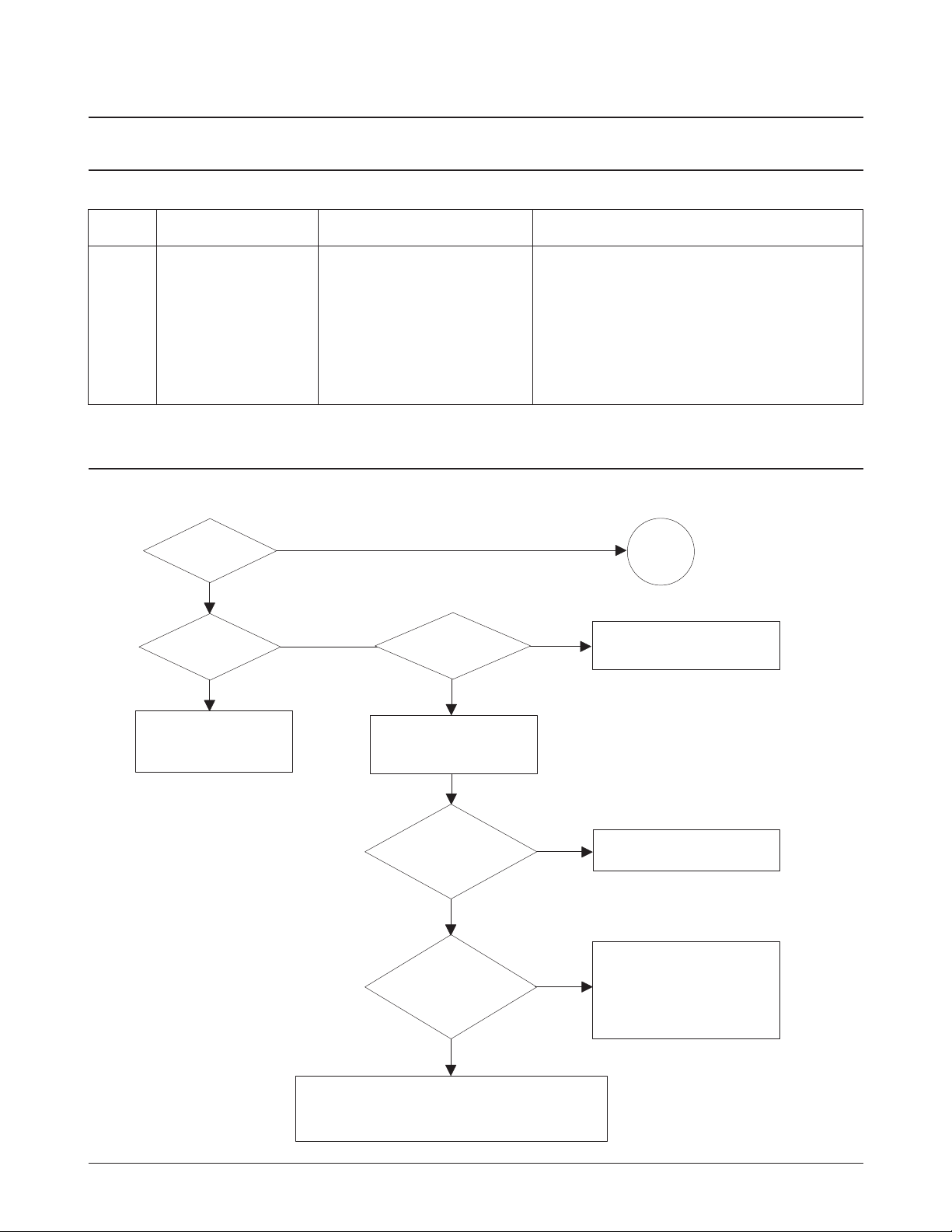
4. Troubleshooting
4-1 Abnormal Image Printing and Defective Roller
If abnormal image prints periodically, check the parts shown below.
