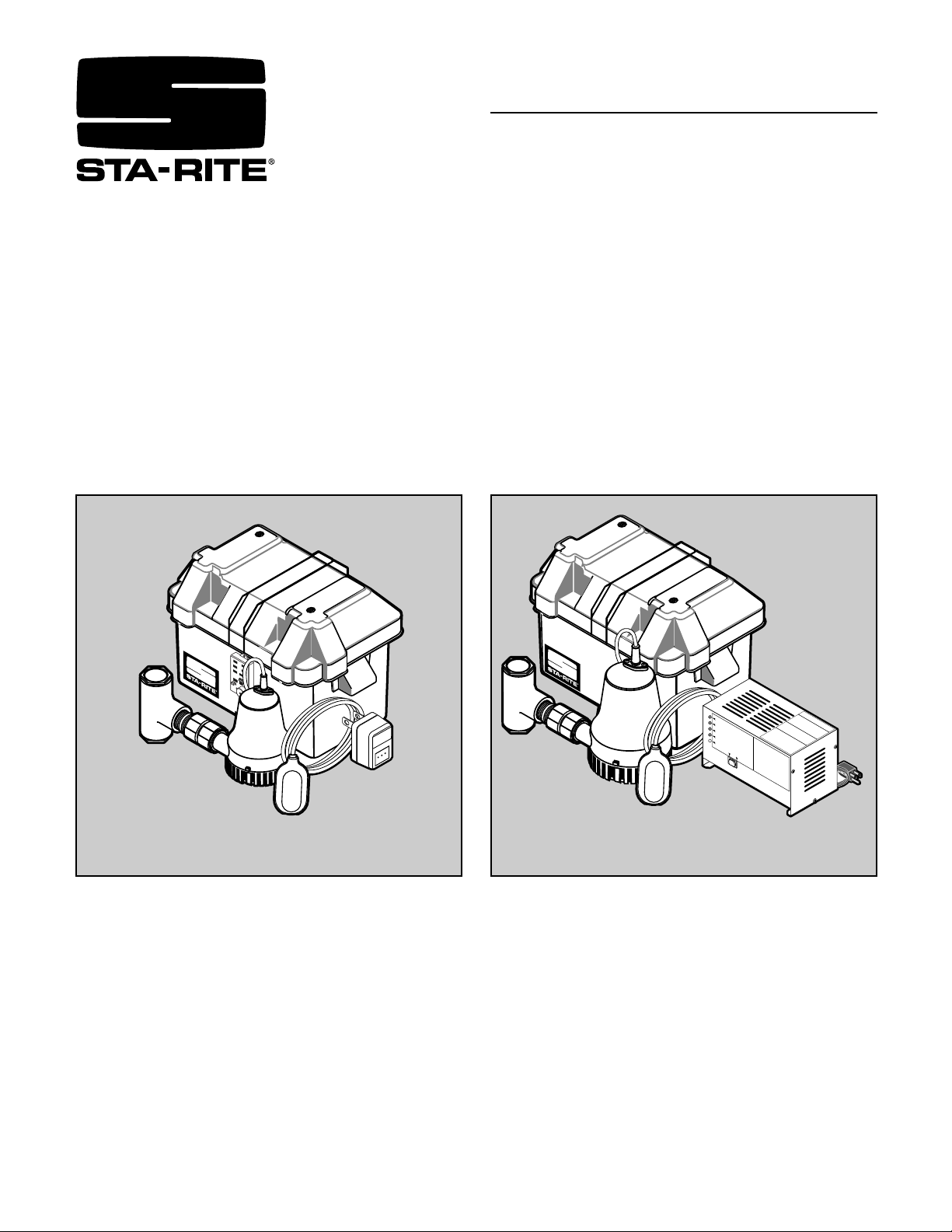
OWNER’S MANUAL
Battery Backup Systems
DB10018T-01
DB20018T
293 Wright Street, Delavan, WI 53115
© 2004, Sta-Rite Industries Printed in U.S.A. S739 (Rev. 4/16/04)
Installation/Operation/Parts
For further operating, installation,
or maintenance assistance:
Call 1-800-323-0620
ACPOWER ON
UMP RUN LARM
UD LE LARM
IR PR E R TR LD
T E BT ERY HR EMI TN R
IE CE
12 VOLT 8 AMP
OW A T
R A AM
HRG G E W
HRGED GREN
AUDB E A
DSA LE
ARM
AA M ES T
SOFT R SET
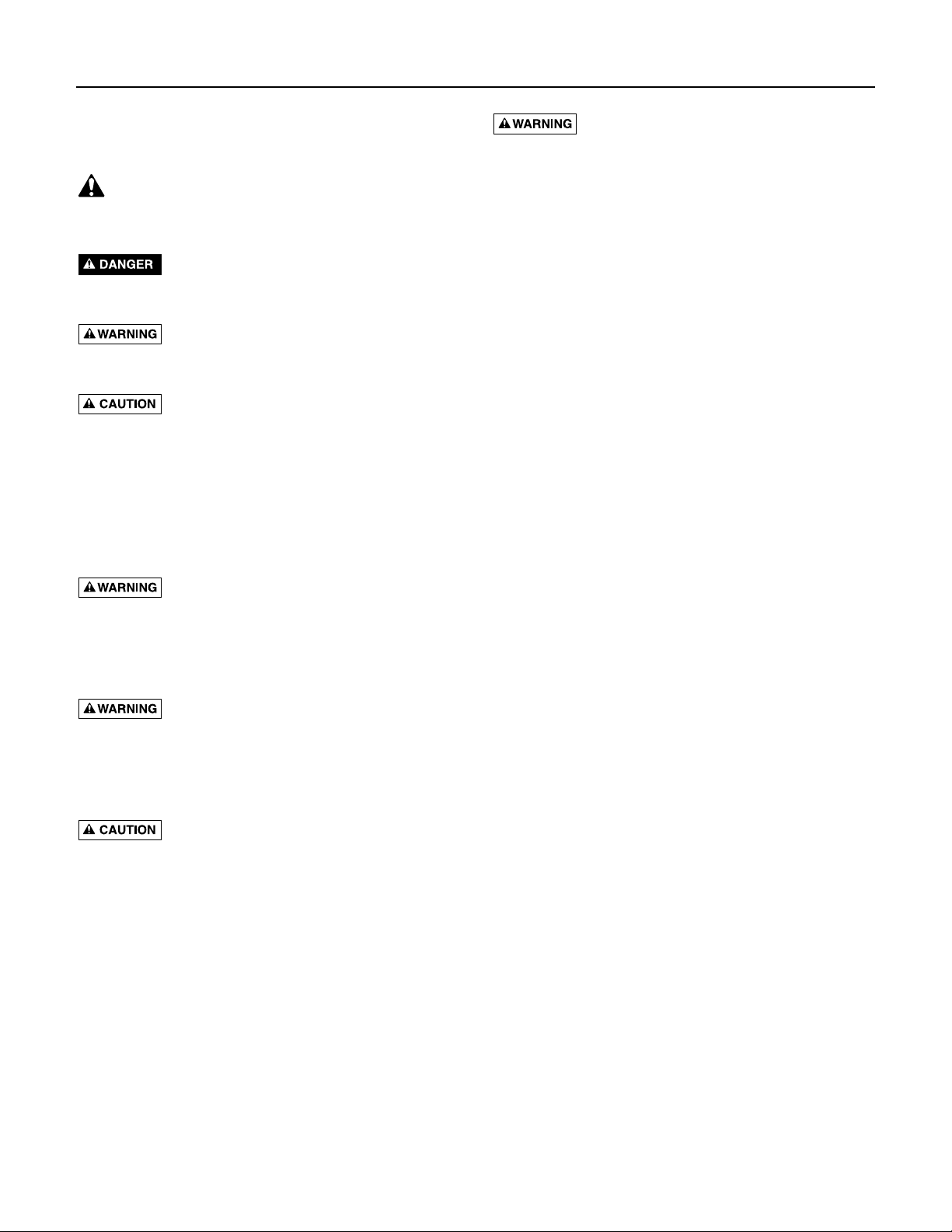
Safety 2
READ AND FOLLOW
SAFETY INSTRUCTIONS!
