure
sealing
surfaces.
the
gaskets.
parts.
and
the
cap
the
screws
For
leaks
the
to
between
water
valve
the
top
For a leak
that
secure
the
cap,
of
the
block,
around
the
the
water
block
and
replace
the
or
tighten
water
valve
valve
the
front
water
valve
the
bolt
cap,
replace
cover,
that
3-7
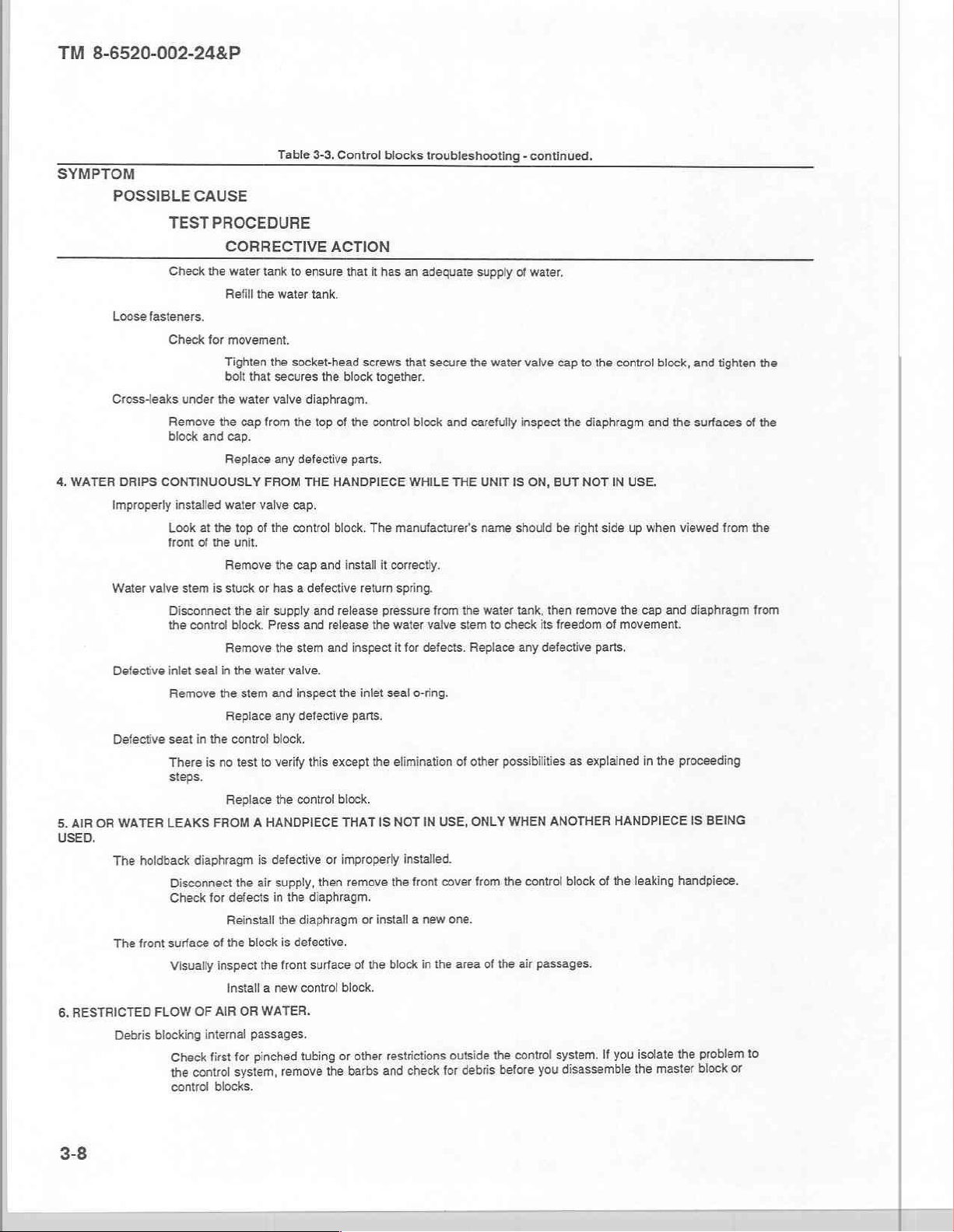
TM
8-6520-002-24&P
SYMPTOM
POSSIBLE
Loose
fasteners.
