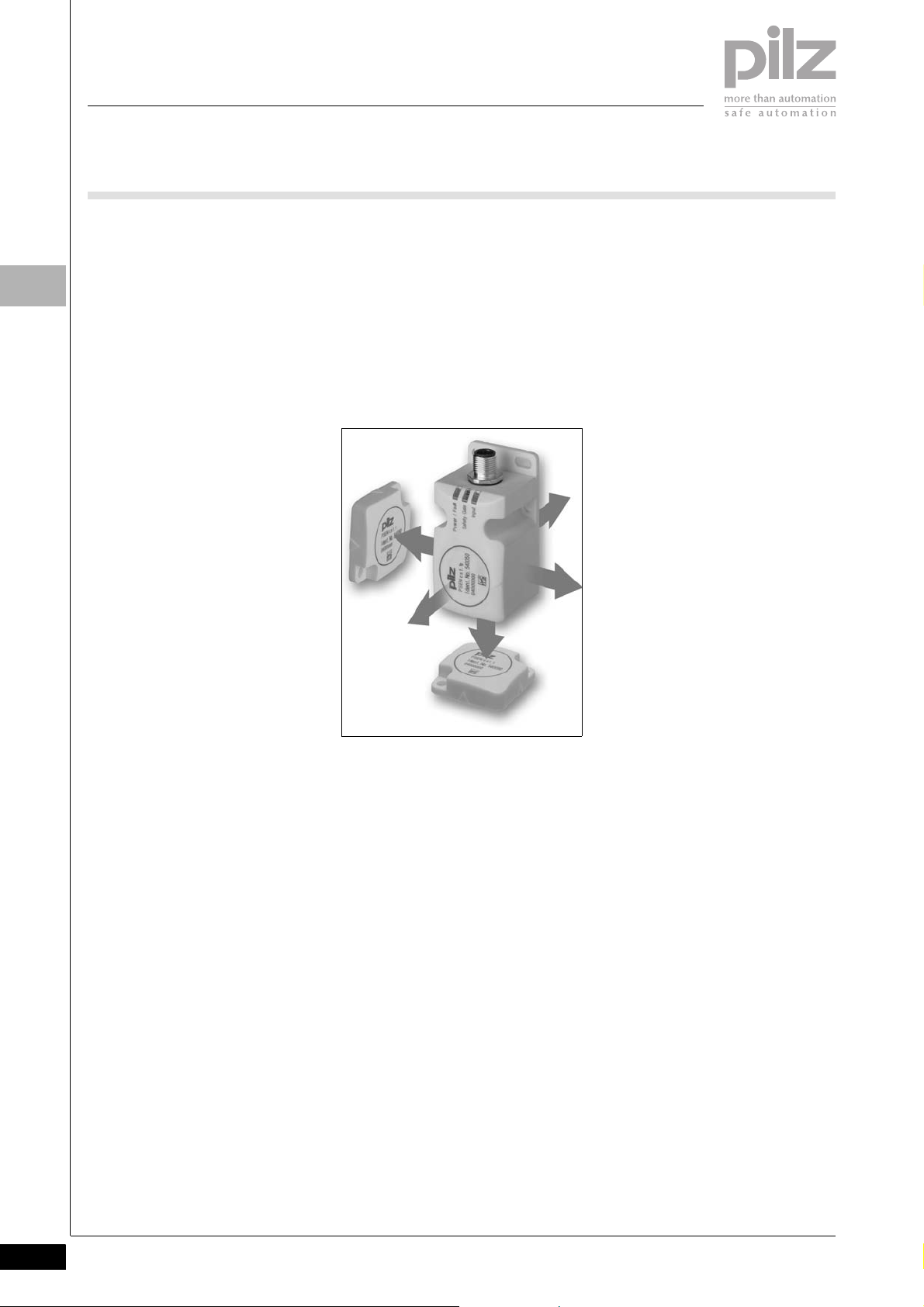
Basics
Description
PSENcode
1.1
PSENcode1.12007-03BasicsDescriptionPSENcodePSEN
Operation of the safety switch
PSENcode safety switches act in conjunction with a coded actuator in noncontact operation (transponder). Each
safety switch has an actuator (transponder). Together with an authorised
evaluation device they form an approved, complete solution.
Two microcontrollers evaluate the input circuits and switch the outputs accordingly. The microcontrollers
monitor each other.
