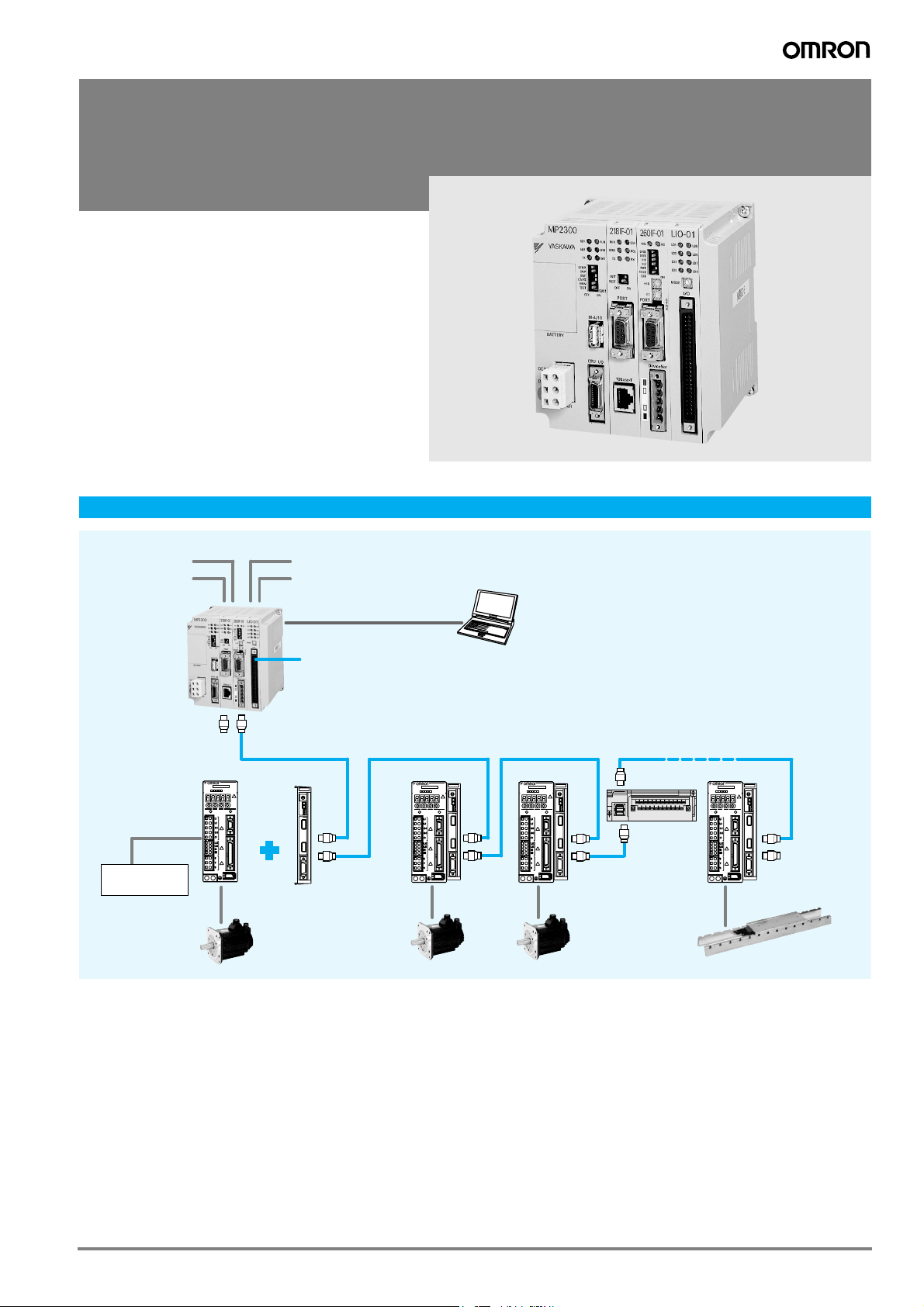
MP2300 - MECHATROLINK-II
Motion controller
Stand-alone solution for advanced
motion control
• Up to 48 axes controlled with minimum wiring
• Self configuration of nodes for an easy setup
• DeviceNet, PROFIBUS and ethernet network interfaces provide easy connectivity to any system
• Supports position, speed and torque control
• Electronic CAM profiles and axes synchronization
• The high-speed bus MECHATROLINK-II is specially
designed for motion control
• Support for I/Os and pulse inputs locally and over the
network
• Access to the complete system from one point.