Cross-leaks
4.
WATER
DRIPS
Improperly
Water
valve
Defective
Defective
WATER
OR
AIR
5.
USED.
The
holdback
The
front
6.
RESTRICTED
FLOW
Debris
blocking
CAUSE
TESTPROCEDURE
CORRECTIVE
Check
the
water
tank
Refill
the
Check
for
movement.
Tighten
the
bolt
that
under
the
water
Remove
block
and
the
cap.
cap
from
Replace
CONTINUOUSLY
installed
Look
at
the
front
of
the
FROM
water
valve
top
of
unit.
Remove
stem
is
stuck
or
Disconnect
the
the
control
block.
air
Press
Remove
inlet
seal
in
the
water
Remove
seat
There
in
the
is
the
no
stem
Replace
control
test
to
steps.
Replace
HANDPIECE
A
FROM
LEAKS
diaphragm
Disconnect
Check
for
is
the
air
defects
Reinstall
surface
of
the
block
Visually
inspect
the
Install a new
OF
AIR
OR
WATER.
internal
passages.
pinched
for
first
Check
the
control
control
blocks.
system,
Table
3-3,
Control
ACTION
to
ensure
that
it
has
water
tank.
socket-head
secures
valve
diaphragm.
the
top
any defective
THE
screws
the
block
together.
of
the
control
parts.
HANDPIECE
cap.
the
control
block.
The
the
cap and
has a defective
supply
the
stem
install
retum
and
release
and
release
and inspect
it
pressure
the
valve.
and
inspect
the
inlet
any defective
parts.
block.
verify
this
except
the
the
control
block.
IS
THAT
defective
supply,
in
or
improperly
then
the
the
is
defective.
front
remove
remove
diaphragm.
diaphragm
surface
of
control
block.
other
or
tubing
the
barbs
or
install a new
the
and
blocks
troubleshooting - continued.
an
adequate
that
secure
block
WHILE
manufacturer's
the
and
carefully
THE
supply
water
UNIT
name
correctly.
spring.
from
the
water
valve
it
for
defects.
seal
o-ring.
elimination
IN
NOT
stem
of
USE,
water
to
Replace
other
possibilities
ONLY
installed.
the front
cover
from
one.
block
in
the
area
of
the
the
check
outside
debris
for
before
restrictions
of
water.
valve cap
inspect
IS
ON,
should
tank,
check
any defective
WHEN
the
control
air
control
to
the
the
diaphragm
BUT NOT
be
right
then
remove
its
freedom
parts.
as
explained
ANOTHER
block
passages.
system.
disassemble
you
control
block,
and
IN
USE.
side
up
when
the
cap
of
movement.
in
the
HANDPIECE
of
the
leaking
isolate
you
If
the
master
and
tighten
the
surfaces
viewed
from
and
diaphragm
proceeding
BEING
IS
handpiece.