This is the safety alert symbol. When you see this
symbol on your pump or in this manual, look for
one of the following signal words and be alert to the
potential for personal injury!
DANGER warns about hazards that will
cause serious personal injury, death or major property
damage if ignored.
WARNING warns about hazards that can
cause serious personal injury, death or major property
damage if ignored.
CAUTION warns about hazards that will or
can cause minor personal injury or property damage if
ignored.
The word NOTICE indicates special instructions which
are important but not related to hazards.
1. To avoid risk of serious bodily injury due to electrical
shock or burns and property damage due to flooding,
read the safety instructions carefully before installing
pump.
Battery acid is corrosive. Do not spill on
skin, clothing, or battery charger. Wear eye and head
protection when working with battery. Connect and disconnect DC output terminals only after removing the
charger from the AC outlet. Never allow the DC terminals to touch each other.
Hazardous Voltage. Can cause severe or
fatal electrical shock. Do not plug in or unplug battery
charger while standing on a wet floor or in water. Be
sure one hand is free when plugging in or unplugging
charger. If basement floor is wet, disconnect power to
basement before walking on floor.
Risk of flooding. Do not run pump dry. To
do so will damage seals and can cause leaking and property damage.
2. Follow local and/or national plumbing and electrical
codes when installing the system. A ground fault circuit interrupter (GFCI) is recommended for use on
any electrical appliance submerged in water.
3. Use this system only for backup sump pump duty in
a residential application. It is not designed as a primary sump pump.
4. Do not lift pump by electrical cord.
Risk of electrical shock. Do not lift the
pump by the electrical cord; lift pump only by the discharge pipe, lifting ring or handle on the pump. Lifting
by the cord can damage the cord.
5. Pump clear water only with this pump.
6. Pump is permanently lubricated at the factory. Do
not try to lubricate it!
7. Keep battery charger and battery box off of the floor
and in a dry, cool, well ventilated area.
NOTICE: If a Carbon Monoxide (CO) sensor is
installed, it must be at least 15 feet away from battery charger in order to avoid nuisance CO alarms.
Please refer to your CO detector’s installation guidelines for more information.
8. To avoid danger of fire or explosion, keep sparks and
flame (pilot light) away from battery.
9. Maximum vertical pumping distance is 16 feet
(4.9M) for Model DB10018T-01 and 18 feet (5.5M)
for Model DB20018T.
10. Make sure sump is clear of debris. Debris can damage the pump which can result in flooding.
GENERAL INFORMATION
The battery back-up sump system is not a substitute for
your primary sump pump. It is designed to temporarily
back up your primary sump pump during a power outage or other problem which prevents normal operation
of the primary pump. Do not use this system to pump
flammable liquids or chemicals. Pump clear water only
with this pump.
Keep battery charger dry and protected from damage.
In an emergency (such as an extended power outage)
which depletes the system deep cycle battery, your automobile battery may be temporarily substituted. Be sure to
replace the system deep cycle battery as soon as possible. Use of an automobile battery instead of a 27M or
24M deep cycle battery in this system will significantly
reduce system total performance. Automobile batteries
are not designed for this type of application and will be
quickly ruined by the repeated charge/discharge cycling.
Do not use GEL-type batteries or maintenance-free
(sealed) batteries with this charger. GEL-type batteries
require a lower voltage than the charger is designed for;
they may overcharge. Maintenance-free (sealed) batteries
require a higher voltage and may never reach full charge.
NOTICE: This unit is not designed for applications involving salt water or brine! Use with salt water or brine will
void warranty.
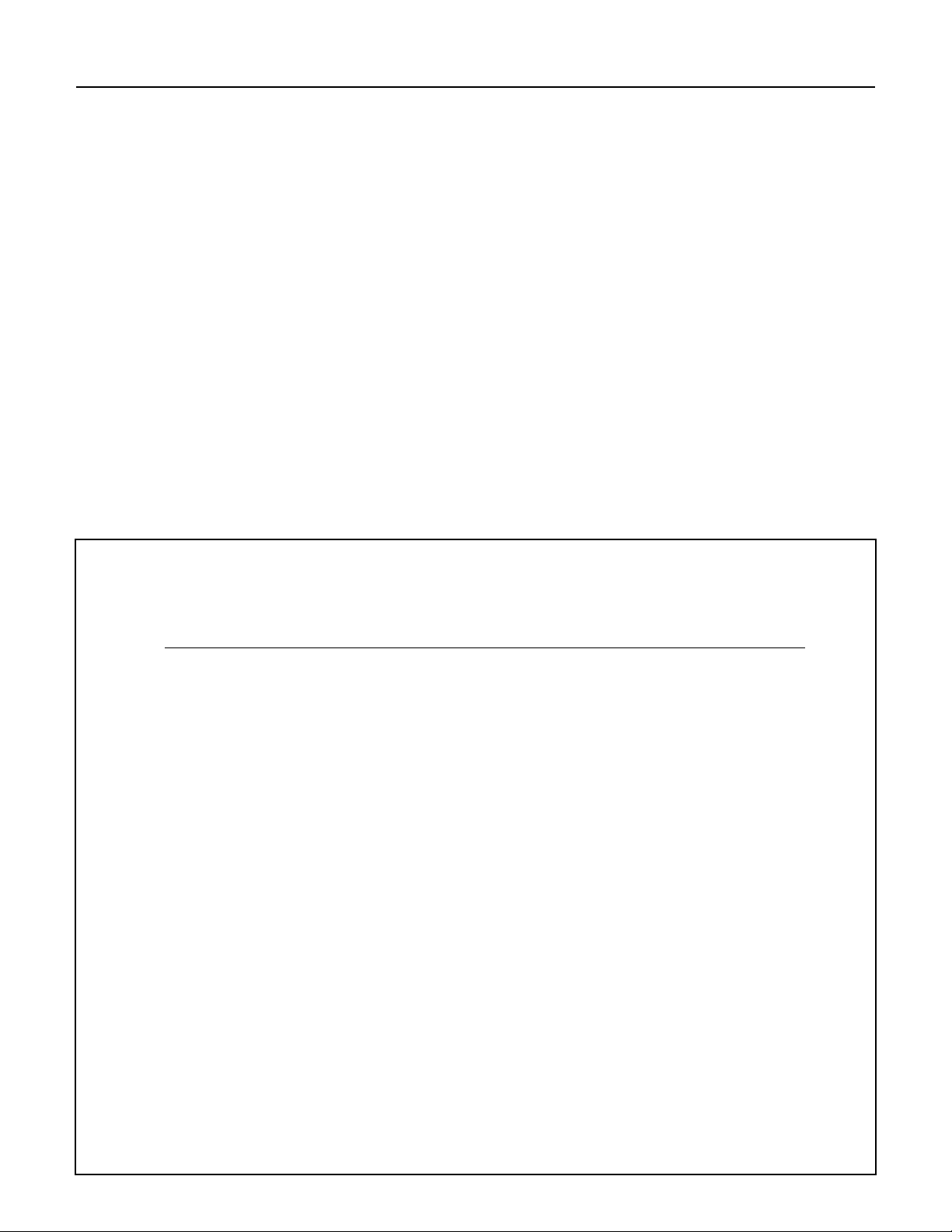
Ta b le of Contents 3
Page
General Safety .....................................................................................................2
Warranty..............................................................................................................3
Installation......................................................................................................4-12
Operation .....................................................................................................13-14
Troubleshooting .................................................................................................14
Repair Parts........................................................................................................15
LIMITED WARRANTY
Sta-Rite Industries, warrants to the original consumer of the products listed below, that they will be free from defects in material and workmanship for the Warranty Period from the date of original installation or manufacture as noted.
Product Warranty Period
Water Systems Products – jet pumps, whichever occurs first:
small centrifugal pumps, submersible pumps 1 year from date of original installation, or
and related accessories 2 years from date of manufacture
Hydro-Flow Filters 1 year from date of purchase
Signature 2000 Fibrewound Tanks 5 years from date of original installation
Pro-Source Steel Pressure Tanks 5 years from date of original installation
Pro-Source Epoxy-Line Tanks 3 years from date of original installation
Sump/Sewage/Effluent Products 1 year from date of original installation, or
2 years from date of manufacture
Our warranty will not apply to any product that has been subject to negligence, misapplication, improper installation or maintenance. In the event a three phase submersible motor is operated with single phase power through a phase converter, or
if three-leg ambient compensated, extra-quick trip overload relays of recommended size are not used, our warranty is void.