System configuration
DeviceNet
PROFIBUS-DP
Sigma-II series
Servo Drive
Input
Limit switches
contact sensors
Terminator
SGDH-
Ver.
CHARGE POWER
SERVOPACK
200V
CN3
CN1
CN2
Ethernet
RS-232C, RS-422/485
Local I/Os
Motion controller MP2300
(one can handle up to 3 Mechatrolink-II networks)
MECHATROLINK-II
SERVOPACK
NS115
S
W
1
A
R
S
W
2
C
N
6
A
C
N
6
B
C
N
4
JUSP-NS115
SGDH-
200V
Ver.
CHARGE POWER
CN3
CN1
CN2
Mechatrolink-II
unit
Sigma-II series
Servo Motor
Personal computer
Software: MPE720 tool
21 nodes max.
18 servo axes max. + I/O stations
Totel lenght: 50 m
NS115
S
W
1
A
R
S
W
2
C
N
6
A
C
N
6
B
C
N
4
SERVOPACK
NS115
SGDH-
S
200V
Ver.
W
1
A
R
S
W
2
CHARGE POWER
CN3
C
N
6
A
CN1
C
N
6
B
C
N
4
CN2
I/O module
RUNTX 1 2 3 4 5 6 7 8 120DDI 34330
C
N
1
C
N
2
SERVOPACK
NS115
SGDH-
S
200V
Ver.
W
1
A
R
S
W
2
CHARGE POWER
CN3
C
N
6
A
CN1
C
N
6
B
Terminator
C
N
4
CN2
Sigma-II series
Linear Motor
67Motion controller
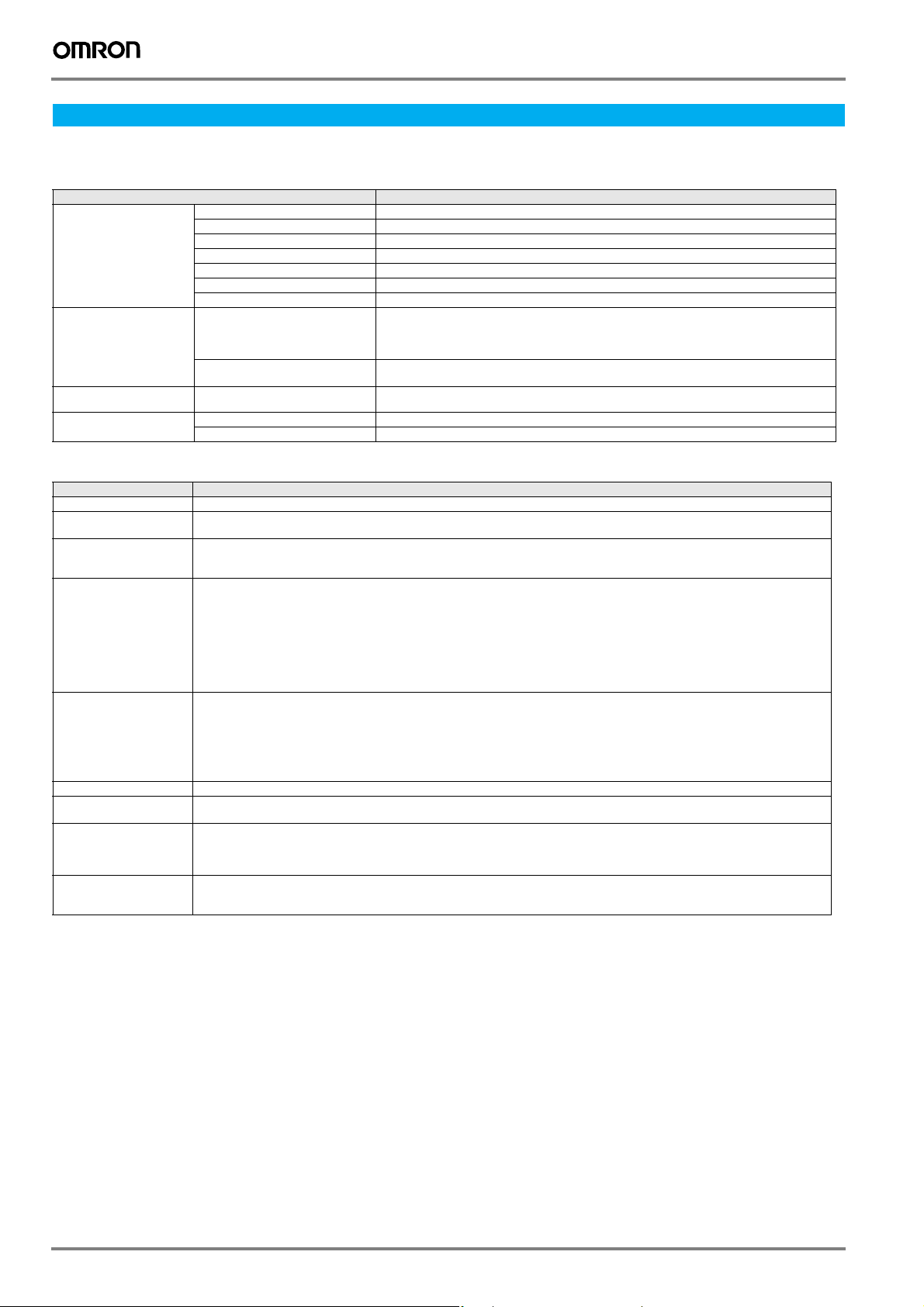
Specifications
General specifications
Hardware specifications
Items Specifications
Environmental conditions Ambient operating temperature 0 to 55 °C
Mechanical operating
conditions
Electrical operating
conditions
Installation
requirements
Sequential function specifications
Items Specifications
Control method Sequence: High-speed and low-speed scan methods
Programming language Ladder diagram: Relay circuit
Scanning Two scan levels: High-speed scan and low-speed scan
User drawings, functions
and motion programs
Data memory Common data (M) registers:
Trace memory Data trace: 128 Kwords (32 Kwords, 4 groups), 16 points defined
Memory backup Program memory: Flash memory: 8 MBytes (user area: 5.5 MBytes) definition files,ladder programs, motion programs, etc.
Data types Bit (relay): ON/OFF
Register designation
method
Ambient storage temperature -25 to 85 °C
Ambient operating humidity 30% to 95% (with no condensation)
Ambient storage humidity 5% to 95% (with no condensation)
Pollution level Pollution level 1 (conforming to JIS B 3501)
Corrosive gas There must be no combustible or corrosive gas.
Operating altitude 2,000 m above sea level or lower
Vibration resistance Conforming to JIS B 3502:
Shock resistance Conforming to JIS B 3502:
Noise resistance Conforming to EN 61000-6-2, EN 55011 (Group 1, Class A)
Ground Ground to 100 Ω max.
Cooling method Natural cooling
Text-type language: Numeric operations, logic operations, etc.