Samsung Electronics 4-1
No Roller Abnormal image period Kind of abnormal image
1 OPC Drum 94.3mm White spot
2 Charge Roller 37.7mm Black spot
3 Supply Roller 40.0mm Horizontal density band
4 Develop Roller 46.1mm Horizontal density band
5 Transfer Roller 47.1mm Black side contamination/transfer fault
6 Heat Roller 56.1mm Black spot and fuser ghost
7 Pressure Roller 56.2mm Black side contamination
Check connection to
computer or replace
controller.
Take out the cartridge
and prepare the tester
for electronic connection.
Repair or replace the GND
terminal.
Check the path between
video controller, engine board
and HVPS. Repair or replace
the defective component
or board.
The mirror in LSU might be misplaced so the light
path to the OPC deviates ->Repair or replace LSU
or remove any defective matters in the machine.
Self test
pattern prints?
No image?
Self testing
is possible via
DCU?
Is the OPC
terminal of machine
well-connected
to Frame?
Does the
video data line to
LSU transit to High/Low
when printing?
Re-test after replacing the
conector or controller board.
A on
next page
NO
NO
NO
NO
NO
YES
YES
YES
YES
YES
4-2 Print Quality
4-2-1 No Image
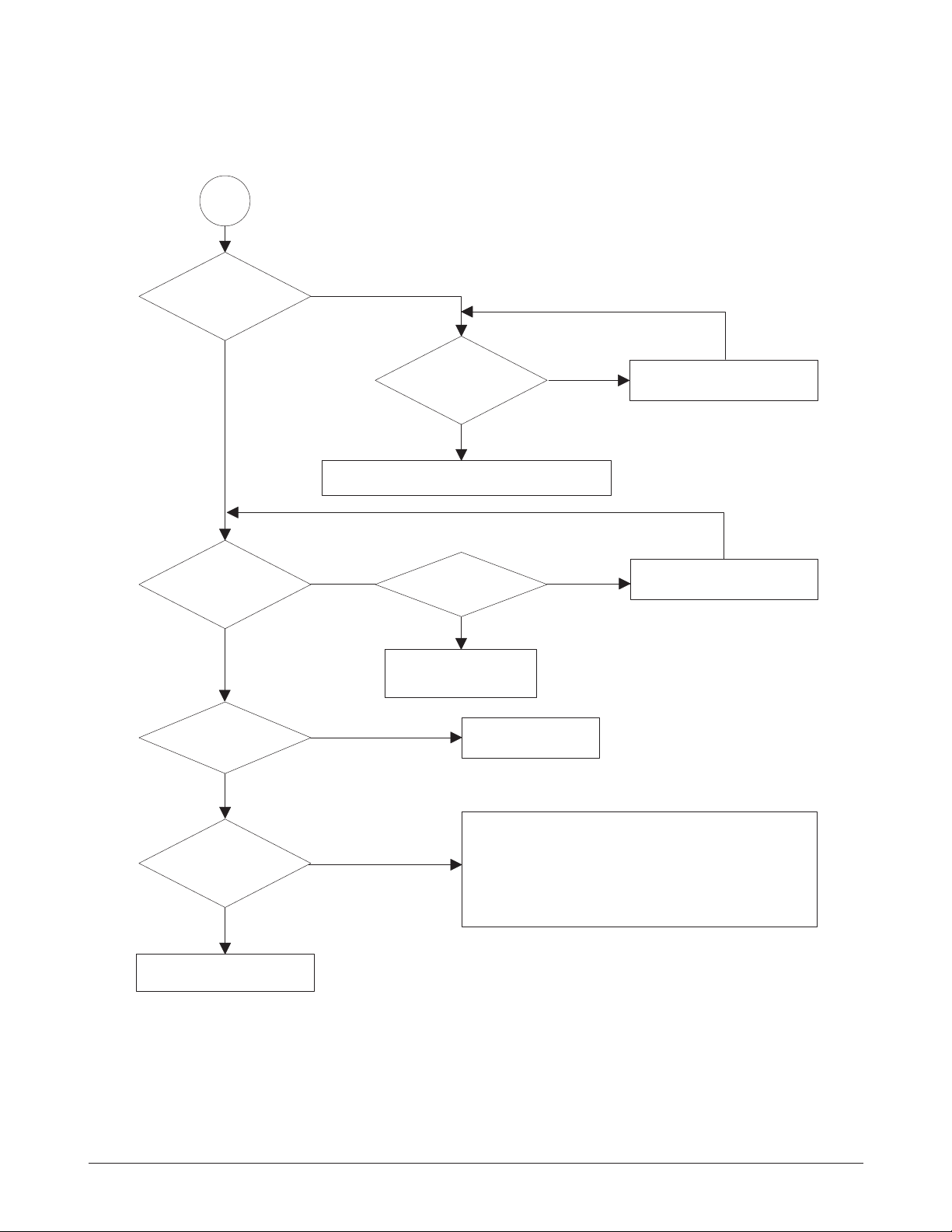
4-2 Samsung Electronics
Troubleshooting
Transfer roller might be out of its location.
