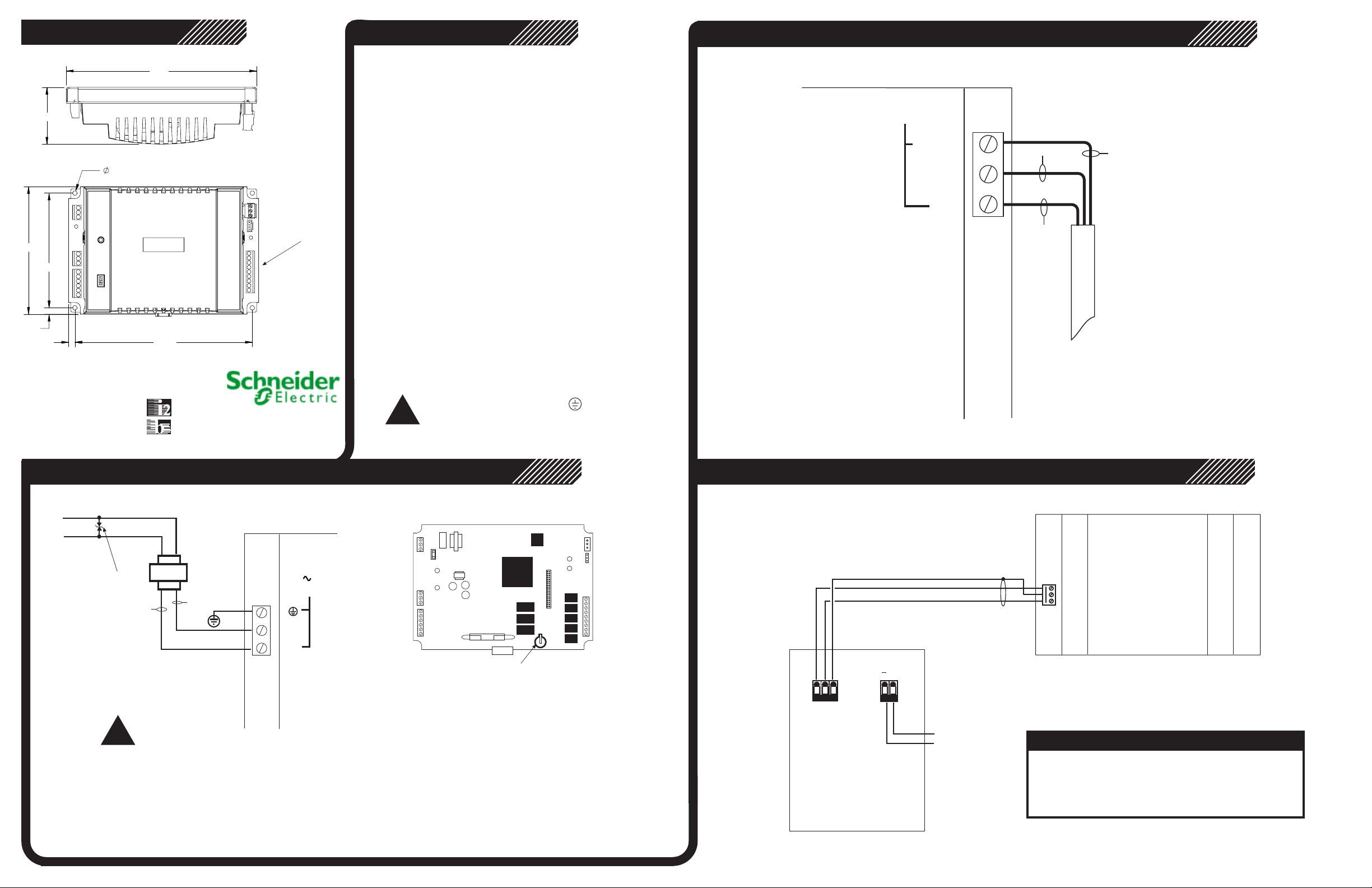
Mechanical
8.16
Wiring Rules
These modules are intended for installation within the enclosure
of another product.