If the correct actuator (transponder) is
in the response range, signal output
Y32 will switch on. If the input circuits
are also closed, safety contacts 12
and 22 conduct and the "Input" LED illuminates yellow.
If the actuator is not within the response range (open safety gate) or the
input circuits are not closed, safety
contacts 12 and 22 and signal output
Y32 are blocked.
If the shutdown occurs via the inputs,
reactivation of the outputs is only possible after both safety inputs are
locked simultaneously (partial operation lock).
procedure at the safety switch
(max. 8 additional learning procedures).
` Safety switch with ATEX approval
for use in potentially explosive atmospheres.
Directions of actuation
PSENcode safety switches have 5 different sensing faces:
1.1-6
Protection against defeat
Safety switches from the PSEN range
are designed to guarantee security
against manipulation through protection against defeat in accordance with
VDE 0660.
Selection criteria
` Coding
– Coded actuator: Safety switch
only accepts PILZ actuators
– Fully coded actuator (unique
code): The actuator has a unique
electronic coding. The safety
switch only reacts to a single actuator.
– Fully coded actuator (unique
code, teachable): The actuator
has a unique electronic coding.
The safety switch only reacts to
a single actuator. New actuators
can be taught in via a learning
2007-03Pilz GmbH & Co. KG, Sichere Automation, Felix-Wankel-Straße 2, 73760 Ostfildern, Germany
Telephone: +49 711 3409-0, Telefax: +49 711 3409-133, E-Mail: pilz.gmbh@pilz.de
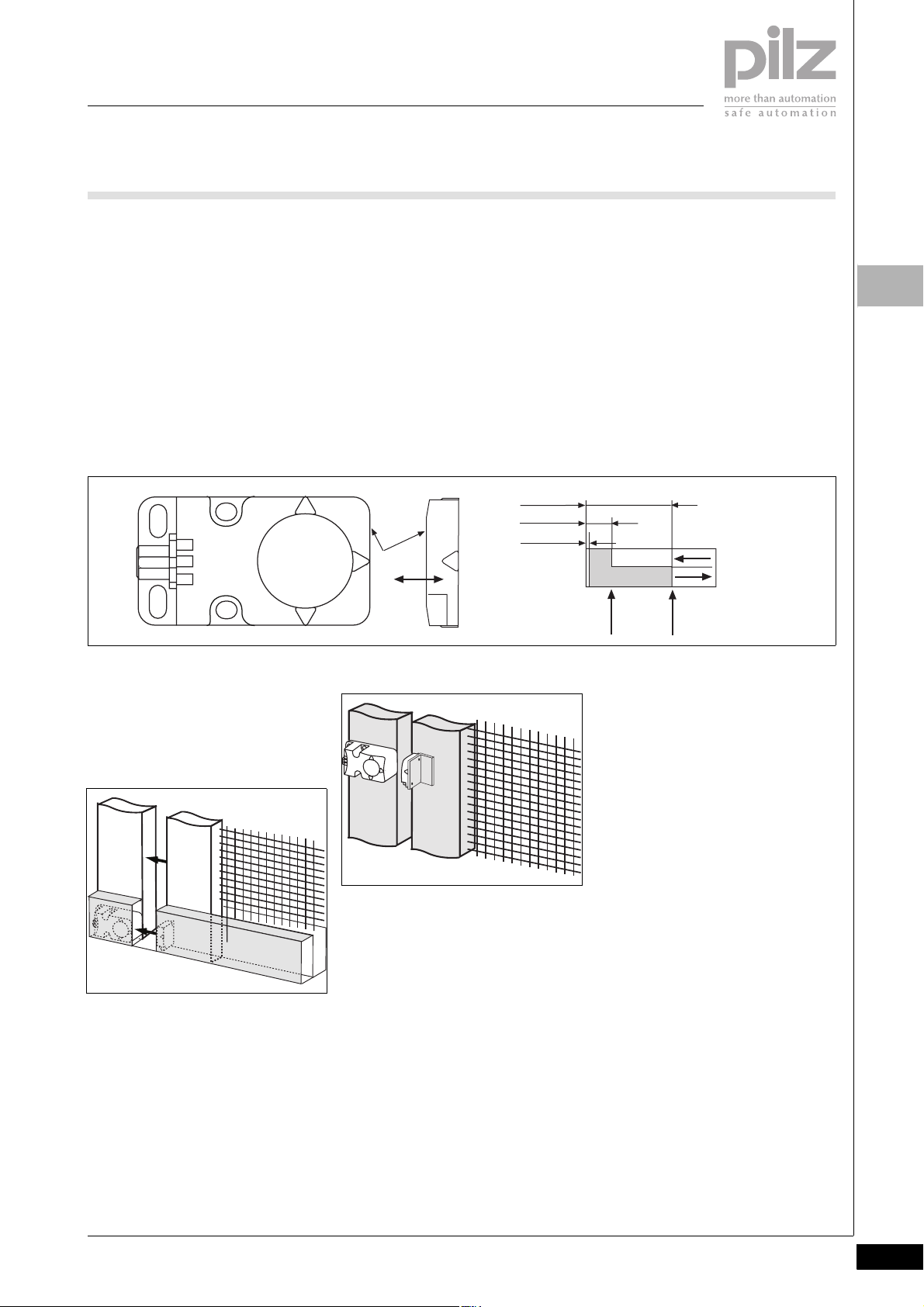
Basics
Description
PSENcode
Operating distance
A high lateral and vertical offset can be
achieved with long operating distances. This will provide greater tolerances
for installation and even less sensitivy
towards spring-back or swinging from
safety gates.