-> Locate the roller into its place.
This could occurrs when the power of LSU is low or
the density is low due to the obstacles on the window
-> Replace LSU or clean the window.
A
Transfer
voltage OK? (on the
transfer roller
shaft)
Are the
connection terminal
and connection
correct?
Repair or replace terminal.
Sealing tape
is removed from the
cartridge?
Replace HVPS or repair defective component.
Is the connection
terminal OK?
Replace HVPS or repair
defective component.
Repair or replace terminal.
Remove the tape.
Developing
(-300V) and supplying
(-500V) voltage
are OK?
Does the
counter indicate over
the toner's guarranty
life?
Replace the toner cartridge.
NO
NO
NO
NO
NO
NO
YES
YES
YES
YES
YES
YES
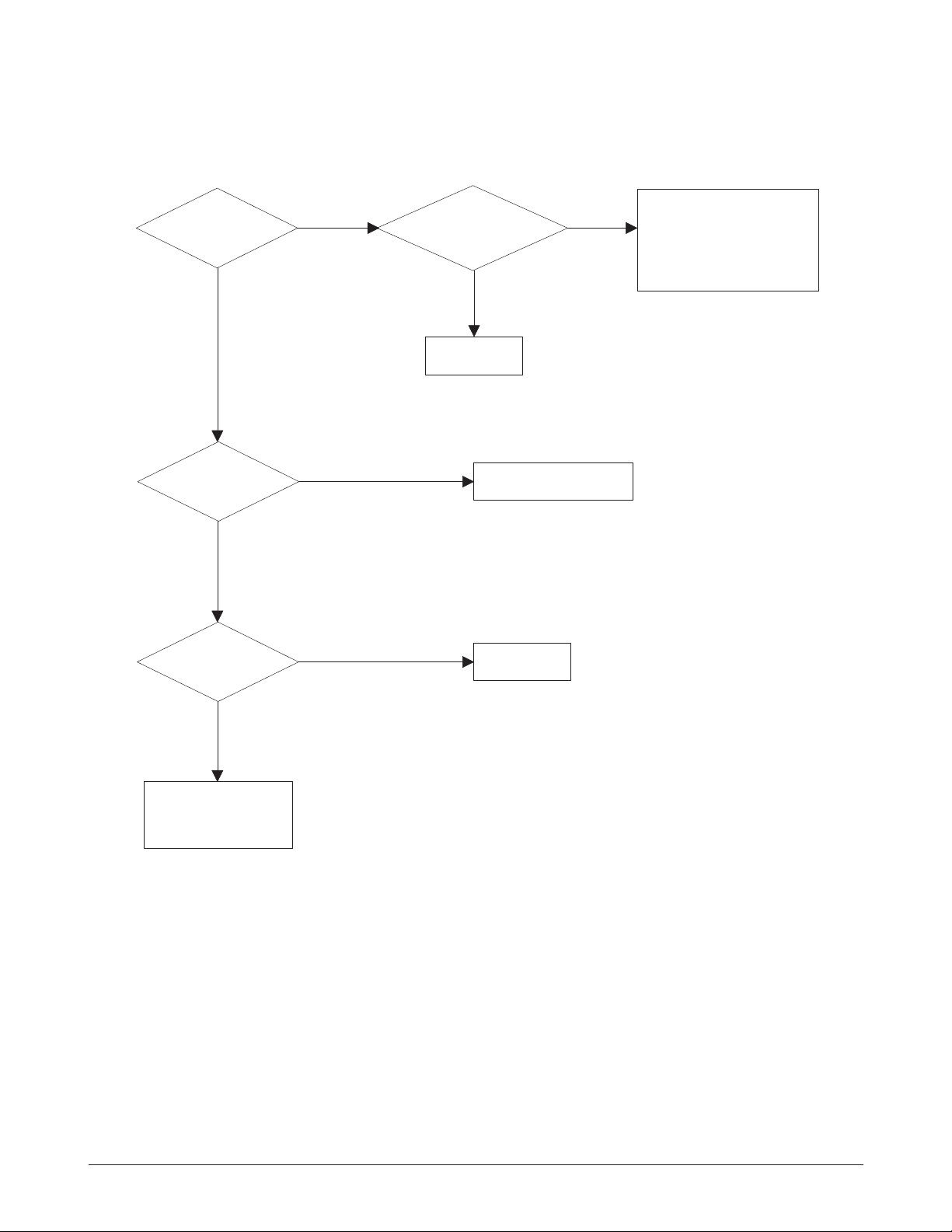
4-3
Samsung Electronics
Troubleshooting
All black in
printing area?
Is transfer
voltage supplied
from HVPS?
Is the
Hsync/ signal received
in LSU?
Transfer part's contact
is bad. -> Repair or
replace toner cartridge.
Does the
video data line to LSU
transit to High/ Low when
printing?
Replace LSU.
Check the path among video
controller, engine board,
HVPS, LSU for the shortage
or open. -> Repair or replace
the boards.
Repair or replace HVPS.
Replace LSU.
NO
NO
NO
NO
YES
YES
YES
YES
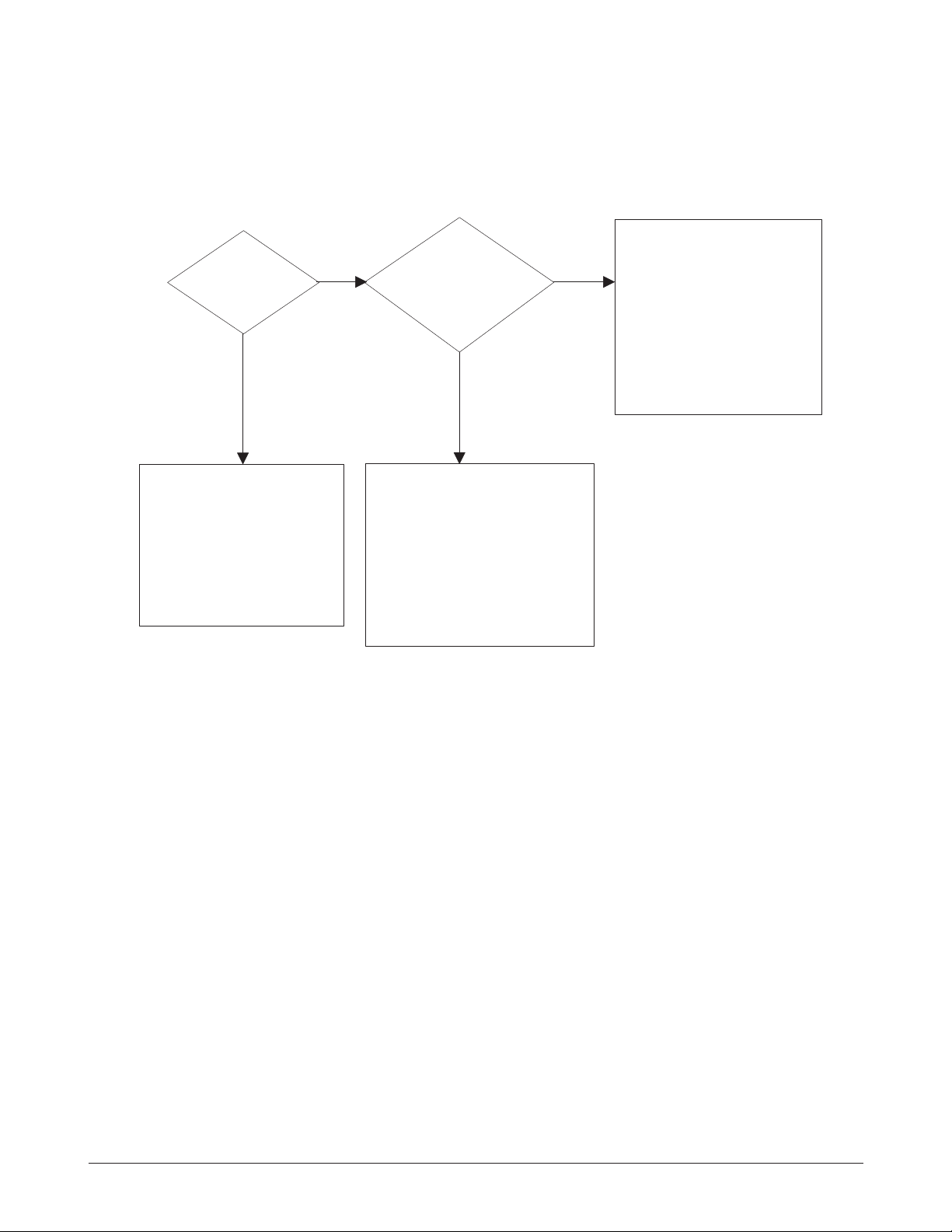
4-4 Samsung Electronics
Troubleshooting
White line
missing definitely?