Do not remotely ground any part of the input sensor wiring.
RS-485 Connection
850 Series Module
5.47
.27
2.44
4.920
7
.2
.187 THRU
To ensure proper
relay operation, do
not mount controller
with this (right-hand)
edge facing down.
7.610
850 Series Installation
b
3
30-3001-808 Rev G
Remote grounds connected to the return terminal could make
the system operate incorrectly or damage the equipment.
The signal return is not true earth ground. It is an electronic
reference point necessary to interpret the sensor properly.
For reliable input operation, follow these input wiring guidelines:
· Never lay wires across the surface of a printed circuit board.
· Wires should never be within 1 in. or 25 mm of any component
on a printed circuit board.
· Use shielded input wire.
· Terminate the shield of the input wires at one end of the run
only—preferably at the end where your I/O module is located.
· Be careful when stripping wire not to drop small pieces of wire
inside the cabinet.
· Don’t run your input wiring in the same conduit with AC power.
· Don’t run your input wiring in the same conduit with your
output wiring.
Grounding the Controller
To insure proper operation of the controller, it is imperative that it be connected
to a good earth ground. It is important that this connection be made as close to
the module as possible.
Caution: Earth ground ( ) must be
!
connected to avoid module damage.
RS-485
SHLD 24
Black (-)
23
-
+
22
White (+)
Shield
RS-485 Cable
AC Power & Battery Backup Connection Smart Sensor Bus Interface (IN5 & SPWR)
AC Line
Power
24 VAC Step-Down
X2
Transformer
White or
Green
Optional Varistor
choose a voltage rating appropriate to the
input voltage applied. i.e 130V or 250V
Black
X1
!
Use care when attaching power
wiring to these connectors.
They are not to be used as a strain relief.
The connectors cannot withstand
excessive bending or flexing.