Operating distances:
` Assured operating distance s
This is the distance from the sensing face, within which the presence
:
ao
of the specified target is correctly
detected under all specified environmental conditions, manufacturing tolerances and internal
component faults.
` Typical operating distance s
This is the distance from the sensing face, within which the presence
of the specified target is typically
detected correctly.
` Release distance S
This is the distance from the sensing face, beyond which the absence
active area
:
r
s
ar
s
ao
s
omin
Assured
operating distance
of the specified target is correctly
detected under all specified environmental conditions and manufacturing tolerances.
` Assured release distance S
o
This is the distance from the sensing face, beyond which the absence
of the specified target is correctly
detected under all specified environmental conditions, manufacturing tolerances and internal
component faults.
On
Off
Assured release
distance
:
ar
1.1
If you install safety switches and actuators in the vicinity of electrically or
magnetically conductive material,
check the operating distances, as
changes can be expected.
Example 1: Concealed installation with
4 mm aluminium, visual contact between actuator and safety switch
Example 2: Installation with actuator
on a 4 mm aluminium bracket and the
safety switch flush on to aluminium
Hysteresis:
The assured release distance is longer
than the assured operating distance
> sao). The safety switches there-
(s
ar
fore have a hysteresis. If the actuator
is within s
not cause the safety switch to de-energise.
vibrations up to sar will
ao,
Lateral and vertical offset:
The operating distances stated in the
technical datails only apply if the active areas of the sensing face and actuator are installed opposite each
other in parallel. Operating distances
may deviate if other arrangements are
used. The maximum permitted lateral
and vertical offset will depend on the
safety switch you are using (see chapter entitled “Unit-specific Descriptions”, section on“Max. lateral and
vertical offset in mm”).
Pilz GmbH & Co. KG, Sichere Automation, Felix-Wankel-Straße 2, 73760 Ostfildern, Germany
