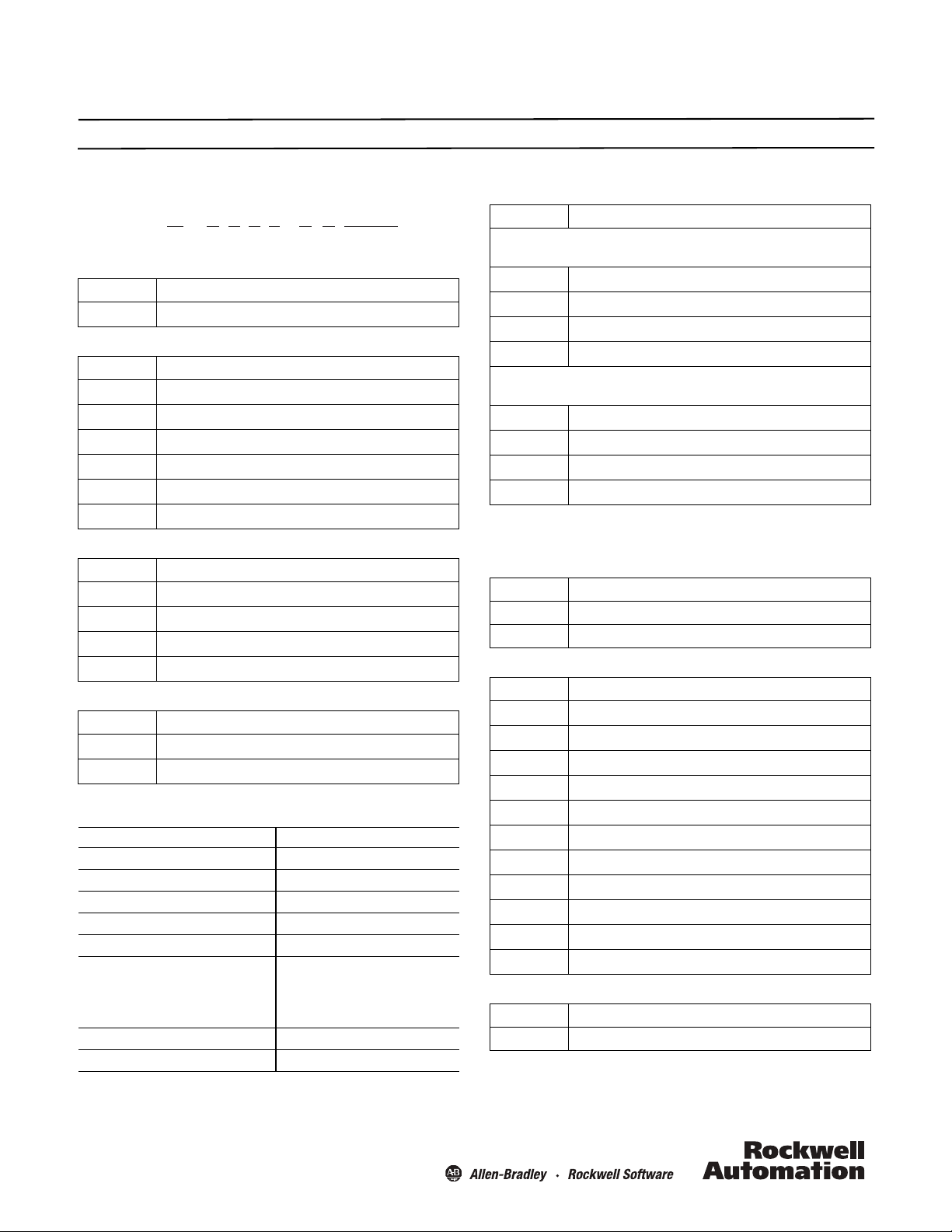
Installation Instructions
IMPORTANT: SAVE THESE INSTRUCTIONS FOR FUTURE USE.