High-speed scan time setting: 1 to 32 ms (Integral multiple of MECHATROLINK communication cycle)
Low-speed scan time setting: 2 to 300 ms (Integral multiple of MECHATROLINK communication cycle)
Startup drawings (DWG.A):
Interrupt processing drawings (DWG.I):
High-speed scan process drawings (DWG.H):
Low-speed scan process drawings (DWG.L):
Number of steps:
User functions:
Motion programs:
Revision history of drawings and motion programs
Security function for drawings and motion programs
System (S) registers:
Drawing local (D) registers:
Drawing constant (#) registers:
Input (I) registers:
Output (O) registers:
Constant (C) registers:
Data memory: Battery backup: 256 Kbytes, M registers, S registers, alarm history, trace data
Integer: -32768 to +32767
Double-length integer: -2147483648 to +2147483647
Real number: ± (1.175E-38 to 3.402E+38)
Register number: Direct designation of register number
Symbolic designation: Up to 8 alphanumeric characters (up to 200 symbols per drawing)
With automatic number or symbol assignment
10 to 57 Hz with single-amplitude of 0.075 mm
57 to 150 Hz with acceleration of 1G
10 sweeps each in X, Y, and Z directions (sweep time: 1 octave/min)
2
Peak acceleration of 147 m/s
(15 G) twice for 11 ms each in the X, Y, and Z directions
64 drawings max. up to three hierarchical drawing levels
64 drawings max. up to three hierarchical drawing levels
200 drawings max. up to three hierarchical drawing levels
500 drawings max. up to three hierarchical drawing levels
Up to 1,000 steps per drawing
Up to 500 functions
Up to 256
64 Kwords
8 Kwords
Up to 16 Kwords per drawing
Up to 16 Kwords per drawing
5 Kwords (including internal input registers)
5 Kwords (including internal output registers)
16 Kwords
68 Motion controllers
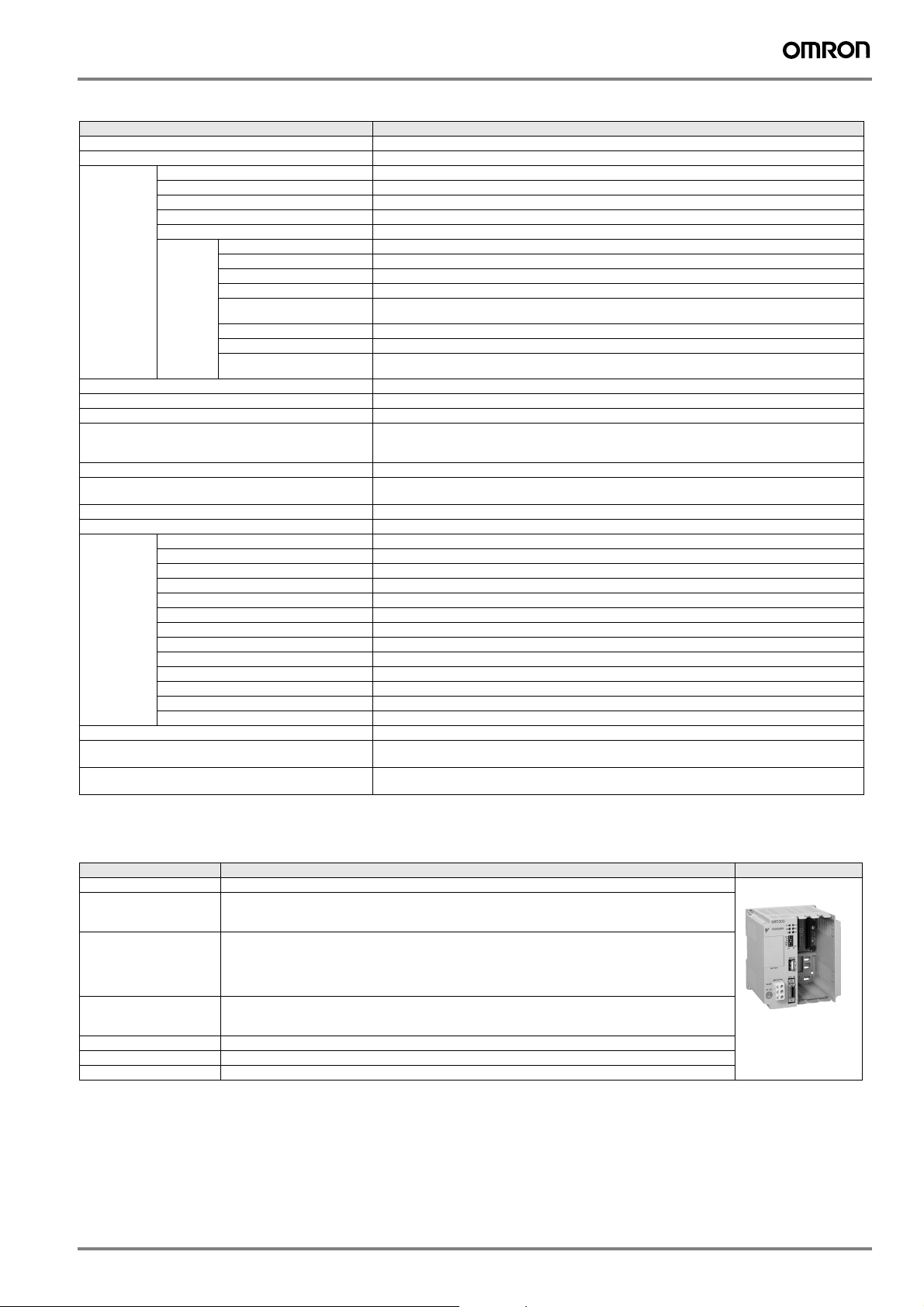
Motion control function specifications
Item Specifications
Interface MECHATROLINK-I, MECHATROLINK-II
Number of controlled axes/module Up to 16 axes
Control
specifications
Reference unit mm, inch, deg, or pulse
Reference unit minimum setting 1, 0.1, 0.01, 0.001, 0.0001, 0.00001
Maximum programmable value -2147483648 to +2147483647 (signed 32-bit value)
Speed reference unit Reference unit/s designation: mm/s, inch/s, deg/s, pulse/s