Use a separate transformer for each unit installed.
850 Series Module
AC POWER
24 VAC
20 VA
50/60 HZ
1
23N
L
BATTERY
BATTERY ENABLE INFORMATION
During shipment, an insulating plastic tab is inserted under
the clip on the battery to prevent it from draining prior to
installation. To activate the battery, this tab must be removed.
Remove the top of the plastic case to access the board.
(SPWR)
(RET)
(IN3)
SMART SENSOR
INF
+
RS-485 +
RS-485 -
850 Series Module
SPWR
RET
IN5
DETAILED PROGRAMMING & TECHNICAL INFORMATION
Refer to the following documents:
i2 Controller Technical Reference, 30-3001-861
b3 and b4920 Controller Technical Reference, 30-3001-862
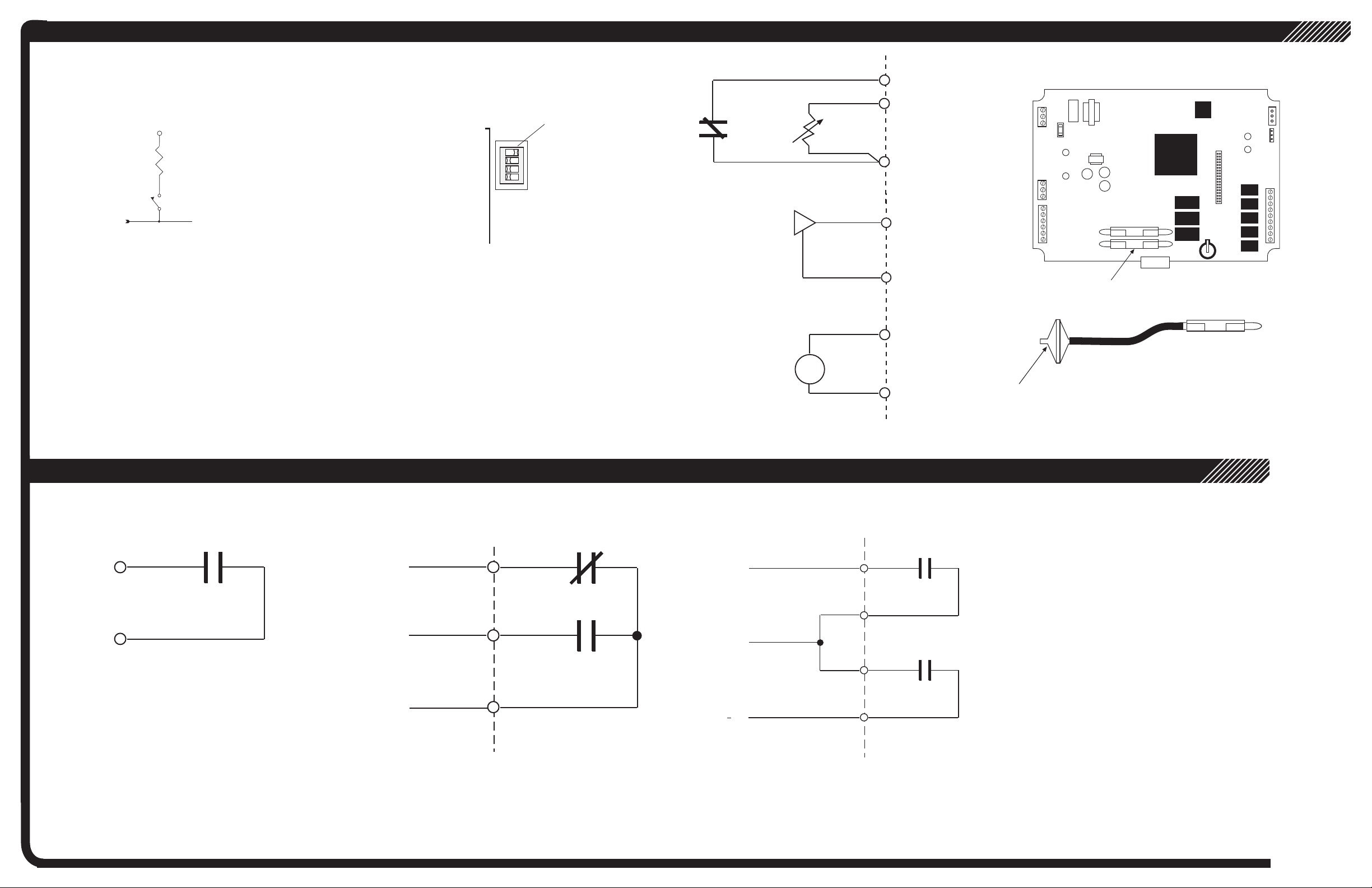
Inputs
INPUT
VREF
Each input includes a reference
resistor that may be disabled.
10K
Switch shown in
‘disabled’ OFF position
Accessing the Reference Resistor Switch
Switch shown in
led Position
710IN 1
8
IN 2
9
RET
IN 3
11
IN 4
12
RET
OFF
1 2 3 4
ON
O N
Enab
1
2
3
4
Contact
Closure
Digital Logic
Signal
+
V
-
Thermistor
DC Voltage
IN x
IN x
Reference
Resistor = ON
RET
IN x
Reference
Resistor = OFF
RET
IN x
Reference
Resistor = OFF
RET
Airflow Sensor Input
Input #7
Input #8
AIR FLOW SENSOR(s)
Filter
Side Marked “IN”
Airflow Sensor
P
1
(mar
ked on sensor case)
Outputs
Digital Form A Output
OUT x
OUT x
Output Rating: 24 V
AC @ 3 A
30 VDC @ 3A
- ON
+ ON
Common
Tristate Output
OUT 1 NC
OUT 1 NO
OUT 1 COM
Max DC Input Voltage = 5V
Tristate from 2 Form A Outputs
+ ON
Common
ON
Using Two Outputs to make
FORM K
OUT x
GND
GND
OUT x
Adjacent output pairs:
OUT1 and OUT2
OUT2 and OUT3
can be combined to form a standard Tri-state output.
The outputs are electrically connected as shown in the
schematic for the built-in Tri-state output.
Configure the output point of the first point of a pair
(i.e., OUT1 of the pair OUT1 and OUT2) with an
Electrical Type of Tri-state.