847
H
a
-
D
b
c
e
-
01024
M1 4 R B
dfgh
847H 2.5 in. Diameter Solid Shaft Incremental Encoders
Selection Guide
a
Code Encoder Diameter/Type
H 2.5-in. diameter solid shaft
b
Code Mounting Configuration
D Standard square flange
E 70 mm diameter servo mount (64 mm bolt circle)
I 90 mm diameter servo mount (70 mm bolt circle
G 65 mm diameter servo mount (48 mm bolt circle)
HStandard servo mount
J 65 mm diameter servo mount (42 mm bolt circle)
c
Code Shaft Size
K 6 mm diameter shaft with flat
L 10 mm diameter shaft with flat
M 1/4 in. diameter shaft with flat
N 3/8 in. diameter shaft with flat
d
Code Power Supply
14.5…5.5V DC
28…30V DC
Accessories
Description Part Number
High-performance flexible coupling 845-FC-*-*
Measuring wheels 845-MW-A-*
Servo clamps 845-SC
Mounting plates 845-MB-*
Pre-wired cables 845-CA-*-*
Mating connectors 845-6P
Differential encoder buffer board 845-BB*
M12 cable 889D-F8FB-*
* See Sensor Catalog for selection
845-7P
845-7P-RT
845-10P
845-10P-RT
e
Code Output Configuration
Signal phasing A-leads-B
clockwise rotation viewed from shaft end, Z gated A
4 4.5…5.5V line driver outputs (TTL)
5 4.5…5.5V open collector outputs
6 8…30V line driver outputs (HTL)
7 8…30V open collector outputs
Signal phasing B-leads-A
clockwise rotation viewed from shaft end, Z gated BN
A 4.5…5.5V line driver outputs (TTL)
B 4.5…5.5V open collector outputs
C 8…30V line driver outputs (HTL)
D 8…30V open collector outputs
Options 5 and B cannot be ordered with option 2 from table d.
Options 6, 7, and C cannot be ordered with option 1 from table d.
f
Code Connector/Cable Exit
AAxial exit
R Radial exit
g
Code Connector/Cable Type
A M12 connector, 8-pin with mating connector
B M12 connector, 8-pin
C MS connector, 6-pin with mating connector
D MS connector, 6-pin
E MS connector, 7-pin with mating connector
F MS connector, 7-pin
G MS connector, 10-pin with mating connector
H MS connector, 10-pin
P 1.5 m (4.9 ft) cable
Q 5 m (16.4 ft) cable
R 10 m (32.8 ft) cable
h
Code Resolution
1…65536 00001…65536 pulses/revolution
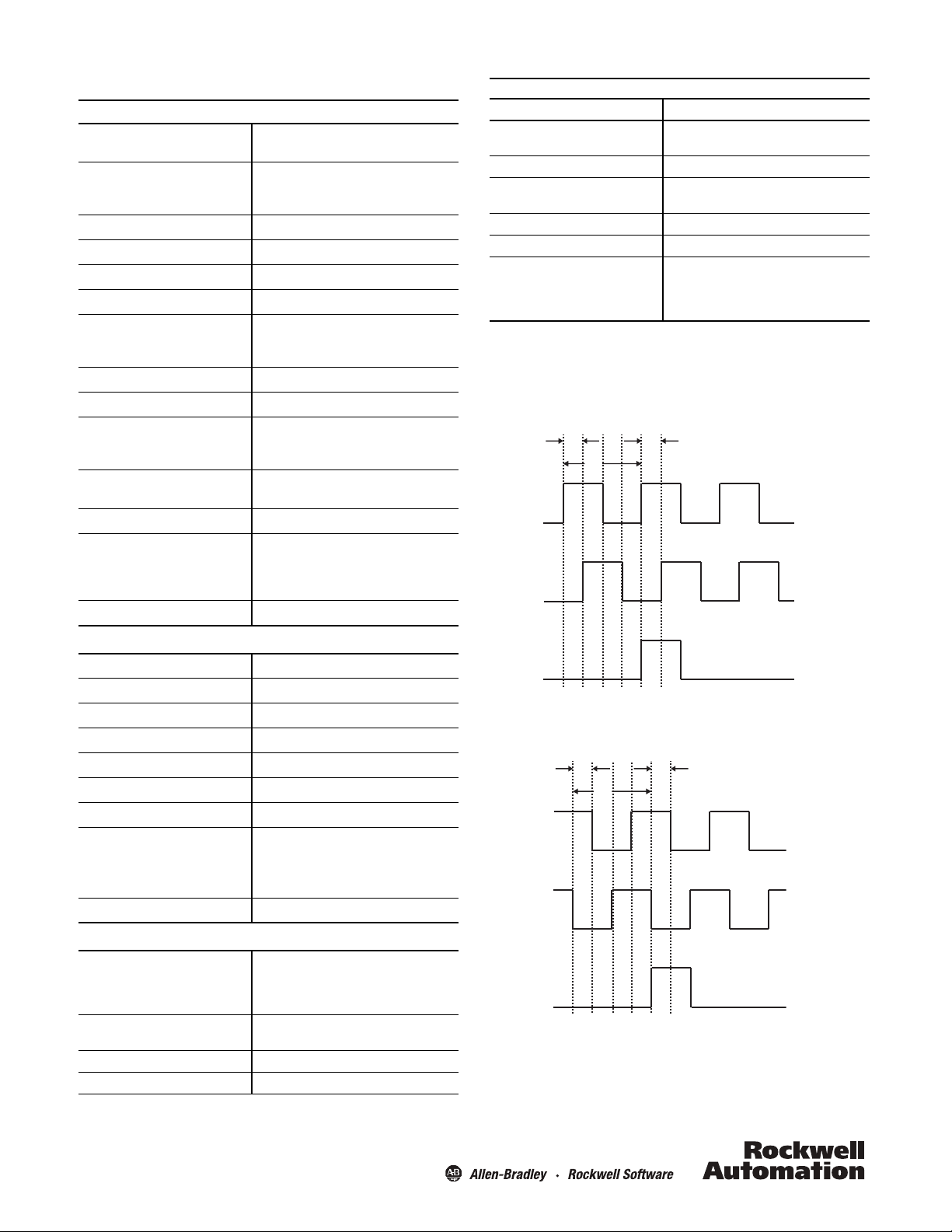
Specifications
Clockwise rotation when facing encoder shaft
Signals and marker option - A leads B (CW rotation)
Measuring step
Complementary signals AN, BN, and ZN are supplied
only on units with line driver outputs.