problem
the
block
or
the
of
the
the
from
to
3-8
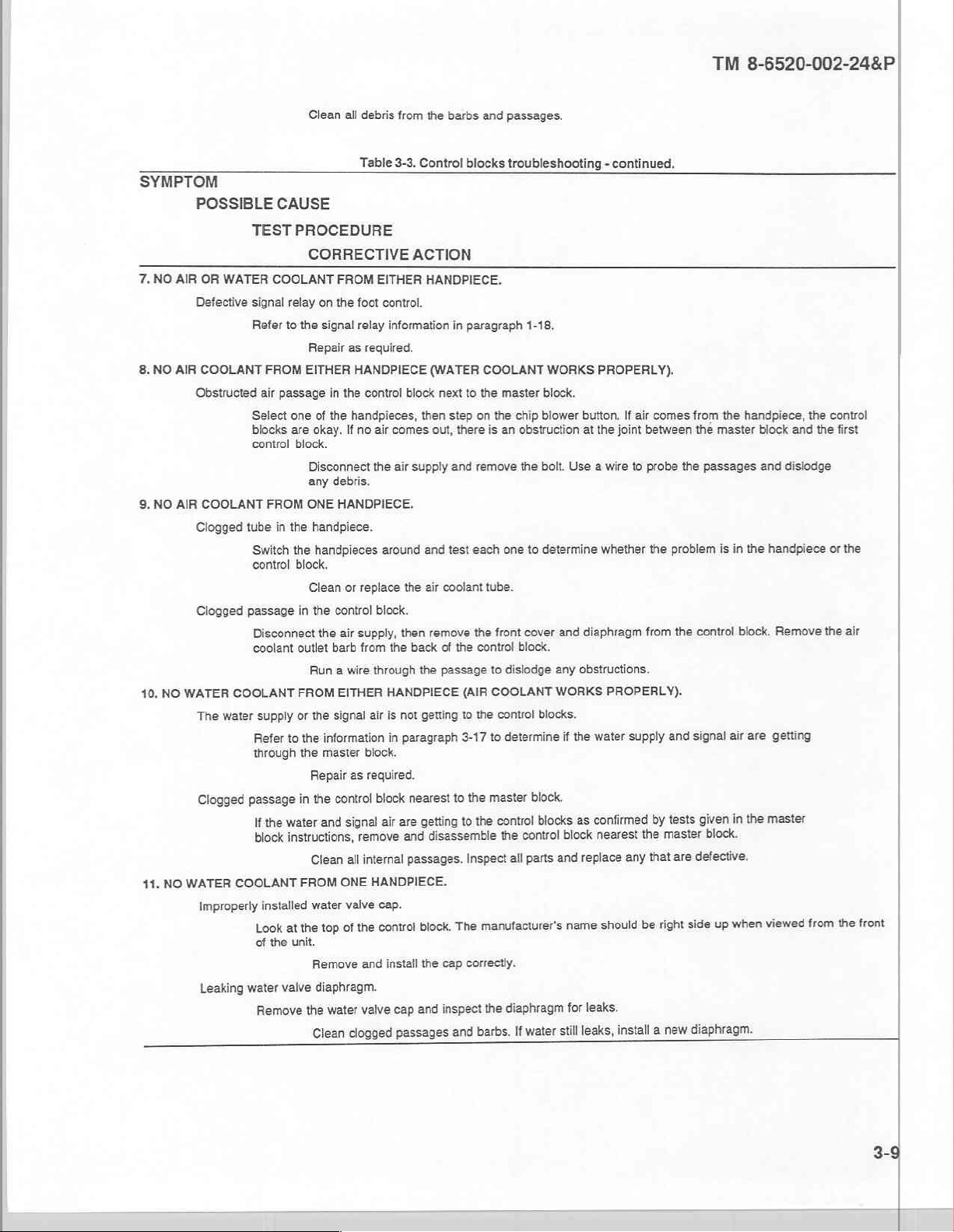
SYMPTOM
POSSIBLE
7.
NO
AIR
OR
Defective
8.
NO
AIR
COOLANT
Obstructed
9.
NO
AIR
COOLANT
Clogged
Clogged passage
10.
NO
WATER
The
Clogged
WATER
NO
41.
Improperly
Leaking
TEST
WATER
water
COOLANT
signal
Refer
FROM
air
Select
blocks
control
FROM
tube
Switch
control
Disconnect
coolant
COOLANT
supply
Refer
through
passage
the
If
block
COOLANT
installed
Look
of
the
water
Remove
Clean
all
CAUSE
PROCEDURE
CORRECTIVE
FROM
relay
on
the
to
the
signal
Repair
as
EITHER
passage
in
valve
in
the
one
of
the
okay.
handpieces,
If
are
block.
Disconnect
any
debris.
ONE
HANDPIECE.
the
handpiece.
the
handpieces
block.
Clean
or
in
the
control
the
air
outlet
barb
Run a wire
FROM
EITHER
or
the
signal
to
the
information
the
master
Repair
as
in
the
control
signal
and
water
instructions,
all
Clean
ONE
FROM
water
valve
of
top
the
at
unit.
Remove
diaphragm.
the
water
clogged
Clean
debris
from
the
Table
3-3.
Control
ACTION
EITHER
foot
relay
required.
