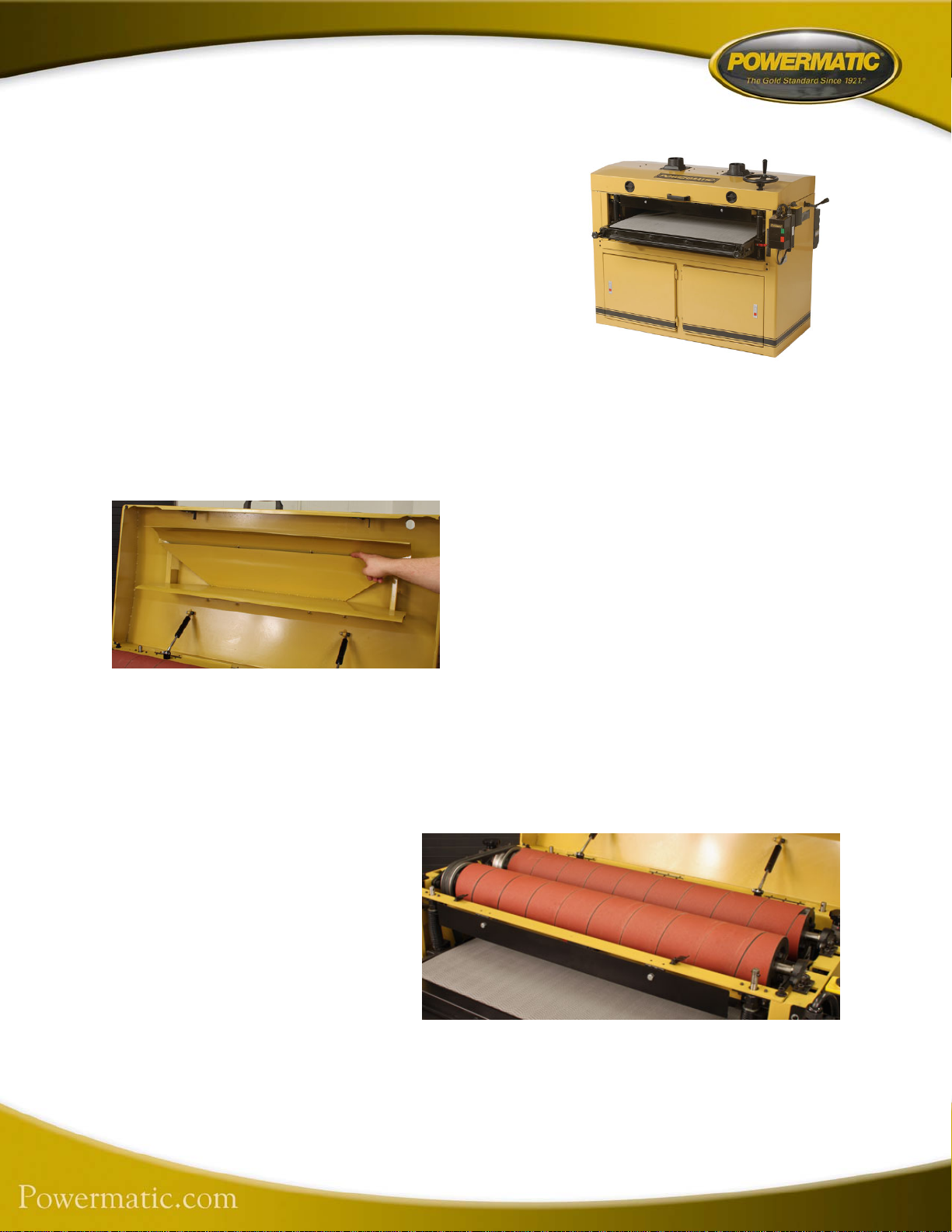
POWERMATIC DDS-225/DDS-237 Dual Drum
Sander
The POWERMATIC DDS-237 Dual Drum Sander is a
production class machine that is loaded with features and
available in configurations to suit your needs. The
#1791321 (DDS-237, 37” drums) is equipped with a
10HP, 230/460V (prewired 230V), 3 PH motor. Also
available are the #1791320 (DDS-237 37”-drums) with a
7.5HP, 230V, 1Ph motor and the #1791290 (DDS-225,
25”-drums) powered by a 5HP, 230V, 1Ph motor. All
POWERMATIC Dual Drum Sanders are protected with a
full magnetic On-Off switch. Aside from the 25” drum
length of the DDS-225, the features remain similar.
The POWERMATIC DDS-237 Dual Drum
Sander is a very capable solution for your
sanding needs.
Size and Capacity
Despite the compact 60”-wide x 45”-deep x 45”tall overall size, (DDS-237 model) the
POWERMATIC Dual Drum Sanders have the
capacity to handle a huge range of jobs from
small to large. With a minimum board length of
just 9”, a minimum thickness of 1/32” and
maximum thickness of 5-1/4”, these sanders offer
expansive job coverage.
The top of the cabinet opens for easy access to the drums
and shows the special dust system that helps keep this
machine performing.
Spacious Cabinet
The POWERMATIC Dual Drum Sanders are enclosed in an all-steel cabinet. Compartments
with latching doors at the bottom enclose the motor, drive systems and provide spacious storage.
Removable panels provide good access to important systems when needed.
The full-width, hinged steel top opens
to make working with the drums and
roller systems easy. Built into the top
are a pair of 4”-diameter dust ports.