Buyer’s only remedy and Sta-Rite Industries’ only duty is to repair or replace defective products (at Sta-Rite Industries’
choice). Buyer agrees to pay all labor and shipping charges associated with this warranty and to request warranty service
through the installing dealer as soon as a problem is discovered. If warranty service is requested more than 30 days after
the Warranty Period has ended, it will not be honored.
STA-RITE INDUSTRIES SHALLNOT BE LIABLE FOR ANY CONSEQUENTIAL, INCIDENTAL, OR CONTINGENT DAMAGES
WHATSOEVER.
THE FOREGOING WARRANTIES ARE EXCLUSIVE AND IN LIEU OF ALL OTHER EXPRESS WARRANTIES. IMPLIED
WARRANTIES, INCLUDING BUT NOT LIMITED TO THE IMPLIED WARRANTIES OF MERCHANTABILITYAND FITNESS
FOR A PARTICULAR PURPOSE, SHALL NOT EXTEND BEYOND THE WARRANTY PERIOD PROVIDED HEREIN.
Certain states do not permit the exclusion or limitation of incidental or consequential damages or the placing of limitations
on the duration of an implied warranty, therefore, the limitations or exclusions herein may not apply. This warranty sets forth
specific legal rights and obligations, however, additional rights may exist, which may vary from state to state.
Supersedes all previous publications.
Sta-Rite Industries, 293 Wright St., Delavan, WI 53115
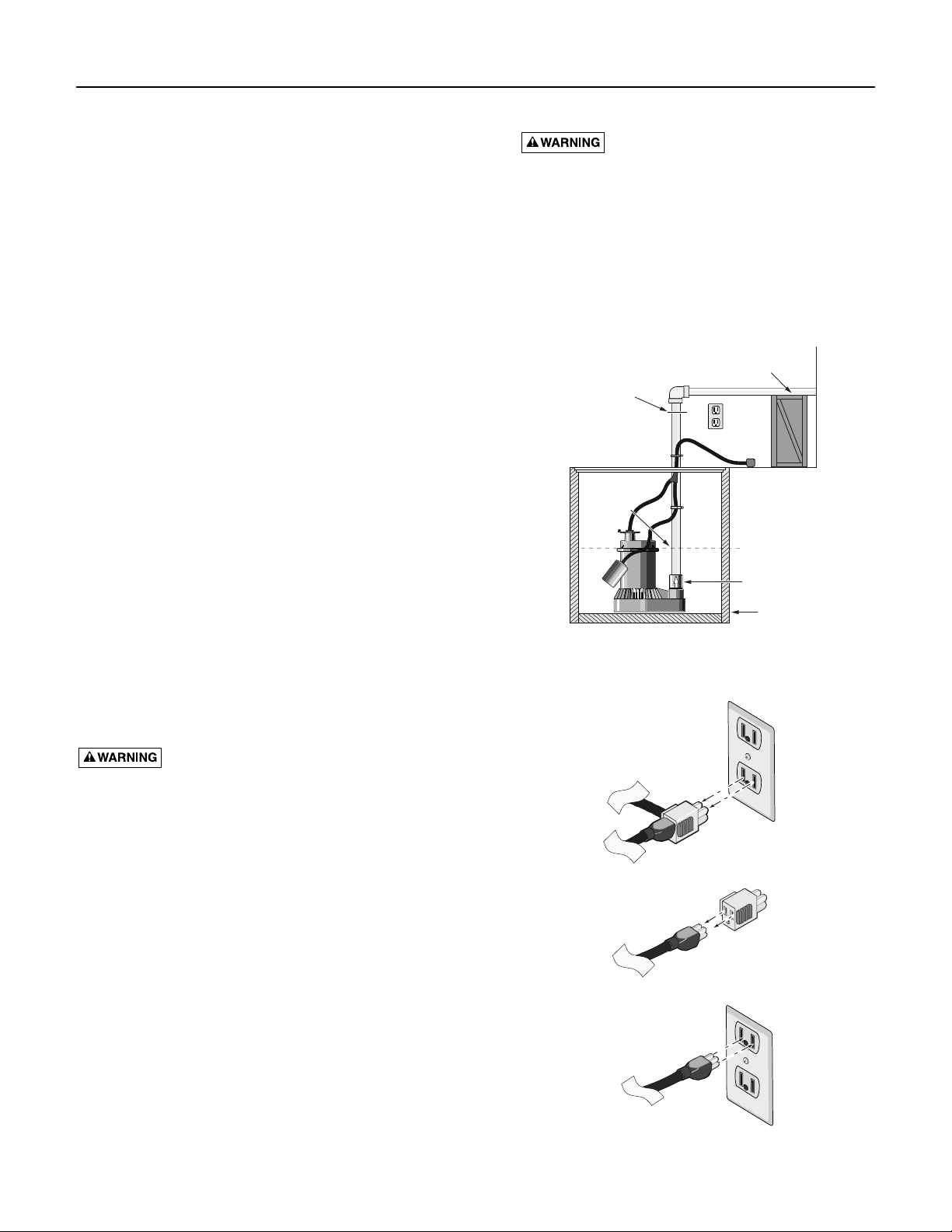
Installation 4
BATTERY BACKUP SYSTEM
INSTALLATION AND OPERATION
NOTICE:
• Install this system during a time when the primary
pump will not be needed. Gather all supplies before
starting. Read all warnings and installation steps
before you start.
• Be prepared for water to leak from the coupling or
piping when disassembling or cutting the discharge
pipe. Protect system components, tools and supplies
from getting wet. Dry any work areas that get wet.
BASIC TOOLS AND
MATERIALS NEEDED
Channel locks or large pliers
Tape measure
Socket wrench or 5/16” Nut driver
Side cutters
Hacksaw (to cut PVC pipe)
Medium size pliers
Pencil
Teflon tape
PVC glue (solvent weld)
PVC pipe cleaner
Cloth towel
Size 24M Marine Deep Cycle Battery
or a
Size 27M Marine Deep Cycle Battery
Required Battery Capacity:
DB10018T-01 – 100 ampere-hour maximum.
DB20018T – 130 ampere-hour maximum.
Personal injury and flood hazard. Do not
turn the pump on until all the fittings are glued and the
glue has dried. Loose fittings can explode off of pipes
and cause personal injury and flooding.
Remove Primary Pump From Sump Pit:
1. Locate the “on” water level of the primary sump
pump. Mark this location on the discharge pipe with
a pencil. See Figure 1.
2. Drain the sump pit. The water level must be pumped
down as low as possible before going on to the next
step. To drain the sump pit follow either step “2A” or
“2B”(below).
2A. Raise the float on the float switch until the
pump turns on. Use a wooden broom handle or
a stick to do this.
2B. If the sump pump has a piggy-back type power
cord, remove the float switch power cord plug
from the outlet and plug the pump power cord
plug directly into the outlet. See Figure 2.
Electrical shock hazard. Shock can burn
or kill. Do not use metal or any other electrical conducting material to raise the float. Do not make contact with the water in the sump pit. Failure to follow
this warning can result in personal injury or death.
3. Drain the sump.
NOTICE: Do not let the pump run dry. This will
damage the pump.
4. Unplug the pump.
Figure 1 – Mark and cut pipe as shown
Figure 2 - To bypass the float switch
Support the
Remove the
hose coupling
or mark the
1st cut here.
Mark pipe with
pencil here
(2nd cut).
Pipe before
cutting.
'Turn on'
water level of
Primary Pump
Check
Valve
Sump Pit
1.
Unplug the "Piggy-back"
float switch cord plug and
the pump power cord plug
from the grounded
electrical outlet.
2.
Separate the float switch cord plug
from the sump pump cord plug.
3.
Plug the pump power cord plug
directly into the outlet.