Dirt of dust stuck onto the
window of internal lens of LSU
-> Clean it or replace LSU.
Preventive obstacles through
the path between OPC of
developer and LSU prevent the
path -> Remove the obstacles.
Check if the
printout is still has the
same problem even right after
passed through the
transfer roller.
Toner material might be stuck to
blade in the developer inside and it
prevents toner supply -> Replace
the developer.
Check both if the toner cartridge's
counter is over its guaranty and
amount of the toner material.
-> Replace the toner cartridge.
The ribs in fuser or toner on the
roller may invoke the image
problem. -> Replace the fuser
cover or the defective part.
The image is originally black or the
black part is far close to the top.
-> Use the pattern which has the
image below bigger than 10mm
from the top.
NO
NO
YES
YES
4-2-3 Vertical White Line (Band)
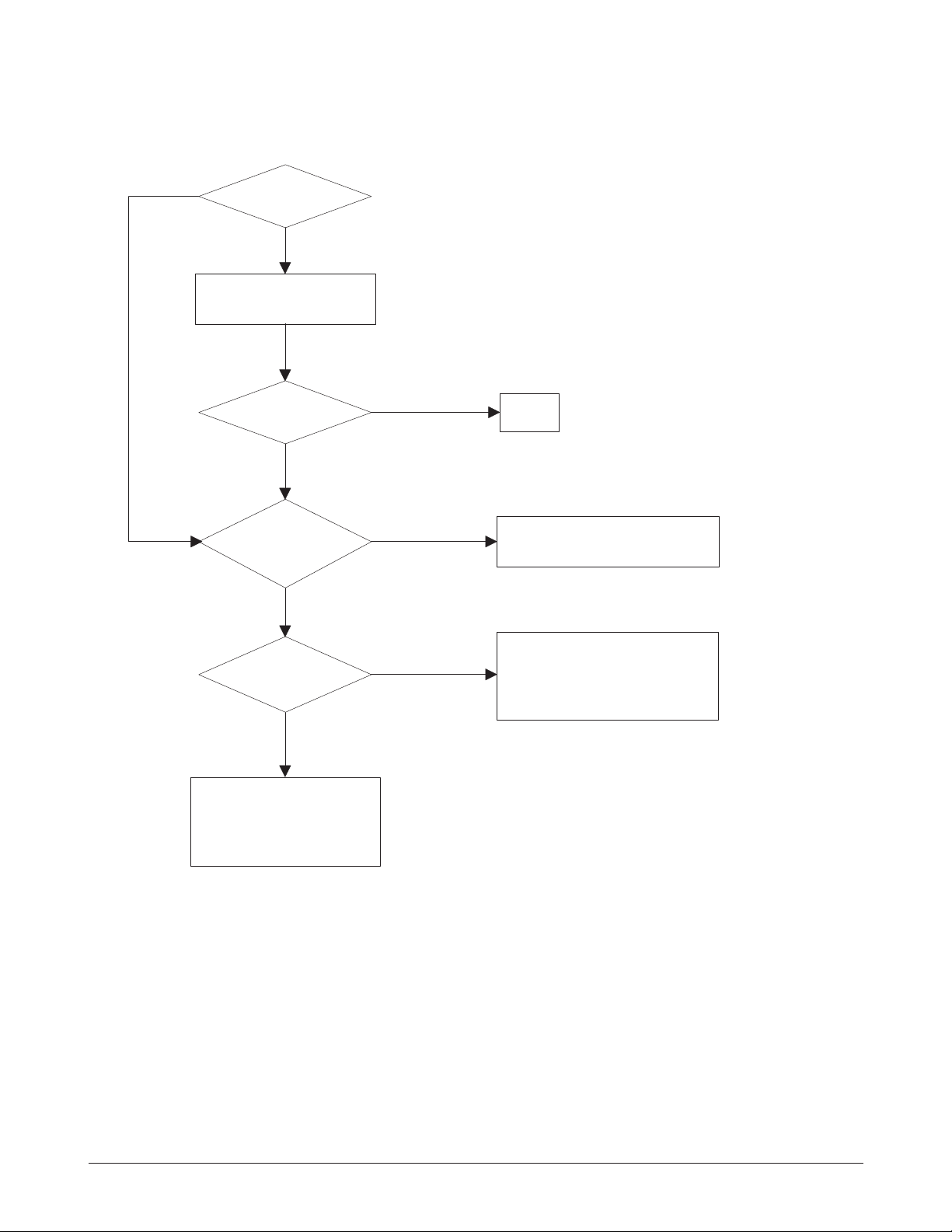
4-5Samsung Electronics
Troubleshooting
'Dark' selected
via RCP?
Change to
'Normal' and test.
Works
correctly with
-300V of Bias
voltage?
Works
correctly after
replaced LSU?
Repair or replace the defective
component.
The power of LSU is set
high or internal problem.
-> Replace LSU or adjust
volume.
Same at 'Normal'?
END
NO
NO
NO
Toner over supply due to the
adjustment fault of metering
blade in developer.
-> Replace developer.