These ports connect to specially
designed directional baffles within the
top that enhance the effectiveness of
the dust evacuation. For maximum
efficiency, a dust collector system
with a minimum 1200-CFM (cubic
feet per minute) capacity should be
The rubber-covered steel drums enhance accuracy and consistency.
used.
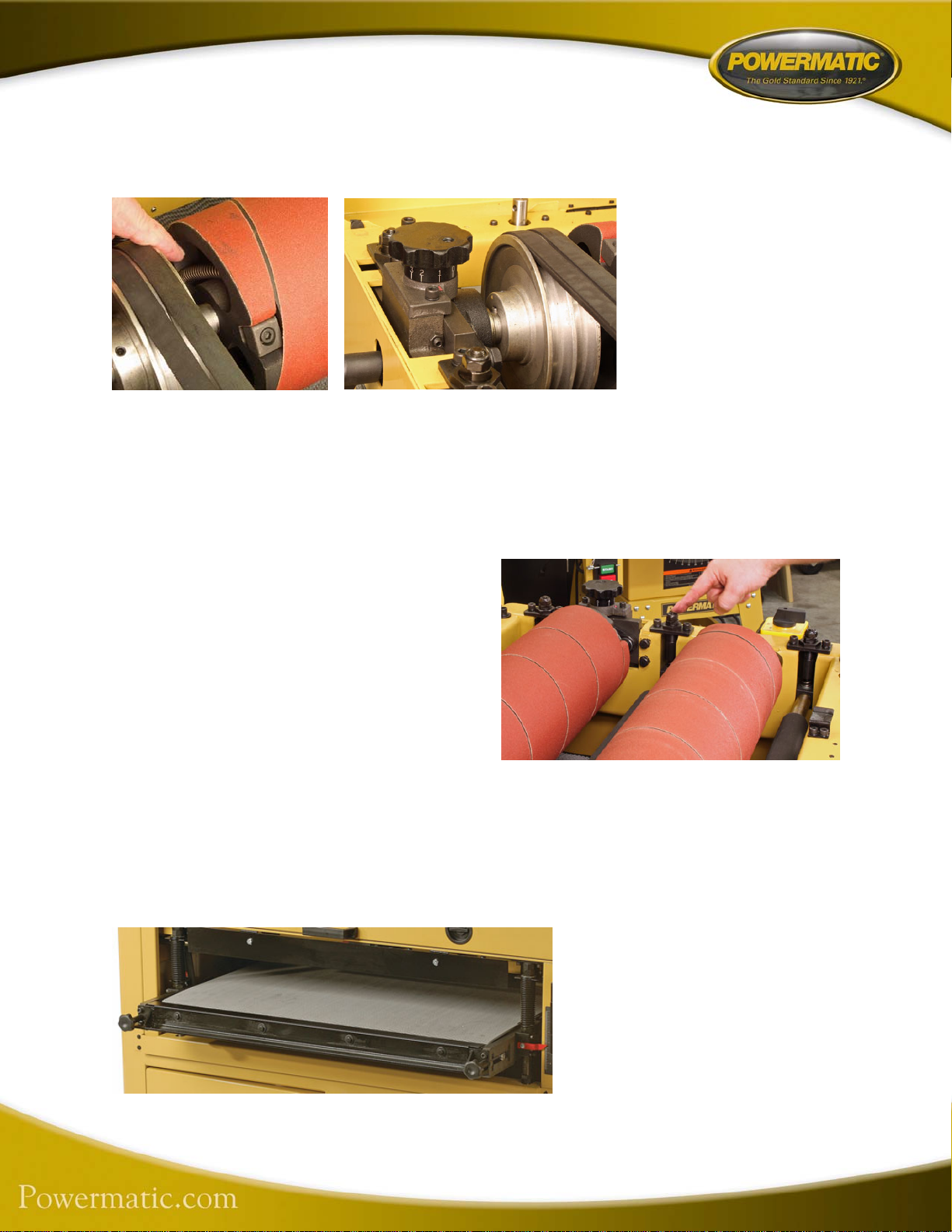
Steel Drums
The POWERMATIC
Dual Drum Sanders
feature dual steel drums
spinning at a consistent
1700-RPM that are
precisely machined and
then given a hard
durometer rubber coating
Installing abrasive strips (left) is easy and secure with the wedge retainers. The rear drum
is adjustable (right) using this knob to compensate when using different abrasive grits
than on the front drum.
that ensures a flat, nonmarring surface. These
6”-diameter steel drums
have the strength to resist
flex during sanding for
maximum accuracy and consistency.
The rear drum is independently adjustable, which allows fine-tuning, especially when it is
equipped with a different grit paper than is on
the front drum. A special graduated knob at
either end of the rear drum makes setting this
height for the abrasive grit being used easy and
accurate. We include a handy chart on the
cabinet below the adjustment that shows the
correct settings for the various grits.
The abrasive strips can be purchased ready to
cut or can be cut in your shop. The strips are
secured to the drums using simple but very
tough and highly effective wedges. Tuck the end
The pressure rollers are easily adjusted with these tough but
simple mechanisms located up top for easy access.
of the paper in, insert the wedge and tighten the
retaining bolt.
The pressure rollers are also fully adjustable. The easy to use adjusters are located on top at
either end of the rollers for easy access. These adjusters are designed to be rugged and to hold
their adjustment during long periods of use. The full adjustment procedure is described in the
instruction manual.
Conveyor Table and Belt
A heavy cast iron table has been
precisely machined to insure
flatness. The table is raised and
The conveyor belt runs on a precision cast iron table for flatness and
consistency.