Grounded
Electrical
Outlet
4166 0402
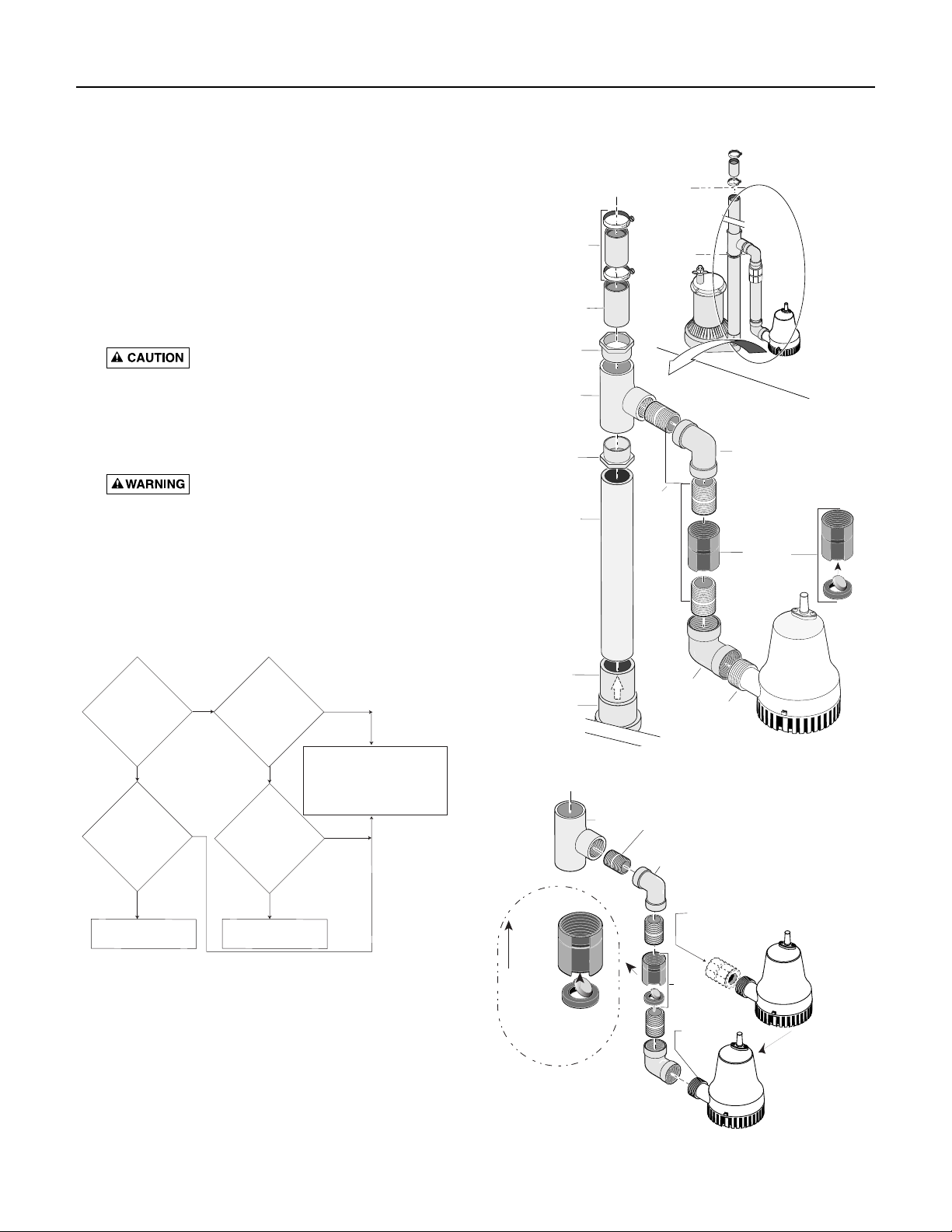
Installation 5
5. To separate the primary pump from the discharge pipe:
5A. For applications with hose couplings: remove
the coupling clamps with a nut driver.
5B. For applications without rubber couplings: cut
the PVC discharge pipe with a hacksaw above
the basement floor, at a comfortable level. New
rubber couplings are included for reassembly.
See Figure 1 on Page 4.
NOTICE: The discharge pipe is filled with water.
Drain the water from the discharge pipe assembly.
Keep the work area dry.
Risk of pinching hands or fingers. To
avoid a hand injury from a collapse of plumbing,
support the pipe above the separation before cutting
or disassembly. See Figure 1.
6. Lift the primary pump and discharge pipe assembly
out of the sump.
Risk of electrical shock. Do not lift the
pump by the electrical cord; lift pump only by the
lifting ring, discharge pipe, or handle on the pump.
Lifting by the cord can damage the cord.
INSTALL BACKUP PUMP
There are two ways to install the Battery Back-up Pump.
Method A and Method B. See Figure 3 to determine
which method to use. Both methods are acceptable.
Not to Scale
Switches and
Wiring omitted
for clarity
Hose Coupling
with Clamps
Cut-Off piece of
discharge pipe.
1-1/2"x1-1/4"
Reducer bushing
Tee
1-1/2"x 1-1/2"
slip x 1-1/4" FNPT
1-1/2"x1-1/4"
Reducer
bushing
Short Length
of Discharge Pipe
(may vary)
Primary Sump
Pump Check Valve
to prevent
recirculation
into the sump.
Backup Pump Installation
(Method A)
First Cut:
Second Cut:
at Marked
Water Line
Close
Pipe
Nipple
(1-1/4"
x 1-1/4")
(1 Nipple
is included
with the
back-up
pump
package)
1-1/4" Elbow
Check Valve
Assembly
Sump Pit
Diameter
at base ≥ 18"?
No No
Sump Pit
Diameter
at base ≥ 13.5"?
BBU System may still
Yes
Yes
be installed but the
installation may need
to be changed.
Sump Pit Depth
≥ 18"?
Yes
Method A
Sump Pit Depth
≥ 22"?
No
Method B
Yes
No
Figure 3 - Choose an installation method
Method A
Method A suggests installing both of the pumps on the
floor of the sump pit. See Figure 4. The minimum required
sump basin diameter, at the bottom of the pit and the recommended depth of the sump basin is 18”.
Some additional materials you will need are 2 1-1/4” 90°
elbows and 2 1-1/4” close pipe nipples.
1-1/4"
Elbow
Primary Pump
Discharge Port
Back-up Pump
Discharge Port
Figure 4 - Method A installation diagram
Close
Pipe
Nipple
Elbow
Check
Valve
Assembly
Battery Back-up Pump comes
preassembled with the check
valve assembly installed on the
discharge.
Remove this check
valve assembly.