Telephone: +49 711 3409-0, Telefax: +49 711 3409-133, E-Mail: pilz.gmbh@pilz.de
2007-03
1.1-7
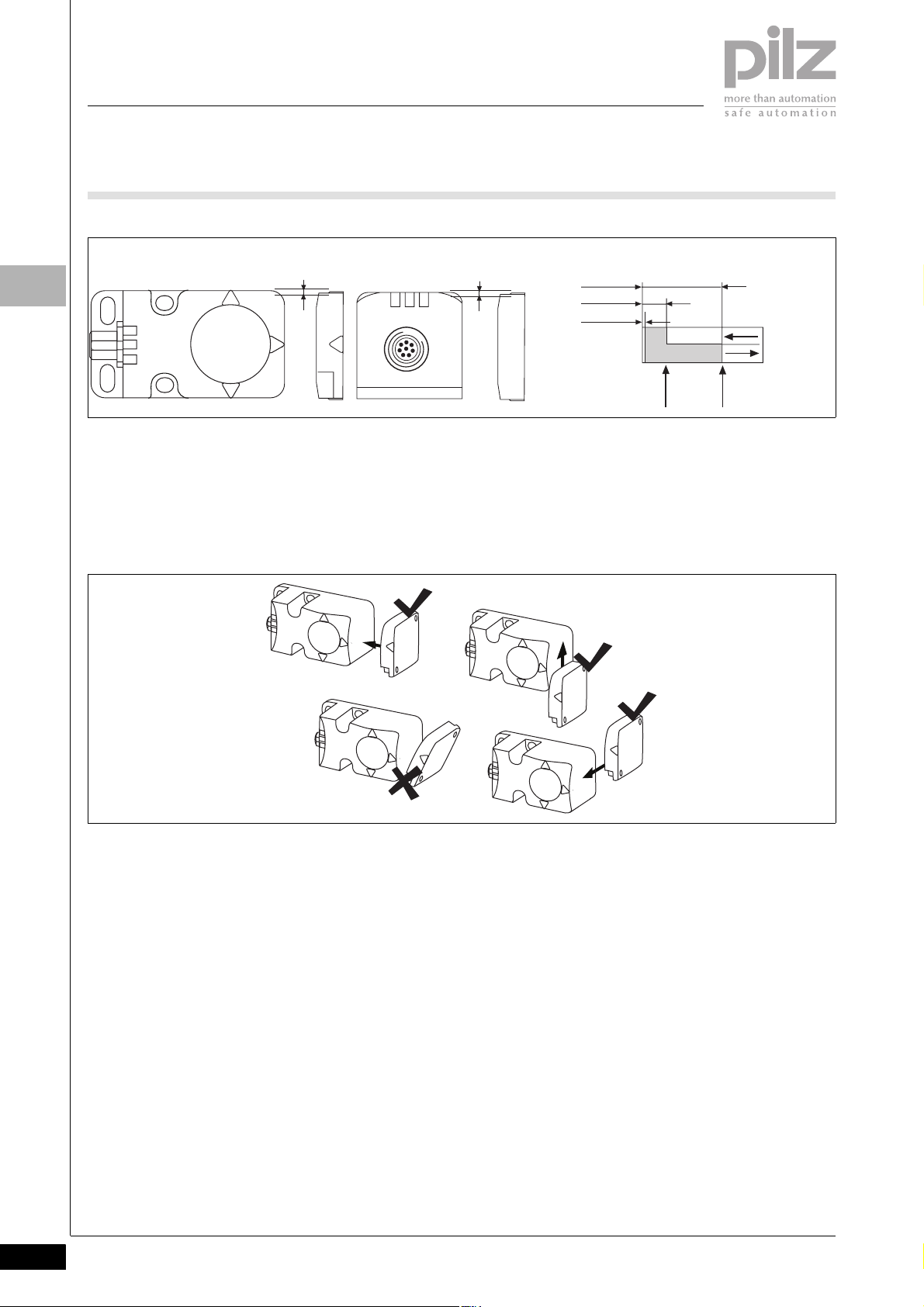
Basics
Description
PSENcode
1.1
Lateral offset Height offset
active area
Actuator's direction of movement
The sensing face of the actuator is
permitted to move in parallel to the
sensing face on the safety switch.
Movements in which the actuator is
Operating distance
s
ar
s
ao
s
omin
Assured
operating distance
tilted in relation to the safety switch are
not permitted.
On
Off
Assured release
distance
1.1-8
Pass-by speed
If the safety switch is being used as a
position switch, the maximum permitted pass-by speed of the actuator is
important. This must be defined so
that the evaluation device can detect
the status of the safety switch. This
value is device-specific.
Evaluation devices
Each safety switch has an approved
evaluation device and possibly also an
interface.
INFORMATION
For details of which evaluation device
is approved for which safety switch,
please refer to the chapter entitled
Telephone: +49 711 3409-0, Telefax: +49 711 3409-133, E-Mail: pilz.gmbh@pilz.de
“Wiring and Commissioning” or to the
details in the chapter entitled “Unitspecific Descriptions”.
Connecting safety switches in series
Several safety switches are connected
in series to an input on an evaluation
device via a junction. This means, for
example, that several safety gates on a
plant can be monitored using a single
evaluation device.
Up to 10 safety switches can be connected in series (can be used for applications up to Category 4 in
accordance with EN 954-1).
The switch status of the individual
safety switches (safety gate open or
closed) is displayed through LEDs and
can be evaluated via the auxiliary output, e.g. with a PLC.
Housing material
The housing of the PSENcode safety
switch is made from silicone-free PBT
plastic, which is insensitive to dirt. For
details of the chemical resistance of
the housing material, please refer to
the table in the chapter entitled
“Chemical resistance”.
2007-03Pilz GmbH & Co. KG, Sichere Automation, Felix-Wankel-Straße 2, 73760 Ostfildern, Germany