HANDPIECE
control
no
air
the
replace
block.
supply,
from
through
air
block.
required.
block
remove
internal
HANDPIECE.
cap.
control
the
and
valve
HANDPIECE.
control.
information
(WATER
block
then step
comes
out,
air
supply
around
and
the
air
then
remove
the
back
the
HANDPIECE
is
not
getting
in
paragraph
nearest
getting
are
air
disassemble
and
passages.
block.
install
the
cap
and
passages
barbs
and
passages.
blocks
troubleshooting - continued.
in
paragraph
COOLANT
next
to
the
master
on
the
there
and
test
coolant
of
the
passage
(AIR
to
3-17
to
to
Inspect
The
cap
correctly.
inspect
and
chip
is
an
obstruction
remove
the
each
one
tube.
the front
control
block.
to
dislodge
COOLANT
the
control
to
determine
the
master
control
the
control
the
all
manufacturer's
the
diaphragm
If
barbs.
1-18.
WORKS
block.
blower
bolt.
Use a wire
to
determine
cover
and
any
WORKS
blocks.
if
block.
blocks
block
and
parts
name
for
still
water
PROPERLY).
button,
If
air
joint
to
comes
between
probe
the
the
problem
from
the
at
the
whether
diaphragm
obstructions.
PROPERLY).
the
water
supply
and
tests
confirmed
as
nearest
replace
should
the
that
any
be
by
master
are
right
leaks.
new
a
install
leaks,
TM
8-6520-002-24&P
from
the
the
control
signal
handpiece,
master
block
passages
given
block.
is
in
air
in
and
the
block.
are
the
handpiece
getting
master
defective.
viewed
when
up
side
diaphragm.
the
control
and
the
first
dislodge
or
Remove
the
from
the
air
front
the
3-9
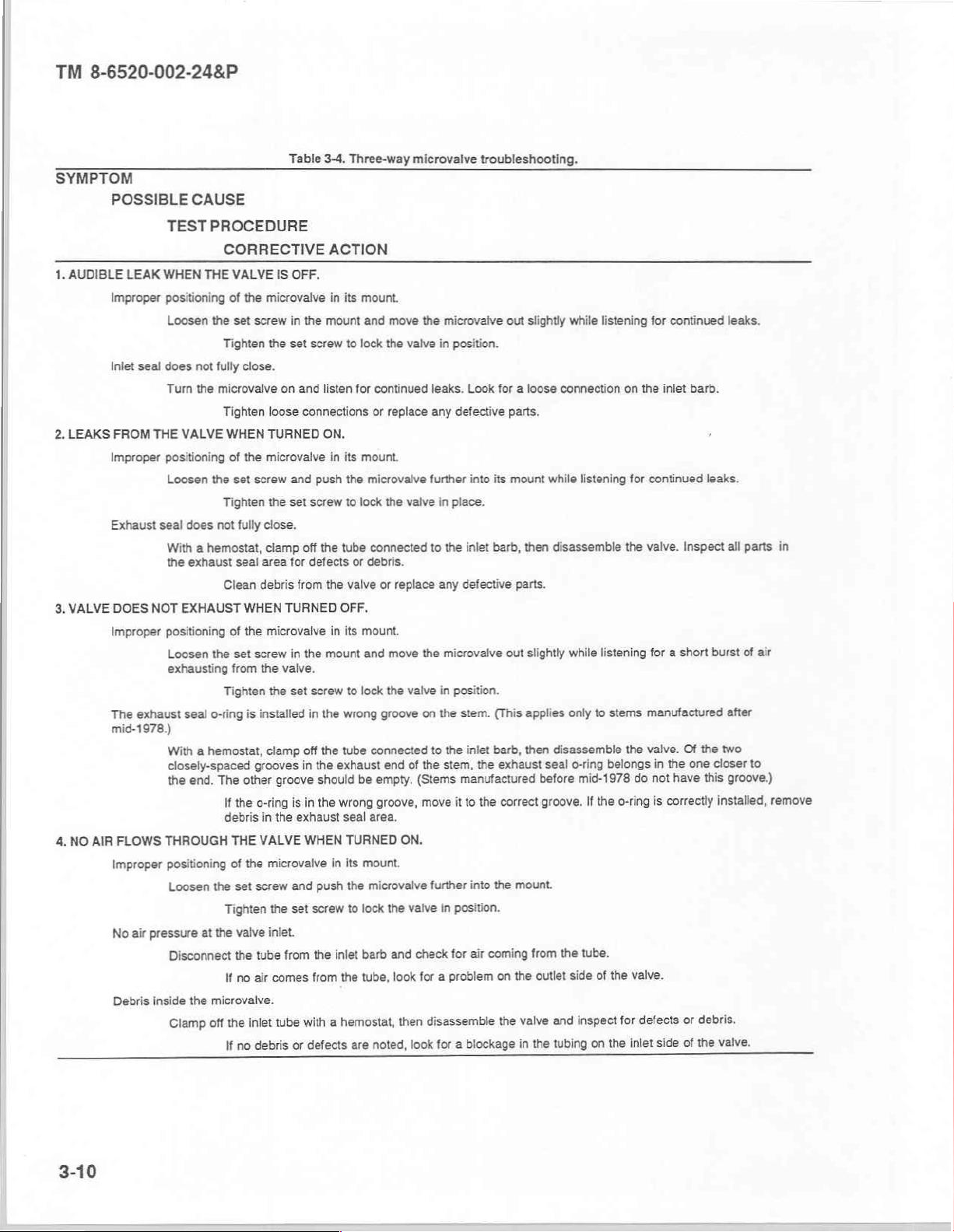
TM
8-6520-002-24&P
SYMPTOM
1,
AUDIBLE
2.
LEAKS
3.
VALVE
POSSIBLE
LEAK
Improper
Inlet
seal
FROM
Improper
Exhaust
DOES
Improper
CAUSE
TEST
PROCEDURE
WHEN
THE
positioning
Loosen
the
does
not
fully
Turn