Back-up Pump
Discharge
Water
Flow
through
valve
(The valve
flap opens
away from the
pump outlet)
Tee
Figure 5 - Remove the pre-assembled check valve
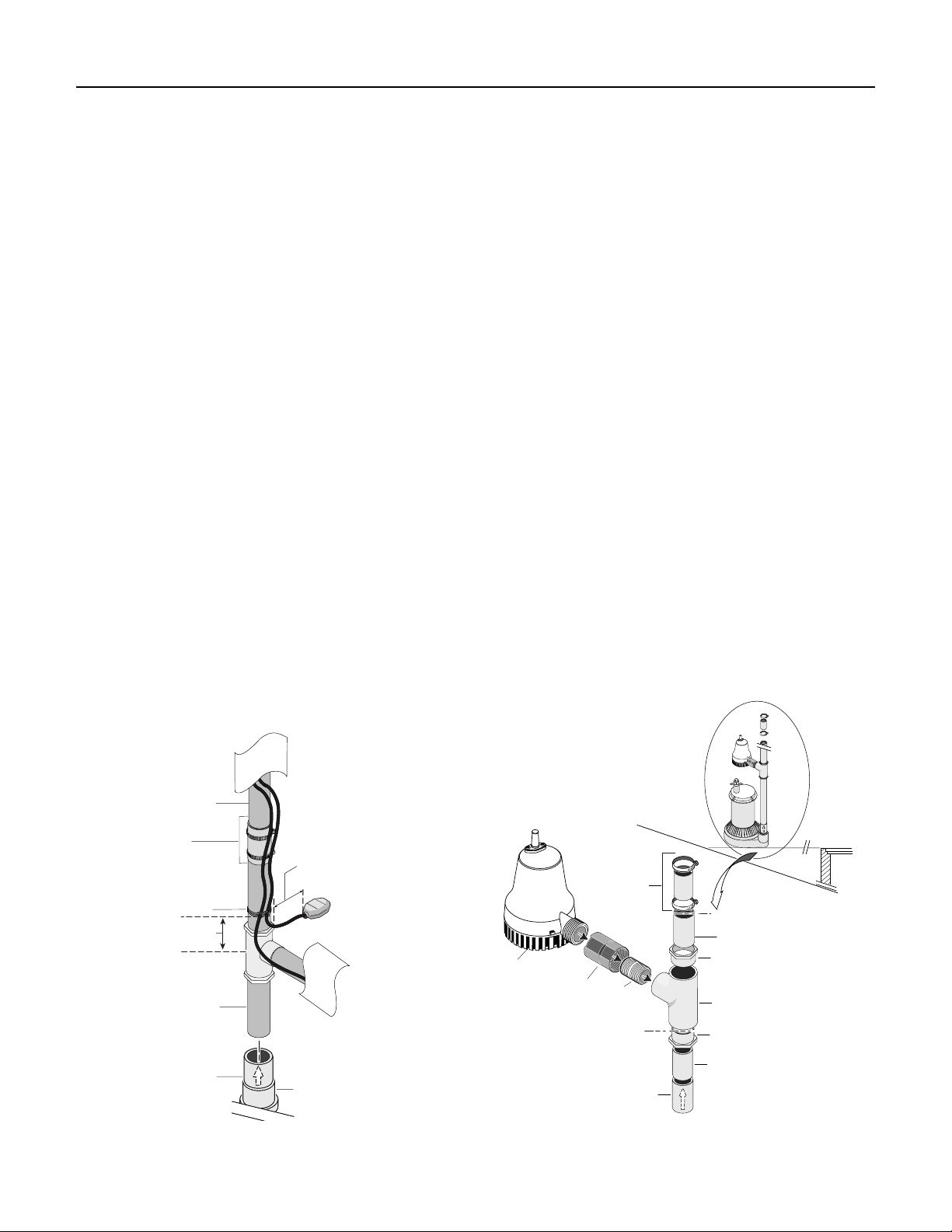
Installation 6
1. Make the second cut in the discharge pipe at the
pencil mark as shown in Figure 1 on page 4, and in
Figure 4, on Page 5. Clean the pipe ends with a
cloth towel and set the cut-off piece of discharge
pipe aside.
2. Remove the check valve assembly (Key No. 4 on
Page 15) from the battery back-up pump (Key No. 5)
discharge and set it aside. See Figure 5. The check
valve assembly will be used later, during assembly.
3. Thread a 90° elbow (purchased locally) onto the discharge of the back-up pump.
4. Wrap the threads of all 3 of the close pipe nipples
(Key No. 3) with 2 turns of Teflon™ tape and thread
one of them into the elbow. Set the other 2 aside.
5. Thread the check valve assembly, removed back in
step 2, onto the close pipe nipple.
NOTICE: Make sure the check valve is installed in the
correct direction. See the inset drawing in Figure 5.
6. Thread a close pipe nipple into the other end of the
check valve.
7 Thread the second 90° elbow onto the pipe nipple.
8. Thread the last pipe nipple into the elbow.
9. Thread the tee onto the pipe nipple and set this
assembly aside.
10. Install a short length of pipe into the top of the check
valve in the primary pump discharge. See Figure 6.
NOTICE: There must be a check valve installed in
the Primary Sump Pump discharge pipe between the
tee and the Primary Sump Pump. This will prevent
recirculation into the Primary Pump when the
Backup Sump Pump comes on.
11. Slip a reducer bushing (Key No. 2A) onto the end of
the pipe coming from the primary pump discharge.
Do not glue this connection yet.
NOTICE: If your discharge pipe diameter is 1-1/4”,
you will need to glue the reducer bushings into the
tee first and then slip the cut off piece of discharge
pipe into the bushing.
12. Slip the tee and the back-up pump subassembly onto
the reducer bushing.
13. Glue the cut off piece of pipe into the top of the
reducer bushing in the top of the tee.
14. Mount the float switch assembly (Key No. 7) loosely
to the discharge pipe with the cable ties (Key Nos.
7A & 7B). See Figure 6. Approximately 2.5” (63.5
mm) of cord length should be left between the float
and the clamp. Do not tighten the cable ties.
Adjustments may be needed later.
15. Skip to the section “Cut the Discharge Pipe”, Page 7.
Method B
Method B suggests installing the back-up pump above
the primary sump pump. See Figure 7. The minimum
required sump basin diameter for this type of installation
is 13.5” at the bottom of the pit, and the minimum recommended depth of the basin is 22”.
1. Make a second cut in the discharge pipe at the pencil
mark made in step 1, on Page 4, and set the cut-off
piece of discharge pipe aside. See Figures 1 and 7.
TM
E.I. DuPont de Nemours and Company Corporation.
Backup Pump Installation
(Method B)
Discharge
Pipe
Hose
Coupling
and Clamps
Cable Ties
2" Minimum
Tee
Short length
of discharge
Pipe (length
may vary).
Check valve
Float Switch
Tether Length
2.5" (63.5 mm)
To the
back-up
pump
discharge
pipe.
Primary Sump
Pump Discharge
Pipe
Figure 6 - Back-up pump float switch tether length and
discharge pipe
Not to Scale
Switches and
Wiring omitted
for clarity
Hose Coupling
with Clamps
First Cut:
Cut-Off piece of
discharge pipe.
Backup
Sump
Pump
Check Valve
Assembly
(Included)
Primary Sump Pump
Check Valve to Prevent
Recirculation into Sump
Close
Pipe
Nipple
Second Cut:
at Marked
Water Line
1-1/2"x1-1/4"
Reducer
Bushing
Tee
1-1/2"x1-1/4"
Reducer
Bushing
Primary Pump
Discharge Pipe
Figure 7 – Method B installation diagram
Basement
Floor
Sump
Pit
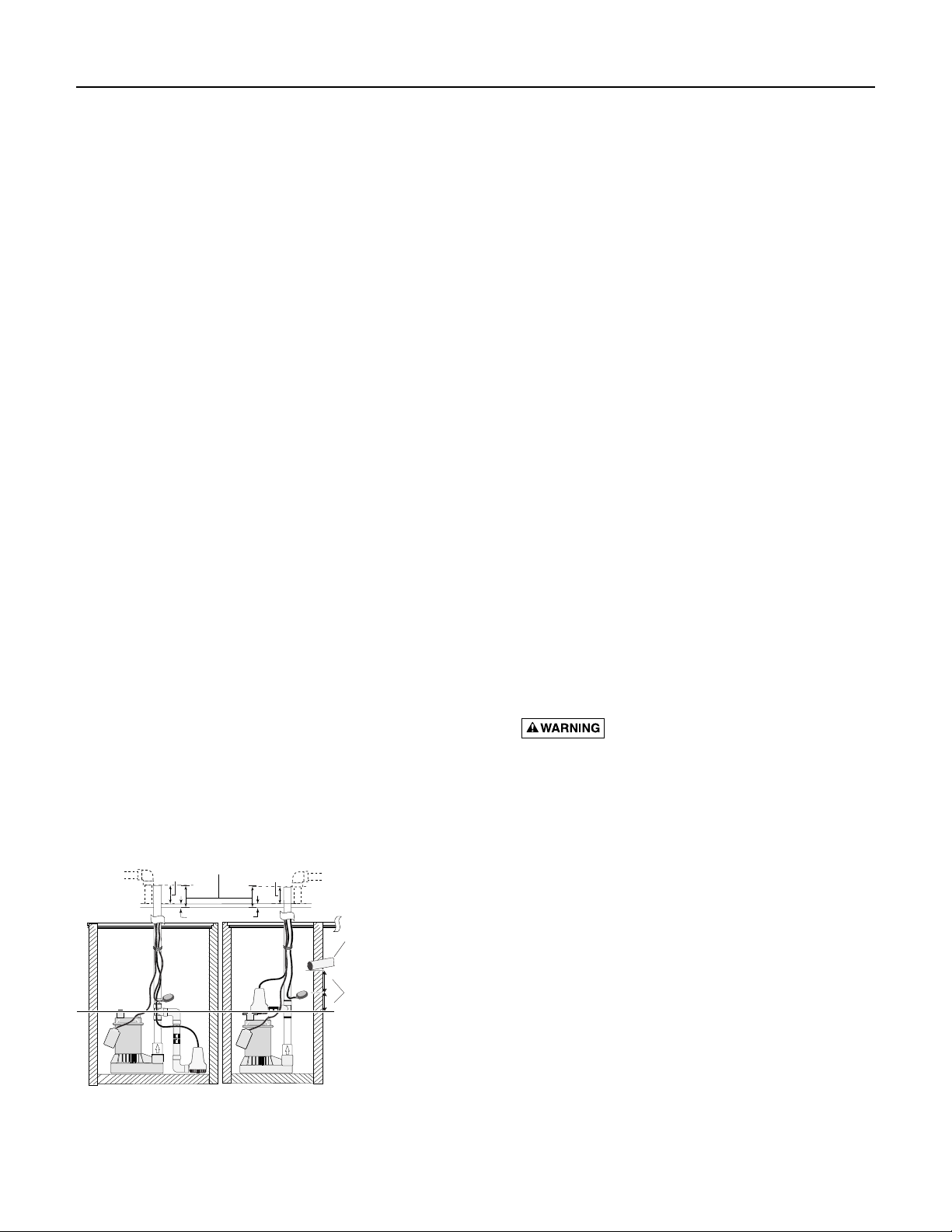
Installation 7
2. Wrap the threads of the close nipple (Key No. 3 on
Page 12) counterclockwise with 2 turns of Teflon
TM
tape and set aside.