Acceleration/deceleration type Linear, asymmetric, S-curve, exponent
Acceleration/deceleration reference unit Reference unit/s
Override function Positioning: 0.01% to 327.67% by axis
Coordinate system Rectangular coordinates
Zero point re-
turn
Applicable servo drives SGDH-@@@E-OY + NS115
Applicable frequency inverters Varispeed V7, F7, G7 with MECHATROLINK-II interface
Encoders Incremental encoder
PTP control Linear, rotary, and infinite-length
Interpolation Up to 16 linear axes, 2 circular axes, and 3 helical axes
Speed reference output Yes
Torque reference output Yes
Phase control Yes
Position
control
DEC1+ phase-C pulse Yes
ZERO signal Yes
DEC1+ ZERO signal Yes
Phase-C pulse Yes
Only phase-C pulse Yes
POT and
POT Yes
Home limit switch and
HOME Yes
NOT and
NOT Yes
INPUT and
INPUT Yes
Positioning Yes
External positioning Yes
Zero point return Yes
Interpolation Yes
Interpolation with position
detection function
JOG operation Yes
STEP operation Yes
Parameter changes during
motion command execution
Reference unit/min. designation: mm/min, inch/ min, deg/min, pulse/min
Percentage designation: Percentage of rated speed
2
Acceleration/deceleration time constant: Time from 0 to rated speed (ms)
phase-C pulse
phase-C pulse
phase-C pulse
phase-C pulse
(for inverter version support contact your OMRON sales office)
Yaskawa absolute encoder
designation: mm/s2, inch/s2, deg/s2, pulse/s
Yes
Yes
Yes
Yes
Yes
Yes
2
MP2300 CPU (basic module)
Items Specifications Appearance
Model JEPMC-MP2300
Power supply Input power voltage: 24 VDC±20%
Motion network One channel for MECHATROLINK-II:
I/O signals Digital input: 8 points (one point can be used for interrupts),
Slot for optional modules 3 slots
Dimensions (mm) 130x120x108 (HxWxD)
Weight 500 g
Current consumption:1 A
Inrush current: 40 A or less
Twenty-one stations, including servo drives and I/O equipment, can be connected.
(16 axes for servo drives and inverters)
Transmission speed: 10Mbps (MECHATROLINK-II)
Transmission distance: See “MECHATROLINK-II repeater”
Digital output: 4 points, 24 VDC, 100 mA, open collector, and sink mode output (NPN)
24 VDC, 4 mA, and source mode or sink mode input
Motion controller 69