the
microvalve
THE
VALVE
positioning
Loosen
the set
seal
does
not
With a hemostat,
the
exhaust
NOT
EXHAUST
positioning
Loosen
the
exhausting
The exhaust
seal
o-ring
mid-1978.)
With a hemostat,
closely-spaced
the
end.
The
4.
NO
AIR
FLOWS
Improper
THROUGH
positioning
Loosen
the set
No
air
Debris
pressure
inside
at
the
Disconnect
the
microvalve.
off
Clamp
Table
CORRECTIVE
VALVE
IS
OFF.
of
the
microvalve
set
screw
in
Tighten
the set
close.
on
Tighten
Tighten
Clean
Tighten
loose
WHEN
TURNED
of
the
microvalve
screw
the set
fully
close.
clamp
seal
area
debris
WHEN
of
the
microvalve
set
screw
from
the
the
is
installed
and
for
TURNED
in
valve.
set
clamp
grooves
other
groove
If
the
o-ring
is
debris
in
the
THE
VALVE
of
the
microvalve
screw
and
Tighten
the
set
vaive
inlet.
the
tube from
If
no
air
comes
tube
inlet
the
or
debris
no
If
3-4.
Three-way
ACTION
in its
the
mount
screw
to
and
listen
connections
ON,
in its
push
the
screw
to
off
the
tube
defects
or
from
the
valve
OFF.
in its
the
mount
screw
to
in
the
wrong
off
the
tube
in
the
exhaust
should
in
the
wrong
exhaust
seal
WHEN
TURNED
in its
push
the
screw
to
the
inlet
from
the
hemostat,
a
with
are
defects
microvalve
mount.
and
move
the
lock
the
valve
for
continued
or
mount.
microvalve
lock
the
connected
debris.
or
mount.
and
lock
groove
connected
end
be
empty.
groove,
area.
mount.
microvalve
lock
barb
tube,
noted,
leaks.
replace
any
further
valve
to
replace any defective
move
the
the
valve
on
to
of
the
(Stems
move
ON.
further
the
valve
and
check
look
for a problem
disassemble
then
look
troubleshooting.
microvaive
in
position.
defective
in
place.
the
microvalve
in
position.
the
the
stem,
Look
for a loose
into
its
inlet
barb,
stem.