NOTICE: There must be a check valve installed in
the Primary Sump Pump discharge pipe between the
tee and the Primary Sump Pump. This will prevent
recirculation into the Primary Pump when the
Backup Sump Pump comes on.
3. The backup pump (Key No. 6) and check valve
assembly (Key Nos. 4 and 5) come preassembled.
Thread the close pipe nipple into the check valve.
4. To thread the tee (Key No. 2B - also included reducer bushings) into the close nipple:
Hold the check valve assembly with the channel
locks, insert the screwdriver into the tee for leverage,
and tighten the tee with the screwdriver. Finish with
the tee in a straight up and down (vertical) position.
5. Clean the pipe ends with the cloth towel.
6. Glue the cut-off piece of discharge pipe into the top
of the tee.
NOTICE: If your pipe is 1-1/4”, you will need to glue
the reducer bushings into the tee and glue the pipe
into the bushing. Place the assembly onto the primary discharge pipe. Do not glue the tee onto the primary pump discharge pipe.
7. Mount the back-up pump float switch assembly (Key
No. 7) loosely to the discharge pipe with the cable ties
(Key Nos. 7A & 7B). See Figure 6, on Page 6.
Approximately 2.5” (63.5 mm) of cord length should
be left between the float and the clamp. Do not tighten the cable ties. Adjustments may be needed later.
Cut the Discharge Pipe:
1. Put the double pump assembly into the sump pit.
NOTICE: The discharge pipe now overlaps the dis-
charge pipe that leads outside.
2. Mark the discharge pipe where it should be cut. Be
sure to leave a 1/4” air gap between the ends of the
pipes. This gap will absorb the noise from vibration
and allow for flexibility.
3. Make the third cut. See Figure 8.
TRIAL ASSEMBLY OF DOUBLE PUMP
ASSEMBLY IN THE SUMP PIT:
1. Connect the discharge pipe to the exterior discharge
pipe with the rubber coupling and clamp kit (Key
No. 1). Do not tighten the clamps until all the final
adjustments are complete.
2. Make the final adjustments. Make sure the pumps
and the switches do not interfere with each other.
Make sure there is plenty of room for the float
switches to either swing or to move up and down
from their “off” to their “on” positions.
Mark and Glue Assembly:
1. Mark the pipe and the fittings at all the connections
with a pencil. These marks will be used as a reassembly guide while gluing to be sure everything is still in
the right place and nothing has moved.
2. Loosen the rubber coupling and clamp connection.
3. Carefully pull the double pump assembly back out of
the pit.
4. Take the tee assembly off of the primary discharge
pipe. Do Not unscrew any of the TeflonTMtaped pipe
nipple connections.
5. Clean all the PVC pipe ends with the PVC cleaner.
Hazardous fumes. Follow the cement
and cleaner manufacturers instructions. Use the PVC
cement in a well ventilated area away from fire or
flames.
6. Glue the PVC fittings where indicated by the pencil
marks. Wait 10 minutes for the glue to cure.
Final Assembly:
1. Put the double pump assembly back into the pit.
2. Install and tighten the rubber coupling and clamp kit.
3. Make the final float switch adjustments and tighten
the cable ties.
Figure 8 – Make the third cut to remove the excess
discharge pipe
Method A Method B
Exterior
discharge
pipe
Make the Third Cut
(the overlap plus
the 1/4" air gap).
overlap
1/4" air gap
overlap
Exterior
discharge
pipe
Sump basin
inlet pipe (from
drain tiles to
sump basin).
2"
Recommended Minimum
2"
Previously marked
"on" water level
of Primary Sump Pump.
(See Figure 1, Page 4)
Note: Always install the back-up sump pump as close
to the bottom of the sump pit as possible.
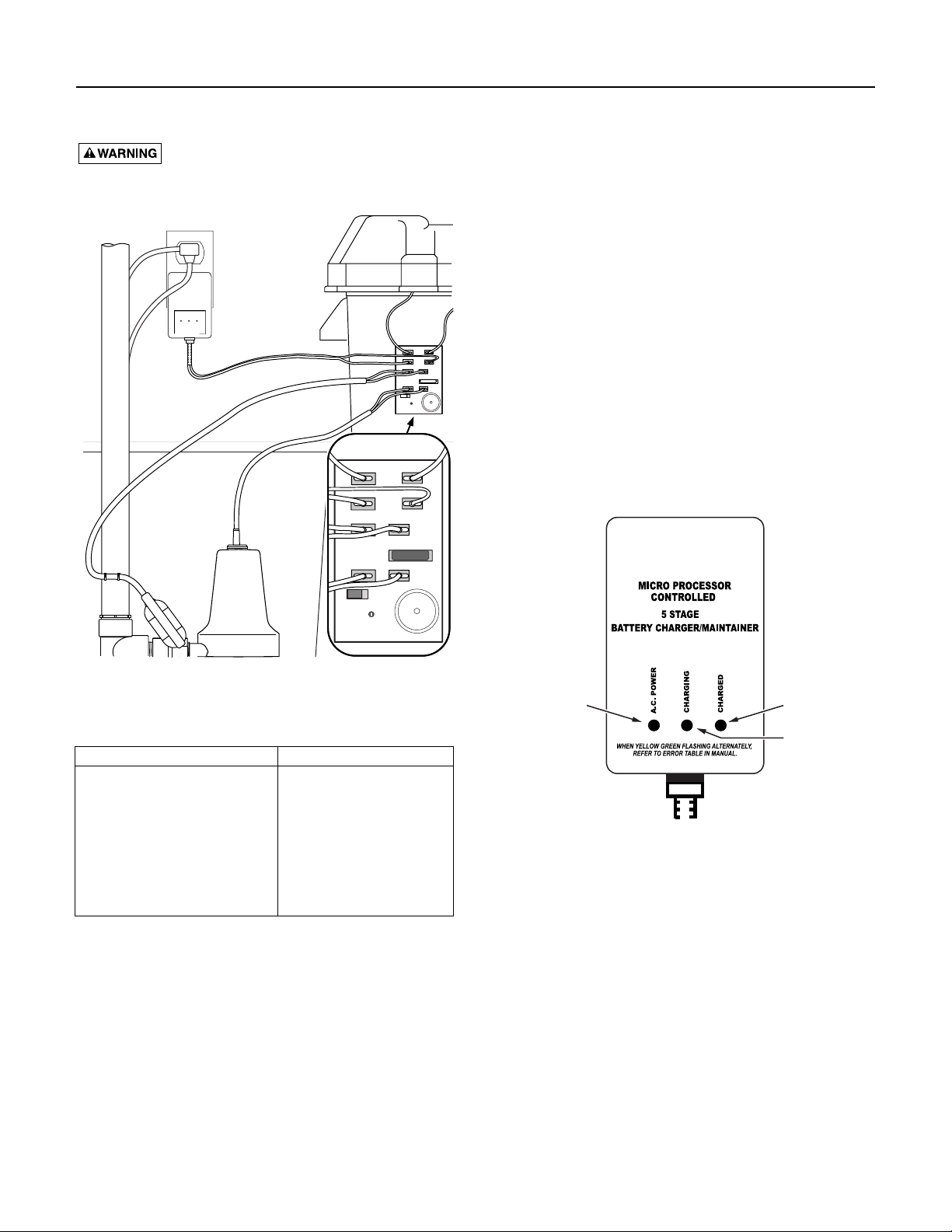
Installation 8
ELECTRICAL CONNECTIONS
Hazardous voltage. Can cause serious or
fatal electrical shock. Review safety instructions before
operating charger. Do not modify cord or plug.