Measuring step
B leads A, 180°
marker gated with BN
Signals and marker option - B leads A (CW rotation)
Clockwise rotation when facing encoder shaft
A leads B, 180°
marker gated with A
Electrical
Code format Incremental
Signal options,
clockwise rotation viewed from
shaft end
Signal phase relation 90° ± 22° channels
Symmetry 50% ± 10%
Zero index channel Gated 1/2 cycle
Supply current 50 mA
Frequency response 4.5…5.5V line driver output: 820 kHz
Resolution 1…65536 pulses/revolution
Load current 30 mA for all output types
Output drivers 4.5…5.5V line driver - IC HD2
Electrical protection Reverse polarity and short circuit for
Cable outer diameter 0.25 in (6.2 mm)
Cable type 300V, 105° C, 26 AWG, 9-conductor
Cable bend radius Minimum 5x outer diameter
2 channels with zero index
A-leads-B, 180° marker gated with A
or
B-leads-A, 180° marker gated with BN
8…30V line driver output: 820 kHz
Open collector: 150 kHz
8…30V line driver - IC HD2
Open collector - 7406
all output types
with overall braided shield, UL AWM
type 20327 for use in fixed (nonflexing) installations; RoHs compliant.
Environmental (continued)
Vibration 30 G/10…2,000 Hz
EMC EN 61000-6-2 and EN 61000-6-3
(M12 connector)
Housing material EN AC-47100 die-cast aluminium
Housing finish Powder coat paint, color RAL 9005,
Pantone black C (jet black)
Flange material 6061-T6 aluminium
Shaft material SAE 303 stainless steel
Certifications RoHS compliant
CE marked for all applicable directives
UL listing valid only for encoders with
cable and M12 connections
Output Waveforms
90°
360°
A
B
Mechanical
Maximum operating speed 9,000 RPM
Angular acceleration 500,000 radians/s²
Moment of inertia 15 g•cm²
Startup torque at 20 ºC (68 ºF) 0.8 N•cm
Operating torque at 20 ºC (68 ºF) 0.6 N•cm
Approximate weight [kg (lb)] 0.28 (0.61) with M12 connector
MTTFd (EN ISO 13849-1) 330 years
Shaft loading
Shaft diameter [mm (in.)] 6 (0.24), 10 (0.39), 6.4 (1/4), 9.5 (3/8)
Environmental
Enclosure rating per IEC 60529 Shaft: IP 65
Temperature -30…80 °C (-22...176 °F) operating
Relative humidity 90% non-condensing
Shock 100G/11ms duration
80 N radial (20 mm from front bearing)
and 40 N axial provide L10 life of
9
revolutions at 9,000 RPM and
3.6 x 10
80° C ambient temperature.
Housing, connector version with
mating connector installed: IP67
Housing, cable version: IP67
-40…100 °C (-4...212 °F) storage
Z
2

Connector Pins and Signal Availability
4 x M4 x 0.7 - 6H
70.0
(2.76)
90.0 (3.54)
B
39.7(1.56)
50.0
(1.97)
9.0
(0.35)
19.1
(0.75)
63.5 (2.50)
A
3 x 8-32 UNC
4.8
(0.19)
47.63
(1.875)
A
Standard Servo Mount Encoder
with Radial M12 Connector
66.7(2.63)
52.4(2.06)
3 x 8-32 UNC
4.8 (0.19)
47.63
(1.875)
5.6 (0.22)
4 x
52.4
(2.06)
66.7
(2.63)
A
Standard Square Flange Encoder
with Radial M12 Connector
64.0
(2.52)
4 x M4 x 0.7 - 6H
70.0 (2.76)
B
39.7
(1.56)
50.0
(1.97)
9.0
(0.35)
19.1
(0.75)
63.5 (2.50)
A
90 mm Diameter Servo Mount Encoder with Radial M12 Connector
(70 mm bolt circle)
70mm Diameter Servo Mount Encoder with
Radial M12 Connector (64 mm bolt circle)
equally spaced
equally spaced
equally spaced
equally spaced
Dimensions [mm (in.)]