(This
inlet
barb,
the
exhaust
out
slightly
parts,
mount
then
parts.
out
slightly
applies
then
manufactured
it
to
the
correct
into
the
mount.
in
position.
for
air
coming
from
on
the
outlet
valve
the
the
for
blockage
a
in
while
listening
connection
while
listening
disassemble
while
listening
only
to
stems
disassemble
seal
o-ring
before
groove.
the
and
tubing
belongs
mid-1978
If
the
o-ring
tube.
side
of
the
for
inspect
the
on
for
continued
on
the
inlet
barb.
,
for
continued
the
valve.
leaks.
Inspect
for a short burst
manufactured
the
valve.
Of
the
in
the
not
have
is
correctly
or
of
side
one
this
debris.
the
do
valve.
defects
inlet
leaks.
all
parts
of
air
after
two
closer
to
groove.)
installed,
valve.
in
remove
3-10

TM
8-6520-002-24&P
SYMPTOM
POSSIBLE
TEST
2.
3.
4.
Defective
AIR
SIGNAL
The
The
AUDIBLE
AIR
Improper
Signal
AUDIBLE
AIR
Improper
Signal
or
Remove
the
FROM
stem
return
Remove
valve
stem
Disassemble
LEAK
seating
Use a soap
relay
If
Inspect
LEAK
seating
Depress
relay
While
CAUSE
PROCEDURE
CORRECTIVE
improperly
diaphragm
THE
is
WHILE
inlet
the
leak
WHILE
exhaust
the
installed
the
signal
must
Replace
SIGNAL
spring
is
the
hex
If
the
stuck
in
the
Replace
THE
of
the
diaphragm.
solution
If
the
replace
seal
does
is
from
the
stem,
Replace
THE
of
the
diaphragm.
the
foot
If
the
If
the
seal
foot
control
Tighten
the
exhaust
missing.
spring
the
leak
leaking
leak
does
Table
3-6.
diaphragm.
relay
from
aligned
be
any
defective
RELAY
DOES
plug
from
the
is
missing
open
position.
signal
relay
any
defective
UNIT
IS
NOT
to
locate
is
at
the
the
diaphragm.
not
fully
close,
the
exhaust
o-rings,
UNIT
control
and seats
any
defective
IS IN
USE.
until
increases
persists,
not
fully
is
depressed,
the
barb
or
seal
area
Signal
relay
valve
ACTION
the
foot
control
passages
the
with
parts.
NOT
SHUT
end
of
the
signal
or
defective,
valve
and
inspect
parts.
IN
USE.
the
source
of
the leak.
diaphragm
holes,
the
replace
close.
the
for
line,
shut
the
for
debris
parts.
relay
is
actuated.
with
pressure
the
diaphragm.
check
for
sleeve
as
debris
or
necessary
troubleshooting - continued.
and
check
for
the
in
OFF.
relay
valve
replace
it.
all
parts
tighten
the
unit
off,
then
or
defects.
While
on
the
leaks
from
defects.
to
Replace
defects,
valve
and
for
defects,
signal
remove
listening
foot
control,
the
exhaust
stop
debris,
bodies.
verify
debris,
relay
mounting
the
to
the
tighten
holes
the leak.
any
defective
or
improper
that
the
spring
or
improper
screws.
signal
relay
leak,
depress
the
signal
in
the
If
air
comes
parts.
installation.
is
in
place.
installation.
If
leaking
from
the
foot
the
foot
control
relay
mounting
signal relay
from
the
body.
exhaust
The
holes
persists,
control.
all
the
way.
screws.
holes,
inspect
in
SYMPTOM
POSSIBLE
1.
AIR
LEAKS
Improper
CAUSE
TEST
PAST
THE
positioning
Loosen
Table
3-7.
PROCEDURE
CORRECTIVE
VALVE
WHEN
TURNED
of
the
microvalve
the set
screw
in
Tighten
the set
Chip
blower
ACTION
in
the
mount,
screw
valve
OFF.
its
mount.
and
and
lock
(two-way
move
the
microvalve
the
valve
in
microvalve)
troubleshooting.
out
slightly
position.
while
listening
for
continued
leaks.