CHARGER/BATTERY INSTALLATION
NOTICE: An alarm, located in the junction box, auto-
matically sounds when the system runs if the alarm is in
the “Enable” position. The alarm is silenced when the
alarm switch is in the “Disable” position.
Model Number DB10018T-01:
1. Apply two pieces of two-sided tape (provided, Key
No. 9) to the back of the junction box. Press the
junction box onto the battery box as illustrated in
Figure 9 and on Page 15 (Exploded View).
2. Connect the charger as shown in Table I and
Figure 9.
3. Plug the charger into a 115-120 Volt AC outlet delivering at least 15 amps. Do not use a switch con-
trolled outlet. Mark circuit in main power panel
“Backup sump pump power supply; do not turn off”.
4. With the charger properly connected and plugged in,
the panel on the front of the charger will show one
of the conditions illustrated in Figure 10.
Red LED - AC power is present
Yellow LED - Prequalification test stage is complete and testing
or charging in process
Green/Occasional Yellow - Charger turns on intermittently to
maintain proper charge
Green LED - Charging complete
Green/Yellow LEDs Alternately Flashing - System is in Error Mode
(see Table II, Page 9)
NOTICE: For more detailed information, see “Charger Operation” on
Page 13.
Figure 9 – Wiring Connections DB10018T-01
Connect the To the Junction Box’s
Positive (+) lead from the battery Positive battery connection
Negative (–) lead from the battery Negative battery connection
Positive lead from the charger Positive charger connection
Negative lead from the charger Negative charger connection
Backup sump pump Float switch
float switch (2 wires) connection (2 wires)
Positive lead from the pump Positive pump connection
Negative lead from the pump Negative pump connection
TABLE I - DB10018T-01 Wiring Connections
Figure 10 – DB10018T-01 LED Panel
4 STAG EAD-ACID
BATTE CHARGER
BLA K ERMNAL EGA IVE )
RED ERM NAL P S T VE ( )
AUT
OMPLTE
HARGE
ATTERY CONNECTION
+
–
CHARGER CONNECTO
+
–
FLOA
T SWITCH CONNECTON
E WTH SAME 25 AMP
36V TYPE AND RATNG ON Y
PUMP FUSE &
CONNECTION
–
DSABLE ENABLE
AUDIBLE ALARM
DSABLE WHEN L T
BATTERY CONNECTION
+
CHARGER CONNECTION
+
FLOAT SWITCH CONNECTION
REPLACE FUSE WITH SAME 20 AMP
36V TYPE AND RATING ONLY
PUMP FUSE &
CONNECTION
+
–
–
20
–
DISABLE ENABLE
AUDIBLE ALARM
DISABLE WHEN LIT
Red
Green
Yellow
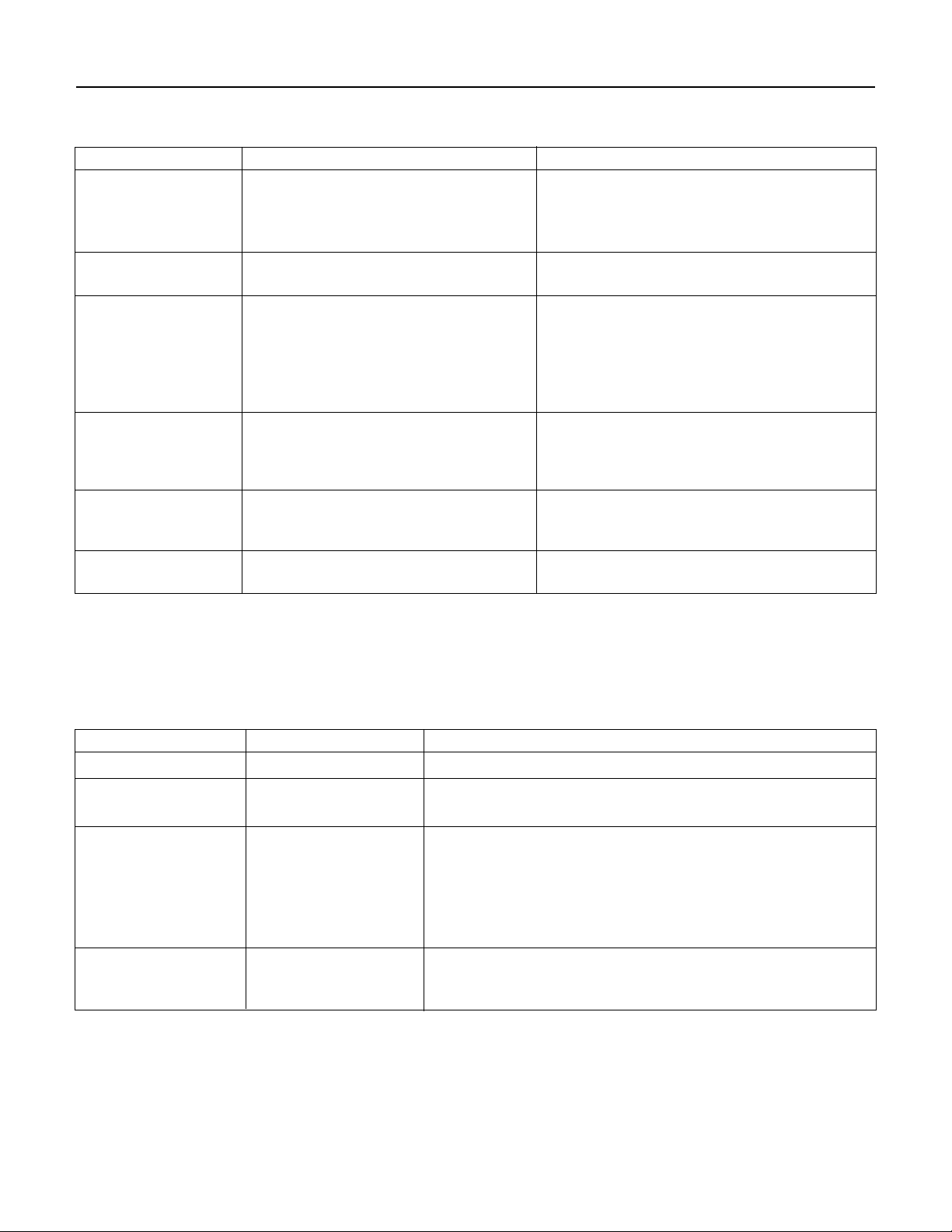
Installation 9
Error Description Possible Causes Fix
The Battery Failed The battery is highly sulfated Replace the battery with a 12-Volt deep-cycle
Pre-Qualification Test marine battery
The charger is connected to a Replace the battery with a 12-Volt deep-cycle
six-volt battery marine battery
Battery Over-Voltage The Charger is connected to a Replace the battery with a 12-Volt deep-cycle
24 Volt Battery marine battery
Charge Time Monitor Battery took too long to complete
its charge:
A. Load applied (e.g. the pump motor Be sure pump cannot start during charging;
started) during charging reset the charger
B. The battery ampere-hour rating Replace with correct size battery (see Page 4)
is too large (Max. 100 ampere-hours)
Excessive Battery Pump motor ran during charging Check primary sump pump. The BBU generally
Drain (that is, with the main A.C. power ON), runs only when the main A.C. power is out.
causing the system to shut down If there has not been any power outage and the BBU
has run, the primary pump itself may have failed
Reverse Battery Charger is connected backwards Reconnect Charger (+) to Battery (+)/(-) to (-)
Connection to the battery. (That is, Charger (+) to
Battery (-) and vice versa)
Battery Overheated Cells in an old battery may Replace battery with a 12-Volt deep-cycle
deteriorate with age marine battery
TABLE II - 800 mA Charger Error Table (Green and Yellow LEDs will flash alternately)
Charger Light On/Off/Flashing Indicates
All Lights Off System is not receiving AC power
Power (Red Light) On System is receiving AC power
Off System is NOT receiving AC power or battery leads are reversed
Charging (Yellow Light) Flashing 1x/Second Charger is running “Pre-Qualification” test (this lasts 45 seconds
to 6 hours)
On, steady Charger is either in “Constant Current” or “Constant Voltage” stage.