Shaft dimensions
Nominal dia.
Shaft A
Flat dim., B
1/4 in. 6.237/6.312 (0.2491/0.2485) 5.5 (0.22)
6 mm 6.000/5.988 (0.2362/0.2357) 5.5 (0.22)
3/8 in. 9.507/9.492 (0.3743/0.3737) 8.5 (0.33)
10 mm 9.977/9.962 (0.3928/0.3922) 9.0 (0.35)
Signal Name MS 6-pin MS 7-pin MS 10-pin M12 8-pin Cable Wire Colors
V DC BDD8Red
Common AFF7Black with red band
A output EAA2White
AN output - - H 1 Black with white band
B output DBB4Blue
BN output --I3Black with blue band
Z output CCC6Green
ZN output - - J 5 Black with green band
Zero set input -EE-Yellow
Case FGG-Black
A
Encoder
connectors/
cable view
Recommended
mating cable
part number
845-CA-A-* 845-CA-B-* 845-CA-C-* 889D-F8FB-* (Attached to encoder)
F
E
B
G
C
D
-
3

Dimensions [mm (in.)] (continued)
Encoder with Axial MS Connector
42.0
(1.65)
3 x M4 x 0.7 - 6H
5.0 (0.20)
2.5
(0.10)
63.5(2.50)
B
2.5
(0.10)
34.7(1.36)
50.0 (1.97)
31.70 ± 0.03
(1.248 ± 0.001)
9.0
(0.35)
19.1
(0.75)
58.7(2.31)
63.5 (2.50)
A
48.0
(1.89)
3 x M3 x 0.5 - 6H
5.0 (0.20)
2.5
(0.10)
B
2.5
(0.10)
34.7
(1.36)
50.0
(1.97)
31.70 ±0.03
(1.248 ±0.001)
9.0
(0.35)
19.1
(0.75)
58.7 (2.31)
63.5 (2.50)
63.5 (2.50)
A
C
21.3
(0.84)
50.0
(1.97)
Encoder with Axial M12 Connector
Encoder with Radial MS Connector
Encoder with Axial Cable
65 mm Diameter Servo Mount Encoder with
Radial M12 Connector (48 mm bolt circle)
65 mm Diameter Servo Mount Encoder with
Radial M12 Connector (42 mm bolt circle)
equally spaced
equally spaced
Dimensions with
Axial MS Connector
Typ e D
6-pin 17.8 [0.70]
7-pin 17.8 [0.70]
10-pin 23.4 [0.92]
Encoder with Radial Cable
per part no.
Dimensions with
Axial Cable or Axial Connector
Encoders C
70 and 90 mm diameter
servo mount
70.9 (2.79)
Other mounting configurations 65.9 (2.59)
Dimensions with Radial
MS Connector
Typ e E
6-pin 63.9 (2.52)
7-pin 63.9 (2.52)
10-pin 69.4 (2.73)
per
part no.
Shaft dimensions
Nominal dia.
Shaft A
Flat dim., B
1/4 in. 6.237/6.312 (0.2491/0.2485) 5.5 (0.22)
6 mm 6.000/5.988 (0.2362/0.2357) 5.5 (0.22)
3/8 9.507/9.492 (0.3743/0.3737) 8.5 (0.33)
10 mm 9.977/9.962 (0.3928/0.3922) 9.0 (0.35)
Cable
options
1.5 m (4.9 ft)
5 m (16.4 ft)
10 m (32.8 ft)
DC
E
Rockwell Automation maintains current product environmental information on its website at
http//www.rockwellautomation.com/rockwellautomation/about-us/sustainability-ethics/product-environmental-compliance.page
www.rockwel lautomation.com
Power, Control and Information Solutions Headquarters
Americas: Rockwell Automation, 1201 South Second Street, Milwaukee, WI 53204-2496 USA, Tel: (1) 414.382.2000, Fax: (1) 414.382.4444
Europe/Middle East/Africa: Rockwell Automation NV, Pegasus Park, De Kleetlaan 12a, 1831 Diegem, Belgium, Tel: (32) 2 663 0600, Fax: (32) 2 663 0640
Asia Pacic: Rockwell Automation, Level 14, Core F, Cyberport 3, 100 Cyberport Road, Hong Kong, Tel: (852) 2887 4788, Fax: (852) 2508 1846
Copyright © 2014 Rockwell Automation, Inc. All rights reserved. 10001065809 Ver 00 July 2014
.
847H-IN001A-EN-P
Printed in USA