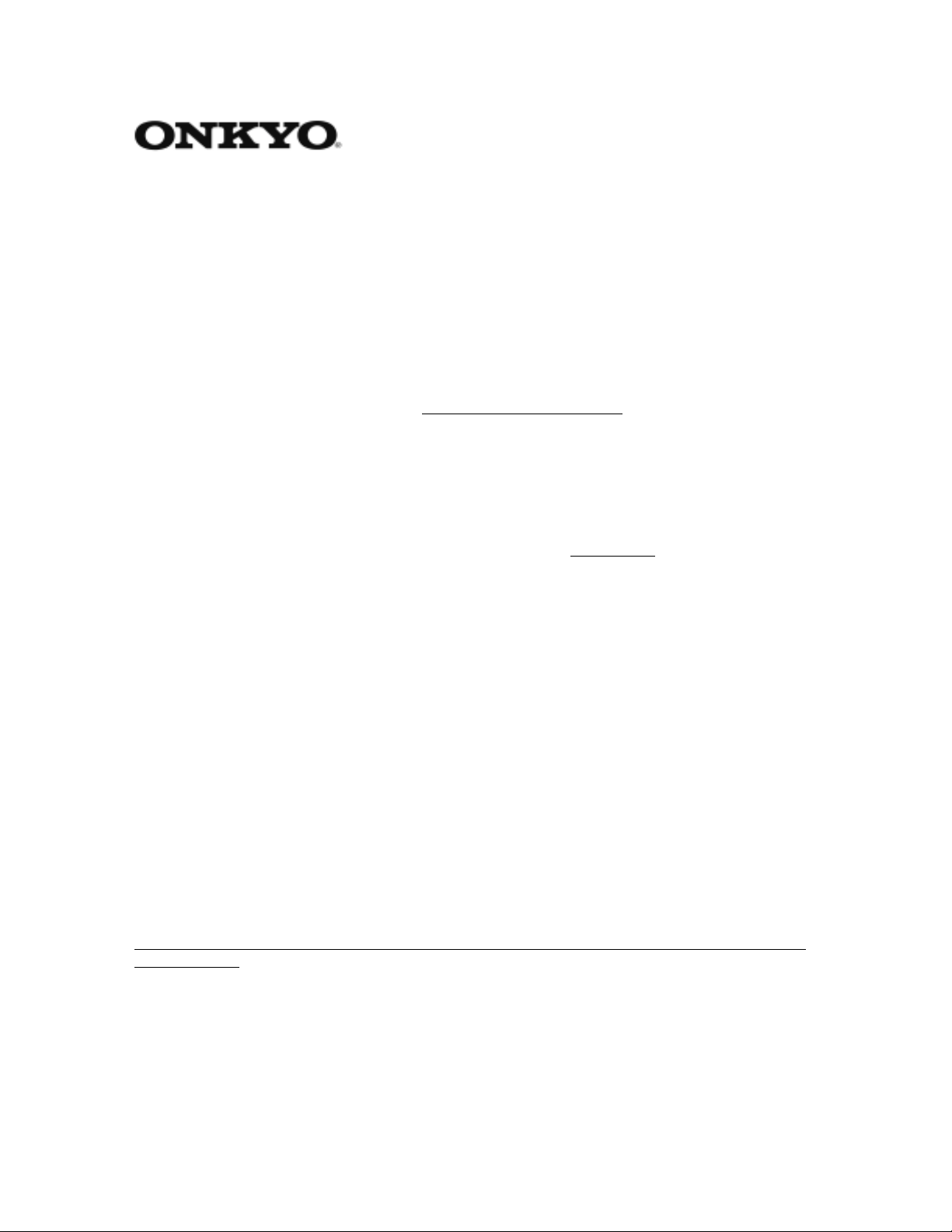
ONKYO USA CORPORATIO N
Troubleshooting News: 05/30/01
In this article we will look at the few steps we need to take prior to beginning work on
any give n product bro ught in for ser vice.
1. Before disassembling and hooking up a system, understand the problem description
as mentioned by customer. The basis of the troubleshooting steps and methods
depends on the problem described by the consumer. H ence, asking the customer as
much questions as possible would help simplify test setup, and expedited ser vice.
2. Consider differentiating between
what is and not working from the consumer
point of view and compare that against bench test fi nding based on operations test.
It is important to know how a unit works. When in doubt please refer to owners
manual. It can be a waste o f time to look for a problem that may be a mater of user
setup error from the start. Most of these errors were mistaken for a microprocessor
problem only to find out was not.
3. One of the major problems in service technology is lack of understanding in how
the circuit operates and establishing breakdown to a bloc k form. A good start will
be the block diagram. In a digital technology such a di vision even becomes blurred,
as most components se em to share a common source o f clock and data line. But all
that can be broken down to establish a problem bloc k.
4. An age-old trouble shooting still rides high in digital age. Check power supply, and
always follow the signal path such as Data, Strobe, Clock etc. All of these signals may be difficult to
catch up without the appropriate tools. However it is not an excuse for failing to address service intrusted by a customer.
5. Now that you have come to pin point the trouble spot to a block, followed by a component, the trick to
removing a defective part becomes an issue. Most of S/M components can be hard to remove safely
unless a proper tool is used. There are number manufacturers who make decent de-soldering (re-work)
stations for such purpose. Discrete components also need handling with care as most are very high gain
and can easily be damaged.
6. Service is a joint venture. One needs the consumer input to resolve the problem and as well as clear
understanding of the product operation as to not misdiagnose claimed product failure. Ability of a global
assessment to a block by block localization leads to a pin pointing of a failed component. Given a good
workmanship in the extraction of defective component, a happy consumer would be born, to become a
best source of service growth.
“A good servicing technology not only need understanding of the part that does not work, but also parts that
are functioning.”
Gedion Teklewolde
Technical Supervisor
ONKYO USA Corp.