This may last up to 96 hours
Flashing alternately System is in an ERROR mode (see Table II, above)
with green light
Charged (Green Light) On, yellow light Off Battery is fully charged
Flashing alternately System is in an ERROR mode (see Table II, above)
with yellow light
TABLE III - 800 mA Charger Light Indications
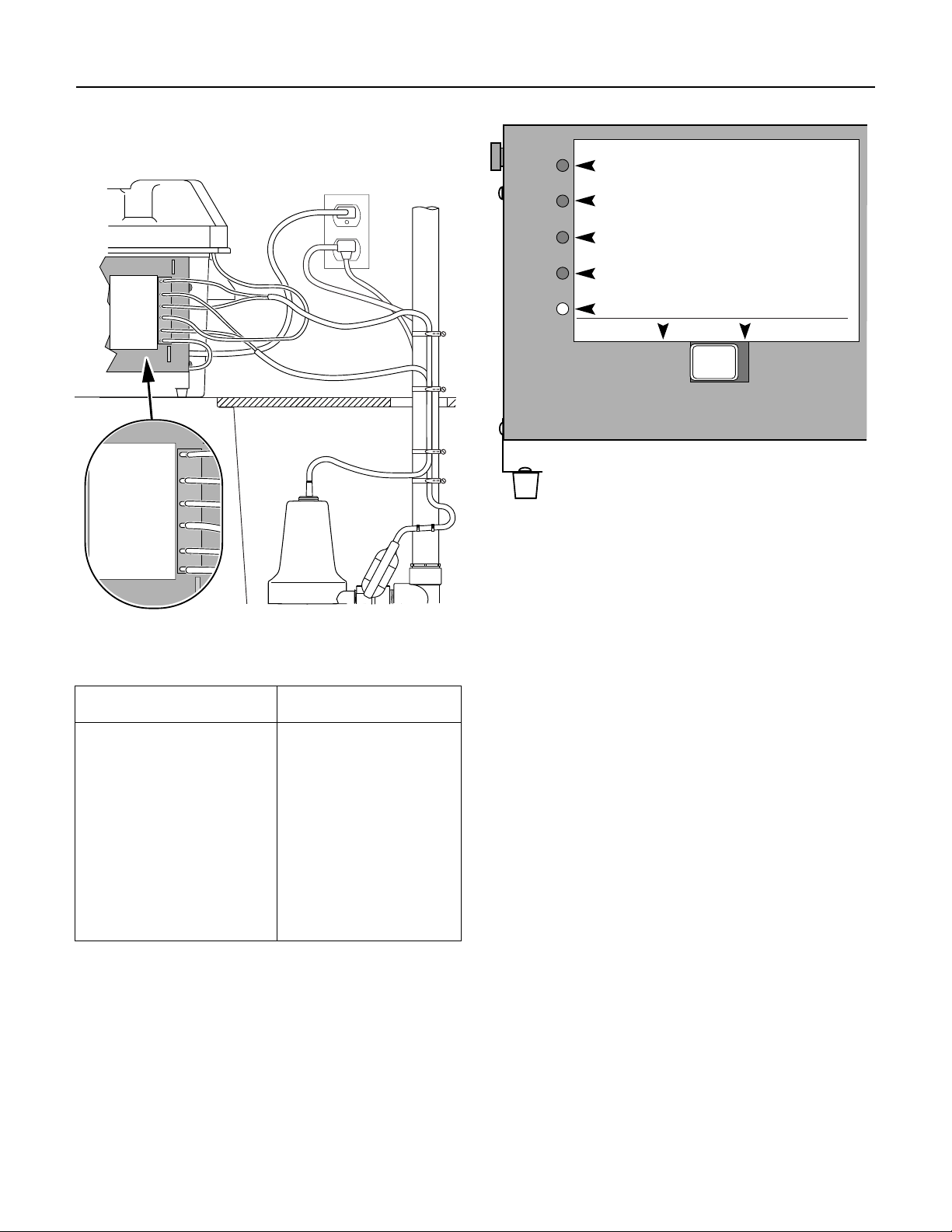
Installation 10
Model Number DB20018T:
1. Connect charger as shown in Table IV and Figure 11.
2. Plug the charger into a 115 Volt AC outlet delivering
at least 15 amps. Do not use a switch controlled
outlet. Mark the circuit in the main power panel
“Backup sump pump power supply; do not turn off”.
3. With the charger properly connected and plugged in,
the panel on the front of the charger will show one or
more of the following conditions (See Figure 12).
Red “AC Power Status” LED - AC power is present
Yellow (bicolor) LED on continuously - Prequalification test is com-
plete and charging is in process
Yellow “Charging” LED flashing on and off quickly - Equalization
charge stage
Green (bicolor) LED is on - Battery is being maintained at full
charge
Bicolor LED flashing yellow/green alternatively - See Charger
Error Table (Table VI, Page 11)
Test the Assembly:
1. Plug the primary pump into a properly grounded
3-prong outlet.
2. Fill the sump with water to start the primary pump.
Check for leaks.
3. Unplug the primary pump and fill the sump with
water to start the backup system pump. Check for
leaks.
4. Plug the primary pump back into a properly grounded
3-prong outlet. The system is now ready for operation.
Figure 11 – Wiring Connections DB20018T
To the position indicated
Connect the below, on the charger
Positive (+) lead from the battery Positive battery terminal
(leads are provided)
Negative (–) lead from the battery Negative battery terminal
(leads are provided)
Positive (+) “Backup sump Pump” Positive pump lead terminal
lead (BROWN wire)
Negative (–) “Backup sump Pump” Negative pump lead terminal
lead (BLACK wire)
Positive (+) Float switch Lead Positive float switch terminal
(WHITE wire)
Negative (–) Float Switch Lead Negative float switch terminal
(BLACK wire)
TABLE IV - DB20018T Wiring Connections
Figure 12 – DB20018T LED Panel
A.C.POWER
STATUS
PUMP RUN
STATUS
ALARM SILENCE
ÉTAT DU COURANT ALTERNATIF.
ESTADO DE LA CORRIENTE ALTERNA.
ÉTAT DE FONCTIONNEMENT DE
LA POMPE.
ESTADO DE FUNCIONAMIENTO DE
LA BOMBA.
ARRÉT D'ALARME.
SILENCIO DE ALARMA.
PUMP/POMPEBOMBA (+)
FLOAT/FLOTTEUR/FLOTADOR (+)
PUMPPOMPE BOMBA ( )
BATTERY/BATTERE/BATERÍA ( )
FLOAT/FLOTTEUR/FLOTADOR ( )
BATTERY/BATTERE BATERÍA (+)
PUMP/POMPE/BOMBA (+)
FLOAT/FLOTTEUR/FLOTADOR (+)
PUMP/POMPE/BOMBA (–)
BATTERY/BATTERIE/BATERÍA (–)
FLOAT/FLOTTEUR/FLOTADOR (–)
BATTERY/BATTERIE/BATERÍA (+)
BATTERY STATUS
CHARGER MODE
SILENCE
ARRÉT/SILENCIO
ÉTAT DE LA BATTERIE.
ESTADO DE LA BATERÍA.
MODE DU CHARGEUR.
MODO DE CARGADO.
ALARM
ALARME/ALARMA
RESET/RÉARMEMENT
REPOSICIÓN
3464 0799