NO
YES
YES
YES
YES
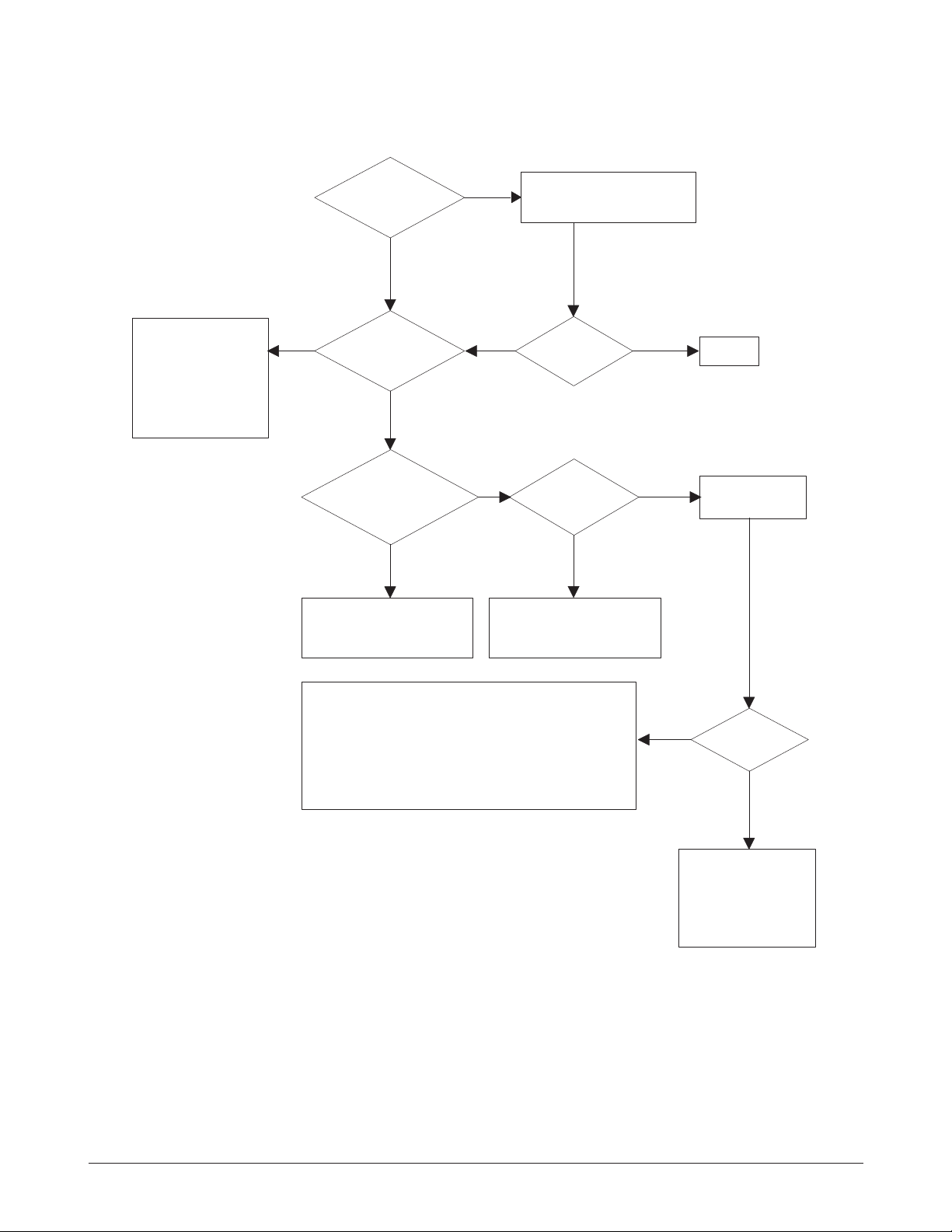
4-6 Samsung Electronics
Troubleshooting
Recommended
paper used?
Transfer,
charge and developing
voltage are OK?
Operating/
storage atmosphere is
too high temperature
/humidity?
Solve the problem under
the recommended condition
(10-32 degree Centigrade).
Dirt or
dust around the
charge roller?
Clean the charge roller
or replace step-up device
/terminal after check.
Work OK?
Internal blade or
suppying part of the
developer is defective.
-> Replace the toner
cartridge.
Check terminals or contacts and 'Guide-Deve Spring'
are misplaced.
-> Repair or replace transfer roller etc.
Check if the LED of PTL in front of the transfer roller
is on when it presses the top cover switch on purpose.
-> If not, replace PTL.
Print 20 to 30 pages using
the recommended paper.
Same problem
occurs?
- Adjust voltage or
replace HVPS.
- Repair or replace
after checking the
terminals' contacts.
END
Replace the
toner cartridge.
NO
NO
NO NO
NO
NO
YES
YES
YES
YES
YES
YES